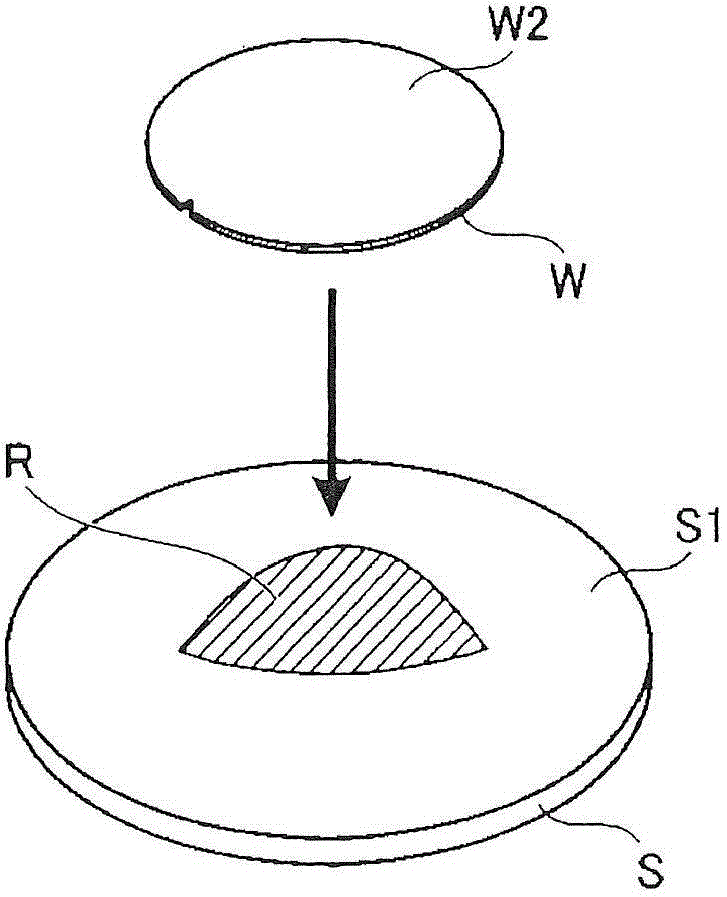
本发明涉及磨削光器件晶片等板状物的磨削方法,特别是涉及对粘贴于支承部件的板状物进行磨削以加工至预定的厚度的板状物的磨削方法。
背景技术:近年来,为了实现小型轻量的光器件,要求使光器件晶片变薄。对于光器件晶片,在表面的由分割预定线划分出的各区域形成光器件后,通过磨削背面来使光器件晶片变薄。为了保护光器件,一般是在薄化时在光器件晶片的表面粘贴保护带(例如,参照专利文献1)。可是,光器件晶片的刚性随着变薄而显著降低。因此,光器件晶片随着进行磨削处理而大幅翘曲,发生裂纹或裂缝等的可能性升高。而且,如果使光器件晶片的外周部刀刃化而变薄,则还存在在外周部发生裂缝或裂纹、缺口等的危险。为了消除与磨削相伴随的上述问题,提出有将作为被加工物的光器件晶片粘贴于刚体的支承部件来进行磨削的方法(例如,参照专利文献2)。在该方法中,通过以由刚体构成的支承部件支承光器件晶片,光器件晶片得到了加强,因此,抑制了磨削时的光器件晶片的翘曲等,从而能够防止破损。专利文献1:日本特开平5-198542号公报专利文献2:日本特开2004-207606号公报在上述的磨削方法中,作为被加工物的光器件晶片例如通过作为固定剂的树脂固定于支承部件的表面,并被磨削至预定的厚度。磨削后的光器件晶片通过在使树脂软化后物理地剥离而与支承部件分离。可是,由于变薄后的光器件晶片的刚性变得非常低,因此,在使支承部件剥离时,有导致光器件晶片破损的危险。
技术实现要素:本发明正是鉴于该情况而作出的,其目的在于提供一种板状物的磨削方法,能够抑制在使支承部件从磨削得较薄的板状物剥离时的板状物的破损。本发明的板状物的磨削方法是对粘贴在支承部件上的板状物的背面进行磨削以使其变薄至预定厚度的板状物的磨削方法,所述板状物的磨削方法的特征在于,所述板状物的磨削方法包括:板状物载置工序,在该板状物载置工序中,对所述板状物的表面和由金属制成的支承部件的表面中的至少一方涂敷光硬化树脂,使所述板状物的表面与所述支承部件的表面面对,按压所述板状物,直至使所述板状物埋没于所述光硬化树脂且光硬化树脂在所述板状物的整个外周的范围隆起至所述板状物的背面,由此载置所述板状物,所述由金属制成的支承部件形成为能够通过来自外部的力而弯曲的厚度;板状物固定工序,在该板状物固定工序中,在实施了所述板状物载置工序后,隔着所述板状物对所述光硬化树脂照射紫外线,从而将板状物固定至所述支承部件上;薄化工序,在该薄化工序中,在实施了所述板状物固定工序后,通过保持工作台来保持所述支承部件侧,并对板状物的背面进行磨削以使所述板状物变薄至所述预定厚度;以及除去工序,在该除去工序中,在实施了所述薄化工序后,对所述光硬化树脂进行加热或加水以使其软化,保持所述板状物的磨削面,使所述支承部件和光硬化树脂弯曲而从所述板状物剥离。根据该结构,由于以由金属制成的支承部件支承板状物,因此,磨削时的板状物的挠曲得以抑制,从而能够将板状物磨削得较薄。而且,由于由金属制成的支承部件形成为能够通过来自外部的力弯曲的厚度,因此,能够在剥离时使支承部件弯曲,从而提高板状物与支承部件的剥离性。因此,能够抑制在使支承部件从磨削得较薄的板状物剥离时的板状物的破损。