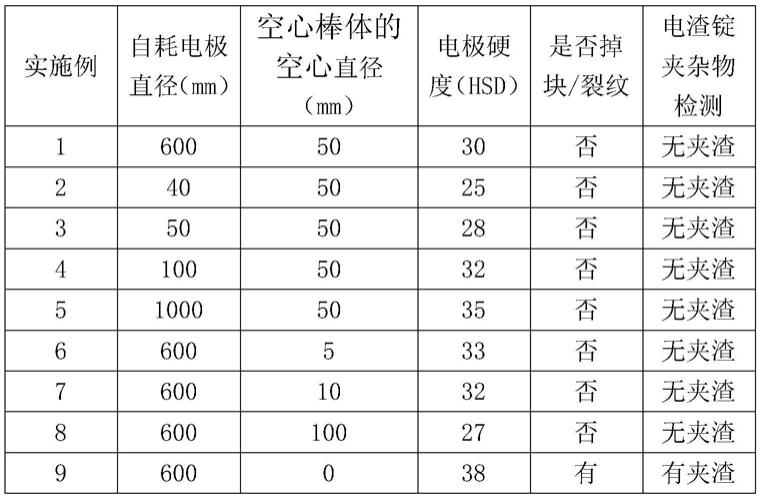
[0001]
本发明涉及电渣冶金技术领域,尤其涉及一种空心电渣重熔自耗电极及其制备方法和电渣重熔方法。
背景技术:[0002]
电渣重熔技术作为治炼优质钢锭的一种手段,其工作原理是将电极插入炉料进行埋弧操作,利用电弧的能量及电流通过炉料,因炉料的电阻而产生能量来满足熔炼所需的高温和补充化学反应所需的热量。并通过熔渣的电阻热使自耗电极熔化,金属熔滴穿过熔渣层而形成熔池,并在结晶器内重新结晶凝固成钢锭的一种方法,并以其优良的反应条件和特殊的结晶方式有着其他炼钢方法所不能代替的优越性。电渣重熔技术主要广泛用在高温合金、模具钢、军工产品等特殊钢冶炼上,其主要目的是提纯金属并获得洁净均匀致密的钢锭。经电渣重熔的钢,纯度高、含硫低、非金属夹杂物少、钢锭表面光滑、洁净均匀致密、金相组织和化学成分均匀。
[0003]
目前,电渣重熔过程一般是在常规大气下进行,由于空气中氧气及水份的存在,电渣重熔过程中电极坯料因导电发热将产生坯料发红并产生表面高温氧化现象;电渣重熔的电弧也将电离空气中的气体及水份,导致熔渣及钢液对氢、氧、氮等气体含量的摄入,进而导致钢中气体及夹杂物的增加,影响钢锭的质量。目前主要通过从电渣重熔炉底吹惰性气体对自耗电极进行重熔冶炼,以提高钢锭质量。现有的电渣重熔工艺需要在电渣重熔炉炉体上设置进气孔以供向炉体中通入惰性气体,上述方法存在惰性气体分布不均、且电渣重熔炉密封性较差,导致钢水温度下降快,必须提供热源保证吹氩时间。
[0004]
因此,亟需提供一种空心电渣重熔自耗电极及其制备方法和电渣重熔方法,以解决电渣冶金过程中的吸气问题。
技术实现要素:[0005]
本发明的目的是针对现有技术存在的问题,提供一种空心电渣重熔自耗电极及其制备方法和电渣重熔方法,通过从自耗电极的空心中通入氩气,以解决电渣冶金过程中的吸气问题。
[0006]
为实现上述目的,本发明采用的技术方案是:
[0007]
一种空心电渣重熔自耗电极,包括轴线沿前后方向延伸的空心棒体,且所述空心棒体上端呈缩口径。
[0008]
作为上述方案的进一步限定,所述空心棒体的空心孔径为5~100mm。以保证空心电渣重熔自耗电极强度的同时,提升空心棒体的气体流量,以提高电渣炉中杂质的去除效果,显著的提高了钢水的质量。
[0009]
作为上述方案的进一步限定,所述空心电渣重熔自耗电极为圆形或方形。
[0010]
作为上述方案的进一步限定,所述自耗电极的直径为50~1000mm。以保证空心电渣重熔自耗电极强度的同时,提升空心棒体的气体流量,并为炉料提供所需的能量,以满足
不同的熔炼需求。
[0011]
本发明的另一目的在于提供所述的一种空心电渣重熔自耗电极的制备方法,步骤如下:
[0012]
1)根据自耗电极对应的待制备的合金铸锭所需各元素的种类及含量配置自耗电极主体的原料并进行合金化冶炼,待出钢后,将钢液浇筑形成空心电渣重熔自耗电极;
[0013]
2)将步骤1)浇筑成的自耗电极进行均质化处理,制得所述空心电渣重熔自耗电极。
[0014]
本发明的再一目的在于提供一种空心电渣重熔自耗电极的电渣重熔方法,包括如下步骤:
[0015]
s1、将空心电渣重熔自耗电极缓慢下降并插入电渣炉的炉渣中,从空心棒体上端缩口径处通入氩气,然后通电起弧,调整重熔电压和重熔电流;
[0016]
s2、自耗电极的端部缓慢熔融,熔融的金属聚集成金属熔滴,从自耗电极端头脱落,穿过渣池进入金属熔池,在水冷结晶器的强制冷却下形成铸锭;
[0017]
s3、脱落的金属熔滴进行熔融时,未熔融的自耗电极暂停10~20s后再下降,且下降速度加速10~20%:
[0018]
s4、电渣重熔完成后所得的铸锭经退火处理后通过机械加工得到成品。
[0019]
作为上述方案的进一步限定,所述自耗电极在渣池中的埋入深度与自耗电极的直径比为0.5~0.7:1。
