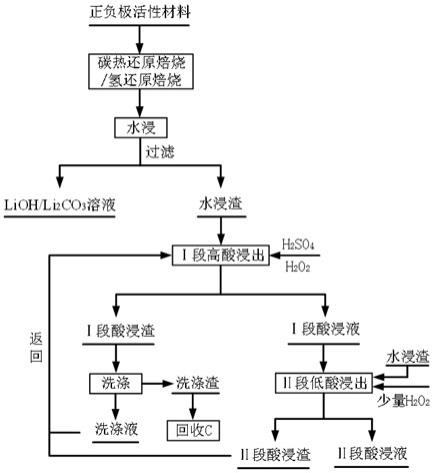
1.本发明涉及动力锂电池回收技术领域,尤其是涉及一种废动力电池正极材料的两段逆流浸出方法。
背景技术:2.新能源汽车的发展作为绿色低碳循环发展经济体系的重大战略决策部署之一,其每年在汽车新车销量的占比情况,始终是关注的热点。在新能源汽车关键核心部件突破等多重助力下,新能源汽车市场占有率日渐新高,预估2025年新车销量将达20%左右。动力电池作为新能源汽车的核心部件之一,其平均寿命大约5~8年,意味着将有大量废动力电池产生。
3.废动力电池含有大量有价金属及有毒电解质,对其进行回收,对缓解镍钴锂等关键矿产供需矛盾、保护生态环境方面具有重要的战略意义和实用价值。关于废动力电池有价金属回收的方法很多,分别为火法冶金、湿法冶金、火法焙烧-湿法冶金联合和生物冶金,其中碳热还原焙烧-水浸和氢还原焙烧-水浸作为火法焙烧-湿法冶金联合两种主要方法,在一定条件下可实现正极活性材料的还原裂解,其中ni/co/mn以金属单质或金属氧化物形式存在,li以可溶于水的li2co3或li2o形式存在,对焙烧料水浸可实现优先提锂,被得到广泛研究及应用。但水浸渣ni/co酸浸过程浸出率仍较低,且酸浸液含有大量残酸及难除杂质cu离子,后续净化除杂需消耗大量中和剂,造成渣量较大,残酸浪费。
4.鉴于此,特提出本发明。
技术实现要素:5.本发明的目的在于提供一种废动力电池正极材料的两段逆流浸出方法,以解决现有技术中存在的ni/co浸出率低、酸浸液残酸高及杂质cu除杂困难等问题。
6.本发明提供的技术方案如下:一种废动力电池正极材料的两段逆流浸出方法,包括:在对所述正极材料进行焙烧、水浸和过滤后,将得到的水浸渣进行两段逆流浸出,所述两段逆流浸出包括ⅰ段浸出和ⅱ段浸出;其中:所述ⅰ段浸出使用浓硫酸和双氧水进行浸出;所述ⅱ段浸出包括在所述ⅰ段浸出后得到的ⅰ段酸浸液中加入所述水浸渣和双氧水,溶液的ph值控制在2~4。
7.本发明通过采用两段逆流浸出方法,不仅能实现废锂电池有价金属ni/co/mn/li的高效浸出、降低酸浸液残酸和减少废水排放量,而且能充分利用水浸渣ni/co金属的还原性,起到初步除铜的目的。
8.在一个实施方案中,在所述ⅰ段浸出的过程中,以液固比3~6:1的比例配置水浸渣浆液(去离子水与水浸渣的液固比3~6:1);所述浓硫酸的用量为理论量的1~2倍,所述双氧水的用量为3~10 vol.%(相对于去离子水的体积百分比)。利用h2so4+h2o2对水浸渣有价金
属进行ⅰ段高酸浸出,过滤,分别得到ⅰ段酸浸液和ⅰ段酸浸渣。
9.在一个实施方案中,所述ⅱ段浸出中,所述水浸渣的用量为使得加入所述水浸渣后溶液的ph保持在 2~4之间。
10.在一个实施方案中,所述ⅱ段浸出中,h2o2用量以溶液不含fe
2+
为准;h2o2的用量为2~5 vol.%。
11.在一个实施方案中,所述ⅰ段浸出和所述ⅱ段浸出的反应温度20~90 ℃,反应时间1~4 h。
