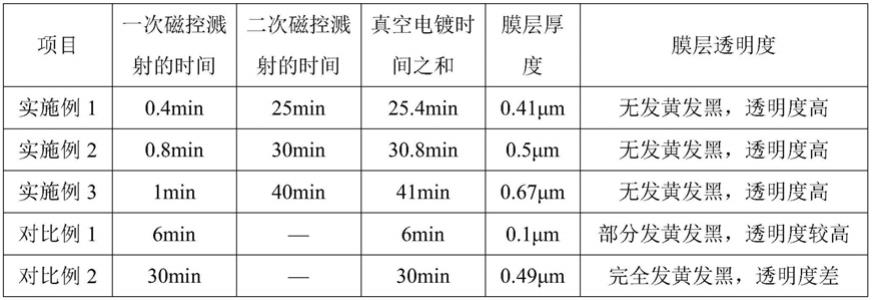
1.本发明涉及首饰制备技术领域,具体涉及一种首饰表面抗氧化膜的制备方法。
背景技术:2.目前,常见的首饰往往包括金、银、铂、钯及其合金等贵金属材质,一般采用手工打造、精密铸造、压力加工、机械加工、电铸、焊接等方法对贵金属材质进行加工制备。用贵金属材质制得的首饰价格一般较昂贵,人们长期佩戴贵金属首饰过程中,首饰表面容易受到外部环境的影响,与人体上的皮肤汗液相互作用而被氧化变色,而且由于贵金属首饰质地较柔软,表面耐磨性能较差,佩戴过程中首饰表面容易被刮花,不仅影响首饰的美观,还会使首饰的质量慢慢变差。
3.为此,在首饰表面往往需要真空电镀二氧化硅或氮化硅作为抗氧化膜,主要起到防止氧化的作用。由于氮化硅颜色偏黄,如果想要氮化硅电镀层达到良好的防氧化、耐磨效果,需要加厚氮化硅电镀层,会明显变黄,影响首饰的美观。相比之下,二氧化硅电镀层具有透明度高、不发黄等优点,是目前首饰表面抗氧化膜的首要选择。
4.现有技术对于二氧化硅电镀层的制备方法包括,将被溅射的硅靶材作为阴极,首饰基件放置在阳极,抽真空后,注入氧气并对硅靶材进行辉光放电,时间为2-5分钟,溅射出的硅离子与氧气在腔体内发生化学反应,生成二氧化硅薄膜沉积在首饰基件上,在首饰表面形成二氧化硅电镀层作为抗氧化膜。然而,由于腔体内注入了纯氧且氧化生成的二氧化硅沉积速度太慢,即使可以应用于纯金或k金这类本身就不易氧化的饰品上,但是对于银镀金、铜镀金等最需要防氧化保护的饰品,往往在真空电镀制备抗氧化膜的过程中,饰品就与氧气发生氧化反应,导致饰品表面极易出现发黄发黑的氧化变色现象。即使通过缩短真空电镀时间来降低饰品被氧化的程度,但是由于真空电镀时间缩短,导致二氧化硅电镀层变薄,抗氧化效果不佳,并不能从根本上解决问题。
5.cn110629063a公开了一种抗氧化耐磨贵金属首饰的制备工艺,待贵金属首饰进行清洗后,在步骤五采用蒸镀溅射方法在首饰工件表面依次镀上铬层、硅层和氟化镁层,但是所述方法并不涉及二氧化硅膜的制备,更未公开如何在二氧化硅膜制备中避免首饰被氧化发黄发黑的问题,同时还可以将二氧化硅膜进一步增厚。
6.cn110172675a公开了一种首饰表面真空处理方法,待首饰清洗后,向抽真空后的真空处理箱充入氩气和高纯度氧气,采用磁控溅射氧化硅靶材或氧化铬靶材,在首饰表面沉积氧化硅镀层或者氧化铬镀层,随后采用电阻式热蒸发的方式蒸发高分子纳米涂层材料,进一步生成高分子纳米涂层,其中,进一步限定氩气和高纯度氧气的比例为1:1,所述高纯度氧气以足以氧化真空处理箱内所有首饰为准。因此,所述方法并未考虑如何在二氧化硅膜制备中避免首饰被氧化发黄发黑的问题。
7.cn103213345a公开了一种具有抗变色耐磨复合膜的形成方法,待工件表面的氧化膜除去后,步骤f限定以多弧离子镀或磁控溅射形成ti膜层作为底层,步骤g限定采用阴极电弧蒸镀与磁控溅射蒸镀交互运用的方法,在ti膜层外表面镀上tisic薄膜层、tisin薄膜
层或tisicn薄膜层作为底部耐磨层。所述方法中ti膜层与耐磨层(透明的类金刚石薄膜层)同时存在,并不涉及将ti膜层转化为tisic薄膜层、tisin薄膜层或tisicn薄膜层的方法。因此,上述方法并不涉及二氧化硅膜的制备,更未公开如何在二氧化硅膜制备中避免首饰被氧化发黄发黑的问题,同时还可以将二氧化硅膜进一步增厚。