[0020]
与现有技术相比,本发明的有益效果是:
[0021]
(1)本发明通过浇筑形成内部空心的电渣重熔自耗电极,以在电渣重熔过程中从自耗电极内部空心通入氩气,解决电渣冶金过程中的吸气问题,并能够有效隔离电渣重熔精炼过程中结晶器内的空气,通过形成良好的气体保护层,有效减小重熔期间钢液对各种气体含量的再次摄入,进而减少因各种因素影响所导致的钢中夹杂物增多,以提高最终电渣钢锭的内部质量。同时本发明能够精简电渣重熔炉结构,以提高其密封性,并促使保护气充满结晶器内部空间形成良好的气体保护层,并使保护气得到充分利用,减少保护气体损耗。
[0022]
(2)本发明将空心电渣重熔自耗电极的空心棒体上端设置成缩口径,方便保护气的导入,并防止导气管与空心棒体上端脱落,以提高电渣重熔过程中各种气体含量的再次摄入,进而减少因各种因素影响所导致的钢中夹杂物增多,以提高最终电渣钢锭的内部质量。
[0023]
(3)本发明通过将空心棒体的空心孔径设置为5~100mm,在保证空心电渣重熔自耗电极强度的同时,能够提升空心棒体的气体流量,以提高去除杂质效果,并适应于不同的电渣重熔工艺需求。
附图说明
[0024]
图1为本发明一种空心电渣重熔自耗电极的结构示意图;
[0025]
图2为本发明一种空心电渣重熔自耗电极的俯视图;
[0026]
图中:1、空心棒体;2、电极把持器。
具体实施方式
[0027]
为了使本发明的目的、技术方案及优点更加清楚明白,以下结合实施例,对本发明进行进一步详细说明;应当理解,此处所描述的具体实施例仅仅用以解释本发明,并不用于限定本发明;除非特别说明,本发明采用的试剂、方法和设备为本技术领域常规试剂、方法和设备。
[0028]
参照图1~2,本发明提供一种空心电渣重熔自耗电极,包括轴线沿前后方向延伸的空心棒体1,且所述空心棒体1上端呈缩口径。
[0029]
在使用时,将空心电渣重熔自耗电极固定于电极夹持器2上,缓慢下降并插入电渣炉的炉渣中,通过将所述空心棒体1上端的缩口径与保护气输出管连接向电渣炉中通入氩气,然后通电起弧,调整重熔电压和重熔电流,以实现钢锭的精炼过程。
[0030]
进一步的,在实际电渣重熔过程中,可根据应用需求,将电渣重熔自耗电极所述空心棒体1的空心孔径设置为5~100mm。以保证空心电渣重熔自耗电极强度的同时,提升空心棒体1的气体流量,以提高电渣炉中杂质的去除效果,显著的提高了钢水的质量。
[0031]
进一步的,所述空心棒体1的材质与现有电渣重熔自耗电极的材质相同,以确保电渣重熔自耗电极的强度,从而减少空心电渣重熔自耗电极在受电极把持器5夹持升降时被挤压变形及损坏。
[0032]
进一步的,述空心电渣重熔自耗电极为圆形或方形,以满足不同的电渣重熔需求,提高自耗电极的应用范围。
[0033]
进一步的,所述自耗电极的直径为50~1000mm。以保证空心电渣重熔自耗电极强度的同时,提升空心电渣重熔自耗电极的气体流量,并为炉料提供所需的能量,以满足不同的熔炼需求。
[0034]
下面通过具体的实施例子并结合附图对本发明做进一步的详细描述。
[0035]
实施例1
[0036]
一种空心电渣重熔自耗电极的制备方法,步骤如下:
[0037]
1)根据自耗电极对应的待制备的合金铸锭所需各元素的种类及含量配置自耗电极主体的原料并进行合金化冶炼,待钢水温度达到1560~1580℃时出钢,将钢液浇筑形成空心电渣重熔自耗电极;
[0038]
2)将步骤1)浇筑成的自耗电极于1200℃下进行均质化处理9h,制得所述空心电渣重熔自耗电极。
[0039]
本实施例制得的电渣重熔自耗电极的直径为600mm;所述空心棒体的空心孔径为50mm。
[0040]
实施例2-9
[0041]
