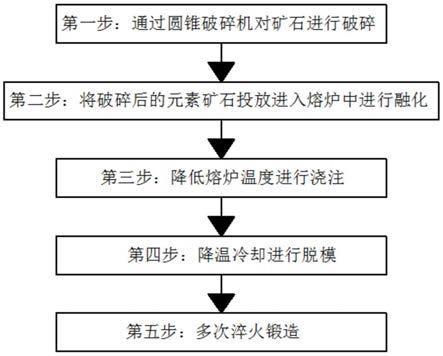
[0001]
本发明属于钢材制备技术领域,具体涉及采用稀土处理和纯净化冶炼的高强韧稀土耐磨钢制备工艺。
背景技术:[0002]
钢,是对含碳量质量百分比介于0.02%至2.11%之间的铁碳合金的统称。钢的化学成分可以有很大变化,只含碳元素的钢称为碳素钢(碳钢)或普通钢;在实际生产中,钢往往根据用途的不同含有不同的合金元素,比如:锰、镍、钒等等。人类对钢的应用和研究历史相当悠久,但是直到19世纪贝氏炼钢法发明之前,钢的制取都是一项高成本低效率的工作。如今,钢以其低廉的价格、可靠的性能成为世界上使用最多的材料之一,是建筑业、制造业和人们日常生活中不可或缺的成分。可以说钢是现代社会的物质基础,然而市面上各种的钢在制备的时候仍存在各种各样的问题。
[0003]
如授权公告号为cn102242314b所公开的一种多元合金强韧化、耐磨中锰钢及制备工艺,其虽然实现了采用稀土硅铁合金、钛铁合金和钒铁合金的复合变质剂进行处理,通过对熔炼、消失模负压成型、水韧处理、回火等工艺过程和参数控制,制备的电铲斗齿、半自磨机衬板、输送机刮板等耐磨钢件,使用寿命比高锰钢提高2倍以上,但是并未解决现有钢材存在的强韧性匹配不高、耐磨损性能降低和服役寿命较短,内部含有大量的磷和氧,工艺简单等的问题,为此我们提出采用稀土处理和纯净化冶炼的高强韧稀土耐磨钢制备工艺。
技术实现要素:[0004]
本发明的目的在于提供采用稀土处理和纯净化冶炼的高强韧稀土耐磨钢制备工艺,以解决上述背景技术中提出的问题。
[0005]
为实现上述目的,本发明提供如下技术方案:采用稀土处理和纯净化冶炼的高强韧稀土耐磨钢制备工艺,包括有以下制备步骤:
[0006]
s1:通过圆锥破碎机对矿石进行破碎;将常规元素矿石通过圆锥破碎机进行破碎处理,并且将常规合金元素矿石和稀土元素矿石进行粉碎,并且分别进行过筛处理;
[0007]
s2:将破碎后的元素矿石投放进入熔炉中进行融化;将破碎后的常规元素矿石按照比列投放进入到熔炉中进行高温热熔,进行热熔4-5h后,第一次降低温度,然后再将常规合金元素矿石按照比例投放进入到熔炉中进行热熔混合,且热熔时长为3-4h,第二次降低温度,将稀土元素矿石按照比例投入到熔炉中进行热熔,升高温度,热熔时长为5-6h;
[0008]
s3:降低熔炉温度进行浇注;在浇注模型的内壁上均匀的涂抹纳米活性炭,然后降低熔炉的温度,再将熔炉中的金属溶液通过浇注速率为20s-26s浇注6m-8m的速率进行浇注,并且在浇注过后立马在溶液上方铺设一层纳米活性炭;
[0009]
s4:降温冷却进行脱模;在浇注过后,并且使得溶液表层的纳米活性炭燃烧结束后,对浇注模具进行急剧的降温冷却,使得浇注模具中的溶液快速的进行冷却成型;
[0010]
s5:多次淬火锻造;通过锻造平台对冷却后的钢材进行加热,然后通过锻造锤进行
捶打,使得钢材能够成型,且在捶打结束后进行淬火,并且对钢材至少进行淬火锻造三次,将钢材表面的纳米活性炭锤出,以及将钢材内部的杂质和空隙锻造排出。
[0011]
优选的,所述s1中的常规元素矿石的破碎后直径保持在10-30cm之间,所述常规合金元素矿石的破碎后直径保持在2-10cm之间,所述稀土元素矿石的破碎后直径保持在0.5-2cm之间。
[0012]
优选的,所述s2中的高温热熔的温度控制在2000℃-2500℃之间,所述第一降低温度的温度控制在1600℃-2000℃之间,所述第二降低温度的温度控制在800℃-1500℃之间,所述升高温度的温度控制在1500℃-1800℃之间。
