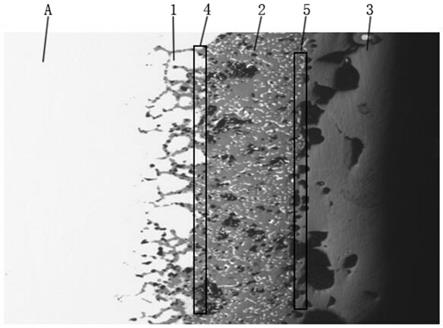
1.本发明涉及一种钢管穿孔顶头及制备方法。
背景技术:2.随着无缝钢管行业竞争加剧,国内外无缝钢管生产企业都在开发高附加值产品,316、2cr13这类材质的钢管耐高温,抗腐蚀性能好,被广泛应用于深海油田、和特殊环境油气管道。但由于这类材质合金含量高、高温强度好,一般只能在专业的生产线上生产。开发高合金材质无缝钢管产品穿孔过程中需要是无缝钢管生产中的关键工模具,在专业生产线上穿孔工序使用的钼基合金陶瓷顶头,高温强度高,但怕急冷急热工况、易碎裂,不适用于普通穿孔机组。在普通穿孔机组上穿轧316、2cr13这类高合金管使用普通顶头其寿命只有1~2支,对无缝钢管的质量、生产效率以及工厂效益都有重要影响,因此研制适合于普通穿孔机组上穿轧高合金管的顶头是无缝钢管生产中的这个比较重要的课题。
3.申请公布号cn101070581a公开了一种用作穿轧不锈钢管的顶头材质,化学成分为:c:0.19~0.39%、si:0.1~1.0%、mn:0.1~0.9%、cr:0.2~1.4%、ni:0.35~2.0%、mo:0.3~2.3%、w:0.5~4%、co:0.3~1.8%、nb:0.1~1.3%,该材质穿孔顶头用于宝钢140机组上穿轧2cr13材质钢管时寿命4~5支,用于天津460机组上穿轧2cr13材质钢管时寿命只有2~3支,还需改进。
4.申请公布号cn105369151a公开了一种用作穿轧不锈钢管的顶头材质,化学成分为:c:0.10~0.25%、si:0.05~0.80%、mn:0.20~1.00%、cr:1.0~2.0%、ni:2.5~3.5%、mo 2.5~3.5%、w:2.5~3.5%、nb:0.07~0.40%、ti:0.03~0.40%,该材质在国内也有使用记录,穿孔顶头用于穿轧2cr13材质钢管时寿命2~3支,未取得明显效果,而且顶头寿命不稳定。
5.申请公布号cn104685085a公开了一种用作穿轧不锈钢管的顶头材质,c:0.08~0.3%、si:0.1~1.0%、mn:0.2~1.5%、ni:0.2~2.0%,而且含有合计为1.5%~8%的w、mo之中的1种或2种。该方案中w含量较高,因w氧化后生成w2o3体积膨胀比大,造成氧化膜附着效果差、容易脱落,达不到保护顶头的效果。
6.申请公布号cn104213069a公开了一种表面刻槽处理从新型顶头,通过表面刻槽预处理后再氧化达到增加有效氧化层厚度,从而实现穿轧高合金钢管的目的。该专利未考虑从材料角度提升顶头本体性能。
技术实现要素:7.本发明提供一种强度高、生成氧化膜附着性能好的钢管穿孔顶头及制备方法。
8.钢管穿孔顶头,钢管穿孔顶头的成分组成按质量百分比计算,含有:
9.c:0.25~0.35%;
10.si:0.30~0.80%;
11.mn:0.40~0.80%;
12.cr:0.50~1.20%;
13.ni:2.00~4.50%;
14.mo:1.00~2.50%;
15.w:2.50~7.50%;
16.al:0.80~1.20%;
17.余量为铁及不可避免的杂质;
18.其中w、mo含量比例为:x=w/mo=1.5~3.0;
19.w+mo元素含量比例为:w+x*mo=2.5~15.0。
20.进一步地,所述w、mo含量比例为x=w/mo=2.0~2.2。
21.进一步地,所述w+x*mo=8.0~11.0。
22.一种钢管穿孔顶头的制备方法,包括以下步骤:
23.将配料好的成分制成顶头毛坯;
24.球化退火热处理,将顶头毛坯加热至760℃退火,保温8小时后,冷却到600℃,保温5小时,随后随炉空冷至350℃;
25.按所需规格顶头形状加工,并进行表面刻槽加工;
26.表面氧化热处理,将顶头表面迅速加热至900~1050℃,在弱氧化性气氛下保温4~6小时,然后空冷,即得到成品顶头。
27.本发明的设计原理为:
28.1、ni的含量为2.0~4.50,镍元素的加入可提高材料的韧性,保证提高硬度后在急冷急热条件下不开裂;同时改善顶头氧化处理时氧化膜的塑性,使氧化膜更牢固。
29.2、在合金中加入含量为1.0~2.5的mo元素,含量为2.5~7.5的w元素,这两种元素都是强碳化物形成元素,增加mo和w的含量使组织得到强化,同时提高热强性能、耐磨性能和热稳定性。
