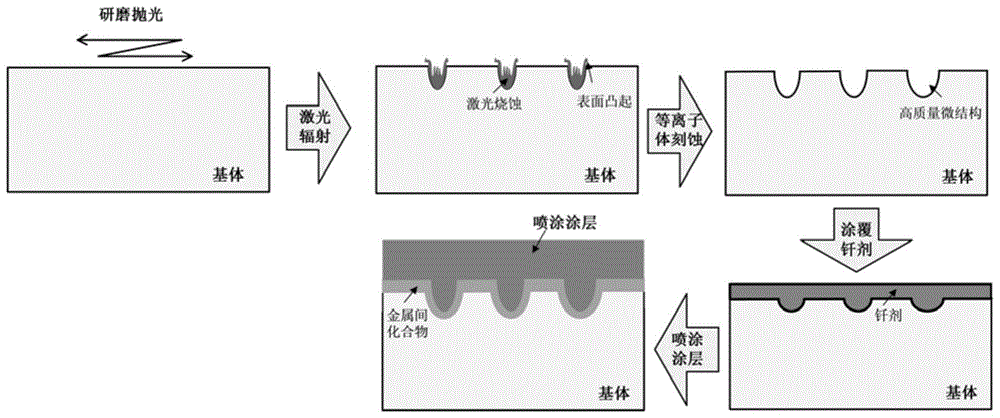
本发明属于热喷涂涂层加工领域,尤其涉及一种促进热喷涂涂层膜基界面间机械和冶金结合的处理方法。
背景技术:
:众所周知,热喷涂涂层具有优良的防腐蚀、耐冲蚀以及抗磨损等特性,若将其涂覆在齿轮、气缸以及活塞环等大型机械设备的核心零件上,能够大幅度提升零件的使用寿命和可靠性,目前已广泛地应用于航空航天、汽车制造、冶金化工等多个领域。但在复杂工况下,热喷涂涂层的首要问题是膜基结合强度不足,导致其在服役过程中涂层提前剥落失效,因此,涂层与基体的结合始终是热喷涂技术在工业领域应用时关注的焦点。然而,热喷涂涂层的膜基结合主要体现在两个方面:1)、机械结合;2)、冶金结合。目前,热喷涂涂层前需对其基体表面进行喷砂喷丸粗化预处理,通过改变基体表面粗糙度来保证涂层良好的膜基结合强度。然而,喷砂喷丸处理存在环保措施不足、制备重复性差、砂粒容易嵌入基体等缺点,且只能改善喷涂涂层膜基间机械结合,对于喷涂涂层膜基间较弱的冶金结合问题无法解决,涂层结合强度并没有得到显著的提高。而在喷涂涂层基体表面进行激光织构化处理,可改变喷涂液滴在基体表面润湿性,增加界面处膜基接触面积率,从而增加喷涂过程中原子的扩散,有利于增强喷涂涂层与基体间微观互锁结合强度。但是,该方法无法改善基体表面在喷涂过程中熔化程度和界面传热系数,对界面冶金结合的程度没有明显影响。技术实现要素:本发明所要解决的技术问题是克服现有技术的不足,提供一种全新的促进热喷涂涂层膜基界面间机械和冶金结合的处理方法。为解决上述技术问题,本发明采取的技术方案如下:一种促进热喷涂涂层膜基界面间机械和冶金结合的处理方法,其步骤如下:1)、基体的表面预处理,其先是对基体表面进行研磨和抛光,然后进行超声波清洗;2)、制备织构化基体,其包括a)、通过物镜将飞秒激光聚焦到步骤1)清洗的基体表面,设定激光扫描工艺路径和激光加工参数,对基体表面进行局部改性,形成改性区与未改性区刻蚀速率的差别;b),自激光烧蚀后的基体表面放置在感应耦合等离子刻蚀系统的刻蚀腔进行干法刻蚀,使得基体表面形成孔或槽状微结构的织构化基体;3)、织构化基体表面处理,其采用钎剂喷在织构化基体表面,干燥后放入真空干燥箱保存;4)、制备涂层,将步骤3)中的基体放入夹具中,并对基体进行预热处理,然后采用等离子喷涂工艺在钎剂的上表面进行喷涂,形成热喷涂涂层,其中喷涂熔滴撞击到基体表面预置钎剂上时,预置钎剂依靠熔滴的长时间加热达到熔化温度,增加喷涂熔滴与基体间的界面传热系数,促使基体接触层发生熔化,熔化的基体会进入熔融的喷涂熔滴中与熔滴发生冶金反应,并在基体和热喷涂涂层之间形成金属间化合物层。优选地,在a)中,采用数值孔径为0.8的物镜,将800nm波长的线性偏振飞秒激光聚焦到在基体表面,通过调节激光脉冲能量、激光频率、激光扫描速度和蚀刻时间,使得改性区呈列阵式分布在基体表面。具体的,物镜的放大倍数为80倍;激光脉冲能量为0.5-2μj;激光频率为500-1000hz;激光扫描速度为100-1000μm/s、刻蚀时间为60-120min。根据本发明的一个具体实施和优选方面,在b)中,感应耦合等离子刻蚀系统在sf6或cl2所形成的等离子体环境下刻蚀,去除激光微织构边缘凸起结构,完成孔或槽状微结构的成型。通过干法刻蚀与激光微加工技术相配合制备基体表面微结构,可解决传统激光加工所制备微结构的尺寸可控性差、规整度难以达到理想状态的问题,制备过程简单,可重复性较高,便于实现大规模生产。