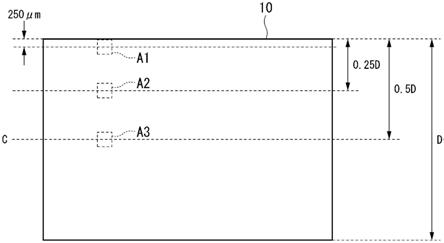
1.本发明涉及钢线以及热轧线材。
2.本技术基于2019年5月16日在日本提出的日本特愿2019
‑
092640号主张优先权,并引用其内容。
背景技术:3.由于冷锻在成型品的尺寸精度、生产性等方面优异,因此在钢制的螺栓、螺钉、螺母等机械部件的成型中,冷锻正在取代传统的热锻。此外,螺栓、螺母等部件多用于结构用途,因此添加c、mn、cr等合金元素以赋予其强度。
4.但是,如果合金元素含量增大,则钢材的变形抗力提高或延展性降低,因此存在在冷锻时对金属模具的负荷增大而发生金属模具的磨损、损伤,以及,成型部件上产生加工裂纹等问题。
5.此外,近年以部件制造成本的降低、部件的高功能化为目的,部件形状不断地复杂化。因此,要求冷锻中使用的钢材是软质的且具有极高的延性。因此,以往,为了提高加工性,通过对热轧材料进行球化退火等热处理而使其软质化。
6.冷锻用钢的加工性中包括影响金属模具负荷的变形抗力和影响加工裂纹的发生的延性。根据钢材的用途,所需的特性有所不同,但一般而言会需要变形抗力和延性两者,或其中一者。
7.在这样的背景下,作为提高钢材的冷锻性的技术,至今已提出了各种方法。
8.专利文献1中,公开了通过将铁素体粒的平均粒径为2~5.5μm、且长径为3μm以下、且长径比为3以下的渗碳体的比例相对于所有渗碳体为70%以上的区域设为距表面为线径的10%以上的区域,来提高冷加工性的技术方案。
9.专利文献2中,公开了通过将渗碳体间距离的标准偏差除以渗碳体间距离的平均值而得到的值设为0.50以下,即,通过使渗碳体间的间隔大致均匀,而冷锻时的变形抗力降低,且裂纹减少的钢线。
10.专利文献3中,公开了通过将铁素体粒的平均粒径设为15μm以上,将球状碳化物的平均粒径设为0.8μm以下,将最大粒径设为4.0μm以下,将每1mm2的个数设为0.5
×
106×
c%~5.0
×
106×
c%个,将粒径为0.1μm以上的球状碳化物间的最大距离设为10μm以下,而使得冷锻性优异。
11.现有技术文献
12.专利文献
13.专利文献1:日本特开2000
‑
73137号公报
14.专利文献2:日本特开2006
‑
316291号公报
15.专利文献3:国际公开第2011/108459号
技术实现要素:16.本发明所要解决的技术问题
17.专利文献1中公开的方法对于裂缝的发生位置出现在轧制线材的表面附近的加工中是的有效的,但对于裂缝的发生位置处于轧制线材内部的加工而言,加工性的提高效果很小。在实际的冷锻中,是在将轧制线材切断后进行冷锻。因此,轧制线材的表面附近并非裂缝的发生位置的情况很多,效果是局限的。
18.在专利文献2中公开的钢线中,影响变形抗力的铁素体粒径、渗碳体的个数密度并未被限定,变形抗力较高,存在在冷锻时金属模具负荷变高这样的问题。
19.专利文献3中公开的钢线的cr含量为0.20%以下,淬透性低,存在如果线径加大,则淬火回火后的部件的强度不稳定的问题。
20.此外,就冷锻中使用的以往的钢线而言,存在如果cr等合金元素的含量提高,则退火后渗碳体不会充分球化,变形抗力较高,容易产生加工裂纹的问题。
21.因此,本发明以提供一种含有合金元素、具有优异的冷锻性的钢线以及用于制造该钢线的热轧线材为目的。
22.解决技术问题的技术手段
23.用于解决所述问题的手段包含以下的方式:
24.<1>、一种钢线,其成分组成以质量%计为:
25.c:0.10~0.60%、
26.si:0.01~0.50%、
27.mn:0.20~1.00%、
28.p:0.030%以下、
29.s:0.050%以下、
30.cr:0.85~1.50%、
31.al:0.001~0.080%、
32.n:0.0010~0.0200%、以及
33.剩余部分:fe以及杂质元素,
34.在包含钢线的中心轴、且与所述中心轴平行的截面中,金属组织的95面积%以上由铁素体以及球状碳化物构成,
35.所述铁素体的平均粒径为10.0~30.0μm,
36.就所述球状碳化物而言,等效圆直径0.1μm以上的球状碳化物的平均长径比为2.5以下,并且,用[c]表示所述钢线中包含的c的含量(质量%)时,等效圆直径0.1μm以上的所述球状碳化物的个数为1.5
×
106×
[c]~7.0
×
106×
[c]个/mm2。
[0037]
<2>、根据<1>所述的钢线,其中,
[0038]
所述截面中,所述等效圆直径0.1μm以上的球状碳化物的平均粒径为0.50μm以下,并且,所述球状碳化物的最大粒径为3.00μm以下。
[0039]
<3>、根据<1>或<2>所述的钢线,其中,
[0040]
所述成分组成以质量%计,满足
[0041]
ti:0~0.050%、
[0042]
b:0~0.0050%、
[0043]
mo:0~0.50%、
[0044]
ni:0~1.00%、
[0045]
cu:0~0.50%、
[0046]
v:0~0.50%、
[0047]
nb:0~0.050%、
[0048]
ca:0~0.0050%、
[0049]
mg:0~0.0050%、以及
[0050]
zr:0~0.0050%中的1项或2项以上。
[0051]
<4>、一种热轧线材,其用于制造<1>~<3>中任一项所述的钢线。
[0052]
发明的效果
[0053]
根据本发明,可以提供一种含有合金元素、具有优异的冷锻性的钢线以及用于制造该钢线的热轧线材。
附图说明
[0054]
[图1]是说明对本发明涉及的钢线的l截面中铁素体粒的粒径进行测定的区域的概要图。
[0055]
本发明的具体实施方式
[0056]
以下将对作为本发明的一个例子的实施方式进行说明。
[0057]
需要说明的是,在本说明书中,用“~”表示的数值范围是指包含记载在“~”的前后的数值作为下限值及上限值的范围。此外,当记载在“~”的前后的数值处还记载有“超过”或“小于”时,数值范围是指不包含这些数值作为下限值或上限值的范围。
[0058]
在本说明书中,就阶段性记载的数值范围而言,某个阶段性的数值范围的上限值或下限值可以被其他的阶段性记载的数值范围的上限值或下限值置换,此外,也可以被实施例中所示的值置换。
[0059]
此外,成分组成的元素的含量有时表示为元素量(例如,c量、si量等)。
[0060]
此外,关于成分组成的元素的含量,“%”表示“质量%”。
