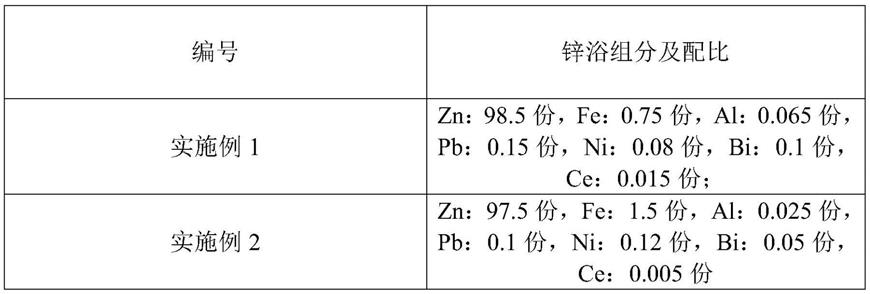
1.本发明涉及热浸镀锌的技术领域,具体涉及到一种钢材的热浸镀锌方法。
背景技术:2.工业中应用最广泛的钢铁材料,它的腐蚀无时无刻都发生。当其在大气、海水、土壤及建筑材料等环境中使用时,均会发生不同程度的腐蚀。据统计,全世界每年因腐蚀而损失的钢铁材料大约可占到其总产量的1/3。为了保证钢铁制品的正常使用,延长其使用寿命,钢铁的防腐蚀保护技术一直受到人们的普遍重视。
3.锌对钢铁具有三重保护:(1)阻挡层保护:锌可以将钢铁与腐蚀环境隔开;(2)腐蚀产物保护:锌自身表面在环境中被氧化,会形成一层致密性的腐蚀产物膜,极大地减小了腐蚀速率;(3)牺牲阳极保护:当镀层破损漏出铁基,锌可以牺牲自己,来保护露出的铁基不被腐蚀。
4.热镀锌是使熔融金属与铁基体反应而产生合金层,从而使基体和镀层二者相结合。热镀锌是先将钢铁制件进行酸洗,为了去除钢铁制件表面的氧化铁,酸洗后,通过氯化铵或氯化锌水溶液或氯化铵和氯化锌混合水溶液槽中进行清洗,然后送入热浸镀槽中。热镀锌具有镀层均匀,附着力强,使用寿命长等优点。
5.热浸镀锌可为分为两大类:连续热镀锌和批量热镀锌。连续热镀锌是将带钢、钢丝及钢管等材料,连续高速地通过锌浴获得热镀锌件的方法。批量热镀锌是将结构制件等材料,分批次浸入锌浴获得热镀锌件的方法。
6.钢材热浸镀锌后镀层性能的好坏,即良好的镀层粘附性、优良的镀层加工成型性受众多因素的影响,例如锌浴的成分、热浸镀锌的温度、浸入速度、浸锌时间、提升速度等等。
7.文献《热浸镀锌钢板的工艺控制对涂层质量的影响分析》中公开了热浸镀锌镀锌层外观质量受表面光整度的影响,并且镀件表面的光整性会影响镀锌层与基材的结合力会影响镀锌层的表面光整度,但并没有公开怎样增强镀锌层与基材之间的结合力。
8.文献《稀土在金属表面处理工艺中的应用技术(6)—稀土热浸镀锌》公开了在热浸镀锌的锌浴中加入稀土会提高镀件的耐腐蚀性和表面光整度,以及增强镀锌层与基材之间的结合力,但其并没有公开稀土元素和其他元素共同作用时能进一步提高提高镀件的耐腐蚀性和表面光整度,以及增强镀锌层与基材之间的结合力。
9.现有技术中,钢材在热浸镀锌过程中其镀层与基材的结合力较弱,从而造成镀层的外观质量较差。
技术实现要素:10.本发明的目的是提供一种钢材的热浸镀锌方法,用于解决现有技术中钢材在热浸镀锌过程中其镀层与基材的结合力较弱的技术问题。
11.为达上述目的,本发明的一个实施例中提供了一种钢材的热浸镀锌方法,包括以
下步骤:
12.步骤(1)镀前处理:对镀覆钢材表面进行处理,为钢材进行热浸镀锌做准备,避免后续热浸镀锌过程中熔锌无法与钢铁正常完全反应,形成最完美的镀锌皮膜组成;
13.步骤(2)热浸镀锌:将已经完成镀前处理的钢材浸入锌浴中,使钢材与熔融锌反应生成一合金化的皮膜,从而完成热浸镀锌;
14.步骤(3)镀后处理:将完成热浸镀锌后的钢材进行后处理,避免破坏镀锌皮膜外观;
15.其中锌浴包括以下按重量份数配比的原料:
16.zn:97.5份~99.5份,fe:0.035份~1.5份,al:0.025份~0.12份,
17.pb:0.1份~0.2份,ni:0.04份~0.12份,bi:0.05份~0.15份,
18.ce:0.005份~0.03份。
19.本发明优选的方案之一,步骤(1)中,镀前处理包括脱脂、酸洗、水洗、助镀以及烘干。
20.本发明优选的方案之一,脱脂为酸性脱脂,采用的脱脂剂为7%~10%盐酸和1.5%~2%脱脂抑制剂的混合液。