12.在一个实施方案中,ⅰ段浸出得到的酸浸渣经洗涤后,洗涤液返回ⅰ段浸出进行循环,洗涤渣用于回收c。洗涤可采用水进行洗涤。
13.在一个实施方案中国,往ⅰ段酸浸液中加入水浸渣,并添加少量h2o2,进行ⅱ段低酸浸出,过滤,得到的ⅱ段酸浸液进入下一步净化除杂工序;ⅱ段酸浸渣无需洗涤直接返回ⅰ段高酸浸出。
14.在一个实施方案中,所述洗涤液、所述ⅱ段酸浸渣和所述水浸渣单独或同时进行ⅰ段浸出。同时进行ⅰ段浸出时,洗涤液能替代少量ⅰ段浸出矿浆配置所需的去离子水,ⅱ段酸浸渣一般较少,可直接加入ⅰ段浸出过程进行浸出,根据i段酸浸液ph《2进行判定,进而调节合适的用量配比。
15.在一个实施方案中,所述焙烧为碳还原焙烧或氢还原焙烧;焙烧温度400~1000℃,焙烧时间1~3 h。对正极材料采取碳热还原焙烧或氢还原焙烧,得到焙烧料,经水浸、过滤,分别得到含ni/co金属水浸渣和富含li水浸液。
16.在一个实施方案中,所述废动力电池正极材料包含镍酸锂、钴酸锂、镍钴锰三元或镍钴铝三元中的一种或多种的组合。
17.本发明涉及的基本原理是:1)采用碳热还原焙烧,在一定焙烧温度下,正极活性材料结构将被破坏,得到焙烧料,其中ni/co将以金属单质或金属氧化物形式存在,mn、li分别主要以mno、li2co3形式存在。对其进行水浸,能实现li的优先提取,ni/co/mn等有价元素则存在于水浸渣中。
18.主要发生的反应如下:li2o+co2(g)=li2co3ꢀꢀꢀꢀꢀꢀꢀꢀ
ꢀꢀꢀꢀꢀꢀꢀꢀꢀꢀꢀꢀꢀꢀꢀꢀꢀꢀꢀꢀꢀꢀꢀꢀꢀꢀꢀꢀꢀꢀꢀꢀꢀꢀꢀ
(1)co3o4+1/2c=3coo+1/2co2(g)
ꢀꢀꢀꢀꢀꢀꢀꢀꢀꢀꢀꢀꢀꢀꢀꢀꢀꢀꢀꢀ
(2)coo+1/2c=co+1/2co2(g)
ꢀꢀꢀꢀꢀꢀꢀꢀꢀꢀꢀꢀꢀꢀꢀꢀꢀꢀꢀꢀꢀꢀꢀꢀ
(3)mno2+1/2c=mno+1/2co2(g)
ꢀꢀꢀꢀꢀꢀꢀꢀꢀꢀꢀꢀꢀꢀꢀꢀꢀꢀꢀꢀꢀ
(4)coo+co(g)=co+co2(g)
ꢀꢀꢀꢀꢀꢀꢀꢀꢀꢀꢀꢀꢀꢀꢀꢀꢀꢀꢀꢀꢀꢀꢀꢀꢀꢀ
(5)nio+1/2c=ni+1/2co2(g)
ꢀꢀꢀꢀꢀꢀꢀꢀꢀꢀꢀꢀꢀꢀꢀꢀꢀꢀꢀꢀꢀꢀꢀꢀꢀ
(6)nio+co(g) =ni+co2(g)
ꢀꢀꢀꢀꢀꢀꢀꢀꢀꢀꢀꢀꢀꢀꢀꢀꢀꢀꢀꢀꢀꢀꢀꢀꢀꢀ
(7)采用氢还原焙烧,通入一定氢气量,在一定焙烧温度下,正极活性材料结构将被破坏,得到焙烧料,其中ni/co将以金属单质或金属氧化物形式存在,mn、li分别主要以mno、li2o形式存在。对其进行水浸,li2o将与h2o反应生成易溶于水的lioh,实现li的优先提取,ni/co/mn等有价元素则存在于水浸渣中。主要发生的反应如下:co3o4+h2(g)=3coo+h2o(g)
ꢀꢀꢀꢀꢀꢀꢀꢀꢀꢀꢀꢀꢀꢀꢀꢀꢀꢀꢀꢀ
(8)coo+h2(g)=co+h2o(g)
ꢀꢀꢀꢀꢀꢀꢀꢀꢀꢀꢀꢀꢀꢀꢀꢀꢀꢀꢀꢀꢀꢀꢀꢀ
(9)
mno2+h2(g)=mno+h2o(g)
ꢀꢀꢀꢀꢀꢀꢀꢀꢀꢀꢀꢀꢀꢀꢀꢀꢀꢀꢀꢀ
(10)nio+h2(g)=ni+h2o(g)
ꢀꢀꢀꢀꢀꢀꢀꢀꢀꢀꢀꢀꢀꢀꢀꢀꢀꢀꢀꢀꢀꢀꢀ
