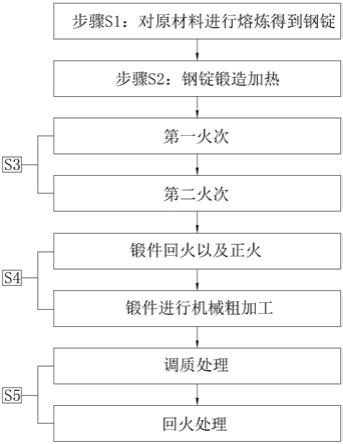
一种焊接结构件用c
‑
mn高强度钢锻件锻造及热处理工艺
技术领域
1.本发明涉及锻件处理领域,特别涉及一种焊接结构件用c
‑
mn高强度钢锻件锻造及热处理工艺。
背景技术:2.低合金高强度钢具有低成本、高强度、易焊接、易加工等特点。广泛应用于汽车制造,建筑结构和海洋工程等领域。随着现代科学技术的不断发展,在设计上对大尺寸构件的力学性能和组织均匀性提出了更高的要求。
3.伴随着国内风电技术的日趋成熟,风力发电机组装机功率也在不断的加大,这就意味着设备结构在不断增大。对于140米及以上的高塔筒,必须采用1000吨以上的履带吊或专用起重船舶,此类设备市场资源少、设备使用费用高、安装场地要求严,传统吊装模式已不能适应高塔架风电机组的吊装需求。为了满足国内高塔架风机的施工,国产化高塔筒风电安装用塔机也就应运而生。但是要求高塔架风电塔机具备良好的机械性能和极高的安全程度,也对于构成其的钢锻件也有更高的要求。目前,传统的低合金结构钢标准仅对厚度尺寸在120mm以下的产品提出了力学性能要求,现有的传统技术已不能满足大工件整体仍旧能保证高强度的要求。而对于大截面厚度的产品无取样及力学性能性能要求。为了满足设计要求的同时保证低成本、高强度、易焊接、易加工等要求。
技术实现要素:4.针对上述现有技术的缺点,本发明的目的是提供一种焊接结构件用c
‑
mn高强度钢锻件锻造及热处理工艺,其优点在于通过提高锻件内在质量,细化晶粒,提高热处理效果,保证产品整体机械性能提高,消除组织不均匀性,大大提供各项性能指标。
5.本发明的上述技术目的是通过以下技术方案得以实现的:
6.1.一种焊接结构件用c
‑
mn高强度钢锻件锻造及热处理工艺,包括以下步骤:
7.步骤s1:对原材料进行熔炼得到钢锭;
8.步骤s2:钢锭锻造加热;
9.步骤s3:钢锭锻造,锻造过程包括两个火次:
10.(1)第一火次:锻造温度为1180
‑
1220℃;在第一火次中,将钢锭依次进行拔长、镦粗;终锻温度≥800℃;
11.(2)第二火次:锻造温度为1150
‑
1180℃;在第二火次中,将钢锭拔长、镦粗成型;终锻温度≥780℃;完成第二火次后,将锻件立即敞开空冷处理;
12.步骤s4:锻后热处理,具体包括:
13.(1)锻件回火以及正火,之后将锻件放在流动的空气中冷却到室温,之后回火处理;
14.(2)锻件进行机械粗加工;
15.步骤s5:锻件进行性能热处理,包括以下步骤:
16.(1)调质处理:锻件加热到900
‑
920℃,之后保温一段时间;
17.(2)回火处理:锻件加热到回火温度480
‑
520℃,之后保温。
18.进一步的,所述锻件中各化学元素的成份重量百分比为:c:≤0.18%,mn:≤2.0%,p:≤0.030%,s≤0.025%,si:≤0.6%,cr:≤0.8%,ni:≤0.8%,n:≤0.015
‑
0.025%;mo:≤0.30%,b:≤0.004%,als:不小于0.015,v:0.01~0.12%,nb:0.01~0.11%,ti:0.006~0.05,,其中als,v,nb,ti可单独或组合加入,保证至少一种合金元素含量不小于规定含量下限,余量为fe及杂质。
19.进一步的,在步骤s1中,对原材料进行电弧炉和炉外精炼的处理过程。
20.进一步的,在步骤s2中,包括以下步骤:(1)、装炉:钢锭装炉温度≤600℃;(2)、升温:钢锭按加热最大功率升温到400
