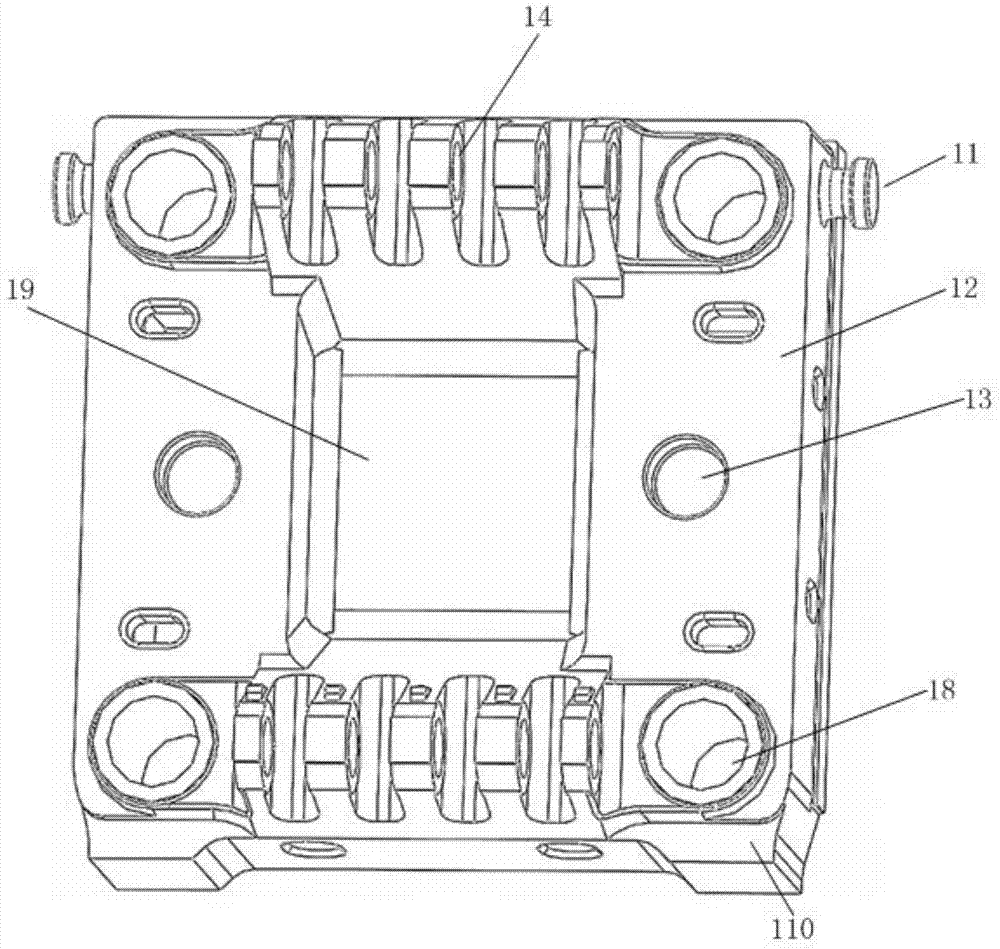
本发明涉及金属铸造
技术领域:
,特别涉及一种厚大断面球铁压铸机模板的铸造方法。
背景技术:
:压铸机在合、开模运动时的速度为变速,在合模运动过程中,中板速度由零很快升到最大值,以后又逐渐减慢,随着曲肘杆逐渐伸直直至终止时,合模速度为零,机构进入自锁状态,在开模过程中,中板移动由慢速转至快速,再由快速转慢至零。压铸机模板包括头板、中板及尾板等,在厚大断面球铁压铸机模板的铸造过程中,头板是压铸机的核心部件之一,在工作中受到交变载荷的作用,在开合模运动过程中不断产生冲击,经过一定的循环次数后容易产生疲劳破坏,机器和结构部件的失效大多数是由于发生疲劳造成的,而压铸机为动载工况下的加工机械,其零部件80%以上为疲劳破坏。中板是压铸机锁模装置的元件之一,锁模装置主要起到实现锁、开模动作和锁紧模具的作用,它也是增力机构的传力部件。尾板是压铸机柱架机构中一个非常关键的零件,它通过锁模机构与动模板联接,三者共同配合完成压铸机的合模、开模,并为锁模机构提供支撑,其结构的优劣直接影响着压铸机生产质量和使用寿命,而且直接影响到相关运动副乃至设备的寿命。因此,如何延长模板的使用寿命,是本领域技术人员亟待解决的技术问题。技术实现要素:本发明的目的是提供一种厚大断面球铁压铸机模板的铸造方法,以延长模板的使用寿命。为实现上述目的,本发明提供一种厚大断面球铁压铸机模板的铸造方法,包括步骤:a1:制作造型操作;a2:进行手工制芯;a3:进行合模操作;a4:对浇铸材料进行熔炼操作;a5:进行浇注操作;a6:对铸件进行冷却操作;a7:对铸件进行开箱操作;所述步骤a1包括设置上层浇道和下层浇道,所述上层浇道和所述下层浇道均包括沿液体流向依次设置的直浇道、横浇道和内浇道,铰耳浇注位置的铰耳凸台设置有浇冒口。优选地,所述横浇道呈双层设置,所述横浇道和直浇道交叉设置。优选地,所述造型为手工造型,所述造型的砂体内设有液体树脂粘结剂和固化剂。优选地,所述步骤a2包括在砂芯内部设置芯骨,所述芯骨的端部设置有圆钢,所述圆钢伸出砂型,所述砂芯为铬矿砂芯。优选地,所述步骤a3包括在顶针孔砂芯的外侧包设有玻璃丝布;砂模水平放置,且所述砂模的底部设有用于与外界隔离的垫块;在所述砂模的外壁和内腔均涂覆锆英粉涂层;通过瓦斯喷枪烘烤砂模及冷铁位置。优选地,所述步骤a4包括:a41:通过电炉对原料加热;a42:电炉将原料加热至1520℃静置预设时间;a43:通过直读光谱仪对炉前铁水进行取样分析,达到预设标准后进入步骤a44;a44:电炉将原料加热至1500℃-1520℃静置预设时间,加入回炉材降温,进行二次除渣;所述炉前铁水标准为按百分含量计:c:3.45%~3.55%、si:2.45%~2.55%、mn:0.25%、p≤0.04%、s:≤0.025%。优选地,所述铸件为中板,所述中板上设有中板油缸孔,且所述中板的相对两侧均设有第一掏料孔,沿所述中板厚度方向,所述中板油缸孔位于所述第一掏料孔的正上方,所述中板的中心设有减重槽。