[0013]
优选的,所述s3中降低熔炉温度的无难度范围控制在500℃-800℃之间,且浇注模型设置成上窄下宽的梯形。
[0014]
优选的,所述s4中的急剧降温通过浇注模型底部的水冷管进行输送冷却水进行降温冷却,且冷却水的温度控制3℃-10℃之间,且钢材冷却时长为2-4h,使得钢材表面冷却至室温时进行脱模。
[0015]
优选的,所述s5中的淬火锻造需要将钢材加热至300℃-500℃之间,然后进行锻造捶打。
[0016]
优选的,所述s2中的常规元素质量百分比如下所示:c 0.12%~0.20%、si 0.02%~0.82%、mn 0.90%~1.40%、s≤0.019%和p<0.031%;常规合金元素质量百分比如下:cr 0.02%~0.10%、mo 0.20%~0.40%、al 0.5%~1%、cu 0.15%~0.25%和n 0.30%~0.40%;稀土元素质量百分比如下所示:v 0.03%~0.12%、nb 0.13%~0.20%、y 0.03%~0.08%和nd 0.02%~0.10%;其余含量为fe。
[0017]
优选的,所述常规元素质量百分比如下所示:c 0.16%、si 0.42%、mn 1.00%、s 0.009%和p 0.021%;所述常规合金元素质量百分比如下:cr 0.08%、mo 0.30%、al 0.8%、cu 0.20%和n 0.35%;所述稀土元素质量百分比如下所示:v 0.10%、nb 0.16%、y 0.05%和nd 0.08%;其余含量为fe。
[0018]
优选的,所述s2中的常规元素质量百分比如下所示:c 0.20%、si 0.82%、mn 1.40%、s 0.019%和p 0.031%;所述常规合金元素质量百分比如下:cr 0.10%、mo 0.40%、al 1%、cu 0.25%和n 0.40%;所述稀土元素质量百分比如下所示:v 0.12%、nb 0.20%、y 0.08%和nd 0.10%,其余含量为fe。
[0019]
优选的,所述s2中的常规元素质量百分比如下所示:c 0.12%、si 0.02%、mn 0.90%、s 0.001%和p 0.008%;所述常规合金元素质量百分比如下:cr 0.02%、mo 0.20%、al 0.5%、cu 0.15%和n 0.30%;所述稀土元素质量百分比如下所示:v 0.03%、nb 0.13%、y 0.03%和nd 0.02%;其余含量为fe。
[0020]
与现有技术相比,本发明的有益效果是:
[0021]
本发明通过在钢材内部的添加稀土元素实现对钢材内部进行改造,提高钢材的冶金质量和力学性能,提高钢材的强度、耐腐蚀性和耐磨性能,并且能够将钢材中的磷和氧气进行排放,降低钢材中的杂质含量,并且加工工艺的控制调节有效的实现对钢材的冶炼控制,使得钢材能够稳定的成型,保持内部结构的紧密型。
附图说明
[0022]
图1为本发明的工艺步骤示意图。
具体实施方式
[0023]
下面将结合本发明实施例中的附图,对本发明实施例中的技术方案进行清楚、完整地描述,显然,所描述的实施例仅仅是本发明一部分实施例,而不是全部的实施例。基于本发明中的实施例,本领域普通技术人员在没有做出创造性劳动前提下所获得的所有其他实施例,都属于本发明保护的范围。
[0024]
请参阅图1,本发明提供一种技术方案:
[0025]
实施例一:
[0026]
采用稀土处理和纯净化冶炼的高强韧稀土耐磨钢制备工艺,包括有以下制备步骤:
[0027]
