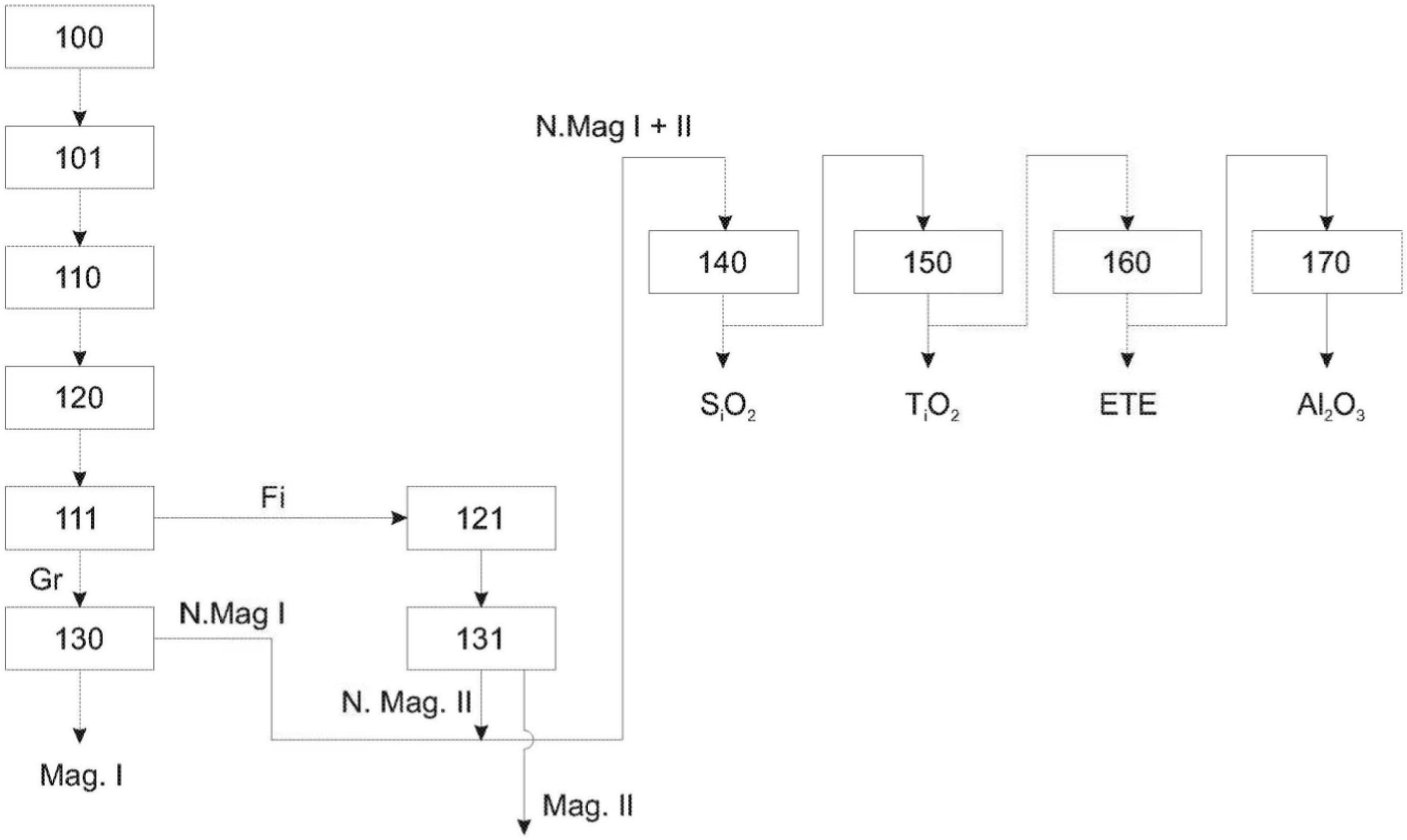
从铝土矿残渣中回收材料的方法、用于加热采矿产品的微波反应器和加热采矿产品的方法
1.本发明涉及一种技术上和经济上可行的通过以其整体利用所述残渣而回收采矿残渣,特别是铝土矿残渣的相关金属和非金属的方法。这样的工艺路线使用微波能量、辅助浸出和步骤的逻辑排序,以便能够在技术上和经济上可行地从从铝土矿残渣,特别是衍生自拜耳法的铝土矿残渣中除去组分。使用微波频谱内的电磁辐射使得这些材料和残渣的处理和加工中的效率改进。本发明还提供一种微波反应器,其构造和操作对用于回收采矿残渣,且更特别是获自拜耳法的铝土矿残渣特别高效。
2.此外,本发明涉及一种用于加热采矿产品的微波反应器,其特别适用于加热采矿产品以回收感兴趣的材料,适用于进行上述铝土矿残渣的衍生材料的回收工艺。
3.背景
4.在采矿过程衍生产品的技术领域中,采矿工业主要用于从铁矿石(铝土矿)中提取铝的著名方法之一是拜耳法。
5.1888年开发的拜耳法在世界范围内最常用于氧化铝生产。这种方法包括通过使用氢氧化钠作为浸出剂在温度和压力下促进铝土矿的溶出(digestion)。溶出阶段使得以三水铝石、勃姆石和水铝石形式包含在铝土矿中的铝能够与氢氧化钠反应,由此形成可溶性化合物铝酸钠。因此,通过增稠和倾析二者,可以将这种含有铝酸钠的料液与拜耳法残渣分离。将该料液进给至结晶步骤以回收氧化铝;获自倾析器的材料是拜耳法的尾矿,其沉积在处置池中。
6.来自拜耳法的这种残渣(被称为铝土矿残渣或赤泥)主要由赤铁矿和针铁矿形式的铁内容物、三水铝石和拜耳方钠石形式的铝、锐钛矿(anatasium)形式的钛和其它微量元素如钪、铀、钍和锆等组成。这种来自拜耳法的尾矿在溶出步骤中不可溶,并且以拜耳方钠石的形式由高岭石的沉淀产生。这种方钠石含有铝以及铁、钠和氢氧化物。这种尾矿还含有一系列对工业具有重要意义的金属,例如锆、钪和钛。
7.尽管如此,由拜耳法氧化铝加工产生的铝土矿残渣是高度污染的:由于其高ph,其是反应性和腐蚀性的;含有重金属,特别是铀和钍;其细且轻,因此需要持续监测;irrigated(灌溉)和紧实;要求土壤防水以避免污染。因此,这样的铝土矿残渣意味着高维护成本,对环境非常有害,并可能引起环境灾难,如匈牙利的ajka工厂的灾难。
8.鉴于上述情况,现有技术旨在提供处理产品和残渣的解决方案以进一步获得感兴趣的材料,包括铝土矿残渣加工。但是,如下面解释,目前已知的此类方法在清除残渣方面缺乏效率,仅限于可能作为感兴趣的材料提取的物质。
9.从概念上讲,处理采矿产品和回收感兴趣的材料的解决方案主要包括转化或加工产品或残渣以便随后通过其它程序(如磁力分离或浸出)分离,由此使得能够从该产品或残渣中提取感兴趣的元素。
10.产品或残渣的转化传统上使用加热以迫使其中存在的元素的相发生变化并使它们能够分离和使用。这种热来自煤燃烧,通常也用作转化过程中的还原剂。以上评论揭示了对现有技术的第一个担忧:通过由污染源如煤生成的热进行转化,煤的燃烧产生已知对环
境有害的co2。
11.现有技术提出了基于使用微波供能,随后加热产品和残渣的解决方案。因此,理论上可以消除燃烧煤以生成转化所需的热的需要,因为在转化和还原中将仅使用还原剂;在这种情况下,应该有可能接近化学计量地进行操作。
12.下面将评估公开了使用微波加热采矿产品的现有技术文献的实例。
13.美国专利文献us6277168建议使用微波室转化和熔化矿石,以进一步在室底部获得熔融金属。尽管如此,us6277168既没有教导也没有提及回收感兴趣的采矿产品衍生物或残渣的程序,因此表明其应用仅限于直接转化矿石并随后获得熔融金属,而没有任何从处理后的产品中选择特定元素进行分离的可能性。因此,us6277168公开的系统对处理残渣如铝土矿残渣是不可行的,因为这些材料并不适合仅通过转化步骤获得金属合金。
14.另一个实例在于美国专利文献us8034320,其提出使用微波将磁性铁球团(磁铁矿)转化成赤铁矿。值得注意的是,us8034320既没有教导也没有提及通过基础产品的处理/加工可以回收感兴趣的材料;实际上,由于其建议将磁铁矿转化成赤铁矿,文献us8034320排除了对感兴趣的衍生物作出任何可能的选择,因为这增加了通过磁选机进行铁加工的难度。
15.另一个实例是美国专利文献us4311520,其公开了从镍、钴和锰的氧化物和硅酸盐,包括红土镍中回收镍、钴和锰的方法。但是,文献us4311520仅教导了使用微波还原基础产品以便随后提取材料,而非使用烘箱或化学程序,从而尝试减少还原所消耗的能量和资源。尽管如此,考虑到us4311520所涵盖的一些类型的产品中感兴趣的元素的含量非常低(例如,镍矿床的红土区),使用微波进行还原不足以使该程序从经济角度看是有利的。
16.除上述文献外,已经不断做出学术努力以确定处理来自拜耳法的铝土矿残渣的可行解决方案。例如,可以参考s.agrawal和n.dhawan的科学论文“investigation of carbothermicmicrowave reduction followed by acid leaching for recovery of iron and aluminum values from indian red mud”,其在实验上建议通过使用微波碳热还原铝土矿残渣,并且随后浸提这种还原残渣以提取铁和铝。另一些学术出版物公开了类似的内容,因此提出通过微波进行残渣还原的火法冶金工艺,然后进行化学处理以便提取铁和铝,以及在某些情况下的稀土。
