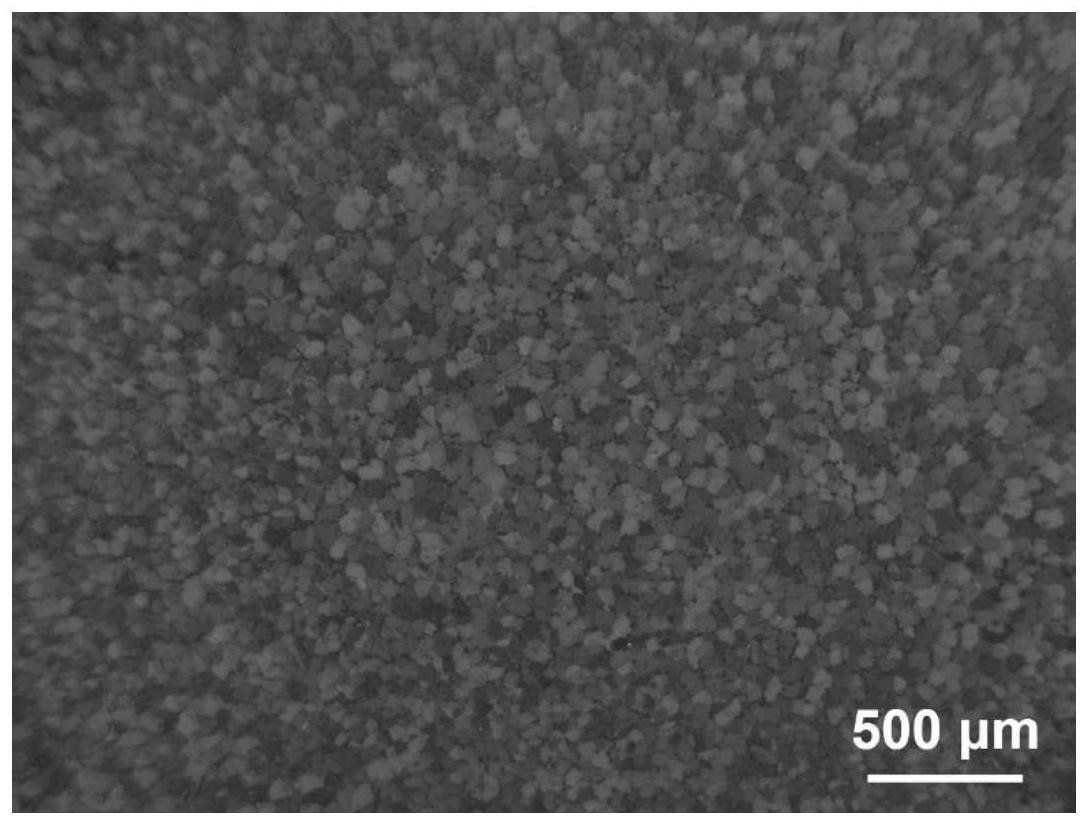
一种提高mg-zr中间合金对镁合金细化效果的方法
技术领域
1.本发明属于铸造镁合金技术领域,涉及一种镁合金晶粒细化的方法,具体地说,涉及一种提高mg-zr中间合金对镁合金细化效果的方法。
背景技术:2.镁合金是目前实际应用中最轻的金属结构材料,具有比强度比刚度高、减震性好、电磁屏蔽性强等优势,因此镁合金部件在航空航天、交通运输、3c产品等领域获得了广泛应用。晶粒细化可以进一步提高镁合金的综合力学性能,并可以改善镁合金的铸造工艺性能,对镁合金的推广应用有重要的意义。
3.zr是镁合金(不含al、mn、si、fe)最有效的晶粒细化剂,在熔炼工艺过程中通过mg-zr中间合金向镁液中加入质量分数为0.5%的zr就可以获得明显的晶粒细化效果。zr在镁合金中的存在形式主要有两种:溶解于镁基体中的溶质原子zr和未溶解的以颗粒形式存在的zr粒子。溶解的溶质原子zr和未溶解的颗粒zr均会对镁合金的晶粒细化起作用:溶质zr主要是通过形成成分过冷效应实现晶粒细化,而颗粒zr主要是通过异质形核效应实现晶粒细化。大量研究表明,溶质zr的成分过冷效应对细化晶粒的贡献较颗粒zr的异质形核效应要高。
4.但并不是所有的未溶解的颗粒zr都能够作为mg的异质形核核心的。颗粒zr需要满足两个条件才能够通过异质形核效应达到晶粒细化的效果:第一,zr的粒径必须满足一定的条件,通常认为粒径为数微米的zr核才能够在镁液中稳定存在并有可能发挥异质形核的效果;第二,符合粒径要求的颗粒zr的表面需要暴露出能与mg基体形成晶格匹配的晶面取向,这样才能使zr核与mg基体之间的界面能最低,使mg依附在zr核上继续生长。然而,由于现有的商用mg-zr中间合金主要通过含zr熔盐电解法制备的,mg-zr中间合金中的zr大量团聚于mg晶粒的晶界处,使得这些大粒径的团聚并不满足zr作为形核核心时对粒径的要求;其次,很难保证通过熔盐电解所制得的纯zr颗粒的表面正好能够暴露出与mg基体合适的晶格匹配面;最后,电解法制备的mg-zr中间合金中,zr主要是以未溶解的颗粒zr为主,而溶质zr含量较低。因此,上述事实导致目前采用商用mg-zr中间合金对镁合金的细化效率并不高,大量团聚的、没有暴露出合适晶格匹配面的zr核是无用的zr,且zr的收得率仅有30%。
5.上述镁合金的zr细化难题已经催生了少量对mg-zr中间合金改性的研究。经专利与文献检索发现,cn201810186568.5公开了一种通过搅拌摩擦加工预处理来打碎商用mg-30wt%zr中间合金中的zr团聚;文献grain refinement of pure magnesium using rolled zirmax(r)master alloy(mg-33.3zr)(通过轧制后的mg-33.3zr中间合金对纯镁进行晶粒细化)(《symposium on magnesium technology》2003;pp215-220)中记载了通过轧制对mg-30wt%zr中间合金进行预处理,破碎大尺寸的zr颗粒团聚。上述这些方法均能显著改善zr核的粒径和分布,有效提高mg-zr中间合金的细化效果。然而,这些方法很难使mg-zr中间合金中zr粒暴露出与mg基体的晶格匹配面,无法实现颗粒zr向溶质zr转变,也很难大幅提高mg-zr中间合金中溶质zr的含量。
