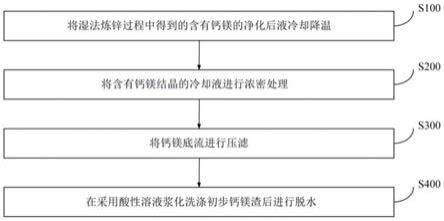
1.本发明涉及湿法炼锌技术领域,具体涉及一种处理湿法炼锌过程中钙镁的方法。
背景技术:2.在湿法炼锌系统中,钙镁元素主要以硫酸盐形式广泛存在于溶液中,不能采用一般净化方法从溶液中去除。钙镁盐在溶液中的大量存在,给湿法炼锌带来了诸如增大溶液密度与粘度使矿浆液固分离和过滤困难,结晶析出使设备损坏与管道堵塞,增大电解液电阻降低电流效率等不良影响。目前,湿法炼锌常用的除钙镁方法主要为稀酸洗涤法、冷却法等,该类方法存在锌回收困难、工艺较复杂等问题。
3.因此,现有湿法炼锌过程中除钙镁的方法有待改善。
技术实现要素:4.本发明旨在至少在一定程度上解决相关技术中的技术问题之一。为此,本发明的一个目的在于提出一种处理湿法炼锌过程中钙镁的方法,采用该方法处理湿法炼锌过程中的钙镁离子,可以较为有效地解决湿法炼锌系统钙镁浓度高的问题以及降低锌金属的损失率。
5.本发明提出了一种处理湿法炼锌过程中钙镁的方法。根据本发明的实施例,所述处理湿法炼锌过程中钙镁的方法包括:
6.(1)将湿法炼锌过程中得到的含有钙镁的净化后液冷却降温,以便得到含有钙镁结晶的冷却液;
7.(2)将所述含有钙镁结晶的冷却液进行浓密处理,以便得到上清液和钙镁底流;
8.(3)将所述钙镁底流进行压滤,以便得到初步钙镁渣;
9.(4)在采用酸性溶液浆化洗涤所述初步钙镁渣后进行脱水,以便得到含锌溶液和钙镁渣。
10.根据本发明实施例的处理湿法炼锌过程中钙镁的方法,通过将湿法炼锌过程中得到的含有钙镁的净化后液冷却降温以析出钙镁结晶,以便得到含有钙镁结晶的冷却液,再将所述含有钙镁结晶的冷却液进行浓密处理,以便得到上清液和钙镁底流,然后将所述钙镁底流进行压滤,产出初步钙镁渣,从而可以较为有效地解决湿法炼锌系统钙镁浓度高的问题,避免给湿法炼锌带来诸如增大溶液密度与粘度使矿浆液固分离和过滤困难,结晶析出使设备损坏与管道堵塞,增大电解液电阻以及降低电流效率等不良影响。最后在采用酸性溶液浆化洗涤所述初步钙镁渣后进行脱水,以便得到含锌溶液和钙镁渣,从而可以较为有效地降低钙镁渣的含锌量,使得锌金属损失率较小,有利于对锌金属进行回收。
11.另外,根据本发明上述实施例的处理湿法炼锌过程中钙镁的方法还可以具有如下附加的技术特征:
12.在本发明的一些实施例中,在步骤(1)中,所述净化后液为所述湿法炼锌过程中性浸出上清液净化后的溶液。
13.在本发明的一些实施例中,在步骤(1)中,将所述湿法炼锌过程中得到的含有钙镁的净化后液冷却降温至25~45摄氏度。由此,可以析出钙镁结晶,以便得到含有钙镁结晶的冷却液。
14.在本发明的一些实施例中,在步骤(2)中,所述浓密处理的时间为6~15小时。由此,可以对钙镁结晶的冷却液进行固液分离,以便得到上清液和钙镁底流。
15.在本发明的一些实施例中,在步骤(2)中,所述钙镁底流的浓度为1.3~1.6g/cm3。由此,可以有效地解决湿法炼锌系统钙镁浓度高的问题。
16.在本发明的一些实施例中,在步骤(3)中,所述压滤过程中采用滤布透气率为5~20l/m2·
s。由此,可以保证一定的压滤效果和压滤效率。
17.在本发明的一些实施例中,在步骤(3)中,所述初步钙镁渣含液率不高于30wt%。由此,可以降低钙镁渣的含锌量,降低锌金属损失率。
18.在本发明的一些实施例中,在步骤(4)中,所述浆化洗涤过程中的液固比为1.5~3l/kg。由此,可以对初步钙镁渣进行充分浆化洗涤,从而降低钙镁渣的含锌量,降低锌金属损失率。