17.尽管如此,众所周知,由铝土矿加工产生的残渣(特别是拜耳法残渣)含有除铁和氧化铝之外的几种其它感兴趣的材料。可以提到例如二氧化钛——专利和学术出版物均未涵盖的来自拜耳法的残渣中所含的另一种工业上感兴趣的材料。但是,现有技术无法期望这些其它感兴趣的组分的完全提取方法,以致迄今已知的回收方法表现出低效率并导致非常大量的被认为来自该方法的尾矿。因此,现有技术不能完全解决与铝土矿残渣有关的主要问题之一,即通过铝土矿处理,特别是通过拜耳法生成的大量尾矿。
18.此外,所述学术出版物就其本身的性质而言仅仅是推测,而没有提出任何有效实现从铝土矿残渣中高效提取多种感兴趣的材料的包括逻辑和顺序步骤的具体方法。这在衍生自拜耳法的铝土矿残渣的范围内特别值得注意,其中用于提取单一感兴趣的产品的残渣管理影响残渣中包含的所有其它产品的潜在提取。迄今,在现有技术中不可能找出高效回收铝土矿残渣,包括回收除铁和氧化铝之外的多种感兴趣的材料的合适且完整的方法。
19.另外,现有技术无法提出专门设计用于回收铝土矿残渣的在这一应用中非常高效
的微波反应器设备。尽管现有技术考虑了使用微波处理残渣,但这种微波呈现了一般性的、实验性的或实验室的用途,无法达到这种用于回收铝土矿残渣的所需应用的合适效率。
20.发明目的
21.考虑到现有技术的上述问题,本发明的第一个目的是提供一种从铝土矿残渣,特别是通过拜耳法生产氧化铝所得的化学残渣中高效回收衍生物的方法。
22.本发明的第二个目的是提供一种从铝土矿残渣中回收衍生物的方法,其包括能够从该方法中提取多种元素而不仅仅是提取铁和氧化铝的具体步骤的逻辑顺序。
23.本发明的第三个目的是提供一种从铝土矿残渣中回收衍生物的方法,其利用了通过微波进行残渣的碳热转化的火法冶金法的优点,以及后续化学加工步骤的逻辑和特定顺序,以便从残渣中特别高效提取感兴趣的元素。
24.本发明的第四个目的是提供一种用于加热采矿产品的微波反应器,其特别高效加热和转化采矿残渣,如铝土矿残渣,并可用于实施本文提出的从铝土矿残渣中回收衍生物的方法。
25.发明概述
26.本发明涉及一种从铝土矿残渣中回收衍生物的方法,其包括以下步骤:将铝土矿残渣与还原剂混合以获得残渣混合物;在微波反应器中加热所述残渣混合物以获得还原的铝土矿残渣;磁力分离所述还原的铝土矿残渣以获得磁性材料部分和非磁性材料部分;浸提非磁性材料部分以获得浸出液,然后倾析和过滤所述浸出液以提取二氧化硅;沉淀浸提的料液副产物(liquor byproduct)以获得二氧化钛;蒸发沉淀的料液副产物以获得饱和液和富氧化铝的残留固体;和煅烧获自蒸发的所述富氧化铝的残留固体以获得氧化铝。
27.在本文提出的从铝土矿残渣中回收衍生物的方法的一个可行实施方案中,还原剂包含小于75μm的粒度,所述混合进行10至30分钟直至形成在5至50%的还原剂比率下的铝土矿残渣和还原剂的碳热混合物。
28.在本文提出的从铝土矿残渣中回收衍生物的方法的另一个可行实施方案中,所述方法包括在加热步骤之前,在混合步骤中获得的残渣混合物的造粒步骤。
29.在本文提出的从铝土矿残渣中回收衍生物的方法的另一个可行实施方案中,在加热步骤中,以每吨碳热混合物10kw.h至100kw.h的功率辐照铝土矿残渣2至18分钟的时间段,其中将温度保持在高于转化为磁性相所需的温度的80%的值,持续达到转化为磁性相所需的温度所花费的时间的至少两倍时间。
30.在本文提出的从铝土矿残渣中回收衍生物的方法的另一个可行实施方案中,所述方法包括以下步骤:对来自加热步骤的副产物进行第一次研磨;对第一次研磨中磨碎的铝土矿残渣进行按尺寸分离,以获得残渣的粗粒部分和细粒部分;在残渣的粗粒部分中进行磁力分离以获得粗粒磁性部分和非磁性部分;在残渣的细粒部分中进行第二次研磨;和在磨碎残渣的细粒部分中进行磁力分离,以获得细粒磁性部分和非磁性部分。
31.在本文提出的从铝土矿残渣中回收衍生物的方法的另一个可行实施方案中,第一次按尺寸分离包括将获自第一次研磨的铝土矿残渣送至第一旋风分离器,其将铝土矿残渣分离成尺寸小于和大于#100的材料部分;将由第一旋风分离器分离的小于#100的材料部分送至第二旋风分离器;通过第二旋风分离器将接收的小于#100的材料部分分离成高于和低于#200的部分,低于#200的部分是细粒部分;和将由第一旋风分离器分离的高于#100的部
分与由第二旋风分离器分离的高于#20的部分汇合,以获得粗粒部分。
32.在本文提出的从铝土矿残渣中回收衍生物的方法的另一个可行实施方案中,浸提以1至10克非磁性部分/10毫升浓度为2mol/l至6mol/l的硫酸溶液的固液比进行。
33.在本文提出的从铝土矿残渣中回收衍生物的方法的另一个可行实施方案中,浸提在30至120分钟的时间段和30℃至90℃的温度内,在400至600rpm的搅拌速度下进行。