6.专利zl202010616056.5中公开了一种通过高频脉冲交流tig焊对mg-zr中间合金板材进行多道次填丝加工,配合重熔后快速冷却,以同时实现颗粒zr团聚的分散、颗粒zr向溶质zr转变的目的。采用该方法预处理的mg-zr中间合金对镁合金的细化效果大幅度提高。但是该方法存在两点不足,其一,通过该方法并不能调整mg-zr中间合金中zr的晶格取向,无法使mg-zr中间合金中的zr核暴露出与mg最有效的晶格匹配面;其次,该预处理方法效率不高,不适合工业化大规模生产。因此在满足能够提高mg-zr中间合金对镁合金细化效果的基础上,开发一种还能适合于工业化大规模生产的mg-zr中间合金预处理方法就显得至关重要。
7.综上所述,发明人认为,针对当前商用mg-zr中间合金对镁合金细化效率不高的问题,必须要开发一种能够同时实现破碎zr团聚、提高zr溶质含量、使zr核能够暴露与mg基体相适合的晶格匹配面的预处理方法,且该预处理方法需要能够适应于工业化大规模生产。
技术实现要素:8.针对现有技术存在的上述不足,本发明的目的在于针对mg-zr中间合金开发一种同时实现破碎zr团聚、提高zr溶质含量、使zr核能够暴露与mg基体相适合的晶格匹配面的预处理方法,且该预处理方法能够适应于工业化大规模生产。通过本方法对现有的商用mg-zr中间合金进行预处理后,能够大幅度提高mg-zr中间合金对镁合金的细化效果,提高所制备的镁合金的力学性能。
9.为了实现上述技术效果,本发明提出了一种全新的mg-zr中间合金预处理方法,这与现有的预处理方法有显著的不同。现有的预处理方法仅能够通过大塑性变形等方法破碎zr粒团聚,很难大幅度mg-zr中间合金里mg基体中的zr溶质含量,也无法实现调控zr核表面的晶格取向,因此现有的mg-zr中间合金的细化潜力还没有被完全挖掘出来。本方法通过重熔和热处理的联用,不仅能够将mg-zr中间合金中部分未溶解的颗粒zr转变为溶质原子zr,还能改善mg-zr中间合金中未溶解zr核的晶格取向,具体是通过以下技术方案实现的:
10.第一方面,本发明提供一种提高mg-zr中间合金对镁合金细化效果的方法,包括将mg-zr中间合金进行加热重熔并随后进行热处理的步骤。这与现有的预处理方法有很大不同,主要在于现有的方法主要是通过挤压、轧制、搅拌摩擦加工等大塑性变形的方法,简单、机械式地将zr粒团聚破碎掉。而本方法首先将mg-zr中间合金进行重熔,以使得通过含zr熔盐电解所制得的mg-zr中间合金中zr颗粒分布得更加均匀。同时,通过zr容颜电解法制备的mg-zr中间合金的mg基体晶粒尺寸较大,通过重熔工艺发挥出zr的合金化效果,则mg基体的晶粒更加细小,这样就可以减小zr粒在后续热处理过程中为了到达理想的固溶效果在mg基体中所需要扩散移动的距离,加速zr粒在mg基体中的溶解和扩散速度,为后续热处理做组织准备。同时,由于采用zr熔盐电解制得的mg-zr中间合金基体一般含有少量杂质,这些杂质通常会降低镁基体的熔点,就会限制了后续热处理温度的提高,即限制了热处理的固溶效果。而由于mg-zr二元合金相图的溶质平衡分配系数>1,即随着mg基体中zr含量的提高,mg基体的熔点会逐渐提高。在固溶热处理之前通过重熔工艺能够适当提高mg基体中的zr溶质浓度,这样就可以提高mg基体的熔点,则后续的固溶热处理的温度就可以更高,避免mg基体在后续固溶处理的过程中发生熔化,提高固溶处理的效果。
