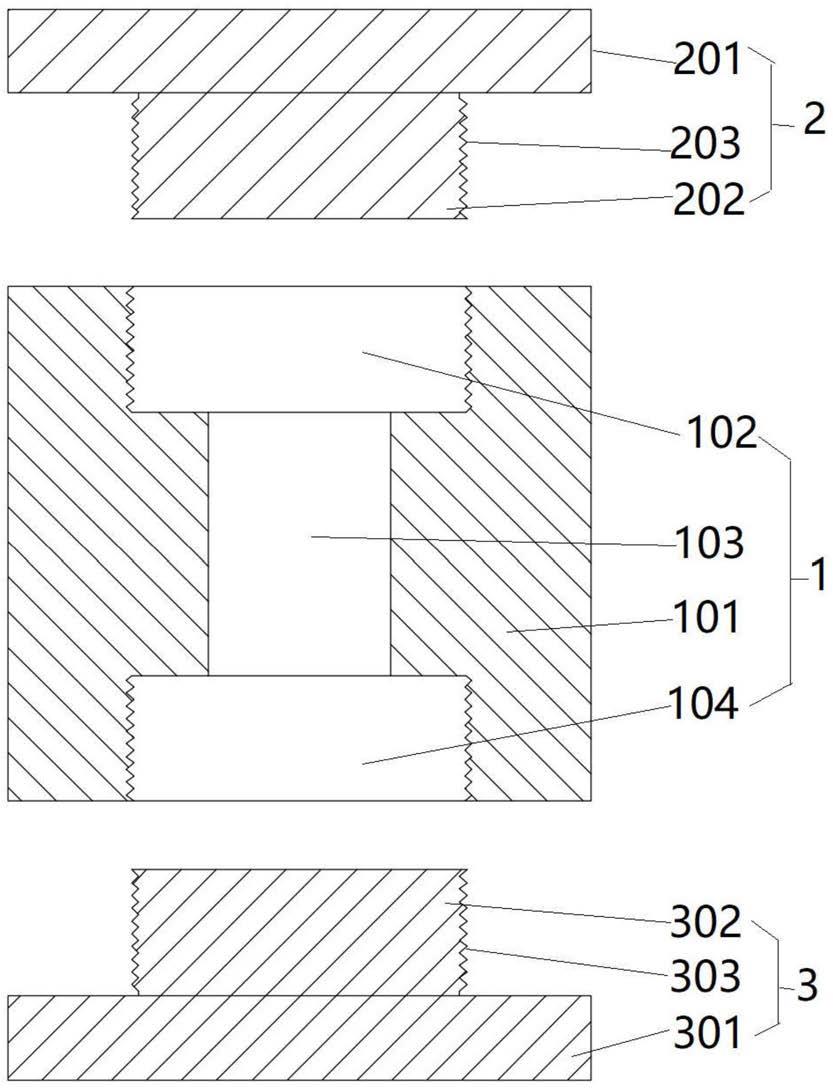
1.本发明涉及一种采用真空自耗电弧熔炼制备铍铜母合金的方法,属于金属材料制造领域。
背景技术:2.铍是一种轻金属元素,主要应于特种合金生产,对有色金属特别是铜、铝合金的强化效应明显,在航空、航天等工业领域有其特殊的价值,在国民经济各部门亦有广泛的应用。
3.目前,常见铍铜母合金生产工艺为大气非自耗电弧熔炼法,采用大气连通式石墨电极生产,其生产现场常需采用各种防护设备设施及措施,以更好地防护操作人员并保护环境,各生产企业投入巨大。该生产方式沿用了数十年,生产工艺比较稳定,为国民经济提供了可靠的原材料。但电弧温度高,碳热还原反应不光生成铍,更大量生成碳化铍。碳热还原反应生成铍后,由于其活性高,容易被氧化、挥发,造成铍的损耗,降低了铍金属的回收率,且污染车间内外的环境。另一方面,大气连通式生产方式,无法避免微小的铍颗粒进入环境,尽管量少,长年累月对生产人员的身体造成不可逆的影响亦不可忽略。故改进现有的生产技术、生产工艺,以达成更高的环保标准,提高产品质量、降低成本就显得非常有必要,具有很大的社会效益。
4.真空冶金是在低于或远低于常压下进行金属及合金的冶炼和加工的冶金方法。真空对冶金过程的重要作用主要是:(1)为有气态生成物的冶金反应创造有利的化学热力学和动力学条件,从而使某些在常压下难以进行的冶金过程在真空条件下得以实现;(2)降低气体杂质及易挥发性杂质在金属中的溶解度,相应地降低其在金属中的含量;(3)降低金属或杂质挥发所需温度,并提高金属与杂质间的分离系数(见真空精炼);(4)减轻或避免金属或其他反应剂与空气的作用,避免气相杂质对金属或合金的污染。真空冶金主要用于真空分离、真空还原、真空精炼、真空熔铸、热处理、真空镀膜等。
5.在真空条件下,还原金属的化合物或矿石以制取金属或合金的方法得到了较广的应用。真空在还原过程中所起的作用,除能避免还原剂和还原出的金属被空气氧化及氮的污染外,更重要的是对生成气态产物(如金属蒸气、co等)的冶金反应特别有利。例如,金属氧化物在碳还原时,其反应式为: (设me为二价)2meo(s)+c(s)=2me+co2(g)(或co)反应产生气态co2或co,有时还产生气态金属me。根据吕查德里原理(principle of lechatelier),降低生成物的分压有利于还原反应的进行,这样势必在设备结构、材质、能耗等方面带来效益。
6.真空还原已在有色金属冶金中广为应用,真空碳还原已成为生产金属铌的主要方法,它也是金属矾、钽的生产的重要方法。在真空中用硅作还原剂的真空硅热还原法,以及在真空中用铝作还原剂的真空铝热还原法生产某些低沸点金属,如钙、镁、钡等,由于其工艺简单、成本较低,而成为这些金属的工业生产方法之一。真空还原通常在真空电阻炉或真
空感应炉中进行。
7.真空冶金在铍铜母合金的生产应用是一个降低生成物的分压有利于还原反应持续且高效进行的典型场景。真空自耗电极电弧熔炼条件下,相当于冶金生产的闪速熔炼条件,bec的生成渣能明显减少,且渣量被控制在最小的程度。当渣量很少时,对产品质量影响很小,而且这种影响也很容易消除。
8.中国发明专利说明书cn106676317a公开了一种高强度高导热性铍铜合金的制备方法,其先将铜、铍等合金元素混合后,压制形成电极板,再重复进行3次自耗电极熔炼后,热处理,获得铍铜合金。该制备方法虽然能获得较为纯净的金属材料坯锭,但是过程相对复杂,需要进行多次熔炼和热处理,且其铍铜合金中铍的含量较低,仅为2.3
‑
3.7%。
9.中国发明专利说明书cn103866155a公开了一种铍铜合金生产及铸锭工艺,其先在石墨坩埚内铺设一层铜原料,再铺设一层氧化铍和炭黑的混合物,反复多次铺设后在上面铺设一层铜原料,再将炉渣覆盖在铜原料上面,随后进行电弧炉熔炼,获得铍含量为3.85
‑
4.1%的铍铜母合金。该工艺中,熔炼原料中铜原料和氧化铍为相对独立的层结构,所需熔炼时间较长,达两个半小时,另外,其后续还需通过铸锭及中频炉熔炼使得铍铜合金的含量更加均匀,这无疑加大了工艺复杂度及生产能耗。
技术实现要素:10.针对现有技术的不足,本发明的目的在于提供一种采用真空自耗电弧熔炼制备铍铜母合金的方法,以方便铍铜母合金的批量化、低成本制备。
11.本发明可有效解决当前铍铜母合金大气连通式石墨非自耗电极电弧炉熔炼生产工艺中存在的一系列问题,如因金属挥发而造成的回收率低、对生产车间内外环境的污染、能耗高成本高等问题,为铍铜母合金,特别是高铍含量的铍铜母合金生产提供一种全新的方法与工艺,有助于实现铍铜母合金的低成本、高性能、零污染生产。
12.本发明的技术方案如下:一种采用真空自耗电弧熔炼制备铍铜母合金的方法;包括如下步骤:s1、根据待制备铍铜母合金中铜、铍含量,称取铜粉和氧化铍粉末;称取石墨粉;其中,所述石墨粉的称取量为通过碳热还原法将所述氧化铍粉末还原获得铍和co2所需碳当量的1.005
‑
1.015倍;s2、对所述氧化铍粉末进行包膜处理后,将氧化铍粉末、铜粉和石墨粉混合均匀,获得混合粉;其中,包膜处理是指对氧化铍粉末的表面施加pva,使得氧化铍粉末的表面覆盖有pva膜层;s3、对s2获得的混合粉进行压制处理,获得厚度为1.5
‑
2.5mm的板坯;其中,压制处理时的压力大小为0.6
‑
1.9t/cm2;s4、对s3中获得的板坯进行轧制,获得碎块后,进一步破碎,获得粒径不超过1mm的坯料粉;其中,轧制时,所用轧机的辊缝大小为0.8
‑
1.2mm;s5、将s4获得的坯料粉于250
‑
310℃条件下退火0.7
‑
1.5h后,添加石蜡粉,混合均
匀,再压制成型,获得柱状生坯;其中,石蜡粉的添加量为坯料粉的0.4
‑
0.6wt%,进一步为坯料粉的0.45
‑
0.55wt%;压制成型时,压力为130
‑
180mpa;s6、将s5获得的柱状生坯装载于石墨模具内,烧结后,脱模,获得工作电极;其中,烧结时,先以2.5
‑
3.5℃/min的升温速率从室温升温至800℃,再以1.5