优选地,感应耦合等离子刻蚀系统的上射频源功率及下射频源功率可调范围分别为0-500w和0-300w,气流通量为40±5sccm。根据本发明的又一个具体实施和优选方面,在步骤2)中,孔或槽的直径或者宽度为20-100μm;孔或槽的深度为30-100μm。优选地,在步骤2)中,位于基体表面的每一个孔或槽的上边缘所形成的开口面积之和占所述基体表面积的30%~50%。此外,在步骤1)中,将基体表面放置在自动金相磨样机上,先经过800#砂纸水磨,随后用无水乙醇清洗后,再采用1000#砂纸进行磨制,接着采用天然纤维抛光布并在w2.5的金刚石抛光剂配合下,进行镜面抛光,最后分别在水和有机溶剂中进行超声波清洗20-30min。优选地,基体的材质为铝合金或不锈钢,热喷涂涂层的为镍基涂层,如nicr涂层或者ni60涂层。优选地,钎剂选用氟铝酸钾盐的nocolok钎剂,使用时,先将nocolok钎剂溶于酒精形成喷剂,然后喷涂在织构化基体表面,其中每升酒精中溶入120~180g氟铝酸钾盐的nocolok钎剂,且喷涂的用量为每平方米10~50g。简言之,本发明采用干法刻蚀辅助激光微细加工技术在喷涂涂层基体表面制备出尺寸可控且高质量的规则微结构,改变基体表面形貌,有效存储后续预涂在基体表面的钎剂,增加钎剂在基体表面的附着力;然后,将钎剂均匀地喷在织构化基体表面上,这样形成热喷涂涂层时,当喷涂熔滴撞击到基体表面上时,基体表面预置钎剂依靠熔滴的长时间加热达到熔化温度,增加熔滴与基体间的界面传热系数,促使基体发生熔化,熔化的基体会迅速进入熔融的高温熔滴中与熔滴发生冶金发应形成金属间化合物,增加熔滴与基体间冶金结合的程度,另外,当预制钎剂完全熔化后,基体表面预制的规则微结构可增加热喷涂颗粒与基体间的结合区域,利于应力松弛,制备的涂层不易脱落,增强涂层膜基界面间的机械结合。对涂层喷涂过程中膜基界面间的机械结合和冶金结合实现同时改善,可显著增强喷涂涂层结合强度,极具有工业化制备和应用前景。由于以上技术方案的实施,本发明与现有技术相比具有如下优点:本发明通过基体表面织构化技术与钎剂预处理相结合应用于喷涂涂层中,既可以改善喷涂涂层膜基间机械嵌接作用,还可提高熔滴与基体间的界面传热系数,增强喷涂涂层与基体间微观互锁结合强度,并同时增加喷涂过程中膜基界面发生冶金结合的机会,提高熔滴与基体间冶金结合的程度,在基体和热喷涂涂层之间形成金属间化合物层,进而显著增强喷涂涂层的膜基结合强度。附图说明图1为本发明促进热喷涂涂层膜基界面间机械和冶金结合处理方法的流程示意图。具体实施方式为使本申请的上述目的、特征和优点能够更加明显易懂,下面结合附图对本申请的具体实施方式做详细的说明。在下面的描述中阐述了很多具体细节以便于充分理解本申请。但是本申请能够以很多不同于在此描述的其它方式来实施,本领域技术人员可以在不违背本申请内涵的情况下做类似改进,因此本申请不受下面公开的具体实施例的限制。在本申请的描述中,需要理解的是,术语“中心”、“纵向”、“横向”、“长度”、“宽度”、“厚度”、“上”、“下”、“前”、“后”、“左”、“右”、“竖直”、“水平”、“顶”、“底”、“内”、“外”、“顺时针”、“逆时针”、“轴向”、“径向”、“周向”等指示的方位或位置关系为基于附图所示的方位或位置关系,仅是为了便于描述本申请和简化描述,而不是指示或暗示所指的装置或元件必须具有特定的方位、以特定的方位构造和操作,因此不能理解为对本申请的限制。