[0061]
此外,“工序”一词,不单指独立的工序,即使在无法与其他工序进行明确区别的情况下,只要该工序能够达成期望的目的,那么该工序就包含在本用语中。
[0062]
此外,“包含钢线的中心轴、且与所述中心轴平行的截面”是指,包含钢线的中心轴、沿钢线的长度方向(即拉线方向)切断的、与中心轴方向平行的截面(也称为l截面)。
[0063]
此外,“中心轴”是指,通过与钢线的轴方向(长度方向)垂直的截面的中心点,在轴方向上延伸的假想的线。
[0064]
此外,“钢线的表层部”是指,从钢线的表面(外圆周面)出发,向着中心轴(朝向径方向),直至500μm深度的区域。
[0065]
此外,“数值xd”是指,将钢线的直径设为d时,从钢线的表面出发,向着中心轴(朝向径方向)的直径d的x倍的深度的位置。例如,“0.25d”表示直径d的0.25倍的深度的位置。
[0066]
本发明涉及的钢线是具有特定的成分组成并且具有满足下述(1)及(2)的金属组织的钢线。
[0067]
(1)l截面中,金属组织的95面积%以上由铁素体和球状碳化物构成。
[0068]
(2)所述铁素体的平均粒径为10.0μm以上,就所述球状碳化物而言,等效圆直径0.1μm以上的球状碳化物的平均长径比(以下,有时也简称为“球状碳化物的平均长径比”)为2.5以下,并且,l截面中每1mm2的个数为1.5
×
106×
[c]~7.0
×
106×
[c]个([c]表示钢线中包含的碳(c)的含量(质量%))。
[0069]
本发明涉及的钢线通过所述构成而成为冷锻性优异的钢线。本发明涉及的钢线是根据以下的发现而发明的。
[0070]
为了提高钢线的冷锻性,降低变形抗力、提高延性是有效的。因此,使用含有0.85%以上的cr的钢,就金属组织对变形抗力和延性的影响进行了探讨。其结果,发现铁素体粒径、碳化物的长径比以及碳化物的个数密度对变形抗力有影响。为了使变形抗力降低、获得良好的加工性,增大铁素体粒径、减小碳化物的个数密度是有效的。另一方面,还发现了碳化物的粒径和长径比会对延性产生影响。为了提高延性、抑制成型时的裂纹,减小碳化物的粒径和长径比是有效的。
[0071]
在现有的技术中,为了使含有0.10~0.60%的碳的中碳钢的铁素体粒粗粒化,需要加大球状碳化物的粒径、降低个数密度。一般而言,由于碳化物的粒径越小,铁素体粒径也越细粒化,因此要使铁素体粒的粗粒化和碳化物粒径的细小化同时实现是很困难的。特别是在cr含量高的钢中,由于cr固溶在碳化物中,碳化物的成长被抑制,要使铁素体粗粒化是很困难的。因此,在现有技术中,如果使碳化物细小化以提高延性,变形抗力就会变高,金属模具寿命会降低。
[0072]
本发明者们,通过对线材和钢线的制造方法进行改良,成功实现了以下的效果:即使是对于含有0.85%以上的cr的钢,也能够使铁素体粒的粗粒化和碳化物的细小化同时实现,同时达成变形抗力的降低和延性的提高。
[0073]
具体而言,本发明者们发现了为了在含有0.85%以上cr的钢中使得铁素体粒的粗粒化和碳化物的细小化同时实现,以下3点是很重要的:
[0074]
(a)将热轧材料的组织设为以先共析铁素体分率小的贝氏体为主体的组织;
[0075]
(b)在热轧后,通过总减面率20%以上的拉线加工等赋予钢线应变;
[0076]
(c)以ac1以下的温度进行球化退火。
[0077]
由此,实现了现有技术中难以实现的以下效果:使含有0.85~1.50%的cr,0.10~0.60%的c的钢的铁素体粒粗粒化、使碳化物细小化、且减小碳化物的长径比。通过得到这样的组织,达成了变形抗力的降低和延性的提高。
[0078]
作为包含由粗大的铁素体粒和细小的球状碳化物所构成的组织的钢线的冷锻性优异的理由,可以认为有以下几点:通过使容易成为成型裂纹的发生起点的粗大的碳化物、长径比较大的球状碳化物的粒径细小化,能够抑制龟裂的发生,并且通过使铁素体粒径粗粒化,可使得强度降低、变形抗力变小。
[0079]
并且,即使是cr等合金元素的含量高的组成,通过提高钢线的变形能力,本发明涉及的钢线也能够通过冷锻进行复杂形状部件的成型,制品出成率、生产性得到提高。此外,对本发明涉及的钢线而言,以往难以进行的具有高强度的复杂形状部件的一体成型也能够实现。也就是说,本发明涉及的钢线可适宜用于作为例如螺栓、螺钉、螺母等机械部件的原材料使用的机械结构用钢。
[0080]
由于本发明涉及的钢线能够抑制成型裂纹,因此有助于部件形状的复杂化带来的
高功能化、机械部件的生产性的提高,在产业上极为有用。
[0081]
以下,对本发明涉及的钢线的成分组成及金属组织具体地进行说明。
[0082]
<成分组成>
[0083]
本发明涉及的钢线的成分组成以质量%计,包含:c:0.10~0.60%、si:0.01~0.50%、mn:0.20~1.00%、p:0.030%以下、s:0.050%以下、cr:0.85~1.50%、al:0.001~0.080%、n:0.0010~0.0200%、以及剩余部分:fe以及杂质元素。
[0084]
但是,本发明涉及的钢线可以含有所述以外的元素以代替fe的一部分,成分组成以质量%计,例如,满足ti:0~0.050%、b:0~0.0050%、mo:0~0.50%、ni:0~1.00%、cu:0~0.50%、v:0~0.50%、nb:0~0.050%、ca:0~0.0050%、mg:0~0.0050%、以及zr:0~0.0050%中的1项或2项以上。ti、b、mo、ni、cu、v、nb、ca、mg以及zr为任意元素。也就是说,钢线可以不包含这些元素。
[0085]
以下,将就对钢线中包含的各元素量的范围进行限定的理由进行说明。
[0086]
(c:0.10~0.60%)
[0087]
c是为了确保作为机械部件的强度而含有的。c量如果小于0.10%,则难以确保作为机械部件所必要的强度。另一方面,c量如果超过0.60%,则延性、韧性以及冷锻性劣化。因此,将c量设为0.10~0.60%。c量可以设为0.15%以上、0.20%以上或0.25%以上。c量可以设为0.55%以下、0.50%以上或0.40%以下。
[0088]
(si:0.01~0.50%)
[0089]