优选的是,在本发明的板状物的磨削方法中,所述支承部件的涂敷光硬化树脂的表面的表面粗糙度形成得比板状物的粘贴面的表面粗糙度大,在剥离时将光硬化树脂与所述支承部件一起剥离。根据该结构,由于支承部件的涂敷光硬化树脂的表面的表面粗糙度形成得比板状物的粘贴面的表面粗糙度大,因此,与板状物和光硬化树脂的紧密贴合性相比,提高了支承部件与光硬化树脂的紧密贴合性。由此,能够使支承部件和光硬化树脂容易地从板状物剥离。根据本发明,能够提供一种板状物的磨削方法,能够抑制在使支承部件从磨削得较薄的板状物剥离时的板状物的破损。附图说明图1A和图1B是示出在本实施方式的载置工序中将光硬化树脂涂敷于支承基板的情况的图。图2A和图2B是示出在本实施方式的载置工序中按压光器件晶片的情况的图。图3是示出在本实施方式的固定工序中对光硬化树脂照射紫外光的情况的图。图4A和图4B是示出在本实施方式的薄化工序中磨削光器件晶片的情况的图。图5A和图5B是示出在本实施方式的除去工序中从光器件晶片剥离支承基板和光硬化树脂的情况的图。图6是示出本实施方式涉及的光器件晶片的磨削方法的流程图。标号说明1:树脂涂敷装置;2:压力装置;3:紫外光照射装置;4:磨削装置;5:剥离装置;11:喷嘴;21:卡盘工作台;22:按压部;31:载置台;32:紫外光源;41:卡盘工作台(保持工作台);42:磨削轮;43:磨削磨具;51:卡盘工作台;C1、C2:旋转轴线;R:光硬化树脂;S:支承基板(支承部件);S1、W1:表面;S2、W2:背面;S3、W4:一端部;UV:紫外光(紫外线);W:光器件晶片(板状物);W3:磨削面。具体实施方式下面,参照附图对本发明的实施方式进行说明。本实施方式涉及的光器件晶片(板状物)的磨削方法包括:载置工序(板状物载置工序),在该载置工序(板状物载置工序)中,将光器件晶片载置于支承基板(支承部件);固定工序(板状物固定工序),在该固定工序(板状物固定工序)中,将光器件晶片固定于支承基板;薄化工序,在该薄化工序中,磨削光器件晶片使其变薄;以及除去工序,在该除去工序中,从光器件晶片剥离支承基板。在载置工序中,将光器件晶片按压并载置于涂敷有光硬化树脂的由金属制成的支承基板。在固定工序中,通过照射紫外光(紫外线)使光硬化树脂硬化来将光器件晶片固定于支承基板。在薄化工序中,对光器件晶片的背面侧进行磨削以使光器件晶片变薄。在除去工序中,在使光硬化树脂软化后使支承基板弯曲并将支承基板与光硬化树脂一起从光器件晶片剥离。在本实施方式中使用的由金属制成的支承基板同时具有薄化工序中的良好的支承性和除去工序中的良好的剥离性。由此,通过本实施方式涉及的光器件晶片的磨削方法,能够在将光器件晶片磨削得较薄的基础上容易地使支承基板剥离。下面,对本实施方式涉及的光器件晶片的磨削方法的详细情况进行说明。参照图1A、图1B和图2A、图2B对载置工序进行说明。图1A和图1B是示出在载置工序中涂敷光硬化树脂的情况的图,图2A和图2B是示出在载置工序中按压光器件晶片的情况的图。如图1A所示,首先,在树脂涂敷装置1中,在支承基板S的表面S1涂敷光硬化树脂R。树脂涂敷装置1具备能够朝向下方喷出液状物的喷嘴11,从该喷嘴11喷出用于将光器件晶片W固定于支承基板S的作为固定剂的光硬化树脂R。