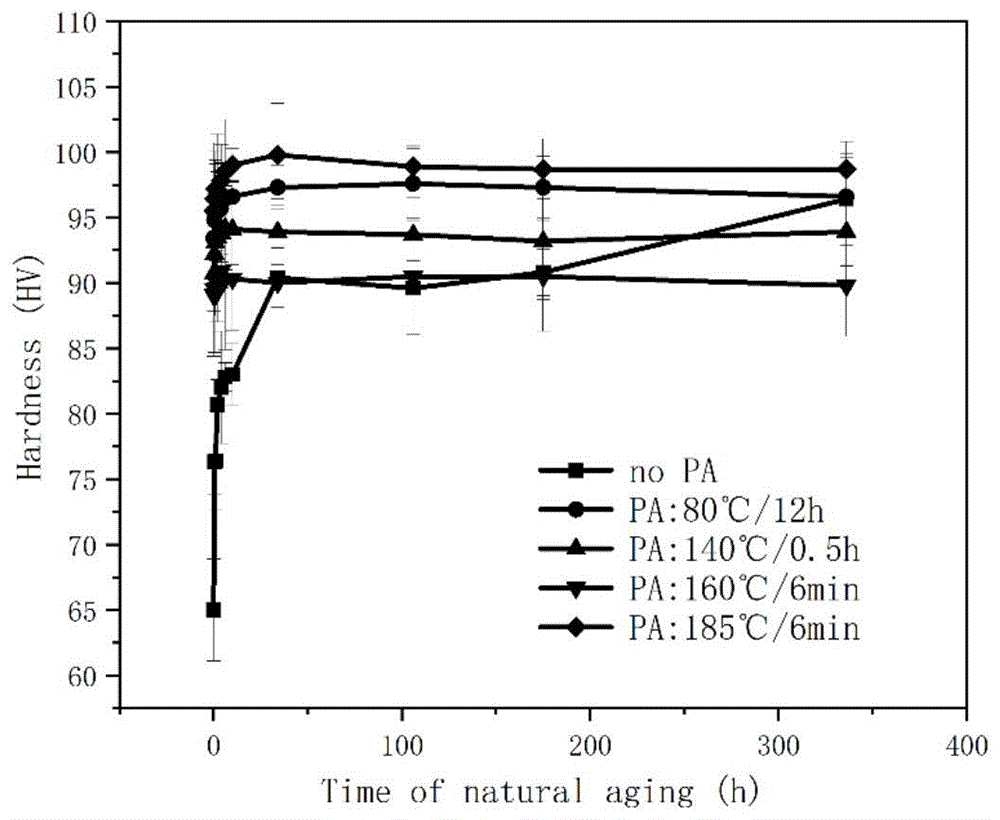
本发明属于铝合金及其制备领域,涉及一种汽车用高烤漆硬化增量的al-mg-si-cu-zn合金及制备方法。
背景技术:
:随着人们对节能的重视,汽车轻量化已成为一种全球性的趋势。铝合金作为重要的轻量化材料受到了广泛的关注。特别是6xxx(al-mg-si)合金由于其在烤漆前(t4p态)拥有优越的成形性能(满足冲压成形的要求),并且烤漆过程中,屈服强度显著增加,满足后续使用过程中的抗凹痕性要求而得到广泛的应用。然而,烤漆工艺的低温(160~185℃)和短时间(20~30min)不能充分发挥潜在的烤漆硬化能力,导致烤漆硬化态合金的屈服强度远低于峰时效态合金。6xxx(al-mg-si)合金目前广泛应用于汽车领域的是6016和6111合金,但其经过185℃保温20min的模拟烤漆工艺后,这两种合金的烤漆硬化增量分别为85和90mpa,两种合金烤漆态的屈服强度只有300mpa左右,远低于钢的屈服强度。因此提高烤漆硬化增量已成为研究热点。合金在使用前必须进行一段时间的运输和储存,而这段时间内的自然时效会明显降低烤漆硬化增量。这是由于固溶处理后在室温下形成的团簇在烤漆过程中并不会作为β″相析出的核心,而是发生回溶并浪费烤漆时间。为了削弱自然时效的恶化效应,研究者们引入了预时效工艺并进行了大量研究,得出固溶淬火后立即加入预时效工艺可有效抑制自然时效恶化效应,提高烤漆硬化增量。此外,研究发现,cu的添加可以提高合金时效响应速度,zn的加入可以提高合金的烤漆硬化增量,从而开发了al-mg-si-cu-zn合金体系。然而,由于考虑网格状微米级析出相对塑性的严重影响,往往在al单相区进行固溶处理以达到微米级析出相全部回溶的目的,但这也限制了合金的含量,mg和si元素含量被严格限制在了1.2wt%以内。即使经过烤漆处理,合金屈服强度仍未达到应用要求,难以满足使用过程中的抗凹痕性要求,烤漆硬化增量仍需进一步提高,如果能突破合金成分限制,在高合金化的同时利用变形和热处理工艺解决网格状微米级析出相对塑性的严重影响,有望在保持合金高成形性的基础上大幅度提高合金烤漆硬化增量和屈服强度从而满足使用要求。然而,这一策略还远未被充分理解,相关的工作也很少报道。技术实现要素:本发明提供一种改进的6xxx(al-mg-si)合金材料,在al-mg-si的基础上加入cu和zn形成al-mg-si-cu-zn合金体系,基于高合金化概念把主元素(mg,si和zn)含量超出6xxx合金范围,利用变形和热处理工艺,改善微米级析出物的形状和大小,解决其对塑性的恶化效应,同时形成多尺度颗粒(微米级和纳米级),通过粗大粒子促进形核细小粒子阻碍晶粒长大原理细化晶粒。和标准6016和6111合金相比,在合金成形性能基本不变的前提下,大幅度提高了合金的力学性能,从而解决6xxx合金烤漆硬化性和抗凹痕性不足的问题。本发明合金的成分范围按重量百分比计为mg:1.2~1.6wt%,si:1.2~1.6wt%,cu:0.1~0.3wt%,zn:2.0~4.0wt%,fe:0.1~0.5wt%,mn:0.5~0.8wt%,ti≤0.03wt%,ni≤0.04wt%,其余为al。