30.3、加入含量为0.8~1.2的al元素,al能细化晶粒,控制晶粒开始粗化的温度,能有效提高钢的可磨削性能和高温强度;al的加入使顶头的表面经氧化处理后的氧化膜致密,且与顶头基体结合牢固。
31.4、本发明控制w和mo元素含量比例,是利用mo元素在提高钢的高温强度方面的作用是相似的,但mo的氧化物在较低温度下(520~720℃)就挥发掉,形成孔洞,有利于氧原子继续向用户膜内扩散,使氧化膜与基体的结合面更粗糙、结合更牢固;同时,给w的氧化物体积膨胀腾出空间,减小氧化膜因体积膨胀产生裂纹导致氧化膜脱落的风险。
32.本发明的优点为:由于增加了mo和w元素的含量,同时加入了适量al元素,提高了材料的强度、耐磨性能、硬度、塑性和热稳定性,使用该材料制作顶头,可经热处理后使其表面形成致密的氧化膜,使顶头穿轧2cr13材质钢管的寿命大幅度提高。
附图说明
33.图1为试样的金相在显微镜下放大后的示意图。
具体实施方式
34.钢管穿孔顶头,钢管穿孔顶头的成分组成按质量百分比计算,含有:
35.c:0.25~0.35%;
36.si:0.30~0.80%;
37.mn:0.40~0.80%;
38.cr:0.50~1.20%;
39.ni:2.00~4.50%;
40.mo:1.00~2.50%;
41.w:2.50~7.50%;
42.al:0.80~1.20%;
43.余量为铁及不可避免的杂质;
44.其中w、mo含量比例为:x=w/mo=1.5~3.0;
45.w+mo元素含量比例为:w+x*mo=2.5~15.0。
46.所述w、mo含量比例为x=w/mo=2.0~2.2。
47.所述w+x*mo=8.0~11.0。
48.本发明的钢管穿孔顶头,按方案1
‑
8生产的顶头实例,其组成成分及各组分的重量百分比为(见表1):
49.表1
[0050][0051]
余量为铁及不可避免的微量杂质。
[0052]
一种钢管穿孔顶头的制备方法,包括以下步骤:
[0053]
根据上述表1中的任意一种配比将配料好的成分制成顶头毛坯;
[0054]
球化退火热处理,将顶头毛坯加热至760℃退火,保温8小时后,冷却到600℃,保温5小时,随后随炉空冷至350℃;
[0055]
按所需规格顶头形状加工,并进行表面刻槽加工;
[0056]
表面氧化热处理,将顶头表面迅速加热至900~1050℃,在弱氧化性气氛下保温4~6小时,然后空冷,即得到成品顶头。
[0057]
在本发明的新材料制造的顶头在第一工厂258机组穿管试验中,轧2cr13材质钢管
的寿命情况如下:
[0058][0059]
采用本发明的新材料制造的直径269规格的顶头在第一工厂的460机组穿管试验中,轧2cr13材质钢管的寿命情况如下:方案1,寿命5支;方案2,寿命12支;方案4,寿命15支。
[0060]
采用本发明的方案2材料制造的直径247、253、263规格的顶头在第二工厂穿管试验中,轧2cr13材质钢管的寿命均大于10支。
[0061]
比目前采用的其他高合金顶头3~5次/只的使用寿命提高了3~5倍以上,大大提高了在普通穿孔机组上轧制2cr13等高合金管的生产效率,降低了钢管废品率。
[0062]
另外,采用上述方法制备的钢管穿孔顶头,对于其表面的氧化膜是否合格,采用以下步骤进行评定:
[0063]
(一)试样的制备
[0064]
(a1)试块准备:取与顶头本体同材质、同工艺状态的材料加工成试块。
[0065]
优选地,试块的直径为20
‑
60mm,试块的长度为30
‑
80mm(根据顶头规格按一定比例设计试块尺寸),要求试块表面粗糙度与顶头表面一致。试块形状可以是方形或圆柱形状,但最好是圆柱形,这样的试块经氧化处理后,氧化膜内的应力状态与顶头相似,更具代表性。
[0066]
(b1)试块的氧化:将准备好的试块随同被检测顶头本体一起装炉氧化,以在试块以及各个顶头本体的表面分别形成氧化膜后,将试块与顶头本体从炉中取出;所述氧化膜包括过渡区1、外层氧化膜3以及位于过渡区1与外层氧化膜3之间的内层氧化膜2。
[0067]
优选地,试块装炉时放在料筐中相对顶头本体的中间位置,确保试块的氧化质量可以代表顶头本体的氧化质量,以使试块表面生成的氧化膜状态与同炉处理的顶头本体相近。
[0068]
如图1,在显微镜下观察,氧化膜结构从内向外依次为:过渡区1、内层氧化膜2、外层氧化膜3,过渡区1为半氧化状态,呈棘爪状或树根状的氧化物与脱碳状态的基体共存,视过渡区1为内层氧化膜2的一部分。内层氧化膜2与外层氧化膜之间有气孔密集的分界线,一般以视场内气孔率突变的位置作为氧化膜内外层氧化膜分界线。