在涂敷光硬化树脂R后,如图1B所示,将光器件晶片W定位于支承基板S的上方。并且,以通过光器件晶片W和支承基板S夹持光硬化树脂R的方式将光器件晶片W重叠在支承基板S的涂敷有光硬化树脂R的区域上。作为被加工物(板状物)的光器件晶片W具备这样的结构:在具有大致圆盘形状的蓝宝石基板的表面层叠有氮化镓类化合物半导体层。在光器件晶片W的表面W1(在图1中未图示,参照图2A和图2B等)设有格子状的分割预定线(未图示),在由该分割预定线划分出的各区域中形成有光器件(未图示)。支承基板S是形成为能够通过外力弯曲的厚度的具有大致圆盘形状的铝板。该支承基板S构成为比光器件晶片W大的面积,以便能够支承光器件晶片W的整体。支承基板S的表面S1的表面粗糙度比光器件晶片W的表面W1的表面粗糙度大。因此,支承基板S与光硬化树脂R的接触面积比光器件晶片W与光硬化树脂R的接触面积广,光硬化树脂R牢固地紧密贴合于支承基板S侧。能够通过例如喷砂或粗磨削处理等来增大表面粗糙度。光硬化树脂R是通过照射紫外光而硬化的无溶剂的光硬化树脂(光硬化性树脂)。如图1A所示,该光硬化树脂R以从树脂涂敷装置1的喷嘴11滴下至支承基板S的表面S1的中央附近的方式进行涂敷。另外,在本实施方式中,示出了使用无溶剂的光硬化树脂R的例子,但是,只要能够将光器件晶片W固定于支承基板S,也可以使用其它的固定剂。例如,可以使用热硬化树脂(热硬化性树脂)等。如图2A和图2B所示,在将光器件晶片W重叠于支承基板S上后,利用压力装置2将光器件晶片W向支承基板S按压。压力装置2具备卡盘工作台21,该卡盘工作台21具有由多孔质陶瓷材料制成的吸附面。通过在卡盘工作台21吸附支承基板S的背面S2,从而将支承基板S保持在卡盘工作台21上。在卡盘工作台21的上方,以能够上下移动的方式设有用于按压光器件晶片W的背面W2的按压部22。如图2A所示,通过使按压部22与光器件晶片W的背面W2接触并通过按压部22施加向下的力,从而将光器件晶片W向下按压。当将光器件晶片W向下按压时,光器件晶片W与支承基板S之间的间隔变窄,如箭头A所示,光硬化树脂R呈放射状扩展。当进一步增强按压部22的按压力时,如图2B所示,使得光器件晶片W埋没于光硬化树脂R。当如此使光器件晶片W埋没于光硬化树脂R时,成为光硬化树脂R在光器件晶片W的整个外周隆起的状态,光硬化树脂R绕到光器件晶片W的背面W2侧。通过隆起并绕至背面W2侧的状态下使光硬化树脂R硬化,能够将光器件晶片W牢固地固定于支承基板S。接下来,参照图3对固定工序进行说明。图3是示出在固定工序中对光硬化树脂R照射紫外光UV的情况的图。在上述的载置工序中载置了光器件晶片W的支承基板S被搬送至紫外光照射装置3并被照射紫外光UV。紫外光照射装置3具备供支承基板S配置的载置台31和位于载置台31的上方的紫外光源32。如图3所示,在固定工序中,将支承基板S配置于载置台31,从紫外光源32向光器件晶片W的背面W2侧照射紫外光UV。光器件晶片W由使预定波长的紫外光UV透过的蓝宝石基板构成,照射的紫外光UV透过光器件晶片W到达光硬化树脂R。隔着光器件晶片W照射了紫外光UV的光硬化树脂R由于化学反应而硬化,从而将光器件晶片W固定于支承基板S。