此外,术语“第一”、“第二”仅用于描述目的,而不能理解为指示或暗示相对重要性或者隐含指明所指示的技术特征的数量。由此,限定有“第一”、“第二”的特征可以明示或者隐含地包括至少一个该特征。在本申请的描述中,“多个”的含义是至少两个,例如两个,三个等,除非另有明确具体的限定。在本申请中,除非另有明确的规定和限定,术语“安装”、“相连”、“连接”、“固定”等术语应做广义理解,例如,可以是固定连接,也可以是可拆卸连接,或成一体;可以是机械连接,也可以是电连接;可以是直接相连,也可以通过中间媒介间接相连,可以是两个元件内部的连通或两个元件的相互作用关系,除非另有明确的限定。对于本领域的普通技术人员而言,可以根据具体情况理解上述术语在本申请中的具体含义。在本申请中,除非另有明确的规定和限定,第一特征在第二特征“上”或“下”可以是第一和第二特征直接接触,或第一和第二特征通过中间媒介间接接触。而且,第一特征在第二特征“之上”、“上方”和“上面”可是第一特征在第二特征正上方或斜上方,或仅仅表示第一特征水平高度高于第二特征。第一特征在第二特征“之下”、“下方”和“下面”可以是第一特征在第二特征正下方或斜下方,或仅仅表示第一特征水平高度小于第二特征。需要说明的是,当元件被称为“固定于”或“设置于”另一个元件,它可以直接在另一个元件上或者也可以存在居中的元件。当一个元件被认为是“连接”另一个元件,它可以是直接连接到另一个元件或者可能同时存在居中元件。本文所使用的术语“垂直的”、“水平的”、“上”、“下”、“左”、“右”以及类似的表述只是为了说明的目的,并不表示是唯一的实施方式。实施例1如图1所示,促进热喷涂涂层膜基界面间机械和冶金结合的处理方法,其基体材料选用al-si-mg系铝合金zl101,热喷涂涂层材料为nicr涂层,所谓的膜基界面是指铝合金zl101表面、nicr涂层与铝合金zl101的结合面。具体的,该膜基界面间机械和冶金结合的处理方法步骤如下:1)、基体的表面预处理:其将基体表面放置在自动金相磨样机上,先经过800#砂纸水磨,随后用无水乙醇清洗后,再采用1000#砂纸进行磨制,接着采用天然纤维抛光布并在w2.5的金刚石抛光剂配合下,进行镜面抛光,最后分别在水和有机溶剂中进行超声波清洗20min;2)、制备织构化基体:其包括a)、将清洗后的涂层基体放置在高精度三维移动平台上,利用数值孔径为0.8的物镜(放大倍数为80倍)将800nm波长的线性偏振飞秒激光聚焦到基体表面,飞秒激光束保持固定,调节激光脉冲能量为3μj,频率为500hz,扫描1遍,通过电脑控制三维移动平台的移动在基体表面加工出密度为30%的凹坑状微结构;然后将具有凹坑状微结构基体试样放置在感应耦合等离子刻蚀系统(icp)的刻蚀腔中,在sf6气体的等离子体环境下干法刻蚀实现结构的制备。调节刻蚀系统的上射频源功率和下射频源功率分别为200w和300w,气流通量为40sccm(体积流量),刻蚀时间为60min,制备出的凹坑状微结构的直径为30μm,深度为50μm;3)、织构化基体表面处理:其采用钎剂喷在织构化基体表面,干燥后放入真空干燥箱保存,其中采用氟铝酸钾盐的nocolok钎剂与酒精溶解,其中每升酒精中溶入150g氟铝酸钾盐的nocolok钎剂,摇匀形成喷剂,然后将喷剂均匀地喷在织构化基体表面上,且每平方米喷剂的喷涂量为10g;4)、制备涂层:将