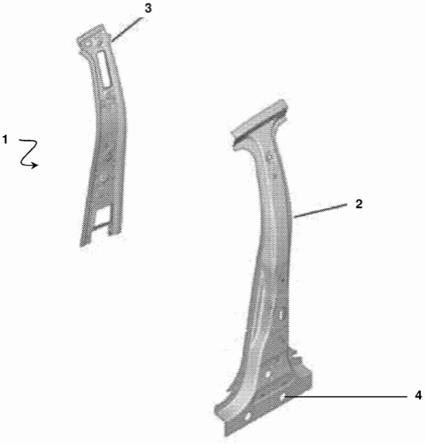
铝组件和具有包含硅、铁、锌和镁,余量为铝的合金涂层的压制硬化钢部件的组合件
1.本发明涉及基于铝的部件和压制硬化钢部件的组合件,所述压制硬化钢部件在其至少一个表面上设置有包含硅、铁、锌、任选的镁,余量为铝的合金涂层,所述压制硬化钢部件被放置成与基于铝的部件接触。
2.这些组合件例如旨在用于汽车车身部件例如门孔等的制造,然而不限于此。
3.对于车辆的复杂部件例如前保险杠横梁/后保险杠横梁、门加强件、横梁量加强件、中足加强件、底板加强件、通道加强件、顶棚纵向梁、顶板横梁,已知使用涂覆有基于铝的合金涂层的压制硬化钢部件。实际上,这样的经涂覆的压制硬化钢部件由于涂层的阻隔效果而确保了安全性和良好的耐腐蚀性。
4.寻求减轻重量以减少co2排放的持续需要导致需要寻求将特别是铝和涂覆有基于铝的合金涂层的压制硬化钢部件组合的混合解决方案。然而,这样的组合产生了两种材料的复杂且不断演变的腐蚀现象。
5.专利申请ep1669153公开了钢/铝焊接结构,所述结构包括:
6.‑
具有涂覆层和al
‑
fe
‑
si三元合金层的热浸镀al钢板,所述涂覆层按质量计由以下组成:3%至12%的si、0.5%至5%的fe,并且除了不可避免的杂质之外,余量为al,以及所述al
‑
fe
‑
si三元合金层在钢基底与涂覆层之间的界面处形成;以及
7.‑
点焊至镀al钢板的铝板或铝合金板;
8.‑
其中al
‑
fe二元合金层与整个al/fe接缝边界的面积比被控制在90%或更小,并且在al
‑
fe二元合金层与al
‑
fe
‑
si三元合金层之间存在无al
‑
fe合金的区域。
9.然而,热浸镀al钢板包括冷轧钢板,即,非压制硬化钢部件,用非压制硬化钢部件不可能生产复杂的部件。此外,随着时间的推移,该组合件的耐腐蚀性持续保持过低,因此存在对其进行改进的需要。
10.此外,已知压制硬化钢部件与铝板的组合件具有差的耐腐蚀性,因为钢使铝板的动力学腐蚀加速。
11.因此,本发明的目的是提供与现有技术的组合件相比具有优异的耐腐蚀性的压制硬化钢部件与基于铝的部件的组合件。
12.为此,本发明涉及根据权利要求1至4中任一项所述的组合件。
13.本发明涉及用于制造根据权利要求5至8中任一项所述的该组合件的方法。
14.本发明还涉及根据权利要求9或10所述的部件、根据权利要求11所述的车辆。
15.最后,本发明涉及根据权利要求12所述的组合件的用途。
16.现在将参照附图通过仅出于信息目的给出并且没有限制的指示性实例来对本发明进行举例说明,其中:
17.‑
图1示意性地表示根据本发明的组合件,以及
18.图2表示描绘了与根据现有技术的组合件相比,根据本发明的组合件内的铝板的最大腐蚀深度的演变的测量曲线。
19.名称压制硬化钢部件意指抗拉强度高至2500mpa并且更优选高至2000mpa的热成
型钢板或热冲压钢板。例如,抗拉强度高于或等于500mpa,有利地高于或等于1200mpa,优选高于或等于1500mpa。例如,钢选自:和
20.基于铝的元件的名称意指纯铝及其包含至少85重量%的铝的所有合金,其中包括1000系列至7000系列,所述1000系列至7000系列包括没有任何合金添加元素的铝和各种组成的合金:
