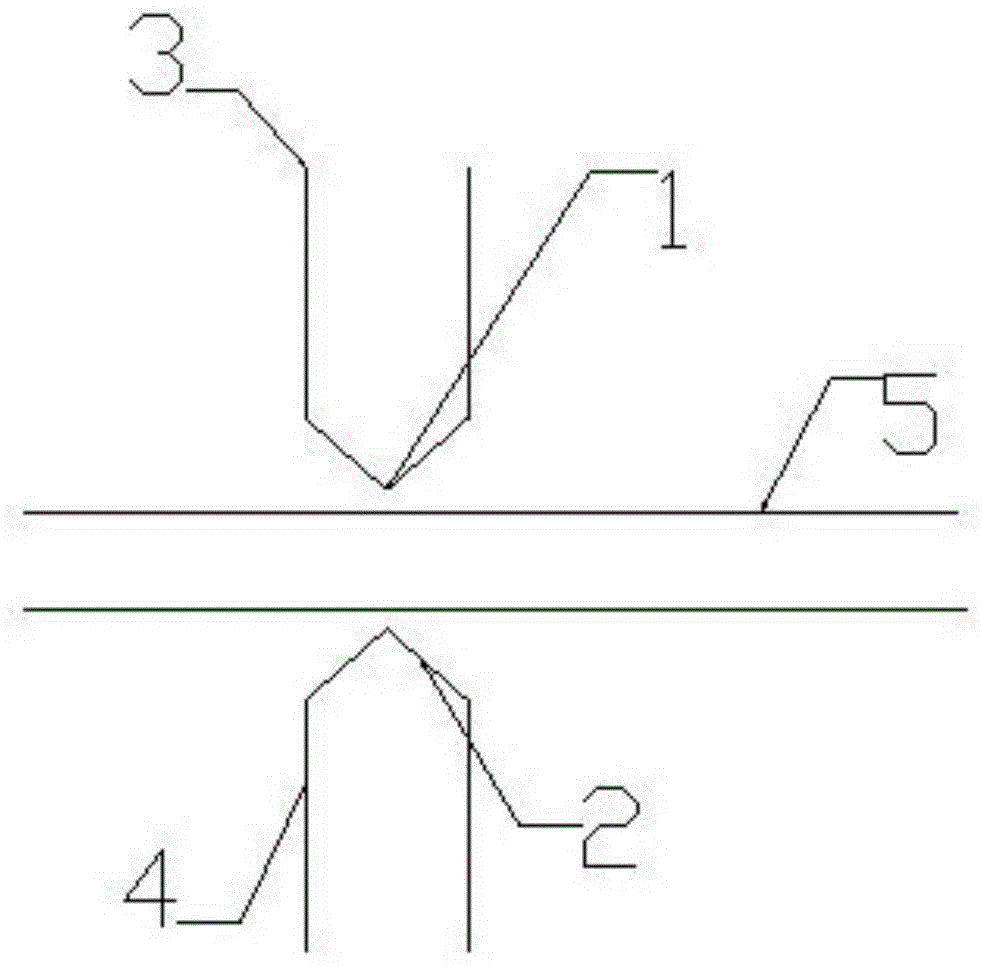
本发明涉及高炉冶炼
技术领域:
,具体地指一种低熟料率的炉料及冶炼方法。
背景技术:
:高炉使用的含铁炉料主要包括烧结矿、球团矿及天然块矿。烧结矿、球团矿是铁矿粉经过高温加工后获得的人造富矿,它们在高炉含铁炉料中所占的比例称之为“熟料比”。相对于经过高温造块工艺加工而成的“熟料”——烧结矿和球团矿而言,直接用常温物理方法从矿山开采出来的块状铁矿石属于“生料”,它在高炉含铁炉料中所占的比例称之为“生矿比”。按照传统的高炉精料理论,应尽可能提高高炉入炉含铁炉料的“熟料比”,即要多用烧结矿和球团矿。因此,长期以来国内高炉“熟料比”一般超过85%,甚至全部使用烧结矿和球团矿的高炉也不少。但是,作为“熟料”之一的球团矿的购入价格远高于天然块矿;另外,烧结矿、球团矿的生产工艺是消耗能源、污染环境的过程。显然,从设备投资、能源消耗及环境保护等角度出发,高炉降低熟料率冶炼是有益的。[文献1~4]是检索到的国内文献。在相关中文文献中,文献1对韶钢高炉降低熟料比的生产实践进行了总结,通过对块矿冶金性能的分析针对低熟料比冶炼对高炉生产的影响,采取料场和筛分系统改造调整送风制度及高炉布料等措施,摸索调整操业制度,克服了降低熟料比导致的炉况波动。但文中未给出具体的炉料配比范围以及具体的操作调整参数范围。文献2以宝钢不锈钢事业部炼铁厂的烧结矿、球团矿、pb矿及纽曼矿为原料,采用中温还原和低温还原粉化测定方法及改进的熔滴性能测定法,研究高块矿比(15%~25%,质量分数)炉料的还原性、低温还原粉化性及熔滴性能。表明块矿配比的质量分数由15%增加到25%,炉料的还原度ri降低5%,低温还原粉化率rdi-3.15升高2%,熔融区间滴落温度td与压差陡升温度ts差升高60℃左右,透气性指数的特征值s升高100kpa·℃。但文中未给出具体的炉料配比范围以及具体的操作调整参数范围。文献3对武钢8号高炉提高块矿比生产实践进行总结通过探索合理的上下部调剂制度,控制合适的炉温及炉渣碱度,加强管理,保持了稳定顺行,将块矿配比提高至16%,取得了较好的经济效。但文中未给出的炉料配比偏低且没有给出对应的操作调整参数范围。文献4对宣钢4号高炉提高块矿配比冶炼实践进行了总结,通过采取下部缩小风口面积,提高鼓风动能,保证炉缸活跃度上部优化“平台+漏斗”料面结构,稳定煤气流分布,加强块矿筛分,减少粉末入炉,适当提高铁水物理温度,保证渣铁良好的渣铁流动性等措施,块矿比由5%提高至15%,高炉稳定顺行。但文中未给出的生料配比偏低且没有给出对应的操作调整参数范围。参考文献1.陈小东,杨国新.“韶钢高炉降低熟料比生产实践.南方金属.12(225).2018参考文献2.吴亮亮,傅元坤.高块矿比高炉炉料的冶金性能研究.安徽工业大学学报.1(31).2014参考文献3.