(11)li2o+h2o=2lioh
ꢀꢀꢀꢀꢀꢀꢀꢀꢀꢀꢀꢀꢀꢀꢀꢀꢀꢀꢀꢀꢀꢀꢀꢀꢀꢀꢀ
(12)综上,经碳热还原焙烧/氢还原焙烧-水浸后,ni/co/mn以金属单质或金属氧化物存在于水浸渣中,li则以li2co3或lioh存在于水溶液中。
19.2)对水浸渣采取两段逆流浸出:ⅰ段酸浸液酸度较高,经ⅱ段低酸浸出,能显著降低ⅰ段酸浸液酸度,充分利用残酸,减少中和剂用量。其中硫酸理论量根据主要金属及杂质与硫酸反应进行计算。
[0020]ⅰ段酸浸主要金属发生的反应如下:ni
(s) + h2so
4(aq) = niso
4(aq) + h
2(g)
ꢀꢀꢀꢀꢀꢀ
ꢀꢀꢀꢀꢀꢀꢀꢀꢀꢀꢀꢀꢀꢀꢀꢀꢀꢀꢀ
(13)co
(s) + h2so
4(aq) = coso
4(aq) + h
2(g)
ꢀꢀ
ꢀꢀꢀꢀꢀꢀꢀꢀꢀꢀꢀꢀꢀꢀꢀꢀꢀꢀꢀꢀꢀꢀ
(14)mno
(s) + h2so
4(aq) = mnso
4(aq) + h2o
(aq)
ꢀꢀꢀꢀꢀꢀꢀꢀꢀꢀꢀꢀꢀ
ꢀꢀꢀꢀꢀ
(15)nio
(s) + h2so
4(aq) = niso
4(aq) + h2o
(aq)
ꢀꢀꢀꢀꢀꢀꢀꢀꢀꢀꢀꢀꢀꢀꢀꢀꢀꢀꢀꢀ
(16)coo
(s) + h2so
4(aq) = coso
4(aq) + h2o
(aq)
ꢀꢀꢀꢀꢀꢀꢀꢀꢀꢀꢀꢀꢀꢀꢀꢀ
(17)ⅰ段酸浸主要杂质的反应如下:2fe
(s) + 3h2so
4(aq) + 3h2o
2 = fe2(so4)
3(aq) + 6h2o
(aq)
ꢀꢀ
ꢀꢀꢀꢀꢀ
(18)2al
(s) + 3h2so
4(aq) = al2(so4)
3(aq) + 3h
2 (g)
ꢀꢀꢀꢀꢀꢀꢀꢀꢀꢀꢀ
ꢀꢀꢀꢀꢀꢀꢀꢀꢀ
(19)cu
(s) + h2so
4(aq) + h2o
2 = cuso
4(aq) + 2h2o
(aq)
ꢀꢀꢀꢀꢀꢀ
ꢀꢀꢀꢀꢀꢀꢀꢀ
(20)ⅱ段酸浸除可能发生(1)~(20)反应外,还将发生如下反应:ni
(s) + cuso
4(aq) = niso
4(aq) + cu
(s)
ꢀꢀꢀꢀꢀꢀꢀꢀꢀꢀꢀꢀꢀꢀꢀꢀꢀ
(21)co
(s) + cuso
4(aq) = coso
4(aq) + cu
(s)
ꢀꢀꢀꢀꢀꢀꢀꢀꢀꢀꢀꢀꢀꢀꢀꢀ
(22)综上,通过对水浸渣采取两段逆流浸出,并控制ⅱ段酸浸液一定ph值,不仅能实现降酸、减少中和剂用量的目的,而且能起到初步除cu的效果。但ⅱ段酸浸液ph值不宜过高,否则将导致fe/al中和沉淀进入ⅱ段酸浸渣,造成杂质循环累积。
[0021]
有益效果:本发明提供的对废动力电池正极材料两段逆流浸出,具有以下优点:1)在酸耗最低的情况下,能实现ni、co高效浸出,达到资源最大化回收;2)ⅱ段酸浸液残酸量少,在净化除杂过程所需中和剂少,不会产生大量渣量;3)充分利用了ni/co的还原性,达到了cu的初步除杂目的。
附图说明
[0022]