‑
2.5℃/min的升温速率升温至820
‑
980℃,保温45
‑
90min;所述石墨模具包括第一盖、第二盖和柱状本体,第一盖、第二盖和本体均由石墨构成,所述本体具有依次直接连通的第一腔体、第二腔体和第三腔体,所述第一腔体与本体的一个端面贯通,所述第三腔体与本体的另一个端面贯通;所述第一盖包括第一盖体和固定于第一盖体上的第一塞,所述第一塞的轴向尺寸不小于第一腔体的轴向尺寸,所述第一塞可拆卸地固定于第一腔体内;所述第二盖包括第二盖体和固定于第二盖体上的第二塞,所述第二塞的轴向尺寸不小于第三腔体的轴向尺寸,所述第二塞可拆卸地固定于第三腔体内;所述第二腔体沿轴向的投影位于第一腔体和第三腔体沿轴向的投影范围内;所述第二腔体与柱状生坯的形状、尺寸相匹配。
13.s7、将s6获得的工作电极装入真空自耗电弧炉,进行真空自耗电极电弧熔炼,获得铍铜母合金。
14.进一步地,所述铜粉呈颗粒状;可选的,通过喷雾法对氧化铍粉末进行施加pva,也可通过cn201620280628.6等现有技术所述的包膜机进行包膜。
15.进一步地,所述铍铜母合金由铍和铜组成,其中铍的含量为8
‑
18wt%,余量为铜及不可避免的杂质。
16.进一步地,所述铍铜母合金中,铍的含量为8wt%
‑
18wt%,铜的含量为82
‑
92wt%。
17.进一步地,所述铍铜母合金中,铍的含量为10wt%
‑
16wt%,更进一步为12
‑
14wt%。
18.进一步地,s2中,pva的施加量为氧化铍粉末的0.8
‑
1.2wt%,进一步为0.9
‑
1.1wt%,优选为0.95
‑
1.05wt%。
19.一般的,板坯的尺寸可根据需要进行调整。进一步地,s3中,所述板坯的宽度为80
‑
120mm,长度为380
‑
420mm,厚度为1.75
‑
2.25mm。板的尺寸亦可更大,生产现场根据轧机的情况进行调整,以提高生产效率降低成本。
20.进一步地,s3中,压制处理时的压力大小为1.3
‑
1.7t/cm2,更进一步为1.5 t/cm2。
21.进一步地,s4中,坯料粉的粒径为0.5
‑
0.8mm,更进一步为0.6
‑
0.7mm。
22.进一步地,s4中,轧机的辊的宽度为200mm。
23.轧制时,板坯开裂,形成大小不等的块体,进一步对块体进行破碎处理,获得粒径不超过1mm的坯料粉。
24.进一步地,s5中,通过冷等静压法压制成型。
25.进一步地,s5中,所述柱状生坯为圆柱状,直径为20
‑
40mm,长度不超过200mm;进一步地,柱状生坯的直径为25
‑
35mm,长度为140
‑
180mm。
26.进一步地,s5中,将s4获得的坯料粉于250
‑
310℃条件下退火0.8
‑
1.2h后,添加石蜡粉,混合均匀,再压制成型,获得柱状生坯。
27.进一步地,所述第一腔体呈圆柱状,所述第一塞呈圆柱状,第一腔体和第一塞之间
通过螺纹连接;所述第三腔体呈圆柱状,所述第二塞呈圆柱状,第三腔体和第二塞之间通过螺纹连接。
28.进一步地,s6中,烧结时,先以3℃/min的升温速率从室温升温至800℃,再以2℃/min的升温速率升温至850
‑
980℃,保温45
‑
90min;进一步地,s7中,进行真空自耗电极电弧熔炼时,控制工作电压为25
‑
40v,工作电流为4000
‑
6000a,工作电极的进给速度(即工作电极的熔化速率)为15
‑
30 mm/min。
29.进一步地,s7中,真空自耗电弧炉内的起始压力不小于6.6
×
10
‑3pa,稳定工作真空度为6.6
×
10
‑1‑
1.33
×
10pa。
30.本发明在进行真空自耗电弧熔炼前,将柱状生坯装载于石墨模具内进行烧结,可有效提高电极的强度并降低其电阻。
31.以下本发明的原理进行进一步解释:碳的还原能力跟温度和环境压力紧密相关。温度越高碳的还原能力越强,甚至能还原在室温下很稳定的氧化物、甚至是元素超活泼生成物超稳定的氧化物,如氧化铍。电弧弧芯温度高达5000k左右,非常有利于氧化铍被还原成金属单质铍,从而生产铍铜合金。
32.通过对板坯进行轧制,能将颗粒状的铜粉变成不规则且凹凸不平的长片状,退火后再压制成高密度的压坯并烧结,保证了还原剂(石墨)与氧化铍的充分接触,为闪速熔炼创造了良好的动力学条件;且片状的铜跟氧化铍和石墨均匀混合,以机械啮合压制在一起,经过烧结后强度特别是韧性足够高,自耗电极棒有足够的强度和韧性,这更进一步保证了铍的闪速熔炼很容易实现,也有助于获得成分均匀的铍铜母合金。
33.一般而言,金属具有延展性,金属粉压制易于成型,压坯的强度高,可直接用做自耗电极。铜是一种面心立方结构fcc晶体结构的金属,其塑性和韧性极好,延展性极好,在轧制的时候容易沿轧制方向变形。氧化铍是一种硬颗粒,在轧制力的作用下,不容易变形,故容易被嵌入铜片。铜粉在轧制的时候虽然变成了嵌入有氧化铍的不规则且凹凸不平的长片状,有利于铜、氧化铍和石墨粉的烧结。但铜粉在轧制的时候,由于金属的加工硬化效应,使铜片很难再变形并被压缩,导致再次压制时的压坯密度低,容易分层、开裂,使自耗电极棒制备失败。为此,申请人在轧制得到嵌入氧化铍的不规则且凹凸不平的长片状铜后,增加退火处理,使铜片发生回复甚至再结晶而回复其延展性与塑性,使后续的自耗电极棒压制、烧结顺利完成。另外,通过上述轧制、退火手段的协同配合,可使得即便原料中含有较多的氧化铍粉末,原料仍然可被顺利压制成型获得高密度生坯,并烧结获得强度韧性优良的工作电极,使得高铍含量的铍铜母合金的制备成为可能。本申请所制备的铍铜母合金中铍的含量可达8wt%以上,远高于cn106676317a、cn103866155a等现有技术的铍铜合金中铍的含量。
34.申请人在研发过程中发现,在真空自耗电弧熔炼的过程中,工作电极会受到强烈的热冲击,工作电极的强度韧性特别是韧性不够的话,起弧的时候,或者在工作的时候都很容易破裂或断裂,不能完成熔炼过程,得不到我们所需要的目标产物。为此,申请人结合轧制、退火、加压烧结等技术手段,使得工作电极的强度韧性得到有效提升,从而使得工作电极的真空自耗电弧熔炼过程顺利完成。