步骤3)中的基体放置在夹具中,利用电阻加热装置进行基体的预热,使基体温度达到300℃,采用等离子喷涂工艺(为本领域常规技术手段,在此不对其进行详细阐述),在织构化/钎剂预处理基体表面沉积厚度为400μm的nicr涂层,其中在喷涂熔滴撞击到基体表面上时,基体表面预置钎剂依靠熔滴的长时间加热达到熔化温度,增加熔滴与基体间的界面传热系数,促使基体发生熔化,熔化的基体会迅速进入熔融的高温熔滴中与熔滴发生冶金发应形成金属间化合物,增加熔滴与基体间冶金结合的程度,另外,当预制钎剂完全熔化后,基体表面预制的规则微结构可增加热喷涂颗粒与基体间的结合区域,并在基体和热喷涂涂层之间形成金属间化合物层,增强涂层膜基界面间的机械结合。对涂层喷涂过程中膜基界面间的机械结合和冶金结合实现同时改善,可显著增强喷涂涂层结合强度。具体的,喷涂涂层工艺参数为:电流550a,电压62v,氩气气流为120l/min,氢气气流为5l/min,送粉率30g/min,喷涂距离为90mm,制备涂层时,枪摆速度为500mm/s。然后,对最终的nicr喷涂涂层试样进行划痕实验,测试涂层结合力结果如表1所示。表1nicr喷涂涂层涂层结合力(单位:n)沉积厚度400μm55对比例1本对比例,所采用的基体材料选用al-si-mg系铝合金zl101,热喷涂涂层材料为nicr涂层。具体的,该处理方法如下:1)、基体的表面预处理:其主要采用喷砂或喷丸对基体表明进行研磨和抛光处理,然后分别在水和有机溶剂中进行超声波清洗20min;2)、制备织构化基体:其将清洗后的涂层基体放置在高精度三维移动平台上,利用数值孔径为0.8的物镜(放大倍数为80倍)将800nm波长的线性偏振飞秒激光聚焦到基体表面,飞秒激光束保持固定,调节激光脉冲能量为3μj,频率为500hz,扫描1遍,通过电脑控制三维移动平台的移动在基体表面加工出密度为30%的凹坑状微结构,制备出的凹坑状微结构的直径为30μm,深度为50μm;3)、制备涂层:采用等离子喷涂工艺,在织构化基体表面沉积厚度为400μm的nicr涂层,其中喷涂涂层工艺参数为:电流550a,电压62v,氩气气流为120l/min,氢气气流为5l/min,送粉率30g/min,喷涂距离为90mm,制备涂层时,枪摆速度为500mm/s。然后,对最终的nicr喷涂涂层试样进行划痕实验,测试涂层结合力结果如表2所示。表2nicr喷涂涂层涂层结合力(单位:n)沉积厚度400μm30由实施例1和对比例1的测试结果相比,利用本实施例1所提供的方法获得的涂层结合力为对比例1所提供的方法获得的涂层结合力1.8倍。实施例2如图1所示,促进热喷涂涂层膜基界面间机械和冶金结合的处理方法,其基体材料选用316奥氏体不锈钢,涂层材料为ni60涂层。具体处理方法的步骤如下:1)、基体的表面预处理:其将基体表面放置在自动金相磨样机上,先经过800#砂纸水磨,随后用无水乙醇清洗后,再采用1000#砂纸进行磨制,接着采用天然纤维抛光布并在w2.5的金刚石抛光剂配合下,进行镜面抛光,最后分别在水和有机溶剂中进行超声波清洗30min;2)、制备织构化基体:将清洗后的涂层基体放置在高精度三维移动平台上,利用数值孔径为0.8的物镜(放大倍数为80倍)将800nm波长的线性偏振飞秒激光聚焦到基体表面,飞秒激光束保持固定,调节激光脉冲能量为3.5μj,频率为500hz,扫描速度800μm/s,扫描2遍,通过电脑控制三维移动平台的移动在基体表