21.本发明优选的方案之一,助镀采用的助镀剂为氯化锌铵助镀液,并且其氯化铵与氯化锌重量比为1:1.2~1:1.6。
22.本发明优选的方案之一,烘干的温度为100℃~150℃。
23.本发明优选的方案之一,步骤(2)中,热浸镀锌的温度为435℃~460℃,热浸镀锌的时间为20s~60s。
24.本发明优选的方案之一,步骤(3)中,镀后处理包括水冷以及钝化。
25.本发明优选的方案之一,钝化采用铬酸盐作为钝化剂。
26.综上所述,本发明具有以下优点:
27.1、本发明制备所得的钢材具有耐腐蚀的优点,并且其热浸镀锌后的镀层品质优良、厚度适宜、表面光亮、致密性、耐久性以及坚实性优异,镀层还具有良好的镀层粘附性、优良的镀层加工成型性。
28.2、本发明通过改变钢材热浸镀锌时锌浴的组分以及配比,从而增强镀层与基材之间的结合力即镀面附着力,改变镀层的外观质量。
具体实施方式
29.实施例1
30.一种钢材的热浸镀锌方法,包括以下步骤:
31.(1)镀前处理:对镀覆钢材表面进行处理,为钢材进行热浸镀锌做准备,避免后续热浸镀锌过程中熔锌无法与钢铁正常完全反应,形成最完美的镀锌皮膜组成;
32.镀前处理包括以下步骤:
33.a.脱脂:将钢铁制件浸入脱脂液中进行脱脂,并且脱脂液为7%~10%盐酸和1.5%~2%脱脂抑制剂的混合液,脱脂温度为25℃~50℃,以去除钢铁制件在加工、贮运过程中碰到的油;
34.b酸洗:将制件放入质量分数30%~33%的盐酸中进行酸洗,酸洗过程中适当搅拌
制件,并且酸洗温度控制在18℃~21℃,以去除制件表面存在的氧化皮和铁锈;
35.c.水洗:将完成酸洗后的制件用清水进行冲洗;
36.d.助镀:将酸洗后的制件再浸入一定成分的氯化锌铵助镀液中完成助镀,助镀液温度为60℃~80℃,助镀的作用在于去除酸洗清洗后残留在制件表面的铁盐或氧化物,使制件在进入锌浴时具有最大的表面活性;同时其在制件表面沉积上一层盐膜,可防止制件从助镀池到进入锌锅的一段时间内在空气中锈蚀,还可净化制件浸入锌浴处的液相锌,使制件与液相锌快速浸润并反应;
37.助镀液中氯化锌铵浓度控制在200g/l~400g/l,并且氯化铵与氯化锌重量比为1:1.2~1:1.6,其中w
fecl2
<1%;
38.e.烘干:在助镀后对制件进行烘干,使附有助镀剂的制件尽可能干透,烘干温度为100℃~150℃;
39.(2)热浸镀锌:将已经完成镀前处理的钢材浸入锌浴中,使钢材与熔融锌反应生成一合金化的皮膜,从而完成热浸镀锌,热浸镀锌的温度为435℃~460℃,镀锌时间控制在20s~60s内;
40.其中锌浴包括以下按重量份数配比的原料:
41.zn:98.5份,fe:0.75份,al:0.065份,
42.pb:0.15份,ni:0.08份,bi:0.1份,
43.ce:0.015份;
44.(3)镀后处理:将完成热浸镀锌后的钢材进行后处理,避免破坏镀锌皮膜外观;
45.镀后处理包括以下步骤:
46.a.水冷:制件从锌浴中取出后应尽快水冷,以防止在缓慢冷却时合金层的过量生长导致灰暗镀层;
47.b.钝化:当制件需要较长时间的储运时,应对制件进行钝化处理,以防止在储运过程中产生腐蚀,钝化时将镀后的制件浸入0.1%~0.2%重铬酸钠中。
48.实施例2、实施例3、实施例4与实施例1热浸镀锌方法相同,其区别在于热浸镀锌时实施例2、实施例3、实施例4与实施例1的锌浴的配比不同。