34.在本文提出的从铝土矿残渣中回收衍生物的方法的另一个可行实施方案中,沉淀包括将tio2晶种添加到料液中;和将含有氢氧化钠的溶液的ph调节至ph1.5至2.5以沉淀二氧化钛。
35.在本文提出的从铝土矿残渣中回收衍生物的方法的另一个可行实施方案中,沉淀在50至200rpm的搅拌速度下、在10℃至90℃的温度下和在30至120分钟的时间段内进行。
36.在本文提出的从铝土矿残渣中回收衍生物的方法的另一个可行实施方案中,蒸发包括将富硫酸铝料液的溶液蒸发至10至16波美度的密度,并加入化学计量量的硫酸钠,并用50%氢氧化钠溶液将该料液的ph调节到6至12之间。
37.在本文提出的从铝土矿残渣中回收衍生物的方法的另一个可行实施方案中,煅烧包括将所述残留固体在400℃至800℃的温度下煅烧30至120分钟的时间段。
38.本发明还涉及一种用于加热采矿产品的微波反应器,其中所述反应器包括由对微波透明的隔热材料构成的外壳;由感受器材料构成的至少一个感受器壁;和由电磁波的反射器材料构成的至少一个反射器板,其中由外壳和至少一个感受器壁限定的区域表征至少一个加热室。
39.在本文提出的用于加热采矿产品的微波反应器的一个可行实施方案中,形成外壳的材料是具有高氧化铝含量的多孔混凝土。
40.在本文提出的用于加热采矿产品的微波反应器的另一个可行实施方案中,外壳由其组成中具有75%至95%的al2o3的多孔混凝土形成。
41.在本文提出的用于加热采矿产品的微波反应器的另一个可行实施方案中,外壳由低密度多孔混凝土构成。
42.在本文提出的用于加热采矿产品的微波反应器的另一个可行实施方案中,外壳由密度为0.7至1.2克/立方厘米的多孔混凝土构成。
43.在本文提出的用于加热采矿产品的微波反应器的另一个可行实施方案中,感受器壁的感受器材料是以下至少一种:碳化硅、矾土水泥(luminite)和金属钛。
44.在本文提出的用于加热采矿产品的微波反应器的另一个可行实施方案中,反射器板包括至少朝向加热室的拉丝(brushed)表面。
45.本发明还涉及一种加热采矿产品的方法,其中这样的方法包括在微波反应器上发出微波的步骤,以使微波穿过由对微波透明的隔热材料构成的微波反应器的外壳,并使所述微波至少到达感受器壁。
46.在本文提出的加热采矿产品的方法的一个可行实施方案中,所述方法包括在反射器板上反射微波的步骤。
47.在本文提出的加热采矿产品的方法的另一个可行实施方案中,在微波反应器上发出微波的步骤涉及将材料加热2至18分钟以达到转化为磁性相所需的温度,并将温度保持在转化为磁性相所需的温度的80%以上,持续达到转化为磁性相所需的温度所花费的时间
的至少两倍时间。
48.附图简述
49.应该基于由附图表示的示例性实施方案更详细地描述本发明。附图显示:
50.图1
–
是在一个优选实施方案中的本发明的微波反应器的顶视图。
51.图2
–
是在一个优选实施方案中的从铝土矿残渣中回收衍生物的方法的流程图;
52.图2a
–
是在回收方法的一个优选实施方案中从铝土矿残渣中分离细粒和粗粒部分的方法的流程图;
53.图3
–
是显示在本发明的铝土矿残渣的回收方法的过程中,铝土矿残渣中所含的多种铁相的转化率随时间的曲线图;
54.图4
–
是显示在本发明的铝土矿残渣的回收方法的过程中,方钠石向霞石的转化率随时间的曲线图;
55.图5
–
是在一个优选实施方案中的从矿石细粒中回收衍生物的方法的流程图;和
56.图6
–
是在一个优选实施方案中的从铝土矿残渣中回收衍生物的方法的流程图。
57.附图详述
58.首先,应该指出,本文所用的术语“优选”不应理解为“强制性的”或“必需的”。术语“优选”表征各种可行实施方案中的本发明的特别有效的实施方案,以使本发明的范围仅受其对于获得所提出的技术效果而言实际上必不可少的特征的限制。
59.此外,本说明书中使用的术语“铝土矿残渣”应理解为是通过铝土矿矿石加工,特别是通过拜耳法生成的残渣,其组成包括赤铁矿和针铁矿形式的矿石、三水铝石和拜耳方钠石形式的铝、锐钛矿形式的钛、钪、铀、钍和锆,可能含有或不含附加元素。
60.另外,为了更好地理解本发明,本文所用的术语“目”(并且对应于符号“#”)旨在界定粒度的区间。本领域技术人员应该理解的是,本文关于单个数字使用的术语“目”并不意味着所加工的产品或残渣的每个粒子恰好具有这一尺寸;相反,“目”尺寸的指示大致表示该类别内的粒子之间的平均尺寸或区间均值。
61.回收方法
–
铝土矿残渣
62.本发明考虑的第一种方法是铝土矿残渣材料,特别是来自拜耳法的残渣的回收方法。
63.因此,本发明提出通过使用微波的加热方法从铝土矿残渣中高效回收感兴趣的材料的方法,其优选实施方案显示在图2中。
64.本发明的方法优选包括将铝土矿残渣与还原剂混合的早期火法冶金步骤100以获得残渣混合物;将所得混合物造粒101并在微波反应器1中加热残渣混合物110以获得还原的铝土矿残渣。
65.混合步骤(100)