s1:通过圆锥破碎机对矿石进行破碎;将常规元素矿石通过圆锥破碎机进行破碎处理,并且将常规合金元素矿石和稀土元素矿石进行粉碎,并且分别进行过筛处理;
[0028]
s2:将破碎后的元素矿石投放进入熔炉中进行融化;将破碎后的常规元素矿石按照比列投放进入到熔炉中进行高温热熔,进行热熔4-5h后,第一次降低温度,然后再将常规合金元素矿石按照比例投放进入到熔炉中进行热熔混合,且热熔时长为3,第二次降低温度,将稀土元素矿石按照比例投入到熔炉中进行热熔,升高温度,热熔时长为5;
[0029]
s3:降低熔炉温度进行浇注;在浇注模型的内壁上均匀的涂抹纳米活性炭,然后降低熔炉的温度,再将熔炉中的金属溶液通过浇注速率为20s浇注6m的速率进行浇注,并且在浇注过后立马在溶液上方铺设一层纳米活性炭;
[0030]
s4:降温冷却进行脱模;在浇注过后,并且使得溶液表层的纳米活性炭燃烧结束后,对浇注模具进行急剧的降温冷却,使得浇注模具中的溶液快速的进行冷却成型;
[0031]
s5:多次淬火锻造;通过锻造平台对冷却后的钢材进行加热,然后通过锻造锤进行捶打,使得钢材能够成型,且在捶打结束后进行淬火,并且对钢材至少进行淬火锻造三次,将钢材表面的纳米活性炭锤出,以及将钢材内部的杂质和空隙锻造排出。
[0032]
为了加快矿石的热熔速度,本实施例中,优选的,所述s1中的常规元素矿石的破碎后直径保持在10,所述常规合金元素矿石的破碎后直径保持在2,所述稀土元素矿石的破碎后直径保持在0.5。
[0033]
为了实现温度的精准控制,使得溶液内部的杂质能够减少,本实施例中,优选的,所述s2中的高温热熔的温度控制在2000℃,所述第一降低温度的温度控制在1600℃,所述第二降低温度的温度控制在800℃,所述升高温度的温度控制在1500℃。
[0034]
为了实现进行浇注,防止溶液流速过快,且为了防止溶液过度接触空气,本实施例中,优选的,所述s3中降低熔炉温度的无难度范围控制在500℃,且浇注模型设置成上窄下宽的梯形。
[0035]
为了实行快速的进行降温,使得钢材内部能够减少空气泡的存在,本实施例中,优选的,所述s4中的急剧降温通过浇注模型底部的水冷管进行输送冷却水进行降温冷却,且冷却水的温度控制3℃,且钢材冷却时长为2h,使得钢材表面冷却至室温时进行脱模。
[0036]
为了实现对钢材进行锻造,本实施例中,优选的,所述s5中的淬火锻造需要将钢材
加热至300℃,然后进行锻造捶打。
[0037]
其中,所述常规元素质量百分比如下所示:c 0.16%、si 0.42%、mn 1.00%、s 0.009%和p 0.021%;所述常规合金元素质量百分比如下:cr 0.08%、mo 0.30%、al 0.8%、cu 0.20%和n 0.35%;所述稀土元素质量百分比如下所示:v 0.10%、nb 0.16%、y 0.05%和nd 0.08%;其余含量为fe。
[0038][0039]
实施例二:
[0040]
采用稀土处理和纯净化冶炼的高强韧稀土耐磨钢制备工艺,包括有以下制备步骤:
[0041]
s1:通过圆锥破碎机对矿石进行破碎;将常规元素矿石通过圆锥破碎机进行破碎处理,并且将常规合金元素矿石和稀土元素矿石进行粉碎,并且分别进行过筛处理;
[0042]
s2:将破碎后的元素矿石投放进入熔炉中进行融化;将破碎后的常规元素矿石按照比列投放进入到熔炉中进行高温热熔,进行热熔5h后,第一次降低温度,然后再将常规合金元素矿石按照比例投放进入到熔炉中进行热熔混合,且热熔时长为4h,第二次降低温度,将稀土元素矿石按照比例投入到熔炉中进行热熔,升高温度,热熔时长为6h;
