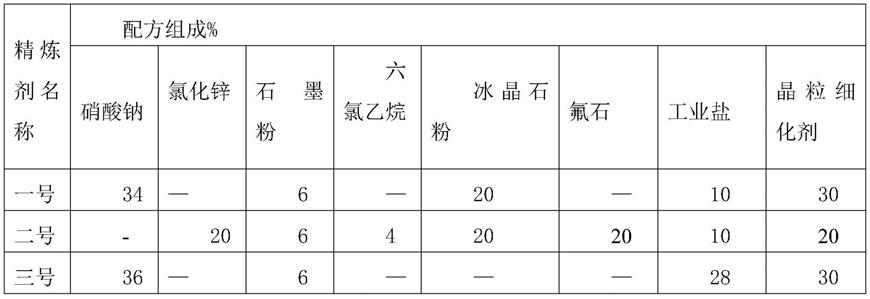
1.本发明涉及一种复合铝合金精炼剂及铝合金精炼方法。
背景技术:2.目前,铝是目前世界上除钢铁外用量最大的金属。在有色全属中,铝无论在储量、产量、用量方面均属前列。
3.废铝是一种重要的资源,做好其回收、再生与利用有利于资源的有效利用,有利于环境保护,有利于节约能源等。废铝的再生与利用是一项社会效益与经济效益巨大的工作,对经济的持续稳定发展有着重要的现实意义。
4.废铝的回收与再生利用不仅使资源得到循环利用,而且可大幅度减少温室气体co2排放,因为再生铝能耗仅相当于原铝生产能耗的3.5%~5.5%。随着铝工业的发展,再生铝行业将得到更好发展。如何将废铝以最低的生产成本变成高附加值产品,关键是在废铝的预处理,熔炼和精炼过程中除杂技术。
5.在铝及铝合金熔炼过程中,氢及氧化夹杂是污染铝熔体的主要物质。而铸造铝合金中的主要缺陷:气孔和夹渣,就是由于残留在合金中的气体和氧化物等固体颗粒造成的。因此,要获得高质量的熔体,不仅要选择正确合理的熔炼工艺,而且熔体的精炼净化处理也是很重要的。
技术实现要素:6.本发明所要解决的技术问题是克服现有技术的缺陷,提供一种复合铝合金精炼剂,将其使用在铝合金精炼过程中,不仅不会产生由于温度高或者过低致晶粒长大,影响铝合金铸件力学性能的问题,而且相容性较好,且能够减少精炼剂的使用,降低生产成本,也提高了生产效率。
7.为了解决上述技术问题,本发明的技术方案是:一种复合铝合金精炼剂,它包括一号精炼剂、二号精炼剂和三号精炼剂;其中,
8.一号精炼剂中的组分和各组分质量百分比为:
9.硝酸钠:34%;石墨粉:6%;冰晶石粉:20%;工业盐:10%;晶粒细化剂:30%;二号精炼剂中的组分和各组分质量百分比为:
10.氯化锌:20%;石墨粉:6%;六氯乙烷:4%;冰晶石粉:20%;caf2:20%;工业盐:10%;晶粒细化剂:20%;
11.三号精炼剂中的组分和各组分质量百分比为:
12.硝酸钠:36%;石墨粉:6%;工业盐:28%;晶粒细化剂:30%;其中,
13.晶粒细化剂是由质量份为1:1的铝锶渣和铝合金母相粉末经过混合、研磨、烧结后得到。
14.进一步,所述烧结的参数为:烧结压强为9~50mpa,烧结温度为450~550℃,烧结时间为10~20min。
15.进一步,铝合金母相粉末中各元素按照质量百分比计,si:10%~12%、mn:0.2%~0.4%、mg:0.22%~0.30%、fe≤0.95%、cu≤1.0
‑
2.0%、zn≤1.0%、ti+zr≤0.15%、sn≤0.01%、pb≤0.01%,余量为al,总计100%。
16.本发明还提供了一种铝合金精炼方法,方法的步骤中含有:
17.加复合铝合金精炼剂除气:
18.将一号精炼剂按照3~4kg/吨铝液的比例送入铝液中,搅拌均匀并进行第一次除气;
19.将二号精炼剂按照3~4kg/吨铝液的比例送入铝液中,搅拌均匀并进行第二次除气;
20.将三号精炼剂按照3~4kg/吨铝液的比例送入铝液中,搅拌均匀并进行第三次除气。
21.进一步,每次除气方式采用浓度为90%的氮气和10%co2对铝液从炉底进行吹气。
22.进一步,每次吹气时间为15~20min。
23.进一步,吹气过程中铝液的温度保持在710~740℃。
24.进一步,所述铝液由铝合金原料熔炼得到;其中,铝合金原料的各元素按照质量百分比计,si:10%~12%、mn:0.2%~0.4%、mg:0.22%~0.30%、fe≤0.95%、cu≤1.0
‑
2.0%、zn≤1.0%、ti+zr≤0.15%、sn≤0.01%、pb≤0.01%,余量为al。
25.进一步,熔炼过程为熔炼、搅拌、扒渣、取样化验、静置保温、精炼、搅拌、扒渣、在线细化。
