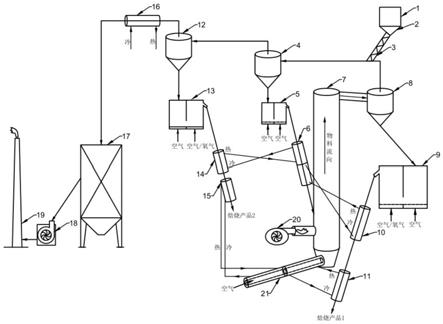
1.本发明属于石煤钒矿提钒技术领域,具体涉及一种石煤钒矿粗细分级氧化焙烧提钒系统及氧化焙烧的方法。
背景技术:2.现行的石煤提钒工艺主要有钠化焙烧-水浸、钙化焙烧-酸(碱)浸、复合添加剂焙烧-浸出、无添加剂氧化焙烧-酸(碱)浸和直接浸出等。悬浮焙烧作为一种流态化焙烧技术,具有气固接触充分、传质传热效率高、作业成本低和节能环保等优势。尤其是neuh系列悬浮焙烧工业化装备及技术在难选铁矿、锰矿、高铁铝土矿、高铁赤泥、含碳金矿和石煤钒矿等难选矿产的高效利用方面取得了一定技术突破,且部分项目已实现工业化应用。相关专利如申请号200720014578.8《悬浮磁化焙烧炉》,cn109943710a《一种铁矿粉多级悬浮态还原焙烧装置及方法》,cn111644267a《一种基于矿相分段精准调控的复杂铁矿石强化分选方法》,cn111500854a《一种工业化处理铁锰矿石的悬浮焙烧系统及方法》,cn107460307a《一种氧化铝悬浮焙烧炉》,cn111485100a《一种含碳金矿悬浮焙烧强化金浸出率的方法》,cn111304465a《一种含钒石煤脱碳-破晶焙烧强化酸浸提钒的方法》,cn111304464a《一种石煤钒矿多段焙烧强化拌酸熟化提钒的方法》,现行的钙化焙烧、复合添加剂焙烧和钠化焙烧过程都存在环保效果差、焙烧效果差和钒浸出率低等问题。而现行的焙烧设备—平窑、竖窑需要将物料制球或烧砖,反应时气固接触不充分,且焙烧产品再破碎、磨矿,会将热量浪费,作业能耗较高。
3.针对石煤钒矿普遍粒度范围较宽,粗粒、细粒含量大的问题,现行悬浮焙烧系统容易出现细粒物料焙烧效果差、浸出率低的问题。这是因为宽粒度分布的石煤钒矿中,细粒物料极易流化,其在反应器中与粗粒物料停留时间短,导致细粒物料焙烧时间不足,焙烧质量不均匀,钒浸出率低。
4.粗粒、细粒石煤的最佳焙烧条件不同,现行装备无法单独控制其操作参数。
5.另外,现行悬浮焙烧设备的排矿温度较高,余热没有有效回收,需要提高热量利用率。
技术实现要素:6.针对现有技术中石煤钒矿普遍粒度范围较宽,粗粒、细粒含量大的问题,本发明的目的是提供一种石煤钒矿粗细分级氧化焙烧提钒系统及氧化焙烧的方法。
7.为达到上述目的,本发明的解决方案是:
8.作为目的之一,本发明提供了一种石煤钒矿粗细分级氧化焙烧提钒系统,其包括给料系统、粗粒物料氧化焙烧系统、细粒物料氧化焙烧系统、负压除尘系统和热量回收系统。
9.给料系统包括料仓和其通过失重称相连的螺旋给料管。
10.粗粒物料氧化焙烧系统包括一级旋风分离器、二级旋风分离器、流动密封阀、主炉
和粗料焙烧反应器,一级旋风分离器上方的进料口通过管道连通至螺旋给料管的底端,一级旋风分离器底部的出料口和流动密封阀相连通,流动密封阀连通至主炉的底端,主炉的底端给料口侧壁设有热交换进气管和燃烧机的燃烧口,主炉的顶端通过管道连通至二级旋风分离器上方的进料口,二级旋风分离器上方的进料口和一级旋风分离器上方的进料口通过管道相连,二级旋风分离器底部的出料口连通至粗料焙烧反应器。
11.细粒物料氧化焙烧系统包括三级旋风分离器和通过其底部的出料口连通的细粒焙烧反应器,三级旋风分离器上方的进料口和一级旋风分离器上方的进料口通过管道相连。
12.负压除尘系统包括依次连通的排气换热器、布袋除尘器、罗茨风机和烟囱,排气换热器和三级旋风分离器上方的进料口通过管道相连。
