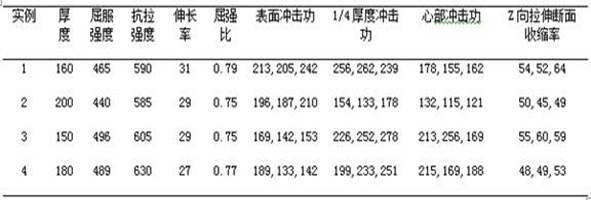
1.本发明属于冶金技术领域,涉及一种低合金高强度高韧性特厚钢板的生产方法。
背景技术:2.低合金高强度高韧性特厚板在船舶、海洋工程、建筑、桥梁、工程机械方面的用途也越来越广。这些使用领域对钢的强度要求越来越高,目前大型建筑已经普遍使用420mpa,460mpa级别高强钢板,大型建筑、海洋工程等往往有120mm以上规格钢板的需求。
3.在海洋工程用钢板和船用钢板选材上,考虑到最大海况以及涉及海面的最低温度,往往对韧性的要求极高。不仅对韧性的需求提升到f级别,对表面冲击以及心部冲击均有严格的要求。比如中海油的特厚海工板,均要求检验表面与心部,1/4厚度的冲击,欧标10225涉及的大厚度海工板也需要检验心部冲击。这对于特厚钢板的均匀性提出了极高的要求。为了满足海工、船板的需求,同时满足q420gje、q460gje对于高韧性低屈强比的要求,特开发低成本不加mo的f420、f460海工船板用钢和q420gje、q460gje建筑用钢板,既满足钢板性能需求,又通过工艺创新降低生产成本,极大的有利于f420、f460特厚船板以及海工用钢和特厚高韧性建筑用钢版q420gje、q460gje的推广。
4.中国专利cn110791711“一种特厚vl e460级别调质型高强船板生产方法”公开了一种特厚vl e460级别调质型高强船板生产方法,其化学成分按重量百分比为:c:0.12
‑
0.14%,si:0.2
‑
0.4%,mn:0.95
‑
1.05%,p≤0.01%,s≤0.005%,cr:0.3
‑
0.38%,ni:0.6
‑
0.7%,mo:0.2
‑
0.28%,nb:0.02
‑
0.03%,ti≤0.05%,v:0.03
‑
0.04%,alt:0.02
‑
0.05%,n≤0.007%,其余为fe及难以避免的杂质;ceq=c+mn/6+(cr+mo+v)/5+(cu+ni)/15: 0.42
‑
0.48。其所处的钢板最大厚度为180mm,由于较高的合金含量以及两次淬火来保证钢板的性能,具有生产成本较高,且生产流程较长,不能使用连续式淬火的特点,不适合批量生产。
5.中国专利cn107805758
ꢀ“
一种高强度优良低温韧性船用钢及其一钢多级热处理工艺”,钢板化学成分的重量百分比为:c:0.12
‑
0.15%,si:0.20
‑
0.30%,mn:1.40
‑
1.70%,ni:0.12
‑
0.15%,cr:0.16
‑
0.25%,mo:0.08
‑
0.12%,nb:0.020
‑
0.030%,ti:0.012
‑
0.018%,v≤0.02%,p≤0.015%,s≤0.002%,b:0.0020
‑
0.0030%,以及余量的fe和不可避免的杂质;涉及一种成分通过不同的热处理工艺实现e460
‑
e550的轧制,但是其主要是通过改变淬火工艺来实现。亚温淬火为不完全奥氏体化的淬火,会增大钢板厚内位置同板差,并不适用于厚板的生产。因此该专利仅限于50mm以下薄板的生产。
6.中国专利cn101705439“低温高韧性f460级超高强度造船用钢板及其制造方法”,钢板成分重量百分比为:c 0.05~0.15%、si 0.15~0.35%、mn 1.20~1.70%、p≤0.020%、s≤0.010%、nb 0.02~0.04%、v 0.04~0.06%、ti 0.0.10~0.020%、cu 0.15~0.40%、cr 0.10~0.30%、ni 0.15~0.40%、al 0.02~0.05%以及余量的fe及和杂质。轧制工艺:tmcp工艺生产60mm以下的f460。其具有成本低,流程短的优点。但是其实际生产的c含量均在0.06%左右。如此低的c含量在生产100mm以上厚板时会出现抗拉强度低的问题,调质处理后由于组织转变,抗拉强度进一步下降,因此并不适用于厚板的生产,因此只