si在发挥作为脱氧元素的功能的同时,对于赋予淬透性、提高回火软化耐性、赋予机械部件必要的强度而言是有效的元素。si量如果小于0.01%,则这些效果不充分。si量如果超过0.50%,则在机械部件的延性、韧性劣化的同时,钢线的变形抗力会上升,使冷锻性劣化。因此,si量设为0.01~0.50%。si量可以设为0.03%以上、0.05%以上或0.10%以上。si量可以设为0.35%以下、0.30%以下或0.25%以下。
[0090]
(mn:0.20~1.00%)
[0091]
mn对于赋予淬透性、赋予机械部件必要的强度而言是必要的元素。mn量如果小于0.20%,则效果不充分。mn量如果超过1.00%,则在机械部件的韧性劣化的同时,钢线的变形抗力会上升,使冷锻性劣化。因此,mn量设为0.20~1.00%。mn量可以设为0.25%以上、0.30%以上或0.35%以上。mn含量可以设为0.90%以下、0.85%以下或0.80%以下。
[0092]
(p:0.030%以下)
[0093]
p作为杂质而包含在钢线中。由于p在淬火回火后的机械部件的晶界处偏析,使韧性劣化,因此优选使其减少。因此,p量的上限设为0.030%。优选p量的上限为0.020%。更优选p量的上限为0.015%以下或0.012%以下。需要说明的是,p量的下限可以为0%(也就是说可以不含),但从降低脱p成本的观点出发,可以超过0%(或为0.0001%以上又或为0.005%以上)。
[0094]
(s:0.050%以下)
[0095]
s以mns等硫化物的形式包含在钢线中。这些硫化物可使钢线的切削加工性提高。s量如果超过0.050%,则会在使钢线的冷锻性劣化的同时,使淬火回火后的机械部件的韧性劣化。因此,s量的上限设为0.050%。优选s量的上限为0.030%。更优选s量的上限为0.015%或0.010%。需要说明的是,s量的下限可以为0%(也就是说可以不含),但从降低脱
s成本的观点出发,可以超过0%(或为0.0001%以上又或为0.005%以上)。
[0096]
(cr:0.85~1.50%)
[0097]
cr对于提高淬透性、赋予机械部件必要的强度而言是必要的元素。并且,通过含有cr,退火后的碳化物的形状会变为球状,使冷加工性提高。cr量如果小于0.85%,则效果不充分。cr量如果超过1.50%,则球化时间变长,在增加制造成本的同时,钢线的变形抗力会上升,使冷锻性劣化。因此,cr量设为0.85~1.50%。cr量可以设为0.87%以上、0.90%以上或0.95%以上。cr量可以设为1.40%以下、1.30%以下或1.20%以下。
[0098]
(al:0.001~0.080%)
[0099]
al在发挥作为脱氧元素的功能的同时,具有形成aln而使得奥氏体结晶粒细粒化,提高机械部件的韧性的效果。此外,al还具有使固溶n固定以抑制动态应变时效、降低变形抗力的效果。al量如果小于0.001%,则这些效果不充分。al量如果超过0.080%,则在效果饱和的同时,可能会降低制造性。因此,al量设为0.001~0.080%。al量可以设为0.010%以上、0.020%以上或0.025%以上。al量可以设为0.060%以下、0.050%以下或0.040%以下。
[0100]
(n:0.0010~0.0200%)
[0101]
n具有与al、ti、nb、v等形成氮化物,使奥氏体结晶粒细粒化,提高机械部件的韧性的效果。n量如果小于0.0010%,则氮化物的析出量不足,无法得到以上效果。n量如果超过0.0200%,则由于固溶n引起的动态应变时效,而使钢线的变形抗力变高,使加工性劣化。因此,n量设为0.0010~0.0200%。n量的范围可以设为0.0020%以上、0.0025%以上或0.0030%以上。n量可以设为0.0080%以下、小于0.0050%或0.0040%以下。
[0102]
本发明涉及的钢线,可以以提高以下记载的特性为目的,而含有ti:0~0.050%、b:0~0.0050%、mo:0~0.50%、ni:0~1.00%、cu:0~0.50%、v:0~0.50%、nb:0~0.050%、ca:0~0.0050%、mg:0~0.0050%、以及zr:0~0.0050%中的1种或2种以上。但是,即使不含有这些元素,本发明涉及的钢线也能够解决所述问题。因此,这些任意元素的含量的下限值为0%。
[0103]
(ti:0~0.050%)
[0104]
ti作为脱氧元素发挥功能。并且ti具有形成氮化物、碳化物,使奥氏体结晶粒细粒化,提高机械部件的韧性的效果;促进固溶b的生成,提高淬透性的效果和使固溶n固定以抑制动态应变时效,降低变形抗力的效果。ti量如果超过0.050%,则在这些效果饱和的同时,会生成粗大的氧化物或氮化物,可能会使机械部件的疲劳强度劣化。因此,ti量可以在超过0~0.050%的范围内含有。ti量可以设为0.005%以上或0.010%以上。ti量可以设为0.030%以下或0.025%以下。
[0105]
(b:0~0.0050%)
[0106]
b具有以固溶b的形式在晶界处偏析,使淬透性提高,赋予机械部件必要的强度的效果。另一方面,b量如果超过0.0050%,则会在晶界处生成碳化物,可能使拉线加工性劣化。因此,b量可以在超过0~0.0050%的范围内含有。b量可以设为0.0003%以上或0.0005%以上。b量可以设为0.0030%以下或0.0020%以下。
[0107]
(mo:0~0.50%)
[0108]
mo具有提高淬透性,赋予机械部件必要的强度的效果。另一方面,mo量如果超过0.50%,则在合金成本增加的同时,钢线的变形抗力上升,使冷锻性劣化。因此,mo量可以在
超过0~0.50%的范围内含有。mo量可以设为0.10%以上或0.15%以上。mo量可以设为0.40%以下或0.30%以下。
[0109]
(ni:0~1.00%)
[0110]
ni具有提高淬透性,赋予机械部件必要的强度的效果。另一方面,ni量如果超过1.00%,则合金成本会增加。因此,ni量可以在超过0~1.00%的范围内含有。ni量可以设为0.02%以上或0.10%以上。ni量可以设为0.50%以下或0.30%以下。
[0111]
(cu:0~0.50%)
[0112]
cu具有在提高淬透性,赋予机械部件必要的强度的同时提高耐腐蚀性的效果。另一方面,cu量如果超过0.50%,则合金成本会增加。因此,cu量可以在超过0~0.50%的范围内含有。cu量可以设为0.02%以上或0.10%以上。cu量可以设为0.40%以下或0.35%以下。