‑
850℃,(3)、保温:分阶段进行保温,第一阶段保温温度为850℃;第二阶段保温温度为1220℃;每个保温阶段的保温时间与钢锭厚度正相关,每200mm厚度的钢锭保温1.2~1.5h。
21.进一步的,在步骤s3的第一火次中,完成第一火次后,将钢锭放入锻造加热炉中进行加热,加热温度为1180
‑
1200℃;加热时间与钢锭厚度正相关,每200mm厚度的钢锭加热1~1.2h。
22.进一步的,在步骤s3的第一火次中,总拔长比>2.5;总镦粗比>2.2。
23.进一步的,在步骤s3中的第二火次中,拔长比>2.5,镦粗比>2.5。
24.进一步的,在步骤s5的调质过程中,保温时间与锻件厚度正相关,每1mm厚度的锻件保温1.5~1.7min,保温结束后出炉将锻件水冷,水温必须小于35℃。
25.进一步的,在步骤s5的调质过程中,调质过程重复进行,水冷过程的重复次数≤2。
26.进一步的,在步骤s5的回火过程中,保温时间与锻件厚度正相关,每1mm厚度的锻件保温2.3~3min。
27.综上所述,本发明具有以下有益效果:
28.1.本发明通过熔炼步骤,将锻件中的化学元素的组份严格控制在要求范围内,本发明调整了cr,ni,mn,v的含量,适当将上述元素的含量做了限定,此部分元素有提高强度增加产品淬透性的效果。通过控制元素组分将碳当量(cev)控制在0.47~0.48%同时保证了材料的焊接性能。
29.2.本发明通过锻造加热步骤,有效减少了钢锭中魏氏体的产生,优化了钢锭的锻造性能。
30.3.本发明的锻造包括两个火次过程,第一火次使得锻件达到了加大的锻造比,通过大的锻比改善钢的内部质量,消除铸态组织。使得锻件内部组织均匀,改善或消除疏松及偏析现象。材料内部夹杂物也可有效锻小或锻碎。同时经过控制火次间的加热及终锻温度使锻件晶粒度更加细化。锻件晶粒细化可提高各方面性能如提高韧性,增加抗疲劳性从而提高使用寿命。
31.4.发明在锻造后冷却步骤中,锻后及时空冷控制了锻件的晶粒不再二次长大。同时控制冷却后的表面温度及时进行锻后热处理即正火以及回火,利于材料内部有害残余气体的排出。
32.5.控制冷却液的浓度及温度,有效保证加热均匀性及快速冷却的效果,即保证了产品的内部组织均匀又有效提高了产品的淬透性,从而提高了产品的整体强度。
附图说明
33.图1是焊接结构件用c
‑
mn高强度钢锻件锻造及热处理工艺的步骤示意图;
34.图2是实验品1的金相图;
35.图3是实验品2的金相图;
36.图4是实验品3的金相图。
具体实施方式
37.为了使本发明的目的、技术方案及优点更加清楚明白,以下结合附图和具体实施方式对本发明提出的装置作进一步详细说明。根据下面说明,本发明的优点和特征将更清楚。需要说明的是,附图采用非常简化的形式且均使用非精准的比例,仅用以方便、明晰地辅助说明本发明实施方式的目的。为了使本发明的目的、特征和优点能够更加明显易懂,请参阅附图。须知,本说明书所附图式所绘示的结构、比例、大小等,均仅用以配合说明书所揭示的内容,以供熟悉此技术的人士了解与阅读,并非用以限定本发明实施的限定条件,故不具技术上的实质意义,任何结构的修饰、比例关系的改变或大小的调整,在不影响本发明所能产生的功效及所能达成的目的下,均应仍落在本发明所揭示的技术内容能涵盖的范围内。
38.实施例1:一种焊接结构件用c
‑