26.进一步,方法的步骤中还含有:
27.将除气后的铝液过滤铝液中的杂质;
28.将去除杂质的铝液铸造成铝合金铸锭。
29.采用了上述技术方案后,本发明具有以下的有益效果:
30.1、通过利用本复合铝合金精炼剂的铝合金精炼方法制备的铝合金铸锭,用复合铝合金精炼剂代替现有普通精炼剂,将熔炼后的铝液熔炼精炼,进而制备出优质的铝合金铸锭,铝合金铸锭中铝合金的晶粒尺寸可以大大的降低,铝合金晶粒可以降低到20~80μm,其他共晶晶粒可以降低到15μm左右,通过该铝合金铸锭制备的铝合金锭在压铸过程中,不会产生由于温度高或者过低致晶粒长大,影响铝合金铸件力学性能的问题;
31.2、利用本复合铝合金精炼剂的铝合金精炼方法,第一次吹气用一号精炼剂,第二次用二号精炼剂,第三次用三号精炼剂,吹气时间均为15~20min,混合物作为精炼剂,利用本体材料作为精炼剂的主要成分,对铝液精炼除气的过程中,相容性较好,且能够减少精炼剂的使用,降低生产成本,也提高了生产效率。
附图说明
32.图1为本发明的铝合金精炼方法的工艺流程图。
具体实施方式
33.本发明提供了一种复合铝合金精炼剂及铝合金精炼方法,本领域技术人员可以借鉴本文内容,适当改进工艺参数实现。特别需要指出的是,所有类似的替换和改动对本领域
技术人员来说是显而易见的,它们都属于本发明保护的范围。本发明的方法及应用已经通过较佳实施例进行了描述,相关人员明显能在不脱离本发明内容、精神和范围内对本文的方法和应用进行改动或适当变更与组合,来实现和应用本发明技术。
34.一种复合铝合金精炼剂,它包括一号精炼剂、二号精炼剂和三号精炼剂;其中,
35.一号精炼剂中的组分和各组分质量百分比为:
36.硝酸钠:34%;石墨粉:6%;冰晶石粉:20%;工业盐:10%;晶粒细化剂:30%;
37.二号精炼剂中的组分和各组分质量百分比为:
38.氯化锌:20%;石墨粉:6%;六氯乙烷:4%;冰晶石粉:20%;caf2:20%;工业盐:10%;晶粒细化剂:20%;
39.三号精炼剂中的组分和各组分质量百分比为:
40.硝酸钠:36%;石墨粉:6%;工业盐:28%;晶粒细化剂:30%;其中,
41.晶粒细化剂是由质量份为1:1的铝锶渣和铝合金母相粉末经过混合、研磨、烧结后得到。
42.以上一号精炼剂、二号精炼剂和三号精炼剂均是混合得到。
43.进一步,所述烧结的参数为:烧结压强为9~50mpa,烧结温度为450~550℃,烧结时间为10~20min。
44.进一步,铝合金母相粉末中各元素按照质量百分比计,si:10%~12%、mn:0.2%~0.4%、mg:0.22%~0.30%、fe≤0.95%、cu≤1.0
‑
2.0%、zn≤1.0%、ti+zr≤0.15%、sn≤0.01%、pb≤0.01%,余量为al。
45.一种铝合金精炼方法,方法的步骤中含有:
46.加以上得到的复合铝合金精炼剂除气:
47.将一号精炼剂按照3~4kg/吨铝液的比例送入铝液中,搅拌均匀并进行第一次除气;
48.将二号精炼剂按照3~4kg/吨铝液的比例送入铝液中,搅拌均匀并进行第二次除气;
49.将三号精炼剂按照3~4kg/吨铝液的比例送入铝液中,搅拌均匀并进行第三次除气。
50.进一步,每次除气方式采用浓度为90%的氮气和10%co2对铝液从炉底进行吹气。具体是采用浓度为90%的氮气和10%co2通过喷粉机铁管深入炉底注入铝液中。
51.进一步,每次吹气时间为15~20min。
52.进一步,吹气过程中铝液的温度保持在710~740℃。
53.氮气化学性质不活泼,在精炼温度下不与铝液及其他溶解的气体发生化学反应,也不溶于铝熔体中。将氮气通入铝液中能形成大量气泡。气泡浮出液面后,气泡中的氢即逸入大气,因此连续产生气泡,即能不断除去溶于铝液中的氢。在气泡上浮过程中,遇到夹杂物时,由于表面张力的作用,夹杂物就粘附在气泡表面上,这些夹杂物随着气泡的上浮而排除。由此可见,在去气体的同时也清除了夹杂物。
