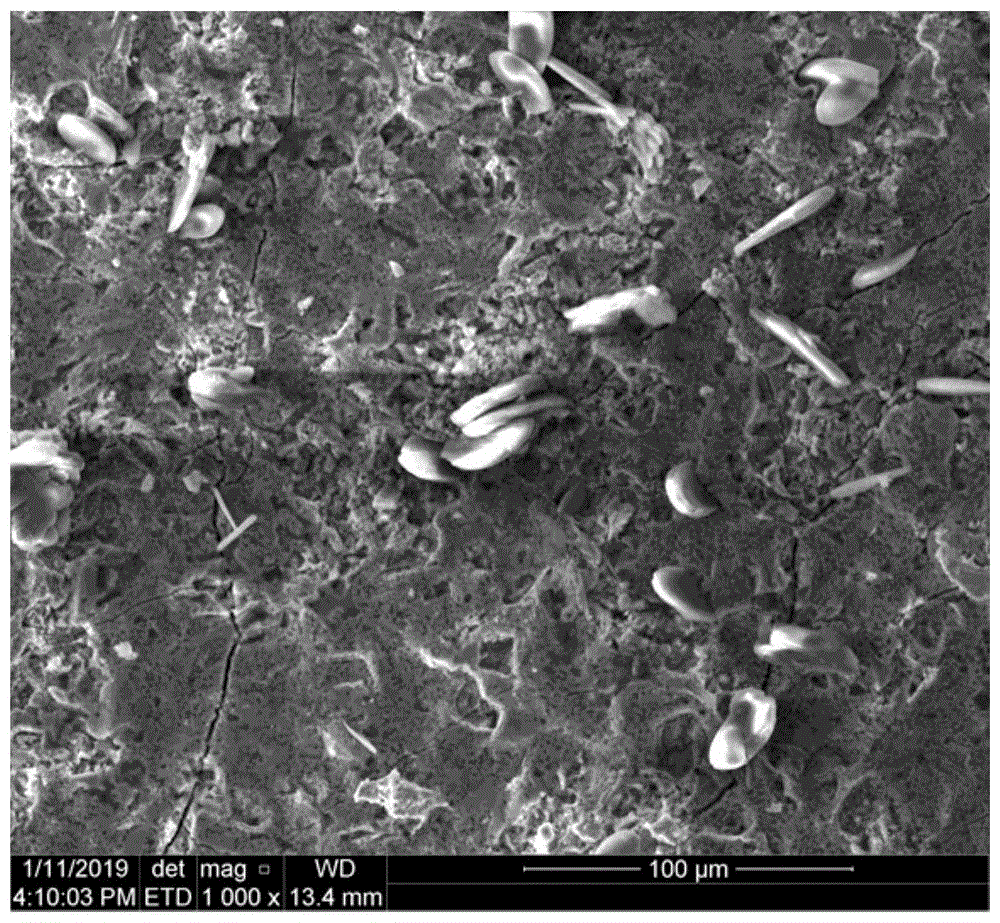
本发明属于热成形钢
技术领域:
,具体涉及一种抗拉强度1800mpa级镀铝钢板及其制造方法及热成形零部件。
背景技术:
:近年以来,节能减排法律法规的严格对车身轻量化提出了较高的要求。为实现车身轻量化的同时保持安全性能,高强度零部件被大量应用于汽车车身制造。冷成形超高强钢由于冲压过程中的回弹效应,在车身超高强零部件中的应用受到局限。热成形技术由于零件尺寸精度高、无回弹效应、强度级别高而得到广泛应用普及。在热冲压成形过程中,无涂层板的使用在加热过程中需要保护气氛防止钢板表面的氧化,但在热冲压过程中,零部件表面仍会发生部分氧化需要后续进行喷丸处理,才能进行焊装、涂装等后道工序。这大大增加了热成形零部件的成本,同时产生了环保压力。在装车后,热成形零部件通常作用b柱等安全件,这些零件处于在车身空腔位置,容易发生电泳不良的风险,在整车服役过程中,车身处于暴露于腐蚀环境中,零件容易产生锈蚀继而存在引发安全问题的风险。因此,涂层热成形钢被不断开发出来以应对上述问题。其中al-si镀层目前使用较广。然而al-si镀层在热成形过程中与空气接触形成铝硅的氧化物薄膜覆盖于表面,这层氧化物不能被磷酸溶解而导致磷化膜无法生成。因此al-si镀层热成形钢零部件在装车涂装时,不能形成质量好的磷化膜用来保证电泳漆层的粘附性和耐蚀性。在另外一方面,铝硅镀层在热成形之后镀层间会形成大量裂纹,在电泳过程中,电泳漆渗入微裂纹区,在裂纹区周围形成油漆较薄的区域,在宏观上造成油漆表面凹凸不平的外观,这些区域在腐蚀环境中容易产生锈点。关于镀层的研究,是目前热成形钢研究领域中重点课题;然而,随着人们对材料轻量化需求以及对车身安全性能的要求不断提高,基材的综合力学性能的提升也成为了研究焦点之一。目前使用量最大的是1500mpa级热成形钢产品,随着需求的不断升级,抗拉强度≥1800mpa级的热成形钢产品不断被人关注。技术实现要素:本发明的目的在于提供一种抗拉强度1800mpa级镀铝钢板及其制造方法,此种钢板在应用于制造热成形零部件,材料经热成形后,抗拉强度满足≥1800mpa性能需求,且具有优良的综合力学性能。本发明还提供了一种热成形零部件,采用所述的镀铝钢板经热成形工艺制备得到,其经磷化处理后,再经电泳涂装处理,得到的漆膜的外观平滑消除了因为微裂纹形成而造成的凹凸不平的缺陷,且附着力及耐腐蚀性良好。本发明采取的技术方案为:一种抗拉强度1800mpa级镀铝钢板,所述镀铝钢板包括基板和镀层,所述基板包括以下重量百分比的化学成分:c:0.25~0.35%、si:1.0~1.5%、mn:0.8~3.0%、p:≤0.05%、s:≤0.05%、al:≤0.10%、cr:0~1.0%、mo:≤0.05%、n:≤0.01%、nb+v:0.05~0.10%,余量为fe和不可避免的杂质;形成镀层的镀液成分为si:3.0~6.0%,sn、cu、mo三者中任意一种或多种的总含量为0.5~2.5%,剩余部分为al和不可避免的杂质。进一步地,所述c含量优选为0.30~0.35%。所述mn含量优选为1.5~2.5%。所述si含量优选为1.0~1.2%。所述nb含量优选为0.02~0.04%。所述v含量优选为0.03~0.05%。