优选地,所述第一掏料孔的开口为沿垂直于所述中板方向延伸的条形孔,所述中板的相对两侧均设有一个所述第一掏料孔。优选地,所述铸件为尾板,在所述尾板的外侧设置铜套。优选地,所述步骤a5包括进行球化处理和浇注处理;所述球化处理包括步骤:将铁液冲向球化包中未放置球化剂的一侧,铁液一次充满球化包,铁水转入浇包1/3时,开始加入投掷孕育剂,转包倒约至2/3时投掷孕育剂全部投完,所述投掷孕育剂的粒度为5mm-30mm,投掷孕育剂按百分含量计包括si>65%,ba:1.3%-3.0%,ca:1/3%-3.0%,al<3%,所述投掷孕育剂加入量为铁液总重量的0.4%~0.6%;所述浇注处理包括步骤:浇注过程中加入随流孕育剂,所述随流孕育剂的加入量为铁液总重量的0.2%,所述随流孕育剂的粒度为0.2mm-0.8mm,所述随流孕育剂按百分含量计包括si>65%,ba:1.3%-3.0%,ca:1/3%-3.0%,al<3%。在上述技术方案中,本发明提供的厚大断面球铁压铸机模板的铸造方法,包括步骤:a1:制作造型操作;a2:进行手工制芯;a3:进行合模操作;a4:对浇铸材料进行熔炼操作;a5:进行浇注操作;a6:对铸件进行冷却操作;a7:对铸件进行开箱操作。其中步骤a1和下层浇道均包括设置上层浇道和下层浇道,上层浇道包括沿液体流向依次设置的直浇道、横浇道和内浇道,铰耳浇注位置的铰耳凸台设置浇冒口。通过上述描述可知,在本申请提供的铸造方法中,通过设置上层浇道和下层浇道,上层浇道起补缩、排渣作用,铰耳凸台设置冒口,冒口可补偿铸件成形过程中产生的收缩,起到防止铸件产生缩孔、缩松并兼有排气、集渣、引导充型的作用,进而避免铁水收缩引起局部应力集中的情况,有效地延长了模板的使用寿命。附图说明为了更清楚地说明本发明实施例或现有技术中的技术方案,下面将对实施例或现有技术描述中所需要使用的附图作简单地介绍,显而易见地,下面描述中的附图仅仅是本发明的实施例,对于本领域普通技术人员来讲,在不付出创造性劳动的前提下,还可以根据提供的附图获得其他的附图。图1为本发明实施例所提供的中板的三维结构图;图2为图1所示中板的后视图;图3为本发明实施例所提供的中板的结构示意图;图4为图3所示中板沿a-a方向的结构示意图;图5为图3所示中板的侧视图;图6为图5所示中板沿b-b方向的结构示意图;图7为图6所示中板沿c-c方向的结构示意图;图8为本发明实施例所提供的尾板的三维结构图;图9为图8所示尾板的后视图;图10为本发明实施例所提供的尾板的结构示意图;图11为图10所示尾板的侧视图;图12为图10所示尾板沿d-d方向的结构示意图;图13为图10所示尾板沿e-e方向的结构示意图;图14为图10所示尾板沿f-f方向的结构示意图;图15为本发明实施例所提供的铸件的三维结构图;图16为本发明实施例所提供的铸件的结构示意图;图17为图16所示铸件沿g-g方向的结构示意图;图18为图17所示铸件的j部放大图;图19为图16所示铸件沿h-h方向的结构示意图;图20为图16所示铸件沿i-i方向的结构示意图;图21为本发明实施例所提供的铸造方法流程图。