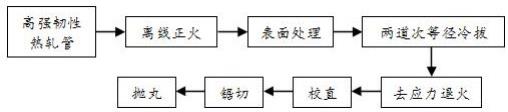
[0001]
本发明涉及冷拔钢管加工技术,具体是一种高强度低应力冷拔钢管及生产方法。
背景技术:[0002]
工程机械特别是起重机、泵车等超远距离作业机械,液压油缸随着作业吊臂伸展到100米以外,油缸重量的累加效应百倍增加,所以,大型工程机械对液压缸的重量要求越来越严苛,开发超高强韧性冷拔管是轻量化技术的最优选择,使用冷拔技术制造油缸可以使液压缸减重10%以上。
[0003]
冷拔钢管的原材料一般是无缝钢管企业生产的热轧钢管。普通热轧钢管在热轧变形过程中,由于在轴向与径向变形率不同,存在变形方向的应力不均匀;热轧钢管冷却不均匀也会导致热应力不均匀。
[0004]
钢管在冷拔成型过程中内外表面受摩擦力作用,而中心层金属在冷拔拉力作用下自由塑性变形,所以冷拔管内外壁表层的金属流速一致,而中心层金属的流速比内外表面层快,钢管在拉拔过程中的塑性变形是不均匀的。受不均匀变形的影响,冷拔钢管内外壁表层与中心层会产生附加应力,这种附加应力在冷拔后仍然残留在钢管中,形成冷拔管的残余应力。
[0005]
冷拔管的残余应力如果过大,在后续机械加工过程中,不均匀的应力不断释放,最终影响到产品的加工精度甚至造成油缸加工报废。另外,对液压缸筒而言,残余应力在方向性影响着缸筒的承载能力。研究认为:残余压应力可以抵消一部分载荷产生的应力,从而可以提高缸筒的承载能力,而残余拉应力刚好相反。因此降低和消除承压结构件的残余应力就十分必要了。
[0006]
中国专利公开了一种高精度冷拔管及其制作方法(cn105463311u),采用低合金高强度结构钢作为坯料,化学元素组成及质量百分比含量为:碳c≤0.20%、硅si≤0 .50%、锰mn≤1 .70%、磷p ≤ 0 .035%、硫s≤0 .035%、铌nb≤0 .07%、钒v≤0 .20%、钛ti≤0 .20%、铬cr≤0 .30%、镍ni≤0 .80%、铜cu≤0 .30%、氮n≤0 .015%、钼mo≤0 .20%,调整炼钢质量和机械性能加入的铝al元素和微量硼b元素,余量为铁fe;制作方法:车头拉拔
→
表面处理
→
两道次冷拔
→
强韧化热处理
→
校直
→
定尺锯切。其中,两个道次总变形量控制在1.25-1.45,第二道次冷拔前停放时间控制在20分钟-5小时,第二道冷拔变形量大于第一道次且减壁量≥ 1mm,两个道次之间无需二次磷化皂化;退火温度为380-500℃,保温时间2 .5-5小时,出炉温度≤ 350℃;控制磷化膜厚度10-30μm。
[0007]
上述现有技术存在的不足是:制作流程第一步需要车拉拔头,使生产周期延长、成本增加;热轧管坯本身应力不均匀,导致后续冷拔钢管的应力不易控制;采用两道次冷拔加工,要求总变形率控制在1.25-1.45,虽然提高了冷拔精度,但也没有解决冷拔管残余应力的问题。
技术实现要素:[0008]
本发明的目的是提供一种高强度低应力冷拔钢管及生产方法,在保证高强度的同时,降低其冷变形过程中产生的残余应力水平,提高其尺寸稳定性,避免后续加工与使用过程中的变形,保证工程机械油缸的尺寸稳定性。
[0009]
本发明通过以下技术方案实现:一种高强度低应力冷拔钢管,其化学元素组成及质量百分比含量为:碳c:0.16~0.23%,硅si:0.1~0.5%,锰mn:1.3~1.7%,磷p:≤0.025%,硫s:≤0.035%,铬cr:≤0.3%,镍ni:≤0.3%,铜cu:≤0.25%,钒v:0.05~0.2%,铝al:0.015~0.06%,其余为铁fe。
[0010]
一种高强度低应力冷拔钢管生产方法,采用高强韧性热轧管冷拔,高强韧性热轧管的化学元素组成及质量百分比含量为:碳c:0.16~0.23%,硅si:0.1~0.5%,锰mn:1.3~1.7%,磷p:≤0.025%,硫s:≤0.035%,铬cr:≤0.3%,镍ni:≤0.3%,铜cu:≤0.25%,钒v:0.05~0.2%,铝al:0.015~0.06%,其余为铁fe;步骤如下,
①
热轧生产高强韧性热轧管作为冷拔坯料;
②
离线正火处理;
③
表面处理;
④
两道次等径冷拔;采用两道次等径冷拔变形,每一道次的冷拔坯料与冷拔后的冷拔钢管的几何中径相差不大于5mm;成品道次变形率为1.05~1.1;
⑤
去应力退火;
⑥
校直;
⑦
锯切;
⑧
抛丸。
[0011]
优选的:步骤
②
中离线正火处理,冷拔坯料在热轧生产后,在920~950℃,保温30min;冷拔坯料利用环切法测量,应力为压应力,应力值大小在50mpa内。
[0012]
优选的:步骤
⑤
中去应力退火,退火温度450~500℃,保温时间2~3h,出炉温度≤300℃。