能生产18
‑
60mm的f460。
技术实现要素:7.本发明的目的是提供一种低合金高强度高韧性特厚钢板的生产方法,利用钢厂先进的轧制与热处理设备,通过成分优化设计,精确控制过程工艺参数,通过模铸生产线生产。
8.本发明通过以下技术方案来实现:一种低合金高强度高韧性特厚钢板的生产方法,钢的生产工艺路线为冶炼—模铸—轧制—精整—淬火—回火;钢的化学成分质量百分比为c=0.09
‑
0.015,si=0.15~0.40,mn=1.2
‑
1.7,p≤0.012,s≤0.002,cr=0.15~0.3,nb=0.3~0.5,v=0.2~0.5,ti=0.01~0.03,cu=0.1~0.25,ni=0.2~0.4,余量为fe和不可避免的杂质;包括以下工艺步骤:(1)冶炼:采用bof
‑
lf
‑
rh生产工艺路径,转炉冶炼控制o≤800ppm,精炼lf炉采用高碱度渣,搅拌脱硫; rh炉生产采用轻脱气工艺,真空处理总时间≤10min;(2)模铸:采用梯形锭模,过热度控制在42~45℃之间,浇铸后冒口位置投放发热剂延缓凝固,锭身锭尾自然冷却;(3)轧制:钢锭开完坯后重新加热轧制,轧制时一阶段轧制采用温差轧制,通过中带高温计与温度模型的中间辊道水冷装置,控制铸坯表面温度与心部温度的温差在200℃左右,采用慢速轧制,道次压下量控制在10%~15%;二阶段采用常规轧制;(4)淬火:淬火采用间断式冷却淬火机,钢板表面进行间断式冷却,控制钢板回温在100℃以内并降低钢板表面和心部的冷速差;淬火温度890℃~930℃,淬火冷速1~2℃/s;(5)回火:回火温度580℃~680℃,回火采用快速加热,保温时间115~125min。
9.采用上述方法生产的低合金高强度高韧性钢板,屈服强度在430
‑
530mpa之间可控,抗拉强度在580
‑
650mpa之间可控,延伸率超过23%,屈强比≤0.8,z向拉伸面缩率≥40%,表面、心部、1/4厚度处
‑
60℃冲击在120j以上。
10.本发明适用于200mm以下f420,f460等船板生产,又能满足q420gje、q460gje特厚板的性能需求,拥有较低的屈强比,优异的焊接性能,良好的抗层状撕裂性能,通过热处理工艺的调整,实现一钢多用,降低钢厂的生产库存。
11.本发明的突出特点体现在42kg级及46kg级特厚板生产不添加昂贵的mo元素,不仅节约生产成本,并且热处理过程中不产生贝式体,因此热处理工艺可以灵活调整,以适应不同钢级、不同钢种的生产需要。
附图说明
12.图1 为钢板生产工艺的流程图。
13.图2 为200mmf460钢板的组织金相图。
具体实施方式
14.下面结合实施例对本发明之成分控制范围、最佳实施方式等主要内容作进一步说明:冶炼实例1:
转炉冶炼一次命中,终点控制c=0.06%,终点氧含量o=470ppm,lf采用高碱度渣脱硫,rh炉真空处理时间9min,测得残余h=1.5ppm。模铸采用29吨锭,钢水浇铸过热度42℃,浇铸前投放发热剂,浇铸后投放保温剂,24小时候脱模。轧制采用二火轧制,开坯轧到450mm后重新加热,均热坑炉保温段心部温度1208℃。保温50分钟后开轧,粗轧展完宽之后,进入专门的快冷装置冷却至表面温度900℃左右,摆动3分钟至目标温度。粗轧采用慢速大压下,道次压下率12%~19%,中间坯厚度190mm,精轧开轧温度775℃,轧成160mm厚。轧后直接进入mulpic层流冷却,返红温度660℃,冷速约1℃/s。热矫后入垛缓冷。热处理采用调质,900℃保温约120分钟,出炉后入间隙式冷却辊底式炉,控制冷速约1.5℃/s,冷却至室温后采用650℃回火,保温180分钟,出炉后堆冷48小时。