李昌齐,刘树俊等.武钢8号高炉提高块矿比生产实践.武钢技术.3(55).2017参考文献4.褚润林,张利波,等.宣钢4号高炉提高块矿比冶炼实践.河南冶金.4(24).2016技术实现要素:本发明的目的就是要提供一种低熟料率的炉料及冶炼方法,本发明能实现在不影响高炉生产或对高炉生产影响较小的情况下降低熟料比,有效的节约工序成本同时实现绿色制造。为实现此目的,本发明所设计的一种低熟料率的炉料,所述炉料的含量用质量百分比记为73%的烧结矿、4~10%的球团矿、17~23%的块矿,所述球团矿包括程球和鄂球,块矿包括纽曼块、库博块和阿块。熟料在所述炉料中所占的质量百分比为77~85%,生料在所述炉料中所占的质量百分比为15%~23%,所述熟料包括结矿和球团矿,生料为块矿。所述球团矿中程球与鄂球的质量比为7:3。所述生料中赤铁矿与磁铁矿的质量比例范围控制在1.2~1.5,其中,赤铁矿为纽曼块,磁铁矿为库博块和阿块。一种低熟料率炉料的冶炼方法,它包括如下步骤:步骤1:将质量百分比为77~85%熟料置于高炉备料料槽的熟料料槽3中,将质量百分比为15%~23%的生料置于高炉备料料槽的生料料槽4;步骤2:开始原料备料时,同时开启熟料排放闸1以及生料排放闸2,将熟料排放闸1的料流控制在0.4~0.7t/s(吨/秒),生料排放闸2的料流控制在0.1~0.3t/s,以备料的时间差来保证生料与熟料的充分接触;步骤3:通过运输皮带5将原料运输入高炉,如图2所述,在高炉的布料9号角位6将布原料的环数设置为1~2环(由原来的3环减少到1~2环),在高炉的布料1号角位7将布原料的环数设置为3环(由原来的1~2环增加到3环),根据燃料的批重,保证高炉中燃料环的环数在1~2环(燃料的批重一般控制在18吨到25吨之间,当批重控制在18-20吨之间时只布料布一圈(即一环),要是批重在20吨及以上,则布料布两圈),所述圆柱体高炉的中心线定义为0号角位,布料9号角位6为与圆柱体高炉中轴线夹角为43~45度的环形面,布料1号角位7为与圆柱体高炉中轴线夹角为9~11度的环形面;步骤4:通过调整高炉中心煤气流,高炉的布料9号角位6布料环数,保证高炉中炉缸上部风温在1200℃±20℃,高炉中富氧率控制在3~4%,实现高炉的稳定顺行。所述高炉震动筛上的筛网的形式由震动梳齿筛更改为网孔圆振筛,能更有效的保证生料的筛分质量。低熟料率的高炉冶炼,会带来诸如爆裂、结晶水分解吸热、软熔性能差等问题。这势必会影响高炉生产,给高炉操作造成困难。因此,本发明设计的低熟料率的炉料结构及冶炼方法,通过上述方案能实现在不影响高炉生产或对高炉生产影响较小的情况下降低熟料比,能有效的节约工序成本同时实现绿色制造。附图说明图1为本发明中原料备料示意图;图2为本发明中原料布料示意图;1—熟料排放闸;2—生料排放闸;3—熟料料槽、4—生料料槽、5—运输皮带、6—布料9号角位、7—布料1号角位、8—炉体截面。