66.混合步骤100旨在加入还原剂以使采矿产品内的某些感兴趣的材料能够随后通过加热转化/还原,由此获得如本文提到的还原的铝土矿残渣。还原剂可以是例如焦炭,但考虑到通过微波进行还原的通用性,可以使用几种其它还原剂,如矿物和植物煤的细粒、木质素、锯屑等。值得注意的是,焦炭专门用于实现铝土矿残渣中存在的材料的转化,而非燃烧或加热残渣本身,因为这种加热是通过微波进行的。因此,本文提出的方法生成较少的温室气体,比现有技术的用于铁还原的碳基工业方法更高效。
67.优选地,在固体还原剂的情况下,还原剂应该预先研磨至低于75μm,并在螺带式掺合机(ribbon blender)类型的设备中混合10至30分钟,优选15至25分钟,直至形成在5至50%,优选10至20%的还原剂比率下,更优选在11%还原剂比率下的铝土矿残渣和还原剂的碳热混合物。将形成碳热混合物的还原剂和铝土矿残渣的混合物完全进给至新的单元操作,即造粒步骤101。
68.造粒步骤(101)
69.造粒步骤是任选的,因为可以在粉末在微波内自由移动的情况下进行冶金还原步骤。尽管如此,造粒旨在使细粒团聚,由此将它们结合,这防止气体携带细粒并促进还原气体在球团内的扩散。这就是为何由造粒获得的高扩散率减少反应所需的时间并产生更快转化的原因。如果进行造粒101,倾斜和旋转的参数应该是铝土矿残渣的特性,如水分、氢氧化钠含量和组成。优选的钠含量为4至8%,优选5至6%,以使这一步骤不需要粘合剂,其中球团本身的组成足以达到此目的。将来自碳热混合物的球团完全进给至下一个单元操作,即加热110。
70.加热步骤(110)
71.在通过微波110进行的加热步骤110中,反应在由100kw微波发生器供能的反应器中进行,其中辐照10kw.h至100kw.h功率/吨碳热混合物,优选20kw.h至60kw.h/吨碳热混合物。上述加热步骤110中使用的微波反应器可以是例如本发明建议的微波反应器1以获得特别高的加热效率。将进一步描述所述反应器1。在这方面,加热时间可优选为2至18分钟不等,将温度保持在转化为磁性相所需的温度的80%以上,持续达到转化为磁性相所需的温度所花费的时间的至少两倍时间,更优选辐照4分钟,而热保持10分钟。例如,所采用的转化为磁性相所需的温度可以为300℃至1000℃。
72.在这方面,使用微波加热采矿产品为该方法带来许多优点和积极效果。首先,微波促进能量的传递,而非热传递;因此,相的加热和转变在更高效的基础上发生。此外,来自微波频谱的电磁波促进分子结构的变化;电偶极子和磁偶极子的旋转导致穿过微波的矿物结构留下结晶形式,这有利于加工。因此,用微波预处理矿石使得能够以较少的试剂消耗回收金属。
73.与许多其它形式的还原和加热,如高炉和旋转炉等相比时,在微波中加工来自拜耳法的尾矿产生若干优点。这是因为由微波设备提供的通过电磁波的加热传递能量而非热,以使加热在原子基础上从内部向外部发生。电磁波改变原子旋转状态,并使它们振动和旋转,由此增加平均动能,并因此提高温度。此外,该过程通过将方钠石转化为霞石、将锐钛矿转化为无定形或金红石(ruthyl)等而改变这种残渣中所含的化合物的原子结构。
74.与电磁波的这种相互作用在残渣内所含的材料中在不均匀的基础上发生,并且介电常数(实数和虚数)是控制这种相互作用强度的性质。一些材料,如磁铁矿表现出高介电常数,且因此应该保持与电磁波的更多相互作用并耗散更多能量。除了将铁相还原之外,这种不均匀的相互作用将促进材料的独有释放,由此促进这些材料的分离并改进反应性。
75.例如,锐钛矿形式的钛是非常惰性的材料。在通过微波辐照后,振动使其变成无定形,并且这导致该材料开始与无机酸反应,由此使其能够增溶和随后回收,如下所示。
76.这是通过使用微波反应器1转化和加热感兴趣的采矿产品产生的有益效果的起源。获得更快和更高效的加热,其中通过不均匀振动预先分离材料,并且不太相关的是,不
需要燃烧污染性燃料,如碳;通过使用微波反应器,可以使用化学计量量的还原剂。另外,对于本文描述的使用微波反应器来还原/转化采矿产品的本发明的所有方法,加以必要的变更,可以观察到这些优点。
77.为了弄清在本发明的方法的过程中在采矿产品的加热中发生的情况,注意到铝土矿残渣(时间0)中存在的赤铁矿和针铁矿相被微波能量和焦炭中存在的co通过bourdouard反应迅速转化。因此,如图3中更好地看出,铁、金属铁和磁铁矿的磁性相在几分钟内开始生长。残渣中所含的其它材料,如方钠石也经历转化。为了更好地说明残渣经历的转化,下表1显示了在通过微波加热过程中铝土矿残渣的相:
[0078][0079][0080]
表1
–
铝土矿残渣在其开始通过微波反应器加热时的相
[0081]
在这方面,仍然值得强调的是,如图4中所见,在通过微波加热过程中,铝土矿残渣的方钠石转化成霞石。到转化结束时,整个方钠石转化成霞石。除了降低残渣的碱性特征外,这种转化还使得这种化合物能够化学浸出。
[0082]
第一研磨步骤(120)
[0083]
铝土矿残渣的相关回收方法在一个可行实施方案中还包括对还原铝土矿残渣的至少一次研磨120、121的步骤。
[0084]
更具体地,这种方法可以涉及至少一个研磨步骤120、121,以解聚要通过磁选机集中的还原铝土矿残渣的磁性相。研磨120、121可以例如通过棒磨机或球磨机,优选通过球磨
机进行。
[0085]
