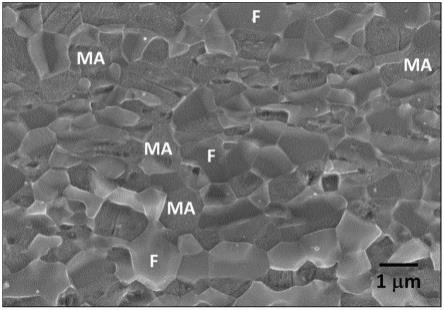
制备可冷成形的高强度钢带的方法和钢带
1.本发明涉及制备用于制造钢制品的可冷成形的涂覆或未涂覆的高强度钢带的方法和这样的钢带。
2.钢片材的冷成形或冷冲压或冷压成形是在制造工业例如汽车、建筑、工程、基础设施等中制备钢部件用于各种应用的方法。已知钢片材的可冷成形性随着钢强度提高而降低。对于常规的钢片材以及第一代先进高强度钢(ahss)尤其如此。
3.由于钢强度和伸长率的这种反比例关系,这些钢材的拉伸强度和伸长率的性质分布有时被称作“香蕉图”。然而,可使用所谓的第二代ahss(2gahss)概念在高强度下实现高可成形性,但是这些钢通常高度合金化并还含有昂贵的合金化元素。实例是mn含量典型地高于12重量%的含高锰的孪生诱发塑性(twip)钢和含有大量的昂贵合金化元素例如铬、镍、钼等的不锈钢。除了非常昂贵,2gahss的另一缺陷是由于它们非常高的合金含量,因而以大工业规模制造它们非常困难。
4.为了克服2gahss的这些问题但还实现在高强度下的合理地高的可冷成形性,引入了各种第三代ahss(3gahss)概念,例如淬火和分配(partitioning)(q&p)钢、不含碳化物的贝氏体(cfb)钢和中等mn钢。这些钢没有2gahss昂贵并可容易在钢厂的现有设备中加工。本发明关注中等mn类型的3gahss。
5.wo16001887公开制造高强度钢片的方法,其中钢以重量百分比计含有0.1≤c≤0.4、4.2≤mn≤8、1≤si≤3、0.2≤mo≤0.5,余量是fe和不可避免的杂质,该方法包括大于ac3的连续退火,淬火至马氏体开始(ms)和结束(mf)之间的温度,在300-500℃之间过时效大于10s并冷却。这基本上是淬火和分配(q&p)方法,其中通过含有一定量的马氏体的钢的过时效步骤实现在奥氏体中的c富集(和可能地一些mn富集)。q&p方法完全不同于临界区退火方法。在该文件中,没有预期大量的mn分配至奥氏体钢中,因为在较低的过时效温度(300-500℃)下钢中的mn扩散极慢。
6.wo2017021464公开热轧或冷轧带形式的高拉伸钢,具有化学组成(以重量%计):c:0.005至0.6;mn:4至10;al:0.005至4;si:0.005至2;p:0.001至0.2;s:至多0.05;n:0.001至0.3;余量为铁与和钢有关的不可避免的元素夹杂物,其中如果柔性热轧的,任选退火的,柔性冷轧的,任选退火的钢进一步柔性冷轧,并随后在600℃至750℃的退火温度下退火1分钟至48小时。这个专利通过控制辊缝应用柔性轧制,其中剪切条件跨带材的宽度而变化。柔性轧制是针对具有变化的壁厚度的部件的不同方法,其不同于本发明中的常规轧制方法,在常规轧制方法中在整个宽度上获得均匀的产物厚度。柔性轧制带材的缺点在于跨带材的宽度获得不均匀的性质。
7.本发明旨在提供在涂覆或未涂覆条件下同时维持高强度的冷轧厚度的可高度冷成形的钢带。
8.本发明的另一目的是提供在涂覆或未涂覆条件下同时维持高强度的热轧厚度范围的可高度冷成形的钢带。
9.本发明的热轧和冷轧钢带都具有高能量吸收能力,即高度耐碰撞的,是可点焊的并耐氢脆。
10.本发明首先体现在制造冷轧和退火的钢带的方法,钢组成以重量%计为:
11.c:0.05-0.3;
12.mn:3.0-12.0;
13.al:0.03-3.0;
14.任选的一种或多种另外的合金化元素:
15.si:小于1.5;
16.cr:小于2.0;
17.v:小于0.1;
18.nb:小于0.1;
19.ti:小于0.1;
20.mo:小于0.5;
21.不可避免的杂质,例如
22.s:小于30ppm;
23.p:小于0.04;和
24.余量为fe;
25.该方法包括以下步骤:
[0026]-将熔融钢浇铸成板坯;
[0027]-预加热板坯并将它保持在1150℃或更高的温度下持续1小时或更多的时间;
[0028]-将钢热轧成带,优选使用大于1000℃的平均f1板坯进入温度;
[0029]-卷绕热轧钢带;
[0030]-酸洗钢带;
[0031]-将钢带在低于650℃的温度下中间分批退火大于24小时以在冷却至室温之后实现至少60体积%铁素体;
[0032]-将钢冷轧成冷轧钢带并将其卷绕;
[0033]-将卷绕的钢带分批退火:
[0034]-在ac1和ac3之间的小于700℃的临界区温度下;
[0035]-在非氧化和非氮化气氛中;
[0036]-将带保持在所述临界区温度的总退火时间为至少5小时、优选至少10小时以便得到:在奥氏体中的mn富集,其使得mn含量为钢的整体mn含量的至少1.25倍;和c富集,使得c含量为钢的整体c含量的至少1.2倍;
[0037]-在空气中、在强制空气中或通过水淬火将分批退火之后的钢冷却。
[0038]
使用特定加工路线将基本上含有0.05至0.3重量%c、3.0-12.0重量%mn、0.03-3.0重量%al和任选其它合金化元素和不可避免杂质的钢加工为热轧规格。将熔融的钢浇铸成板坯,然后将板坯再加热至1150℃或更高的温度持续1小时或更多的时间。然后优选使用大于1000℃的精轧入口温度(f1)将板坯热轧成带材。f1入口温度是精轧机的第一基座中带材的进入温度。精轧机是进行精轧的热轧机的部分,这发生在粗轧机中的板坯的粗轧或开坯轧制之后并在输出辊道冷却之前。在它通过输出辊道之后,热轧带材缠绕成卷,并且然后在低于650℃的温度下将这些卷中间分批退火持续至少24小时使得在冷却至室温之后在钢带中实现至少60体积%的铁素体。然后在酸溶液中在比如说50-90℃的温度下酸洗钢带