35.申请人在研究中发现,采用热等静压烧结等加压烧结技术对生坯进行烧结,可以获得强度韧性良好的工作电极,并可满足后续真空电弧熔炼的需求,但是加压烧结技术往往需要借助专门的加压烧结炉进行,成本很高且产量较小,导致市场竞争力低,生产价值不
高,可见,虽然加压烧结具备良好啊的技术可行性,但是其经济可行性较低。另外,常见的钟罩式烧结炉在技术上也可行,但其单炉量少生产效率低,在经济上也没有市场竞争力。
36.为了提升铍铜母合金生产的经济可行性,提升所制备铍铜母合金的性价比,申请人经过深入研究,转换思路,自行设计了一种石墨模具,用于模拟等静压环境,具体地,可将柱状生坯装入石墨模具,石墨模具的两端用与石墨模具螺纹连接的石墨盖堵住,柱状生坏与石墨模具之间滑动配合,被限制于石墨模具内。由于石墨模具的膨胀率极小,而柱状生坯的膨胀率比石墨模具的大很多。因膨胀率的不同,柱状生坯在高温状态下与石墨模具相互有较大的压力,使柱状生坯的烧结处于一个受压的过程,也就是柱状生坯的烧结是一个类似的等静压状态。这种烧结状态,对柱状生坯改善最明显的是韧性和强度,这对于电弧熔炼的完成也至关重要,无需借助专门的加压设备即可获得与加压烧结类似的效果,且单炉即可完成多个工作电极的烧结制备,有效降低工作电极的制作成本。如此,可有效提升性价比,既在技术上可行,也在经济上可行,大大降低了铍铜母合金的工业化生产难度,具有推广意义。
37.另外,烧结过程中,石墨模具内部可形成微还原气氛,可对生坯起到保护作用。
38.s3的压制过程中,控制压力大小为0.6
‑
1.9t/cm2,可防止单位压力太大或太小,比如大于等于2t/cm2时,或小于等于0.5t/cm2时,板坯的质量都会受到影响,对后续的工作电极的质量产生不利影响。压力过大会使板开裂,则不利于板的后续轧制,一轧就容易出现大块碎;压力过小,则板坯的强度、密度均小,使板的厚度太大,也不利于轧制,一轧就容易出现粉碎,达不到使氧化铍跟铜粉互相嵌套的作用,对后续提高工作电极的强度特别是韧性不利。
39.s6的升温速度、保温温度、保温时间都是经过优化的结果。申请人研究发现,升温太快,如高于4℃/min,虽然时间短能耗低,但由于氧化铍表面的pva在退火时未充分分解或外加石蜡微粉分解太快短时间产生气体太多而容易使生坯开裂,而且生坯内部也容易产生热应力而出现裂纹,这些原因所产生的裂纹反而会导致成品率降低进而使成本提高。生坯在石墨模具内烧结时,气体仅可通过石墨模具的狭小缝隙逸出,可逸出通道小,故包膜或石蜡微粉等有机物的分解速度不能太大,否则会造成烧结失败。升温太慢如1℃/min,则工作电极质量一般没有问题,但因升温时间长而能耗高,使成本提高,导致产品市场竞争力降低。保温温度低、保温时间短,虽然效率高但工作电极的成品率低;保温温度太高,可能使晶粒粗大甚至出现重熔而使工作电极制作失败。因此,s6中的升温速度、保温温度、保温时间显得尤为重要。
40.真空可数量级提高碳热还原铍的效率,使真空自耗电极法碳还原氧化铍在很短的时间内生成铍,既实现铍的闪速熔炼,电弧的热全部用于碳热还原反应,电热效率极高,比当前非自耗电弧炉工作时电热必须持续、反复加热铜和氧化铍的效率高,故可进一步提高生产效率。
41.碳热还原生产铍铜母合金过程中产生的烟气与粉尘在密封的空间,完全不会向泄露,所以能完全控制,彻底消除车间内外环境中的有毒氧化铍粉尘。生产环境的显著改善,于操作工人、于管理人员都有利,正所谓利国利民,能产生明显的社会效益和经济效益。
42.工作电极(自耗电极棒)从下往上逐渐熔化,且熔化速率在一定的范围内可调。即熔即凝,be+c反应生成bec的时间极短,大量减少bec渣的生成(闪速熔炼)。当前生产工艺中
大量的bec渣是由于非自耗电弧炉工作时电弧必须持续、反复加热铜和氧化铍而生成。
43.所用的原料均为细粉,具体为铜粉、石墨粉和氧化铍粉,经过中间处理工序后压制成高密度的压坯并烧结,既保证了还原剂碳与氧化铍的充分接触又保证了电极棒的强度韧性,为自耗电极电弧闪速熔炼创造了良好的动力学条件。这更进一步使得铍的闪速熔炼很容易实现。
44.所用的铜粉、石墨粉与氧化铍粉混合可定量计算,铍的生成亦可计算可控,能实现铍含量的名义含量与实测含量的一致性。闪速熔炼的实现,能减少bec渣的生成机会,所生成的铍全部进入铜液,即生产高铍含量的铍铜母合金成为可能。
45.原料铜熔化后很快凝固,即熔即凝,铜不会长期处于高温液态,这跟非自耗电弧炉工作时电热必须持续、反复加热铜和氧化铍相比,也会更省电节能低碳。
46.真空自耗电弧炉能实现闪速熔炼,其生产效率比大气非自耗电弧炉生产效率至少高1倍以后,综合生产成本也更低。
47.本发明的方法无需坩埚熔炼,也无需借助专门的加压烧结炉进行,所得合金熔体干净无污染,产品纯度及品质好,可用于制备铍含量高的铍铜母合金,且易于工业化生产。
附图说明
48.图1是本发明实施例1的石墨模具的非装配状态下的结构示意图。
49.图2是本发明实施例1的石墨模具的装配状态下的结构示意图。
50.图3是本发明实施例1的石墨模具的使用状态下的结构示意图。
51.图4是本发明实施例1的第一盖体的俯视图。
52.图5是本发明实施例1的第二盖体的俯视图。
具体实施方式
53.以下将参考附图并结合实施例来详细说明本发明。需要说明的是,在不冲突的情况下,本发明中的实施例及实施例中的特征可以相互组合。为叙述方便,下文中如出现“上”、“下”、“左”、“右”字样,仅表示与附图本身的上、下、左、右方向一致,并不对结构起限定作用。若无特别说明,相关百分数为质量百分数。各实施例和对比例中,所用铜粉的粒径为
‑
100目,氧化铍粉的粒径为
‑
300目,石墨粉的粒径为
‑
500目。