49.实施例1、实施例2、实施例3以及实施例4的锌浴的具体组分与配比如表1所示;
50.表1:实施例1、实施例2、实施例3以及实施例4的锌浴的具体组分与配比
51.[0052][0053]
实施例5、实施例6、实施例7以及实施例8与实施例1的钢材的热浸镀锌方法相同,其区别在于实施例5、实施例6、实施例7以及实施例8与实施例1热浸镀锌时锌浴的组分及配比不同。
[0054]
实施例5、实施例6、实施例7以及实施例8锌浴的组分及配比如表2所示;
[0055]
表2:实施例5、实施例6、实施例7以及实施例8锌浴的组分及配比
[0056][0057]
实验检测
[0058]
本实施例1
‑
8制备所得的钢材,对其热浸镀锌后的镀层进行性能以及外观质量检测,包括镀层厚度、镀层外观质量、镀层附着力、镀层均匀性、镀层耐腐蚀性能以及漏镀面积。
[0059]
镀层厚度根据g b/t2694
‑
2010《输电线路铁塔制造技术条件》中的检测方法检测,具体如下:采用金属涂镀层测厚仪测试,测试时钢板试样每面6处各1电,2面共12点,测试结果按各个测试点所测得的数据以算术平均值计算。
[0060]
镀层外观质量根据gb/t13912
‑
2002《热镀锌标准》中所规定的:热镀层的外观质量指标主要包括主要表面应平滑、无滴瘤、粗糙和锌刺、无起皮、无漏镀、无残留的熔剂渣,在可能影响热浸镀锌工作的使用或耐腐蚀性能的部位不应有锌瘤和锌灰,本发明采用10倍放大镜观察镀层外观质量。
[0061]
镀层附着力根据gb/t2694
‑
2010《输电线路铁塔制造技术条件》中的检测方法检测,具体如下:采用落锤试验方法,测试时试验用的锤子安装在固定的木制试台上,试验面应保持与锤子底座同样高度;试件置于水平,调整试样,使打击点距试样边、角、端部不小于10mm,锤头面向台架中心,锤柄与底座平面垂直后自由落下,以4mm的间隔平行打击5点,检查镀层表面状态。
[0062]
镀层均匀性根据文献《热浸镀锌质量要求及测试方法》中公开的现用的大部分标准如gb/t13912
‑
92、gb/t2694
‑
81中对于镀层的均匀性的控制都是通过控制最小镀层的厚度来控制镀层的均匀性。
[0063]
镀层耐腐蚀性采用5%hcl浸泡20min,5%nacl溶液浸泡20d,考察试片的耐腐蚀性能,通过其失重的百分比来判定耐腐蚀性能的优劣,失重的百分比越小说明镀层耐腐蚀性能越好。
[0064]
漏镀面积根据gb/t13912
‑
2002《热镀锌标准》中的检测方法检测,并且其规定要求每个漏镀面的面积不应超过10cm2。
[0065]
本实施例制备所得的钢材其镀层性能的检测结果如表3所示:
[0066]
表3:本实施例制备所得的钢材其镀层性能的检测结果
[0067]
[0068][0069]
从表3中可以看出:钢材在不同组分以及配比的锌浴中进行热浸镀锌后所得到的镀层的外观质量以及性能具有差异。本发明实施例1
‑
8制备所得的钢材的镀层其性能及外观都符合国家标准,并且其耐腐蚀性、表面光整度、均匀性以及附着力优异,特别是实施例7和实施例8。本实施例1
‑
4在锌浴中掺入稀土ce元素制备所得的镀层其镀层厚度符合国家标准、镀层均匀性、镀面光整度、镀面附着力以及镀面耐腐蚀性能较为优异、镀面漏镀面积小;本实施例5在锌浴中掺入sb和稀土ce元素制备所得的镀层其镀层厚度符合国家标准、镀层均匀性优异、镀面漏镀面积小,但其镀面光整度、镀面附着力以及镀面耐腐蚀性能较差;本实施例6在锌浴中掺入co元素和稀土ce元素制备所得的镀层其镀层厚度符合国家标准、镀层均匀性、镀面光整度、镀面附着力以及镀面耐腐蚀性能较为优异、镀面漏镀面积小;本实施例7和本实施例8在锌浴中掺入co、sb和稀土ce元素制备所得的镀层其镀层厚度符合国家标准、镀层均匀性、镀面光整度、镀面附着力以及镀面耐腐蚀性能优异,并且整个镀面无漏镀;本实施例9未掺入稀土ce元素制备所得的镀层其镀层均匀性、镀面光整度、镀面附着力以及镀面耐腐蚀性能较差、镀面漏镀面积较大。