11.重熔后的热处理的目的则在于,通过高温固溶处理使zr粒在高温下固溶到mg基体
中,进一步提高mg基体中zr溶质原子的浓度,使大量的颗粒zr转变成为溶质原子zr。再通过低温时效处理,实现与mg基体存在共格关系的zr沉淀相的大量析出,这样就可以改善原本mg-zr中间合金中zr核的晶格取向,提高mg-zr中间合金的细化效果。可见,本发明无论是在原理和技术方案上均与现有的简单塑性变形方法有很大不同。
12.作为本发明的一个实施方案,重熔包括以下步骤:
13.a1、将mg-zr中间合金置于熔炼炉中进行加热,加热温度为650~680℃;
14.a2、待mg-zr中间合金熔化后,对熔体进行机械搅拌5~10min;
15.a3、将mg-zr中间合金浇铸到模具中进行凝固,所述模具的选择满足合金液冷却速度为20℃/s-200℃/s。模具可选择导热速度快的材质,在一些实施例中选择浇铸到水冷的铜质模具中。
16.熔体温度越高,熔体的粘度就越小。将mg-zr中间合金在650~680℃的较低温度下加热重熔,其目的是为了使重熔的中间合金熔体的粘度保持在一个较大范围,这样,就抑制了mg-zr中间合金中大密度的zr粒在坩埚中发生沉降,避免mg-zr中间合金在重熔过程中的均质程度发生降低,也避免了因zr粒沉降而导致的损耗。采用机械搅拌或外加能量对mg-zr中间合金熔体处理5~10min是为了使zr团聚被分散,且外加能量下能够加速zr的溶解与在基体中的扩散。处理时间太短不利于zr团聚的分散,而处理时间过长会导致熔体吸气严重,使有益的zr核被氧化烧损。处理过后将mg-zr中间合金熔体浇铸到水冷的铜质模具中,一方面是为了通过快速冷却的方式使得大量在高温条件下的溶质zr固溶进mg基体中,另一方面是为了细化mg基体的晶粒,减小在后续固溶处理过程中为达到理想的固溶状态zr粒所需要扩散迁移的距离。
17.作为本发明的一个实施方案,所述外加能量场为超声场、电场、磁场中的单一能量场或者多个能量场复合。
18.作为本发明的一个实施方案,热处理包括固溶处理和时效处理两个步骤。固溶处理主要是为了使zr粒尽可能多的固溶进mg基体,提高mg基体中溶质zr的含量,而通过时效处理,则能够促进溶质zr重新转变成与mg基体具有一定位向关系的zr沉淀相,改善细化处理过程中zr粒的异质形核效果。
19.作为本发明的一个实施方案,固溶处理温度为620~650℃,固溶处理时间为5~10h。时效处理温度为80~150℃,时效处理时间为1~15h。zr在镁基体固相中固溶度的是随着温度的提高而显著提高的,但是当镁基体转变为液相后,zr在镁液中的固溶度会迅速降低。因此,需要在保证mg-zr中间合金基体不熔化的条件下尽可能提高固溶温度。这与结构材料的固溶处理有着本质的区别,结构材料在固溶处理过程中要兼顾固效果和晶粒在高温下的粗化,而mg-zr中间合金是熔炼的原材料,不需要考虑晶粒粗化的问题,因此在保证不熔化的基础上,固溶温度越高越好。由于在较低温度下zr在mg基体中的平衡固溶度很低,因此其脱溶倾向较其他的合金元素大。只有在较低的时效温度下,才有利于获得非常细小、均匀的zr沉淀相,这样更有利于这些zr沉淀相在用作细化处理时发挥出异质形核的效果,显著提高mg-zr中间合金的细化效果。
