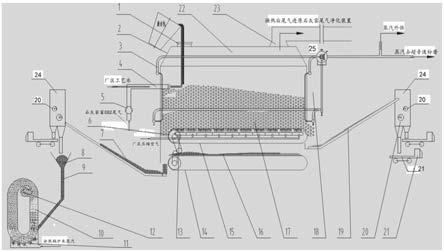
1.本发明属于冶金固废资源化利用技术领域,具体涉及一种转炉渣联用淬化消碱磁化热回收装置和方法。
背景技术:2.公开该背景技术部分的信息仅仅旨在增加对本发明的总体背景的理解,而不必然被视为承认或以任何形式暗示该信息构成已经成为本领域一般技术人员所公知的现有技术。
3.我国主要采用长流程转炉炼钢工艺,转炉钢渣占钢渣总量的88%,处理工艺主要采用的水淬热闷法,主要矿物组分为钙镁橄榄石(cao
·
mgo
·
sio2)、硅酸二钙(c2s)、硅酸三钙(c3s)、钙镁蔷薇辉石(3cao
·
mgo
·
2sio2)、铁酸二钙(2cao
·
fe2o3)、金属氧化物相(ro),其数量每约1.2亿t增长,处理过程中环境友好度低、铁、热回收效果差、资源化程度非常不理想,大量堆存或填埋破坏生态环境,环保问题突出,严重制约钢铁工业实现全面绿色制造。
4.当前转炉渣资源化利用存在的突出问题为:
①
转炉渣存在游离氧化钙(f
‑
cao)和游离氧化镁(f
‑
mgo)以及微量的fes和mns,遇水易形成碱性化合物,用作水泥材料后安定性、体积稳定性差;
②
钢渣中含20~30%的基本无胶凝活性的feo
x
(以fe2o3计),使得c3s、c2s相对含量减少,且c3s、c2s晶体发育完整、缺陷少、胶凝活性差,也影响其利用率提升;
③
钢渣中的铁赋存相可通过弱磁选的金属铁、磁铁矿占比小,无磁性的褐铁矿、赤铁矿占比超过60%,除铁后钢渣全铁含量仍高达5~30%;
④
熔融钢渣蕴含大量的热能(~1.2gj/t渣,约41kg标准煤热值),现处理工艺(水淬、热闷、滚筒、粒化轮法)多采用大量的水介质对其急冷,产生热水或蒸汽,热介质热量低(一般<100℃)且含有大量颗粒杂质和悬浮物,品味差并易造成换热器、输送管道结垢,整体热能回收率实际非常不理想。
技术实现要素:5.针对上述现有技术中存在的问题,本发明的目的是提供一种转炉渣联用淬化消碱磁化热回收装置和方法。基于“渣、铁、热“统筹资源化利用目标,提供一种转炉渣h2o/co2/air联用淬化消碱磁化热回收装置。
6.为了解决以上技术问题,本发明的技术方案为:
7.一种转炉渣联用淬化消碱磁化热回收装置,包括废气/水双流体喷射装置、联淬室、双层气流喷吹磁化分选传输机,联淬室为封闭的空腔结构,联淬室的顶部一端设置溢流槽,另一端设置气体排出口,废气/水双流体喷射装置包括进料筒和喷嘴结构,喷嘴结构位于联淬室的内部,进料筒部分位于联淬室的外部,位于联淬室外部的进料筒设置气体进口和液体进口,进入的气体中含有二氧化碳,喷嘴结构位于溢流槽的正下方,双层气流喷吹磁化分选传输机位于联淬室的底部。
8.熔融钢渣从联淬室的顶部溢流槽进入到联淬室中,废气/水双流体喷射装置向联
淬室中喷入气水混合物,与熔融钢渣接触,对熔融钢渣形成高压冲击、分割、粒化与急冷高温碳酸化消碱的作用,钢渣急冷淬化形成钢渣,落入到双层气流喷吹磁化分选传输机上。
9.气水混合物受热后形成气态通过气态排出口排出,实现了熔融钢渣热能的回收,消碱的作用。并且形成了固态钢渣。解决了钢渣中含有的游离氧化钙(f
‑
cao)和游离氧化镁(f
‑
mgo)以及微量的fes和mns,遇水易形成碱性化合物,用作水泥材料后安定性、体积稳定性差的问题;解决了熔融钢渣的热能回收的问题;
