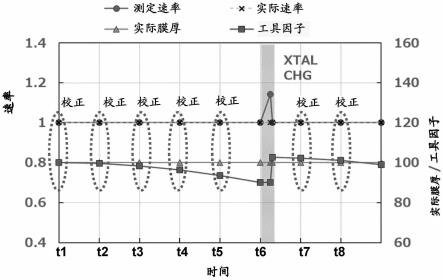
1.本发明涉及成膜装置、成膜方法以及电子器件的制造方法。
背景技术:2.在制造有机el显示器等时所使用的成膜装置中,要求提高蒸镀材料相对于基板的成膜的精度。在专利文献1中记载了利用光学的膜厚测定装置测定在基板上成膜的蒸镀材料的膜厚,在膜厚不足的情况下对该基板进行追加的成膜。在专利文献2中记载了使用设置于成膜室内的晶体振子监视器,计算蒸镀材料的膜厚和成膜速率。
3.现有技术文献
4.专利文献
5.专利文献1:日本特开2005-322612号公报
6.专利文献2:日本特开2019-065391号公报
技术实现要素:7.发明要解决的课题
8.晶体振子监视器基于晶体振子的谐振频率与晶体振子的电极上的蒸镀材料的蒸镀量(堆积的蒸镀材料的质量)的关系,根据谐振频率的变动测定蒸镀材料的放出量。但是,晶体振子的特性有时根据时效变化、个体差异而变动。在不考虑这样的晶体振子监视器的特性而基于蒸镀材料的放出量的测定值控制成膜动作的情况下,有可能无法以所期望的精度进行成膜。
9.本发明的目的在于,在基于蒸镀材料的放出量的测定值控制成膜动作的成膜装置中,提高成膜的精度。
10.用于解决课题的方案
11.本发明是一种成膜装置,该成膜装置将蒸镀材料蒸镀到基板上来进行成膜,其特征在于,该成膜装置具备:
12.监视部件,其测定来自放出所述蒸镀材料的蒸发源的所述蒸镀材料的放出量;以及
13.膜厚测定部件,其测定所述基板上的所述蒸镀材料的膜厚,
14.基于所述膜厚测定部件对所述膜厚的测定值,校正基于所述监视部件对所述放出量的测定值进行控制的成膜动作。
15.另外,本发明是一种成膜装置,该成膜装置将蒸镀材料蒸镀到基板上来进行成膜,其特征在于,该成膜装置具备:
16.监视部件,其测定来自放出所述蒸镀材料的蒸发源的所述蒸镀材料的放出量;以及
17.膜厚测定部件,其测定所述基板上的所述蒸镀材料的膜厚,基于所述膜厚测定部件的测定值,修正所述监视部件的测定值。
18.另外,本发明的成膜方法的特征在于,该成膜方法具有如下工序:
19.在基板上蒸镀从蒸发源放出的蒸镀材料来进行成膜;
20.获取来自所述蒸发源的所述蒸镀材料的放出量的测定值;
21.获取所述基板上的所述蒸镀材料的膜厚的测定值;以及
22.基于所述膜厚的测定值,校正基于所述放出量的测定值进行控制的成膜动作。
23.另外,本发明的成膜方法的特征在于,该成膜方法具有如下工序:
24.在基板上蒸镀从蒸发源放出的蒸镀材料来进行成膜;
25.获取来自所述蒸发源的所述蒸镀材料的放出量的测定值;
26.获取所述基板上的所述蒸镀材料的膜厚的测定值;以及
27.基于所述膜厚的测定值,修正所述放出量的测定值。
28.发明的效果
29.根据本发明,能够在基于蒸镀材料的放出量的测定值控制成膜动作的成膜装置中,提高成膜的精度。
附图说明
30.图1是电子器件的制造装置的示意图。
31.图2是表示成膜装置的结构的剖视图。
32.图3是表示成膜速率监视器的结构的示意图。
33.图4是表示通路室和膜厚测定部的结构的剖视图。
34.图5是表示膜厚测定部的结构的框图。
35.图6是表示基板的被成膜面侧的结构的俯视图。
36.图7是成膜装置的控制框图。
37.图8是表示进行成膜控制的校正的时机的一例的图。
38.图9是表示进行成膜控制的校正的时机的另一例的图。
39.图10是表示刚更换晶体振子之后的测定速率等的图。
40.图11是实施例2的电子器件的制造装置的俯视图。