mn高强度钢锻件锻造及热处理工艺,锻件中各化学元素的成份重量百分比为:c:≤0.18%,mn:≤2.0%,p:≤0.030%,s≤0.025%,si:≤0.6%,cr:≤0.8%,ni:≤0.8%,n:≤0.015
‑
0.025%;mo:≤0.30%,b:≤0.004%,als:不小于0.015,v:0.01~0.12%,nb:0.01~0.11%,ti:0.006~0.05,,其中als,v,nb,ti可单独或组合加入,保证至少一种合金元素含量不小于规定含量下限,余量为fe及杂质。
39.如图1所示,工艺包括以下步骤:
40.步骤s1,对原材料进行熔炼得到钢锭。具体为对原材料进行电弧炉和炉外精炼的处理。
41.步骤s2,钢锭锻造加热,包括:(1)、装炉:钢锭装炉温度≤600℃;(2)、升温:钢锭按加热最大功率升温到400
‑
850℃,(3)、保温:分阶段进行保温,第一阶段保温温度为850℃;第二阶段保温温度为1220℃;每个保温阶段的保温时间与钢锭厚度正相关,每200mm厚度的钢锭保温1.2~1.5h。
42.步骤s3,锻造;锻造过程包括两个火次:
43.(1)第一火次:将钢锭加热到锻造温度1180℃,之后依次进行拔长、镦粗,总拔长比>2.5;总镦粗比>2.2,并且保证终锻温度≥800℃。完成第一火次后,将钢锭放入锻造加热炉中进行加热,加热温度为1180℃;加热时间与钢锭厚度正相关,每200mm厚度的钢锭加热1~1.2h。第一火次使得锻件达到了加大的锻造比,通过大的锻比改善钢的内部质量,消除铸态组织,进而使得锻件内部组织均匀,改善或消除疏松及偏析现象。
44.(2)第二火次:将钢锭加热到锻造温度1150℃,之后钢锭拔长、镦粗成型,拔长比>2.5,镦粗比>2.5,并且保证终锻温度≥780℃。完成第二火次后,将锻件立即敞开空冷处理。将锻件内部的夹杂物有效锻小或锻碎,并且通过控制火次的加热和终锻温度,使锻件的终锻温度更加细化,提高锻件各方面性能,增加抗疲劳性从而提高使用寿命。
45.步骤s4,锻后热处理,具体包括:
46.(1)锻件正火和回火处理:锻件正火,将锻件加热到温度区间910~920℃,正火后将锻件放至流动空气中冷却,锻件冷却至室温后再进行回火处理,将锻件加热到温度区间600~620℃。锻后及时空冷控制了锻件的晶粒不再二次长大。同时控制冷却后的表面温度及时进行锻后热处理即正火以及回火,利于材料内部有害残余气体的排出。
47.(2)锻件进行机械粗加工。
48.步骤s5,锻件进行性能热处理,包括以下步骤:
49.(1)调质处理:将锻件加热到900℃,之后保温一段时间,保温时间与锻件厚度正相关,每1mm厚度的锻件保温1.5~1.7min,保温结束后出炉将锻件水冷,水温必须小于35℃,控制冷却液的浓度及温度,有效保证加热均匀性及快速冷却的效果,即保证了产品的内部组织均匀又有效提高了产品的淬透性,从而提高了产品的整体强度。调质过程重复进行,水冷过程的重复次数≤2。
50.(2)回火过程:锻件加热到回火温度480℃,之后保温,保温时间与锻件厚度正相关,每1mm厚度的锻件保温2.3~3min。
51.实施例2:一种焊接结构件用c
‑
mn高强度钢锻件锻造及热处理工艺,与实施例1不同的步骤在于:
52.步骤s3,锻造;锻造过程包括两个火次:
53.(1)第一火次:将钢锭加热到锻造温度1200℃,之后依次进行拔长、镦粗,总拔长比>2.5;总镦粗比>2.2,并且保证终锻温度≥800℃。完成第一火次后,将钢锭放入锻造加热炉中进行加热,加热温度为1190℃;加热时间与钢锭厚度正相关,每200mm厚度的钢锭加热1~1.2h。