[0113]
(v:0~0.50%)
[0114]
v具有使碳化物vc析出,提高机械部件的强度的效果。另一方面,v量如果超过0.50%而含有,则合金成本会增加。因此,v量可以在超过0~0.50%的范围内含有。v量可以设为0.01%以上或0.05%以上。v量可以设为0.20%以下或0.15%以下。
[0115]
(nb:0~0.050%)
[0116]
nb具有使碳化物、氮化物析出,提高机械部件的强度的效果;使奥氏体结晶粒细粒化,提高韧性的效果;减少固溶n,使变形抗力降低的效果等。另一方面,nb量如果超过0.050%,则在这些效果饱和的同时,有可能使冷锻性劣化。因此,nb量可以在超过0~0.050%的范围内含有。nb量可以设为0.001%以上或0.005%以上。nb量可以设为0.030%以下或0.020%以下。
[0117]
(ca:0~0.0050%)
[0118]
(mg:0~0.0050%)
[0119]
(zr:0~0.0050%)
[0120]
ca、mg、zr可以以脱氧为目的而使用。这些元素具有使氧化物细小化,提高疲劳强度的效果。另一方面,这些元素各自的含量如果超过0.050%,则在效果饱和的同时,生成粗大的氧化物,有可能使疲劳特性劣化。因此,ca量、mg量以及zr量分别可以在超过0~0.050%的范围内含有。ca量、mg量以及zr量分别可以设为0.0001%以上、0.0005%以上。ca量、mg量以及zr量分别可以设为0.030%以下或0.020%以下。
[0121]
(剩余部分:fe以及杂质元素)
[0122]
在本发明涉及的钢线的成分组成中,剩余部分为fe及杂质元素。
[0123]
此处,杂质元素是指,例如原材料中包含的成分或制造的工序中意外混入的成分,是指并非有意使其含有的成分。并且,杂质元素还包含:虽然是有意使其含有的成分,但是是以不对钢线的性能造成影响的范围的量而含有的成分。
[0124]
作为杂质元素,例如,可以举出o等。o在钢线中作为al、ti等的氧化物而存在。o量如果高,则会形成粗大的氧化物,成为导致机械部件的疲劳强度降低的原因。因此,优选将o量抑制在0.01%以下。
[0125]
<金属组织>
[0126]
接下来,对于本发明涉及的钢线的金属组织的限定理由进行说明。
[0127]
在本发明涉及的钢线中,在包含钢线的中心轴、且与所述中心轴平行的截面(l截
面)中,金属组织的95面积%以上由铁素体和球状碳化物(球状渗碳体)构成。金属组织中如果含有马氏体组织、贝氏体组织、珠光体组织等,则在变形抗力增大的同时延性会降低,冷锻性会劣化,因此优选不含这些组织。因此,在本发明涉及的钢线中,包含钢线的中心轴、且与中心轴平行的截面(l截面)中,金属组织的97面积%以上、98面积%以上或99面积%以上可以由铁素体和球状碳化物(球状渗碳体)构成。需要说明的是,l截面中金属组织的95面积%以上由铁素体和球状碳化物构成是指,对l截面进行观察时,金属组织的95面积%以上由铁素体和球状碳化物形成。
[0128]
铁素体和球状碳化物的面积%通过以下的步骤求出。对包含钢线的中心轴并且与中心轴平行的截面(l截面)进行镜面研磨后,将样品浸渍到室温的硝酸酒精腐蚀液(5%硝酸+95%乙醇溶液)中20秒,使金属组织露出。使用该样品,通过扫描型电子显微镜(sem),以距离表面(钢线的外圆周面)的250μm深度部(表层部的深度方向的中央部位)、0.25d深度部(从钢线的表面出发,在朝向中心方向上为钢线的直径d的0.25倍的深度的部分)、0.5d深度部(钢线的中心部分)为中心,在深度方向上为90μm,在中心轴方向上为120μm的区域各取2视野,对总共6视野以1000倍的倍率进行照片拍摄。从得到的组织照片中,以肉眼观察标记马氏体、贝氏体、珠光体部,通过对拍摄照片进行图像解析(软件名:nireco制小型通用图像处理解析系统luzex_ap)得到马氏体、贝氏体以及珠光体的合计面积%。就铁素体和球状碳化物的面积%而言,可以通过将从拍摄视野整体中减去马氏体、贝氏体和珠光体的合计面积而得到的值视为铁素体和球状碳化物的面积,用该值除以拍摄视野的面积而得出。需要说明的是,将长径比(长轴/短轴)超过5.0的碳化物以层状存在的组织作为珠光体组织。
[0129]
(铁素体粒)
[0130]
‑
铁素体粒的平均粒径
‑
[0131]
铁素体粒的粗粒化使变形抗力降低,提高冷锻时的金属模具寿命。在铁素体粒的平均粒径小于10.0μm的情况下,变形抗力的降低效果小。因此,铁素体粒的平均粒径的下限可以设为10.0μm。铁素体粒的平均粒径的优选下限为11.5μm。铁素体粒的平均粒径的更优选下限为13.0μm。另一方面,如果试图获得超过30.0μm的铁素体粒径,则退火时间会变长,制造成本会增加。因此铁素体粒的平均粒径的上限设为30.0μm。优选铁素体粒的平均粒径的上限为20.0μm。
[0132]
‑
铁素体粒的测定方法
‑
[0133]
铁素体粒的平均粒径可以通过电子背散射衍射(ebsd:electron back scattering diffraction)法测定。具体而言,如图1所示,以距离包含钢线10的中心轴c并且与中心轴c平行的截面(l截面)的表面的250μm深度部(表层部的深度方向的中央部位)、0.25d深度部(从钢线的表面出发,在朝向钢线的中心的方向上为钢线的直径d的0.25倍的深度的部分)、0.5d深度部(钢线的中心部分)为中心,在深度方向(径方向)上为500μm,在中心轴方向为500μm的区域,也就是说,图1中a1、a2、a3所示的各自500μm见方的区域中,将测定步幅设为1.0μm,对区域内的各测定点处的bcc
‑
fe的晶体取向进行测定。此处,将取向差为15度以上的边界定义为铁素体晶界。并且,以被该铁素体晶界包围的5像素以上的区域作为铁素体粒。铁素体粒的平均粒径是使用作为以混粒为前提的粒集团的平均粒径求法的johnson
‑
saltykov的测定方法(参照“计量形态学”内田老鹤圃新社,s47.7.30发行,原著:r.t.dehoff.f.n.r biness.p189)而得到的。通过其对2个样品进行测定,将在合计6个测定
区域中测定的平均粒径的平均值作为铁素体粒的平均粒径。
[0134]
(球状碳化物)
[0135]
‑
球状碳化物的平均长径比
‑
[0136]