另外,硬化后的光硬化树脂R能够在后面的薄化工序中与光器件晶片W一起磨削。接下来,参照图4A和图4B对薄化工序进行说明。图4A和图4B是示出在薄化工序中磨削光器件晶片W的情况的图。在固定工序中固定了光器件晶片W的支承基板S通过磨削装置4磨削光器件晶片W的背面W2侧。磨削装置4具备卡盘工作台(保持工作台)41,该卡盘工作台41具有由多孔质陶瓷材料制成的吸附面。在卡盘工作台41的下方设有未图示的旋转机构,卡盘工作台41绕旋转轴线C1旋转。利用该卡盘工作台41吸附支承基板S的背面S2来保持支承基板S。在卡盘工作台41的上方,以能够上下移动的方式设有磨削轮42。在磨削轮42的上方设有未图示的旋转机构,磨削轮42绕旋转轴线C2旋转。在磨削轮42的下部配置有磨削磨具43。如图4A所示,通过在使磨削磨具43与光器件晶片W的背面W2接触的状态下使卡盘工作台41与磨削轮42相对旋转,从而磨削光器件晶片W的背面W2侧。此时,在外周部隆起的光硬化树脂R也同时被磨削。另外,磨削轮42以比卡盘工作台41快的速度旋转。在卡盘工作台41的附近设有游标高度尺(未图示),从而能够测量光器件晶片W的厚度。通过一边利用该游标高度尺测量光器件晶片W的厚度一边进行磨削,从而如图4B所示地使光器件晶片W变薄为预定厚度。由于通过光硬化树脂R加强了光器件晶片W的外周部,因而防止了由刀刃化引起的裂缝或裂纹、缺口等。在变薄后的光器件晶片W,通过磨削形成的磨削面W3露出。参照图5A和图5B对除去工序进行说明。图5A和图5B是示出在除去工序中从光器件晶片W剥离支承基板S和光硬化树脂R的情况的图。在该除去工序中,通过剥离装置5使支承基板S和光硬化树脂R从变薄的光器件晶片W剥离。剥离装置5具备卡盘工作台51,该卡盘工作台51具有由多孔质陶瓷材料制成的吸附面。利用该卡盘工作台51吸附在薄化工序中露出的光器件晶片W的磨削面W3。在卡盘工作台51设有用于使光硬化树脂R软化的加热器(未图示)。在除去工序中,首先,使光器件晶片W的磨削面W3吸附于卡盘工作台51并由加热器加热,使光硬化树脂R软化。该软化也可以通过加水处理来进行。通过加水处理使光硬化树脂R膨胀,由此使光硬化树脂R软化。接下来,如图5A所示,将支承基板S的一端部S3向斜上方上拉而使支承基板S弯曲,从而使支承基板S从光器件晶片W的一端部W4剥离。由于支承基板S的表面S1的表面粗糙度比光器件晶片W的表面W1的表面粗糙度大,因此,光硬化树脂R比光器件晶片W侧牢固地紧密贴合于支承基板S侧。因此,光硬化树脂R在与支承基板S而不是光器件晶片W紧密贴合的状态下被剥离。即,支承基板S和光硬化树脂R被一体地从光器件晶片W剥离。由于支承基板S形成为能够弯曲的厚度,因此,如果将一端部S3向斜上方上拉,则支承基板S弯曲,并从一端部S3(一端部W4)侧逐渐剥离。在一端部S3(一端部W4)侧剥离后,如图5B所示,将支承基板S的一端部S3进一步向斜上方上拉,使支承基板S弯曲。由此,进行光器件晶片W与支承基板S和光硬化树脂R的剥离,最终,支承基板S和光硬化树脂R完全从光器件晶片W剥离。图6是示出本实施方式涉及的光器件晶片W的磨削方法的流程图。