54.(2)第二火次:将钢锭加热到锻造温度1165℃,之后钢锭拔长、镦粗成型,拔长比>2.5,镦粗比>2.5,并且保证终锻温度≥780℃。完成第二火次后,将锻件立即敞开空冷处理。
55.步骤s5,锻件进行性能热处理,包括以下步骤:
56.(1)调质处理:将锻件加热到910℃,之后保温一段时间,保温时间与锻件厚度正相关,每1mm厚度的锻件保温1.5~1.7min,保温结束后出炉将锻件水冷,水温必须小于35℃。调质过程重复进行,水冷过程的重复次数≤2。
57.(2)回火过程:锻件加热到回火温度500℃,之后保温,保温时间与锻件厚度正相关,每1mm厚度的锻件保温2.3~3min。
58.实施例3:一种焊接结构件用c
‑
mn高强度钢锻件锻造及热处理工艺,与实施例1不同的步骤在于:
59.步骤s3,锻造;锻造过程包括两个火次:
60.(1)第一火次:将钢锭加热到锻造温度1220℃,之后依次进行拔长、镦粗,总拔长比>2.5;总镦粗比>2.2,并且保证终锻温度≥800℃。完成第一火次后,将钢锭放入锻造加热炉中进行加热,加热温度为1200℃;加热时间与钢锭厚度正相关,每200mm厚度的钢锭加热1~1.2h。
61.(2)第二火次:将钢锭加热到锻造温度1180℃,之后钢锭拔长、镦粗成型,拔长比>2.5,镦粗比>2.5,并且保证终锻温度≥780℃。完成第二火次后,将锻件立即敞开空冷处理。
62.步骤s5,锻件进行性能热处理,包括以下步骤:
63.(1)调质处理:将锻件加热到920℃,之后保温一段时间,保温时间与锻件厚度正相关,每1mm厚度的锻件保温1.5~1.7min,保温结束后出炉将锻件水冷,水温必须小于35℃。调质过程重复进行,水冷过程的重复次数≤2。
64.(2)回火过程:锻件加热到回火温度520℃,之后保温,保温时间与锻件厚度正相关,每1mm厚度的锻件保温2.3~3min。
65.锻件综合性能检测:
66.a、锻件综合力学实验:
67.1、实验组:从实施例1
‑
3中随机抽取一个锻件,分别记为实施品1、实验品2和实验品3进行实验。
68.2、实验结果见下表。
[0069][0070]
实验结果分析:锻件的抗拉强度平均为619.3mpa,符合标准,并且锻件的上下限差距为20mpa,说明通过本方法制备的锻件,性能稳定;锻件的屈服强度提升约5%
‑
10%;锻件的延伸率超越标准约10%,说明锻件具有更好的韧性,不易断裂;锻件的冲击功远远超过标准,说明锻件在抗冲击性能上有巨大的提升。
[0071]
a、锻件金相检测:
[0072]
1、锻件金相组织:实验组1金相组织见图2,晶粒度为7.5级;实验组2金相组织见图3,晶粒度为8级;实验组3金相组织见图4,晶粒度为8级。
[0073]
金相组织分析:所有锻件的晶粒度均大于7.5级,金相组织细密并均匀,没有明显的晶界断裂和缺陷。
[0074]
以上所述实施例的各技术特征可以进行任意的组合,为使描述简洁,未对上述实施例中的各个技术特征所有可能的组合都进行描述,然而,只要这些技术特征的组合不存在矛盾,都应当认为是本说明书记载的范围。
[0075]
以上所述实施例仅表达了本发明的几种实施方式,其描述较为具体和详细,但并
不能因此而理解为对发明专利范围的限制。应当指出的是,对于本领域的普通技术人员来说,在不脱离本发明构思的前提下,还可以做出若干变形和改进,这些都属于本发明的保护范围。因此,本发明专利的保护范围应以所附权利要求为准。