20.作为本发明的一个实施方案,在固溶热处理过程中,mg-zr中间合金被包埋在mgo粉末中。由于本发明中所需要的固溶处理温度非常高,一方面,将mg-zr中间合金包埋在mgo粉末中可以从热力学的角度抑制mg-zr中间合金中mg基体的氧化反应,另一方面,由于mgo
粉末在高温热处理过程中会逐渐被烧结成型,因此烧结成型后的mgo粉对mg-zr中间合金还有一定的支撑和保护作用,既隔绝了空气,同时又避免在热处理过程中mg-zr中间合金因偶有熔化而导致合金坍塌外溢。
21.第二方面,本发明还提供一种根据前述的方法获得的mg-zr中间合金。该mg-zr中间合金可作为镁合金细化专用mg-zr中间合金。
22.第三方面,本发明还提供一种前述的mg-zr中间合金在制备镁合金中的应用,在向镁合金熔体中加入mg-zr中间合金进行细化处理时,对镁合金熔体进行两段式加热保温。采用本发明预处理后的mg-zr中间合金制备镁合金能有效提高mg-zr中间合金对镁合金的晶粒细化效果。
23.作为本发明的一个实施方案,所述镁合金包括但不限于mg-y-zr、mg-gd-zr、mg-nd-zr、mg-zn-zr、mg-gd-y-zr。
24.作为本发明的一个实施方案,在向镁合金熔体中加入mg-zr中间合金进行细化处理时,对镁合金熔体进行两段式加热保温。两段式加热保温的目的主要在于:在高温段下保温时,镁合金熔体粘度较低,此时不仅便于mg-zr中间合金中zr粒的均匀分散,同时高温下zr在mg液中的固溶度更高,利于zr的溶解扩散;在低温段下保温时,由于zr在mg液中的固溶度较高温段有所降低,此时由于zr过饱和而在mg液中均匀析出大量的细小弥散的zr核,这些zr核能够作为镁合金浇铸后凝固时的异质形核核心,大幅提高熔体中有效形核核心的数量。
25.作为本发明的一个实施方案,两段式加热保温的具体参数为:首先将镁合金熔体温度加热到780~820℃,向镁合金熔体中加入经过热处理的mg-zr中间合金,待mg-zr中间合金全部熔化后保温5~10min,将镁合金熔体温度缓慢降低到680~720℃并保温5~10min,浇铸。高温段温度充分考虑了zr在mg液中的溶解扩散速度,而低温段温度则即综合考虑了zr异质形核核心的析出和镁液浇铸后的的流动充型能力。
26.作为本发明的一个实施方案,所述mg-zr中间合金用量为镁液质量的1%~10%。
27.与现有技术相比,本发明具有如下有益效果:
28.1)本发明通过简单的重熔和热处理的联用,可实现商用mg-zr中间合金中颗粒zr向溶质原子zr的大幅度转变,同时还能够显著细化未溶解zr核的尺寸,改善其在mg基体中的位向关系,大幅度提高其对镁合金的细化效果与衰退效应。
29.2)在对镁合金熔体的细化处理过程中,通过两段式加热保温方法,先在高温段下使大量的zr溶解扩散进入镁液中,随后在低温段下使zr核过饱和析出,在镁液中产生大量细小、弥散的zr异质形核核心,提高mg-zr中间合金的细化效果。
30.3)本发明无需对mg-zr中间合金进行复杂的塑性变形等处理,仅仅通过常规的热处理便能够实现mg-zr中间合金细化效果的大幅度提高,非常适合于工业化推广应用。
附图说明