其中图1-20中:11-吊耳、12-中板机身、13-中板油缸孔、14-中板铰耳、15-第一掏料孔、16-掏料连接孔、17-第二掏料孔、18-中板哥林柱孔、19-减重槽、110-中板底脚;21-尾板铰耳、22-第三掏料孔、23-十字头导杆孔、24-尾板底脚、25-尾板油缸孔、26-尾板机身、27-尾板哥林柱孔、28-减重孔;31-钢板、32-圆钢、33-芯骨、34-纵向板、35-横向板、36-第一芯头、37-t型铁、38-第二芯头、39-吊钩;4、砂体。具体实施方式本发明的核心是提供一种厚大断面球铁压铸机模板的铸造方法,以延长模板的使用寿命。为了使本领域的技术人员更好地理解本发明的技术方案,下面结合附图和实施方式对本发明作进一步的详细说明。请参考图1至图21,在一种具体实施方式中,本发明具体实施例提供的厚大断面球铁压铸机模板的铸造方法,包括步骤:a1:制作造型操作。优选,造型为手工造型,造型的砂体内设有液体树脂粘结剂和固化剂,制作时,将砂模放置于型板上部,通过定位销定位,再将模具放置于砂模中间,室温下通过混砂机向砂模中下砂,使砂体充填至砂模中除模具的各个部位,此时先将砂型舂好,翻箱,舂制上砂型,由于砂体内设有液体树脂粘结剂和固化剂,这种常温自硬不仅可以节能节材,还可改善工人的作业条件,在可使用时间内流动性好,能在较小紧实力作用下,明显减轻工人的劳动强度。具体通过液体树脂粘结剂和固化剂对掏料孔和砂芯双重定位,砂芯稳固使型腔不再扩大,因铁水从型腔表面凝固,使得型腔稳固间接固定了凝固时冒口的补缩量,冒口不再影响铸件的正常收缩,并保证各部位的凝固速度趋于一致,降低了应力集中,避免了裂纹。采用自硬树脂砂造型、制芯方法,向型、芯砂中加入液体树脂粘结剂及固化剂,使之在芯盒或砂模中在一定时间内自行硬化成形,具体的参照国家标准jb/t9224-1999,如表1,表1(树脂用)砂规格手工造型,粘结剂为水玻璃砂,加入量为树脂重量的0.9%~1.2%,如表2,表2(水玻璃用)砂规格固化剂可以为铸造用磺酸——参照标准hg/t2345-92,加入量为树脂重量的30~50%,如表3,表3固化剂规格项目强酸固化剂a弱酸固化剂b密度(g/cm3)1.2~1.51.2~1.5粘度(mpa.s,20℃)10~3010~30总酸度(h2so4)20~355~20游离硫酸(%)≤15≤5步骤a1包括设置上层浇道和下层浇道,上层浇道和下层浇道均包括沿液体流向依次设置的直浇道、横浇道和内浇道,铰耳浇注位置的铰耳凸台设置浇冒口。具体的,横浇道呈双层设置,横浇道和直浇道交叉设置。为了提高铸件的加工质量,优选,模具上对应的哥林柱凸台设置出气管,出气管可以排出型腔、砂芯及金属液析出的各种气体,减小充型时型腔内的气体压力,改善金属液充型能力,便于观察金属充填型腔的状态及充满程度,排出先行充填型腔的低温金属液和浮渣,减重孔处设置成型冷铁,冷铁通过φ50钢管引气通至上箱,目的是加快铁水的冷却速度,模面均布冷铁,冷铁厚度为模面厚度的1/2。a2:进行手工制芯。步骤a2包括在砂芯内部设置芯骨33,芯骨33的端部设置有圆钢32,圆钢32伸出砂型。