为了更清楚地说明本发明具体实施方式或现有技术中的技术方案,下面将对具体实施方式或现有技术描述中所需要使用的附图作简单地介绍,显而易见地,下面描述中的附图是本发明的一些实施方式,对于本领域普通技术人员来讲,在不付出创造性劳动的前提下,还可以根据这些附图获得其他的附图。
[0023]
图1为本发明的工艺流程图。
具体实施方式
[0024]
下面将结合实施例对本发明的技术方案进行清楚、完整地描述,显然,所描述的实
施例是本发明一部分实施例,而不是全部的实施例。基于本发明中的实施例,本领域普通技术人员在没有做出创造性劳动前提下所获得的所有其他实施例,都属于本发明保护的范围。
[0025]
实施例1对废licoo2电池采取放电、拆解、破碎等预处理步骤后,得到正负极活性材料。采用碳热还原焙烧法,对正负极活性材料进行焙烧,在焙烧温度700℃、焙烧时间2 h和含碳量20%条件下,得到焙烧料;焙烧料经水浸,液固分离,分别得到含锂水浸液和含co等金属水浸渣。
[0026]
(1)对水浸渣进行ⅰ段高酸浸出,在h2so4用量为理论量的1.3倍、液固比4:1、h2o2用量5 vol.%、反应温度70℃和反应时间2 h条件下,co、li浸出率分别大于99.8%、99.7%,ⅰ段酸浸液中,各离子含量如下:co 60.25 g/l、li 4.36 g/l、al 3.89 g/l、fe 0.3 g/l、cu 0.25 g/l和f 1.25 g/l,ⅰ段酸浸渣洗涤后,得到洗涤液和洗涤渣,洗涤渣送往回收c。
[0027]
(2)往ⅰ段酸浸液中缓慢加入水浸渣,控制ⅱ段酸浸液ph 3.3,经反应温度70℃、反应时间2 h后,过滤,分别得到ⅱ段酸浸液和ⅱ段酸浸渣,ⅱ段酸浸液中,各离子含量如下:co 62.25 g/l、li 4.58 g/l、al 3.78 g/l、fe 0.35 g/l、cu 5.00 mg/l和f 1.38 g/l,ⅱ段酸浸液进行下一步净化除杂工序。
[0028]
(3)按ⅰ段高酸浸出条件,合理配入洗涤液、ⅱ段酸浸渣、水浸渣及外加纯水(根据i段酸浸液ph《2进行判定,进而调节合适的用量配比),依次进行ⅰ段高酸浸出和ⅱ段低酸浸出,循环7~8次后,ⅱ段酸浸渣留存另做处理。
[0029]
经过步骤(1)~(3)后,co、li浸出率分别大于99.7%、99.5%,cu除杂率大于97%,ⅱ段酸浸液ph 3.3,残酸少,且杂质al/fe/f不存在杂质循环累积,废水排放量少。图1为本发明的工艺流程图。
[0030]
实施例2对废licoo2电池采取放电、拆解、破碎等预处理步骤后,得到正负极活性材料。采用氢还原焙烧法,对正负极活性材料进行焙烧,在焙烧温度500℃、焙烧时间2 h和氢气流量为3 l/h条件下,得到焙烧料;焙烧料经水浸,液固分离,分别得到含锂水浸液和含co金属水浸渣。
[0031]
(1)对水浸渣进行ⅰ段高酸浸出,在h2so4用量为理论量的1.3倍、液固比4:1、h2o2用量5 vol.%、反应温度70℃和反应时间2 h条件下,co、li浸出率分别大于99.8%、99.7%,ⅰ段酸浸液中,各离子含量如下:co 60.20 g/l、li 4.40 g/l、al 3.79 g/l、fe 0.28 g/l、cu 0.27 g/l和f 1.28 g/l,ⅰ段酸浸渣洗涤后,得到洗涤液和洗涤渣,洗涤渣送往回收c。