[0069]
外层氧化膜3主要成分为fe2o3,结构比较松脆,易脱落。在穿孔过程中,其保护作用不大,一般首次使用后就完全脱落,但外层氧化膜3是氧化处理工艺形成氧化膜过程中的必然产物。
[0070]
内层氧化膜2主要成分为feo,在穿孔轧制过程中,会被碾压成粉末然后与基体粘合成非常致密的氧化膜保护层,这是顶头表面氧化膜的关键部分。
[0071]
(c1)金相试样的制备:将形成有氧化膜的试块切割得到试片,选择试片上氧化膜完好的位置近表面处切取试样用于金相检测。
[0072]
优选地,先在试块中间部位线切割切取厚度为10
‑
15mm的试片,优先切取厚度为15mm的试片,然后在选择氧化膜完好的位置近表面处切取宽度为10
‑
15mm的试样用于金相
检测,其中用于金相检测的面与试块外表面(待检测的氧化膜表面)垂直。
[0073]
(二)测量内层氧化膜的厚度
[0074]
将试样在金相显微镜下放大n倍以获得试样的金相图片,n的值为90至110,本实施例中,n的值优先采用100。在金相图片上通过图像处理及分析软件设置第一评判框4,将第一评判框4平移到内层氧化膜2与过渡区1之间且第一评判框4内氧化物面积占比为40
‑
60%的第一位置;以及设置第二评判框5,将第二评判框5平移到内层氧化膜2与外层氧化膜3之间且第二评判框5内的气孔面积占比为40
‑
60%的第二位置;通过图像处理及分析软件测量第一评判框5与第二评判框6的之间的间距离以获得内层氧化膜2的厚度。
[0075]
本实施例中的图像处理及分析软件优先采用image
‑
pro plus,image
‑
pro plus是一款功能强大的2d和3d图像处理、增强和分析软件,具有丰富的测量和定制功能。它包含了丰富的增强和测量工具,并允许用户自行编写针对特定应用的宏和插件。本实施例中,第一评判框和第二评判框的长为10μm,高为500μm。
[0076]
如图1所示,在金相显微镜下放大100倍观察,将第一评判框从内侧向外平移到内层氧化膜2与过渡区1交界区域,当位于第一评判框4内氧化物的面积占比为50%时定位为第一位置。同样的方法,将第二评判框5从内向外平移到内层氧化膜2与外层氧化膜3交界区域,当位于第二评判框5内的气孔面积占比为50%时定位为第二位置,测量两评定框之间的间距离即为内层氧化膜2厚度。
[0077]
内层氧化膜2的厚度理论上越厚越好,一般要求不小于0.1mm,即当内层氧化膜2的厚度小于0.1mm时,试块的氧化是不合格的,随之也就表明随试块同炉氧化出来的顶头本体也是不合格的。
[0078]
进一步地,本发明还对内层氧化膜2与试样基体a结合状态进行评定,具体如下:
[0079]
所述过渡区1与内层氧化膜2的结合部呈锯齿状或高低起伏状,所述过渡区1由若干棘爪状或树根状的半氧化物组成,从过渡区1中选取多个半氧化物的顶点,通过图像处理及分析软件测量这些顶点至第一评判框4之间的垂直距离并计算出第一平均值;从过渡区1中选取多个半氧化物,通过图像处理及分析软件测量这些半氧化物之间的间距(每相邻两个半氧化物之间的间距)并计算出第二平均值,以得出内层氧化膜与试块基体结合状态。
[0080]
表1(评级表)
[0081][0082]
在本公司内规定,对于内层氧化膜2与试样基体a结合状态的级别评定,根据表1,内层氧化膜2与基体结合状态分为5级。x1.0级非常好,x2.0级较好,x3.0级一般,x4.0级较差(能用),x5.0级很差(不能用)。
[0083]
进一步地,本发明还通过图像处理及分析软件计算金相图片上内层氧化膜2中的孔洞在内层氧化膜中的百分比,以得出内层氧化膜2的致密度。如下表2:
[0084]
表2(内层氧化层致密度评定分级)
[0085]
[0086][0087]
内层氧化膜致密度分为5级。m1.0级非常好,m2.0级较好,m3.0级一般,m4.0级较差(能用),m5.0级很差(不能用)。
[0088]
因此,我们设计的氧化膜质量指标主要针对内层氧化膜质量进行评判,具体包括:内层氧化膜厚度、内层氧化膜与基体结合状态评判、内层氧化膜致密度评判。
[0089]
以上所述仅为本发明示意性的具体实施方式,并非用于限定本发明的范围,任何本领域的技术人员,在不脱离本发明的构思和原则的前提下做出的等同变化与修改,均应属于本发明的保护范围。