由于掏料孔只利用第一芯头36一方固定会出现浮动情况,因此砂芯内部放置芯骨33,具体的,芯骨33焊接φ50mm圆钢32伸出砂芯,圆钢32上焊接钢板31(200mm*800mm*30mm),钢板31伸出砂芯外600mm,具体的,钢板31和圆钢32的数量根据实际需要而定,本申请不做具体限定。由于钢板31外侧被砂体4包围,钢板31与芯骨33焊接,且第二芯头38外部补砂,具体砂厚为90mm-100mm,优选的,砂厚为100mm,下方砂较厚,砂子硬化后,翻箱时钢板31不会移动,这样砂芯被有效固定,则不会有浮动危险。铰耳孔下方的掏料孔一面由第一芯头36固定,由于上面为铰耳,不能从上方固定,优选在内侧利用设置t型铁固定砂芯,其中,优选,t型铁为四个,砂芯相对两侧均设有两个对向设置的t型铁,具体的,t型铁包括与砂芯固定的纵向板34及向内部伸入的横向板35,其中横向板35由两个30mm*50mm钢板,叠加成50mm*60mm,长度400mm板体,纵向板34由厚度钢板30mm,长度和宽度分别为300mm、100mm板体结构而成,与相对方向的铰耳孔固定方式同理。由于砂模上顶针孔位置较厚,有烧结危险,此处砂芯采用铬矿砂,铸造用铬矿砂是天然铬铁矿经破碎筛分等工艺加工的产品,其主要化学成分为cr2o3,这种砂受热体积稳定、热导率高,与熔融金属接触时不仅具有良好的抗碱性渣的作用,不与氧化铁等起化学反应,而且本身具有固相烧结的特点,能较好的防止熔融金属的渗透,避免产生粘砂缺陷。具体的在制芯时,先在芯盒内放入芯砂,舂实,将芯骨33放入芯盒,放入出气管,刮去高出芯盒上平面的芯砂,做出出气孔,将烘干板放在芯盒上,松动后取下芯盒,挖出吊钩,修整砂芯涂上涂料。a3:进行合模操作。步骤a3包括在顶针孔砂芯的外侧包设有玻璃丝布;砂模水平放置,且砂模的底部设有用于与外界隔离的垫块;在砂模外壁涂覆锆英粉涂层;通过瓦斯喷枪烘烤砂模及冷铁位置。具体的,在顶针孔砂芯缠两层玻璃丝布,玻璃丝布耐热性高、吸潮性小,可防止铸件烧结,铸型水平摆放,并在砂模四角用垫块垫起,以防顶破铸型;涂刷两遍锆英粉涂料,锆英粉涂料相比其它涂料烧结温度最高,约1600℃~1800℃,并迅速点火烧干;用瓦斯喷枪将铸型及冷铁部位烘烤一遍,确保型腔充分干燥;用盖片将浇冒口盖起来,防止落砂;砂模法兰处锁好螺杆,保证浇入铁水后不涨箱(砂箱膨胀),这样开箱出来的铸件不易变形,尺寸稳定,也就提高了加工的稳定性。a4:对浇铸材料进行加热操作。步骤a4包括:a41:通过电炉对原料加热;a42:电炉将原料加热至1520℃静置预设时间;a43:通过直读光谱仪对炉前铁水进行取样分析,达到预设标准后进入步骤a44;a44:电炉将原料加热至1500℃-1520℃静置预设时间,加入回炉材降温,进行二次除渣。具体的,若检测成分不达标则工作人员根据需求做调整,达标后将温度升至1500~1520℃静置5min~8min,通过让铁水翻滚,使内部渣子浮至表面,加入回炉材降温,再进行二次除渣,考虑到炉后烧损会减少碳的含量,孕育后会增加si的含量,1400~1450℃出炉(具体可以根据浇温调整)。