所述cr含量优选为0.2~0.5%。上述基板成分中,c元素的添加,主要目的是提高热成形后基体马氏体的组织硬度,c的添加量不得<0.25%,否则抗拉强度无法满足≥1800mpa的力学性能要求,c的添加量不得>0.35%,否则热成形后马氏体硬度过高,延伸率和冷弯性能无法满足要求,且对焊接性能带来不利影响。mn元素的添加,主要作用是增加mn元素含量能降低ac1和ac3温度,可以保证热处理后显微组织中保留一定量的残余奥氏体。si元素的添加,主要作用是能够阻碍渗碳体的析出,起到稳定奥氏体的作用,si的添加量不得<1.0%,否则无法形成足够稳定的残余奥氏体含量;si的添加量不得>1.5%,否则将引起钢板表面在退火过程中的选择性氧化,在加热过程中产生氧化铁皮,在热轧时,当氧化铁皮被压入板材表面,会使得板材的表面质量下降。nb的添加,主要作用是细化晶粒,nb的添加量不得<0.02%,否则晶粒细化效果不明显;nb的添加量不得>0.04%,否则多于的nb元素无法完全以析出物存在,从而造成合金成本增加。v的析出物比nb的析出物更细小,一般用于设置氢陷阱的合金元素,对于高强钢而言,添加一定量的v元素有利于提高材料的抗延迟断裂性能,v的添加量不得<0.03%,否则析出量不满足氢陷阱需求;v的添加量不得>0.05%,否则过多的v无法完全以析出态存在,从而造成合金成本增加。cr元素的添加来保证钢基体的淬透性。本发明的基板成分中不含ti元素,通过去除ti元素,消除ti(n,c)大颗粒的析出,避免nb合金元素与ti(n,c)形成共晶析出物,一方面消除大颗粒金属析出,提高组织均匀性;另一方面,降低了nb合金元素的无效消耗量。上述镀液成分中,si可在钢板表面形成fe-al-si抑制层,可以有效阻碍脆性相fe2al5形成,提高镀层粘附性。si含量低于3%时,fe-al合金层变厚,镀层粘附性降低,si含量大于6%时,影响镀层表面质量,根据以上情况,本发明镀液中添加si含量控制为3~6%。sn、cu、mo:具有抑制热成形后镀层中微裂纹形成的作用,减小了电泳涂装过程中的电泳漆液渗入微裂纹的几率;同时sn、cu、mo在热成形过程中抑制硅氧化膜的形成,促进热成形后磷化反应的进行,sn、cu、mo的总含量为0.5~2.5%,低于0.5%,效果不明显,大于2.5%引起镀层表面质量的下降和镀液成本的增加。本发明还提供了所述的抗拉强度1800mpa级镀铝钢板的制造方法,所述制造方法包括以下步骤:铁水预处理→转炉冶炼→合金微调→精炼→连铸→热轧→酸洗冷轧→清洗→连续退火→热浸镀→镀层厚度控制→合金化→冷却→涂油。所述热轧步骤中,加热温度≥1230℃,卷取温度560℃~680℃。所述酸洗冷轧步骤后得到的钢板的厚度为0.8~2.5mm。所述连续退火步骤中,退火温度为730~800℃,优选为730~750℃;退火温度不宜<730℃,否则退火不充分;退火温度不宜>800℃,否则在退火后的基体组织中会出现条带状马氏体组织,从而导致后续的合金化段无法满足mn和c元素的进一步球化和富集。所述热浸镀在连续热浸镀产线上进行,连续热浸镀产线配有合金化炉;热浸镀时使用气刀吹扫控制镀层厚度控制。所述热浸镀步骤中,钢带入镀液温度620~680℃,热浸镀镀液温度600~660℃,浸镀时间2~6s。