41.图12是说明电子器件的制造方法的图。
42.附图标记说明
43.s:基板,205:成膜速率监视器,310:膜厚测定部,206:成膜控制部。
具体实施方式
44.以下,参照附图,说明本发明的优选实施例。但是,以下的记载只不过是例示性地表示本发明的优选的结构,本发明的范围并不限定于这些结构。另外,以下的说明中的装置的硬件结构及软件结构、处理流程、制造条件、尺寸、材质、形状等只要没有特别记载,其宗旨就不是要将本发明的范围限定于此。
45.本发明可理解为在基板上进行成膜的成膜装置或成膜方法。本发明也可理解为使用了该成膜装置或成膜方法的电子器件的制造装置或电子器件的制造方法。本发明也可理解为上述各装置的控制方法。
46.本发明能够优选地应用于经由掩模在基板的表面形成所期望的图案的薄膜材料
层的情况。作为基板的材料,能够利用玻璃、树脂、金属、硅等任意的材料。作为蒸镀材料(成膜材料),能够利用有机材料、无机材料(金属、金属氧化物)等任意的材料。本发明的技术典型地应用于电子器件、光学元件的制造装置。特别适合于有机el显示器、使用它的有机el显示装置、薄膜太阳能电池、有机cmos图像传感器等有机电子器件。但是,本发明的应用对象不限于此。
47.[实施例1]
[0048]
在实施例1中,作为本发明的基本的实施例,对装置的整体结构和膜厚测定及控制的基本原理进行说明。
[0049]
《电子器件制造装置》
[0050]
图1是示意性地表示电子器件制造装置的一部分结构的俯视图。图1的电子器件制造装置例如用于智能手机用的有机el显示装置中使用的有机el面板的制造。
[0051]
电子器件制造装置将多个集群型单元(以下也简称为“单元”)cu1~cu3经由连结室连结,构成生产线。各集群型单元是多个成膜室配置于基板输送机器人的周围的结构。此外,单元的数量不限于3个。另外,属于各集群的腔室的数量不限于以下记载的数量。另外,也可以按每个集群而腔室的种类、数量不同。以下,在对所有单元通用的说明和不特定单元的说明中,使用如“cux”这样用“x”代替数字进行标记的附图标记,在对个别单元的说明中,使用如“cu1”这样标记数字的附图标记(对于单元以外的结构标注的附图标记,也是同样的)。
[0052]
图1示出了在整个电子器件制造装置中将蒸镀材料蒸镀到基板上来进行成膜的成膜装置的一部分。在成膜装置的上游,例如也可以设置基板的储料器、加热装置、清洗等预处理装置等,在成膜装置的下游,例如也可以设置密封装置、加工装置、处理完的基板的储料器等,将它们整体合在一起构成电子器件制造装置。基板从上游侧向下游侧以沿着箭头f的方向的流动进行输送。
[0053]
集群型单元cux具有中央的输送室trx和配置于输送室trx的周围的多个成膜室evx1~evx4及掩模室msx1~msx2。相邻的2个单元cux与cux+1之间通过连结室cnx连接。集群型单元cux内的各室trx、evx1~evx4、msx1~msx2以及连结室cnx在空间上相连,其内部被维持为真空或氮气等非活性气体气氛。在本实施例中,构成单元cux和连结室cnx的各室与未图示的真空泵连接,能够分别独立地进行真空排气。各个室也被称为“真空腔室”或者简称为“腔室”。此外,在本说明书中,“真空”是指充满比大气压低的压力的气体的状态。
[0054]