由于传统的球铁材料抗拉强度、硬度与延伸率成反比,基体组成为“珠光体+铁素体”,珠光体提高抗拉强度,铁素体提高延伸率,这对于力学性能要求高的压铸机模板来说,两者无疑是个矛盾之处,为调整抗拉强度与延伸率之间的关系,采用高硅球铁材质,改变了传统球铁基体,将基体组成转变为“铁素体”基体,在满足高延伸率的同时又达到了高强度,以往的高硅球铁加入锑合金,本材质中加入ni,可改善其对壁厚的敏感性,ni可促进铁素体,特别是距石墨远的部分,组织变成细微的珠光体,提高了强度,铁素体的存在可确保适当的延展性,进而达到高强度、高延展性,也就是由于ni的铁素体的促进作用,mn则促进粒界偏析而生成细微的珠光体,从而使基体复合化,是此项合金的特点。原材料加入比例,生铁30%~50%,废钢40%~50%,回炉材0%~20%,增碳剂100kg~200kg,硅铁、锰铁视情况而定,熔炼设备采用中频感应电炉——cw2-pa2000,加料采用电子台秤,先加入废钢,按照国家标准(gb/t4223-2004)购料,成分如表4。表4废钢成分熔炼温度一直上升,待废钢熔化部分后加入生铁,按照国家标准(gb/t718-2005)购料,成分如表5。表5生铁成分待熔化部分后加入回炉材,主料熔化的同时加入增碳剂,成分如表6。表6增碳剂成分加入硅铁,按照国家标准(gb2272-87)购料,成分如表7。表7硅铁成分加入锰铁,按照国家标准(gb3795-87)购料,成分如表8。表8锰铁成分加入碳化硅,按照国家标准(gb/t2480—2008)购料,成分如表9。表9碳化硅成分碳化硅不仅起到增硅、增碳的作用,同时还能延缓孕育衰退的时间,因为碳化硅能持续、缓慢释放硅元素,延长孕育时间,对炉料也能起到脱氧的作用,可减少铁液的过冷度,对降低合金量有很大帮助,而且使用碳化硅的铸件,延长了刀具的使用寿命,切削性能可得到明显改善。具体的,待电炉升至1520℃静置,对炉前铁水取样进行光谱分析,采用直读光谱仪(具体可以为arl3460·oes),铁水表层有很多浮渣,需要清理除掉,成分检测按照表10炉前标准。表10炉前成分标准本申请中,c促进石墨化,减少白口倾向,增加铁素体,提高镁吸收率,有利于石墨球化、细化和圆整,c在此材质中提高铁水了铸造性能,即增加了铁水的流动性,有利于浇注成形及补缩,提高球化效果;c对力学性能的影响主要是通过对金属基体的影响起作用,即减少游离渗碳体,提高延伸率。si强烈促进石墨化,细化石墨有利于石墨球化、细化和圆整,si溶于铁素体,有抑制珠光体、促进铁素体的作用,而且能够使铁素体强化,高硅球铁主要利用硅固溶于铁素体基体的原理,使铁水中的o、n含量降低,间接低增强si对石墨化的作用。球铁中,s和o已经在用镁或铈处理时被去除,或者结合成稳定的化合物,因此,少量的mn可作为合金元素而发挥作用,此时mn的作用就是形成碳化物和珠光体。因为球铁的凝固方式及残余镁量决定了其有很大的白口倾向,因此把mn量保持在最低的水平。mn对珠光体的作用也很明显,无论何种基体,mn都可提高抗拉强度和硬度。