21.‑
没有合金元素的铝:1000;
22.‑
铝+铜:2000;
23.‑
铝+锰:3000;
24.‑
铝+硅:4000;
25.‑
铝+镁:5000;
26.‑
铝+镁+硅:6000,以及
27.‑
铝+锌+镁:7000。
28.本发明涉及至少基于铝的元件2和压制硬化钢部件3的组合件1,所述压制硬化钢部件3在其至少一个表面上设置有包含以下的合金涂层:硅、铁、锌、任选的镁,余量为铝、不可避免的杂质以及可能的选自sb、pb、ti、ca、mn、sn、la、ce、cr、sr、ni或bi中的一种或更多种另外的元素,所述压制硬化钢部件3被接合至所述基于铝的元件2。
29.虽然经涂覆的压制硬化钢部件单独的电化学电位为
‑
0.68v至
‑
0.75v,即,非常接近于相对于饱和甘汞电极(sce)的为
‑
0.6v至
‑
0.78v的钢的电化学电位,导致坏的牺牲保护,但是与现有技术的组合件相比,根据本发明的组合件具有高的耐腐蚀性。本发明人发现在基于铝的元件与涂覆有包含硅、铁、锌、任选的镁,余量为铝的合金涂层的压制硬化钢部件之间存在协同作用。实际上,认为氧化物层存在于压制硬化钢部件的合金涂层的表面上。该氧化物层具有导致腐蚀动力学的降低和铝组件与压制硬化钢部件之间的电电流耦合的减少的阻隔效果。因此,尽管困难重重,组装区中的耐腐蚀性得到显著改善。
30.根据本发明,第一基于铝的元件可以采取板2的形式。该板2具有适合于根据本发明的组合件的后续用途的合适的尺寸。在一个优选的实施方案中,所讨论的组合件1为b柱。有利地,基于铝的板定位在车辆的外侧。
31.基于铝的板2还可以在其表面的至少一部分上包括一层或更多层保护涂层,例如磷酸盐化类型涂层和/或电泳类型涂层,例如通常施加在用于车辆的白车身上的那些。与第二压制硬化钢涂覆部件3的组装通常在使白车身通过包含诸如磷酸盐化涂料和/或电泳涂料的涂料类型的浴中之前进行。位于组装区外部的部件被涂覆。由于组装区内部的涂料的低渗透,因此组装区只能被部分涂覆。
32.因此,根据本发明的组合件的第二元件为在其至少一个表面上设置有合金涂层的压制硬化钢部件3,所述合金涂层按重量百分比计包含0.1%至15.0%的硅、15.0%至70%的铁、0.1%至20.0%的锌、0.1%至4.0%的镁,余量为铝、不可避免的杂质以及可能的选自sb、pb、ti、ca、mn、sn、la、ce、cr、ni、sr或bi中的一种或更多种另外的元素。
33.各另外的元素的按重量计的含量通常小于0.3%。另外的元素尤其可以提供改善钢元件上的涂层的延展性或粘合性的能力。知晓它们对涂层特性的影响的本领域技术人员将知晓根据另外的或补充的期望目标使用它们。
34.当使用热浸镀工艺时,涂层可能最终包含来源于例如涂覆浴的残余元素。其可能受到来源于进给锭或由使钢元件通过涂覆浴中产生的杂质污染。
35.优选地,压制硬化钢部件的合金涂层包含5.0重量%至14重量%的锌,例如7.0重量%至12.0重量%的锌。
36.优选地,压制硬化钢部件的合金涂层包含0.1重量%至6.0重量%的硅,例如2.0重量%至6.0重量%的硅。
37.优选地,压制硬化钢部件的合金涂层包含1.0重量%至4.0重量%的镁。
38.有利地,压制硬化钢部件的合金涂层包含40重量%至60重量%的铁。铁来源于进给锭或者由使钢元件通过涂覆浴中产生以及在奥氏体化处理期间由钢产生。