13.热量回收系统包括换热器、第一一段冷却器、第一二段冷却器、第二一段冷却器、第二二段冷却器和热交换进气管,第一一段冷却器和第一二段冷却器相连接,第二一段冷却器和第二二段冷却器相连接,第一一段冷却器和第二一段冷却器均连通至换热器,用于加热入炉物料;第一一段冷却器的顶端连通至粗粒焙烧反应器的出料口,第二一段冷却器的顶端连通至细粒焙烧反应器的出料口;第一二段冷却器和第二二段冷却器均连通至热交换进气管,用于预热入炉空气。
14.作为本发明的一种优选实施例,流动密封阀、粗料焙烧反应器和细料焙烧反应器的结构相同,均包括反应器腔体和包裹反应器腔体的电热炉套,反应器腔体内设有中心隔板、流化室、松动室和布风板,反应器腔体由顶部的中心隔板分隔开,中心隔板的底端和反应器腔体之间留有空隙并设置布风板,布风板和反应器腔体底部平行,流化室设置在中心隔板的左侧,流化室的外侧中上部设有出料口,松动室设置在中心隔板的右侧,松动室的顶部中心设有进料口。
15.作为本发明的一种优选实施例,流动密封阀、粗料焙烧反应器和细料焙烧反应器内均通入流化风和松动风;流动密封阀内通入流化风的体积流量为1-4m3/h,松动风的体积流量为2-5m3/h,松动风和流化风均为空气;粗料焙烧反应器和细料焙烧反应器内通入流化风的体积流量为12-22m3/h,流化风为空气和氧气混合气,氧气浓度为21-30%,松动风的体积流量为4-9m3/h,松动风为空气。
16.作为本发明的一种优选实施例,电热炉套的温度为600-1050℃。
17.作为本发明的一种优选实施例,粗料焙烧反应器中焙烧温度为850-960℃,焙烧时间为6-30h;细料焙烧反应器中焙烧温度为850-960℃,焙烧时间为5-25h。
18.作为本发明的一种优选实施例,罗茨风机的风机负压为(-3.0)-(-3.5)kpa。
19.作为本发明的一种优选实施例,换热器为套管式换热器,热交换进气管为间壁式热交换进气管,具体为管壳式热交换进气管。
20.作为本发明的一种优选实施例,该石煤钒矿粗细分级氧化焙烧提钒系统中的石煤钒粉矿中v2o5含量0.4-1.7%。
21.作为目的之二,本发明提供了一种利用上述的石煤钒矿粗细分级氧化焙烧提钒系统进行石煤钒矿氧化焙烧的方法,其包括如下步骤:
22.(1)、物料通过给料系统进行入粗粒物料氧化焙烧系统的一级旋风分离器中进行粗细分级,粗粒物料由底部排出,经过流动密封阀进入主炉下部给料口,物料在主炉内提
升,经上部管道进入二级旋风分离器并从其底部的出料口排出,进入粗粒焙烧反应器中进行高温氧化焙烧;
23.(2)、从粗粒焙烧反应器中排出的物料,经过热量回收系统中的第一一段冷却器后,转移至套管式换热器中,从第一一段冷却器底部排出的物料经过第一二段冷却器后,转移至间壁式热交换进气管中,用于加热入炉物料;
24.(3)、从一级旋风分离器分离出的细粒物料,由细粒物料氧化焙烧系统中的三级旋风分离器的底部排出,接着进入细粒焙烧反应器中进行高温氧化焙烧;
25.(4)、从细粒焙烧反应器中排出的物料,经过热量回收系统中的第二一段冷却器后,转移至换热器中,从第二一段冷却器底部排出的物料经过第二二段冷却器后,转移至热交换进气管中,用于预热入炉空气;
26.(5)、从三级旋风分离器排出的烟尘经过负压除尘系统中的排气换热器,收集在布袋除尘器中,气体通过罗茨风机和烟囱排出。
27.由于采用上述方案,本发明的有益效果是:
28.第一、本发明的系统通过设置粗粒焙烧反应器和细粒焙烧反应器,通过一级旋风分离器实现粗细分级,分别对粗粒物料和细粒物料进行单独焙烧,一方面解决了原有焙烧系统细粒物料焙烧效果差、浸出率低的问题,从而避免了粗粒和细粒石煤在一个反应器内,细粒物料易流化效果好,先从反应器中逃出,导致焙烧时间不足,钒浸出率低的问题;另一方面,两个焙烧过程的操作参数可单独控制,如反应温度、反应时间、焙烧气量、氧气浓度等,能针对性优化粗粒、细粒焙烧产品的质量及钒浸出率。