p有微弱的石墨化作用,不影响球化,却是有害元素,因此控制在最低。s是保证稳定球化、提高质量的关键,只有当铁液中s降到0.02%以下,又有一定的残余镁量和稀土量,才能保证球化良好,根据原铁液含s量决定球化剂加入量。ni在铁液中和固态球墨铸铁中均能无限溶解,ni不与c形成碳化物,它是作为石墨化元素,可使白口倾向降低,ni对石墨形态没有影响,对共晶团数量也没有影响,在铁素体球墨铸铁中,ni强化铁素体,显著提高强度。通过使用高硅材质,去除了传统球铁中增大凝固区间的合金,如锑、铬及锡等,因去除这些合金后,凝固过程加快,树枝晶量减少,这样就加快了液体金属的流动,液体金属可愈合树枝晶晶界间撕裂的液膜,避免了凝固裂纹,并且合金偏析降低,低熔点成分分散在晶界处,导致晶界不再薄弱,进而降低了热裂倾向。加入ni合金,改善其对壁厚的敏感性,组织变成细微的珠光体,使性能达到高强度、高延展性。a5:进行浇注操作。步骤a5包括进行球化处理和浇注处理;球化处理包括步骤:将铁液冲向球化包中未放置球化剂的一侧,铁液一次充满球化包,铁水转入浇包1/3时,开始加入投掷孕育剂,转包倒约至2/3时投掷孕育剂全部投完,投掷孕育剂的粒度为5mm-30mm,投掷孕育剂按百分含量计包括si>65%,ba:1.3%-3.0%,ca:1/3%-3.0%,al<3%,投掷孕育剂加入量为铁液总重量的0.4%~0.6%;浇注处理包括步骤:浇注过程中加入随流孕育剂,随流孕育剂的加入量为铁液总重量的0.2%,随流孕育剂的粒度为0.2mm-0.8mm,随流孕育剂按百分含量计包括si>65%,ba:1.3%-3.0%,ca:1/3%-3.0%,al<3%。按工艺要求放置浇冒口、浇口杯及压铁等,选取重稀土镁球化剂进行球化处理,将球化剂放在处理包底里侧,球化剂表面均匀覆盖一层矽钢片,矽钢片表面覆盖大面积铁片,防止球化剂反应过快导致球化不良,球化剂加入量为铁液总量的1.1%,球化剂dy-7f参照国家标准(zbj31010-90),成分如表11。表11球化剂规格具体的,球化处理时,将铁液冲向球化包中未放置球化剂一侧,将铁液一次充满球化包,铁水转入浇包1/3时,开始加入(投掷)孕育剂yfy-1a,孕育剂选取75sife,孕育剂加入量为铁液总量的0.4%~0.6%,孕育剂(投掷)参照国家标准(gb/t066-1995),如表12。表12孕育剂(投掷)规格转包倒约至2/3时全部投完,先将铁水表层充分搅拌,使孕育剂充分溶化吸收,除渣至铁水表面无明显杂质上浮为宜,用风枪将包壁残留的除渣剂吹干净,测温:当温度高于所需温度时,用冷铁降温,合格后在铁水表面覆盖除渣剂(珍珠岩),挡渣,最后浇注,浇注过程中加入(随流)孕育剂yfy-1a,孕育剂加入量为铁液总量的0.2%,孕育剂(随流)参照国家标准(gb/t066-1995),如表13。表13孕育剂(随流)规格a6:对铸件进行冷却操作。通过冷却,防止铸件在浇注后因冷却过快而产生变形、裂纹等缺陷,保证铸件在清砂时有足够的强度和韧性。具体的,铸件在型腔内应有足够的冷却时间,放入热砂坑中缓慢冷却,冷却时间根据具体需求而定,本申请不做具体限定。