在输送室trx设置有作为输送基板s和掩模m的输送部件的输送机器人rrx。输送机器人rrx例如是具有在多关节臂安装有保持基板s和掩模m的机械手的构造的多关节机器人。在集群型单元cux内,基板s保持其被成膜面朝向重力方向下方的水平状态不变地由输送机器人rrx、后述的输送机器人rcx等输送部件输送。输送机器人rrx进行上游侧的通路室psx-1、成膜室evx1~evx4、下游侧的缓冲室bcx之间的基板s的输送。另外,输送机器人rrx进行掩模室msx1~2与成膜室evx1~4之间的掩模m的输送。
[0055]
掩模室msx1~msx2是设置有分别收纳用于成膜的掩模m和使用完的掩模m的掩模储料器的室。在蒸镀成膜的情况下,作为掩模m,优选利用形成有许多开口的金属掩模。成膜室evx1~evx4是用于在基板s的表面(被成膜面)形成膜的室。
[0056]
连结室cnx具有将单元cux与单元cux+1连接并将在单元cux成膜后的基板s交接到
后段的单元cux+1的功能。本实施例的连结室cnx从上游侧起依次包括缓冲室bcx、回旋室tcx以及通路室psx。但是,连结室cnx的结构不限于此,也可以仅由缓冲室bcx或通路室psx构成。
[0057]
缓冲室bcx是用于在单元cux内的输送机器人rrx与连结室cnx内的输送机器人rcx之间进行基板s的交接的室。缓冲室bcx具有通过暂时地收纳多个基板s来调整基板s的送入速度、送入时机的功能。
[0058]
回旋室tcx是用于使基板s的朝向旋转180度的室。在回旋室tcx内设置有从缓冲室bcx向通路室psx交接基板s的输送机器人rcx。输送机器人rcx在支承着在缓冲室bcx接收的基板s的状态下回旋180度,将其移交到通路室psx。由此,将基板s向成膜室送入时的朝向在上游侧的单元cux和下游侧的单元cux+1为相同的朝向,因此,能够使相对于基板s的成膜的扫描方向、掩模m的朝向在各单元cux中一致。
[0059]
通路室psx是用于在连结室cnx内的输送机器人rcx与下游侧的单元cux+1内的输送机器人rrx+1之间进行基板s的交接的室。在本实施例中,在通路室psx内配置有膜厚测定部(详细情况将在后述)。
[0060]
在成膜室evx1~evx4、掩模室msx1~msx2、输送室trx、缓冲室bcx、回旋室tcx、通路室psx之间可以设置有能够开闭的门(例如,门阀或闸阀),也可以是始终开放的构造。
[0061]
《真空蒸镀装置》
[0062]
图2示意性地示出了设置于成膜室evx1~evx4的真空蒸镀装置200的结构。真空蒸镀装置200具有保持掩模m的掩模保持器201、保持基板s的基板保持器202、蒸发源单元203、移动机构204、成膜速率监视器205、成膜控制部206。掩模保持器201、基板保持器202、蒸发源单元203、移动机构204以及成膜速率监视器205设置于真空腔室207内。成膜控制部206为了使在基板s上成膜的薄膜的膜厚达到目标值,基于成膜速率监视器205的输出值来控制蒸发源单元203、移动机构204,从而控制由真空蒸镀装置200进行的成膜。
[0063]
真空蒸镀装置200还具有未图示的位置调整机构(对准机构),该位置调整机构使掩模保持器201和基板保持器202中的至少一方移动,进行保持于掩模保持器201的掩模m与保持于基板保持器202的基板s的位置对齐(对准)。本实施例的位置调整机构通过在与基板s的被成膜面大致平行的面内使基板保持器202进行xy移动和θ旋转,调整基板s相对于掩模m的相对位置。在此,xy方向是在与基板s的被成膜面平行的面内的不平行的2个方向,θ方向是绕与xy平面垂直的z方向的旋转方向。
[0064]