[0013]
与现有技术相比,本发明的有益效果是:1,冷拔钢管原材料应力小,此新材料高强韧性热轧管利用环切法测量,应力为压应力,应力值大小在50mpa内;2,采用两道次等径冷拔变形工艺,保证冷拔坯料与冷拔钢管的几何中径值相等或相差不大于5mm,钢管的外径与内径变形率相等,钢管压力分布均匀,降低冷拔管最终残余应力;3,“去应力退火+抛丸处理”,进一步降低钢管在冷变形过程中产生的应力,优化应力分布,最终冷拔管应力为压应力,应力最大值不大于100mpa;4,冷拔钢管抗拉强度≥820mpa,屈服强度≥720mpa,超过普通国标材料冷拔管屈服强度160mpa,断后伸长率≥15%,且在-20℃下,v2型缺口冲击试样的测试结果≥27j;该冷拔钢管加工成液压油缸缸筒,其全长直线度≤0.25mm,内孔圆度≤0.05mm,综合性能达到国际领先水平。
附图说明
[0014]
图1是本发明生产方法的流程图。
具体实施方式
[0015]
以下是本发明的一个具体实施例,现结合附图对本发明做进一步说明。
[0016]
实施例一一种高强度低应力冷拔钢管,其化学元素组成及质量百分比含量为:碳c:0.16~0.23%,硅si:0.1~0.5%,锰mn:1.3~1.7%,磷p:≤0.025%,硫s:≤0.035%,铬cr:≤0.3%,镍ni:≤0.3%,铜cu:≤0.25%,钒v:0.05~0.2%,铝al:0.015~0.06%,其余为铁fe。
[0017]
实施例二一种高强度低应力冷拔钢管生产方法,采用高强韧性热轧管冷拔,高强韧性热轧管的化学元素组成及质量百分比含量为:碳c:0.16~0.23%,硅si:0.1~0.5%,锰mn:1.3~1.7%,磷p:≤0.025%,硫s:≤0.035%,铬cr:≤0.3%,镍ni:≤0.3%,铜cu:≤0.25%,钒v:0.05~0.2%,铝al:0.015~0.06%,其余为铁fe;步骤如下,
①
热轧生产高强韧性热轧管作为冷拔坯料;
②
离线正火处理;冷拔坯料在热轧生产后,在920~950℃,保温30min;离线正火处理后的冷拔坯料利用环切法测量,应力为压应力,应力值大小在50mpa内;
③
表面处理;
④
两道次等径冷拔;采用两道次等径冷拔变形,每一道次的冷拔坯料与冷拔后的冷拔钢管的几何中径相差不大于5mm;成品道次变形率为1.05~1.1;
⑤
去应力退火;退火温度450~500℃,保温时间2~3h,出炉温度≤300℃;
⑥
校直;
⑦
锯切;
⑧
抛丸;本发明实施例使用的原材料通过添加对改善材料强韧性有益的合金成分,提高钢管材料的原始性能,使高强韧性热轧钢管在正火状态下交货,也可以达到很高的强韧性指标,并保证原材料残余应力最小。这样的材料有利于在后续冷拔过程中减小残余应力。在冷拔工艺研究方面,本实施例公开等径冷拔工艺以及冷拔管应力消除技术,保证冷拔钢管的环切法应力为压应力,应力值大小在100mpa内。
[0018]
本实施例技术效果在于:高强韧性热轧管采用“低碳、中锰、微合金化”提高热轧管坯性能,屈服强度比普通国标材料高160mpa;通过添加细化晶粒元素v、al、cr提高原材料性能;钢管在热轧生产后,采用离线正火处理(920~950℃,保温30min),消除原材料及热轧过程中产生的加工应力与热应力。保证冷拔钢管原材料应力最小,此新材料高强韧性热轧管利用环切法测量,应力为压应
力,应力值大小在50mpa内。
[0019]
采用两道次等径冷拔变形工艺,保证冷拔坯料与冷拔钢管的几何中径值相等或相差不大于5mm,钢管的外径与内径变形率相等,钢管压力分布均匀;且成品道次变形率设计为1.05~1.1,优化成品道次变形量,首次冷拔变形产生的应力,在二次变形时得到均匀化,达到降低冷拔管最终残余应力的技术效果;对冷拔后的钢管进行“去应力退火+抛丸处理”,进一步降低钢管在冷变形过程中产生的应力,优化应力分布,避免后续加工过程变形,提高产品的尺寸稳定性;采用退火温度450~500℃,保温时间2~3h,出炉温度≤300℃,得到的冷拔管性能最佳,残余应力小;对校直后的冷拔管进行抛丸处理,一方面可提高涂装时油漆附着力;另一方面非均匀的外表层塑性变形在钢管表面形成残余压应力,最终冷拔管利用切环法测量应力为压应力,应力最大值不大于100mpa。
[0020]
利用本发明得到的冷拔钢管,其抗拉强度≥820mpa,屈服强度≥720mpa,超过普通国标材料冷拔管屈服强度160mpa,断后伸长率≥15%,且在-20℃下,v2型缺口冲击试样的测试结果≥27j;该冷拔钢管加工成液压油缸缸筒,放置6个月后用激光跟踪仪检测,其全长直线度≤0.25mm,内孔圆度≤0.05mm,综合性能达到国际领先水平。