如图6所示,首先,在载置工序(步骤ST1)中,在支承基板S的表面S1涂敷光硬化树脂R,将光器件晶片W重叠于支承基板S上。然后,按压光器件晶片W,以使光器件晶片W埋没于光硬化树脂R。通过该按压,使光硬化树脂R绕至光器件晶片W的背面W2侧为止,从而在光器件晶片W的整个外周使光硬化树脂R隆起。接下来,在固定工序(步骤ST2)中,照射紫外光UV使光硬化树脂R硬化。由此,将光器件晶片W固定于支承基板S。另外,在使用其它固定剂的情况下,只要应用与固定剂对应的硬化处理(固定处理)即可。例如,在使用热硬化树脂的情况下,通过加热使热硬化树脂硬化从而将光器件晶片W固定于支承基板S。然后,在薄化工序(步骤ST3)中,对光器件晶片W的背面W2侧进行磨削,使光器件晶片W变薄为预定厚度。在本实施方式中,由于使用了刚性较高的由金属制成的支承基板S,因此,能够对伴随着磨削的光器件晶片W的刚性的降低通过支承基板S进行补足。由此,能够抑制在通过磨削变薄时的光器件晶片W的破损。然后,在除去工序(步骤ST4)中,使光硬化树脂R软化,并使支承基板S和光硬化树脂R从变薄的光器件晶片W剥离。在本实施方式中,由于使用了形成为能够弯曲的厚度的由金属制成的支承基板S,因此,通过使由金属制成的支承基板S弯曲,能够提高除去工序中的剥离性,从而抑制剥离时的光器件晶片W的破损。而且,由于支承基板S的表面S1的表面粗糙度比光器件晶片W的表面W1的表面粗糙度大,因此能够使支承基板S和光硬化树脂R一体地从光器件晶片W剥离。这样,在本实施方式中使用的由金属制成的支承基板S同时具有薄化工序中的良好的支承性和除去工序中的良好的剥离性。因此,在将光器件晶片磨削得较薄后,能够容易地将支承部件剥离。下面,基于实施例和比较例,验证上述实施方式涉及的磨削方法的效果。但是,本发明并不限定于下面所示的实施例。(实施例)在本实施例中,按照上述实施方式所示的各工序,在将假定为光器件晶片的蓝宝石基板变薄至60μm的厚度后,将支承基板剥离。作为蓝宝石基板,使用了直径为4英寸且厚度为0.7mm的蓝宝石基板。作为支承基板,使用了直径为8英寸且厚度为0.3mm的铝板。该铝板构成为能够通过外力弯曲的厚度。作为光硬化树脂,使用了电气化学工业株式会社制造的TEMPLOC。关于磨削后的蓝宝石基板,确认了在外周是否存在光硬化树脂的剥落、是否存在裂纹、是否存在裂缝。而且,确认了是否能够通过上述实施方式的除去工序在不使蓝宝石基板破损的情况下将铝板剥离。在下述表1中示出确认结果。表1示出了5次的实验结果。圆圈标记表示光硬化树脂的剥落、裂纹、裂缝、以及剥离时的蓝宝石基板的破损一次也没有发生,叉号标记表示各种不良现象发生了一次以上。(比较例)作为比较例,对于使用与实施例不同的支承基板的情况,确认了是否在外周存在光硬化树脂的剥落、是否存在裂纹、是否存在裂缝,并且确认了是否能够在不使蓝宝石基板破损的情况下将支承基板剥离。作为支承基板,在比较例1中,采用厚度为0.7mm的硅基板,在比较例2中,采用厚度为1.0mm的玻璃基板,在比较例3中,采用厚度为0.3mm的PET板。其它条件等与实施例相同。在下述的表1中示出比较例的确认结果。表1示出了各5次的实验结果,评价基准与实施例相同。