并冷轧至较薄的规格。本发明不受热轧或冷轧规格范围的限制。然而,典型地热轧规格将在2至10mm的范围内并且冷轧规格在0.5至2mm的范围内。然后,将冷轧钢在小于700℃、优选小于660℃的临界区温度下在非氧化和非氮化气氛中分批退火至少5小时、优选至少10小时的持续时间,使得临界区奥氏体的mn含量达到钢的整体mn含量的至少1.25倍且临界区奥氏体的c含量达到整体c含量的至少1.2倍。优选10小时的较长时间,因为在退火期间较大量的mn可从铁素体分配至奥氏体中。mn典型地花费较长时间扩散,因为它是铁中的大的置换合金化元素。随着分批退火的温度降低,临界区奥氏体中的锰富集提高,这使在分批退火后的冷却之后钢中的奥氏体在降至室温时更稳定。分批退火时间定义为钢带保持在所述分批退火温度下的时间段,不包括将带加热至目标温度的时间。
[0039]
将发生最终分批退火,即在本文中的卷绕带的分批退火持续在权利要求中提到的持续时间,其足够长以在钢中获得相对等轴的铁素体晶粒形态,其中晶粒长度和宽度之比优选为3或更小。然后例如在空气、强制空气或水中将钢以任何冷却速率冷却至室温。
[0040]
通过执行按照本发明的方法,获得以下优点:
[0041]-含有提到的合金化元素连同3-12重量%mn的中等mn钢减小了mn的偏析。当如本发明中mn以相对高的量存在时这是影响机械性质的考虑因素。选择大于1150℃、优选1200℃、更优选大于1250℃的相对高的板坯再加热温度和1小时的最小再加热时间,以便使偏析最小并将mn均匀分布在基体中。另外,最终机械性质可能受损。再加热温度的选择将依赖于合金的mn含量。当合金的mn含量接近要求保护的mn范围的下限时,接近1150℃的再加热温度将足以使mn分布均匀,并且随着mn含量提高,将优选更高的板再加热温度。
[0042]-钢可以工业规模热轧,具有相当大的带宽度,例如大于1000mm。这通过在热轧过程中维持大于1000℃的高f1温度从而使需要的热轧力低来实现。使用较低的f1温度,钢带的热轧将变得困难。
[0043]-钢变得适合于以工业规模冷轧。这凭借使用热轧钢的中间分批退火步骤变为可能。在钢的临界区温度下,优选小于650℃进行中间分批退火,在这样的所选择温度下使得在钢带中实现至少60体积%铁素体,余量是残余奥氏体和马氏体。
[0044]-卷绕钢带的小于700℃的(进一步)分批退火实际产生恰当的显微组织。它应为至少5小时、优选至少10小时。在这个方法步骤期间,本发明钢的mn和c在临界区奥氏体和铁素体之间分配使得奥氏体通过mn和c变得高度富集,并使相稳定直至室温。因为奥氏体富集使得mn含量为钢的整体mn含量的至少1.25倍和c含量为钢的整体c含量的至少1.2倍,钢实际上对实际冷却速率不敏感,并因此在分批退火之后钢可在空气、强制空气或水中冷却。分批退火温度越低,低于700℃,mn含量越丰富的是临界区奥氏体。
[0045]
本发明的第二实施方案是制造热轧和退火的钢带的方法,钢组成以重量%计为:
[0046]
c:0.05-0.3;
[0047]
mn:3.0-12.0;
[0048]
al:0.03-3.0;
[0049]
任选的一种或多种另外的合金化元素:
[0050]
si:小于1.5;
[0051]
cr:小于2.0;
[0052]
v:小于0.1;
[0053]
nb:小于0.1;
[0054]
ti:小于0.1;
[0055]
mo:小于0.5;
[0056]
不可避免的杂质,例如
[0057]
s:小于30ppm;
[0058]
p:小于0.04;和
[0059]
余量为fe;
[0060]
该方法包括以下步骤:
[0061]-将熔融钢浇铸成板坯;
[0062]-在1150℃或更高的温度下再加热板坯持续1小时或更多的时间;
[0063]-将钢热轧成带,优选使用大于1000℃的平均f1板坯进入温度;
[0064]-卷绕热轧钢带;
[0065]-酸洗钢带;
[0066]-将卷绕的钢带分批退火:
[0067]-在ac1和ac3之间的小于700℃的临界区温度下;
[0068]-在非氧化和非氮化气氛中;
[0069]-将带保持在所述临界区温度的总退火时间为至少5小时、优选至少10小时以便得到:在奥氏体中的mn富集,使得mn含量为钢的整体mn含量的至少1.25倍;和c富集,使得c含量为钢的整体c含量的至少1.2倍;
[0070]-在空气中、在强制空气中或通过水淬火将分批退火之后的钢冷却。
[0071]
如上所述,根据第一实施方案加工直至热轧步骤的钢然后在酸洗之后跳过中间步骤直接进行最终分批退火步骤。分批退火将根据权利要求进行足够长的时间以在钢中获得相对等轴的铁素体晶粒形态,其中晶粒长度和宽度之比优选为3或更小。
[0072]
因此,将钢制造为热轧带材而不是冷轧带材,然而具有如第一实施方案的冷轧带材那样在机械性质方面的所有优点。
[0073]
本发明还体现在其中在1200℃或更高的温度下再加热板坯的方法中。这实现铸造状态的钢板坯中mn较好的均匀化从而减小它的偏析。
[0074]
本发明还体现在其中在1250℃或更高的温度下再加热板坯的方法中。这实现铸造状态的钢板坯中存在的mn的任何微偏析的甚至进一步减小。
[0075]
本发明还体现在其中在小于660℃的临界区温度下发生将卷绕的钢带分批退火的方法中。这实现mn在临界区奥氏体中的较高富集,使得可最小化最终显微组织中的马氏体含量。本发明还体现在其中所得的带涂覆有通过热浸镀锌、镀锌退火、电镀锌、镀铝或任何其它方法例如物理气相沉积(pvd)、化学气相沉积(cvd)施加的任何金属性涂层的方法中。这实现钢带在应用或使用中的好的美学外观和需要的耐腐蚀性。