19.在本发明的一些实施例中,在步骤(4)中,所述浆化洗涤过程的搅拌时间不低于15分钟。由此,可以对初步钙镁渣进行充分浆化洗涤,从而降低钙镁渣的含锌量,降低锌金属损失率。
20.在本发明的一些实施例中,在步骤(4)中,所述酸性溶液的酸度为5~30g/l,含锌量不高于1g/l。由此,一方面可以对初步钙镁渣进行充分浆化洗涤,从而降低钙镁渣的含锌量,降低锌金属损失率;另一方面可以避免对设备造成严重腐蚀。
21.在本发明的一些实施例中,其特征在于,在步骤(4)中,所述脱水过程采用的离心机滤网目数为100~300目。由此,可以对浆化后钙镁渣矿浆进行脱水,从而得到含锌溶液和钙镁渣。
22.在本发明的一些实施例中,在步骤(4)中,所述离心机的转速为700~1000r/min,所述脱水时间为5~10min。由此,可以对浆化后钙镁渣矿浆进行固液分离,从而得到含锌溶液和钙镁渣。
23.在本发明的一些实施例中,在步骤(4)中,所述钙镁渣的含液率不高于15wt%。由此,降低了钙镁渣含锌量,降低了锌金属损失率。
24.在本发明的一些实施例中,进一步包括:(5)采用洗水对所述钙镁渣洗涤后脱水,以便得到脱水钙镁渣和分离后液。由此,可以进一步降低钙镁渣含锌量,降低锌金属损失率,产出外排钙镁渣。
25.在本发明的一些实施例中,在步骤(5)中,所述洗水与所述钙镁渣的液固比为0.1~1l/kg。由此,可以对钙镁渣进行充分洗涤,从而进一步降低钙镁渣含锌量,降低锌金属损失率,产出外排钙镁渣。
26.在本发明的一些实施例中,在步骤(5)中,所述洗涤和脱水在离心机中进行,并且所述洗涤过程中,所述离心机的转速为300~600r/min,所述洗涤时间为2~8min。由此,保证了一定的洗涤效率和洗涤效果。
27.在本发明的一些实施例中,在步骤(5)中,所述脱水过程中,所述离心机的转速为700~1000r/min,所述脱水时间为5~10min。由此,有利于将洗水与钙镁渣进行固液分离。
28.在本发明的一些实施例中,在步骤(5)中,所述脱水钙镁渣含水率不高于12wt%,含锌率不高于5wt%。
29.本发明的附加方面和优点将在下面的描述中部分给出,部分将从下面的描述中变得明显,或通过本发明的实践了解到。
附图说明
30.本发明的上述和/或附加的方面和优点从结合下面附图对实施例的描述中将变得明显和容易理解,其中:
31.图1是根据本发明一个实施例的处理湿法炼锌过程中钙镁的方法流程示意图;
32.图2是根据本发明再一个实施例的处理湿法炼锌过程中钙镁的方法流程示意图;
33.图3是根据本发明一个实施例的处理湿法炼锌过程中钙镁的工艺流程简图。
具体实施方式
34.下面详细描述本发明的实施例,所述实施例的示例在附图中示出。下面通过参考附图描述的实施例是示例性的,旨在用于解释本发明,而不能理解为对本发明的限制。
35.本发明提出了一种处理湿法炼锌过程中钙镁的方法。根据本发明的实施例,参考图1-3,该处理湿法炼锌过程中钙镁的方法包括:
36.s100:将湿法炼锌过程中得到的含有钙镁的净化后液冷却降温
37.该步骤中,湿法炼锌过程中得到的含有钙镁的净化后液具体来源于湿法炼锌过程中性浸出上清液净化后的溶液,钙的存在形式为ca
2+
,镁的存在形式为mg
2+
,锌的存在形式为zn
2+