a7:对铸件进行开箱操作,具体的,开箱后去除浇冒口及清除冷铁。铸件为中板,中板上设有中板油缸孔13,且中板的相对两侧均设有第一掏料孔15,沿中板厚度方向,中板油缸孔13位于第一掏料孔15的正上方,中板的中心设有减重槽。进一步,第一掏料孔15的开口为沿垂直于中板方向延伸的条形孔,中板的相对两侧均设有一个第一掏料孔15。由于中板的中部设有减重槽,侧部壁厚较厚,通过将中板油缸孔13设置在两侧第一掏料孔15上部,掏料孔由分孔改为通孔,位置变化使油缸、掏料孔、机身壁厚差适中,去除了壁厚突变引发开裂的倾向。具体的,中板包括中板机身12,中板机身12上设置有吊耳11和中板铰耳14,中板机身12底端设有中板底脚110,第一掏料孔15为通孔形式,中板机身上两个第一掏料孔15中间的侧部设有第二掏料孔17。铸件为尾板,压铸机尾板通过十字头导杆与十字头连接,在开锁模过程中,梯形结构承载大部分力,尾板一般在侧面梯形结构处开裂,本申请将梯形结构去除,由于传统梯形结构是承载十字头导杆的作用力,去除之后,十字头导杆作用力由中板承载,中板在中板油缸孔13处安装十字头导杆,现中板改变中板油缸孔13位置,中板油缸孔13设置于第一掏料孔15上方,拉大了中心距,十字头导杆作用力分布较之前分散且平均,这样就分担了部分尾板的承载力。具体的,尾板包括尾板机身26,尾板机身26上设有尾板铰耳21、第三掏料孔22、十字头导杆孔23、尾板油缸孔25、尾板哥林柱孔27和减重孔28,尾板机身26的底部设有尾板底脚24,尾板油缸孔25位于尾板机身26中部。压铸机中板在模面需每隔100mm钻一个顶针孔,具体的顶针孔在横向和纵向上呈线性排布,经加工后,顶针孔内无任何缺陷。通过上述描述可知,在本申请具体实施例所提供的铸造方法中,通过设置上层浇道和下层浇道,上层浇道起补缩、排渣作用,铰耳凸台设置冒口,冒口可补偿铸件形成过程中产生的收缩,起到防止铸件产生缩孔、缩松并兼有排气、集渣、引导充型的作用,进而避免铁水收缩引起局部应力集中的情况,有效地延长了模板的使用寿命。检测结果分别见表14,表14附铸试块性能检测具体的,通过本申请加工防范,模板的抗拉强度可达530mpa以上,延伸率可达14%以上,硬度可达180hb以上,球化率可达国家标准3级,石墨大小可达国家标准4级,原球铁材质获得的铸件本体硬度差范围在5hb~30hb,高硅材质制备的铸件本体硬度差范围在5hb~10hb,本体硬度更加均匀,与铁素体-珠光体混合基体的球墨铸铁相比,疲劳强度增加,组织更加均匀,机械性能呈现各向同性。本说明书中各个实施例采用递进的方式描述,每个实施例重点说明的都是与其他实施例的不同之处,各个实施例之间相同相似部分互相参见即可。对所公开的实施例的上述说明,使本领域专业技术人员能够实现或使用本发明。对这些实施例的多种修改对本领域的专业技术人员来说将是显而易见的,本文中所定义的一般原理可以在不脱离本发明的精神或范围的情况下,在其它实施例中实现。因此,本发明将不会被限制于本文所示的这些实施例,而是要符合与本文所公开的原理和新颖特点相一致的最宽的范围。当前第1页12