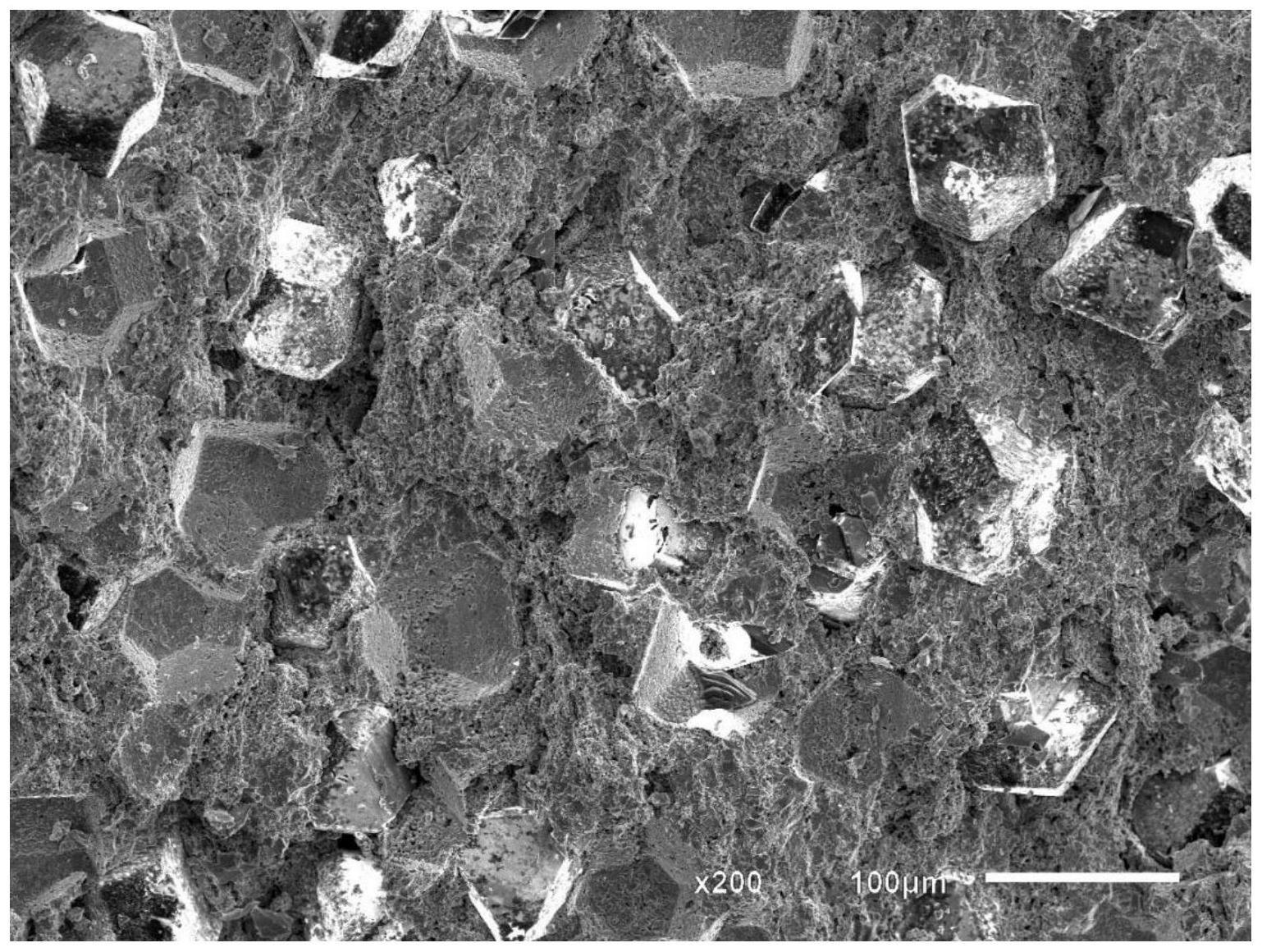
1.本发明属于磨具磨料磨削技术领域,尤其涉及一种用于汽车玻璃磨削的金刚石砂轮。
背景技术:2.汽车玻璃普遍采用高强度、承载能力大、耐冲击以及热稳定性好的钢化玻璃,属于典型的硬脆难加工材料,其强度极限与弹性极限十分接近,因此,当玻璃所承受的载荷稍微超过弹性极限时,就会发生断裂性破坏,导致在加工表面常常会产生凹坑和裂纹,从而在一定程度上约束着玻璃的性能,并且,汽车玻璃是一种边缘处都带有一定弧度的大曲面异性玻璃。因此,由于汽车玻璃自身的硬脆特性以及边缘处特殊的几何形状,使其磨削过程复杂,效率低,成本高,且磨边质量差。
3.超硬材料磨具具有硬度高、耐磨性好、热稳定性好等优点,已经广泛应用到机械加工领域。超硬材料磨具是将结合剂和磨料固结成一定形状,使其具有一定的强度和硬度。而结合剂的选择直接影响着磨具的性能,如果结合剂选择不佳,会使其在磨削加工过程中出现一系列问题,如当胎体对磨料的把持力不够,使其在磨削过程中磨料脱落过快;磨具的自锐性差或气孔率低,使其在磨削时易堵塞等,这些不仅会使得磨削效率低、磨削质量差、磨具寿命低,而且对磨料也会造成严重的浪费。而co作为综合性能最好的结合剂,其与金刚石之间独有的特性,致使在磨削高端汽车玻璃领域具有广泛的应用前景。专利201110157561.9公开发表了一种磨削玻璃金刚石磨轮及其制备方法,其胎体粉末成分为cu75-85wt%、sn15-25wt%的预合金粉末,但由于cu与金刚石的润湿性较差、把持力低,导致在使用时金刚石磨料易脱离。并且,铜基结合剂本身具有较差的自锐性和较低的气孔率,在磨削时易堵塞,导致加工效率降低。
技术实现要素:4.本发明的目的在于克服现有技术的不足之处,提供一种金刚石砂轮,该砂轮具有良好的自锐性和保型性,并且胎体对金刚石磨料的把持力强。另外,本发明的金刚石砂轮主要应用于汽车玻璃的磨削加工,相比传统的fe-co-cu-sn基玻璃砂轮,具有更高的磨削效率、更好的磨边质量以及更长的使用寿命等优点,尤其对高端、特殊的汽车玻璃磨削加工时更为显著。
5.本发明是通过以下技术方案实现的:
6.一种用于汽车玻璃磨削的金刚石砂轮,其中,所述金刚石砂轮原料所占质量百分比为:co粉60~85%、sn粉10~25%、金刚石0.5~5%、造孔剂0~5%。