54.实施例1制备名义铍含量为8wt%的铍铜母合金,名义铜含量为92wt%。碳当量与氧化铍的量符合化学计量(按2beo+c=2be+co2计,下同),且过量加入0.5%(即按碳当量的1.005倍加入石墨粉,下同)。铜粉的用量,则按上述碳热还原反应生成的铍,根据目标铍铜母合金中的铍含量进行配比计算。按计算好的原料铜粉、氧化铍粉和石墨粉混合均匀,获得混合粉,氧化铍混料之前先用pva进行包膜处理(通过喷雾法进行,下同),pva的用量为氧化铍粉末的1wt%。将混合粉采用1.5t/cm2的压力压制成2mm*100mm*400mm的板坯,然后用轧机轧制,轧制时辊缝1mm。将轧制所得的碎块进一步破碎成粒度不超过1mm的坯料粉,然后在280℃退火1小时,然后外加质量为坯料粉的0.5wt%的石蜡微粉,二次混匀后在150mpa冷等静压法压制成长而细的圆柱状生坯,生坯直径为25mm,生坯长度为200mm。采用普通烧结炉和自行设计的石墨模具对生坯进行烧结,将生坯装载于石墨模具内,再将石墨模具置于普通烧结炉内
进行烧结,以提高电极的强度韧性并减小电极的电阻,获得工作电极。烧结工艺如下:以3℃/min的升温速率从室温升温至800℃,以2℃/min的升温速率升温至980℃,保温时间为45min。将工作电极装入真空自耗电极电弧炉中即可按其操作规范进行熔炼生产。熔炼时,控制工作电压为25v和电流为5000a,电弧炉内起始极限真空度为1
×
10
‑2pa,稳定工作真空度为1.8pa,结晶器直径为90mm,熔炼电极自动进给速度(即自耗电极熔化速率):15mm/min。
55.其中,参见图1至图5,所述石墨模具包括第一盖2、第二盖3和柱状本体101,第一盖2、第二盖3和本体101均由石墨构成,所述本体101具有依次直接连通的第一腔体102、第二腔体103和第三腔体104,所述第一腔体102与本体101的顶端面贯通,所述第三腔体104与本体101的底端面贯通;所述第一盖2包括第一盖体201和固定于第一盖体201上的第一塞202,所述第一塞202的轴向尺寸等于第一腔体102的轴向尺寸,所述第一塞202可拆卸地固定于第一腔体102内,第一塞的底端面与第一腔体的底端面抵接;所述第二盖3包括第二盖体301和固定于第二盖体301上的第二塞302,所述第二塞302的轴向尺寸等于第三腔体104的轴向尺寸,所述第二塞302可拆卸地固定于第三腔体104内,第二塞的顶端面与第三腔体的顶端面抵接;所述第二腔体103沿轴向的投影位于第一腔体102和第三腔体104沿轴向的投影范围内。所述第一腔体102、第二腔体103和第三腔体104共中心轴线。第二腔体103用于容纳生坯4。盖体沿轴向的投影呈六边形状。所述第一腔体102呈圆柱状,第一腔体102的内侧壁上设有第一内螺纹;所述第一塞202呈圆柱状,第一塞202的外侧壁上设有与第一内螺纹配合的第一外螺纹203。所述第三腔体104呈圆柱状,第三腔体104的内侧壁上设有第二内螺纹;所述第二塞302呈圆柱状,第二塞302的外侧壁上设有与第二内螺纹配合的第二外螺纹303。所述第二腔体103呈圆柱状,尺寸与生坯相匹配,直径略小于生坯即可。第一腔体102的直径是第二腔体103的直径的2倍,第三腔体104的直径是第二腔体103的直径的2倍。其中,轴向是指柱状本体的长度方向。烧结时,可将第一盖2拧开,将生坯装入第二腔体103,再将第一盖和第二盖拧紧,然后将装有生坯的石墨模具置于普通烧结炉内进行烧结。烧结完成后,冷却,将第二盖拧出,再将本体101向上提起,一般即可实现石墨模具与工作电极之间的脱离。
56.所得工作电极在真空自耗电极电弧熔炉过程中,表现良好,未发生碎裂。申请人单炉烧结多个生坯,获得多个工作电极,将这些工作电极用于真空自耗电弧熔炼,均可顺利完成熔炼。
57.从结晶器中所得的铍铜母合金棒上取样检测铍铜的铍含量为8.06%,铜含量为91.94%。
58.对比例1重复实施例1,区别之处仅在于:通过热等静压烧结炉对生坯进行热等静压烧结,控制烧结压力控制为130mpa。
59.从结晶器中所得的铍铜母合金棒上取样检测铍铜的铍含量为8.05wt%,铜含量为91.95wt%。
60.对比例2(舍弃包膜处理)制备名义铍含量质量分数为8%的铍铜母合金,其名义铜含量为92%。碳当量与氧化铍的量符合化学计量,且过量加入0.5%。铜粉的用量,则按上述碳热还原反应生成的铍,根据目标铍铜母合金中的铍含量进行配比计算。按计算好的原料铜粉、氧化铍粉和石墨粉混合均匀,获得混合粉,氧化铍粉混料之前未用pva进行包膜处理。采用1.5t/cm2的压力将混
合粉压制作成2mm*100mm*400mm的板坯,板坯开裂,不能完成后续轧制,制备失败。
61.对比例3(不添加石蜡微粉)制备名义铍含量质量分数为10%的铍铜母合金,其名义铜含量90%。碳当量与氧化铍的量符合化学计量,且过量加入0.5%。铜粉的用量,则按上述碳热还原反应生成的铍,根据目标铍铜母合金中的铍含量进行配比计算。按计算好的原料铜粉、氧化铍粉和石墨粉混合均匀,获得混合粉,氧化铍混料之前先用pva进行包膜处理,pva的用量为氧化铍的质量分数1%。采用1.5t/cm2的压力将混合粉压制作成2mm*100mm*400mm的板坯,然后用轧机轧制,轧制时辊缝1mm。将轧制所得的碎块进一步破碎成粒度不超过1mm的坯料粉,然后在280℃退火1小时,并经二次混匀后在150mpa冷等静压法压制成长而细的工作电极。在随后的装入实施例1所述的石墨模具的过程中,电极棒强度低断裂,制备失败。
62.对比例4(不添加石蜡微粉)制备名义铍含量质量分数为8%的铍铜母合金,其名义铜含量92%。碳当量与氧化铍的量符合化学计量,且过量加入0.5%。铜粉的用量,则按上述碳热还原反应生成的铍,根据目标铍铜母合金中的铍含量进行配比计算。按计算好的原料铜粉、氧化铍粉和石墨粉混合均匀,获得混合粉,氧化铍混料之前先用pva进行包膜处理,pva的用量为氧化铍的质量分数1%。采用1.5t/cm2的压力将混合粉压制作成2mm*100mm*400mm的板坯,然后用轧机轧制,轧制时辊缝1mm。将轧制所得的碎块进一步破碎成粒度不超过1mm的坯料粉,然后在280℃退火1小时,并经二次混匀后在150mpa冷等静压法压制成长而细的工作电极。在随后的装入实施例1所述的石墨模具的过程中,电极棒强度低断裂,制备失败。