【表1】根据表1可知,在使用刚性较低的PET板的情况下,在薄化工序中会发生裂纹和裂缝,在使用刚性较高的铝板、硅基板、玻璃基板的情况下,在薄化工序不会发生裂纹和裂缝。可以认为,在刚性较低的PET板发生裂纹和裂缝的原因是PET板因磨削时的负载而挠曲从而在磨削中的蓝宝石基板发生翘曲等。与此相对,铝板、硅基板、玻璃基板这样的刚性较高的支承基板不容易因磨削时的负载而挠曲,从而能够良好地支承蓝宝石基板。而且,根据表1可知,在使用PET板或铝板的情况下,在除去工序中能够使支承基板适当地剥离,在使用硅基板或玻璃基板的情况下,在除去工序中无法使支承基板适当地剥离。这可以认为是因为PET板或铝板构成为能够弯曲,从而能够通过弯曲而对蓝宝石基板与光硬化树脂的紧密贴合部分作用适当的力从而从端部逐渐进行剥离。与此相对,由于无法使硅基板和玻璃基板弯曲,因此在剥离时容易施加过大的力,从而导致蓝宝石基板破损的可能性较高。如以上那样,根据本实施方式涉及的磨削方法,由于以由金属制成的支承基板(支承部件)S支承光器件晶片(板状物)W,因此,能够抑制磨削时的光器件晶片W的挠曲并将光器件晶片W磨削得较薄。而且,由于由金属制成的支承基板S形成为能够通过来自外部的力弯曲的厚度,因此,能够在剥离时使支承基板S弯曲,从而提高光器件晶片W与支承基板S的剥离性。由此,能够抑制在使支承基板S从磨削得较薄的光器件晶片W剥离时的光器件晶片W的破损。而且,在本实施方式涉及的磨削方法中,由于支承基板S的涂敷光硬化树脂R的表面的表面粗糙度形成得比光器件晶片W的粘贴面的表面粗糙度大,因此,支承基板S与光硬化树脂R的紧密贴合性比光器件晶片W与光硬化树脂R的紧密贴合性高。由此,能够使支承基板S和光硬化树脂R容易地从光器件晶片W剥离。另外,本发明并不限于上述实施方式的记载,能够进行各种变更来实施。例如,在上述实施方式中,举例示出了在支承基板(支承部件)侧涂敷光硬化树脂的方法,但也可以在光器件晶片(板状物)侧涂敷光硬化树脂。在这种情况下,涂敷于光器件晶片的表面的光硬化树脂被间接地涂敷到支承基板的表面。而且,在上述实施方式中,举例示出了使卡盘工作台直接吸附光器件晶片的磨削面并以加热器进行加热的方法,但也可以在光器件晶片的磨削面粘贴保护带后用卡盘工作台吸附。在这种情况下,优选采用不会因加热而变质的保护带。而且,在上述实施方式中,举例示出了使用剥离装置使支承基板和光硬化树脂从光器件晶片剥离的方法,但也可以通过操作员的手动作业进行剥离。而且,在上述实施方式中,举例示出了采用由蓝宝石基板构成的光器件晶片作为要变薄的被加工物(板状物)的情况,但被加工物并不限于此。例如,也能够采用由硅构成的半导体晶片、砷化镓(GaAs)基板、碳化硅(SiC)基板、化合物半导体基板等各种基板。而且,在上述实施方式中,举例示出了采用铝板作为支承基板的情况,但支承基板并不限于此。只要同时具备薄化工序中的良好的支承性和除去工序中的良好的剥离性,可以使用任何基板。例如,能够将具备较高刚性的不锈钢板或铜板等加工成适当的厚度来使用。而且,支承基板的形状也不限于是圆盘形状,可以是任意的形状。此外,上述实施方式涉及的结构、方法等只要不脱离本发明的目的的范围就能够适当地变更并实施。工业上的可利用性本发明在对光器件晶片等板状物进行磨削以将其加工成预定的厚度时是有用的。