优选地,进行第一研磨步骤120以实现残渣的第一次解聚。在其它相关步骤的上下文中,本文还将提出关于研磨步骤120、121,且特别是关于第二研磨步骤121的进一步细节。
[0086]
尺寸分离步骤(111)
[0087]
在这种第一研磨步骤120之后,该方法优选至少包括铝土矿残渣的尺寸分离步骤111,以获得残渣的粗粒部分gr和细粒部分fi。所述尺寸分离111可以例如通过一个或多个旋风分离器进行。
[0088]
更优选地,如图2a中所示,通过串联的两个旋风分离器进行尺寸分离111。第一旋风分离器sc1接收来自第一研磨步骤120的铝土矿残渣rb,并将其分离成尺寸低于和高于#100的材料部分(分别为-#100和+#100),然后将低于#100的材料部分进给到第二旋风分离器sc2,其将接收的部分分离成高于和低于#200的部分(分别为-#200和+#200)。将由第一旋风分离器sc1分离的高于#100的部分添加到由第二旋风分离器sc2分离的高于#200的部分中,并得到粗粒部分gr。由第二旋风分离器sc2分离的低于#200的部分得到细粒部分fi。
[0089]
粗粒部分(gr)的磁力分离步骤(130)
[0090]
在尺寸分离111之后,将粗粒部分gr直接送至磁力分离步骤130,其中获得第一磁性部分mag.i和第一非磁性部分n.magi。粗粒部分的所述磁力分离130优选在磁选机中用300至800rpm的速度和约300高斯的低强度磁场进行。如下所示,这种第一非磁性部分n.mag.i随后与第二非磁性部分n.mag.ii合并。
[0091]
第二研磨步骤(121)
[0092]
转向残渣的细粒部分fi,其经受第二研磨步骤121。在这方面,要指出,如上所述,粗粒部分gr已经含有还原和释放的铁,其可以容易地通过仅磁力分离130集中。残渣的细粒部分fi聚集到其它矿物,使得额外研磨有利于释放磁性粒子并允许进一步合适的磁力分离。
[0093]
细粒部分(fi)的磁力分离步骤(131)
[0094]
然后,残渣的磨碎细粒部分fi经受额外的磁力分离步骤131,其旨在将细粒部分fi分离成两个其它部分,即超细非磁性部分n.magii(优选高于#500)和超细磁性部分mag.ii。这一步骤可以通过优选具有900至1,100rpm的速度和约800高斯的磁场强度的磁选机进行。
[0095]
在磁力分离后,获得磁性部分mag.i和mag.ii,以致可以有效地提取金属铁和磁铁矿(两者都是铝土矿残渣中所含的感兴趣的材料)以供进一步使用。作为一个实例,下表2公开了通过使用如本发明提供的铝土矿残渣回收方法,不同尺寸(级分)的解聚的铝土矿残渣之间的比率及其含量(%):
[0096]
级分%重量含量(%)所含的铁分布(%)+100#8.385.717.1125.79-100#和+200#8.578.326.6524.14-200#和+400#31.423.57.3826.75-400#和+600#16.513.12.167.84-600#35.312.14.2715.49总计
ꢀꢀ
27.58100.00
[0097]
表2
–
级分之间的比率和含量(%)
[0098]
表2公开了关于在微波反应器中处理后的各个铝土矿残渣级分中所含的铁的信息。第一列显示铁在tyler级数尺度下的粒度范围;第二列是指保留在各筛网中的重量百分比;第三列是在各级分中测得的铁含量;第四列是指如通过第2列重量百分比和第3列含量的乘积计算的该级分中所含的铁。第五列是指通过将级分中所含的铁量除以总铁而计算的各级分中的铁分布。
[0099]
因此,本文提出的火法冶金处理和磁力分离过程能够获得含有金属铁和磁铁矿(它们代表根据本发明的方法提取的第一增值产物)的磁性部分mag.i和mag.ii。
[0100]
转向超细非磁性部分n.mag.ii,将其与获自粗粒部分gr的非磁性部分n.mag.i合并以获得合并的非磁性部分n.magi+ii,将其进给到如下所示的化学加工步骤以提取其它感兴趣的材料。
[0101]
关于化学加工,根据本发明的铝土矿残渣的衍生物的回收方法包括必须以所示顺序进行的以下步骤,以便能够正确提取感兴趣的材料:
[0102]
(i)浸提非磁性材料的部分140以获得浸出液,随后倾析和过滤所述浸出液,以提取二氧化硅sio2;
[0103]
(ii)沉淀150浸提140的料液副产物(liquor byproduct)以获得二氧化钛tio2;
[0104]
(iii)蒸发160沉淀150的料液副产物以获得饱和液和富氧化铝的残留固体;和
[0105]
(iv)煅烧170获自蒸发160的所述富氧化铝的残留固体以获得氧化铝。
[0106]
进行上述处理步骤以从硫酸中回收残渣的非磁性部分n.magi+ii的特定材料。此外,我们将提供关于各个上述步骤的细节。
[0107]
浸提步骤(140)
[0108]
浸提140通过将非磁性部分n.magi+ii添加到浸提槽中进行,其中将硫酸添加到该槽中。
[0109]
浸提以1至10克非磁性部分/10毫升硫酸溶液的固液比进行,条件是浓度可为2mol/l至6mol/l不等,优选4mol/l。浸提时间可为30至120分钟,优选50至75分钟不等。温度可为30℃至90℃,优选50℃至70℃不等,其中搅拌速度轴为400至600rpm,优选500至550rpm以避免死区。