63.对比例5制备名义铍含量质量分数为12%的铍铜母合金,名义铜含量88%。碳当量与氧化铍的量符合化学计量,且过量加入0.5%。铜粉的用量,则按上述碳热还原反应生成的铍,根据目标铍铜母合金中的铍含量进行配比计算。按计算好的原料铜粉、氧化铍粉和石墨粉混合均匀,获得混合粉,氧化铍混料之前先用pva进行包膜处理,pva的用量为氧化铍的质量分数1%。采用1.5t/cm2的压力将混合粉压制作成2mm*100mm*400mm的板坯,然后用轧机轧制,轧制时辊缝1mm。将轧制所得的碎块进一步破碎成粒度不超过1mm的坯料粉,然后在280℃退火1小时,然后外加质量为坯料粉的0.5wt%的石蜡微粉,二次混匀后在150mpa冷等静压法压制成长而细的圆柱状生坯。生坯直径为25mm,长度为200mm。采用普通烧结炉和实施例1所述的石墨模具对生坯进行烧结,具体地,将生坯装载于石墨模具内,再将石墨模具置于普通烧结炉内进行烧结,以提高电极的强度韧性并减小电极的电阻,获得工作电极。烧结工艺如下:以4℃/min的升温速率从室温升温至800℃,以4℃/min的升温速率升温至980℃,保温时间为45min。
64.将烧结过的工作电极装入真空自耗电极电弧炉,在装炉的过程中工作电极发生断裂现象,经检查发现断口有微裂纹产生,制备失败。
65.对比例6制备名义铍含量质量分数为8%的铍铜母合金,其名义铜含量92%。碳当量与氧化铍的量符合化学计量,且过量加入0.5%。铜粉的用量,则按上述碳热还原反应生成的铍,根据目标铍铜母合金中的铍含量进行配比计算。按计算好的原料铜粉、氧化铍粉和石墨粉混合均匀,获得混合粉,氧化铍混料之前先用pva进行包膜处理,pva的用量为氧化铍的质量分数
1%。采用1.5t/cm2的压力将混合粉压制作成2mm*100mm*400mm的板坯,然后用轧机轧制,轧制时辊缝1mm。将轧制所得的碎块进一步破碎成粒度不超过1mm的坯料粉,然后在280℃退火1小时,然后外加0.5%的石蜡微粉,二次混匀后在150mpa冷等静压法压制成长而细的圆柱状生坯。所述生坯的直径为25mm,长度为200mm。采用普通烧结炉和实施例1所述的石墨模具对生坯进行烧结,将生坯装载于石墨模具内,再将石墨模具置于普通烧结炉内进行烧结,以提高电极的强度韧性并减小电极的电阻。烧结工艺如下:以3℃/min的升温速率从室温升温至800℃,以2℃/min的升温速率升温至820℃,保温30min,获得工作电极。
66.将烧结过的工作电极装入真空自耗电极电弧炉,在装炉的过程中电极棒脆性较大,断裂,制备失败。
67.对比例7制备名义铍含量质量分数为8%的铍铜母合金,其名义铜含量92%。碳当量与氧化铍的量符合化学计量,且过量加入0.5%。铜粉的用量,则按上述碳热还原反应生成的铍,根据目标铍铜母合金中的铍含量进行配比计算。按计算好的原料铜粉、氧化铍粉和石墨粉混合均匀,获得混合粉,氧化铍混料之前先用pva进行包膜处理,pva的用量为氧化铍的质量分数1%。采用1.5t/cm2的压力将混合粉压制作成2mm*100mm*400mm的板坯,然后用轧机轧制,轧制时辊缝1mm。将轧制所得的碎块进一步破碎成粒度不超过1mm的坯料粉,然后在280℃退火1小时,然后外加0.5%的石蜡微粉,二次混匀后在150mpa冷等静压法压制成长而细的圆柱状生坯。生坯的直径为25mm,长度为200mm。通采用普通烧结炉和实施例1所述的石墨模具对生坯进行烧结,将生坯装载于石墨模具内,再将石墨模具置于普通烧结炉内进行烧结,以提高电极的强度韧性并减小电极的电阻,获得工作电极。烧结工艺如下:以3℃/min的升温速率从室温升温至800℃,以2℃/min的升温速率升温至1080℃,保温60min。
68.将烧结过的工作电极装入真空自耗电极电弧炉,在装炉的过程中电极棒强度不足断裂,经检查发现断口有局部重熔现象出现,制备失败。
69.对比例8(普通烧结)制备名义铍含量质量分数为8%的铍铜母合金,其名义铜含量92%。碳当量与氧化铍的量符合化学计量,且过量加入0.5%。铜粉的用量,则按上述碳热还原反应生成的铍,根据目标铍铜母合金中的铍含量进行配比计算。按计算好的原料铜粉、氧化铍粉和石墨粉混合均匀,获得混合粉,氧化铍混料之前先用pva进行包膜处理,pva的用量为氧化铍的1wt%。采用1.5t/cm2的压力将混合粉压制作成2mm*100mm*400mm的板坯,然后用轧机轧制,轧制时辊缝1mm。将轧制所得的碎块进一步破碎成粒度不超过1mm的坯料粉,然后在280℃退火1小时,然后外加0.5%的石蜡微粉,二次混匀后在150mpa冷等静压法压制成长而细的圆柱状生坯。生坯的直径为25mm,长度为200mm。将生坯置于普通烧结炉内烧结,获得工作电极,以提高电极的强度韧性并减小电极的电阻。烧结工艺如下:以3℃/min的升温速率从室温升温至800℃,以2℃/min的升温速率升温至980℃,保温45min。将烧结过的工作电极装入真空自耗电极电弧炉中即可按其操作规范进行熔炼生产。工作电压25v和电流5000a,真空自耗电极电弧炉中起始极限真空度1
×
10
‑2pa,稳定工作真空度1.8pa,结晶器直径90mm,熔炼电极自动进给速度(即自耗电极熔化速率):15mm/min。
70.启弧正常,但工作电极很快出现崩裂,熄弧,熔炼过程不能正常完成。
71.实施例2
制备名义铍含量质量分数为10%的铍铜母合金,名义铜含量90%。碳当量与氧化铍的量符合化学计量,且过量加入1.0%。铜粉的用量,则按上述碳热还原反应生成的铍,根据目标铍铜母合金中的铍含量进行配比计算。按计算好的原料铜粉、氧化铍粉和石墨粉混合均匀,获得混合粉,氧化铍混料之前先用pva进行包膜处理,pva的用量为氧化铍的质量分数1%。采用1.5t/cm2的压力将混合粉压制作成2mm*100mm*400mm的板,然后用轧机轧制,轧制时辊缝1mm。将轧制所得的碎块进一步破碎成粒度不超过1mm的坯料粉,然后在280℃退火1小时,然后外加0.5%的石蜡微粉,二次混匀后在150mpa冷等静压法压制成长而细的圆柱状生坯。生坯的直径为35mm,长度为200mm。采用普通烧结炉和实施例1所述的石墨模具对生坯进行烧结,将生坯装载于石墨模具内,再将石墨模具置于普通烧结炉内进行烧结,以提高电极的强度韧性并减小电极的电阻。烧结工艺如下:以3℃/min的升温速率从室温升温至800℃,以2℃/min的升温速率升温至950℃,保温60min。将烧结过的工作电极装入真空自耗电极电弧炉中即可按其操作规范进行熔炼生产。熔炼时,控制工作电压为30v和电流为4800a,真空自耗电极电弧炉中起始极限真空度为1