实施例2-9提供一种空心电渣重熔自耗电极的制备方法,与实施例1相比,不同之处在于,改变所述自耗电极的直径、空心棒体的空心孔径大小,除上述区别外,其他操作均相同,在此不再赘述;具体实验条件参数及测试结果如下表所示。
[0042][0043]
由上表结果可知,当浇筑制成的自耗电极的直径为50~1000mm时,制备的自耗电极硬度在29~35hsd,由此说明本发明制得的空心电渣重熔自耗电极具备较高的硬度;且与实施例9制得的不具有空心结构的电渣重熔自耗电极相比,本发明实施例制备的自耗电极在电渣重熔过程均未出现掉块与开裂现象,而对照试验出现掉块与裂纹;电渣锭夹杂物检测结果显示,在本发明优化限定的各条件参数下,制得的自耗电极均无夹渣,而对照试验有夹渣;且通过电极金相组织结果显示:在本发明优化限定的各条件参数下制得的自耗电极均为片状珠光体,而对照试验为(实施例9)点球状珠光体。
[0044]
实施例10
[0045]
本实施例以gh37合金作为自耗电极,自耗电极坯尺寸为∮500mm,结晶器尺寸为∮600mm。
[0046]
选用如下重量份组分的重熔精炼渣:caf
2 50份、al2o
3 20份、cao 15份、tio
2 10份和mgo 5份。其中,caf2、al2o3、cao、tio2和mgo中sio2的质量含量均≤1.0%。
[0047]
采用如下方法对gh37合金进行电渣重熔,包括如下步骤:
[0048]
s1、将上述重熔精炼渣于800℃下保温烘烤10小时,以上述gh37合金作为自耗电极,装配好电渣重熔炉,并将空心电渣重熔自耗电极缓慢下降并插入电渣炉的炉渣中,将脱氧剂和步骤1)烘烤好的重熔精炼渣,加入到专门化渣炉内熔化,熔渣全部熔化完后倒入重熔炉内;其中,所述重熔精炼渣的添加量为240kg(所述自耗电极重量的4%);所述化渣时加入脱氧剂的质量为3600g,所述脱氧剂为钛铁粉和铝粉,所述钛铁粉加入质量为1350g,铝粉的加入质量为2250g;控制自耗电极在渣池中的埋入深度与自耗电极的直径比为0.6:1;
[0049]
s2、步骤s1的熔渣全部熔化完倒入重熔炉内后,从空心棒体上端缩口径处通入氩气,然后通电起弧,调节电压为64v,电流为11500a,在惰性气体氩气保护下对所述自耗电极进行重熔冶炼,自耗电极的端部缓慢熔融,熔融的金属聚集成金属熔滴,从自耗电极端头脱落,穿过渣池进入金属熔池,在水冷结晶器的强制冷却下形成铸锭;冶炼过程中加入钛铁粉和铝粉进行脱氧,钛铁粉和铝粉的总添加量与所述自耗电极的质量比为0.8:1000,所述钛铁粉和铝粉的质量比为1:1,所述钛铁粉和铝粉加入的总量为4800g;所述氩气的流速控制
为20l/min,冶炼过程中所述钛铁粉和铝粉按照9g/min的速度进行添加;
[0050]
s3、脱落的金属熔滴进行熔融时,未熔融的自耗电极暂停15s后再下降,且下降速度加速15%:
[0051]
s4、电渣重熔完成后所得的铸锭经退火处理后通过机械加工得到成品。
[0052]
本实施例采用的自耗电极gh37合金钢标准[al]%:1.8~2.3、[ti]%:1.7~2.3,制得6吨重量的电渣锭,对制得的电渣锭进行性能检测。结果显示:未重熔前自耗电极中al的含量为2%,ti的含量为2.1%,重熔后获得的电渣钢锭al的收得率为96%,偏差在5%以内;ti的收得率为99%,偏差在5%以内,且钢锭头部、中部、尾部中al、ti的分布均匀。
[0053]
以上所述,仅为本发明的说明实施例,并非对本发明任何形式上和实质上的限制,应当指出,对于本技术领域的普通技术人员,在不脱离本发明方法的前提下,做出的若干改进和补充也应视为本发明的保护范围;凡熟悉本专业的技术人员,在不脱离本发明精神和范围的情况下,利用以上所揭示的技术内容做出的些许更改、修饰与演变的等同变化,均为本发明的等效实施例;同时,凡依据本发明的实质技术对上述实施例所做的任何等同变化的更改、修饰与演变,均仍属于本发明的保护范围。