8.综上所述,目前亟需开发一种新型的首饰表面抗氧化膜的制备方法,不仅可以在二氧化硅膜制备中避免首饰被氧化发黄发黑的问题,还可以将二氧化硅膜进一步增厚,提高抗氧化和耐磨性能。
技术实现要素:9.鉴于现有技术中存在的问题,本发明提供了一种首饰表面抗氧化膜的制备方法,将待处理首饰作为阳极,硅靶材作为阴极,先在氩气氛围下经一次磁控溅射在待处理首饰表面形成硅膜,可以有效阻隔氧气与首饰表面的接触,杜绝首饰被氧化变色,随后充入氧气经二次磁控溅射将灰色的硅膜氧化成无色透明的二氧化硅膜,并进一步将硅离子氧化成二氧化硅沉积,使得二氧化硅膜明显增厚。本发明所述制备方法不仅可以在二氧化硅膜制备中避免首饰被氧化发黄发黑的问题,还可以利用更厚的二氧化硅膜提高首饰的透明度、耐磨性、光泽度和抗氧化等性能,而且降低了对待处理首饰材质的限制。
10.为达此目的,本发明采用以下技术方案:
11.本发明的目的在于提供一种首饰表面抗氧化膜的制备方法,所述制备方法包括如下步骤:
12.(1)在真空电镀腔室内,将待处理首饰作为阳极,硅靶材作为阴极,进行一次抽真空,充入氩气,经一次磁控溅射在所述待处理首饰表面形成硅膜;
13.(2)对步骤(1)所述真空电镀腔室进行二次抽真空,充入氧气,经二次磁控溅射将步骤(1)所述硅膜氧化成二氧化硅膜并沉积增厚,在首饰表面形成抗氧化膜。
14.本发明所述制备方法先在氩气氛围下经一次磁控溅射在待处理首饰表面形成硅膜,可以有效阻隔氧气与首饰表面的接触,杜绝首饰被氧化变色,随后充入氧气经二次磁控溅射将灰色的硅膜氧化成无色透明的二氧化硅膜,并进一步将硅离子氧化成二氧化硅沉积,使得二氧化硅膜明显增厚。本发明所述制备方法不仅可以在二氧化硅膜制备中避免首饰被氧化发黄发黑的问题,还可以延长4倍以上的真空电镀时间,从而获得厚度为现有技术所得厚度4倍以上的二氧化硅膜作为抗氧化膜,有效提高了首饰的透明度、耐磨性、光泽度和抗氧化等性能,而且降低了对待处理首饰材质的限制。
15.值得说明的是,本发明所述制备方法使用真空磁控溅射镀膜机,将待处理首饰固定在夹具上,关闭镀膜机门,从而形成了真空电镀腔室。
16.作为本发明优选的技术方案,在步骤(1)所述一次磁控溅射之前,所述制备方法还包括步骤(1’):在真空电镀腔室内,将待处理首饰作为阳极,铬靶材作为阴极,进行首次抽真空,充入氩气,经首次磁控溅射在所述待处理首饰表面形成铬膜。
17.值得说明的是,在磁控溅射形成抗氧化膜之前,将铬离子沉积在首饰表面上形成铬膜,可以有效增强抗氧化膜与首饰表面之间的附着力度。
18.作为本发明优选的技术方案,所述首次磁控溅射的时间为0.2-1min,例如0.2min、0.3min、0.4min、0.5min、0.6min、0.7min、0.8min、0.9min或1min等,但并不仅限于所列举的
数值,该数值范围内其他未列举的数值同样适用。
19.值得说明的是,由于待处理首饰往往具有复杂多样的造型,并不容易测定其膜层厚度,本领域技术人员往往根据真空电镀时间来间接反映膜层的厚度。
20.优选地,所述首次磁控溅射的电流为0.8-1.2a,例如0.8a、0.9a、1.0a、1.1a或1.2a等,但并不仅限于所列举的数值,该数值范围内其他未列举的数值同样适用。