54.用氮气去气精炼,精炼温度应控制在710~740℃范围内,温度过高,氮气可能与铝起化学反应,氮气压力控制在10~15kpa范围内。
55.进一步,所述铝液由铝合金原料熔炼得到;其中,铝合金原料的各元素按照质量百
分比计,si:10%~12%、mn:0.2%~0.4%、mg:0.22%~0.30%、fe≤0.95%、cu≤1.0
‑
2.0%、zn≤1.0%、ti+zr≤0.15%、sn≤0.01%、pb≤0.01%,余量为al。
56.进一步,熔炼过程为熔炼、搅拌、扒渣、取样化验、静置保温、精炼、搅拌、扒渣、在线细化。
57.进一步,方法的步骤中还含有:
58.将除气后的铝液过滤铝液中的杂质;过滤可以采用通过蜂窝陶瓷过滤器;
59.将去除杂质的铝液铸造成铝合金铸锭;铸造可以通过半连续铸造的方法。
60.熔剂精炼作用主要是通过其与熔体中的氧化夹杂物发生吸附和溶解来实现。精炼剂以氯化物为基础,加入氟化物,如caf2、na3alf6等来吸附、溶解al2o3,以增大净化效果。它们能够清除氧化夹杂,也可以去除一些气体,但不彻底。加入nano3可有效提升低温铝灰渣的铝灰温度,通过搅拌使各点的铝灰温度均匀,在搅拌过程中,铝灰里的金属镁等低燃点金属燃烧释放热量,使铝灰温度继续升高。如果铝灰里不含低燃点的可燃物,则加入nano3提高温度。
61.随着温度的升高,铝灰里的金属铝开始熔化形成细小的铝珠子,形成的液态金属铝颗粒表面张力随着温度升高而降低。在搅拌的作用下,包覆在液态金属铝颗粒表面的致密氧化膜被固态的铝灰杂质揉搓摩擦而破裂,铝液流动性增加。
62.精炼时,先调整铝液温度到高于浇注温度20~30℃。把熔剂撒在铝合金熔体表面,由于铝合金使用的熔剂密度比铝液小,它们都浮在上面。搅拌5~10min,静止5~10min,然后清除合金上面的渣并撒上一层覆盖剂,精炼完毕即可浇注。
63.在本发明中,加入硝酸钠可有效提升低温铝灰渣的铝灰温度,通过精炼、气体动力搅拌使各点的铝灰温度均匀,在搅拌过程中,铝灰里的金属镁等低燃点金属燃烧释放热量,使铝灰温度继续升高。如果铝灰里不含低燃点的可燃物,则加入硝酸钠提高温度。随着温度的升高,铝灰里的金属铝开始熔化形成细小的铝珠子,形成的液态金属铝颗粒表面张力随着温度升高而降低。在搅拌的作用下,包覆在液态金属铝颗粒表面的致密氧化膜被固态的铝灰杂质揉搓摩擦而破裂,铝液流动性增加。
64.氯化锌和六氯乙烷:氯盐净化的原理是利用它们和铝反应生成不溶于铝液的低沸点化合物(如alcl3沸点182.7℃),在铝液中形成气泡,上浮时起去气、清除杂质的作用。一是提高了熔剂和熔体间的界面张力,增强了熔剂对氧化物的吸附作用;二是氟化物与铝熔体具有更高的反应能力,在液态铝
‑
氧化物界面上形成具有表面活性的反应产物氟化亚铝气体及液态钠等,促进了氧化物的排除。而仅用氯化物处理时,则仅产生少量的氯化亚铝气态产物,故精炼效果不如加氟化物的好。
65.石墨粉主要是避免精炼过程升温过快的助剂加入。
66.冰晶粉主要起精炼作用,如吸附、溶解al2o3。
67.萤石(caf2)具有能降低难熔物质的熔点,促进炉渣流动,使渣和金属很好分离,在冶炼过程中脱硫、脱磷,增强金属的可煅性和抗张强度等特点。能增大混合熔盐的表面张力,使已吸附氧化物的熔盐球状化,便于与熔体分离,减少固熔渣夹裹铝而造成的损耗,而且由于熔剂——熔体表面张力的提高,加速了熔剂吸附夹杂的过程。
68.由质量份为1:1的铝锶渣和铝合金母相粉末经过混合、研磨、烧结后得到的晶粒细化剂:晶粒细化剂将对铝合金铸件内部晶粒的尺寸和组织产生作用,形成更细的晶粒尺寸。