,钙离子浓度为200~400mg/l,镁离子浓度为10~15g/l,锌离子浓度为130~180g/l,将该湿法炼锌过程中得到的含有钙镁的净化后液供给至冷却塔中进行冷却降温,caso4、mgso4的溶解度随着温度的降低而降低,然后结晶析出,得到含有钙镁结晶的冷却液。需要说明的是,本领域技术人员可以根据实际需要对冷却塔的类型进行选择,只要能实现上述功能即可。进一步地,上述湿法炼锌过程中得到的含有钙镁的净化后液冷却降温至25~45℃,优选为30~40℃,更优选为35~40℃。发明人发现,若温度太高,可能会造成仍有一定量的钙离子和镁离子留在溶液中无法被脱除,导致其在湿法炼锌系统的后续工序中,当局部温度下降时,可能会以结晶的方式的析出,并且会降低锌电积电流效率,给正常生产带来管道堵塞、能耗增加以及影响产品质量等问题;而若温度太低,则冷却设备需要承担更高的工作负荷以及更长的冷却时间。由此,采用本技术的温度范围可以在保证钙镁充分结晶析出的同时避免承担较大的降温负荷。
38.s200:将含有钙镁结晶的冷却液进行浓密处理
39.该步骤中,将含有钙镁结晶的冷却液供给至浓密机进行浓密处理,以便得到上清液和钙镁底流。在该过程中,主要是借助于钙镁结晶的自身重力进行沉降,从而使含有钙镁结晶的冷却液分为上清液和钙镁底流两个部分。需要说明的是,本领域技术人员可以根据实际需要对浓密机的具体类型进行选择,只要能实现上述功能即可。进一步地,上述浓密处理的时间为6~15小时,优选为7~12小时,更优选为8~11小时。发明人发现,若浓密处理的时间过短,可能会导致浓密处理不充分,使得到的上清液中仍悬浮有一定量的钙镁结晶,这部分钙镁结晶并没有被排出湿法炼锌系统,导致其在湿法炼锌系统的后续工序中,当局部
温度下降时,可能会以结晶的方式的析出,并且会降低锌电积电流效率,给正常生产带来管道堵塞、能耗增加以及影响产品质量等问题;而若浓密处理时间过长,则冷却液中悬浮的钙镁结晶早已沉降至钙镁底流中,从而造成时间上的浪费,降低了生产效率。同时上述钙镁底流的浓度为1.3~1.6g/cm3。由此,采用本技术的浓密处理时间可以使钙镁结晶充分沉降至钙镁底流,且可以保证一定的生产效率。
40.s300:将钙镁底流进行压滤
41.该步骤中,通过采用压滤机对步骤s200中得到的钙镁底流进行压滤,钙镁底流经过滤布时,固体停留在滤布上,而液体部分则会渗透过滤布,成为不含固体的清液,从而可以将钙镁底流中的固体提取出来,实现固液分离,以便得到初步钙镁渣。需要说明的是,本领域技术人员可以根据实际需要对压滤机的具体类型进行选择,只要能够实现上述功能即可。进一步地,上述压滤过程中采用滤布透气率为5~20l/m2·
s,优选为7~18l/m2·
s,更优选为10~15l/m2·
s。发明人发现,若滤布透气率过高,则滤布的孔径可能大于钙镁结晶的粒径,钙镁结晶会和液体一起渗透过滤布,从而无法对钙镁底流实现固液分离。而若滤布透气率过低,会造成所需压滤时间较长,压滤效率较低。由此,采用本技术的滤布透气率可以实现对钙镁底流进行高效固液分离。同时,上述初步钙镁渣含液率不高于30wt%。发明人发现,若初步钙镁渣含液率过高,则会增加锌金属损失率。
42.s400:在采用酸性溶液浆化洗涤初步钙镁渣后进行脱水
43.该步骤中,在浆化搅拌槽内采用酸性溶液对初步钙镁渣进行浆化洗涤,初步钙镁渣中的硫酸锌可以溶解于该酸性溶液中,而钙镁渣中的钙以caso4·
2h2o形式存在而几乎不发生溶解,镁以mgso4形式附着在caso4·
2h2o上也几乎不发生溶解,因而会继续以固体的形式留在初步钙镁渣中,浆化洗涤结束后利用离心机进行脱水,以便得到含锌溶液和钙镁渣,从而将初步钙镁渣中的锌元素与钙镁元素进行分离。需要说明的是,本领域技术人员可以根据实际需要对浆化搅拌槽和离心机的具体类型进行选择,只要能够实现上述功能即可。另外,本领域技术人员可以根据实际需要对酸性溶液的具体类型进行选择,只要能实现对初步钙镁渣的浆化洗涤即可,例如,酸性溶液为沉锌浸液。