39.优选地,合金涂层包括金属间层fe3al和相互扩散层fe
‑
si
‑
al。
40.有利地,金属涂层的显微组织包含zn2mg相或mg2si相或两者。
41.金属涂层的厚度通常小于或等于30μm或甚至25μm且大于或等于3μm或甚至5μm。
42.如先前在上面所提及的,两个元件2、3以使得压制硬化钢部件3的涂覆表面与基于铝的元件2至少部分接触的方式组装。在一个优选的实施方案中,组装可以特别通过两个元件在位于图1中示出的示例中的组装区4中的粘合剂粘结、焊接、封接、压接、钩紧或铆接来完成。
43.例如,焊接可以通过点焊、激光烧蚀焊接或电弧焊接来进行。
44.这样的压接可以由所述元件中的一者围绕另一者的简单折叠组成,如图1所示,其中元件2被布置成包封元件3。当然可以进行本领域技术人员已知的任何其他类型的机械组装。
45.还可以通过利用粘合剂或结构密封剂的结构粘结来组装根据本发明的板,这使得能够实现这样的组合件:使得元件2、3中的一者或另一者所经受的机械应力转移至另一个元件3、2。粘合剂和/或密封剂的层非常薄(通常小于5mm,或者甚至小于1mm,并且甚至小于200μm),可以认为,这样的粘结组装相当于以与简单机械组装相同的方式使两个元件2、3接触。
46.很明显可能的是将结构粘结和机械组装组合以增强组合件的坚固性。
47.本发明还涉及用于制造根据本发明的组合件的方法,所述方法包括:
48.a.提供在至少一个表面上预涂覆有预涂层的钢板,所述预涂层按重量百分比计包含0.1%至20.0%的硅、0%至10%的铁、0.1%至25.0%的锌、0.1%至6.0%的镁,余量为铝、不可避免的杂质以及可能的选自sb、pb、ti、ca、mn、sn、la、ce、cr、ni或bi中的一种或更多种另外的元素,
49.b.将经预涂覆的钢板切割以获得坯件,
50.c.对坯件进行奥氏体化处理以在钢中获得完全奥氏体显微组织,
51.d.将坯件转移至压制工具中,
52.e.将坯件热成型,
53.f.将坯件冷却以获得在至少一个表面上设置有合金涂层的压制硬化钢部件(3),所述合金涂层包含硅、铁、锌、任选的镁,余量为铝、不可避免的杂质以及可能的选自sb、pb、ti、ca、mn、sn、la、ce、cr、ni或bi中的一种或更多种另外的元素,以及
54.g.将在至少一个表面上设置有所述合金涂层的压制硬化钢部件与基于铝的元件
组装。
55.例如,在步骤a)中,钢板可以通过热浸镀、通过物理气相沉积或者通过电沉积来预涂覆。优选地,钢板通过热浸镀来预涂覆。
56.之后,在步骤b)中将根据本发明的预涂覆有预涂层的钢板切割以获得坯件。
57.优选地,在步骤c)中,在炉中在非保护气氛下在800℃至1100℃,更优选800℃至1000℃并且有利地880℃至930℃的奥氏体化温度下向坯件施加奥氏体化处理。有利地,将所述坯件保持1分钟至12分钟,优选3分钟至9分钟的停留时间tm。在热成型之前的热处理期间,涂覆形成包含硅、铁、锌、任选的镁,余量为铝,并且对腐蚀、磨损、磨耗和疲劳具有高抗性的合金层。钢使铁扩散至预涂层中。
58.在步骤e)中,例如在600℃至900℃的温度下,坯件被转移至热成型工具中并进行热成型。热成型可以为热冲压或辊轧成型。优选地,对坯件进行热冲压。