本发明合金的优选成分范围按重量百分比计为mg:1.2~1.4wt%,si:1.4~1.6wt%,cu:0.1~0.2wt%,zn:2.0~3.0wt%,fe:0.2~0.4wt%,mn:0.5~0.6wt%,ti:0.01~0.02wt%,ni:0.02~0.03wt%,其余为al。本发明合金的制备工艺为:将al-mg-si-cu-zn合金按上述合金成分范围进行熔炼,再将所得铸锭进行双级均匀化处理,然后进行热轧、冷制及退火处理,退火后的冷轧板材先进行固溶处理并水淬,之后立即进行预时效处理,即将冷轧板放入80~185℃等温时效炉中保温4min~15h,制得高烤漆硬化增量的al-mg-si-cu-zn合金。所述双级均匀化处理,即以20~40℃/h的速度升温至510~520℃保温6~10h,然后再以20~40℃/h的速度升温至540~560℃保温15~20h。所述热轧、冷轧及退火处理工艺是热轧开轧温度520~540℃,总变形量为90~93%,之后进行总变形量为40~60%的冷轧,冷轧后进行380~420℃保温0.5~1.5h的中间退火,退火后再将板材进行总变形量为50~70%的冷轧。所述固溶处理是将冷轧板材在540~560℃盐浴炉中进行1~10min。优选的预时效工艺为140~180℃保温4~8min。制得的al-mg-si-cu-zn合金的烤漆硬化增量为130~180mpa.14天自然放置后t4p态的延伸率为23~26%,14天自然放置加时效处理(模拟烤漆)后屈服强度330~370mpa,抗拉强度380~410mpa。本发明在6xxx(al-mg-si)合金的基础上加入cu和zn,提高主元素含量,并优化预时效工艺,有效抑制了自然时效的恶化效应,并极大提高了烤漆硬化增量,通过高烤漆硬化增量,提高了合金烤漆后的屈服强度从而增强了抗凹痕性能,同时t4p态合金拥有良好塑性,合金t4p态延伸率达25%,与6016合金相同,高于6111合金,但烤漆硬化增量高达180mpa,是6016和6111合金的两倍以上。因此,本发明合金不仅具有6xxx(al-mg-si)合金高塑性可以整体冲压成形的优势,而且极大地提高了烤漆硬化增量,从而解决了6xxx(al-mg-si)合金屈服强度过低无法满足抗凹痕性的问题。本发明合金具有极大的工业应用价值,可以适用于汽车外板。附图说明图15#合金不同预时效工艺处理后的自然时效硬化曲线。图25#合金固溶淬火态合金晶粒尺寸示意图。具体实施方式下面结合具体实施案例对本发明做进一步的补充和说明。本发明所用原材料为99.9wt%的纯金属(al,mg和zn)和中间合金(al-20wt%si,al-50wt%cu,al-10wt%mn,和al-20wt%fe)。实施合金的具体化学成分见表1。其中1#为商用合金6016,2#为商用合金6111,1#和2#合金为参考合金;3#、4#、5#、6#、7#为本发明所设计的合金成分。