29.第二、本发明的系统中设有两段冷却器和换热器,焙烧产品的热量被高效回收利用,用于加热物料和入炉空气,大大提高了能量利用率。即第一一段冷却器和第二一段冷却器将焙烧产品中的大部分热量转移至套管式换热器中,用于加热入炉物料;第一二段冷却器和第二二段冷却器将焙烧产品中的剩余热量再次回收,使排料温度《90℃,该部分热量被转移至间壁式热交换进气管中,用于预热入炉空气,这大大提高了能量利用率,使该系统整体能耗更低。
30.第三、本发明的系统属于无添加剂的氧化焙烧工艺,可实现石煤粉矿中粗粒、细粒分级氧化焙烧的目的,进而优化焙烧效果,提高钒浸出率。故本发明的石煤钒矿粗细分级氧化焙烧系统具有粗粒、细粒物料焙烧过程分别可控、气固接触充分、能量利用率高、传质传热效率高、作业成本低和高效环保等优点。
附图说明
31.图1为本发明的石煤钒矿粗细分级氧化焙烧提钒系统示意图。
32.图2为本发明的流动密封阀、粗料焙烧反应器和细料焙烧反应器的结构示意图。
33.图3为本发明的石煤钒矿粗细分级氧化焙烧提钒系统能量流动示意图。
34.附图标记:1-料仓、2-失重称、3-螺旋给料管、4-一级旋风分离器、5-流动密封阀、6-换热器、7-主炉、8-二级旋风分离器、9-粗料焙烧反应器、10-第一一段冷却器、11-第一二段冷却器、12-三级旋风分离器、13-细粒焙烧反应器、14-第二一段冷却器、15-第二二段冷却器、16-排气换热器、17-布袋除尘器、18-罗茨风机、19-烟囱、20-燃烧机、21-热交换进气管、22-中心隔板、23-松动室、24-流化室、25-布风板、26-电热炉套。
具体实施方式
35.本发明提供了一种石煤钒矿粗细分级氧化焙烧提钒系统及氧化焙烧的方法。
36.本发明的石煤钒矿粗细分级氧化焙烧提钒系统包括给料系统、粗粒物料氧化焙烧系统、细粒物料氧化焙烧系统、负压除尘系统和热量回收系统四个部分。
37.其中,如图1所示,给料系统包括料仓1和其通过失重称2相连的下端螺旋给料管3,通过失重称2的电机频率可实现给矿量的精确调整。
38.粗粒物料氧化焙烧系统包括一级旋风分离器4、二级旋风分离器8、流动密封阀5、主炉7和粗料焙烧反应器9,一级旋风分离器4上方的进料口通过管道连通至螺旋给料管3的底端,一级旋风分离器4底部的出料口和流动密封阀5相连通,流动密封阀5连通至主炉7的底端,主炉7的底端给料口侧壁设有热交换进气管21(具体为间壁式热交换进气管)和燃烧机20的燃烧口,室温空气被热交换进气管21加热后进入主炉7。燃烧机20以天然气为燃料持续燃烧,将空气进一步加热。主炉7的顶端通过管道连通至二级旋风分离器8上方的进料口,二级旋风分离器8上方的进料口和一级旋风分离器4上方的进料口通过管道相连,二级旋风分离器8底部的出料口连通至粗料焙烧反应器9。由此,一级旋风分离器4、流动密封阀5、主炉7和二级旋风分离器8形成闭路,物料由二级旋风分离器8底部排矿口排出,进入粗粒焙烧反应器9,在此进行高温氧化焙烧。
39.细粒物料氧化焙烧系统包括三级旋风分离器12和通过其底部的出料口连通的细粒焙烧反应器13,三级旋风分离器12上方的进料口和一级旋风分离器4上方的进料口通过管道相连,三级旋风分离器12的固气分离能力极强,所以一级旋风分离器4分离出的细粒物料都由三级旋风分离器12的底部排出,从而进入细粒焙烧反应器13,在此进行高温氧化焙烧。