具体实施方式以下结合附图和具体实施例对本发明作进一步的详细说明:针对降低高炉熟料比的生产需求,结合生产实际,本发明提出了如下高炉炉料结构设计的基本思想:1、降低高炉熟料比的实质是以块矿替换部分球团矿。因此,需要使用的块矿种类的选择以及应当减去的球团矿种类的确定,是非常重要的技术关键。2、上述问题归属于高炉优化配矿技术,应遵循的技术原理是:既要以单一炉料的冶金性能为基础,又要重视它们与烧结矿的高温反应能力,因为后者往往是改善单一炉料软熔性能的重要因素,使其综合炉料的软熔性能变好,最终能在综合炉料结构的软熔滴落性能上得到反映。3、从块矿资源以及经济性角度考虑,并根据含铁炉料的自身特性,需要运用互补原理进行块矿搭配模式的设计。4、根据高炉的实际生产情况,入炉含铁原料的综合二元碱度取为1.5。根据以上高炉含铁炉料结构的设计思想,结合实际需求,给出了如下11组含铁炉料结构的设计方案。以下方案均表示配比含量,单位%方案1234567891011烧结矿7373737373737373737373程球66622260200鄂球44455544504纽曼块170.00.012.011.90.09.513.82016.80.0库博块0.0170.01.08.18.07.59.20.010.28.8阿块0.00.0177.00.012.00.00.00.00.014.2合计100100100100100100100100100100100熟料8383838080808377807377块矿1717172020201723202723各种含铁炉料结构方案对应的软熔滴落性能如下:分析降低熟料比对综合炉料软熔滴落性能影响规律的基础上,在炉料结构优化方面寻找技术对策,得到以下结论:1、在块矿的种类、搭配模式选择不当时,随着熟料比的降低,块矿用量的增加,综合炉料的软熔滴落性能有变差的趋势。2、在降低熟料比时,应尽量避免单独使用自身软熔性能不佳的纽曼块,且搭配比例不宜过大。3、在降低熟料比时,用反应性高的块矿替代反应性低的,会使块矿与烧结矿的高温交互反应作用得以加强,有助于改善综合炉料的软熔滴落性能。4、块矿的搭配模式是决定综合炉料软熔滴落性能的重要因素,虽然采用“纽曼+库博”的搭配模式也可以改善低熟料比炉料的软熔滴落性能,但其效果远不如采用“库博+阿块”搭配模式的情况。优化的炉料结构是采用“纽曼+库博”的块矿搭配模式,它可以使块矿比例从17%增至23%过程中综合炉料的软熔滴落性能“非降反升”。因此,优选纽曼块+库博块的搭配模式,总配比可达23%,且1.2≤纽曼块:库博块≤1.5。为了使各个炉料结构设计方案的工艺参数和经济技术指标的解析结果符合生产实际情况,选取和基准期相同的焦炭和煤粉成分、生铁成分、各元素在生铁和炉渣中的分配率、炉顶煤气成分、焦比、煤比、出铁量、利用系数、理论风量、鼓风湿度、富氧流量、鼓风温度、炉顶温度、出渣温度、铁水温度、铁的直接还原度和氢的利用率等。