表1合金具体化学成分(质量百分数,wt%)mgsicuznfemntinial1#0.61.10.20.20.40.20.02/余量2#0.90.70.60.150.40.50.02/余量3#1.21.20.23.00.40.50.020.03余量4#1.21.40.23.00.40.50.020.03余量5#1.21.60.23.00.40.50.020.03余量6#1.41.20.23.00.40.50.020.03余量7#1.61.20.23.00.40.50.020.03余量将上述al-mg-si-cu-zn合金进行熔炼;将所得铸锭进行双级均匀化处理,即以30℃/h的速度升温至520℃保温8h,然后再以30℃/h的速度升温至550℃保温16h;均匀化后进行热轧,开轧温度540℃,总变形量90~93%;之后进行总变形量为50%的冷轧;冷轧后进行400℃保温1h的中间退火;退火后再将板材进行总变形量为67%的冷轧。最终得到1#~7#合金的1mm冷轧板材。对比例1将用上述方法得到的1#合金的1mm冷轧板进行取样,放入盐浴炉中进行550℃保温8min的固溶处理,然后迅速水淬。将淬火后的试样放入时效炉中进行80℃/12h的预时效处理。然后室温放置14天(t4p态)。一组直接进行拉伸;另一组先进行2%的预拉伸(模拟冲压成形),然后进行185℃/20min的时效处理(模拟烤漆处理)。从而得到t4p态的延伸率和烤漆硬化增量。对比例2将用上述方法得到的2#合金的1mm冷轧板进行取样,放入盐浴炉中进行550℃保温8min的固溶处理,然后迅速水淬。将淬火后的试样放入时效炉中进行80℃/12h的预时效处理。然后室温放置14天(t4p态)。一组直接进行拉伸;另一组先进行2%的预拉伸(模拟冲压成形),然后进行185℃/20min的时效处理(模拟烤漆处理)。从而得到t4p态的延伸率和烤漆硬化增量。对比例3将用上述方法得到的5#合金的1mm冷轧板进行取样,放入盐浴炉中进行550℃保温8min的固溶处理,然后迅速水淬。然后室温放置14天(t4态)。一组直接进行拉伸;另一组先进行2%的预拉伸(模拟冲压成形),然后进行185℃/20min的时效处理(模拟烤漆处理)。从而得到t4p态的延伸率和烤漆硬化增量。实施例1将用上述方法得到的5#合金的1mm冷轧板进行取样,放入盐浴炉中进行550℃保温8min的固溶处理,然后迅速水淬。将淬火后的试样放入时效炉中进行80℃/12h的预时效处理。然后室温放置14天(t4p态)。一组直接进行拉伸;另一组先进行2%的预拉伸(模拟冲压成形),然后进行185℃/20min的时效处理(模拟烤漆处理)。从而得到t4p态的延伸率和烤漆硬化增量。实施例2将用上述方法得到的5#合金的1mm冷轧板进行取样,放入盐浴炉中进行550℃保温8min的固溶处理,然后迅速水淬。将淬火后的试样放入时效炉中进行140℃/0.5h的预时效处理。然后室温放置14天(t4p态)。一组直接进行拉伸;另一组先进行2%的预拉伸(模拟冲压成形),然后进行185℃/20min的时效处理(模拟烤漆处理)。从而得到t4p态的延伸率和烤漆硬化增量。实施例3将用上述方法得到的5#合金的1mm冷轧板进行取样,放入盐浴炉中进行550℃保温8min的固溶处理,然后迅速水淬。将淬火后的试样放入时效炉中进行160℃/6min的预时效处理。然后室温放置14天(t4p态)。一组直接进行拉伸;另一组先进行2%的预拉伸(模拟冲压成形),然后进行185℃/20min的时效处理(模拟烤漆处理)。从而得到t4p态的延伸率和烤漆硬化增量。实施例4将用上述方法得到的5#合金的1mm冷轧板进行取样,放入盐浴炉中进行550℃保温8min的固溶处理,然后迅速水淬。