基板s以使被成膜面朝下的方式载置于保持为水平状态的掩模m的上表面。在掩模m的下方设置有放出蒸镀材料的蒸发源单元203。蒸发源单元203概略而言具备收纳蒸镀材料的容器(坩埚)、加热容器内的蒸镀材料的加热器等。另外,根据需要,也可以在蒸发源单元203设置用于提高加热效率的反射器或传热构件、挡板等。
[0065]
移动机构204是使蒸发源单元203与基板s的被成膜面平行地移动(扫描)的部件。在本实施例中,例示了使用了1轴的移动机构204的往复扫描方式,但根据蒸发源单元203的形状、基板s的尺寸,也可以是使用了2轴以上的移动机构的光栅扫描方式。另外,成膜速率根据基板s与蒸发源单元203的相对速度而变化,因此,也可以构成为使基板s在平面内相对于蒸发源单元203相对移动来代替使蒸发源单元203相对于基板s相对移动。
[0066]
此外,在本实施例中,将基板s载置于掩模m的上表面,但只要是基板s与掩模m充分
地紧贴的结构,则也可以不将基板s载置于掩模m的上表面。例如,也可以是使基板s紧贴于掩模m的下表面并使蒸镀材料从上方飞出的结构、或将紧贴的基板s和掩模m纵向(与z方向平行)配置的结构。另外,也可以使未图示的磁体单元靠近基板s的与被成膜面相反一侧的面,利用磁力吸引掩模m的掩模箔,提高掩模m向基板s的紧贴性。另外,可以设置冷却基板s的冷却单元,也可以由磁体单元兼用作该冷却单元。另外,蒸发源单元203也能够采用将多个蒸发源单元或容器排列配置并使它们作为一体进行移动的结构。根据这样的结构,能够在每个蒸发源单元或容器中收纳不同的材料并使其蒸发,能够形成混合膜、层叠膜。
[0067]
成膜速率监视器205是测定来自蒸发源单元203的蒸镀材料的放出量的监视部件。本实施例的成膜速率监视器205是晶体振荡式成膜速率监视器,与蒸发源单元203一起移动,具有配置于从蒸发源单元203放出的蒸镀材料会蒸镀(堆积)且不妨碍蒸镀材料到达基板s而形成薄膜的位置的晶体振子。根据在晶体振子上蒸镀的材料的量,晶体振子的谐振频率发生变化。成膜速率监视器205基于晶体振子的电极上的蒸镀材料的蒸镀量(膜厚或堆积的蒸镀材料的质量)与晶体振子的谐振频率(固有频率)的变化的关系,计算每单位时间的蒸镀材料的附着量即成膜速率(蒸镀速率)即,成膜速率监视器205测定每单位时间的晶体振子的谐振频率的变化,将与此对应的蒸镀材料的蒸镀量作为成膜速率输出。成膜速率是间接地表示来自蒸发源单元203的蒸镀材料的单位时间的放出量(放出速度)的量,在这个意义上,成膜速率监视器205是获取来自蒸发源单元203的蒸镀材料的放出量的测定值的监视部件的一例。
[0068]
图3是表示成膜速率监视器205的概略结构的图。成膜速率监视器205具备监视器头11、遮蔽构件12、晶体振子13(13a、13b)、晶体保持器14。
[0069]
监视器头11在其内部装入有晶体保持器14,该晶体保持器14对在圆周方向上等间隔地配置的多个晶体振子13(13a、13b)进行支承。在监视器头11设置有一个比晶体振子13稍大的监视器开口11a,设置于晶体保持器14的多个晶体振子中的1个(晶体振子13a)经由监视器开口11a暴露在外部(蒸发源单元203),其他晶体振子13b作为使用完或更换用的晶体振子隐藏在监视器头11的内部。晶体保持器14与未图示的伺服马达的马达轴16a连结,被驱动旋转。由此,能够依次切换经由监视器开口11a暴露在外部的晶体振子13。当经由监视器开口11a暴露在外部的晶体振子13的蒸镀材料400的蒸镀量超过规定量而晶体振子13达到寿命时,晶体保持器14旋转,使新的晶体振子13移动到与监视器开口11a重叠的位置。由此,晶体振子13构成为能够更换。