44.进一步地,上述浆化洗涤过程中的液固比为1.5~3l/kg,优选为1.5~2.5l/kg,更优选为1.5~2l/kg。发明人发现,若液固比过低,则无法对初步钙镁渣进行充分浆化洗涤,从而导致得到的钙镁渣中仍含有一定量的硫酸锌未被溶解,增加了锌金属损失率;而若液固比过高,则会增加后续脱水过程的负荷,从而降低了生产效率。由此,采用本技术的液固比可以使得锌金属损失率较小,且可以避免增加后续脱水过程的负荷。同时,上述浆化洗涤过程的搅拌时间不低于15分钟。发明人发现,若浆化洗涤过程的搅拌时间过短,同样会导致得到的钙镁渣中仍含有一定量的硫酸锌未被溶解,从而增加了锌金属损失率。由此,采用本技术的搅拌时间,可以使得锌金属损失率较小,有利于对锌金属进行回收。并且上述酸性溶液的酸度为5~30g/l,优选为10~25g/l,更优选为15~20g/l;含锌量不高于1g/l,优选为不高于0.8g/l,更优选为不高于0.5g/l。发明人发现,若酸度太低,则zn
2+
会水解沉淀;若酸度太高,则附着在caso4·
2h2o上的mgso4会发生溶解。同时若含锌量太高,会抑制初步钙镁渣中硫酸锌的溶解,导致湿法炼锌过程中锌的回收率降低。由此,采用本技术的酸性溶液,可以较为有效地解决湿法炼锌系统钙镁浓度高的问题以及降低锌金属的损失率。
45.进一步地,上述脱水过程采用的离心机滤网目数为100~300目,优选为150~300
目,更优选为200~250目。发明人发现,若离心机滤网的目数过低,则滤网网孔的孔径可能会大于钙镁渣的粒径,因而无法对进行浆化洗涤后的初步钙镁渣进行固液分离;若离心机滤网的目数过高,则钙镁渣可能堵塞滤网网孔,因而无法对进行浆化洗涤后的初步钙镁渣进行固液分离。由此,采用本技术的离心机滤网目数可以对进行浆化洗涤后的初步钙镁渣进行高效固液分离,从而可以较为有效地解决湿法炼锌系统钙镁浓度高的问题以及降低锌金属的损失率。上述离心机的转速为700~1000r/min,优选为750~950r/min,更优选为800~900r/min;脱水时间为5~10min,优选为6~9min。更优选为7~8min。发明人发现,若离心机的转速过低,则无法对浆化洗涤后的初步钙镁渣进行充分的固液分离,从而导致得到的钙镁渣中含液率较高,增加了锌金属损失率;而若离心机的转速过高,则会导致一部分浆化洗涤后的初步钙镁渣直接溢流而出,无法进行充分的固液分离。若脱水时间过短,同样也无法对浆化洗涤后的初步钙镁渣进行充分的固液分离,从而导致得到的钙镁渣中含液率较高,增加了锌金属损失率;而若脱水时间过长,会降低生产效率。另外,所述钙镁渣的含液率不高于15wt%。发明人发现,若钙镁渣的含液率过高,则会增加锌金属的损失率。由此,采用本技术的脱水条件可以对浆化洗涤后的初步钙镁渣进行充分且高效的固液分离,从而可以较为有效地解决湿法炼锌系统钙镁浓度高的问题以及降低锌金属的损失率。
46.进一步地,参考图2,上述处理湿法炼锌过程中钙镁的方法包括步骤s500:采用洗水对钙镁渣洗涤后脱水
