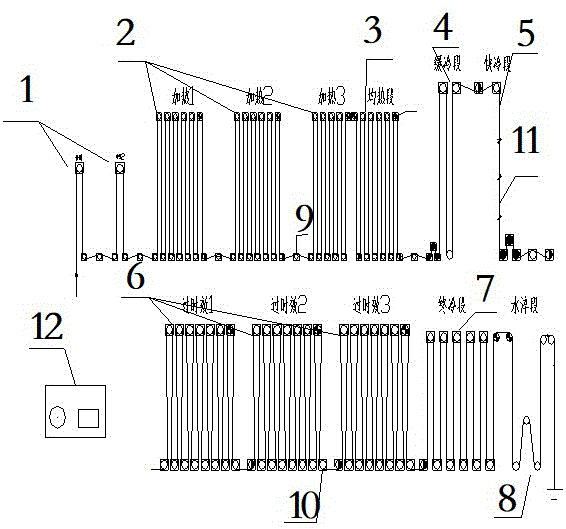
本发明涉及一种消除连续退火炉炉辊压痕缺陷的方法,属于连续退火炉
技术领域:
。
背景技术:
:连续退火生产线是以生产冷轧薄板为主的生产机组,其中连续退火炉是对冷轧薄板进行再退火工艺处理的关键设备。连续退火炉采用全封闭式炉膛结构,炉内充入h2和n2混合气体构成还原性氛围,用于隔绝空气,确保板带在连退炉内不会出现板带氧化情况。连续退火炉通常分为预热段、加热段、均热段、缓冷段、快冷段、过时效段、终冷段和水淬段。不同工艺段的炉内的炉辊辊径不同,预热段到均热段炉辊辊径为小辊径,缓冷到水淬段炉辊辊径为大辊径。连续退火炉炉内带钢在张力作用下通过炉辊带动运行,从而完成整个退火工艺。在生产过程中,当出现炉内带钢严重跑偏碰撞炉墙或者带钢褶皱的时候,或者由于炉内带钢表面有夹杂、氧化铁皮等附着物的时候,特别容易出现异物脱落粘附或者压入到炉辊表面。在退火过程中,炉内带钢在高温环境下会变的较软,炉辊表面的异物在张力作用下会在带钢表面硌出凹坑,表现为炉辊压痕缺陷。炉辊压痕缺陷的特点是形貌位置与炉辊表面异物相对应,且在带钢上的间距具有周期性。炉辊压痕缺陷会导致批量质量问题,造成产品降级,影响生产节奏和产品销售。已有技术出现炉辊压痕缺陷传后的处理方法是停车降温,打开炉盖;接着安排人员进入炉内逐根炉辊排查,确定产生压痕的炉辊后,进行打磨处理;然后重新封闭炉盖,进行炉膛氮气置换,按照规程要求逐步恢复生产。存在问题时:整个处理过程耗费大量人力物力和时间,给平稳生产带来极大不便。技术实现要素:本发明的目的是提供一种消除连续退火炉炉辊压痕缺陷的方法,基于连续退火炉炉辊压痕缺陷产生机理,并通过静止状态的低温带钢与运动状态的炉辊之间的滑动摩擦来消除炉辊表面异物,进而消除连续退火炉炉辊压痕缺陷;该方法不需要开炉处理,不需要人员进入炉膛作业,具有简单高效,可操作性强,省时省力的特点,解决已有技术存在的上述问题。本发明的技术方案是:一种消除连续退火炉炉辊压痕缺陷的方法,包含如下步骤:制定连续退火炉转向辊压痕区域速查表和连续退火炉转向辊位置速查表,通过测量带钢表面压痕缺陷距离,比对退火炉转向辊压痕区域速查表,确定连续退火炉炉辊压痕缺陷产生区域;再利用低温小张力使得炉辊压痕形状变小或消失,并以此计算产生压痕炉辊距离出炉基准点距离,比对连续退火炉转向辊位置速查表确定压痕炉辊位置;然后通过静止状态的低温带钢与运动状态的炉辊之间的滑动摩擦来消除炉辊表面异物,进而消除连续退火炉炉辊压痕缺陷。本发明的具体步骤如下:a)制定连续退火炉转向辊压痕区域速查表;b)以连续退炉出口地面为基准点,制定连续退火炉转向辊位置速查表;c)测量带钢表面压痕缺陷周期zm,判定连续退火炉炉辊压痕及其产生区域;d退火炉停车降温,炉膛温度降至500℃;e退火炉重新建立较小张力,以sp速度运行,在退火炉出口基准点位置观察压痕情况,记录运行时间t1,同时f在画面上对标靶炉辊hs-b和ova-b的旋转圈数进行清零及计数重启;g如果发现压痕缺陷变小或消失,产线停车并记录下运行时间t2,计算出压痕缺陷产生位置离标准点的距离l=sp×(t2-t1);h通过标靶炉辊运行里程对压痕缺陷产生位置距标准点的距离有效性进行核实;通过炉辊压痕距离标准点的距离,回查连续退火炉转向辊位置速查表,确定产生压痕缺陷的炉辊g-x,并通过缺陷在带钢表面位置进行再次确认;i通过调整炉内张力,并强制给予炉辊g-x处于t1速度运行,先后进行顺时针和逆时针转动,点动保持一定时间,并反复多次进行;j炉辊打磨结束后,恢复退火炉张力,连续退火炉启动爬行模式运行,在炉区出口基准点位置观察带钢表面质量情况并计时t3,待t3≥t时;k质检人员到达炉区出口基准点位置观察带钢表面质量,查看带钢表面炉辊压痕缺陷是否消失;若炉辊压痕不消失则重复步骤i至j;若炉辊压痕消失则执行步骤e;l退火炉升温至生产温度,产线运行;m在炉区出口基准点位置观察带钢表面质量,若炉辊压痕缺陷不消失,则重复所述步骤d至所述步骤m,若炉辊压痕缺陷消失,则完成退火炉炉辊压痕缺陷消除工作。