会减少缩松,降低缩松孔隙的尺寸,同时改善补缩,降低缩孔缩松形成倾向。铝锶渣对合金系统的硅起作用,将共晶硅的形貌从长条状变成细小的颗粒状。变质的结果提高了力学性能,特别是抗拉强度和伸长率。
69.为了使本发明的内容更容易被清楚地理解,下面根据具体实施例并结合附图,对本发明作进一步详细的说明。
70.实施例一
71.如图1所示展示了铝合金精炼方法的工艺流程图,铝合金精炼方法的具体步骤如下:
72.1、配料:铝合金型材原料中各元素按照质量百分比计,si:10%、mn:0.2%、mg:0.22%、fe:0.5%、cu:1.0%、zn:0.5%、ti+zr:0.10%、sn:0.01%、pb:0.01%,余量为al,称取上述质量份的各种原料组分备好;
73.2、制备晶粒细化剂:
74.a、将铝锶渣和步骤1制备的铝合金母相粉末按照质量份数比为1∶1的比例均匀混合后研磨成粉末备用;b、将步骤a研磨后的混合物粉末在烧结炉中烧结,烧结压强为9~50mpa,烧结温度为450~550℃,烧结时间为10~20min,制得晶粒细化剂;
75.3、熔炼:将步骤1称好的各种原料组分全部投入熔炼炉中熔炼;熔炼具体为:熔炼、搅拌、扒渣、取样化验、静置保温、精炼、搅拌、扒渣、在线细化;
76.4、加精炼剂除气:将步骤2制得的晶粒细化剂和如下成分混合分别得到一号精炼剂、二号精炼剂和三号精炼剂:
[0077][0078]
5、按照3~4kg/吨铝液送入铝液中,通过喷粉机将精炼剂和铝液搅拌均匀,并进行除气;除气方式为采用浓度为90%的氮气和10%co2对搅拌均匀的铝液通过喷粉机铁管深入炉底进行吹气,吹气时间为15~20min,吹气过程中铝液的温度保持在710~740℃,第一次吹气用一号精炼剂,第二次用二号精炼剂,第三次用三号精炼剂,吹气时间均为15~20min;
[0079]
6、过滤:将除气后的铝液通过蜂窝陶瓷过滤器过滤铝液中的杂质;
[0080]
7、铸造:将去除杂质的铝液通过半连续铸造的方法铸造成铝合金铸锭。
[0081]
本实施例制备得到的铝合金铸锭,晶粒度达到二级,铝合金铸件力学性能:硬度达到90hb,抗拉强度为220mpa,精炼剂的使用量为铝液的1.5
‰
,精炼剂使用量变小,降低了生产成本,也提高了生产效率。
[0082]
实施例二
[0083]
本实施例的方法与实施例一基本相同,不同的是:铝合金型材原料中各元素按照
质量百分比计,si:12%、mn:0.4%、mg:0.30%、fe:0.95%、cu:2.0%、zn:1.0%、ti+zr:0.15%、sn:0.01%、pb:0.01%,余量为al,总计100%。
[0084]
本实施例制备得到的铝合金铸锭,晶粒度达到二级,铝合金铸件力学性能:硬度达到95hb,抗拉强度为240mpa,精炼剂的使用量为铝液的1.5
‰
,精炼剂使用量变小,降低了生产成本,也提高了生产效率。
[0085]
实施例三
[0086]
本实施例的方法与实施例一基本相同,不同的是:铝合金型材原料中各元素按照质量百分比计,si:11%、mn:0.3%、mg:0.25%、fe:0.8%、cu:1.5%、zn:0.8%、ti+zr:0.10%、sn:0.005%、pb:0.005%,余量为al,总计100%。
[0087]
本实施例制备得到的铝合金铸锭,晶粒度达到二级,铝合金铸件力学性能:硬度达到92hb,抗拉强度为230mpa,精炼剂的使用量为铝液的1.5
‰
,精炼剂使用量变小,降低了生产成本,也提高了生产效率。
[0088]
以上所述的具体实施例,对本发明解决的技术问题、技术方案和有益效果进行了进一步详细说明,所应理解的是,以上所述仅为本发明的具体实施例而已,并不用于限制本发明,凡在本发明的精神和原则之内,所做的任何修改、等同替换、改进等,均应包含在本发明的保护范围之内。