21.优选地,所述首次磁控溅射的电压为380v-410v,例如380v、385v、390v、395v、400v、405v或410v等,但并不仅限于所列举的数值,该数值范围内其他未列举的数值同样适用。
22.优选地,所述首次磁控溅射的温度低于50℃,能广泛应用于各种不耐高温的镶嵌类首饰。
23.作为本发明优选的技术方案,步骤(1)所述一次磁控溅射的时间为0.1-2min,例如0.1min、0.2min、0.4min、0.6min、0.8min、1min、1.2min、1.6min、1.8min2min等,但并不仅限于所列举的数值,该数值范围内其他未列举的数值同样适用。
24.值得说明的是,由于待处理首饰往往具有复杂多样的造型,并不容易测定其膜层厚度,本领域技术人员往往根据真空电镀时间来间接反映膜层的厚度。
25.优选地,步骤(1)所述一次磁控溅射的电流为2.8-3.2a,例如2.8a、2.9a、3.0a、3.1a或3.2a等,但并不仅限于所列举的数值,该数值范围内其他未列举的数值同样适用。
26.优选地,步骤(1)所述一次磁控溅射的电压为380v-410v,例如380v、385v、390v、395v、400v、405v或410v等,但并不仅限于所列举的数值,该数值范围内其他未列举的数值同样适用。
27.优选地,步骤(1)所述一次磁控溅射的真空度为5.5-6.5
×
10-3
pa,例如5.5
×
10-3
pa、5.7
×
10-3
pa、6.0
×
10-3
pa、6.1
×
10-3
pa、6.3
×
10-3
pa或6.5
×
10-3
pa等,但并不仅限于所列举的数值,该数值范围内其他未列举的数值同样适用。
28.优选地,步骤(1)所述一次磁控溅射的温度低于50℃,能广泛应用于各种不耐高温的镶嵌类首饰。
29.作为本发明优选的技术方案,步骤(2)所述二次磁控溅射的时间为20-50min,例如20min、24min、28min、32min、36min、40min、44min、46min、48min或50min等,但并不仅限于所列举的数值,该数值范围内其他未列举的数值同样适用。
30.值得说明的是,由于待处理首饰往往具有复杂多样的造型,并不容易测定其膜层厚度,本领域技术人员往往根据真空电镀时间来间接反映膜层的厚度;相比于现有技术采用硅靶材在氧气氛围下进行2-5分钟磁控溅射,本发明先进行0.1-2min的一次磁控溅射形成硅膜,可以有效阻隔氧气与首饰表面的接触,杜绝首饰被氧化变色,再进行20-50min的二次磁控溅射将硅膜氧化成二氧化硅膜并进一步沉积增厚,即,本发明所述制备方法的总真空电镀时间达到现有技术真空电镀时间的4倍以上,从而获得厚度为现有技术所得厚度4倍以上的二氧化硅膜作为抗氧化膜,有效提高了首饰的透明度、耐磨性、光泽度和抗氧化等性能,而且降低了对待处理首饰材质的限制。
31.作为本发明优选的技术方案,步骤(2)所述二次磁控溅射的电流为2.8-3.2a,例如2.8a、2.9a、3.0a、3.1a或3.2a等,但并不仅限于所列举的数值,该数值范围内其他未列举的数值同样适用。
32.优选地,步骤(2)所述二次磁控溅射的电压为380v-410v,例如380v、385v、390v、395v、400v、405v或410v等,但并不仅限于所列举的数值,该数值范围内其他未列举的数值同样适用。