×
10
‑2pa,稳定工作真空度为2.0pa,结晶器直径90mm,熔炼电极自动进给速度(即自耗电极熔化速率):20mm/min。
72.工作电极在真空自耗电极电弧熔炉过程中,表现良好,未发生断裂,熔炼过程顺利完成。从结晶器中所得的铍铜母合金棒上取样检测铍铜的铍含量为9.8%,铜含量为90.2%。
73.对比例9(普通烧结)制备名义铍含量质量分数为10%的铍铜母合金,名义铜含量90%。碳当量与氧化铍的量符合化学计量,且过量加入1.0%。铜粉的用量,则按上述碳热还原反应生成的铍,根据目标铍铜母合金中的铍含量进行配比计算。按计算好的原料铜粉、氧化铍粉和石墨粉混合均匀,获得混合粉,氧化铍混料之前先用pva进行包膜处理,pva的用量为氧化铍的质量分数1%。采用1.5t/cm2的压力将混合粉压制作成2mm*100mm*400mm的板,然后用轧机轧制,轧制时辊缝1mm。将轧制所得的碎块进一步破碎成粒度不超过1mm的坯料粉,然后在280℃退火1小时,然后外加0.5%的石蜡微粉,二次混匀后在150mpa冷等静压法压制成长而细的圆柱状生坯(直径35mm,长度200mm)。将生坯置于普通烧结炉内烧结,获得工作电极,以提高电极的强度韧性并减小电极的电阻。烧结工艺如下:以3℃/min的升温速率从室温升温至800℃,以2℃/min的升温速率升温至950℃,保温60min。将烧结过的工作电极装入真空自耗电极电弧炉中即可按其操作规范进行熔炼生产。工作电压30v和电流4800a,真空自耗电极电弧炉中起始极限真空度1
×
10
‑2pa,稳定工作真空度2.0pa,结晶器直径90mm,熔炼电极自动进给速度(即自耗电极熔化速率):20mm/min。
74.启弧正常,但随后工作电极棒裂,熄弧,熔炼过程不能正常完成。
75.对比例10制备名义铍含量质量分数为12%的铍铜母合金,其铜含量88%。碳当量与氧化铍的量符合化学计量,且过量加入1.2%。铜粉的用量,则按上述碳热还原反应生成的铍,根据目标铍铜母合金中的铍含量进行配比计算。按计算好的原料铜粉、氧化铍粉和石墨粉混合均匀,获得混合粉,氧化铍混料之前先用pva进行包膜处理,pva的用量为氧化铍的质量分数1%。采用1.5t/cm2的压力将混合粉压制作成2mm*100mm*400mm的板坯,然后用轧机轧制,轧制时辊缝1mm。将轧制所得的碎块进一步破碎成粒度不超过1mm的坯料粉,然后在280℃退火1小时,然后外加0.5%的石蜡微粉,二次混匀后在150mpa冷等静压法压制成长而细的圆柱状
生坯。生坯直径为25mm,长度为200mm。通过热等静压烧结炉对生坯进行热等静压烧结,获得工作电极,以提高电极的强度韧性并减小电极的电阻。烧结工艺如下:以3℃/min的升温速率从室温升温至800℃,以2℃/min的升温速率升温至920℃,保温时间为70min,烧结压力为130mpa。将烧结过的工作电极装入真空自耗电极电弧炉中即可按其操作规范进行熔炼生产。工作电压35v和电流4200a,真空自耗电极电弧炉中起始极限真空度1
×
10
‑2pa,稳定工作真空度1.6pa,结晶器直径90mm,熔炼电极自动进给速度(即自耗电极熔化速率):30mm/min。
76.工作电极在真空自耗电极电弧熔炉过程中,表现良好,熔炼过程顺利完成。从结晶器中所得的铍铜母合金棒上取样检测铍铜的铍含量为12.04%,铜含量为87.96%实施例3重复对比例10,区别仅在于:不采用热等静压烧结炉对生坯进行烧结,具体地,采用普通烧结炉和实施例1所述的石墨模具对生坯进行烧结,将生坯装载于石墨模具内,再将石墨模具置于普通烧结炉内进行烧结。
77.工作电极在真空自耗电极电弧熔炉过程中,表现良好,未发生断裂,熔炼过程顺利完成。从结晶器中所得的铍铜母合金棒上取样检测铍铜的铍含量为12.10%,铜含量为87.90%。
78.对比例11(普通烧结)制备名义铍含量质量分数为12%的铍铜母合金,其铜含量88%。碳当量与氧化铍的量符合化学计量,且过量加入1.2%。铜粉的用量,则按上述碳热还原反应生成的铍,根据目标铍铜母合金中的铍含量进行配比计算。按计算好的原料铜粉、氧化铍粉和石墨粉混合均匀,获得混合粉,氧化铍混料之前先用pva进行包膜处理,pva的用量为氧化铍的质量分数1%。采用1.5t/cm2的压力将混合粉压制作成2mm*100mm*400mm的板坯,然后用轧机轧制,轧制时辊缝1mm。将轧制所得的碎块进一步破碎成粒度不超过1mm的坯料粉,然后在280℃退火1小时,然后外加0.5%的石蜡微粉,二次混匀后在150mpa冷等静压法压制成长而细的圆柱状生坯。生坯直径为25mm,长度为200mm。将生坯置于普通烧结炉内烧结,获得工作电极,以提高电极的强度韧性并减小电极的电阻。烧结工艺如下:以3℃/min的升温速率从室温升温至800℃,以2℃/min的升温速率升温至920℃,保温70min。将烧结过的工作电极装入真空自耗电极电弧炉中即可按其操作规范进行熔炼生产。工作电压35v和电流4200a,真空自耗电极电弧炉中起始极限真空度1
×
10
‑2pa,稳定工作真空度1.6pa,结晶器直径90mm,熔炼电极自动进给速度(即自耗电极熔化速率):30mm/min。
79.启弧正常,但随后工作电极棒断,熄弧,熔炼过程不能正常完成。