[0043]
s3:降低熔炉温度进行浇注;在浇注模型的内壁上均匀的涂抹纳米活性炭,然后降低熔炉的温度,再将熔炉中的金属溶液通过浇注速率为26s浇注8m的速率进行浇注,并且在浇注过后立马在溶液上方铺设一层纳米活性炭;
[0044]
s4:降温冷却进行脱模;在浇注过后,并且使得溶液表层的纳米活性炭燃烧结束后,对浇注模具进行急剧的降温冷却,使得浇注模具中的溶液快速的进行冷却成型;
[0045]
s5:多次淬火锻造;通过锻造平台对冷却后的钢材进行加热,然后通过锻造锤进行捶打,使得钢材能够成型,且在捶打结束后进行淬火,并且对钢材至少进行淬火锻造三次,将钢材表面的纳米活性炭锤出,以及将钢材内部的杂质和空隙锻造排出。
[0046]
为了加快矿石的热熔速度,本实施例中,优选的,所述s1中的常规元素矿石的破碎后直径保持在30cm,所述常规合金元素矿石的破碎后直径保持在10cm,所述稀土元素矿石的破碎后直径保持在2cm。
[0047]
为了实现温度的精准控制,使得溶液内部的杂质能够减少,本实施例中,优选的,所述s2中的高温热熔的温度控制在2500℃,所述第一降低温度的温度控制在2000℃,所述第二降低温度的温度控制在1500℃,所述升高温度的温度控制在1800℃。
[0048]
为了实现进行浇注,防止溶液流速过快,且为了防止溶液过度接触空气,本实施例中,优选的,所述s3中降低熔炉温度的无难度范围控制在800℃,且浇注模型设置成上窄下宽的梯形。
[0049]
为了实行快速的进行降温,使得钢材内部能够减少空气泡的存在,本实施例中,优选的,所述s4中的急剧降温通过浇注模型底部的水冷管进行输送冷却水进行降温冷却,且冷却水的温度控制10℃,且钢材冷却时长为4h,使得钢材表面冷却至室温时进行脱模。
[0050]
为了实现对钢材进行锻造,本实施例中,优选的,所述s5中的淬火锻造需要将钢材加热至500℃,然后进行锻造捶打。
[0051]
其中,所述常规元素质量百分比如下所示:c 0.20%、si 0.82%、mn 1.40%、s 0.019%和p 0.031%;所述常规合金元素质量百分比如下:cr 0.10%、mo 0.40%、al 1%、
cu 0.25%和n 0.40%;所述稀土元素质量百分比如下所示:v 0.12%、nb 0.20%、y 0.08%和nd 0.10%,其余含量为fe。
[0052]
实施例三:
[0053]
采用稀土处理和纯净化冶炼的高强韧稀土耐磨钢制备工艺,包括有以下制备步骤:
[0054]
s1:通过圆锥破碎机对矿石进行破碎;将常规元素矿石通过圆锥破碎机进行破碎处理,并且将常规合金元素矿石和稀土元素矿石进行粉碎,并且分别进行过筛处理;
[0055]
s2:将破碎后的元素矿石投放进入熔炉中进行融化;将破碎后的常规元素矿石按照比列投放进入到熔炉中进行高温热熔,进行热熔4.5h后,第一次降低温度,然后再将常规合金元素矿石按照比例投放进入到熔炉中进行热熔混合,且热熔时长为3.4h,第二次降低温度,将稀土元素矿石按照比例投入到熔炉中进行热熔,升高温度,热熔时长为5.6h;
[0056]
s3:降低熔炉温度进行浇注;在浇注模型的内壁上均匀的涂抹纳米活性炭,然后降低熔炉的温度,再将熔炉中的金属溶液通过浇注速率为26s浇注8m的速率进行浇注,并且在浇注过后立马在溶液上方铺设一层纳米活性炭;
[0057]
s4:降温冷却进行脱模;在浇注过后,并且使得溶液表层的纳米活性炭燃烧结束后,对浇注模具进行急剧的降温冷却,使得浇注模具中的溶液快速的进行冷却成型;