31.通过阅读参照以下附图对非限制性实施例所作的详细描述,本发明的其它特征、目的和优点将会变得更明显:
32.图1为实施例5中通过本发明中预处理后的mg-30zr(wt%)中间合金细化的mg-9gd-3y合金的金相显微组织图;
33.图2为实施例5中通过商用的mg-30zr(wt%)中间合金细化的mg-9gd-3y合金的金相显微组织图。
具体实施方式
34.下面结合具体实施例对本发明进行详细说明。以下实施例将有助于本领域的技术人员进一步理解本发明,但不以任何形式限制本发明。应当指出的是,对本领域的普通技术人员来说,在不脱离本发明构思的前提下,还可以做出若干变化和改进。这些都属于本发明的保护范围。
35.需要说明的是,以下实施例1-5中采用的虽然都是普通的mg-30wt%zr中间合金铸锭,但不是同一块铸锭或切取位置不同,从而其zr颗粒平均粒径、溶质zr含量等数据不一致。
36.实施例1
37.以熔炼mg-3wt%y-0.5wt%zr镁合金为例,分两组进行实验。
38.一.mg-zr中间合金的预处理
39.从商用的mg-30wt%zr中间合金铸锭中切取一块板材,未预处理前的mg-zr中间合金中zr平均粒径约为12μm,溶质zr含量为0.22wt%。将mg-zr中间合金置于熔炼炉中进行加热,加热温度为650℃,待mg-zr中间合金熔化后,对熔体进行机械搅拌处理5min,再将mg-zr中间合金浇铸到水冷的铜质模具中进行凝固。将重熔得到的mg-zr中间合金进行固溶加时效处理,固溶温度为620℃,固溶时间为5h,固溶热处理时,mg-zr中间合金被包埋在mgo粉末中。时效处理温度为100℃,时效处理时间为1h。预处理后的mg-zr中间合金中zr平均粒径约为1.2μm,溶质zr含量为2.44wt%。
40.二.熔炼浇注mg-3wt%y-0.5wt%zr镁合金
41.第一组熔炼实验按照目标成分为mg-3wt%y-0.5wt%zr预先按比例配置纯镁锭,mg-25wt%y、以及前述步骤预处理后的mg-zr中间合金锭,并对mg-3wt%y镁合金熔体进行两段式加热保温。首先将mg-3wt%y镁合金熔体温度加热到780℃,向镁合金熔体中加入经过热处理的mg-zr中间合金,待mg-zr中间合金全部熔化保温5min,将镁合金熔体温度缓慢降低到680℃并保温5min,浇铸。经过金相晶粒尺寸统计分析,使用预处理后的mg-zr中间合金细化的mg-3wt%y-0.5wt%zr合金平均晶粒尺寸为49μm。
42.第二组熔炼实验与第一组实验的熔炼、浇注条件均一致,仅将第一组实验中使用的预处理后的mg-zr中间合金改为商用的mg-30wt%zr中间合金,经金相晶粒尺寸统计分析,第二组熔炼实验制备的mg-3wt%y-0.5wt%zr合金平均晶粒尺寸为91μm。
43.上述两组实验结果对比表明,本发明的方法能有效提高mg-zr中间合金对镁合金的晶粒细化效果。
44.实施例2
45.以熔炼mg-3wt%gd-0.5wt%zr镁合金为例,分两组进行实验。
46.一.mg-zr中间合金的预处理
47.从商用的mg-30wt%zr中间合金铸锭中切取一块板材,未预处理前的mg-zr中间合金中zr平均粒径约为12μm,溶质zr含量为0.21wt%。将mg-zr中间合金置于熔炼炉中进行加热,加热温度为660℃,待mg-zr中间合金熔化后,对熔体进行超声处理6min,再将mg-zr中间