40.具体地,如图2所示,流动密封阀5、粗料焙烧反应器9和细料焙烧反应器13的结构相同,均包括反应器腔体和包裹反应器腔体的电热炉套26,即电热炉套26包裹在反应器腔体的外壁四周,为反应器腔体提供辅助加温,其控温范围为600-1050℃。反应器腔体内设有中心隔板22、流化室24、松动室23和布风板25,反应器腔体中间由顶部的中心隔板22分隔开,中心隔板22的底端和反应器腔体之间留有空隙(即中心隔板22下侧留有通道,用于物料流通)并设置布风板25,布风板25距离反应器腔体底部有一定距离且平行于反应器腔体底部,流化室24设置在中心隔板22的左侧,流化室24的外侧中上部设有出料口,松动室23设置在中心隔板22的右侧,松动室23的顶部中心设有进料口。由下部吹入的松动风和流化风会透过布风板25,使得反应器腔体内的物料呈现悬浮态。
41.实际上,流动密封阀5、粗料焙烧反应器9和细料焙烧反应器13均通入流化风和松动风,其中的物料在流化风和松动风的作用下形成非机械锁,能起到良好的密封作用,防止窜气。流动密封阀5内通入流化风的体积流量为1-4m3/h,松动风的体积流量为2-5m3/h,松动风和流化风均为空气;粗料焙烧反应器9和细料焙烧反应器13内通入流化风的体积流量为12-22m3/h,流化风为空气和氧气混合气,氧气浓度为21-30%,松动风的体积流量为4-9m3/h,松动风为空气。粗料焙烧反应器9中焙烧温度为850-960℃,焙烧时间为6-30h;细料焙烧反应器13中焙烧温度为850-960℃,焙烧时间为5-25h。焙烧产品被冷却至<90℃后排出。
42.负压除尘系统包括依次连通的排气换热器16、布袋除尘器17、罗茨风机18和烟囱19,罗茨风机18为整体系统提供负压,排气换热器16和三级旋风分离器12上方的进料口通
过管道相连。系统中气体流向为:热交换进气管21
→
主炉7
→
二级旋风分离器8
→
一级旋风分离器4
→
三级旋风分离器12
→
布袋除尘器17
→
罗茨风机18
→
烟囱19。
43.热量回收系统包括换热器6(具体为套管式换热器)、第一一段冷却器10、第一二段冷却器11、第二一段冷却器14、第二二段冷却器15和热交换进气管21(具体为间壁式热交换进气管),第一一段冷却器10和第一二段冷却器11相连接,第二一段冷却器14和第二二段冷却器15相连接,第一一段冷却器10和第二一段冷却器14均连通至换热器6,用于加热入炉物料,即反应器排出的物料温度较高,第一一段冷却器10和第二一段冷却器14可将焙烧产品的热量回收,转移至换热器6中,用于加热下料斜管中的物料;第一一段冷却器10的顶端连通至粗粒焙烧反应器9的出料口,第二一段冷却器14的顶端连通至细粒焙烧反应器13的出料口;第一二段冷却器11和第二二段冷却器15均连通至热交换进气管21,用于预热入炉空气,即第一二段冷却器11和第二二段冷却器15可将焙烧产品的热量再次回收,使排料温度《90℃。该部分热量被转移至热交换进气管21中,用于预热入炉空气。具体地,第一一段冷却器10、第一二段冷却器11、第二一段冷却器14、第二二段冷却器15的上端均为热端,下端均为冷端。
44.该系统的物料流向:失重称2经螺旋给料管3将物料给入管道中,再进入一级旋风分离器4。粗粒物料由一级旋风分离器4下部排出,经过流动密封阀5给入主炉7底部。物料在主炉7内提升,经上部横管进入二级旋风分离器8,再进入到粗粒焙烧反应器9。最后焙烧品1经过两级冷却(即第一一段冷却器10和第一二段冷却器11)后排出;细粒物料由一级旋风分离器4上部排出,经三级旋风分离器12进入细粒焙烧反应器13,最后焙烧品2经过两级冷却(即第二一段冷却器14和第二二段冷却器15)后排出。