[0032]
(2)往ⅰ段酸浸液中缓慢加入水浸渣,控制ⅱ段酸浸液ph 3.3,经反应温度70℃、反应时间2 h后,过滤,分别得到ⅱ段酸浸液和ⅱ段酸浸渣,ⅱ段酸浸液中,各离子含量如下:co 62.15 g/l、li 4.61 g/l、al 3.80 g/l、fe 0.32 g/l、cu 4.50 mg/l和f 1.34 g/l,ⅱ段酸浸液进行下一步净化除杂工序。
[0033]
(3)按ⅰ段高酸浸出条件,合理配入洗涤液、ⅱ段酸浸渣、水浸渣及外加纯水(根据i段酸浸液ph《2进行判定,进而调节合适的用量配比),依次进行ⅰ段高酸浸出和ⅱ段低酸浸出,循环7~8次后,ⅱ段酸浸渣留存另做处理。
[0034]
经过步骤(1)~(3)后,co、li浸出率分别大于99.8%、99.6%,cu除杂率大于98%,ⅱ段
酸浸液ph 3.3,残酸少,且杂质al/fe/f不存在杂质循环累积,废水排放量少。
[0035]
实施例3对废lini
x
coymnzo2电池采取放电、拆解、破碎等预处理步骤后,得到正负极活性材料。采用碳热还原焙烧法,对正负极活性材料进行焙烧,在焙烧温度700℃、焙烧时间2 h和含碳量20%条件下,得到焙烧料;焙烧料经水浸,液固分离,分别得到含锂水浸液和含ni/co金属水浸渣。
[0036]
(1)对水浸渣进行ⅰ段高酸浸出,在h2so4用量为理论量的1.1倍、液固比3:1、h2o2用量5 vol.%、反应温度70℃和反应时间2 h条件下,ni、co、mn、li浸出率分别大于99.7%、99.7%、99.9%、99.6%,ⅰ段酸浸液中,各离子含量如下:ni 67.52 g/l、co 23.68 g/l、mn 49.40 g/l、li 7.27 g/l、al 5.72 g/l、fe 0.14 g/l、cu 0.19 g/l和f 1.41 g/l,ⅰ段酸浸渣洗涤后,得到洗涤液和洗涤渣,洗涤渣送往回收c。
[0037]
(2)往ⅰ段酸浸液中缓慢加入水浸渣,控制ⅱ段酸浸液ph 3.3,经反应温度70℃、反应时间2 h后,过滤,分别得到ⅱ段酸浸液和ⅱ段酸浸渣,ⅱ段酸浸液中,各离子含量如下:ni 69.57 g/l、co 24.41 g/l、mn 51.20 g/l、li 8.10 g/l、al 6.17 g/l、fe 0.15 g/l、cu 5.10 mg/l和f 1.42g/l,ⅱ段酸浸液进行下一步净化除杂工序。
[0038]
(3)按ⅰ段高酸浸出条件,合理配入洗涤液、ⅱ段酸浸渣、水浸渣及外加纯水(根据i段酸浸液ph《2进行判定,进而调节合适的用量配比),依次进行ⅰ段高酸浸出和ⅱ段低酸浸出,循环7~8次后,ⅱ段酸浸渣留存另做处理。
[0039]
经过步骤(1)~(3)后,ni、co、mn、li浸出率分别大于99.8%、99.8%、99.9%、99.9%,cu除杂率大于98%,ⅱ段酸浸液ph 3.3,残酸少,且杂质al/fe/f不存在杂质循环累积,废水排放量少。