实施本发明,首先找到形貌相同的3个连续压痕缺陷点,测量两个压痕之间的距离c1和c2,即第一组数据;接着间隔100多米后,再次找到形貌相同的3个连续压痕缺陷点,测量两个压痕之间的距离c3和c4,即第二组数据,然后根据两组数据进行退火炉炉辊压痕判定,当两组数据不具有固定周期性,则判定为非退火炉炉辊压痕,当两组数据具有周期性,且两组数据值与连续退火炉转向辊压痕区域速查表中的数据zx(x=1,2,3)接近,则判定为退火炉炉辊压痕,否则判定为非退火炉炉辊压痕;最后根据退火炉炉辊压痕位于带钢上/下表面位置,回查所述连续退火炉转向辊压痕区域速查表,确定炉辊压痕产生区域。所述步骤e)中,退火炉重新建立张力,压痕所在区域的张力n1为原运行张力n的30%,其他区域保持原运行张力。所述步骤g)中,通过画面上显示标靶炉辊hs-b和ova-b的旋转圈数,计算标靶炉辊hs-b运行里程l-hs和ova-b运行里程l-ova,计算满足公式:l-hs=n-hs×π×d1l-ova=n-ova×π×d2当标靶炉辊hs-b运行里程l-hs和ova-b运行里程l-ova与压痕缺陷距离基准点距离l的偏差不得超过30m则认为l值有效。所述步骤j)中,退火炉恢复张力时,压痕区域段炉内张力n2提高至原运行张力n的150%。本发明积极效果:可以简单高效的查找出产生压痕的炉辊位置,并通过静止状态的低温带钢与运动状态的炉辊之间的滑动摩擦来消除炉辊表面异物,进而消除连续退火炉炉辊压痕缺陷。该方法有效的避免长时间停车开炉查找压痕炉辊的复杂步骤,极大降低了缺陷排查阶段的能源介质消耗,降低炉辊压痕缺陷带来的产品降级损失,该方法不需要开炉处理,不需要人员进入炉膛作业,具有简单高效,可操作性强,省时省力的特点。附图说明图1是本发明实施例连续退火炉结构及炉辊布置图;图2是本发明实施例现场点动炉辊打磨示意图;图中标记如下:1、预热段ph,2、加热段hs,3、均热段ss,4、缓冷段scs,5、快冷段rcs,6、过时效段ova,7、终冷段fcs,8、水淬段wq,9、前段标靶炉辊hs-b,10、后段标靶炉辊ova-b,11、带钢,12、现场操作箱。具体实施方式下面结合附图,通过实施例对本发明作进一步说明。一种消除连续退火炉炉辊压痕缺陷的方法,包含如下步骤:制定连续退火炉转向辊压痕区域速查表和连续退火炉转向辊位置速查表,通过测量带钢表面压痕缺陷距离,比对退火炉转向辊压痕区域速查表,确定连续退火炉炉辊压痕缺陷产生区域;再利用低温小张力使得炉辊压痕形状变小或消失,并以此计算产生压痕炉辊距离出炉基准点距离,比对连续退火炉转向辊位置速查表确定压痕炉辊位置;然后通过静止状态的低温带钢与运动状态的炉辊之间的滑动摩擦来消除炉辊表面异物,进而消除连续退火炉炉辊压痕缺陷。本实施例中,图1所示,连续退火炉按照由入口到出口的方向分为预热段ph、加热段hs、均热段ss、缓冷段scs、快冷段rcs、过时效段ova、终冷段fcs和水淬段wq。图1所示,连续退火炉各段炉辊分布为:预热段7根炉辊,加热段38根炉辊,均热13根炉辊,缓冷5根炉辊,快冷7根炉辊,过时效段45根炉辊,终冷段13根炉辊,水淬段3根炉辊。图1所示的预热段ph、加热段hs、均热段ss的炉辊辊径均为800mm,缓冷段scs、快冷段rcs、过时效段ova、终冷段fcs炉辊辊径均为1300mm,水淬段wq炉辊辊径1200mm。图1所示的炉辊hs-b为前段标靶炉辊,炉辊ova-b为后段标靶炉辊。图1所示张力计辊布置在各段入口位置,用来测量各段张力值。本发明的执行过程为:1.制定连续退火炉转向辊压痕区域速查表根据连续退火炉各段转向辊的直径dx(x=1,2,3),计算出每根炉辊的周长zx=πdx(x=1,2,3),用于退火炉转向辊压痕区域速查,如表1。