15.冶炼实例2:转炉冶炼一次命中,控制c=0.07%,终点o含量320ppm,lf采用高碱度渣脱硫,rh炉真空处理时间12min,测得残余h=1.3ppm。模铸采用50吨锭,钢水浇铸过热度45℃,浇铸前投放发热剂,浇铸后投放保温剂,36小时候脱模。轧制采用二火轧制,开坯轧到565mm后重新加热,加热炉保温段心部温度1205℃。保温60分钟后开轧,粗轧展完宽之后,进入专门的快冷装置冷却至表面温度920℃左右,摆动5分钟至目标温度。粗轧采用慢速大压下,道次压下率10%
‑
14%,中间坯厚度240mm,精轧开轧温度780℃,轧成200mm厚。轧后直接进入mulpic层流冷却,返红温度679℃,冷速约1℃/s。热矫后入垛缓冷。热处理采用调质,900℃保温约150分钟,出炉后入间隙式冷却辊底式炉,控制冷速约1.5℃/s,冷却至室温后采用650℃回火,保温230分钟,出炉后堆冷72小时。
16.冶炼实例3:转炉冶炼一次命中,控制c=0.09%,终点氧含量o=305ppm,,lf采用高碱度渣脱硫,rh炉真空处理时间10min,测得残余h=1.4ppm。模铸采用35吨锭,钢水浇铸过热度43℃,浇铸前投放发热剂,浇铸后投放保温剂,24小时候脱模。轧制采用二火轧制,开坯轧到453mm后重新加热,加热炉保温段心部温度1203℃。保温60分钟后开轧,粗轧展完宽之后,进入专门的快冷装置冷却至表面温度900℃左右,摆动3分钟至目标温度。粗轧采用慢速大压下,道次压下率13%
‑
19%,中间坯厚度185mm,精轧开轧温度772℃,轧成150mm厚。轧后直接进入mulpic层流冷却,返红温度665℃,冷速约1℃/s。热矫后入垛缓冷。热处理采用调质,900℃保温约120分钟,出炉后入间隙式冷却辊底式炉,控制冷速约1.5℃/s,冷却至室温后采用580℃回火,保温200分钟,出炉后堆冷48小时。
17.冶炼实例4:转炉冶炼一次命中,控制c=0.07%,终点氧含量o=395ppm,,lf采用高碱度渣脱硫,rh炉真空处理时间12min,测得残余h=1.3ppm。模铸采用40吨锭,钢水浇铸过热度44℃,浇铸前投放发热剂,浇铸后投放保温剂,36小时候脱模。轧制采用二火轧制,开坯轧到540mm后重新加热,加热炉保温段心部温度1210℃。保温60分钟后开轧,粗轧展完宽之后,进入专门的快冷装置冷却至表面温度910℃左右,摆动4分钟至目标温度。粗轧采用慢速大压下,道次压下率11%
‑
15%,中间坯厚度220mm,精轧开轧温度782℃,轧成180mm厚。轧后直接进入mulpic层流冷却,返红温度665℃,冷速约1℃/s。热矫后入垛缓冷。热处理采用调质,930℃保温约150分钟,出炉后入间隙式冷却辊底式炉,控制冷速约1.2℃/s,冷却至室温后采用580℃回火,保温280分钟,出炉后堆冷72小时。
18.各冶炼实例成分控制如表1:表1实例控制成分(wt%) 表2实例各项性能(冲击温度
‑
60℃)从表2可看出,本发明钢板可以生产强度级别从42kg级到46kg级的特厚板,厚内各位置的冲击韧性良好,可以满足海工项目对于f420与f460钢板强度与低温韧性的特殊需求。此外钢板强度稳定,拥有较低的屈强比,又可以满足q420gje、q460gje的各项性能需求。特厚板的一钢多级、一钢多用对于钢厂的生产组织具有极大的优势。
19.从图2可以看出,钢板调质以后,组织为铁素体和退化珠光体组织,组织自小,退化珠光体为残余奥氏体回火过程中形成,具有较高的强度,是42kg
‑
46kg级高韧性钢的理想组织。为实现这样的组织,对钢板相变控制极其严格。