10.气水混合物与熔融钢渣直接接触,钢渣急冷淬化,气水混合物受热形成气体,这个过程中,该过程形成的气体与常规水淬工艺形成的剧烈热流相比,在气体流动在辐射对流余热锅炉受热面时夹带钢渣淬化后的钢渣颗粒大幅降低,受热面同步吸收了熔融钢渣的辐射换热,热回收效率显著提升,所以解决了热能回收率不高的问题。
11.第二方面,利用上述的转炉渣联用淬化消碱磁化热回收装置进行转炉渣联用淬化消碱磁化热回收的方法,具体步骤为:
12.熔融钢渣通过溢流槽进入到联淬室中,废气/水双流体喷射装置喷出气水混合物,在溢流槽的下方,冲击熔融钢渣,使钢渣急冷淬化,气水混合物受热成为气体从联淬室的顶部排出;
13.钢渣淬化后的粗颗粒从联淬室一侧底部排出,细颗粒通过双层气流喷吹磁化分选传输机后排出。
14.本发明一个或多个技术方案具有以下有益效果:
15.围绕“渣、铁、热“统筹资源化利用目标,在转炉渣h2o/co2/air联用淬化消碱磁化热回收装置内同步完成钢渣淬化造粒、粒化钢渣消碱、粒化钢渣磁化除铁、熔融钢渣热回收,在钢渣品性方面形成了弱碱性、低ro相、高c3s/c2s含量且富含高含量非晶态组分、优质高值、不同尺寸<3mm、<1mm、<70微米三级活性钢渣产品,可用于分别用于建材集料、骨料、原料;熔融钢渣热量经辐射和对流换热被余热锅炉吸收,转化为高温高压蒸汽,热能回收率>75%,蒸汽可直接外供或为钢渣在超音速蒸汽粉磨中磨制钢渣微粉提供动力,“渣、铁、热“统筹资源化利用程度高,具备良好的市场应用前景。
附图说明
16.构成本发明的一部分的说明书附图用来提供对本申请的进一步理解,本发明的示意性实施例及其说明用于解释本发明,并不构成对本发明的不当限定。
17.图1为转炉渣联用淬化消碱磁化热回收装置的结构示意图;
18.其中,1、溢流槽,2、外壳,3、热管,4、废气/水双流体喷射装置,5、风机,6、双层气流喷吹磁化分选传输机,7、细渣输送机,8、料斗,9、溜槽,10、超音速蒸汽粉磨,11、拉瓦尔喷嘴,12、钢渣微粉,13、空气喷嘴,14、输送带,15、上层皮带,16、细钢渣,17、粗钢渣,18、辐射对流余热锅炉,19、粗渣输送机,20、磁选机,21、运输车,22、联淬室,23、气体排出口,24、渣仓,25、汽包。
具体实施方式
19.应该指出,以下详细说明都是例示性的,旨在对本发明提供进一步的说明。除非另有指明,本文使用的所有技术和科学术语具有与本发明所属技术领域的普通技术人员通常
理解的相同含义。
20.需要注意的是,这里所使用的术语仅是为了描述具体实施方式,而非意图限制根据本申请的示例性实施方式。如在这里所使用的,除非上下文另外明确指出,否则单数形式也意图包括复数形式,此外,还应当理解的是,当在本说明书中使用术语“包含”和/或“包括”时,其指明存在特征、步骤、操作、器件、组件和/或它们的组合。
21.一种转炉渣联用淬化消碱磁化热回收装置,包括废气/水双流体喷射装置、联淬室、双层气流喷吹磁化分选传输机,联淬室为封闭的空腔结构,联淬室的顶部一端设置溢流槽,另一端设置气体排出口,废气/水双流体喷射装置包括进料筒和喷嘴结构,喷嘴结构位于联淬室的内部,进料筒部分位于联淬室的外部,位于联淬室外部的进料筒设置气体进口和液体进口,进入的气体中含有二氧化碳,喷嘴结构位于溢流槽的正下方,双层气流喷吹磁化分选传输机位于联淬室的底部。
22.在本发明的一些实施方式中,废气/水双流体喷射装置的气体进口与风机连接,风机进口进入钢厂石灰窑排放的富含co2的废烟气。充分利用废烟气中的二氧化碳或者其它富含二氧化碳的气体,与熔融钢渣接触后,熔融钢渣中游离氧化钙(f