根据这些已知的工艺参数和指标以及前面确定的各系数,就能够计算得出各炉料结构设计方案的工艺参数和指标。采用增大鼓风动能、适当打通中心气流、确保炉缸活跃性以及布料兼顾中心和边缘等的操作制度,将有助于高炉在低熟料比下的稳定顺行以及获取优良的技术经济指标。冶炼技术要求如下:(1)为了改善低熟料比高炉软熔带的透气性、透液性,适当发展中心煤气流,在高度方向上拉长软熔带,有利于增加焦窗面积,提高其透气性、透液性。另外,随着布料容易滚向炉子中心的球团矿使用量的减少,也需要适当发展中心煤气流。保证中心1-2环焦炭的布置。边缘矿石适当放松。(2)因块矿用量的增加,综合炉料的熔化滴落有可能在相对较低的温度下发生。为了防止炉料有可能提前软熔滴落而对炉缸热状态造成负面影响,确保较高的炉缸温度和充沛的炉缸热量是有必要的。因此,可以通过保持足够高的风温、一定的富氧率以及较高的鼓风动能等活跃炉缸的技术措施予以实施。保证风温1200℃±20℃,富氧率控制在3%-4%。(3)选择适宜的备料模式。为了改变块矿软熔性能相对差的特性,希望它与烧结矿在炉内有良好的交互反应,以此改善综合炉料的软熔滴落性能,故在布料模式上可以考虑块矿与烧结矿的均匀接触问题;在矿槽布料时,保证熟料的a槽的下料率为0.4-0.7t/s,b槽的生料下料率为0.1-0.3t/s,以时间差来保证生料与熟料的充分接触。(4)强化块矿入炉前的筛分工作。这是因为天然块矿的含粉量较高,再加上其本身的湿度较大,黏附在其表面的小颗粒的矿粉很难通过筛分去除,从而造成天然块矿带入高炉的粉末量较多,影响炉内块状带的透气性。因此可以将目前使用的间距为6mm的震动棒条筛更改为孔径为8mm的圆周震动打孔筛,保证筛分效率的提高。为什么了验证本发明的效果,申请人对高炉改变高炉的炉料结构,将鄂球的配比降低近4%,经过一个星期的摸索调节,最终将球团矿全部停掉,块矿配比用到17%,烧结配比用到80%。炉料结构调节如下表所示:全月低熟料率操作的纽曼块与库博块的使用比例处于1.45~1.5之间的水平,其中焦炭的布料制度在降低熟料率后由变为中心环带的焦炭由1.5环增加到2环,矿石的布料制度由变为边缘矿石减少了,同时开放了中心和边缘的两股气流。全月平均富氧率3.57%,降低熟料率后富氧率由月初的2.43%提高到4%,炉况平稳过渡后富氧率稳定在3.5%,风温全月稳定在1200℃±10℃的水平。在使用低熟料率冶炼的1-28号之间,焦比平均为301kg/t,较5月份焦比降低约2kg/t,其中有7天时间焦比基本维持在300kg/t以下,有效实现了在一定炉料结构条件下的低碳冶炼。本说明书未作详细描述的内容属于本领域专业技术人员公知的现有技术。当前第1页12