45.如图3所示,在该系统稳定运行期间,可认为输入该系统的热量基本都被用于将室温物料、室温气体加热为《90℃的物料和气体。系统热利用率极高,能耗很低。
46.本发明利用上述的石煤钒矿粗细分级氧化焙烧提钒系统进行石煤钒矿氧化焙烧的方法,其包括如下步骤:
47.(1)、启动罗茨风机18,控制风机负压为(-3.0)-(-3.5)kpa,为系统内部提供负压。启动燃烧机20,在罗茨风机18负压的作用下,将天然气燃烧生成的高温烟气抽入主炉7。
48.(2)、向流动密封阀5通入一定量空气(流化风:1-4m3/h,松动风:2-5m3/h)。向细粒焙烧反应器13和粗粒焙烧反应器9底部通入一定量的流化风和松动风。松动风为空气(4-9m3/h),流化风为空气和氧气混合气(12-22m3/h,氧气浓度21-30%)。空气气源由空气压缩机提供。
49.(3)、将石煤钒粉矿(v2o5含量0.4-1.7%)给入料仓1中,启动失重称2,粉矿经螺旋给料管3输送到一级旋风分离器4内,此时物料被加热至350-400℃。在一级旋风分离器4中进行粗细分级,粗粒物料由底部排出,粉矿进入流动密封阀5,流动密封阀5内囤积物料在松动风和流化风作用下形成非机械锁,起到料封作用。再继续进入主炉7下部给料口,粉矿在主炉7内受负压和热气流作用向上提升进入二级旋风分离器8,此时物料被加热到500℃左右。矿粉中的吸附水、层间水以及其他挥发组分被部分脱除,得到预热料。预热料进入粗粒焙烧反应器9中进行高温氧化焙烧,设定电热炉套26的温度为850-960℃,调整预热料在反应器内停留时间为6-30h,该过程中,石煤中的碳质、吸附水、结晶水及黄铁矿等还原性物质几乎被完全脱除。随后,层状硅酸盐含钒矿物(常为白云母、绢云母、伊利石等)的晶体结构
被破坏。晶格破坏过程为:al-o八面体中两oh-受热生成h2o逸出,形成离子空位。这一方面使六元环状结构失衡变形,另一方面使晶格沿c轴方向拉伸膨胀。因为v原子所在八面体伸长变形,结合能降低,故更易被浸出。最终,得到焙烧产品1。
50.(4)、从一级旋风分离器4分离出的细粒物料,由三级旋风分离器12的底部排出,接着进入细粒焙烧反应器13中进行高温氧化焙烧;设定温度为850-960℃,调整物料在反应器内停留时间为5-25h。该过程同样发生上述步骤(3)的反应,最终得到焙烧产品2。
51.(5)、焙烧产品1经过第一一段冷却器10和第一二段冷却器11冷却至小于90℃后排出,焙烧产品2经过第二一段冷却器14和第二二段冷却器15冷却至小于90℃后排出,得到最终的石煤钒矿焙烧产品。
52.(6)、石煤钒矿焙烧产品用于后续硫酸浸出提钒。
53.以下对本发明实施例中的技术方案进行清楚、完整的描述。应当指出的是,本发明描述的实施例仅用来进一步解释和说明,而非对其应用范围进行限制。基于本发明,本领域技术人员在没有作出创造性劳动前提下获得的所有其它实施例,都属于本发明专利的保护范围。
54.实施例1:
55.对某石煤钒矿进行粗细分级氧化焙烧,其中v2o5含量为1.25%,-0.038mm含量为61%,+0.1mm含量为23%。
56.(1)、启动罗茨风机18,控制风机负压为-3.0kpa,为系统内部提供负压启动燃烧机20点燃天然气,使高温烟气进入主炉7。保持主炉7顶部温度为720℃左右。