热浸镀温度过低或时间过短,基体镀层之间的扩散层未充分形成导致漏镀风险增加。热浸镀温度过高或时间过长造成能耗较高及生产效率的降低。所述合金化步骤中,钢带以400~500℃温度进入合金化炉,合金化炉温度为550~700℃,合金化时间3~20s;合金化温度优选为600℃~700℃,合金化温度不宜<550℃,否则富mn和富c的珠光体无法充分析出,对热成形后的涂装性能提升作用降低;温度不宜>700℃,否则富mn和富c的珠光体会进一步分解,从而在后续的热成形过程中无法形成稳定的残余奥氏体,镀层表面质量下降。合金化工艺后镀层厚度为6~20μm。所述合金化步骤中,合金化炉使用还原性气氛或惰性气氛进行保护。所述还原性气氛优选为n2和h2的混合气;所述惰性气氛为n2。在热浸镀产线上进行合金化处理,同时在合金化处理的过程中使用保护气氛保护。这样做的益处在于:由于钢板是以热态进入合金化炉,可以在几秒内达到热成形过程中1~3min才能达到的镀层合金化效果,同时在此过程中钢板被保护性气氛包围,镀层不发生氧化,因此总的暴露于空气中的时间减少,si的氧化膜形成减少,热成形后钢板可磷化性增强,磷化膜可覆盖部分镀层表面裂纹,提升电泳涂装之后的附着力、耐蚀性。本发明还提供了一种热成形零部件,将所述的镀铝钢板经热成形工艺制备得到。所述热成形工艺为:基板厚度为0.8~1.6mm时,加热温度860~950℃,优选为880℃~900℃,加热时间2.0~5.0min,优选为3.0~4.0min;热成形温度650~780℃,然后以≥30℃/s的冷却速率保压淬火至ms点以下mf点以上的温度,温度区间为300~350℃;保压过程中维持模具温度为300~350℃,保温时间60~300s,优选为90~120s,保温过程中,富mn和富c的奥氏体会被保留下来,且残余奥氏体的存在位置不局限于境界处;保温结束后冷却至mf点以下,然后出模。基板厚度为1.6~2.5mm且不包含1.6mm时,加热温度900~950℃,优选为900℃~930℃,加热时间2.0~5.0min,优选为4.0~5.0min;热成形温度650~780℃,然后以≥30℃/s的冷却速率保压淬火至ms点以下mf点以上的温度,温度区间为300~350℃;保压过程中维持模具温度为300~350℃,保温时间60~300s,优选为90~120s,保温过程中,富mn和富c的奥氏体会被保留下来,且残余奥氏体的存在位置不局限于境界处;保温结束后冷却至mf点以下,然后出模。进一步地,所述冷却速率优选为30~50℃/s,以利于马氏体充分转变。进一步地,保压过程中,关闭模具中的冷却水,并通过模具上的感应加热设备,使模具保温至目标温度300~350℃;保温结束后,在模内通水冷却至mf点以下。本发明提供了一种镀铝钢板,此种钢板在应用于制造热成形零部件,材料经热成形后,抗拉强度满足≥1800mpa性能需求,且具有优良的综合力学性能,使用此种钢板制造热成形零部件可消除传统铝硅钢板在电泳之后形成的凹凸不平的外观,提升了电泳涂装之后附着力、耐蚀性。附图说明图1为实施例5中的镀铝钢板热成形后镀层磷化后的表面形貌;图2为对比例中的镀铝钢板热成形后镀层磷化后的表面形貌;图3为对比例(a)及实施例5(b)中的热成形试样电泳涂漆后的外观。具体实施方式下面结合实施例对本发明进行详细说明。