[0076]
在根据除了权利要求2的权利要求的方法的实施方案中,所得的钢带经历光整冷轧,还称为平整。这甚至进一步改进可冷成形性质。
[0077]
在实施方案中,光整冷轧以5%或更小的厚度压下进行。这使拉伸测试中钢带的屈服点伸长率最小化,由此改进冷成形钢带的可冷成形性和美学外观。
[0078]
本发明还体现在可以是或根据本发明第一或第二实施方案的方法制造的钢带,其
中钢带具有钢组成,所述钢组成以重量%计为:
[0079]
c:0.05-0.3;
[0080]
mn:3.0-12.0;
[0081]
al:0.03-3.0;
[0082]
任选的一种或多种另外的合金化元素:
[0083]
si:小于1.5;
[0084]
cr:小于2.0;
[0085]
v:小于0.1;
[0086]
nb:小于0.1;
[0087]
ti:小于0.1;
[0088]
mo:小于0.5;
[0089]
不可避免的杂质,例如
[0090]
s:小于30ppm;
[0091]
p:小于0.04;和
[0092]
余量为fe;
[0093]
其中钢带具有残余奥氏体组成,其具有的mn含量为钢组成的整体mn含量的至少1.4倍且c含量为钢组成的整体c含量的至少2.3倍,以便获得亚稳的残余奥氏体以使钢具有在准静态拉伸测试中对于7%应变范围而言的屈服点伸长后测量的至少0.3的高应变硬化指数,其中卷绕钢带的最终分批退火之后的显微组织以体积%计包含:
[0094]
铁素体:30-70%;
[0095]
残余奥氏体:20-65%;
[0096]
马氏体:《20%,包括0体积%。
[0097]
钢带具有在最终使用条件下的钢的最终显微组织的亚稳奥氏体中mn和c富集的水平以使它具有高的加工硬化或应变硬化速率。
[0098]
此外,根据本发明,冷轧或热轧钢带优选具有显微组织,其中存在在20至65体积%的范围内的残余奥氏体,在30至70体积%的范围内的铁素体和小于20体积%(包括0体积%)存在的马氏体。铁素体优选是超细的,晶粒在0.2至2μm的范围内。这种超细铁素体由于卷绕钢带的足够长的分批退火得到或多或少的等轴形状,其中晶粒的长度/宽度比≤3。与典型地短的(以分钟计而不是以小时计)产生具有高纵横比(长度/宽比比)的细长形状晶粒的不连续类型退火不同,在本发明中采用冷轧带材的长的分批退火期间发生铁素体晶粒的充分再结晶。
[0099]
本发明的其它实施方案根据权利要求10至14,其赋予当根据本发明制造时在钢带中实现的高机械和可冷成形性质。这些性质是(双轴)可拉伸性、可弯曲性、扩孔能力、屈服强度、极限拉伸强度、总伸长率和屈服点伸长率。
[0100]
如上所述,本发明还体现在经历了光整冷轧(还称为平整)的钢带中。
[0101]
本发明基于钢组成的改性和使用所有提到的步骤加工它以实现优化的显微组织。由于实现的显微组织,冷轧和/或热轧形式的钢带具有高的可冷成形性和高的机械性质。
[0102]
钢的必要元素是mn、c和al。mn和c是钢中的奥氏体稳定元素并因此以预定的量将这些添加至钢中以稳定奥氏体。al是铁素体稳定剂,但是它使ac1和ac3之间的温度范围变
宽(ac1=加热期间奥氏体转变开始时的温度;ac3=加热期间奥氏体转变完成时的温度)。添加al以提高钢对工业加工的稳健性,因为它使钢在临界加工期间对不期望的小温度变化较不敏感。本发明没有限制钢中其它任选元素的存在和不可避免的杂质。在相关权利要求中给出这些任选的和不可避免的合金化元素的范围。
[0103]
钢中mn的量升高,在3至12重量%的范围内,将在卷绕状态的热轧或冷轧钢带的分批退火期间引起大量的mn富集在奥氏体中。因为c也是奥氏体稳定元素,所以这种mn富集与c富集一起通过抑制钢的ms温度(ms=冷却期间马氏体转变开始时的温度)从而提高临界区奥氏体的热稳定性。因此,在卷绕钢带的分批退火之后冷却至室温过程中,临界区奥氏体没有大程度转变为马氏体,使得大量的奥氏体(》20体积%)可残留在钢的室温显微组织中。在加载(成形或任何其它变形)期间这种具有最佳机械稳定性的残余奥氏体转变为马氏体,从而引起转变诱发塑性(trip)效应。由于提高加工或应变硬化速率的trip效应,在产物中实现在本发明的钢带中的高强度、高伸长率和高可冷成形性。由于极端偏析以及塑性增强的机制将从trip变为twip(twip=孪生诱发塑性),高于12重量%的mn含量将使钢的连续铸造困难,并且低于3重量%的含量在奥氏体中将不会产生足够的mn富集以实现室温显微组织中足量的残余奥氏体。
[0104]
与如上述mn的效果类似,在最终分批退火期间c也分配至临界区奥氏体中,提高奥氏体的热稳定性并在室温显微组织中引起奥氏体稳定化。然而,c比mn以更小的量有效并因此在本发明中用于改性钢化学性质的c含量的范围为0.05至0.3重量%。如果c含量小于0.05重量%,没有获得足够的奥氏体稳定效果,并且c含量大于0.3重量%将引起冷成形之后后处理所制造的带材例如点焊困难。焊接在将汽车部件组装成车体方面必不可少,因此考虑这个方面非常重要。还将c添加至本发明的钢中以提高强度。
[0105]
铝不是钢中的奥氏体稳定元素,而是铁素体稳定元素。然而,它至多3重量%添加至钢以扩大钢的临界区温度范围(ac1至ac3)。具有高水平的mn,钢变得对工业规模加工中加工温度的小变化敏感。添加al确保钢的加工稳健性,使得可选择钢带的分批退火温度具有小的变化,以实现期望的显微组织。当有意不向钢添加al作为合金化元素时(即当al含量为约0.03重量%时,因为它通常作为脱氧剂添加至钢水),有必要使用更精确的炉,但是本发明仍然起作用。al的最高量限制为3重量%以减小热轧期间氧化物皮形成和热轧和冷轧期间的轧制力。