‑
cao)和游离氧化镁(f
‑
mgo)以及微量的fes和mns,遇水形成碱性化合物,然后碳酸与其进行中和,所以具有消减的作用。
23.在本发明的一些实施方式中,废气/水双流体喷射装置设置若干个,在同一高度横向排列。设置多个废气/水双流体喷射装置,实现提高熔融钢渣的消碱和回收处理效果。
24.在本发明的一些实施方式中,还包括辐射对流余热锅炉,辐射对流余热锅炉与联淬室通过热管连接,辐射对流余热锅炉的水进入到热管中,热管穿过联淬室设置,分别穿过联淬室的上部和下部。
25.利用辐射对流余热锅炉进行热量回收,急冷淬化后的颗粒与热管接触换热,气体流动与热管换热,所以热管中的液体温度升高,部分成为气体,成为气体后,部分作为蒸汽外供,部分进入到超音速粉磨装置中再利用。
26.在本发明的一些实施方式中,所述双层气流喷吹磁化分选传输机包括上层皮带和下层输送带,上层皮带和下层输送带通过齿轮联动,上层皮带、下层输送带分别绕着转动辊转动,由一套齿轮啮合提供动力,上层皮带上设置落粉孔。绝大部分粒度小于1mm钢渣在微湍动过程中从孔隙落到下层皮带,完成二次分选。
27.可选的,上层皮带的落粉孔的直径为0.8
‑
1.2mm,孔隙率30~60%。
28.在本发明的一些实施方式中,上层皮带的内侧阵列设置空气喷嘴,喷吹作用区域50~60%。空气喷嘴喷入空气,细颗粒进入上层皮带的内侧,进一步降温,细颗粒中的氧化铁,在空气中氧气的作用下,发生不完全氧化反应。
29.在本发明的一些实施方式中,还包括输送带、细渣仓、磁选机,输送带位于双层气流喷吹磁化分选传输机的下方,输送带的一侧设置细渣输送机,细渣输送机与细渣仓连接,细渣仓与磁选机连接。
30.在本发明的一些实施方式中,还包括超音速蒸汽粉磨装置,位于磁选机的下方,磁选机的出料口通过料斗和溜槽与超音速蒸汽粉磨装置连接。
31.在本发明的一些实施方式中,双层气流喷吹磁化分选传输机的一端与联淬室的侧壁设置粗料出口。
32.在本发明的一些实施方式中,还包括粗渣输送机、粗渣仓、磁选机,粗料出口的一侧设置粗渣输送机,粗渣输送机与粗渣仓连接,粗渣仓与磁选机连接。
33.细渣和粗渣排出后经过磁选分离后排出。
34.第二方面,利用上述的转炉渣联用淬化消碱磁化热回收装置进行转炉渣联用淬化消碱磁化热回收的方法,具体步骤为:
35.熔融钢渣通过溢流槽进入到联淬室中,废气/水双流体喷射装置喷出气水混合物,在溢流槽的下方,冲击熔融钢渣,使钢渣急冷淬化,气水混合物受热成为气体从联淬室的顶部排出;
36.钢渣淬化后的粗颗粒从联淬室一侧底部排出,细颗粒通过双层气流喷吹磁化分选传输机后排出。
37.在本发明的一些实施方式中,粗颗粒<3mm,细颗粒小于1mm。
38.在本发明的一些实施方式中,细颗粒在双层气流喷吹磁化分选传输机中进行不完全氧化反应,得到磁铁矿。
39.在本发明的一些实施方式中,粗颗粒和细颗粒排出后通过磁选去除铁相。
40.装置中固碳反应过程采用钢厂自身石灰窑尾气和工业水形成雾化水气混合物对熔融钢渣进行快速淬化、碳酸化消碱;钢渣消碱改性后在装置下部的输送机对feo
x