合金浇铸到水冷的铜质模具中进行凝固。将重熔得到的mg-zr中间合金进行固溶加时效处理,固溶温度为630℃,固溶时间为6h,固溶热处理时,mg-zr中间合金被包埋在mgo粉末中。时效处理温度为110℃,时效处理时间为5h。预处理后的mg-zr中间合金中zr平均粒径约为1.1μm,溶质zr含量为2.41wt%。
48.二.熔炼浇注mg-3wt%gd-0.5wt%zr镁合金
49.第一组熔炼实验按照目标成分为mg-3wt%gd-0.5wt%zr预先按比例配置纯镁锭,mg-25wt%gd、以及前述步骤预处理后的mg-zr中间合金锭,并对mg-3wt%gd镁合金熔体进行两段式加热保温。首先将mg-3wt%gd镁合金熔体温度加热到790℃,向镁合金熔体中加入经过热处理的mg-zr中间合金,待mg-zr中间合金全部熔化保温6min,将镁合金熔体温度缓慢降低到690℃并保温6min,浇铸。经过金相晶粒尺寸统计分析,使用预处理后的mg-zr中间合金细化的mg-3wt%gd-0.5wt%zr合金平均晶粒尺寸为47μm。
50.第二组熔炼实验与第一组实验的熔炼、浇注条件均一致,仅将第一组实验中使用的预处理后的mg-zr中间合金改为商用的mg-30wt%zr中间合金,经金相晶粒尺寸统计分析,第二组熔炼实验制备的mg-3wt%y-0.5wt%zr合金平均晶粒尺寸为86μm。
51.上述两组实验结果对比表明,本发明的方法能有效提高mg-zr中间合金对镁合金的晶粒细化效果。
52.实施例3
53.以熔炼mg-3wt%nd-0.5wt%zr镁合金为例,分两组进行实验。
54.一.mg-zr中间合金的预处理
55.从商用的mg-30wt%zr中间合金铸锭中切取一块板材,未预处理前的mg-zr中间合金中zr平均粒径约为13μm,溶质zr含量为0.19wt%。将mg-zr中间合金置于熔炼炉中进行加热,加热温度为670℃,待mg-zr中间合金熔化后,对熔体进行外加磁场处理8min,再将mg-zr中间合金浇铸到水冷的铜质模具中进行凝固。将重熔得到的mg-zr中间合金进行固溶加时效处理,固溶温度为640℃,固溶时间为8h,固溶热处理时,mg-zr中间合金被包埋在mgo粉末中。时效处理温度为130℃,时效处理时间为10h。预处理后的mg-zr中间合金中zr平均粒径约为0.9μm,溶质zr含量为2.15wt%。
56.二.熔炼浇注mg-3wt%nd-0.5wt%zr镁合金
57.第一组熔炼实验按照目标成分为mg-3wt%nd-0.5wt%zr预先按比例配置纯镁锭,mg-25wt%nd、以及前述步骤预处理后的mg-zr中间合金锭,并对mg-3wt%nd镁合金熔体进行两段式加热保温。首先将mg-3wt%nd镁合金熔体温度加热到800℃,向镁合金熔体中加入经过热处理的mg-zr中间合金,待mg-zr中间合金全部熔化保温8min,将镁合金熔体温度缓慢降低到700℃并保温8min,浇铸。经过金相晶粒尺寸统计分析,使用预处理后的mg-zr中间合金细化的mg-3wt%gd-0.5wt%zr合金平均晶粒尺寸为46μm。
58.第二组熔炼实验与第一组实验的熔炼、浇注条件均一致,仅将第一组实验中使用的预处理后的mg-zr中间合金改为商用的mg-30wt%zr中间合金,经金相晶粒尺寸统计分析,第二组熔炼实验制备的mg-3wt%y-0.5wt%zr合金平均晶粒尺寸为94μm。