球状碳化物是指,以碳化物的长径/短径表示的长径比为5.0以下的渗碳体。如果球状碳化物的长径比(长径/短径)变大,则容易从受到应变的碳化物的周围产生裂缝而形成裂纹。特别是,等效圆直径0.1μm以上的球状碳化物的平均长径比如果超过2.5,则延性会降低,变得容易产生加工裂纹。因此,将等效圆直径0.1μm以上的球状碳化物的平均长径比的上限设为2.5。等效圆直径0.1μm以上的球状碳化物的平均长径比的优选上限为2.0。等效圆直径0.1μm以上的球状碳化物的平均长径比的更优选上限为1.8。
[0137]
‑
球状碳化物的最大粒径
‑
[0138]
只要满足上述的要件,球状碳化物的粒径就无特别限定。但是,球状碳化物的最大粒径会影响成型裂纹的产生。如果最大粒径变小,则能够防止从受到应变的碳化物的周围产生裂缝,能够进一步有效地防止钢线的裂纹。例如,如果球状碳化物的最大粒径为3.00μm以下,则延性进一步提高,进一步易于防止冷锻裂纹。因此,球状碳化物的最大粒径的上限可以设为3.00μm。球状碳化物的最大粒径的优选上限为2.00μm。球状碳化物的最大粒径的更优选上限为1.50μm。
[0139]
‑
球状碳化物的平均粒径
‑
[0140]
此外,如果将球状碳化物的平均粒径设为0.50μm以下,则延性进一步提高,进一步易于防止冷锻裂纹。因此球状碳化物的平均粒径的上限可以设为0.50μm。球状碳化物的平均粒径的优选上限为0.40μm。球状碳化物的平均粒径的更优选上限为0.32μm。
[0141]
需要说明的是,如果球状碳化物以外的渗碳体占全部渗碳体的面积率小于5%,则对冷锻性的影响较小,因此也可以含有小于5%的球状碳化物以外的渗碳体。需要说明的是,球状碳化物的平均粒径是指,球状碳化物的等效圆直径的个数平均。个数平均是在将等效圆直径小于0.1μm的球状碳化物除外的基础上计算的。
[0142]
‑
球状碳化物的个数密度
‑
[0143]
如果在包含钢线的中心轴、且与中心轴平行的截面(l截面)的每1mm2中,等效圆直径0.1μm以上的球状碳化物(在本说明书中,有时也称为“每1mm2的球状碳化物”)的个数小于1.5
×
106×
[c]个,则在冷锻时,可能发生在碳化物的周围产生裂缝,产生加工裂纹的情况。因此,将每1mm2的等效圆直径0.1μm以上的球状碳化物的下限设为1.5
×
106×
[c]个。此处,[c]表示,以质量%表示的钢线中的c含量。等效圆直径0.1μm以上的球状碳化物的每1mm2的个数的优选下限为3.0
×
106×
[c]个或3.5
×
106×
[c]个。
[0144]
另一方面,等效圆直径0.1μm以上的球状碳化物的每1mm2的个数如果超过7.0
×
106×
[c]个,则变形抗力会增加,使金属模具负荷增加。因此,将每1mm2的等效圆直径0.1μm以上的球状碳化物的上限设为7.0
×
106×
[c]个。等效圆直径0.1μm以上的球状碳化物的每1mm2的个数的优选上限为6.5
×
106×
[c]个或6.0
×
106×
[c]个。需要说明的是,“[c]”是指如上所述的钢线中包含的c含量(质量%),例如如果c含量为0.35质量%,则[c]=0.35。后述计算ac1温度的公式中的[mn]、[si]、[cr]也是同样,分别表示钢材中的各元素的含量(质量%)。
[0145]
‑
球状碳化物的测定方法
‑
[0146]
球状碳化物的最大粒径、球状碳化物的平均粒径、球状碳化物的长径比、球状碳化物的个数密度,通过对扫描型电子显微镜(sem)照片进行图像解析而求出。
[0147]
具体而言,对包含钢线的中心轴、且与所述中心轴平行的截面(l截面)进行镜面研磨后,将样品浸渍在室温的苦味酸酒精腐蚀液(5%苦味酸+95%乙醇溶液)中50秒,使金属组织露出。接下来,通过sem,以距离钢线的表面的250μm深度部(表层部的深度方向上的中央部位)、0.25d深度部、以及0.5d深度部作为测定视野的中心,以5000倍的倍率对深度方向上为20μm、中心轴方向上为25μm的区域的各5视野,共计15视野的金属组织进行照片拍摄。通过对拍摄照片进行图像解析(软件名:nireco制小型通用图像处理解析系统luzex_ap)可以求出球状碳化物的所述各参数。
[0148]
将0.1μm以上的球状碳化物的等效圆直径的个数平均作为球状碳化物的平均粒径,将测定视野中的最大粒径作为球状碳化物的最大粒径。球状碳化物的等效圆直径是指,具有与球状碳化物的面积相等面积的圆的直径。0.1μm以上的球状碳化物的长径比通过长轴的长度/短轴的长度而求出。球状碳化物的个数密度通过等效圆直径0.1μm以上的球状碳化物的个数除以测定视野的面积而求出。
[0149]
<钢线的制造方法>
[0150]
以下将对本发明涉及的钢线的制造方法的一个例子进行说明。但是,以下说明的钢线的制造方法并不限制本发明涉及的钢线。即,无关其制造方法,满足上述的要件的钢线即为本发明涉及的钢线。
[0151]
本发明涉及的钢线的制造方法的一个例子具备:
[0152]
将以贝氏体为主体的线材,以总减面率20~50%进行拉线加工的工序;和
[0153]
将拉线加工后的线材,在650℃以上ac1温度(℃)以下保持3小时以上并冷却,以进行退火的工序。
[0154]
在该钢线的制造方法中,可以如下制造以贝氏体为主体的线材:
[0155]
将具有所述本发明涉及的钢线的成分组成的钢片加热至950~1150℃的工序;
[0156]
将加热后的钢片,在终轧温度850~1000℃下进行热轧以得到线材的工序;
[0157]
热轧后,将850~1000℃的线材冷却至400~小于500℃的温度范围的工序,其中将从850℃至550℃的平均冷却速度设为30~250℃/s;
[0158]
将冷却后的线材,保持在400℃~小于500℃的温度范围内20秒以上的工序(第一保持工序);以及
[0159]
进一步,将经过第一保持工序的线材,保持在500℃~600℃的温度范围内30秒以上的工序(第二保持工序)。
[0160]
以下,将对各工序详细地进行说明。
[0161]
(加热工序)
[0162]
在加热工序中,将具有所述本发明涉及的钢线的成分组成的钢片,加热至950~1150℃。加热温度如果小于950℃,则热轧时的变形抗力增大,轧制成本升高。加热温度如果超过1150℃,则表面的脱碳会变得显著,使最终制品的表面硬度降低。
[0163]