7.本发明提供的金刚石砂轮,包括金属结合剂、金刚石和造孔剂,其中,所述金属结合剂为纯co、sn元素粉和co-sn预合金粉末中的至少一种;金属结合剂粉末粒度范围为1~50微米,粉末氧含量均小于0.2%。
8.所述造孔剂为石墨、si粉和氧化铝空心球中的一种。
9.上述金刚石砂轮的制备方法,具体包括以下步骤:
10.步骤1:根据权利要求1所述配比称取原材料;
11.步骤2:将步骤1所称取的原材料置于三维混料机中进行混料,混料时间12~24小时,使其混合均匀;
12.步骤3:将步骤2所得粉末中加入3-5%的成型剂和适量溶剂,过 30目筛网进行造粒,并将造粒后的粉末放置干燥箱中进行干燥,干燥温度为75~95℃;
13.步骤4:将步骤3所得混合物粉末倒入圆环模具中,将其放置在热压机上热压成型,最终烧结温度为600~900℃,保温30~60分钟,烧结压力为15~25mpa;
14.步骤5:将步骤4所得的砂轮环,采用ag基钎料和焊剂,钎焊于钢基体上,钎焊温度500~600℃;然后将所制备砂轮进行修型和精加工。
15.本发明的有益效果在于:
16.1.钴作为综合性能最好的结合剂,对金刚石的润湿性好,粘结力大,韧性好,自锐性好,具有较好的耐磨性,钴与金刚石磨料的结合方式为机械镶嵌结合和化学键结合的叠加作用,使得胎体对金刚石的把持力较强。钴基结合剂具有很好的成形性、可烧结性和高温性能,可使胎体的抗弯强度提高,而锡元素熔点低,引入到钴基结合剂中,能够降低其烧结温度和烧结时间,使得在烧结过程中金刚石不会由于温度过高而发生损伤,并且,钴与锡易形成金属间化合物,可以进一步提高胎体对金刚石的把持力,提高磨具的出刃效果和锋利度,在汽车玻璃磨削加工领域具有广泛的应用前景。
17.2.本发明采用预合金粉末以及通过加入适量成形剂和适量溶剂的方式进行造粒,可以使获得的粉末不易团聚,流动性更好,同时,也可以避免成分发生偏析,从而改善了胎体的强度和硬度,提高了胎体对金刚石磨料的把持力。另外,采用预合金粉末也可以进一步降低烧结温度和烧结时间。本发明制备所获得的金刚石砂轮组织均匀、性能稳定,适用于在汽车玻璃磨削中的应用。
附图说明
18.图1为实施例1中金刚石砂轮显微组织sem照片
19.图2为实施例2中金刚石砂轮显微组织sem照片