80.实施例4制备名义铍含量质量分数为18%的铍铜母合金,名义铜含量82%。碳当量与氧化铍的量符合化学计量,且过量加入1.5%。铜粉的用量,则按上述碳热还原反应生成的铍,根据目标铍铜母合金中的铍含量进行配比计算。按计算好的原料铜粉、氧化铍粉和石墨粉混合均匀,获得混合粉,氧化铍混料之前先用pva进行包膜处理,pva的用量为氧化铍的质量分数1%。采用1.5t/cm2的压力将混合粉压制作成2mm*100mm*400mm的板,然后用轧机轧制,轧制时辊缝1mm。将轧制所得的碎块进一步破碎成粒度不超过1mm的坯料粉,然后在280℃退火1小时,然后外加0.5%的石蜡微粉,二次混匀后在150mpa冷等静压法压制成长而细的圆柱状生坯(直径25mm,长度200mm)。采用普通烧结炉和实施例1所述的石墨模具对生坯进行烧结,
将生坯装载于石墨模具内,再将石墨模具置于普通烧结炉内进行烧结,获得工作电极,以提高工作电极的强度韧性并减小电极的电阻。烧结工艺如下:以3℃/min的升温速率从室温升温至800℃,以2℃/min的升温速率升温至850℃,保温90min。将烧结过的工作电极装入真空自耗电极电弧炉中即可按其操作规范进行熔炼生产。工作电压25v和电流5000a,真空自耗电极电弧炉中起始极限真空度1
×
10
‑2pa,稳定工作真空度1.8pa,结晶器直径90mm,熔炼电极自动进给速度(即自耗电极熔化速率):20mm/min。
81.顺利完成真空自耗电极电弧熔炼。从结晶器中所得的铍铜母合金棒上取样检测铍铜的铍含量为17.70%,铜含量为82.30%。
82.对比例12(普通烧结)制备名义铍含量质量分数为18%的铍铜母合金,名义铜含量82%。碳当量与氧化铍的量符合化学计量,且过量加入1.5%。铜粉的用量,则按上述碳热还原反应生成的铍,根据目标铍铜母合金中的铍含量进行配比计算。按计算好的原料铜粉、氧化铍粉和石墨粉混合均匀,获得混合粉,氧化铍混料之前先用pva进行包膜处理,pva的用量为氧化铍的质量分数1%。采用1.5t/cm2的压力将混合粉压制作成2mm*100mm*400mm的板坯,然后用轧机轧制,轧制时辊缝1mm。将轧制所得的碎块进一步破碎成粒度不超过1mm的坯料粉,然后在280℃退火1小时,然后外加0.5%的石蜡微粉,二次混匀后在150mpa冷等静压法压制成长而细的圆柱状生坯(直径25mm,长度200mm)。将生坯置于普通烧结炉内烧结,获得工作电极,以提高电极的强度韧性并减小电极的电阻。烧结工艺如下:以3℃/min的升温速率从室温升温至800℃,以2℃/min的升温速率升温至850℃,保温90min。将烧结过的工作电极装入真空自耗电极电弧炉中即可按其操作规范进行熔炼生产。工作电压25v和电流5000a,真空自耗电极电弧炉中起始极限真空度1
×
10
‑2pa,稳定工作真空度1.8pa,结晶器直径90mm,熔炼电极自动进给速度(即自耗电极熔化速率):20mm/min。
83.启弧正常,但随后电极棒断,熄弧,熔炼过程不能正常完成。
84.实施例5制备名义铍含量质量分数为16%的铍铜母合金,名义铜含量84%。碳当量与氧化铍的量符合化学计量,且过量加入1.3%。铜粉的用量,则按上述碳热还原反应生成的铍,根据目标铍铜母合金中的铍含量进行配比计算。按计算好的原料铜粉、氧化铍粉和石墨粉混合均匀,获得混合粉,氧化铍混料之前先用pva进行包膜处理,pva的用量为氧化铍的质量分数1%。采用1.5t/cm2的压力将混合粉压制作成2mm*100mm*400mm的板,然后用轧机轧制,轧制时辊缝1mm。将轧制所得的碎块进一步破碎成粒度不超过1mm的坯料粉,然后在280℃退火1小时,然后外加0.5%的石蜡微粉,二次混匀后在150mpa冷等静压法压制成长而细的圆柱状生坯(直径35mm,长度200mm)。采用普通烧结炉和实施例1所述的石墨模具对生坯进行烧结,将生坯装载于石墨模具内,再将石墨模具置于普通烧结炉内进行烧结,以提高电极的强度韧性并减小电极的电阻。烧结工艺如下:以3℃/min的升温速率从室温升温至800℃,以2℃/min的升温速率升温至950℃,保温60min。将烧结过的工作电极装入真空自耗电极电弧炉中即可按其操作规范进行熔炼生产。工作电压40v和电流4000a,真空自耗电极电弧炉中起始极限真空度1
×
10
‑2pa,稳定工作真空度2.0pa,结晶器直径90mm,熔炼电极自动进给速度(即自耗电极熔化速率):25mm/min。
85.从结晶器中所得的铍铜母合金棒上取样检测铍铜的铍含量为16.1%,铜含量为
83.9%。
86.对比例13(普通烧结)制备名义铍含量质量分数为16%的铍铜母合金,名义铜含量84%。碳当量与氧化铍的量符合化学计量,且过量加入1.3%。铜粉的用量,则按上述碳热还原反应生成的铍,根据目标铍铜母合金中的铍含量进行配比计算。按计算好的原料铜粉、氧化铍粉和石墨粉混合均匀,得混合粉,氧化铍混料之前先用pva进行包膜处理,pva的用量为氧化铍的质量分数1%。采用1.5t/cm2的压力将混合粉压制作成2mm*100mm*400mm的板,然后用轧机轧制,轧制时辊缝1mm。将轧制所得的碎块进一步破碎成粒度不超过1mm的坯料粉,然后在280℃退火1小时,然后外加0.5%的石蜡微粉,二次混匀后在150mpa冷等静压法压制成长而细的圆柱状生坯(直径35mm,长度200mm)。将生坯置于普通烧结炉内烧结,获得工作电极,以提高电极的强度韧性并减小电极的电阻。烧结工艺如下:以3℃/min的升温速率从室温升温至800℃,以2℃/min的升温速率升温至950℃,保温60min。将烧结过的工作电极装入真空自耗电极电弧炉中即可按其操作规范进行熔炼生产。工作电压40v和电流4000a,真空自耗电极电弧炉中起始极限真空度1
×
10
‑2pa,稳定工作真空度2.0pa,结晶器直径90mm,熔炼电极自动进给速度(即自耗电极熔化速率):25mm/min。
87.启弧正常,但随后电极棒断,熄弧,熔炼过程不能正常完成。