通过铁水预处理→转炉冶炼→合金微调→精炼→连铸→热轧→酸洗→冷轧→得到表1中各成分的厚度0.8~2.5mm的冷轧带钢,然后将各冷轧带钢分别经清洗→连续退火→热浸镀→镀层厚度控制→合金化→冷却→涂油并按照表2-3中的参数进行控制,制备得到镀铝钢板。表1为各实施例和对比例中的基板化学成分及重量百分比(wt%)csimnpsalcrbnnb+vti实施例10.351.202.000.0050.0030.050.25-≤0.0010.080-实施例20.301.201.800.0050.0080.060.45-≤0.0010.071-实施例30.341.001.520.0060.0100.040.20-≤0.0010.082-实施例40.321.001.960.0040.0080.050.40-≤0.0010.077-实施例50.321.202.000.0040.0060.050.40-≤0.0010.073-实施例60.301.251.970.0040.0080.060.50-≤0.0010.072-对比例0.341.351.200.0040.0080.060.200.004≤0.001-0.036表2各实施例及对比例中的镀液化学成分及重量百分比(wt%)表3热轧、退火及热浸镀生产主要工艺参数将上述各实施例和对比例得到的镀铝钢板经热成形工艺加工成热成形零部件,具体热成形工艺参数如表4所示,得到的热成形零部件的力学性能如表5所示。表4热成形工艺表5热成形后力学性能使用如表6的磷化药剂及试验参数对热成形后试样进行磷化处理,磷化完成后使用sem分析表面形貌并参照《gb/t9792-2003金属材料上的转化膜单位面积膜质量的测定重量法》测定磷化膜重。以实施例5为例,实施例5中的镀铝钢板热成形后镀层磷化后的表面形貌如图1所示,由于镀层中元素的添加抑制了铝硅元素的表面氧化,使电泳前处理的磷化反应得以进行,虽然由于硅仍发生了部分氧化使磷化层未能全部覆盖于钢板表面,但磷化膜重大于0.5g/m2,结合镀层本身的粗糙形貌及镀层裂纹的抑制作用,有以下效果:电泳涂漆之后不存在凹凸不平的油漆外观,如图3中(b)所示,并且电泳涂装之后附着力及耐蚀性良好;而对比例中的磷化膜重仅为0.11g/m2,电泳涂漆之后存在凹凸不平的油漆外观,如图3(a)所示,并且电泳涂装之后附着力及耐蚀性较差。使用上述磷化工艺得到磷化板并配套关西lb-810型号电泳漆进行电泳涂装,电泳干膜厚度为18μm,随后进行外观评价、附着力(gb/t9286-1998)、耐蚀性测试((每循环包括:35±2℃下使用5%nacl喷雾4h、23±2℃温度50±6%rh湿度存放4h,40±2℃温度100%rh湿度存放16h,共30循环)。结果列于表7,实施例提升了可磷化性并消除了凹凸不平的电泳外观,并减少了由于此外观而造成的非划线区的锈点,同时附着力及划痕腐蚀扩展宽度指标优异。表6磷化过程参数表9为案例1~6的磷化性能、油漆附着力测试结果、耐腐蚀性能测试结果。表7涂装性能上述参照实施例对一种抗拉强度1800mpa级镀铝钢板及其制造方法及热成形零部件进行的详细描述,是说明性的而不是限定性的,可按照所限定范围列举出若干个实施例,因此在不脱离本发明总体构思下的变化和修改,应属本发明的保护范围之内。当前第1页12