(热轧工序)
[0164]
在热轧工序中,将加热后的钢片以终轧温度850~1000℃进行热轧。如果终轧温度小于850℃,则铁素体粒会细粒化,无法在退火工序后得到铁素体粒的平均粒径为10.0~
30.0μm的组织。终轧温度如果超过1000℃,则第一保持工序中的转化完成时间变长,制造成本增加。需要说明的是,终轧温度是指,精轧刚结束后的线材的表面温度。
[0165]
(冷却工序)
[0166]
冷却工序中,在热轧后,将850~1000℃的线材冷却至400~小于500℃的温度范围,其中将从850℃至550℃的平均冷却速度设为30~250℃/s。例如,将热轧后的线材卷成环状,浸渍在熔融盐槽中以达到所述平均冷却速度即可。平均冷却速度如果小于30℃/s,则容易导致退火工序后铁素体和球状碳化物的面积率降低、球状碳化物的个数密度降低。另一方面,要使平均冷却速度达到250℃/s以上,制造成本会升高。需要说明的是,冷却速度是指,线材的表面冷却速度。从850℃到550℃的平均冷却速度是指,将300℃(=850℃
‑
550℃)除以将线材的表面温度从850℃降至550℃所需要的时间而得到的值。
[0167]
(第一保持工序)
[0168]
在第一保持工序中,将冷却后的线材保持在400℃~小于500℃20秒以上。保持温度如果小于400℃,则退火工序后的强度变高,使冷锻性劣化。保持温度如果为500℃以上,则第一保持工序中的转化完成时间显著变长,在第一保持工序及第二保持工序后会有未转化部分残存。未转化部分会导致在拉线加工工序中发生断线,且使退火工序后的冷锻性劣化。
[0169]
第一保持工序中的保持时间如果小于20秒,则在第一保持工序后及第二保持工序后会有未转化部分残存,导致在拉线加工工序中发生断线,且使退火工序后的冷锻性劣化。从制造成本的观点出发,保持时间的上限可以为120秒。第一保持工序,例如,可以通过将线材浸渍到熔融盐槽中来实施。
[0170]
(第二保持工序)
[0171]
在第二保持工序中,将经过了第一保持工序的线材保持在500℃~600℃30秒以上。保持温度如果小于500℃,则线材的强度较高,因此会导致在拉线加工工序中发生断线。保持温度如果为600℃以上,则制造成本增加。从制造成本的观点出发,保持时间的上限可以为150秒。第二保持工序,例如,可以通过将其浸渍到熔融盐槽中来实施。
[0172]
第二保持工序后,冷却至室温的线材具有先共析铁素体和珠光体被抑制并且以贝氏体为主体的组织。具体而言,线材的组织的c截面中测定的贝氏体的面积率为50%以上、马氏体的面积率为0%以上。线材的c截面中,马氏体的面积率也可以是0%,优选为超过0%。本发明者们发现,通过对线材的组织进行这样的控制,可使球化退火后的延性提高。其理由推定如下。
[0173]
使用碳含量为0.50%以下的亚共析钢,以通常的方法进行热轧、冷却而制造的线材的组织为铁素体及珠光体的混合组织。在这样的混合组织中,钢中的碳会在珠光体部中不均匀分布。因此,球化退火后,碳化物在退火前在珠光体所在的部分不均匀分布,使延性降低。如果以铁素体被抑制的贝氏体组织或马氏体组织作为线材的组织,则钢中的碳均匀地分布,因此球化退火后碳化物会均匀地分散,使延性提高。由于马氏体会使球化退火后的碳化物细小化,因此对延性的提高是有效的,但另一方面,也会使退火后的铁素体粒径细粒化,使变形抗力增大。因此,为了使球化退火后的钢线的延性提高且使变形抗力降低,将以贝氏体为主体的组织作为线材的组织是有效的。
[0174]
需要说明的是,本发明中的贝氏体与珠光体同样,包含铁素体相(α)和渗碳体相
(fe3c)。但是,珠光体是铁素体相和渗碳体交替连续地以层状叠层的组织。另一方面,贝氏体是在粒内包含细条(针状的下部组织),且分散有粒状或针状的碳化物的组织。在这一点上,珠光体和贝氏体有所区别。
[0175]
线材的贝氏体、铁素体以及马氏体的各个面积率(面积%)通过以下的步骤确定。
[0176]
首先,对作为测定对象的线材(以下有时也称为“对象物”)的c截面进行镜面研磨后,将对象物浸渍到室温的苦味酸酒精腐蚀液(5%苦味酸+95%乙醇溶液)中50秒,使组织露出。
[0177]
接下来,对对象物的c截面中的9个点,使用扫描型电子显微镜(sem)拍摄倍率为1000倍的组织照片。9个测定点的具体的位置如下。以下,对象物的直径以d表示。
[0178]
(1)表层部中的4点
[0179]
将从该对象物的表面出发,深度为250μm的深度位置(表层部的深度方向上的中央部位)处的、对象物的周向上以90
°
间隔的4点,作为表层部中的测定点。视野形状设为深度方向上的长度为80μm、周向上的长度为120μm的长方形,使视野的中心与上述的测定位置一致。
[0180]
(2)0.25d的深度位置处的4点
[0181]
将从该对象物的表面出发,深度为0.25d的深度位置处的、对象物的周向上以90
°
间隔的4点,作为0.25d的深度位置处的测定点。视野形状设为深度方向上的长度为80μm、周向上的长度为120μm的长方形,使视野的中心与上述的测定位置一致。
[0182]
(3)中心轴处的1点
[0183]
将与中心轴重叠的部分(从表面出发,深度为0.5d的深度位置)的1点作为中心轴处的测定点。视野形状设为以中心轴为中心的长宽80μm的正方形。
[0184]
本发明中,在拍摄到的组织照片中,以(长轴的长度)/(短轴的长度)为5.0以上的渗碳体以及铁素体交替连续地以层状叠层,且这些层之间不含有粒状或针状的渗碳体的组织作为珠光体。需要说明的是,珠光体包含疑似珠光体。疑似珠光体是指,分裂的渗碳体以列状排列,列间不含有粒状或针状的碳化物,并且,粒内不含有细条(针状的下部组织)的组织。贝氏体则是粒内包含细条,并且细条间或细条内分散有粒状或针状的碳化物的组织。
[0185]
此外,拍摄到的组织照片中的贝氏体、铁素体、马氏体、珠光体、奥氏体以及先共析渗碳体的各个组织是通过肉眼观察标记的。并且,各组织的区域的面积通过图像解析(软件名:nireco制小型通用图像处理解析系统luze x_ap)求出。需要说明的是,上述的一系列操作至少对于2个样品进行,对这些样品中的组织的面积率进行测定和计算,求出它们的平均值,以该平均值作为本发明中的线材的各组织的面积%。
[0186]