[0106]
钢组成和方法步骤的组合导致发明的有益效果。作为钢化学性质改性的必要合金化元素的mn当它的含量大于约2重量%时有在铸造之后偏析的趋势。这将通过产生不均匀性质来影响产物性能并还可在加工步骤期间导致开裂。因此,优选的是铸造板坯非常均匀。通过使用大于1150℃、优选大于1200℃、更优选大于1250℃的相对高的板坯再加热温度和持续足够长的时间、优选持续60分钟或更多来实现板坯好的均匀化。
[0107]
然后,由于钢相对高的合金含量,在带材的热轧期间轧制力高。为了以工业规模轧制相当宽的带材,典型地比1000mm更宽,热轧优选在钢的奥氏体相的相对高的温度下进行,大于ar3,其中ar3是在冷却过程中在钢中开始形成铁素体时的温度。这可通过使用大约1000℃或更高的开始精轧温度(f1)来确保。比这更低的f1温度可提高热轧力并将导致可使热轧对于工业大规模加工困难的临界区热轧。除了提高轧制力,临界区热轧还可引起热轧带材的不充分再结晶。
[0108]
然后,当在热轧带材上施加冷轧以减小最终钢产品的规格时,将不可冷轧材料,除非采用合适的预加工。特别地,在热轧之后卷绕状态的钢经受在钢的临界区温度范围内低的温度下中间分批退火处理24小时或更长。因为它持续相对长时间段,所以它是间歇式退火。中间分批退火温度应低于650℃,因为在高于这的温度下在将钢冷却至室温之后将形成大量残余奥氏体。另外,如果使用较高的分批退火温度,可在显微组织中出现大量的马氏体。马氏体和残余奥氏体都通过提高轧制力而使冷轧困难。虽然马氏体相硬,但是在冷轧自身期间残余奥氏体转变为硬马氏体从而提高轧制力。因此,卷绕状态材料的中间分批退火是根据这种实施方案的方法的部分,以保持残余奥氏体和马氏体的含量为较低的值并提高铁素体的量。铁素体相在冷轧期间没产生与残余奥氏体一样高的加工硬化,并因此保持低的轧制力,使冷轧成为可能。在热轧钢的这种间歇式退火之后,使其适于冷轧所需的铁素体相的最小量为60体积%。
[0109]
热轧产物的情况下的热轧钢带和冷轧产物的情况下的冷轧钢带的最终分批退火对为了使本发明工作的在最终产物中获得期望的显微组织部件非常关键。必须在小于700℃、优选小于660℃的临界区温度(在ac1至ac3的范围内)下进行这种最终分批退火。这是因为热力学计算建议对于发明的钢化学性质范围,小于660℃在临界区奥氏体中发生c的峰值富集,然而mn富集随着从700℃降低温度单调提高。因此,使用小于660℃的最终分批退火温度,在临界区奥氏体中确保最佳的最大(c+mn)富集。必须以这样的方式选择退火温度,使得发生最大量的mn和c分配至奥氏体中。在临界区温度下的这个最终分批退火期间,在临界区奥氏体中将存在c和mn富集,因为c和mn是奥氏体稳定剂。虽然c因为在钢中是小的间隙元素而快速扩散分配,但作为大的置换元素的mn扩散慢。因此,需要优选5小时或更长、更优选10小时或更长的分批退火时间以在奥氏体中实现大量的mn。在奥氏体中的mn富集应使得mn含量为钢的整体mn含量的至少1.25倍、优选至少1.4倍。c富集应使得c含量为钢的整体c含量的至少1.2倍、优选至少2.3倍。需要在临界区奥氏体中这些水平的mn和c富集以适当稳定奥氏体至室温,使得在室温显微组织中获得至少20体积%残余奥氏体。另外,这些水平的mn和c富集对于实现残余奥氏体的最佳机械稳定性(称作亚稳定性)是必要的,使得在变形期间钢可具有至少0.3的应变硬化指数。如果mn和c富集在奥氏体中低于提到的值,没有实现残余奥氏体的最佳稳定性,并因此也没有实现最小0.3的应变硬化指数。因此,当退火持续时间短于5小时,没有满足本发明的这些要求。如果使用高于700℃的分批退火温度,将出现类似的缺陷。在临界区奥氏体中将没有所需的c和mn富集,并因此临界区奥氏体将不够稳定以产生在分批退火之后室温显微组织的最小为20体积%的残余奥氏体连同所需的高应变硬化速率要求的亚稳定性。因此,高残余奥氏体分数和它的最佳机械稳定性的组合导致期望的高应变硬化速率。高于700℃的退火温度还将导致大于20体积%的马氏体,这将不会产生期望的应变硬化速率。正是这种高应变硬化速率导致高的可冷成形性以及最终产物的强度和延展性的高组合。高应变硬化速率强化钢片同时在成形期间(例如通过拉伸)变薄,这导致高的可冷成形性。
[0110]
在非氧化和非氮化气氛中进行最终分批退火以使由氧和氮所致钢带的任何表面劣化最小化。因为分批退火持续时间需要最少5小时,所以如果不使用非氧化气氛,钢表面可氧化。另外,将发生脱碳,降低钢的c含量,使本发明不太有效。由于同样的原因,氮可与钢表面中存在的al反应,从而在钢表面上形成它的氮化物。所有这些形式的表面劣化对于钢
的机械性质和可成形性有害。优选的退火气氛可为真空、氢或氩气氛。
[0111]
对钢和它的加工的以上修改导致最终产物中适当的显微组织从而使本发明成功。高的残余奥氏体分数(》20体积%),与低的马氏体分数(《20体积%)和最佳分数的铁素体(30-70体积%)由于高的应变硬化速率而产生高强度、延展性和可成形性的组合。大于65体积%的残余奥氏体含量不可能在钢的组成边界内实现,并且对于实现最小所需的应变硬化速率也是不必要的。此外,高于70体积%的残余奥氏体也可在点焊中引起问题,引起严重的液体金属脆化以及在使用中差的耐氢脆性。因此,考虑这些因素选择本发明钢材的组成边界。如果铁素体含量大于70体积%,将不会实现最小0.3的高应变硬化指数,这主要来自通过trip效应的亚稳的残余奥氏体。不需要铁素体分数小于30体积%来获得最小应变硬化速率。马氏体相主要有助于强度而没有过多贡献应变硬化速率。此外,大量的马氏体(》20体积%)可与较软的相例如铁素体和残余奥氏体产生弱的界面。这些界面对高延展性和可成形性有害,因为这些充当损害开始的成核位置。因此,马氏体含量应保持小于20体积%,包括不存在马氏体。