59.上述两组实验结果对比表明,本发明的方法能有效提高mg-zr中间合金对镁合金的晶粒细化效果。
60.实施例4
61.以熔炼mg-6wt%zn-0.5wt%zr镁合金为例,分两组进行实验。
62.一.mg-zr中间合金的预处理
63.从商用的mg-30wt%zr中间合金铸锭中切取一块板材,未预处理前的mg-zr中间合金中zr平均粒径约为13μm,溶质zr含量为0.24wt%。将mg-zr中间合金置于熔炼炉中进行加热,加热温度为680℃,待mg-zr中间合金熔化后,对熔体进行外加电场处理10min,再将mg-zr中间合金浇铸到水冷的铜质模具中进行凝固。将重熔得到的mg-zr中间合金进行固溶加时效处理,固溶温度为650℃,固溶时间为10h,固溶热处理时,mg-zr中间合金被包埋在mgo粉末中。时效处理温度为150℃,时效处理时间为15h。预处理后的mg-zr中间合金中zr平均粒径约为0.9μm,溶质zr含量为2.34wt%。
64.二.熔炼浇注mg-6wt%zn-0.5wt%zr镁合金
65.第一组熔炼实验按照目标成分为mg-6wt%zn-0.5wt%zr预先按比例配置纯镁锭,纯zn锭、以及前述步骤预处理后的mg-zr中间合金锭,并对mg-6wt%zn镁合金熔体进行两段式加热保温。首先将mg-6wt%zn镁合金熔体温度加热到820℃,向镁合金熔体中加入经过热处理的mg-zr中间合金,待mg-zr中间合金全部熔化保温10min,将镁合金熔体温度缓慢降低到720℃并保温10min,浇铸。经过金相晶粒尺寸统计分析,使用预处理后的mg-zr中间合金细化的mg-6wt%zn-0.5wt%zr合金平均晶粒尺寸为49μm。
66.第二组熔炼实验与第一组实验的熔炼、浇注条件均一致,仅将第一组实验中使用的预处理后的mg-zr中间合金改为商用的mg-30wt%zr中间合金,经金相晶粒尺寸统计分析,第二组熔炼实验制备的mg-6wt%zn-0.5wt%zr合金平均晶粒尺寸为97μm。
67.上述两组实验结果对比表明,本发明的方法能有效提高mg-zr中间合金对镁合金的晶粒细化效果。
68.实施例5
69.以熔炼mg-9wt%gd-3wt%y-0.5wt%zr镁合金为例,分两组进行实验。
70.一.mg-zr中间合金的预处理
71.从商用的mg-30wt%zr中间合金铸锭中切取一块板材,未预处理前的mg-zr中间合金中zr平均粒径约为13μm,溶质zr含量为0.21wt%。将mg-zr中间合金置于熔炼炉中进行加热,加热温度为680℃,待mg-zr中间合金熔化后,对熔体进行外加电场处理10min,再将mg-zr中间合金浇铸到水冷的铜质模具中进行凝固。将重熔得到的mg-zr中间合金进行固溶加时效处理,固溶温度为650℃,固溶时间为10h,固溶热处理时,mg-zr中间合金被包埋在mgo粉末中。时效处理温度为150℃,时效处理时间为15h。预处理后的mg-zr中间合金中zr平均粒径约为1.1μm,溶质zr含量为2.55wt%。
72.二.熔炼浇注mg-9wt%gd-3wt%y-0.5wt%zr镁合金