需要说明的是,如果难以判别铁素体和马氏体,则以以下说明的方法进行判别。在对象物的c截面上施加压痕以使得能够判别观察位置,浸渍到室温的苦味酸酒精腐蚀液中50秒,使组织露出并拍摄组织照片。然后,对对象物进行再研磨,浸渍到室温的硝酸酒精腐蚀液(5%硝酸+95%乙醇溶液)中20秒,使组织露出。并且,使用sem,以倍率1000倍拍摄与苦味酸酒精腐蚀液蚀刻照片同一处的组织照片。
[0187]
将苦味酸酒精腐蚀液蚀刻照片与硝酸酒精腐蚀液蚀刻照片进行比较,将被硝酸酒精腐蚀液腐蚀,但苦味酸酒精腐蚀液的腐蚀较弱的区域判定为马氏体,将硝酸酒精腐蚀液、苦味酸酒精腐蚀液的腐蚀都弱的区域判定为铁素体。并且,以上述的方法通过肉眼观察对
各组织的区域进行标记,通过图像解析求出各组织的面积%。
[0188]
如果难以判别贝氏体和疑似珠光体,则以以下说明的方法进行判别。对作为测定对象的线材或钢线的c截面进行镜面研磨。接下来,浸渍到室温的硝酸酒精腐蚀液中20秒,使组织露出。然后,使用sem以倍率5000倍拍摄c截面中的9个区域内全域的组织照片。将粒内存在细条(针状的下部组织),并且存在粒状或针状碳化物的组织判定为贝氏体。需要说明的是,“c截面中的9个区域”是指,上述的(1)表层部中的4点、(2)0.25d的深度位置处的4点、以及(3)中心轴处的1点。
[0189]
(拉线加工工序)
[0190]
在拉线加工工序中,在第二保持工序后,将冷却至室温的线材,以总减面率20~50%进行拉线加工。通过进行拉线加工,能够在退火工序时促进碳化物的球化的同时,促进铁素体粒的成长。拉线加工时的总减面率如果小于20%,则这些效果不充分,冷锻性会劣化。即使总减面率超过50%,也可能效果饱和,且钢线直径变小,而用途被制限。
[0191]
需要说明的是,本发明涉及的钢线直径(直径)无特别限制,根据用途决定即可,例如,用作螺栓、螺钉、螺母等机械部件的原材料时,例如,可以进行使其成为直径为3.5~16.0mm的钢线的拉线加工。
[0192]
(退火工序)
[0193]
在退火工序中,将通过拉线加工得到的钢线,保持在650℃以上ac1温度(℃)以下3小时以上并冷却。此处,ac1=723
‑
10.7
×
[mn]+29.1
×
[si]+16.9
×
[cr]。退火温度如果小于650℃,则铁素体粒的平均粒径变得小于10μm,使冷锻性劣化。退火温度如果超过ac1,则铁素体粒的平均粒径变得小于10μm,并且,存在碳化物的个数减少,使冷锻性劣化的可能性。保持时间如果小于3小时,则铁素体粒的平均粒径变得小于10μm,使冷锻性劣化。
[0194]
通过所述工序,能够适宜地制造本发明涉及的钢线。但是,如上所述,本发明涉及的钢线的制造方法没有特别限制。由所述工序构成的钢线的制造方法不过是用于获得本发明涉及的钢线的一个适宜的例子。
[0195]
接下来,对本发明涉及的线材进行说明。本发明涉及的线材是用于制造本发明涉及的钢线的热轧线材。用线材制造钢线时,其化学成分不变化。因此,本发明涉及的线材必然具有与本发明涉及的钢线几乎相同的化学成分。另一方面,只要是经过任意的加工(例如拉线加工、热处理等)而得到本发明涉及的钢线,就对本发明涉及的线材的金属组织以及球状碳化物的各方式等没有特别限制。就线材金属组织的优选的一个例子而言,其c截面中,贝氏体的面积率为50%以上,马氏体的面积率为0%以上。对于具有这样的金属组织线材,可以通过以总减面率20%以上的拉线加工等赋予钢线应变,并以ac1以下的温度进行球化退火,而得到本发明涉及的钢线。
实施例
[0196]
以下,对于本发明的钢线,将举出实施例更具体地进行说明。但是,这些实施例并不限制本发明的钢线。
[0197]
[钢线的制造]
[0198]
使用具有表1所示的成分组成的钢种a~p的钢片,以后述的表2
‑
1~表4
‑
2所示的条件,如下地制造了钢线。需要说明的是,表1中以
“‑”
表示的部分,代表没有有意地添加该
栏中的元素。
[0199]
此外,表2
‑
1~表4
‑
2中,下划线部分表示不在本发明中所要求的范围内或不在任选的优选范围内。
[0200][0201]
具体而言,表2
‑
1~表2
‑
4所示的试验编号1~16、32~36、41的钢线是如下制造的。
[0202]
首先,将钢片加热后,进行热轧,将得到的线材卷成环状,浸渍到设置于热轧线后
方的熔融盐槽中,冷却至470~520℃。
[0203]
接下来,使在熔融盐槽中浸渍了的线材在两个槽的熔融盐浴中进行第一保持及第二保持。然后,将冷却至室温(25℃)的线材以表2
‑
1及表2
‑
2所示的总减面率进行拉线加工,在拉线后加热并进行了退火处理。需要说明的是,试验编号1~12、15、32、35的钢线的退火处理是保持在710℃5小时后进行空冷,试验编号16的钢线的退火处理是保持在760℃5小时后进行空冷,试验编号33的钢线的退火处理是保持在740℃5小时后进行空冷,试验编号34的钢线的退火处理是保持在695℃5小时后进行空冷,试验编号36的钢线的退火处理是保持在730℃5小时后进行空冷,试验编号41的钢线的退火处理是保持在735℃5小时后进行空冷。
[0204]
通过这些工序,制造了试验编号1~16、32~36所示的钢线。需要说明的是,试验编号13和14的钢线在拉线中途出现断线,因此没有进行退火处理。表2
‑
1及表2
‑
2中关于制造条件的栏的
“‑”
表示没有实施,关于组织的
“‑”
表示没有测定。
[0205]
试验编号31的钢线是如下制造的。
[0206]
首先,将钢片加热后,进行热轧,将得到的线材卷成环状,通过鼓风冷却冷却至470℃。然后,将得到的线材浸渍到两个槽的熔融盐槽中进行第一保持及第二保持。然后,将冷却至室温(25℃)的线材以表2
‑
2所示的总减面率进行拉线加工,拉线后保持在710℃5小时,之后进行了空冷。
[0207]
此外,表2
‑
1~表2
‑
4所示的试验编号17~28、37~40的钢线是如下制造的。
[0208]
首先,将钢片加热后,进行热轧,将得到的线材卷成环状,进行鼓风冷却。然后,将冷却至室温(25℃)的线材以表2
‑
1以及表2
‑
2所示的总减面率进行拉线加工,拉线后加热并进行了退火处理。需要说明的是,就试验编号17~28、37~40的钢线的退火处理是保持在760℃5小时后,以冷却速度15℃/h冷却至660℃,然后进行空冷。
[0209]
通过这些工序,制造了试验编号17~28、37~40所示的钢线。
[0210]
此外,表3