33.优选地,步骤(2)所述二次磁控溅射的真空度为5.5-6.5
×
10-3
pa,例如5.5
×
10-3
pa、5.7
×
10-3
pa、6.0
×
10-3
pa、6.1
×
10-3
pa、6.3
×
10-3
pa或6.5
×
10-3
pa等,但并不仅限于所列举的数值,该数值范围内其他未列举的数值同样适用。
34.优选地,步骤(2)所述二次磁控溅射的温度低于50℃,能广泛应用于各种不耐高温的镶嵌类首饰。
35.值得说明的是,步骤(2)所述二次磁控溅射使得真空电镀腔室内的氧气既可以和首饰表面的单质硅保护膜发生化学反应,又可以和溅射出来的硅离子发生化学反应,在首饰表面上形成透明的二氧化硅薄膜。
36.作为本发明优选的技术方案,在步骤(2)所述二次磁控溅射之后,所述制备方法还包括步骤(3):对步骤(2)所述真空电镀腔室进行三次抽真空,经真空蒸镀在所述抗氧化膜表面沉积氟化镁层。
37.值得说明的是,在真空电镀腔室内对氟化镁材料进行蒸发,使得氟化镁沉积在抗氧化膜表面形成氟化镁层,可以进一步获得疏水防污的效果。
38.作为本发明优选的技术方案,在步骤(3)所述真空蒸镀中,将氟化镁蒸发源与所述抗氧化膜相对且间隔设置在所述真空电镀腔室内,间距为50-300mm,例如50mm、100mm、150mm、200mm、250mm或300mm等,但并不仅限于所列举的数值,该数值范围内其他未列举的数值同样适用。
39.优选地,步骤(3)所述真空蒸镀的时间为1-5min,例如1min、2min、3min、4min或5min等,但并不仅限于所列举的数值,该数值范围内其他未列举的数值同样适用。
40.值得说明的是,由于待处理首饰往往具有复杂多样的造型,并不容易测定其膜层厚度,本领域技术人员往往根据真空蒸镀的时间来间接反映氟化镁膜层的厚度。
41.优选地,步骤(3)所述真空蒸镀的电流为90-100ma,例如90ma、91ma、93ma、95ma、97ma或100ma等,但并不仅限于所列举的数值,该数值范围内其他未列举的数值同样适用。
42.优选地,步骤(3)所述真空蒸镀的电压为2-3v,例如2v、2.1v、2.3v、2.5v、2.6v、2.8v或3v等,但并不仅限于所列举的数值,该数值范围内其他未列举的数值同样适用。
43.优选地,步骤(3)所述真空蒸镀的真空度为5.5-6.5
×
10-3
pa,例如5.5
×
10-3
pa、5.7
×
10-3
pa、6.0
×
10-3
pa、6.1
×
10-3
pa、6.3
×
10-3
pa或6.5
×
10-3
pa等,但并不仅限于所列举的数值,该数值范围内其他未列举的数值同样适用。
44.优选地,步骤(3)所述真空蒸镀的温度低于50℃,能广泛应用于各种不耐高温的镶嵌类首饰。
45.作为本发明优选的技术方案,所述制备方法包括如下步骤:
46.(1’)在真空电镀腔室内,将待处理首饰作为阳极,铬靶材作为阴极,进行首次抽真空,充入氩气,经首次磁控溅射在所述待处理首饰表面形成铬膜;
47.其中,控制所述首次磁控溅射的时间为0.2-1min,电流为0.8-1.2a,电压为380v-410v,温度低于50℃;
48.(1)在步骤(1’)所述真空电镀腔室内,将待处理首饰作为阳极,硅靶材作为阴极,