表1-某冷轧厂连续退火炉转向辊压痕区域速查表压痕位置产生压痕的转向辊压痕间距(mm)辊径(mm)对应炉辊区域带钢上表面底辊2512800预热段、加热段、均热段带钢下表面顶辊2512800预热段、加热段、均热段带钢上表面底辊40821300缓冷段、快冷段、过时效段、终冷段带钢下表面顶辊40821300缓冷段、快冷段、过时效段、终冷段带钢上表面底辊37681200水淬段带钢下表面顶辊37681200水淬段2.制定连续退火炉转向辊位置速查表以连续退火炉出口地面为基准点,参照连续退火炉炉内炉辊分布图,根据连续退火炉炉辊辊径、底辊和顶辊高度差、炉辊标高等数据,计算每根炉辊入口侧距基准点的长度li(i=1,2,3…),见表2所示。表2-某冷轧厂连续退火炉转向辊位置速查表炉辊位置炉辊编号辊径mm炉辊到出炉基准点长度m预热段phs18002393.713预热段phs28002380.933…………加热段hs238001903.229加热段hs248001881.753…………均热段ss108001402.231均热段ss118001380.755…………过时效段oas613001113.746过时效段oas151300922.458…………水淬段wq3120045.5313.判定连续退火炉炉辊压痕及其产生区域质检人员发现带钢表面出现压痕缺陷后,确定压痕产位于带钢上表面,首先找到相同形貌的3个连续压痕缺陷点,测量两个压痕之间的距离c1(2510mm)和c2(2512mm),即第一组数据;接着间隔150多米后,再次找到相同形貌的3个连续压痕缺陷点,测量两个压痕之间的距离c3(2512mm)和c4(2511mm),即第二组数据;然后根据两组数据与表1中数据2512mm相近,偏差在2mm以内,则判定为退火炉炉辊压痕,且产生炉辊压痕辊径为800mm,区域为预热段,加热段和均热段;4.降速停炉。首先连续退火炉立即切换至停止模式,在产线速度降至0m/min后并卸掉退火炉内的带钢张力,然后连续退火炉启动降温模式,将退火炉温度从860℃降至500℃。5.记录初始数据。待连续退火炉温度降至500℃后,对连续退火炉重新建立张力,其中预热段、加热段和均热段张力设定为4.5kn,其他区域张力保持原运行张力,然后连续退火炉启动爬行模式,速度30m/min,质检人员记录运行开始时间t1,并在连续退火炉出口基准点位置观察压痕情况,同时在画面上对标靶炉辊hs-b和ova-b的旋转圈数进行清零及计数重启。6.计算炉辊压痕与基准点距离。质检人员发现压痕缺陷明显变小或消失时,产线立即停车并记录下运行停止时间t2,则产线运行时长t=t2-t1=47min,压痕缺陷产生位置距离基准点距离l=30m/min×47min=1410m;7.数据有效性核实停车时画面显示标靶炉辊hs-b旋转圈数为560,标靶炉辊hs-b旋转圈数为342,则标靶炉辊运行里程分别为。l-hs=560×3.14×800mm=1406ml-ova=342转×3.14×1300mm=1396m标靶炉辊hs-b运行里程l-hs和标靶炉辊ova-b运行里程l-ova与压痕缺陷产生位置距离基准点距离l偏差在4m,小于规定的误差值30米;8.根据退火炉炉辊压痕缺陷距离基准点距离l=1410m,回查所述步骤2连续退火炉转向辊位置速查表,与均热段ss10辊距离标准点位置接近,且ss10为底辊,与压痕缺陷位于带钢上表面相吻合,所以确定产生此压痕缺陷的炉辊为ss10。9.现场炉辊打磨:保持退火炉均热段炉内张力为4.5kn不变,通过现场控制箱或者操作画面,单独点动炉辊ss10,转速为45m/min,炉辊先顺时针点动5分钟,然后再逆时针转动5分钟,如此反复进行7次。。10.炉辊打磨结束后,提高均热段张力至22.5kn,连续退火炉启动爬行模式,运行速度30m/min,运行时间t3=60min>47min。11.质检人员到达炉区出口基准点位置观察带钢表面质量,查看带钢表面炉辊压痕缺陷消失。12.退火炉升温至生产温度,产线运行。13.质检人员到达炉区出口基准点位置观察带钢表面质量,带钢表面炉辊压痕缺陷消失。当前第1页1 2 3