将淬火后的试样放入时效炉中进行185℃/6min的预时效处理。然后室温放置14天(t4p态)。一组直接进行拉伸;另一组先进行2%的预拉伸(模拟冲压成形),然后进行185℃/20min的时效处理(模拟烤漆处理)。从而得到t4p态的延伸率和烤漆硬化增量。实施例5将用上述方法得到的3#合金的1mm冷轧板进行取样,放入盐浴炉中进行550℃保温8min的固溶处理,然后迅速水淬。将淬火后的试样放入时效炉中进行160℃/6min的预时效处理。然后室温放置14天(t4p态)。一组直接进行拉伸;另一组先进行2%的预拉伸(模拟冲压成形),然后进行185℃/20min的时效处理(模拟烤漆处理)。从而得到t4p态的延伸率和烤漆硬化增量。实施例6将用上述方法得到的4#合金的1mm冷轧板进行取样,放入盐浴炉中进行550℃保温8min的固溶处理,然后迅速水淬。将淬火后的试样放入时效炉中进行160℃/6min的预时效处理。然后室温放置14天(t4p态)。一组直接进行拉伸;另一组先进行2%的预拉伸(模拟冲压成形),然后进行185℃/20min的时效处理(模拟烤漆处理)。从而得到t4p态的延伸率和烤漆硬化增量。实施例7将用上述方法得到的6#合金的1mm冷轧板进行取样,放入盐浴炉中进行550℃保温8min的固溶处理,然后迅速水淬。将淬火后的试样放入时效炉中进行160℃/6min的预时效处理。然后室温放置14天(t4p态)。一组直接进行拉伸;另一组先进行2%的预拉伸(模拟冲压成形),然后进行185℃/20min的时效处理(模拟烤漆处理)。从而得到t4p态的延伸率和烤漆硬化增量。实施例8将用上述方法得到的7#合金的1mm冷轧板进行取样,放入盐浴炉中进行550℃保温8min的固溶处理,然后迅速水淬。将淬火后的试样放入时效炉中进行160℃/6min的预时效处理。然后室温放置14天(t4p态)。一组直接进行拉伸;另一组先进行2%的预拉伸(模拟冲压成形),然后进行185℃/20min的时效处理(模拟烤漆处理)。从而得到t4p态的延伸率和烤漆硬化增量。表2不同成分和状态的合金试样经过185℃/20min(模拟烤漆)处理前后的力学性能由表2可以看出,在1#(6016),2#(6111)对比合金基础上,基于高合金化概念,提高mg,si和zn元素含量超过传统6xxx系铝合金的元素范围,从烤漆后强度和烤漆硬化增量来看,3#~7#合金明显高于对比合金;且t4p态延伸率并没有下降,甚至高于2#(6111)合金。对比对比例1和实施例1~4,可以看出预时效工艺可以有效抑制自然时效恶化效应,显著提高烤漆硬化增量。尤其是实施例5的烤漆硬化增量是对比例1和和对比例2的两倍以上,且t4p态延伸率与对比例1相同高于对比例2。从图1可以看出160℃/6min的预时效工艺对自然时效的恶化效应抑制最为明显。所以其他合金的实施例均采用这一工艺。从图2可以看出合金晶粒尺寸细小,平均晶粒尺寸只有12um,这是由于合金内多尺度(纳米-微米)析出相,通过粗大粒子促进形核,细小例子阻碍再结晶长大效应细化晶粒,起到细晶强化作用。尽管已经提出并描述了本发明的实施例,但需要指出的是,对于本领域的普通技术人员而言,在不脱离本发明原理和概念的情况下可以对这些实施例进行多种变化、修改、替换和变型,本发明的范围由所附权利要求及等同限定。当前第1页12