[0110]
在这些条件下,对硫酸惰性的非磁性二氧化硅保持固态;可以倾析和过滤这种成分,由此能够从铝土矿残渣中提取无定形二氧化硅sio2。由此产生的浸出液在水相中富含并充满硫酸铝、硫酸氧钛和硫酸钠。
[0111]
沉淀步骤(150)
[0112]
在浸提140后,富含硫酸铝和硫酸氧钛且不含二氧化硅的料液在沉淀槽中水解和沉淀150。为此,加入tio2晶种,并用氢氧化钠将该溶液的ph调节到1.5至2.5,优选1.8至2.2的ph,并以50至200rpm,优选100至150rpm的转子速度在10至90℃,优选30至40℃的温度下搅拌30至120分钟,优选60至80分钟的时间段。这迫使二氧化钛tio2沉淀,其随后例如通过压滤机和干燥器从料液中提取。
[0113]
蒸发步骤(160)
[0114]
通过将搅拌150的副产物添加到蒸发器中而进行蒸发160。所述蒸发包括将富硫酸铝料液的溶液蒸发至10至16波美度,优选11至13波美度的密度,以获得富氧化铝的残留固体。为此,加入化学计量量的硫酸钠以用50%氢氧化钠溶液将ph提高到6至12,优选7至8的
范围。必须倾析和过滤铝沉淀物。将饱和液再循环到沉淀器。
[0115]
煅烧步骤(170)
[0116]
通过将从压滤机提取的蒸发160的副产物添加到煅烧炉中而进行煅烧170。通过蒸发160获得的残留固体在400至800℃,优选550至650℃的温度下煅烧30至120分钟,优选40至70分钟的时间段,以获得氧化铝al2o3。
[0117]
煅烧炉也可用于获得二氧化硫so2和三氧化硫so3,它们可以在煅烧炉排气过程中提取。如果需要酸再生,所述气体可用于酸再生。
[0118]
因此,本文提出的铝土矿残渣的回收方法使得能够在高效和快速的基础上通过微波加热和随后的化学加工步骤获得各种感兴趣的材料。该方法遵循特定步骤的顺序,其逻辑确保提取除仅铁和氧化铝以外的元素的可能性。
[0119]
除了通过微波转化促进的有利速度外,本文提出的铝土矿残渣的回收方法使得能够回收残渣中存在的各种材料以进行合适的加工。该方法不仅涉及铁和氧化铝,而且以有利的比例提供它们的回收。下表3显示通过使用本发明的铝土矿残渣的回收方法对各材料预期的全局回收率百分比:
[0120]
化合物全局回收率(%)质量(kg)/ton.r.b.金属铁68.64115.60氧化铝57.0984.76二氧化硅89.95105.27钛58.1621.28固体残渣-183.20
[0121]
表3
–
全局回收率%
[0122]
微波反应器和加热方法
[0123]
鉴于上述情况,图1公开了本发明的微波反应器1的一个优选实施方案。如上文所阐明,前述铝土矿残渣的回收方法可以使用本文的反应器1,以达到该方法的特别有利的效率。
[0124]
所述反应器1包含由对微波透明的隔热材料构成的外壳10。外壳10可以呈现任何合适的几何形状以将待加热的矿石产品包围在其内部,包括立方体、平行六面体或圆柱体几何形状。外壳10可通过一组壁或单个壁(例如,在圆柱体几何的情况下)形成。
[0125]
在一个可行实施方案中,外壳10可由具有高氧化铝含量的多孔混凝土构成,优选在组成中具有75%至95%的al2o3,更优选在组成中具有85%至92%的al2o3,且更优选在其组成中具有92%的al2o3。
[0126]
所述外壳10还优选由低密度多孔混凝土构成,优选0.05至2克/立方厘米,更优选0.7至1.2克/立方厘米,且更优选0.9克/立方厘米。其应该通过在其结构中生成气泡的方法制作,以使其保持充气并且甚至在加热后也保持来自微波的透明电磁辐照。
[0127]
反应器1还至少包括由感受器材料构成的感受器壁20、21、22。在一个可行实施方案中,反应器1包括至少覆盖外壳10的内部部分的几个感受器壁20、21、22。构成感受器壁的感受器材料必须是能够适当吸收电磁波并将它们的能量转换成热的材料。感受器壁20、21、22的材料必须具有高介电常数和高磁矩,以及耐化学性、耐热性和耐机械性。在一个可行实施方案中,感受器壁20、21、22由以下至少一种构成:碳化硅、钛铁矿(limenite)和金属钛。
考虑到反应器1的构造和容量,所选材料应该优选能够在尽可能短的时间内最大限度加热采矿产品,该时间可能优选为2至18分钟不等,其中将温度保持在转化为磁性相所需的温度的80%以上,持续达到转化为磁性相所需的温度所花费的时间的至少两倍时间,更优选辐照4分钟,而热保持10分钟。这些优先区间适用于使用微波反应器来转化任何采矿产品的任何方法,并且特别适用于下述方法(从铝土矿残渣、矿粉和红土镍中回收材料)
[0128]
优选地,这种感受器壁20、21、22的宽度应该为1至10mm宽度不等,更优选3至7mm,更优选5mm。在这种可行实施方案中,约40至50%的电磁波被壁吸收,而剩余部分被来自拜耳法的残渣和还原剂之间的混合物吸收,由此使得该方法最大限度有益于传递的能量。
[0129]