进行一次抽真空,充入氩气,经一次磁控溅射在所述待处理首饰表面形成硅膜;
49.其中,控制所述一次磁控溅射的时间为0.1-2min,电流为2.8-3.2a,电压为380v-410v,真空度为5.5-6.5
×
10-3
pa,温度低于50℃;
50.(2)对步骤(1)所述真空电镀腔室进行二次抽真空,充入氧气,经二次磁控溅射将步骤(1)所述硅膜氧化成二氧化硅膜并沉积增厚,在首饰表面形成抗氧化膜;
51.其中,控制所述二次磁控溅射的时间为20-50min,电流为2.8-3.2a,电压为380v-410v,真空度为5.5-6.5
×
10-3
pa,温度低于50℃;
52.(3)将氟化镁蒸发源与所述抗氧化膜相对且间隔设置在所述真空电镀腔室内,间距为50-300mm,对步骤(2)所述真空电镀腔室进行三次抽真空,经真空蒸镀在所述抗氧化膜表面沉积氟化镁层;
53.其中,控制所述真空蒸镀的时间为1-5min,电流为90-100ma,电压为2-3v,真空度为5.5-6.5
×
10-3
pa,温度低于50℃。
54.与现有技术方案相比,本发明至少具有以下有益效果:
55.(1)本发明所述首饰表面抗氧化膜的制备方法先在氩气氛围下经一次磁控溅射在待处理首饰表面形成硅膜,可以有效阻隔氧气与首饰表面的接触,杜绝首饰被氧化变色,随后充入氧气经二次磁控溅射将灰色的硅膜氧化成无色透明的二氧化硅膜,并进一步将硅离子氧化成二氧化硅沉积,使得二氧化硅膜明显增厚;
56.(2)本发明所述首饰表面抗氧化膜的制备方法不仅可以在二氧化硅膜制备中避免首饰被氧化发黄发黑的问题,还可以延长4倍以上的真空电镀时间,获得厚度为现有技术所得厚度4倍以上的二氧化硅膜作为抗氧化膜,有效提高了首饰的透明度、耐磨性、光泽度和抗氧化等性能;
57.(3)本发明所述首饰表面抗氧化膜的制备方法降低了对待处理首饰材质的限制。
具体实施方式
58.为便于理解本发明,本发明列举实施例如下。本领域技术人员应该明了,所述实施例仅仅是帮助理解本发明,不应视为对本发明的具体限制。
59.实施例1
60.本实施例提供了一种首饰表面抗氧化膜的制备方法,所述制备方法包括如下步骤:
61.(1’)在真空电镀腔室内,将待处理首饰作为阳极,铬靶材作为阴极,进行首次抽真空,充入氩气,经首次磁控溅射在所述待处理首饰表面形成铬膜;
62.其中,控制所述首次磁控溅射的时间为0.5min,电流为1a,电压为400v,温度低于50℃;
63.(1)在步骤(1’)所述真空电镀腔室内,将待处理首饰作为阳极,硅靶材作为阴极,进行一次抽真空,充入氩气,经一次磁控溅射在所述待处理首饰表面形成硅膜;
64.其中,控制所述一次磁控溅射的时间为0.4min,电流为3a,电压为400v,真空度为6
×
10-3
pa,温度低于50℃;
65.(2)对步骤(1)所述真空电镀腔室进行二次抽真空,充入氧气,经二次磁控溅射将步骤(1)所述硅膜氧化成二氧化硅膜并沉积增厚,在首饰表面形成抗氧化膜;
66.其中,控制所述二次磁控溅射的时间为25min,电流为3a,电压为400v,真空度为6
×
10-3
pa,温度低于50℃;
67.(3)将氟化镁蒸发源与所述抗氧化膜相对且间隔设置在所述真空电镀腔室内,间距为150mm,对步骤(2)所述真空电镀腔室进行三次抽真空,经真空蒸镀在所述抗氧化膜表面沉积氟化镁层;