[0040]
实施例4对废lini
x
coymnzo2电池采取放电、拆解、破碎等预处理步骤后,得到正负极活性材料。采用碳热还原焙烧法,对正负极活性材料进行焙烧,在焙烧温度700℃、焙烧时间2 h和含碳量20%条件下,得到焙烧料;焙烧料经水浸,液固分离,分别得到含锂水浸液和含ni/co金属水浸渣。
[0041]
(1)对水浸渣进行ⅰ段高酸浸出,在h2so4用量为理论量的1.1倍、液固比3:1、h2o2用量5 vol.%、反应温度70℃和反应时间2 h条件下,ni、co、mn、li浸出率分别大于99.7%、99.7%、99.9%、99.6%,ⅰ段酸浸液中,各离子含量如下:ni 67.52 g/l、co 23.68 g/l、mn 49.40 g/l、li 7.27 g/l、al 5.72 g/l、fe 0.14 g/l、cu 0.19 g/l和f 1.41 g/l,ⅰ段酸浸渣洗涤后,得到洗涤液和洗涤渣,洗涤渣送往回收c。
[0042]
(2)往ⅰ段酸浸液中缓慢加入水浸渣,控制ⅱ段酸浸液ph 3.5,经反应温度70℃、反应时间2 h后,过滤,分别得到ⅱ段酸浸液和ⅱ段酸浸渣,ⅱ段酸浸液中,各离子含量如下:ni 70.10 g/l、co 25.31 g/l、mn 52.30 g/l、li 8.23 g/l、al 5.38 g/l、fe 0.13 g/l、cu 0.40 mg/l和f 1.44 g/l,ⅱ段酸浸液进行下一步净化除杂工序。
[0043]
(3)按ⅰ段高酸浸出条件,合理配入洗涤液、ⅱ段酸浸渣、水浸渣及外加纯水,依次进行ⅰ段高酸浸出和ⅱ段低酸浸出,循环7~8次后,ⅱ段酸浸渣留存另做处理。
[0044]
经过步骤(1)~(3)后,ni、co、mn、li浸出率分别大于99.8%、99.8%、99.9%、99.9%,cu除杂率大于99%,ⅱ段酸浸液ph 3.3,残酸少,且杂质al/fe/f不存在杂质循环累积,废水排
放量少。
[0045]
实施例5对废lini
x
coymnzo2电池采取放电、拆解、破碎等预处理步骤后,得到正负极活性材料。采用氢还原焙烧法,对正负极活性材料进行焙烧,在焙烧温度500℃、焙烧时间2 h和氢气流量为3 l/h条件下,得到焙烧料;焙烧料经水浸,液固分离,分别得到含锂水浸液和含ni/co金属水浸渣。
[0046]
(1)对水浸渣进行ⅰ段高酸浸出,在h2so4用量为理论量的1.1倍、液固比3:1、h2o2用量5 vol.%、反应温度70℃和反应时间2 h条件下,ni、co、mn、li浸出率分别大于99.8%、99.7%、99.9%、99.7%,ⅰ段酸浸液中,各离子含量如下:ni 67.53 g/l、co 23.75 g/l、mn 49.42 g/l、li 7.30 g/l、al 5.78 g/l、fe 0.16 g/l、cu 0.23 g/l和f 1.43 g/l,ⅰ段酸浸渣洗涤后,得到洗涤液和洗涤渣,洗涤渣送往回收c。
[0047]