[0112]
超细晶粒是本发明的另一显微组织要求。铁素体晶粒应小于2μm,在0.2-2μm的范围内。这种超细晶粒尺寸赋予产物好的延展性,并还通过晶粒细化引起强化,从而有助于本发明中钢带好的机械性质。还通过选择小于700℃的低的最终分批退火温度(限制晶粒生长)来确保这种超细显微组织。此外,由于本发明钢组成和临界区最终分批退火的要求,退火温度下的相(铁素体和奥氏体)彼此约束并不能生长。所有这些因素导致铁素体的期望的超细晶粒尺寸。大于2μm铁素体晶粒尺寸将引起较低强度和延展性。晶粒尺寸这里主要由晶粒的长度表示。由于最终分批退火期间钢带的充分再结晶,铁素体晶粒的宽度将大于长度的1/3。这实际将在最终分批退火之后产生铁素体晶粒的相对等轴形状。
[0113]
关于以上超细铁素体晶粒尺寸的片材可成形性效果可为产物的工程应力-应变曲线中屈服点伸长率的出现。由于应变集中以及冷成形部件的美学外观劣化,这可对钢的可冷成形性有害。因此,以这样的方式选择工艺变量,使得最终显微组织中铁素体分数为最大70体积%。这将确保屈服点伸长率(如果存在)将限制为最大10%工程应变以获得冷成形部件的最好的片材可成形性和/或美学外观。然而,大于10%工程应变的屈服点伸长率不是本发明起作用的限制因素。这是因为在成形前通过平整和/或在成形期间使用适当润滑,可减轻屈服点伸长率的潜在负作用。
[0114]
为了去除屈服点伸长率(如果存在),在本发明中通过平整或光整冷轧,钢带任选地具有少量的冷轧压下,厚度压下为至多5%。在一个或多个道次中施用的这种少量冷轧将除去屈服点伸长率而没有以任何可感知的程度改变钢带的机械性质。然而,在没有这个平整步骤的情况下本发明仍然起作用而产生高的可冷成形性,即使存在屈服点伸长率总计小于10%工程应变。
[0115]
任选地,热轧或冷轧带材在它们的最终分批退火之后被金属性涂层涂覆以提高在使用中它们的美学外观和耐腐蚀性。涂覆方法可为但不限于热浸镀锌、镀锌退火、电镀锌、pvd、cvd等。最终分批退火的钢带就它的显微组织而言非常稳定并因此不会由于施加薄的涂层而实质上改变它的特性。
[0116]
可在施加或没有施加合适润滑以减小钢和工具之间的摩擦力的情况下进行钢带材或片材或坯件的冷成形。在两种情况下,本发明提供高的可冷成形性。润滑体系的非限制
性实例是轻质油、kl
ü
ber press pate、特氟龙箔或这些的组合。
[0117]
根据本发明的方法中使用的钢是包含碳、锰和铝作为主要成分的中等mn钢。可存在选自硅、铬、钒、铌、钛和钼的任选其它合金化元素。可存在不可避免的杂质如n、p、s、o、cu、ni、sn、sb等(来源于制备钢组成的起始材料)。它们没有被有意地添加或特意控制在预定界限内。钢组成的余量为铁。
[0118]
碳以0.05-0.3重量%、例如0.05-0.20重量%、优选0.07-0.20重量%的量存在。虽然c也有助于稳定奥氏体,但主要考虑强度而添加。在本组成中锰的奥氏体稳定作用由于它的较高比例而明显得多。c的优选范围为0.05-0.25,和更优选的范围是0.08-0.21重量%。太少的c将不会产生800mpa的期望强度水平,并且如果c高于0.21,形成的零件的可焊接性可能变差。
[0119]
锰以3.0-12.0重量%的量存在。锰减小ac1和ac3温度,稳定奥氏体,提高强度和韧性,并通过稳定室温显微组织的奥氏体从而引起trip效应。在小于3.1重量%的水平下没有实现目标效果,而以大于10.5重量%的量将引起铸造和偏析的问题。另外,变形机制将从转变诱发塑性(trip)变为孪生诱发塑性(twip)。如果mn含量太低,则将在室温下残余不充足的奥氏体并且残余奥氏体的稳定性将太低,结果是不能获得延展性和应变硬化好处。优选地mn含量在3.5-10.0重量%的范围内。在实施方案中mn总计为5.0-9.0重量%。在其它实施方案中它是5.5-8.5重量%,例如6.0-7.5重量%。
[0120]
添加铝以扩大温度范围ac1至ac3从而在工业应用方面提高方法的稳健性。al以从0.03且直至3.0重量%、例如0.6-2.9重量%、优选在1.0-2.2重量%的范围内的量存在。
[0121]
以小于1.5重量%的量添加硅(如果存在)用于通过固溶强化来提高强度。如果存在,量典型地大于0.01重量%且小于1.5重量%。它的优选范围是0.1-1.0重量%。
[0122]
al和si都有助于抑制渗碳体析出以避免延展性的劣化。此外,al和si都还提高峰值退火温度用于在最终分批退火之后获得最高量的室温下残余奥氏体。因此,在临界区退火之后促进mn的扩散以具有有效的mn分配在奥氏体中。
[0123]
任选存在一种或多种另外的微合金化元素,选自v、nb、ti和mo。这些微合金化元素通过它们的碳化物、氮化物或碳氮化物的析出硬化而提高强度。cr(本发明的另一任选元素)也提高峰值退火温度用于实现最高量的室温下残余奥氏体并减小残余奥氏体的含量对退火温度的敏感性。这些导致mn有效分配在奥氏体中和在退火期间提高的方法稳健性。如果存在,这些任选合金化元素的优选添加为v:0.01-0.1重量%;和/或nb:0.01-0.1重量%;和/或ti:0.01-0.1重量%;和/或mo:0.05-0.5重量%;和/或cr:0.1-2.0重量%。
[0124]