[0070]
遮蔽构件12是大致圆盘状的构件,其中心与未图示的伺服马达的马达轴15a连结,由伺服马达驱动旋转。在遮蔽构件12设置有扇型的开口狭缝12a,通过遮蔽构件12旋转,监视器头11的监视器开口11a与遮蔽构件12的开口狭缝12a重叠的状态和不重叠的状态交替变化。在监视器开口11a与开口狭缝12a重叠的状态下,容许蒸镀材料向晶体振子13a的蒸镀,在不重叠的状态下,通过遮蔽构件12中除了开口狭缝12a之外的部分即遮蔽部12b阻碍蒸镀材料400向晶体振子13a的蒸镀。
[0071]
《膜厚测定部》
[0072]
图4是示意性地表示通路室psx的结构的剖视图。图4表示图1的a-a线的截面。通路室psx是配置于单元cux的下游并被送入在单元cux的成膜室中完成了成膜的基板s的腔室。在通路室psx的真空腔室300内部配置有保持由输送机器人rcx输送来的基板s的基板托盘
301和测定基板s上的蒸镀材料的膜厚的膜厚测定部310。
[0073]
此外,也可以不在通路室psx配置膜厚测定部310,而设置用于膜厚测定的检查室。另外,也可以根据上游侧的集群型单元cux中的处理的内容来决定是否在通路室psx配置膜厚测定部310。例如,在单元cux形成发光层的情况下配置膜厚测定部310,在单元cux形成电极间层的情况下配置膜厚测定部310,在单元cux使用每个像素的精细掩模的情况下配置膜厚测定部310等。
[0074]
在图4中示出了1个膜厚测定部310,但也可以配置多个膜厚测定部。通过一次评价多个位置,能够得到基板面内的膜厚的偏差的信息、评价在多个成膜室成膜的多种蒸镀材料的膜厚。
[0075]
膜厚测定部310是光学地测定膜厚的传感器,在本实施例中,使用具有反射分光式的光学传感器的膜厚计。膜厚测定部310概略而言由膜厚评价单元311、传感器头312、以及将传感器头312和膜厚评价单元311连接的光纤313构成。传感器头312配置于真空腔室300内的基板托盘301的下方,经由安装于真空腔室300的底面的真空凸缘314而与光纤313连接。传感器头312具有将经由光纤313引导的光的照射区域设定为规定的区域的功能,能够使用光纤以及针孔、透镜等光学部件。
[0076]
图5是膜厚测定部310的框图。膜厚评价单元311具有光源320、分光器321、测定控制部322。光源320是输出测定光的设备,例如使用氘灯、氙灯、卤素灯等。作为光的波长,能够使用200nm~1μm的范围。分光器321是对从传感器头312输入的反射光进行分光并进行光谱(每个波长的强度)的测定的设备,例如由分光元件(光栅、棱镜等)和进行光电转换的检测器等构成。测定控制部322是进行光源320的控制和基于反射光谱的膜厚的计算等的设备。
[0077]
从光源320输出的测定光经由光纤313向传感器头312引导,从传感器头312向基板s投射。由基板s反射的光从传感器头312经由光纤313向分光器321输入。此时,由基板s上的薄膜的表面反射的光和由薄膜与其基底层的界面反射的光相互干涉。由于这样受到因薄膜导致的干涉、吸收的影响,从而反射光谱受到光程长度差、即膜厚的影响。通过利用测定控制部322分析该反射光谱,能够计算薄膜的膜厚。
[0078]