20.图3为实施例3中金刚石砂轮显微组织sem照片
具体实施方式:
21.以下由特定的具体实施例说明本发明的制备方式及工艺性能,本领域技术人员可由本说明书所揭示的内容全面地了解本发明的优点及作用。
22.实施例1
23.1)将粒度为1~50微米,且含氧量小于0.2%的70%co粉、25%纯粉,2%金刚石以及3%石墨置于三维混料机中进行混料,混料时间 14小时,得到混合物粉末;
24.2)将步骤1所得混合物粉末中加入4%的成形剂和适量溶剂,过 30目筛网进行造粒,并将造粒后的粉末放置干燥箱中进行干燥,干燥温度为78℃;
25.3)将步骤2所得混合物粉末倒入圆环模具中,将其放置在热压机上热压成型,最终烧结温度为850℃,保温45分钟,烧结压力为20mpa;
26.4)将步骤3所得的砂轮环,采用ag基钎料和焊剂,钎焊于钢基体上,钎焊温度520℃;然后将所制备砂轮进行修型和精加工。
27.实施例2
28.1)将粒度为1~50微米,且含氧量小于0.2%的80%co粉、15%sn 粉、1%金刚石以及4%石墨置于三维混料机中进行混料,混料时间 18小时,得到混合物粉末;
29.2)将步骤1所得混合物粉末中加入3%的成形剂和适量溶剂,过 30目筛网进行造粒,并将造粒后的粉末放置干燥箱中进行干燥,干燥温度为78℃;
30.3)将步骤2所得混合物粉末倒入圆环模具中,将其放置在热压机上热压成型,最终烧结温度为650℃,保温40分钟,烧结压力为25mpa;
31.4)将步骤3所得的砂轮环,采用ag基钎料和焊剂,钎焊于钢基体上,钎焊温度550℃;然后将所制备砂轮进行修型和精加工。
32.实施例3
33.1)将粒度为1~50微米,且含氧量小于0.2%的80%co粉、15%sn 粉、2%金刚石以及3%石墨置于三维混料机中进行混料,混料时间 18小时,得到混合物粉末;
34.2)将步骤1所得混合物粉末中加入3%的成形剂和适量溶剂,过 30目筛网进行造粒,并将造粒后的粉末放置干燥箱中进行干燥,干燥温度为78℃;
35.3)将步骤2所得混合物粉末倒入圆环模具中,将其放置在热压机上热压成型,最终烧结温度为850℃,保温30分钟,烧结压力为25mpa; 4)将步骤3所得的砂轮环,采用ag基钎料和焊剂,钎焊于钢基体上,钎焊温度580℃;然后将所制备砂轮进行修型和精加工。