[0058]
s5:多次淬火锻造;通过锻造平台对冷却后的钢材进行加热,然后通过锻造锤进行捶打,使得钢材能够成型,且在捶打结束后进行淬火,并且对钢材至少进行淬火锻造三次,将钢材表面的纳米活性炭锤出,以及将钢材内部的杂质和空隙锻造排出。
[0059]
为了加快矿石的热熔速度,本实施例中,优选的,所述s1中的常规元素矿石的破碎后直径保持在20cm,所述常规合金元素矿石的破碎后直径保持在8cm,所述稀土元素矿石的破碎后直径保持在1cm。
[0060]
为了实现温度的精准控制,使得溶液内部的杂质能够减少,本实施例中,优选的,所述s2中的高温热熔的温度控制在2300℃,所述第一降低温度的温度控制在1800℃,所述第二降低温度的温度控制在1000℃,所述升高温度的温度控制在1600℃。
[0061]
为了实现进行浇注,防止溶液流速过快,且为了防止溶液过度接触空气,本实施例中,优选的,所述s3中降低熔炉温度的无难度范围控制在700℃,且浇注模型设置成上窄下宽的梯形。
[0062]
为了实行快速的进行降温,使得钢材内部能够减少空气泡的存在,本实施例中,优选的,所述s4中的急剧降温通过浇注模型底部的水冷管进行输送冷却水进行降温冷却,且冷却水的温度控制5℃之间,且钢材冷却时长为3h,使得钢材表面冷却至室温时进行脱模。
[0063]
为了实现对钢材进行锻造,本实施例中,优选的,所述s5中的淬火锻造需要将钢材加热至400℃,然后进行锻造捶打。
[0064]
其中,常规元素质量百分比如下所示:c 0.12%、si 0.02%、mn 0.90%、s 0.001%和p 0.008%;所述常规合金元素质量百分比如下:cr 0.02%、mo 0.20%、al 0.5%、cu 0.15%和n 0.30%;所述稀土元素质量百分比如下所示:v 0.03%、nb 0.13%、y 0.03%和nd 0.02%;其余含量为fe。
[0065]
本发明的工艺流程:
[0066]
第一步:通过圆锥破碎机对矿石进行破碎;将常规元素矿石通过圆锥破碎机进行
破碎处理,并且将常规合金元素矿石和稀土元素矿石进行粉碎,并且分别进行过筛处理;
[0067]
第二步:将破碎后的元素矿石投放进入熔炉中进行融化;将破碎后的常规元素矿石按照比列投放进入到熔炉中进行高温热熔,进行热熔4.5h后,第一次降低温度,然后再将常规合金元素矿石按照比例投放进入到熔炉中进行热熔混合,且热熔时长为3.4h,第二次降低温度,将稀土元素矿石按照比例投入到熔炉中进行热熔,升高温度,热熔时长为5.6h;
[0068]
第三步:降低熔炉温度进行浇注;在浇注模型的内壁上均匀的涂抹纳米活性炭,然后降低熔炉的温度,再将熔炉中的金属溶液通过浇注速率为26s浇注8m的速率进行浇注,并且在浇注过后立马在溶液上方铺设一层纳米活性炭;
[0069]
第四步:降温冷却进行脱模;在浇注过后,并且使得溶液表层的纳米活性炭燃烧结束后,对浇注模具进行急剧的降温冷却,使得浇注模具中的溶液快速的进行冷却成型;
[0070]
第五步:多次淬火锻造;通过锻造平台对冷却后的钢材进行加热,然后通过锻造锤进行捶打,使得钢材能够成型,且在捶打结束后进行淬火,并且对钢材至少进行淬火锻造三次,将钢材表面的纳米活性炭锤出,以及将钢材内部的杂质和空隙锻造排出。
[0071]
已经示出和描述了本发明的实施例,对于本领域的普通技术人员而言,可以理解在不脱离本发明的原理和精神的情况下可以对这些实施例进行多种变化、修改、替换和变型,本发明的范围由所附权利要求及其等同物限定。