47.该步骤中,通过采用洗水对钙镁渣进行洗涤,可以使钙镁渣上附着的硫酸锌进一步溶解到洗水中,洗涤结束后进行脱水,以便得到脱水钙镁渣和分离后液,从而使原本钙镁渣上附着的硫酸锌大部分进入分离后液而与脱水钙镁渣实现分离。进一步地,上述洗水与钙镁渣的液固比为0.1~1l/kg,优选为0.3~0.8l/kg,更优选为0.3~0.5l/kg。发明人发现,若液固比过小,无法对钙镁渣上附着的硫酸锌进行充分溶解,从而导致洗涤不彻底;而若液固比过大,则会增加后续脱水过程的负荷和对洗水的浪费。由此,采用本技术的液固比可以对钙镁渣进行高效洗涤,有效降低钙镁渣含锌量。另外,上述洗涤和脱水在离心机中进行,并且洗涤过程中,离心机的转速为300~600r/min,优选为350~550r/min,更优选为400~500r/min;洗涤时间为2~8min,优选为3~7min,更优选为4~6min。发明人发现,若离心机的转速过低,则洗水不能与钙镁渣充分接触,不能对钙镁渣进行充分洗涤;而若离心机的转速过高,则洗水与钙镁渣接触时间过短,不能对钙镁渣进行充分洗涤。若洗涤时间过短,则洗水不能与钙镁渣充分接触,同样也不能对钙镁渣进行充分洗涤;而若洗涤时间过长,则会降低生产效率。由此,采用本技术的离心机转速和洗涤时间可以对钙镁渣进行充分洗涤,有效降低钙镁渣含锌量。需要说明的是,离心机的类型同于上文描述,此处不再赘述。同时,上述脱水过程中,离心机的转速为700~1000r/min,优选为750~950r/min,更优选为800~900r/min;脱水时间为5~10min,优选为7~8min。发明人发现,若离心机的转速过低,会导致脱水效果不理想,从而造成脱水钙镁渣中含水率较高;而若离心机的转速过高,会降低系统的安全性。若脱水时间过短,同样也会导致脱水效果不理想,从而造成脱水钙镁渣中含水率较高;而若脱水时间过长,会降低生产效率。由此,采用本技术的离心机转速和脱水时间可以有效降低钙镁渣中的含水率。另外,所述脱水钙镁渣含水率不高于12wt%,含锌率不高于5wt%。
48.发明人发现,通过将湿法炼锌过程中得到的含有钙镁的净化后液冷却降温以析出
钙镁结晶,以便得到含有钙镁结晶的冷却液,再将所述含有钙镁结晶的冷却液进行浓密处理,以便得到上清液和钙镁底流,然后将所述钙镁底流进行压滤,产出初步钙镁渣,从而可以较为有效地解决湿法炼锌系统钙镁浓度高的问题,避免给湿法炼锌带来诸如增大溶液密度与粘度使矿浆液固分离和过滤困难,结晶析出使设备损坏与管道堵塞,增大电解液电阻以及降低电流效率等不良影响。最后在采用酸性溶液浆化洗涤所述初步钙镁渣后进行脱水,以便得到含锌溶液和钙镁渣,从而可以较为有效地降低钙镁渣的含锌量,使得锌金属损失量较小,有利于对锌金属进行回收。
49.下面详细描述本发明的实施例,需要说明的是下面描述的实施例是示例性的,仅用于解释本发明,而不能理解为对本发明的限制。另外,如果没有明确说明,在下面的实施例中所采用的所有试剂均为市场上可以购得的,或者可以按照本文或已知的方法合成的,对于没有列出的反应条件,也均为本领域技术人员容易获得的。
50.实施例1
51.对含钙离子300mg/l、镁离子12g/l、锌离子含量为150g/l的净化后液经冷却塔冷却降温至40℃,进入浓密机浓密8h,产出密度为1.6g/cm3的钙镁底流;使用滤布透气率为10l/m2·
s的压滤机对钙镁底流进行液固分离作业,产出含液率为30wt%的初步钙镁渣,初步钙镁渣卸渣后进入浆化搅拌槽,在浆化搅拌槽内用酸度为10g/l,含锌量为0.5g/l的沉锌滤液浆化洗涤初步钙镁渣,浆化洗涤的液固比为2l/kg,浆化搅拌时间为20min;使用离心机对浆化洗涤后的初步钙镁渣矿浆进行脱液作业,离心机滤网为250目,离心机脱液转速为700r/min,脱液时间为10min,产出含液率为10wt%的钙镁渣;脱液完成后,泵入洗水在离心机高速旋转下充分洗涤钙镁渣并脱水,洗水与钙镁渣的液固比为0.3l/kg,离心机洗涤转速为300r/min,洗涤时间为5min;洗涤完成后继续进行脱水,离心机脱水转速为700r/min,脱水时间为5min;最终外排钙镁渣的含水率为10wt%,含锌率为1.0wt%,净化后液钙离子浓度从300mg/l降至150mg/l,镁离子浓度从12g/l降至11.5g/l。