‑
1以及表3
‑
2所示的试验编号29的钢线是如下制造的。
[0211]
将钢片加热后,进行热轧,将得到的线材卷成环状,进行鼓风冷却。然后,将冷却至室温(25℃)的线材加热至850℃并淬火,加热至650℃并回火。然后,以表3
‑
1所示的总减面率进行拉线加工,拉线后加热并进行了退火处理。
[0212]
此外,表4
‑
1以及表4
‑
2所示的试验编号30的钢线是如下制造的。
[0213]
将钢片加热后,进行热轧,将得到的线材卷成环状,进行鼓风冷却。然后,将冷却至室温(25℃)的线材加热,进行了第一退火处理。然后,将冷却至室温(25℃)的线材以表4
‑
1所示的总减面率进行拉线加工,在拉线后加热进行了第二退火处理。需要说明的是,第一退火处理及第二退火处理是保持在760℃5小时后,以冷却速度15℃/h冷却至660,然后进行空冷。
[0214]
[评价]
[0215]
就这些钢线而言,对于在拉线加工中出现了断线的试验编号13、14以外的钢线进行了金属组织的观察,并进行了压缩试验。
[0216]
钢线的铁素体和球状碳化物的合计面积率、平均铁素体粒径、球状碳化物的平均长径比、等效圆直径0.1μm以上的球状碳化物的个数密度、等效圆直径0.1μm以上的球状碳化物的平均粒径(表中,记载为“平均粒径”)以及等效圆直径0.1μm以上的球状碳化物的最
大粒径(表中,记载为“最大粒径”)是依照前面所述的方法进行测定的。结果如表所示。需要说明的是,表中的“个数/c%”是将各钢线的l截面每1mm2中观察到的等效圆直径0.1μm以上的球状碳化物的个数除以该钢线中包含的c含量(%)所得的值。
[0217]
钢线的变形抗力和极限压缩率通过压缩试验测定。
[0218]
将退火后的钢线以减面率8%进行拉线加工,由拉线后的钢线制作了直径d、高度1.5d的圆柱状的试验片。
[0219]
压缩试验方法是基于日本塑性加工学会冷锻分科会基准(塑性和加工,vol.22,no.211,1981,p139),以同心圆状且有凹槽的金属模具固定住端面,而进行压缩试验。
[0220]
变形抗力设为根据小坂田的方法(k.osakada:ann.cirp,30
‑
1(1981),p135),以等效应变1.6、压缩率73.6%的条件加工时的等效应力。
[0221]
就极限压缩率而言,使用由所述拉线后钢线以机械加工制作的直径5.0mm、高度7.5mm的圆柱状试验片在外周部轴方向上具有曲率0.15mm、深度0.8mm、角度30
°
的缺口的试验片,进行了压缩试验。观察到长度0.5mm以上的裂纹时认定为产生裂纹,以不产生裂纹的最大的压缩率作为极限压缩率。
[0222]
[0223]
[0224]
[0225]
[0226]
[0227]
[0228]
[0229][0230]
表中表示了变形抗力和极限压缩率的测定结果,并且,还表示了与通常钢线(试验编号17~28及37~40)的比较结果。变形抗力和/或极限压缩率记载为“同等”的试验编号的钢线是与通常钢线(试验编号17~28及37~40)相比,变形抗力在
±
20mpa以内和/或极限压缩率在
±
2%以内。记载为“良”的试验编号的钢线具有比通常钢线更优异的特性,记载为“不良”试验编号的钢线的特性比通常钢线差。
[0231]
从所述结果中可以看出,满足本发明限定的所有要件的试验编号1~12、33~36以及41的钢线的变形抗力与通常钢线(试验编号17~28及37~40)相比为同等或更优。并且,满足本发明限定的所有要件的试验编号1~12、33~36以及41的钢线的极限压缩率与通常钢线相比更优。需要说明的是,关于这些钢线中的一部分,对拉线前的组织(即线材的组织)进行评价的结果,确认了其具有贝氏体主体的组织(参照后述表5)。
[0232]
通常钢线17~28及37~40是在推测其拉线前的组织不会是以贝氏体为主体的组织的制造条件下进行制造的。关于这些通常钢线的一部分,对拉线前的组织(即线材的组织)进行了评价的结果,确认了其并非贝氏体主体(参照后述的表5)。
[0233]
在试验编号13中,由于拉线中出现了断线,因此未能制造钢线。推测这是因为第一保持工序中的保持温度过高而导致拉线前的线材的硬度过剩。
[0234]
钢线14中,由于拉线中出现了断线,因此未能制造钢线。推测这是因为第一保持工序中的保持时间过短而导致拉线前的线材的硬度过剩。
[0235]
在试验编号15的钢线中,铁素体以及球状碳化物的合计面积率不足,且铁素体的平均粒径过小,因此变形抗力及极限压缩率比通常钢线差。推测这是因为拉线加工中的总减面率不足。
[0236]
在试验编号16的钢线中,等效圆直径0.1μm以上的球状碳化物的个数不足,且铁素体的平均粒径过小,因此变形抗力及极限压缩率没有比通常钢线更加优异。推测这是因为拉线加工后的退火中的退火温度超过了ac1点。
[0237]
在试验编号31的钢线中,铁素体以及球状碳化物的合计面积率不足,且等效圆直径0.1μm以上的球状碳化物的个数不足,因此变形抗力及极限压缩率没有比通常钢线更优异。推测这是因为精轧后的平均冷却速度不足。
[0238]
在试验编号32的钢线中,铁素体以及球状碳化物的合计面积率不足,且铁素体的平均粒径过小,因此变形抗力比通常钢线差,极限压缩率没有比通常钢线更优异。推测这是因为没有进行第二保持工序。
[0239]
此外,关于全部的发明范围内的实施例钢线以及一部分的发明范围外的比较例钢线,对作为其原材料的线材的金属组织也进行了评价。评价方法如本说明书中所述。评价结果如表5所示。
[0240]
[表5]
[0241][0242]
作为满足本发明中限定的所有要件的试验编号1~12、33~36、41的钢线的材料的线材,在拉线加工前的阶段,c截面中的贝氏体的面积率为50%以上,马氏体的面积率为0%以上。
[0243]
另一方面,在拉线加工时发生断线的试验编号13以及14的线材中,贝氏体量不足,并且马氏体量较大。
[0244]
在球状碳化物的平均长径比超过本发明的上限,并且球状碳化物的个数密度小于本发明的下限的钢线所涉及的试验编号19的线材中,不含有贝氏体及马氏体双方。
[0245]
在平均铁素体粒径小于本发明的下限的钢线所涉及的试验编号22及24的线材中,虽然包含贝氏体及马氏体双方,但其量不足。
[0246]
符号的说明
[0247]
10 钢线
[0248]
c 中心轴
[0249]
d 钢线的直径。