没有限制金属性涂层的组成。可施加基于zn的涂层,例如主要含锌、至少0.1重量%al、和任选至多5重量%al和至多4重量%mg的锌,涂层组成的其余部分包含全部单独地小于0.3重量%的其它元素和不可避免的杂质。可以小于0.3重量%的少量存在例如以便形成锌花和/或防止浮渣形成的其它额外元素可选自包含以下的组:pb、sb、ti、ca、mn、sn、la、ce、cr、ni、zr和bi。pb、sn、bi和sb。少量的这种额外元素对于通常应用而言没有以任何显著程度改变浴或所得涂层的性质。优选地,当涂层中存在一种或多种额外元素时,每种以《0.02重量%的量存在,优选每种以《0.01重量%的量存在。涂覆方法还可从热浸镀锌(gi)、镀锌退火、加热涂覆循环、电镀锌变化。还可施加基于铝的涂层例如al-si-x涂层,其中si可从0.1至10重量%变化和x=以任何需要量存在的任何其它涂层改性元素,加上基本上不改
变涂层特性的不可避免的杂质。涂覆方法例如pvd、cvd等也可适用。
[0125]
最终分批退火工序不限于使用的炉类型或甚至卷中带的加热速率和冷却速率。应理解卷的加热速率当它们经历分批退火时可从表面至中心变化。但对于本发明而言,必要的是使卷绕的带在目标分批退火温度下持续最少5小时,优选大于10小时,使得卷的每一部分经历在奥氏体中的足够的c和mn富集。分批退火之后的冷却速率与本发明不相关,因为大量mn的存在提高钢的淬透性。因此,卷可在分批退火炉内冷却,空气冷却,强制空气冷却或甚至水淬火。
[0126]
可要么在裸露的钢带上要么在涂覆的钢带上完成平整或光整冷轧。这还可在单个道次或多个单次中完成。
[0127]
获得的钢带优选具有三相或双相显微组织,包含(以体积%计):
[0128]
铁素体:30-70%;
[0129]
残余奥氏体:20-65%;
[0130]
马氏体:小于20%,包括0%;和
[0131]
铁素体晶粒尺寸:0.2-2μm。
[0132]
获得的钢带具有残余奥氏体的以下组成特征:
[0133]
mn:钢的整体mn组成的1.25倍、优选1.4倍
[0134]
c:钢的整体c组成的1.2倍、优选2.3倍
[0135]
有利地,钢带具有以下性质:
[0136]
屈服强度:600mpa或更大;
[0137]
极限拉伸强度:800mpa或更大;
[0138]
总伸长率:20%或更大;
[0139]
应变硬化指数:0.3或更大
[0140]
屈服点伸长率:优选10%工程应变或更小
[0141]
1.0mm厚度下最小弯曲角:100
°
或更大;
[0142]
扩孔能力:20%或更大;
[0143]
双轴拉伸中最小拉伸应变:10%或更大。
[0144]
通过使用x-射线衍射(xrd)测定以上提到的相分数。通过xrd在样品的1/4厚度位置测定残余奥氏体的量。在panalytical xpert pro标准粉末衍射仪(cok
α-辐射)上在45至165
°
(2θ)的范围内记录xrd图样。通过rietveld分析使用用于rietveld精修的bruker topas软件包进行相比例的定量测定。马氏体含量由衍射图中铁素体衍射位置处的峰分裂测定。
[0145]
从显微组织的扫描电子显微镜(sem)图像来确定相的晶粒尺寸。通过电子探针微量分析仪(epma)测定残余奥氏体的mn浓度。通过由dyson和holmes提出的众所周知的公式估算残余奥氏体的c含量。这个公式使可由xrd数据测定的奥氏体的晶格参数与它的c含量有关。这个公式可在以下文章中获得:d.j.dyson,b.holmes,effect of alloying additions on the lattice parameter of austenite.journal of iron steel institute,第208卷,1970年,第469-474页。
[0146]
由室温下根据nen 10002标准的准静态(应变速率3
×
10-4
s-1
)拉伸测试测定屈服强度、极限拉伸强度、屈服点伸长率和总伸长率。拉伸试样的几何形状为沿轧制方向的80mm
规格长度、30mm宽度和1.5mm的标称厚度。在拉伸曲线中屈服点伸长率之后在7%应变的范围内测量应变硬化速率。通过按照vda 238-100标准的三点弯曲测试在标称1.5mm厚、40mm
×
30mm试样上在纵向和横向两个方向上测定可弯曲性。弯曲轴沿着30mm尺寸并且弯曲半径为0.4mm。使用下式将从标称1.5mm试样获得的弯曲角转化为对应于1.0mm厚度的角度:1.0mm厚度下的弯曲角=测量的角度
×
以mm为单位的实际厚度的平方根。从这些转化的弯曲角,对于特定热处理条件而言,取纵向和横向试样的最低值来要求本发明的范围。根据iso/ts 16630:2003(e)标准测定扩孔能力(hec)。从钢带材切割尺寸90mm
×
90mm
×
1.5mm的试样。在试样的中间冲出10mm直径的孔,并且进行扩孔测试。从测量的数据计算扩孔能力(hec=(孔的初始直径的扩大/孔的初始直径)
×
100%)。从在erichsen压机上使用75mm直径平冲头连同79.78mm直径冲模进行的双轴拉伸测试来测定双轴拉伸应变。冲头头部(punch nose)具有10mm的半径和冲模为8mm。将坯料夹持器力设定为最大机器能力(~580kn)以确保不会发生内缩。测试速度设定为20mm/min。通过在具有精细标记的片材上施加10mm的方形网格来进行应变测量。
[0147]