(2)往ⅰ段酸浸液中缓慢加入水浸渣,控制ⅱ段酸浸液ph 3.3,经反应温度70℃、反应时间2 h后,过滤,分别得到ⅱ段酸浸液和ⅱ段酸浸渣,ⅱ段酸浸液中,各离子含量如下:ni 67.00 g/l、co 24.58 g/l、mn 51.35 g/l、li 8.24 g/l、al 6.18 g/l、fe 0.18 g/l、cu 6.00 mg/l和f 1.46 g/l,ⅱ段酸浸液进行下一步净化除杂工序。
[0048]
(3)按ⅰ段高酸浸出条件,合理配入洗涤液、ⅱ段酸浸渣、水浸渣及外加纯水,依次进行ⅰ段高酸浸出和ⅱ段低酸浸出,循环7~8次后,ⅱ段酸浸渣留存另做处理。
[0049]
经过步骤(1)~(3)后,ni、co、mn、li浸出率分别大于99.8%、99.8%、99.9%、99.9%,cu除杂率大于98%,ⅱ段酸浸液ph 3.3,残酸少,且杂质al/fe/f不存在杂质循环累积,废水排放量少。
[0050]
对比例1对废licoo2电池采取放电、拆解、破碎等预处理步骤后,得到正负极活性材料。采用碳热还原焙烧法,对正负极活性材料进行焙烧,在焙烧温度700℃、焙烧时间2 h和含碳量20%条件下,得到焙烧料;焙烧料经水浸,液固分离,分别得到含锂水浸液和含co等金属水浸渣。
[0051]
对水浸渣直接进行高酸浸出,在h2so4用量为理论量的1.3倍、液固比4:1、h2o2用量5 vol.%、反应温度70℃和反应时间2 h条件下,co、li浸出率分别大于99.8%、99.7%,酸浸液各离子含量如下:co 60.25 g/l、li 4.36 g/l、al 3.89 g/l、fe 0.3 g/l、cu 0.25 g/l和f 1.25 g/l,酸浸液送往净化除杂工序。
[0052]
送往净化除杂酸浸液ph《0,酸度较高,调节ph至达到fe、al除杂完全,需加入大量中和剂,造成残酸浪费,中和渣量过大,夹带大量co有价金属,损失严重。
[0053]
对比例2如实施例3的方法步骤,不同之处在于,往ⅰ段酸浸液中缓慢加入水浸渣,控制ⅱ段酸浸液ph 4.3,经反应温度70℃、反应时间2 h后,过滤,分别得到ⅱ段酸浸液和ⅱ段酸浸渣。ⅱ段酸浸液中,各离子含量如下:ni 66.60 g/l、co 24.20 g/l、mn 50.85 g/l、li 8.30 g/l、al 0.22 g/l、fe 0.49 mg/l、cu 0.25 mg/l和f 0.26 g/l,ⅱ段酸浸液进行下一步净化除杂工序。
[0054]
当ph略高于本发明限定的ph范围时,除了cu被除杂,al、fe、f等杂质也会因中和或絮凝沉淀存在于渣中,当渣再次返回高酸浸出时,al、fe、f等杂质再次溶解进入酸浸液中,
导致杂质循环反复酸浸-沉淀。
[0055]
最后应说明的是:以上各实施例仅用以说明本发明的技术方案,而非对其限制;尽管参照前述各实施例对本发明进行了详细的说明,本领域的普通技术人员应当理解:其依然可以对前述各实施例所记载的技术方案进行修改,或者对其中部分或者全部技术特征进行等同替换;而这些修改或者替换,并不使相应技术方案的本质脱离本发明各实施例技术方案的范围。