上述反射分光式的膜厚评价由于相对于几nm~几百nm的厚度的有机膜的评价,能够在短时间内进行高精度的评价,因此,是作为有机el元件的有机层的评价而言优选的方法。在此,作为有机层的材料,可列举出αnpd:α-萘基苯基联苯二胺等空穴传输材料、ir(ppy)3:铱-苯基嘧啶络合物等发光材料、alq3:三(8-羟基喹啉)铝、liq:8-羟基喹啉-锂等电子传输材料等。并且,也可以应用于上述有机材料的混合膜。分光干涉仪不需要马达,因此,在要求较高的真空度的蒸镀装置内也容易利用,具有能够在基板的附近进行测定的优点。但是,膜厚测定部310并不限定于此,也可以是椭圆偏振仪等。
[0079]
图6示出了用于使膜厚测定部310进行的测定变得容易的基板s的被成膜面侧的结构例。在该例的基板s的中央部设置有形成多个显示面板340的区域,在成膜完成后通过切分基板s来制作多个面板。在基板s的输送方向(箭头f)前方的、不与显示面板340区域重叠的区域设置有膜厚测定区域330。在各成膜室中的成膜处理时,与显示面板340的部分的成膜并行地,也进行膜厚测定区域330内的预先决定的位置的成膜,从而在膜厚测定区域330内形成膜厚测定用的薄膜(以后,称为测定用膜片331。有时也称为测定用片或评价用有机
膜)。这能够通过在各成膜室中使用的掩模m上预先形成用于测定用膜片331的开孔来实现。
[0080]
膜厚测定区域330设定为能够形成多个测定用膜片331的面积,可以按每个成为膜厚的测定对象的层来改变测定用膜片331的形成位置。即,可以在想要测定由1个成膜室形成的膜(可以是单一膜,也可以是多个膜层叠而成的层叠膜)的膜厚的情况下,在测定用膜片331的部分也仅形成由1个成膜室形成的膜,在想要测定经过多个成膜室形成的层叠膜的膜厚的情况下,在测定用膜片331的部分也形成与想要测定的层叠膜相同的层叠膜。通过这样按每个成为测定对象的层来使测定用膜片331不同,能够实现膜厚的准确的测定。为了形成这样的测定用膜片331,按每个成膜室使掩模m的开口部的位置不同即可。
[0081]
膜厚测定部310配置于在成膜室evx1~evx4中完成了成膜的基板s被输送机器人rcx输送的前方的通路室psx。膜厚测定部310能够根据测定用膜片331的形成方法,测定在成膜室evx1~evx4中成膜的膜厚或其中几个的合计。
[0082]
《成膜控制》
[0083]
由成膜速率监视器205输出的成膜速率的测定值(测定速率)有时与成膜中的基板s的实际的成膜速率(实际速率)不一致。其主要原因在于,相对于蒸发源单元203的成膜速率监视器205的晶体振子的位置与基板s的位置不同。为了消除该偏离,通常使用被称为工具因子(tf)的系数来修正由成膜速率监视器205输出的测定速率。
[0084]
然而,即使使用工具因子进行修正,测定速率与实际速率仍然有时会产生偏离。这是因为,蒸镀材料的蒸镀量与谐振频率的变化量的关系不是一定的,而是取决于谐振频率或蒸镀量而变化。通常,随着晶体振子上的蒸镀量增加,晶体振子的谐振频率减小。然后,晶体振子的谐振频率相对于一定的蒸镀量的变化量发生变化。换言之,即使晶体振子的谐振频率的变化量恒定,用于产生该变化量的成膜量也会根据此前堆积于晶体振子的蒸镀材料的总量而变化。因此,即使在晶体振子刚更换后测定速率与实际速率一致,测定速率与实际速率的偏离也会随着时间的经过而变大。
[0085]
另外,在晶体振子的谐振频率的变化量与蒸镀材料的蒸镀量的关系中存在因晶体振子的个体差异导致的偏差,因此,即使在某个晶体振子中测定速率与实际速率一致,在更换为其他晶体振子时测定速率与实际速率有时也会发生偏离。在使用根据成膜装置的结构而设定的常数作为工具因子的情况下,无法应对这样的晶体振子监视器的时效变化、个体差异所导致的偏差,因此,有可能无法通过基于测定速率的成膜控制而以所期望的精度进行成膜。
[0086]