优选地,由外壳10和至少一个感受器壁20限定的区域表征至少一个加热室a、b。加热室a、b的实施方案可以以几种形式实施。例如,在外壳10的圆柱体实施方案和感受器壁20的环形实施方案的情况下,加热室应该配置在由外壳10和感受器壁20限定的内部区域中。来自图1的反应器1的实例图示两个加热室a、b的实施方案——通过由外壳10和感受器壁20、21以及21、22联合限定以形成矩形室a、b。设定加热室a、b以接收和包围要在反应器1中加热的产品。室的尺寸和数量根据要加热的产品的传热能力和所需的热流而变。
[0130]
在一个可行实施方案中,反应器1至少包括由电磁波的反射器材料,如不锈钢或任何其它发光反射金属,如铝构成的反射器板30。优选地,反射器板30至少包括朝向加热室a、b的拉丝表面31,以使电磁波在室a、b上和感受器壁20、21、22上能够高效反射。更优选地,反应器1包括一对反射器板30,被安置在外壳10的相对的纵向端处。还优选地,反射器板30包括0.5mm至5mm,更优选1mm至3mm,且再更优选2mm的宽度。
[0131]
值得注意的是,本发明的微波反应器1特别高效地应用于加热材料以从这些材料中进一步回收感兴趣的元素。本文提出的反应器1能够快速加热采矿产品以使其转化/还原,并随后回收它们的元素。特别地,本发明的微波反应器使用具有对电磁波透明的材料的外壳10,由此能够快速且均匀地加热产品,而不需要专门的开口让波进入。感受器壁20、21、22和外壳10的布置以形成室a、b使得能够高效加热产品。由于将电磁波朝向室a、b反射和朝向感受器壁20、21、22反射,反射器板30的任选应用还改进这种效率。
[0132]
根据微波反应器的上述描述,本发明还提供一种通过微波加热产品的方法,其包括在微波反应器1上发出微波的步骤,使得这些波穿过微波反应器1的由隔热材料构成并且对微波10透明的外壳10,并使得所述微波至少到达感受器壁20。在一个可行实施方案中,该方法还可包括在反射器板30上反射微波的步骤。
[0133]
因此,本发明还包括衍生自采矿残渣的材料的回收方法。
[0134]
回收方法
–
铁矿粉
[0135]
本发明还涉及一种从矿粉中回收材料的方法。矿粉是具有低含量和低总价值并形成衍生自采矿过程的细粒级分的铁矿石。细粒级分通常被弃置,或需要大量加工;在大多数情况下,由于其低粒度和差的组成,其不太可能在不通过造粒或合成进行加工和团聚的情况下用于传统铁转化(高炉)。
[0136]
因此,本发明提出一种铁矿粉的回收方法,其不需要预先加工或团聚,而是能够从这种采矿产品中提取感兴趣的材料。图5显示这种方法的一个优选实施方案。
[0137]
矿粉的回收方法包括以下步骤:
[0138]-在微波反应器中加热铁矿粉210以获得还原铁矿粉。
[0139]
这一加热步骤使得能够转化矿粉内的材料而不需要预先造粒或团聚。该转化以与上文关于铝土矿残渣回收方法的描述类似的方式进行,在这种情况下要考虑铁矿粉中所含的材料。
[0140]
在一个可行实施方案中,该方法还可包括以下步骤:
[0141]-将铁矿粉与来自还原剂的细粉混合200,以获得细粉混合物;和
[0142]-在微波反应器1中加热所述细粉混合物210以获得还原铁矿粉。
[0143]
上述步骤旨在使得细粉内所含的材料能在加热过程中转化。在这种情况下,还原剂也以细粉形式引入。例如,还原剂可以是煤粉。应该重申,在使用煤粉的情况下,煤仅用作还原剂,而非用作加热的燃料,因为通过微波直接进行加热。
[0144]
在一个可行实施方案中,该方法还可包括以下步骤:
[0145]-进行至少一个研磨步骤220和一个磁力分离步骤240以获得磁性材料部分magi和非磁性材料部分n.magi。
[0146]
研磨220可以在加热210后通过球磨机进行,而磁力分离可以通过任何合适的磁选机进行。
[0147]
优选地,该方法还可包括在研磨步骤220和磁力分离步骤240之间进行至少尺寸分离步骤230的步骤。尺寸分离步骤230可以通过旋风分离器进行。更优选地,该方法还包括将获自尺寸分离230的铁矿粉的细粒级分fin送回混合步骤200的步骤231。在这方面,要指出,将细粒级分再循环以使在首次通过期间未燃烧的还原剂得以完全使用,以及未转化成金属铁的赤铁矿和磁铁矿得以完全使用。通过在闭合过程中使用再循环,细粒的总转化率倾向于接近100%。粗粒级分(是指转化为金属的铁)通过离开旋风分离器的底部而被旋风分离器分离,而未转化的铁级分与未反应的还原剂一起通过顶部离开并回到还原阶段。
[0148]
从铁矿粉中提取的磁性材料部分mag.i包含生铁,而非磁性材料部分n.magi包含可用于相关工艺的元素,如二氧化硅、铝和煤。
[0149]
因此,本文提出的铁矿粉衍生物的回收方法使得能够以高效方式转化细粉以及提取感兴趣的材料,而不需要为此对细粉进行合成或造粒。
[0150]
为了举例说明上述说法,下表4公开了在50%赤铁矿和50%矿物煤的条件下通过本发明的回收方法获得铁矿粉的不同级分的组成试验(主要化合物):
[0151]
矿粉的级分金属铁(%)al(%)si(%)+100#94.481.173.15-100#和+200#94.801.093.35-200#和+270#94.931.083.17-270#和+600#46.791.253.29-600#14.240.571.47