[0070]
通过实施例1和实施例2
‑
4的对比可知:实施例1在锌浴中掺入稀土ce元素与实施例2
‑
4在锌浴中稀土ce元素制备所得的钢材的镀层其镀层厚度、镀层外观质量、镀层附着
力、镀层均匀性、镀层耐腐蚀性能以及镀面漏镀面积差别不大,无显著变化。因此,说明在锌浴组分相同的条件下,在一定范围内改变锌浴的配比对镀层外观质量以及性能有一定的影响,但其影响较小。
[0071]
通过实施例1在锌浴中掺入稀土ce元素和实施例9在锌浴中未掺入稀土ce元素对比可知:实施例1与实施例9制备所得的钢材其其镀层厚度与镀层均匀性差异不是很大,无显著变化,但是镀层外观质量、镀层附着力、镀面漏镀面积以及镀层耐腐蚀性能差异较大,具有显著变化,实施例1的镀层外观质量、镀层附着力以及镀层耐腐蚀性能优于实施例9。因此,在钢材热浸镀锌的锌浴中掺入稀土ce元素能提高镀面的附着力、光整度以及耐腐蚀性能。
[0072]
通过实施例1在锌浴中掺入稀土ce元素和实施例5在锌浴中掺入sb和稀土ce元素对比可知:实施例1与实施例5制备所得的钢材其镀层厚度与镀层均匀性差异不是很大,无显著变化,但是镀层外观质量、镀层附着力以及镀层耐腐蚀性能差异较大,具有显著变化,实施例1的镀层外观质量、镀层附着力以及镀层耐腐蚀性能优于实施例5。因此,在钢材热浸镀锌的锌浴中同时掺入sb和稀土ce元素,sb能抑制稀土ce元素对钢材镀层镀面光整度、镀面附着力以及镀面耐腐蚀性能的积极作用。
[0073]
通过实施例1在锌浴中掺入稀土ce元素和实施例6在锌浴中掺入co元素和稀土ce元素对比可知:实施例1与实施例6制备所得的钢材其其镀层厚度、镀层外观质量、镀层附着力、镀层均匀性、镀层耐腐蚀性能以及镀面漏镀面积差别不大,无显著变化。因此,在钢材热浸镀锌的锌浴中同时掺入co元素和稀土ce元素,co元素不会抑制也不会加强稀土ce元素对钢材镀层镀面光整度、镀面附着力以及镀面耐腐蚀性能的积极作用。
[0074]
通过实施例1在锌浴中掺入稀土ce元素和实施例7
‑
8在锌浴中掺入co、sb和稀土ce元素对比可知:实施例1与实施例7
‑
8制备所得的钢材其镀层厚度与镀层均匀性差异不是很大,无显著变化,但是镀层外观质量、镀层附着力、镀面漏镀面积以及镀层耐腐蚀性能差异较大,具有显著变化,实施例7
‑
8的镀层外观质量、镀层附着力以及镀层耐腐蚀性能优于实施例1。因此,在钢材热浸镀锌的锌浴中同时掺入co、sb和稀土ce元素,co和sb两元素共同作用能加强稀土ce元素对钢材镀层的镀面光整度、镀面附着力以及镀面耐腐蚀性能的积极作用,使得制备所得钢材镀层具有更优异的性能。
[0075]
由此可见,本发明制备所得的钢材其镀层性能优良,并且本发明在钢材热浸镀锌的锌浴中掺入稀土ce元素能提高镀层的镀面光整度、镀面附着力以及镀面耐腐蚀性能,进一步本发明在钢材热浸镀锌的锌浴中同时掺入co、sb和稀土ce元素,co和sb两元素共同作用能加强稀土ce元素对钢材镀层的镀面光整度、镀面附着力以及镀面耐腐蚀性能的积极作用,使得制备所得钢材镀层具有更优异的性能。