88.实施例6制备名义铍含量质量分数为13%的铍铜母合金,铜含量87%。碳当量与氧化铍的量符合化学计量,且过量加入1.3%。铜粉的用量,则按上述碳热还原反应生成的铍,根据目标铍铜母合金中的铍含量进行配比计算。按计算好的原料铜粉、氧化铍粉和石墨粉混合均匀,获得混合粉,氧化铍混料之前先用pva进行包膜处理,pva的用量为氧化铍的质量分数1%。采用1.5t/cm2的压力将混合粉压制作成2mm*100mm*400mm的板,然后用轧机轧制,轧制时辊缝1mm。将轧制所得的碎块进一步破碎成粒度不超过1mm的坯料粉,然后在280℃退火1小时,然后外加0.5%的石蜡微粉,二次混匀后在150mpa冷等静压法压制成长而细的圆柱状生坯(直径25mm,长度200mm)。采用普通烧结炉和实施例2所述的石墨模具对生坯进行烧结,将生坯装载于石墨模具内,再将石墨模具置于普通烧结炉内进行烧结,获得工作电极,以提高电极的强度韧性并减小电极的电阻。烧结工艺如下:以3℃/min的升温速率从室温升温至800℃,以2℃/min的升温速率升温至820℃,保温时间为90min。将烧结过的工作电极装入真空自耗电极电弧炉中即可按其操作规范进行熔炼生产。工作电压25v和电流6000a,真空自耗电极电弧炉中起始极限真空度1
×
10
‑2pa,稳定工作真空度1.6pa,结晶器直径90mm,熔炼电极自动进给速度(即自耗电极熔化速率):30mm/min。
89.从结晶器中所得的铍铜母合金棒上取样检测铍铜的铍含量为12.90%,铜含量为87.10%。
90.对比例14(普通烧结)制备名义铍含量质量分数为13%的铍铜母合金,铜含量87%。碳当量与氧化铍的量符合化学计量,且过量加入1.3%。铜粉的用量,则按上述碳热还原反应生成的铍,根据目标铍铜母合金中的铍含量进行配比计算。按计算好的原料铜粉、氧化铍粉和石墨粉混合均匀,获得混合粉,氧化铍混料之前先用pva进行包膜处理,pva的用量为氧化铍的质量分数1%。采用1.5t/cm2的压力将混合粉压制作成2mm*100mm*400mm的板坯,然后用轧机轧制,轧制时辊
缝1mm。将轧制所得的碎块进一步破碎成粒度不超过1mm的坯料粉,然后在280℃退火1小时,然后外加0.5%的石蜡微粉,二次混匀后在150mpa冷等静压法压制成长而细的圆柱状生坯(直径25mm,长度200mm)。将生坯置于普通烧结炉内烧结,获得工作电极,以提高电极的强度韧性并减小电极的电阻。烧结工艺如下:以3℃/min的升温速率从室温升温至800℃,以2℃/min的升温速率升温至820℃,保温90min。将烧结过的工作电极装入真空自耗电极电弧炉中即可按其操作规范进行熔炼生产。工作电压25v和电流6000a,真空自耗电极电弧炉中起始极限真空度1
×
10
‑2pa,稳定工作真空度1.6pa,结晶器直径90mm,熔炼电极自动进给速度(即自耗电极熔化速率):30mm/min。
91.启弧正常,但随后电极棒断,熄弧,熔炼过程不能正常完成。
92.对比例15(低温退火)制备名义铍含量质量分数为12%的铍铜母合金,铜含量88%。碳当量与氧化铍的量符合化学计量,且过量加入1.2%。铜粉的用量,则按上述碳热还原反应生成的铍,根据目标铍铜母合金中的铍含量进行配比计算。按计算好的原料铜粉、氧化铍粉和石墨粉混合均匀,获得混合粉,氧化铍混料之前先用pva进行包膜处理,pva的用量为氧化铍的质量分数1%。采用1.5t/cm2的压力将混合粉压制作成2mm*100mm*400mm的板坯,然后用轧机轧制,轧制时辊缝1mm。将轧制所得的碎块进一步破碎成粒度不超过1mm的坯料粉,然后在200℃退火1小时,然后外加0.5%的石蜡微粉,二次混匀后在150mpa冷等静压法压制成长而细的圆柱状生坯(直径25mm,长度200mm)。在熔炼之前,先将生坯装载于实施例1所述的石墨模具中烧结,但在装模的过程中电极棒断裂,制备失败。
93.对比例16(短时间退火)制备名义铍含量质量分数为12%的铍铜母合金,铜含量88%。碳当量与氧化铍的量符合化学计量,且过量加入1.2%。铜粉的用量,则按上述碳热还原反应生成的铍,根据目标铍铜母合金中的铍含量进行配比计算。按计算好的原料铜粉、氧化铍粉和石墨粉混合均匀,氧化铍混料之前先用pva进行包膜处理,pva的用量为氧化铍的质量分数1%。采用1.5t/cm2的压力将混合粉压制作成2mm*100mm*400mm的板坯,然后用轧机轧制,轧制时辊缝1mm。将轧制所得的碎块进一步破碎成粒度不超过1mm的坯料粉,然后在280℃退火20分钟,然后外加0.5%的石蜡微粉,二次混匀后在150mpa冷等静压法压制成长而细的圆柱状生坯(直径25mm,长度200mm)。在熔炼之前,先将生坯装载于实施例1所述的石墨模具中烧结,但在装模的过程中电极棒断裂,制备失败。
94.对比例17(短时间退火)制备名义铍含量质量分数为12%的铍铜母合金,铜含量88%。碳当量与氧化铍的量符合化学计量,且过量加入1.2%。铜粉的用量,则按上述碳热还原反应生成的铍,根据目标铍铜母合金中的铍含量进行配比计算。按计算好的原料铜粉、氧化铍粉和石墨粉混合均匀,获得混合粉,氧化铍混料之前先用pva进行包膜处理,pva的用量为氧化铍的质量分数1%。采用1.5t/cm2的压力将混合粉压制作成2mm*100mm*400mm的板坯,然后用轧机轧制,轧制时辊缝1mm。将轧制所得的碎块进一步破碎成粒度不超过1mm的坯料粉,然后在280℃退火40分钟,然后外加0.5%的石蜡微粉,二次混匀后在150mpa冷等静压法压制成长而细的圆柱状生坯(直径25mm,长度200mm)。电极在熔炼之前先行烧结,以提高电极的强度韧性并减小电极的电阻。烧结工艺如下:以3℃/min的升温速率从室温升温至800℃,以2℃/min的升温速率
升温至920℃,保温70min。将烧结过的工作电极装入真空自耗电极电弧炉中即可按其操作规范进行熔炼生产。在电弧炉中装夹电极棒时因其脆性较大,断裂,制备失败。
95.上述实施例阐明的内容应当理解为这些实施例仅用于更清楚地说明本发明,而不用于限制本发明的范围,在阅读了本发明之后,本领域技术人员对本发明的各种等价形式的修改均落入本申请所附权利要求所限定的范围。