[0152]
表4
–
通过本发明的方法获得的矿粉的不同级分的组成
[0153]
如表4中可以看出,表4公开了在微波中还原、研磨和在tyler尺度下的筛网中筛分的结果,在微波中的第一还原步骤在高于#270的级分中产生具有商业纯度的金属铁。低于#270的级分应该通过旋风分离器顶部流再循环到旋风分离器(be re-circulated by a current on the top of to cyclone)以提高其含量和尺寸,而低于#270的级分中所含的剩余材料是指在该第一步骤中未转化的还原剂,其也应该再循环以改进工艺效率。
[0154]
回收方法
–
红土镍
[0155]
本发明还涉及衍生自红土镍(即镍矿床的包壳部分)的材料的回收方法。镍精炼厂和铁-镍精炼厂目前不使用这一部分,因为含量不适合在常规炉中的熔融工艺和在压力和温度下的浸出。目前,采矿公司将这一部分储存,同时等待用于铁-镍富集和后续使用的加工技术。这些矿床分布在全世界的几个地点,特别是在热带地理区域,并且巴西和世界上最大的矿床具有大量的红土镍。因此,实现能够从这种采矿产品中回收感兴趣的材料的方法显然是有意义的。
[0156]
本发明提出一种回收红土镍的衍生物的方法,其使用获得铁-镍精矿的特定步骤和能够处理这种精矿以便回收感兴趣的材料的后续步骤。
[0157]
这种方法包括以下步骤:
[0158]-擦洗红土镍以获得解聚的红土镍300;
[0159]-将解聚的红土镍尺寸分离成至少细粒级分ff和至少粗粒级分fg310;和
[0160]-磁力分离粗粒级分fg以获得磁性级分fm320。
[0161]
擦洗步骤300旨在物理上有益于红土镍以从这种采矿产品中松解铁-镍附聚物。随后的尺寸分离步骤使得能够获得红土镍的细粒级分ff和粗粒级分fg。擦洗步骤300可以例如在强力擦洗滚筒筛内进行,而尺寸分离步骤310可以通过旋风分离器进行。
[0162]
发现如这种方法提出的擦洗步骤300能够富集红土镍细粒级分中的镍含量。作为实例,下表5至8显示擦洗时间的增加与所得细粒级分中的镍含量之间的比较:
[0163][0164]
[0165][0166][0167]
表5至8-擦洗时间的增加(5分钟、20分钟)与所得细粒级分中的镍含量之间的比较研究
[0168]
施加到擦洗器的四个样品——都具有红土型分布和0.5%镍、0.9%镍、1.2%镍和1.4%镍的含量,在表5中分别称为0.5%ni、0.9%ni、1.2%ni和1.4%ni——在暴露于擦洗器的强烈磨损的时间期间表现出提高的含量。擦洗导致镍附聚物恢复为粒子,并且能使被细镍包封的其它粒子被释放并集中在细粒级分中。如镍分布所示,所有测试的级分在暴露于擦洗器的时间期间都表现出细粒级分的增加。
[0169]
此外,下表6显示在擦洗20分钟后细粒级分中的红土镍的组成,其中可以观察到铁和镍的显著集中:
[0170]
[0171]
表6
–
在20分钟擦洗后的红土镍的组成
[0172]
在尺寸分离步骤310中获得的粗粒级分fg然后进行磁力分离320以获得磁性部分fm。非磁性部分被视为尾矿。
[0173]
在一个可行实施方案中,这种方法还包括将磁性级分fm与细粒级分ff合并以获得铁-镍精矿cn的步骤。细粒级分ff没有通过磁力分离进行加工,因为其具有足够的铁和镍含量。
[0174]
从这一点开始,本发明的方法可以遵循两种不同的可能路径,即:(i)浸提cn精矿以获得第一系列的感兴趣的材料,或(ii)处理cn精矿以获得铁-镍。
[0175]
在上述两种可能性(i)和(ii)中,该方法都还可包括在微波反应器1中加热330铁-镍精矿cn以获得还原精矿。微波反应器1可以如本文所述,或是适于加热采矿产品的任何其它微波反应器。如果选择浸提精矿cn的可能性(i),应该强调,浸提可以通过微波加热330辅助或没有通过微波加热330辅助。
[0176]
如果选择浸提(i),在一个可行实施方案中,该方法还包括以下步骤:
[0177]-浸提铁-镍精矿cn以至少获得衍生材料csn340。
[0178]
通过浸提过程获得的衍生物是例如硫酸镍和电池钴的精矿csn。浸提340之后可以例如在压滤机中加工以获得感兴趣的衍生物。
[0179]
在选择处理(ii)以获得铁-镍的情况下,在一个可行实施方案中,该方法还包括以下步骤:
[0180]-研磨350和磁力分离360铁-镍精矿cn以至少获得衍生物fen。
[0181]
通过这些附加步骤获得的衍生物是铁-镍fen。研磨350可以通过球磨机进行,而磁力分离360可以通过任何合适的磁选机进行。
[0182]
因此,该红土镍衍生物的回收方法使得能够通过一系列步骤从这种采矿产品中获得感兴趣的材料,这些步骤能够获得铁-镍精矿,以随后根据所需的感兴趣的材料,通过进一步加工提取衍生物。
[0183]
值得强调的是,本文提出的红土镍衍生物的回收方法可用于所有红土带,从红色褐铁矿,经过黄色褐铁矿,直到早期腐泥土。在某些情况下,可以用研磨代替或补充强力擦洗步骤(例如,每当涉及腐泥土时)。
[0184]
在描述优选实施方案的一个实例后,必须理解的是,本发明的范围包含其它可能的变化,其仅受所附权利要求书的内容,包括任何可能的等同物的限制。