73.第一组熔炼实验按照目标成分为mg-9wt%gd-3wt%y-0.5wt%zr预先按比例配置纯镁锭,mg-25wt%gd、mg-25wt%y、以及前述步骤预处理后的mg-zr中间合金锭,并对mg-9wt%gd-3wt%y镁合金熔体进行两段式加热保温。首先将mg-9wt%gd-3wt%y镁合金熔体温度加热到820℃,向镁合金熔体中加入经过热处理的mg-zr中间合金,待mg-zr中间合金全部熔化保温10min,将镁合金熔体温度缓慢降低到720℃并保温10min,浇铸。金相显微组织图如图1,经过金相晶粒尺寸统计分析,使用预处理后的mg-zr中间合金细化的mg-9wt%gd-3wt%y-0.5wt%zr合金平均晶粒尺寸为41μm。
0.5wt%zr合金平均晶粒尺寸为69μm。
86.对比例6
87.本对比例与实施例1的mg-zr中间合金的预处理方法基本相同,采用的未预处理前的mg-zr中间合金中zr平均粒径与溶质zr含量与实施例1相同,在熔炼细化过程中采用的方法相同,不同之处仅在于:对重熔后的mg-zr中间合金进行固溶处理时,固溶温度为600℃。由于固溶处理温度较低,固溶效果不佳。预处理后mg-zr中间合金中zr平均粒径约为3.6μm,溶质zr含量为1.15wt%。经过熔炼细化处理后的mg-3wt%y-0.5wt%zr合金平均晶粒尺寸为72μm。
88.对比例7
89.本对比例与实施例1的mg-zr中间合金的预处理方法基本相同,采用的未预处理前的mg-zr中间合金中zr平均粒径与溶质zr含量与实施例1相同,在熔炼细化过程中采用的方法相同,不同之处仅在于:对重熔后的mg-zr中间合金进行时效处理时,时效温度为160℃。由于时效处理温度较高,沉淀zr发生粗化。预处理后mg-zr中间合金中zr平均粒径约为1.9μm,溶质zr含量为1.94wt%。经过熔炼细化处理后的mg-3wt%y-0.5wt%zr合金平均晶粒尺寸为61μm。
90.对比例8
91.本对比例与实施例1的mg-zr中间合金的预处理方法相同,采用的未预处理前的mg-zr中间合金中zr平均粒径与溶质zr含量与实施例1相同,在熔炼细化过程中采用的方法基本相同,不同之处仅在于:用预处理后的mg-zr中间合金对镁合金进行细化处理时,未对其进行两段式加热保温,仅在780℃保温10min后将熔体温度降低到680℃进行浇铸。这样一来,在高温下溶解到mg液中的溶质zr并不能重新析出形成细小弥散的zr粒,经过熔炼细化处理后的mg-3wt%y-0.5wt%zr合金平均晶粒尺寸为63μm。
92.对比例9
93.本对比例与实施例1的mg-zr中间合金的预处理方法相同,采用的未预处理前的mg-zr中间合金中zr平均粒径与溶质zr含量与实施例1相同,在熔炼细化过程中采用的方法基本相同,不同之处仅在于:用预处理后的mg-zr中间合金对镁合金进行细化处理时,未对其进行两段式加热保温,仅在680℃保温10min后直接进行浇铸。这样一来,mg-zr中间合金中的zr粒很难在高温下分散、溶解,经过熔炼细化处理后的mg-3wt%y-0.5wt%zr合金平均晶粒尺寸为65μm。
94.以上对本发明的具体实施例进行了描述。需要理解的是,本发明并不局限于上述特定实施方式,本领域技术人员可以在权利要求的范围内做出各种变化或修改,这并不影响本发明的实质内容。在不冲突的情况下,本技术的实施例和实施例中的特征可以任意相互组合。