因此,在本实施例的成膜装置中,进行图7的控制框图所示的控制。在图7中,在成膜室ev中进行基板s2的成膜。另外,在通路室ps中,进行在基板s2之前进行成膜并在成膜完成之后送入到通路室ps的基板s1的膜厚测定。基于由成膜速率监视器205得到的测定速率,通过成膜控制部206控制基板s1的成膜。成膜控制部206从膜厚测定部310获取基板s1的膜厚的测定值,基于基板s1的膜厚的测定值对基板s2的成膜控制进行校正。
[0087]
成膜速率监视器205设置于成膜室ev内,因此,测定速率能够在成膜中获取。相对于此,膜厚测定部310设置于成膜室ev的后段的通路室ps,只有在完成了成膜的基板s1送入到通路室ps之后才能够获取膜厚的测定值。因此,在基于成膜速率监视器205的测定速率的反馈控制中,反映此时进行的基板s2的成膜的信息,但在基于膜厚测定部310的膜厚的测定值的反馈控制中,反映在此以前进行的基板s1的成膜的信息。
[0088]
另外,为了使膜厚测定部310输出新的测定值,需要花费至少完成1张基板的成膜所需的时间,相对于此,成膜速率监视器205能够在短时间内输出新的测定值。在基于成膜速率监视器205的测定速率的反馈控制和基于膜厚测定部310的膜厚的测定值的反馈控制中,反馈新的测定值的频率大不相同。因此,在本实施例中,将膜厚测定部310的膜厚的测定值反馈给成膜控制这一动作表达为“校正”。意思是,虽然成膜速率监视器205的测定速率有时根据晶体振子的特性的时效变化而相对于实际速率产生偏离,但基于膜厚测定部310的膜厚的测定值来修正该偏离。
[0089]
基于成膜速率监视器205的测定速率进行的成膜控制部206的成膜控制通过以使测定速率接近目标值的方式控制真空蒸镀装置200的各种动作参数来进行。作为成为控制对象的真空蒸镀装置200的动作参数,例如有蒸发源单元203的加热器温度(加热器电流)、挡板开度、基于移动机构204的蒸发源单元203的扫描速度、成膜时间、扫描次数等。例如,若提高扫描速度,则成膜速率变小,若降低扫描速度,则成膜速率变大。若增加流过加热器的电流,则发热量增大,蒸镀材料的放出量增加,因此,成膜速率变大,若减小电流,则成膜速率变小。
[0090]
基于膜厚测定部310的膜厚的测定值进行的成膜控制的校正通过基于膜厚的测定值对成膜速率监视器205的测定速率进行修正来进行。该修正通过相对于晶体振子的谐振频率的变化量的规定单位量变更输出的成膜量的测定值来进行。具体而言,如下述的式(1)那样,通过对工具因子进行修正来进行测定速率的修正。
[0091]
[数1]
[0092][0093]rmes,cal
=tf
cal
×rmes
ꢀꢀꢀ
(2)
[0094]
在此,tfcal是修正后的工具因子,tforg是修正前的工具因子,thmes是膜厚测定部310的膜厚的测定值,thtrg是基板s的蒸镀材料的膜厚的目标值,rmes,cal是修正后的测定速率,rmes是修正前的测定速率。成膜控制部206基于使用修正后的工具因子tfcal利用式(2)计算出的修正后的测定速率rmes,cal对蒸发源单元203、移动机构204进行反馈控制,从而能够进行将晶体振子的谐振频率与蒸镀材料的蒸镀量的关系的时效变化考虑在内的成膜控制。
[0095]