52.实施例2
53.对含钙离子250mg/l、镁离子12g/l、锌离子含量为160g/l的净化后液经冷却塔冷却降温至36℃,进入浓密机浓密10h,产出密度为1.6g/cm3的钙镁底流;使用滤布透气率为15l/m2·
s的压滤机对钙镁底流进行液固分离作业,产出含液率为30wt%的初步钙镁渣,初步钙镁渣卸渣后进入浆化搅拌槽,在浆化搅拌槽内用酸度为30g/l,含锌量为0.5g/l的沉锌滤液浆化洗涤钙镁渣,浆化洗涤的液固比为2l/kg,浆化搅拌时间为20min;使用专用离心机对浆化洗涤后的初步钙镁渣矿浆进行脱液作业,离心机滤网为200目,离心机脱液转速为800r/min,脱液时间为10min,产出含液率为9.5wt%的钙镁渣;脱液完成后,泵入洗水在离心机高速旋转下充分洗涤钙镁渣并脱水,洗水与钙镁渣的液固比为0.5l/kg,离心机洗涤转速为300r/min,洗涤时间为5min;洗涤完成后继续进行脱水,离心机脱水转速为700r/min,脱水时间为5min;最终外排钙镁渣的含水率为9.3wt%,含锌率为0.95wt%,净化后液钙离子浓度从250mg/l降至150mg/l,镁离子浓度从12g/l降至11.5g/l。
54.实施例3
55.对含钙离子200mg/l、镁离子11g/l、锌离子含量为165g/l的净化后液经冷却塔冷却降温至38℃,进入浓密机浓密9h,产出密度为1.6g/cm3的钙镁底流;使用滤布透气率为10l/m2·
s的压滤机对钙镁底流进行液固分离作业,产出含液率为30wt%的初步钙镁渣,初
步钙镁渣卸渣后进入浆化搅拌槽,在浆化搅拌槽内用酸度为20g/l,含锌量为0.5g/l的沉锌滤液浆化洗涤初步钙镁渣,浆化洗涤的液固比为3l/kg,浆化搅拌时间为20min;使用专用离心机对浆化后的初步钙镁渣矿浆进行脱液作业,离心机滤网为200目,离心机脱液转速为800r/min,脱液时间为10min,产出含液率为8.1wt%的钙镁渣;脱液完成后,泵入洗水在离心机高速旋转下充分洗涤钙镁渣并脱水,洗水与钙镁渣的液固比为0.5l/kg,离心机洗涤转速为300r/min,洗涤时间为5min;洗涤完成后继续进行脱水,离心机脱水转速为700r/min,脱水时间为5min;最终外排钙镁渣的含水率为9.0wt%,含锌率为1.0wt%,净化后液钙离子浓度从200mg/l降至150mg/l,镁离子浓度从11g/l降至10.5g/l。
56.在本说明书的描述中,参考术语“一个实施例”、“一些实施例”、“示例”、“具体示例”、或“一些示例”等的描述意指结合该实施例或示例描述的具体特征、结构、材料或者特点包含于本发明的至少一个实施例或示例中。在本说明书中,对上述术语的示意性表述不必须针对的是相同的实施例或示例。而且,描述的具体特征、结构、材料或者特点可以在任一个或多个实施例或示例中以合适的方式结合。此外,在不相互矛盾的情况下,本领域的技术人员可以将本说明书中描述的不同实施例或示例以及不同实施例或示例的特征进行结合和组合。
57.尽管上面已经示出和描述了本发明的实施例,可以理解的是,上述实施例是示例性的,不能理解为对本发明的限制,本领域的普通技术人员在本发明的范围内可以对上述实施例进行变化、修改、替换和变型。