57.(2)、向流动密封阀5通入2.5m3/h松动风(空气)、2.8m3/h流化风(空气);向粗粒焙烧反应器9通入5m3/h松动风(空气)、20m3/h流化风(空气);向细粒焙烧反应器13通入4.4m3/h松动风(空气)、19m3/h流化风(16m3/h空气,3m3/h氧气)。
58.(3)、设置失重称2给料为120kg/h,进行封料作业。当出料量稳定在120kg/h时,封料完成,降低给矿量至45kg/h,正式开始焙烧作业。
59.(4)、原矿经管道输送到一级旋风分离器4内,经过一次旋风分离的粗粒物料进入流动密封阀5,细粒物料进入三级旋风分离器12中,烟尘收集在布袋除尘器17中,气体通过罗茨风机18和烟囱19排出。
60.(5)、粗粒物料由主炉7进入,受负压驱动向上运动并进入二级旋风分离器8,此时物料被加热到500℃左右。矿粉中的吸附水、层间水以及其他挥发组分被部分脱除。此时获得的产品为预热焙烧料。
61.(6)、预热焙烧料进入粗粒焙烧反应器9中,物料在松动风和流化风作用下形成悬浮态u型料柱。物料的焙烧时间约为15h,设定焙烧温度为880℃。该过程中,含钒矿物的晶格结构被大规模破坏。焙烧产品1被冷却后排出,排矿温度为89℃。
62.(7)、细粒物料进入细粒焙烧反应器13,物料的焙烧时间约为16h,设定焙烧温度为870℃。最后,焙烧产品2被冷却后排出,排矿温度为86℃。
63.(8)、石煤钒矿焙烧产品用于后续硫酸浸出。在相同浸出条件下(浓硫酸用量为9wt%,液固比为1.25:1,助浸剂(氟化钙)用量为2.5%,浸出温度为75℃,浸出时间为7.5h,搅拌转速为850r/min),产品总浸出率为86.32%。总浸出率相比原矿提高了23.34个百分点,相比不分级焙烧料浸出率提高9.67个百分点。
64.实施例2:
65.实施例2方法同实施例1,不同点在于:
66.(1)、对某v2o5含量为0.82%的石煤钒矿进行焙烧。原矿-0.038mm含量为79%,+0.1mm含量为19%。
67.(2)、给料量为35kg/h,粗粒焙烧反应器9的温度为910℃,焙烧时间为24h;细粒焙烧反应器13的温度为900℃,焙烧时间为22h。
68.(3)、焙烧样品在浓硫酸用量为12wt%,液固比为1.1:1,助浸剂(氟化钙)用量为2.25%,浸出温度为85℃,浸出时间为8h,搅拌转速为680r/min的条件下,钒浸出率达85.92%,相比原矿提高了29.58个百分点,相比不分级焙烧料浸出率提高7.28个百分点。
69.实施例3:
70.实施例3方法同实施例1,不同点在于:
71.(1)、对某v2o5含量为1.46%的石煤钒矿进行焙烧。原矿-0.038mm含量65%,+0.1mm含量29%。
72.(2)、给料量为32kg/h,粗粒焙烧反应器9的温度为950℃,焙烧时间为30h;细粒焙烧反应器13温度为940℃,焙烧时间为25h。
73.(3)、焙烧样品在浓硫酸用量为15wt%,液固比为1.25:1,助浸剂(氟化钙)用量为3.5%,浸出温度为90℃,浸出时间为10h,搅拌转速为1000r/min的条件下,钒浸出率达80.62%,相比原矿提高了29.71个百分点,相比原有一段悬浮焙烧料浸出率提高10.03个百分点。
74.上述对实施例的描述是为了便于该技术领域的普通技术人员能理解和使用本发明。熟悉本领域技术人员显然可以容易的对这些实施例做出各种修改,并把在此说明的一般原理应用到其他实施例中,而不必经过创造性的劳动。因此,本发明不限于上述实施例。本领域技术人员根据本发明的原理,不脱离本发明的范畴所做出的改进和修改都应该在本发明的保护范围之内。