68.其中,控制所述真空蒸镀的时间为3min,电流为95ma,电压为2.5v,真空度为6
×
10-3
pa,温度低于50℃。
69.实施例2
70.本实施例提供了一种首饰表面抗氧化膜的制备方法,所述制备方法包括如下步骤:
71.(1’)在真空电镀腔室内,将待处理首饰作为阳极,铬靶材作为阴极,进行首次抽真空,充入氩气,经首次磁控溅射在所述待处理首饰表面形成铬膜;
72.其中,控制所述首次磁控溅射的时间为0.5min,电流为1a,电压为400v,温度低于50℃;
73.(1)在步骤(1’)所述真空电镀腔室内,将待处理首饰作为阳极,硅靶材作为阴极,进行一次抽真空,充入氩气,经一次磁控溅射在所述待处理首饰表面形成硅膜;
74.其中,控制所述一次磁控溅射的时间为0.8min,电流为2.8a,电压为380v,真空度为5.5
×
10-3
pa,温度低于50℃;
75.(2)对步骤(1)所述真空电镀腔室进行二次抽真空,充入氧气,经二次磁控溅射将步骤(1)所述硅膜氧化成二氧化硅膜并沉积增厚,在首饰表面形成抗氧化膜;
76.其中,控制所述二次磁控溅射的时间为30min,电流为2.8a,电压为380v,真空度为5.5
×
10-3
pa,温度低于50℃;
77.(3)将氟化镁蒸发源与所述抗氧化膜相对且间隔设置在所述真空电镀腔室内,间距为150mm,对步骤(2)所述真空电镀腔室进行三次抽真空,经真空蒸镀在所述抗氧化膜表面沉积氟化镁层;
78.其中,控制所述真空蒸镀的时间为3min,电流为95ma,电压为2.5v,真空度为6
×
10-3
pa,温度低于50℃。
79.实施例3
80.本实施例提供了一种首饰表面抗氧化膜的制备方法,所述制备方法包括如下步骤:
81.(1’)在真空电镀腔室内,将待处理首饰作为阳极,铬靶材作为阴极,进行首次抽真空,充入氩气,经首次磁控溅射在所述待处理首饰表面形成铬膜;
82.其中,控制所述首次磁控溅射的时间为0.5min,电流为1a,电压为400v,温度低于50℃;
83.(1)在步骤(1’)所述真空电镀腔室内,将待处理首饰作为阳极,硅靶材作为阴极,进行一次抽真空,充入氩气,经一次磁控溅射在所述待处理首饰表面形成硅膜;
84.其中,控制所述一次磁控溅射的时间为1min,电流为3.2a,电压为410v,真空度为6.5
×
10-3
pa,温度低于50℃;
85.(2)对步骤(1)所述真空电镀腔室进行二次抽真空,充入氧气,经二次磁控溅射将
步骤(1)所述硅膜氧化成二氧化硅膜并沉积增厚,在首饰表面形成抗氧化膜;
86.其中,控制所述二次磁控溅射的时间为40min,电流为3.2a,电压为410v,真空度为6.5
×
10-3
pa,温度低于50℃;
87.(3)将氟化镁蒸发源与所述抗氧化膜相对且间隔设置在所述真空电镀腔室内,间距为150mm,对步骤(2)所述真空电镀腔室进行三次抽真空,经真空蒸镀在所述抗氧化膜表面沉积氟化镁层;
88.其中,控制所述真空蒸镀的时间为3min,电流为95ma,电压为2.5v,真空度为6
×
10-3
pa,温度低于50℃。
89.对比例1
90.本对比例提供了一种首饰表面抗氧化膜的制备方法,所述制备方法包括如下步骤:
91.(1)在真空电镀腔室内,将待处理首饰作为阳极,铬靶材作为阴极,进行首次抽真空,充入氩气,经首次磁控溅射在所述待处理首饰表面形成铬膜;