在钢带制造中,如以上解释通过使用在小于700℃的钢的临界区温度下的最终分批退火步骤,发生mn从铁素体分配至奥氏体,从而提高临界区奥氏体的稳定性。在最终分批退火之后在冷却期间临界区奥氏体没有显著转变为马氏体,这是因为它由低ms所致的高稳定性,产生了铁素体和残余奥氏体的双相显微组织。对于低的mn含量,例如小于8重量%,一些临界区奥氏体可转变为马氏体,但是马氏体含量将为20体积%或更小。因此,通过增强水平的mn和低的分批退火温度(例如小于700℃),可保证大量的残余奥氏体(20体积%或更大)与最佳亚稳定性。在成型步骤中的变形期间这种大量的残余奥氏体部分转变为马氏体,从而引起转变诱发塑性(trip)效应,导致高应变硬化指数(=高伸长率和高可成形性)。
[0148]
由于钢组成,钢带的总伸长率优选为20%或更大并且应变硬化指数为0.3或更大。优选使用中等mn钢途径的临界区分批退火步骤以获得超细铁素体(0.5-2.0微米)与马氏体和高残余奥氏体的区域的混合显微组织。因此,获得高延展性和高硬化速率。这些导致钢带的高的可冷成形性。
[0149]
优选的钢带用作制造汽车部件的材料,特别是要求带材可成形性的具有复杂形状的那些。要求高能量吸收结合高强度的部件也适合由钢带制造。非限制性实例包括汽车的内部零件、b柱和纵向筋等。
[0150]
将参考图1和以下描述的实例阐明本发明。
[0151]
图1显示通过最终分批退火(钢a,650℃/10小时)获得的根据本发明制造的钢的sem显微组织,其中f=铁素体,ma=马氏体-奥氏体。
[0152]
通过在真空感应炉中熔融进料来铸造具有尺寸200mm
×
100mm
×
100mm的三种本发明化学组成a、b和c的钢锭。在表1中给出这些本发明钢化学组成以及两种参考钢d和e的化学组成。钢d是孪生诱发塑性(twip)钢和钢e是dh1000牌号,都以它们的最终冷轧和退火条件接收。这些接收状态的钢的厚度分别为1.7mm和1.5mm。然后将它们在1250℃下再加热2小时并粗轧至30mm厚度。然后,将带材再次在1250℃下再加热30分钟,并使用1150℃的轧制开始温度和900℃(其对于全部三种钢而言在奥氏体相区内)的精轧温度(frt)将钢a和b热轧至3mm厚度和将钢c热轧至4mm厚度。对于mn的合适均匀化使用1250℃的高再加热温度和2小时的长持续时间。
[0153]
通过膨胀测定法测量钢a、b和c的奥氏体至铁素体转变温度(ar3)分别为785、770和723℃。然后,在马弗炉中从680℃对热轧钢材进行卷冷却模拟,并由此冷却至室温。然后,在600℃下中间分批退火a和b的热轧带材96小时,然而在马弗炉中在氩的保护性气氛下在550℃下中间分批退火c的带材并空气冷却至室温。以这样的方式选择这些退火温度,使得实现期望量的铁素体分数以促进该方法中后期的冷轧。在表2中给出在热轧带材的这种中间分批退火之后钢a、b和c的相分数。通过如之前描述的xrd测量从带材的四分之一厚度位置测定相分数。看出这三种钢材中铁素体分数都高于60体积%。
[0154]
接下来,在hcl酸中在90℃下酸洗带材以去除氧化物,并然后将全部钢材从它们各自的热轧规格冷轧至1.5mm的最终厚度。
[0155]
使用马弗炉在650℃下分批退火a和b的冷轧带材10小时并且在640℃下分批退火钢c的冷轧带材4和16小时。使用氩气氛用于退火,使得气氛不含有氧和氮以最小化带材的氧化和来自大气的氮和来自钢的铝之间任何不需要的反应以在表面上形成氮化物层。在退火之后,将样品空气冷却至室温。出于对比,还在650℃下类似的方式退火a的冷轧带材2分钟、5分钟和1小时并在640℃下退火c 4小时。一些试样进行至多5%厚度压下的光整冷轧或平整。
[0156]
以上已描述材料表征和测试的工序。回想一下,样品的显微组织使用xrd和sem表征。通过epma和xrd分析进行相化学组成的微量分析。通过具有80mm规格长度和30mm宽度的试样(a80试样几何形状)的拉伸测试来测定拉伸性质。通过弯曲、扩孔和使用合适润滑的双轴拉伸测试来评价带材的可成形性。对于可弯曲性,l和t试样的定义如下:l=纵向试样,其中弯曲轴平行于轧制方向,t=横向试样,其中弯曲轴垂直于轧制方向。
[0157]
图1中显示在钢a的冷轧带材的最终分批退火之后获得的典型显微组织,其中可观察到铁素体和马氏体-奥氏体区域。另外,可实现超细的铁素体的晶粒尺寸。提供在冷轧样品的不同最终退火处理之后钢a、b和c的显微组织特性。对于所有条件下的所有钢材,铁素体的晶粒尺寸在0.5至1.9μm的范围内。对于钢a和c,由于更多mn分配至奥氏体中残余奥氏体含量随着在它们的各自退火温度下退火时间增加而提高。mn含量越高,残余奥氏体含量也越高(钢c具有比a和b更高的残余奥氏体),显示mn对奥氏体稳定的影响。在所有条件下,除了650℃下退火2分钟的钢a,获得了高分数的残余奥氏体(大于33体积%)。表4中给出的钢材的退火条件的mn和c含量显示在钢材的所有这些不同条件的残余奥氏体中mn富集范围为钢的整体mn含量的1.286-2.139倍,除了钢a-650℃/2min条件,其中mn含量仅为整体mn含量的1.09倍。对于在残余奥氏体中的c富集,c含量范围为钢的整体c含量的1.17-3.085倍,除了钢a-650℃/2min条件,其中这个值为1.063倍。由于在奥氏体中的这些低c和mn富集,钢a-650℃/2min条件的残余奥氏体含量也低于20体积%,并因此马氏体含量高于20体积%(39.8体积%)。在所有其它本发明钢和条件下,马氏体含量为16.7体积%或更低,包括0体积%(钢c-640℃/960min)。
[0158]
钢a-650℃/2min条件的较低残余奥氏体分数明显由于以下事实:2min的退火时间对于足够的mn扩散至奥氏体中而言太短,即使退火温度在钢a的临界区温度范围中并且小于700℃。