组分进行磁化,与限定量常温空气接触,在二次冷却的同时,完成干燥欠氧环境下feo发生不完全氧化反应,转化为磁铁矿,后续磁选有助于降低钢渣全铁含量并增加易磨性;辐射对流余热锅炉将高温钢渣的辐射热及干燥热载气的显热转化为高温高压蒸汽,热回收率显著改善,换热后的热载气仍进入钢厂现有石灰窑尾气净化装备,环境友好度极高;气水淬化钢渣粒度小于3mm,在上层输送机上进行不完全氧化反应同步完成初步筛分,大幅降低原钢渣处理系统的破碎筛分出力;钢渣经固碳消碱磁化后,feox含量降低,c3s、c2s相对含量增加,钢渣胶凝活性、安定性大幅提升;余热锅炉产生的高温高压蒸汽部分用于推动超音速蒸汽粉磨,钢渣进行高速对撞、剪切,制作钢渣微粉同时进行气流分选,细颗粒非晶态组分增加活性良好,可直接可用作水泥原料,富集fe、mg、mn金属元素的粗颗粒磁选后可用作细集料替代矿粉,钢渣高值利用程度大幅提升。
41.下面结合实施例对本发明进一步说明
42.实施例1
43.主要包括:废气/水双流体喷射装置4、联淬室22、辐射对流余热锅炉18、双层气流喷吹磁化分选传输机6、超音速蒸汽粉磨10构成。其联淬室22由耐温防火溢流槽1和保温钢制外壳2制成,溢流槽1外部钢壳焊接在保温钢制外壳2的左上顶部,气体排出口23连接,换热尾气管道焊接在保温钢制外壳2的右上顶部;双层气流喷吹磁化分选传输机6布置在联淬室22的下部,承接淬化钢渣;辐射对流余热锅炉18内的热管3充满水,接受熔融钢渣辐射热及冷却钢渣空气显热后转化为高质蒸汽,部分蒸汽可外供,部分进入超音速蒸汽粉磨10制作钢渣微粉;淬化钢渣颗粒落到双层气流喷吹磁化分选传输机6的上层皮带15(耐热橡胶)上,<1mm细钢渣16经上层皮带15的孔隙结构落到下层常规耐热橡胶输送带14上;<3mm粗钢渣17可直接经粗渣输送机19送至渣仓24,经磁选后用作建材集料;<1mm细钢渣16可经细渣输送机7直接至渣仓24,经磁选后用作建材集料和骨料;磁选后也可送至超音速蒸汽粉磨10制作钢渣微粉,用作建材原料。
44.本发明的实施例简述如下:熔融钢渣在渣水包内,用炉渣跨行车将渣水包吊起,渣缓慢倒入联淬室22左上部的耐温防火溢流槽1中,钢厂石灰窑排放的废烟气经风机5增压后与水经废气/水双流体喷射装置4,在联淬室22内对熔融态钢渣进行垂直高压冲击、分割、粒化与急冷高温碳酸化消碱,钢渣急冷淬化,形成<3mm粗钢渣17可直接经粗渣输送机19送至渣仓,经磁选机20磁选后被分类运输车21运至建材加工厂用作集料、表明骨料使用;淬化粗钢渣17首先落到双层气流喷吹磁化分选传输机6的上层耐热橡胶皮带15上,限定量厂区压缩空气经上层耐热橡胶皮带15下部阵列设置空气喷嘴13与粒化钢渣接触,在二次冷却的同时,完成干燥欠氧环境下feo的不完全氧化反应,转化为磁铁矿,绝大部分粒度小于1mm细钢渣16在微湍动过程中从上层耐热橡胶皮带15孔隙中落到下层常规耐热橡胶输送带14上;<1mm细钢渣16可经细渣输送机7直接至磁选机20后用作建材集料和骨料,也可落入超音速蒸汽粉磨10的进口料斗8经溜槽9送至超音速蒸汽粉磨10内,余热锅炉来的蒸汽经拉瓦尔喷嘴11进入超音速蒸汽粉磨10,气流带动钢渣高速剧烈对撞、剪切,粉碎后物料进入超音速蒸汽粉磨10上部形成的强制涡流中进行分级,成品钢渣微粉12及蒸汽进入后续的布袋除尘器收集,作为建材原料高值利用。辐射对流余热锅炉18内的热管3充满水,接受熔融钢渣辐射热及冷却钢渣空气显热后转化为高质蒸汽,蒸汽经过汽包25后,部分蒸汽可外供,部分蒸汽驱动超音速蒸汽粉磨10制粉。换热尾气管道经气体排出口23进入钢厂原有石灰窑尾气净化装备,环境友好度极高。
45.以上所述仅为本发明的优选实施例而已,并不用于限制本发明,对于本领域的技术人员来说,本发明可以有各种更改和变化。凡在本发明的精神和原则之内,所作的任何修改、等同替换、改进等,均应包含在本发明的保护范围之内。