面加工出密度为50%的沟槽状微结构;然后将具有沟槽状微结构基体试样放置在感应耦合等离子刻蚀系统(icp)的刻蚀腔中,在cl2气体的等离子体环境下干法刻蚀实现结构的制备,其中调节刻蚀系统的上射频源功率和下射频源功率分别为250w和350w,气流通量为40sccm,刻蚀时间为90min,制备出的沟槽状微结构宽度为50μm,深度为60μm;3)织构化基体表面钎剂处理:其采用钎剂喷在织构化基体表面,干燥后放入真空干燥箱保存,其中采用氟铝酸钾盐的nocolok钎剂与酒精溶解,其中每升酒精中溶入160g氟铝酸钾盐的nocolok钎剂,摇匀形成喷剂,然后将喷剂均匀地喷在织构化基体表面上,且每平方米喷剂的喷涂量为14g;4)、制备涂层:将步骤3)中的基体放置在夹具中,利用电阻加热装置进行基体的预热,使基体温度达到400℃,采用等离子喷涂工艺,在织构化/钎剂预处理基体表面沉积厚度为400μm的ni60涂层,其中在喷涂熔滴撞击到基体表面上时,基体表面预置钎剂依靠熔滴的长时间加热达到熔化温度,增加熔滴与基体间的界面传热系数,促使基体发生熔化,熔化的基体会迅速进入熔融的高温熔滴中与熔滴发生冶金发应形成金属间化合物,增加熔滴与基体间冶金结合的程度,另外,当预制钎剂完全熔化后,基体表面预制的规则微结构可增加热喷涂颗粒与基体间的结合区域,并在基体和热喷涂涂层之间形成金属间化合物层,增强涂层膜基界面间的机械结合。对涂层喷涂过程中膜基界面间的机械结合和冶金结合实现同时改善,可显著增强喷涂涂层结合强度。具体的,喷涂涂层工艺参数为:电流500a,电压55v,氩气气流为100l/min,氢气气流为3l/min,送粉率20g/min,喷涂距离为90mm。制备涂层时,枪摆速度为500mm/s。然后,对最终的ni60喷涂涂层试样进行划痕实验,测试涂层结合力结果如表3所示。表3ni60喷涂涂层涂层结合力(单位:n)沉积厚度400μm50对比例2本对比例,所采用的基体材料选用316奥氏体不锈钢,涂层材料为ni60涂层。具体的,该处理方法如下:1)、基体的表面预处理:其主要采用喷砂或喷丸对基体表明进行研磨和抛光处理,然后分别在水和有机溶剂中进行超声波清洗30min;2)、制备织构化基体:将清洗后的涂层基体试样放置在感应耦合等离子刻蚀系统(icp)的刻蚀腔中,在cl2气体的等离子体环境下干法刻蚀实现结构的制备,其中调节刻蚀系统的上射频源功率和下射频源功率分别为250w和350w,气流通量为40sccm,刻蚀时间为90min,制备出的沟槽状微结构宽度为50μm,深度为60μm;3)、制备涂层:采用等离子喷涂工艺,在织构化基体表面沉积厚度为400μm的ni60涂层,其中喷涂涂层工艺参数为:电流500a,电压55v,氩气气流为100l/min,氢气气流为3l/min,送粉率20g/min,喷涂距离为90mm。制备涂层时,枪摆速度为500mm/s。然后,对最终的ni60喷涂涂层试样进行划痕实验,测试涂层结合力结果如表4所示。表4ni60喷涂涂层涂层结合力(单位:n)沉积厚度400μm25由实施例2和对比例2的测试结果相比,利用本实施例2所提供的方法获得的涂层结合力为对比例2所提供的方法获得的涂层结合力2倍。以上对本发明做了详尽的描述,其目的在于让熟悉此领域技术的人士能够了解本发明的内容并加以实施,并不能以此限制本发明的保护范围,凡根据本发明的精神实质所作的等效变化或修饰,都应涵盖在本发明的保护范围内。当前第1页12