[0159]
可在表5中给出的钢的拉伸性质中观察到以上显微组织特征的结果。获得较少量的残余奥氏体和分别低于1.25倍的mn和2倍的c的它的主体mn和c含量的钢a-650℃/2min表
现出非常高的屈服强度和极限拉伸强度但总伸长率仅为3.1%。这是因为在拉伸测试期间,所有它的残余奥氏体由于通过低mn和c富集预想的它的低稳定性所致非常快地转变为马氏体。在甚至没有显示任何屈服点伸长率的情况下在变形期间非常早地消耗了少量残余奥氏体。因此,这种钢条件的拉伸性质差并不可用于冷成形。在另一方面,在其它退火条件下的钢a和在所有条件下的钢b和c显示高于693mpa的屈服强度、高于860mpa的极限拉伸强度和高于23.4%的总伸长率。这些钢材还显示高的能量吸收能力(由极限拉伸强度和总伸长率的乘积确定)和不同量的屈服点伸长率。如从表3看出,由于铁素体晶粒尺寸提高,对于钢a和c而言屈服点伸长率随着退火时间降低。这些本发明钢组成的拉伸性质可与表6中列出的参考钢材相比较。由于钢化学组成-加工-显微组织组合,本发明钢化学组成在长的最终分批退火条件下具有比常规的dh1000牌号(参考钢e)高得多的总伸长率以及能量吸收能力。钢e在它的显微组织中具有非常小量的残余奥氏体。此外,虽然twip钢(参考钢d)具有比本发明钢材高得多的总伸长率,但是一些本发明钢材的能量吸收能力在具有完全奥氏体显微组织的twip钢的范围内。
[0160]
表7中显示与参考钢相比本发明钢材的可成形性参数。比较的可成形性参数是在轧制和横向方向上的应变方面的双轴可拉伸性、在片材纵向和垂直方向上的可弯曲性和由hec值表示的可拉伸翻边性。钢a显示当在650℃下进行最终分批退火少于10小时时,双轴拉伸应变值为0,尽管其它参数非零。在650℃下退火2分钟的钢a显示非常差的可弯曲性以及可拉伸翻边性。虽然随着不断增加的退火时间可弯曲性和可拉伸翻边性改进,但是材料不可拉伸直至10小时的最终分批退火。在650℃下退火10小时的钢b也显示与具有相同退火条件的钢a类似的可成形性参数。在640℃下退火4小时的钢c显示高的可弯曲性和可拉伸翻边性但低的可拉伸性。当将钢c退火16小时时,也改进可拉伸性。
[0161]
钢片的可冷成形性是各种参数例如可拉伸性、可弯曲性和可拉伸翻边性的组合。当本发明钢材在它们的临界区温度范围中小于700℃最终分批退火时,如先前已经观察到的退火时间对于在残余奥氏体中产生需要量的mn和c富集而言是重要的,因为mn是钢中的缓慢扩散元素。高的mn和c富集对于实现高的应变硬化速率是必要的。因此,表现出较低应变硬化指数的退火小于10小时的钢材也表现出低的可拉伸性,但是其它可成形性参数好。大于0.3的高应变硬化指数对于实现本发明钢中好的可拉伸性是必要的;否则可发生过早的局部开裂。因此,从结果看起来如在权利要求中提到的好的可冷成形性(可拉伸性、可弯曲性和可拉伸翻边性的组合),最小10小时最终分批退火对于本发明钢是必要的,以便实现在残余奥氏体中mn和c富集的最小值。
[0162]
当10小时分批退火的样品的可成形性与本发明钢材对比时,观察到本发明钢材的可成形性参数在高可成形twip钢(参考钢e)的范围内并比常规dh1000(参考钢d)高得多。甚至当退火仅4小时时钢c的双轴拉伸应变高于常规dh1000的那些。本发明钢材的这种高的可冷成形性是因为高分数的亚稳残余奥氏体与高mn和c富集,其在本发明钢材中通过本发明加工步骤实现。
[0163]
在表8中显示在650℃下退火10小时的钢b的平整对机械性质的影响。明显的是屈服点伸长率随着不断提高的平整压下而降低。使用2%压下,屈服点伸长率消失。拉伸性质没有过多改变,仍在本发明要求保护的范围内。最重要地,甚至至多5%厚度压下,应变硬化指数也保持高。因此,在至多5%平整的情况下,屈服点伸长率的这种消除而没有机械性质
明显改变将使本发明的钢带甚至更加可冷成形,因为这将降低拉伸成型期间应变集中的风险以及成型制品表面上的拉伸痕迹(stretcher mark)。
[0164]
表1:钢的组成(以重量%计)
[0165]
钢cmnsialpsbcrmonicua0.0947.150.201.540.0010.00140.00010.0030.010.00150.02b0.137.320.221.570.0010.00110.00020.0040.0010.0020.03c0.169.810.191.400.0020.00180.00010.0240.0010.0140.03d0.7214.50.250.050.0020.00120.00030.0300.0020.0030.03e0.152.241.00.0330.0010.00010.00020.0020.0010.0160.02
[0166][0167][0168]
表2:在热轧带材的中间分批退火之后的相分数
[0169]
钢铁素体(体积%)残余奥氏体(体积%)马氏体(体积%)a83.314.42.3b79.518.42.1c71.628.40
[0170]
表3:在冷轧带材的最终分批退火之后的相分数和平均奥氏体和铁素体晶粒尺寸
[0171][0172]
表4:冷轧材料的最终退火之后在残余奥氏体中的锰和碳富集
[0173][0174]
表5:在冷轧钢的退火之后钢的拉伸性质
[0175][0176]
表6:参考钢的拉伸性质和显微组织
[0177][0178]
表7:在最终退火之后钢的可成形性参数
[0179][0180]
表8:钢b在热处理至最好可成形条件之后施用的平整条件中的拉伸性质
[0181]