92.其中,控制所述首次磁控溅射的时间为0.5min,电流为1a,电压为400v,温度低于50℃;
93.(2)在步骤(1)所述真空电镀腔室内,将待处理首饰作为阳极,硅靶材作为阴极,进行一次抽真空,充入氧气,经一次磁控溅射在所述待处理首饰表面形成抗氧化膜;
94.其中,控制所述一次磁控溅射的时间为6min,电流为3a,电压为400v,真空度为6
×
10-3
pa,温度低于50℃;
95.(3)将氟化镁蒸发源与所述抗氧化膜相对且间隔设置在所述真空电镀腔室内,间距为150mm,对步骤(2)所述真空电镀腔室进行二次抽真空,经真空蒸镀在所述抗氧化膜表面沉积氟化镁层;
96.其中,控制所述真空蒸镀的时间为3min,电流为95ma,电压为2.5v,真空度为6
×
10-3
pa,温度低于50℃。
97.对比例2
98.本对比例提供了一种首饰表面抗氧化膜的制备方法,参照对比例1所述制备方法,区别仅在于:步骤(2)所述一次磁控溅射的时间为30min。
99.上述实施例和对比例均采用相同的待处理首饰,对于制备方法完成后的首饰进行如下表征:
100.(1)膜层厚度:按照轻工行业标准qb/t 1135-2006《首饰金、银覆盖层厚度的测定x射线荧光光谱法》中规定的方法,采用x射线荧光光谱仪,依次经过仪器校准、标样的校准与仪器的调整、样品的测试进行膜层厚度的测定;
101.(2)膜层透明度:在一定日光灯照明条件下,采用目测方式观察膜层是否发黄发黑,判断膜层透明度情况。
102.值得说明的是,上述表征针对的是制备方法结束后首饰表面的复合膜层,但是位于中部的二氧化硅膜层(抗氧化膜)是主要膜层,可以从复合膜层厚度间接反映二氧化硅膜层(抗氧化膜)的厚度情况,具体表征结果见表1。
103.表1
[0104][0105]
综上所述,本发明所述制备方法先在氩气氛围下经一次磁控溅射在待处理首饰表面形成硅膜,可以有效阻隔氧气与首饰表面的接触,杜绝首饰被氧化变色,随后充入氧气经二次磁控溅射将灰色的硅膜氧化成无色透明的二氧化硅膜,并进一步将硅离子氧化成二氧化硅沉积,使得二氧化硅膜明显增厚。本发明所述制备方法不仅可以在二氧化硅膜制备中避免首饰被氧化发黄发黑的问题,还可以延长4倍以上的真空电镀时间,获得厚度为现有技术所得厚度4倍以上的二氧化硅膜作为抗氧化膜,有效提高了首饰的透明度、耐磨性、光泽度和抗氧化等性能,而且降低了对待处理首饰材质的限制。
[0106]
对比例1所述制备方法生成的二氧化硅沉积速度太慢,导致氧气在于溅射出来的硅离子发生氧化反应的同时,氧气也和真空电镀腔室内的首饰表面发生氧化反应,抗氧化膜会稍微发黄发黑,而当待处理首饰的材质为易被氧化的银镀金、铜镀金等,往往有20-30%出现氧化变色、发黄发黑的现象;对比例2在对比例1的基础上,将一次磁控溅射的时间延长至实施例1所述的30min,将会进一步加深首饰表面氧化变色的程度,导致抗氧化膜完全发黄发黑,透明度变差。
[0107]
申请人声明,本发明通过上述实施例来说明本发明的详细工艺设备和工艺流程,但本发明并不局限于上述详细工艺设备和工艺流程,即不意味着本发明必须依赖上述详细工艺设备和工艺流程才能实施。所属技术领域的技术人员应该明了,对本发明的任何改进,对本发明产品各原料的等效替换及辅助成分的添加、具体方式的选择等,均落在本发明的保护范围和公开范围之内。