59.在步骤f)中,然后部件在热成型工具中被冷却或者在转移至特定的冷却工具之后被冷却。
60.优选地,在步骤g)中,压制硬化钢部件(3)通过粘合剂粘结、通过焊接、通过封接、通过压接、通过钩紧或通过铆接接合至所述基于铝的元件(2)。
61.对于汽车应用,在磷酸盐化步骤之后,将部件浸入电涂覆浴中。通常,磷酸盐层的厚度为1μm至2μm,以及电涂层的厚度为15μm至25μm,优选小于或等于20μm。电泳层确保了另外的抗腐蚀保护。
62.在电涂覆步骤之后,可以沉积另外的涂料层,例如涂料的底漆涂层、底涂层和顶涂层。
63.在部件上施加电涂覆之前,预先将部件脱脂和磷酸盐化以确保电泳的附着性。
64.本发明涉及用于车辆的压制硬化钢部件,所述部件包括至少一个根据本发明的组合件1。
65.本发明涉及根据本发明的压制硬化钢部件,其为前横梁、后保险杠横梁、门加强件、挡风玻璃立柱加强件、b柱加强件、底板加强件和顶板加强件、顶板或前围板横向构件。
66.本发明涉及至少包括所述压制硬化钢部件的车辆。
67.最后,本发明涉及根据本发明的组合件用于制造压制硬化钢部件或车辆的用途。
68.为了强调通过使用根据本发明的组合件而获得的增强的性能,将与基于现有技术的组合件进行比较来详述实施方案的一些具体实施例。
实施例
69.由制成的钢板涂覆有如表1中收集的可变组成的锌合金或铝合金,在两侧上具有20μm的均匀厚度。然后将这样的钢板在900℃下压制硬化5分钟以获得具有如表2中所描述的合金组成的部件。然后用由铝aa6061制成的板和那些经涂覆的压制硬化部件来产生组合件样品。
70.根据规范sep1160,用粘合胶带将由铝aa6061制成的板和经涂覆的压制硬化钢部件接合,在组装区留出120μm的间隙。然后,将板的边缘用电线连接在一起以产生电
‑
电流耦合。在组装区中不存在涂层。
71.使铝板和压制硬化钢部件的组合件样品经受vda 233
‑
102测试,其规定使样品经
受一系列的处理循环,每个循环持续一周,各自具有一连串24小时的子循环a、b和c:
72.‑
循环a:包括通过在35℃下在盐喷雾的存在下放置的三小时时段的处理的循环;
73.‑
循环b:不具有在25℃到50℃之间变化的温度和在70%到95%之间变化的相对湿度下用盐喷雾处理的24小时的循环;
74.‑
循环c:不具有在
‑
15℃到50℃之间变化的温度和在70%到95%之间变化的相对湿度下用盐喷雾处理的24小时的循环。
75.所使用的盐水溶液为包含1重量%的氯化钠的水溶液。
76.在每个循环结束时,通过在样品的整个表面上方的激光三角测量绘图,然后提取以微米计的最大观察值来对第一样品进行铝元素的腐蚀蚀刻深度的测量。
77.6次循环和12次循环的结果总结并呈现在表3中,并且逐个循环的详细结果呈现在图2中。
78.表1
‑
钢板涂层组成在压制硬化之前的钢板具有以下涂层组成:
[0079][0080]
在900℃下压制硬化5分钟之后,钢部件被具有下表2中收集的组成的合金涂层覆盖。
[0081]
表2
‑
具有合金涂层组成的钢部件
[0082][0083]
*:根据本发明
[0084]
表3
‑
腐蚀的最大深度
[0085][0086]
*:根据本发明
[0087]
与试验1和2相比,根据本发明的试验3显示出高的耐腐蚀性的改善。