例如,假设为了以目标膜厚进行蒸镀而以目标速率进行了100秒的蒸镀。即,以使成膜速率监视器205的测定速率接近的方式对蒸发源单元203、移动机构204进行反馈控制。工具因子tforg设为100%。假设利用膜厚测定部301测定成膜完成后的基板s的蒸镀材料的膜厚,结果,测定膜厚为在该情况下,意味着,成膜速率监视器205的测定速率为但实际速率为即,根据晶体振子的频率变化计算出的测定速率过大。根据上述式子,修正后的工具因子tfcal成为98%,根据晶体振子的频率变化计算的修正后的成膜速率为这样输出与实际速率相同的值。若
以该测定速率接近目标速率的方式进行蒸发源单元203、移动机构204的反馈控制,则例如会进行使蒸发源单元203的加热器温度上升的控制,作为结果,蒸镀量增加,能够使实际速率接近目标速率
[0096]
工具因子是表示晶体振子的谐振频率与晶体振子上的蒸镀材料的蒸镀量的关系的值,因此,工具因子的修正是晶体振子的谐振频率与晶体振子上的蒸镀材料的蒸镀量的关系的修正的一例。
[0097]
此外,基于膜厚测定部310的膜厚的测定值的成膜控制的校正也可以通过基于膜厚的测定值修正基于测定速率进行的真空蒸镀装置200的动作参数的调整量(控制量)来进行。例如,通过下述的式(3)对蒸发源单元203的加热器电流进行修正。
[0098]
[数2]
[0099][0100][0101]
在此,rmes是测定速率,rtrg是目标速率,iprev是通过基于测定速率的反馈控制进行调整之前的加热器电流,inew是通过基于测定速率的反馈控制进行调整之后的新的加热器电流,inew,cal是修正后的新的加热器电流。在不进行式(2)那样的测定速率的修正的情况下,通过基于测定速率的反馈控制进行调整后的新的电流值通过式(4)进行计算,因此,在如上述例子那样测定速率相对于实际速率过大的情况下,新的电流值与本来应有的值相比过小。通过如式(3)第1项那样基于膜厚的测定值对该新的电流值进行修正,新的电流值inew,cal成为本来应有的值。如式(3)第2项所示,这等价于使用通过式(2)进行了修正的测定速率对电流值进行反馈控制。
[0102]
此外,也可以将基于膜厚的测定值对成膜速率监视器205的测定速率进行修正和基于膜厚的测定值对真空蒸镀装置200的动作参数(例如加热器电流值)的调整量进行修正这两者组合。
[0103]
此外,在成膜装置具有多个集群型单元cux的情况下,膜厚测定部310也可以设置于各集群型单元cux的后段,但不一定需要在所有通路室psx配置膜厚测定部310。膜厚测定部310至少设置于位于生产线的最下游的集群型单元cux的后段的通路室psx即可。当仅在一部分集群型单元cux的后段设置膜厚测定部310的情况下,某个膜厚测定部310的测定结果能够用于位于比该膜厚测定部310靠上游侧的位置的集群型单元cux的成膜控制的校正。
[0104]
《进行校正的时机》
[0105]
参照图8,对基于膜厚测定部310的膜厚的测定值进行成膜控制的校正的时机的一例进行说明。图8是表示测定速率(
○
)、实际速率(
×
)、成膜中的基板上的实际膜厚(
△
)、工具因子(
□
)的时间变化的一例的图表。本实施例的成膜速率监视器205如图3所示具备多个晶体振子,在使用中的晶体振子13a达到寿命的情况下,使晶体保持器14旋转以使未使用的晶体振子13b暴露在外部,从而更换晶体振子。图8示出了每次更换晶体振子时进行成膜控
制的校正的例子。在图8的例子中,在更换了晶体振子之后,在适当的时机进行1次校正。在图8的例子中,在时刻t2进行晶体振子的更换(xtal chg),在时刻t1对更换前的晶体振子进行校正,在时刻t3对更换后的晶体振子进行校正。通过进行这样的校正,能够修正因晶体振子的个体差异而导致的测定速率的偏差。
[0106]
在图8的例子中,在时刻t1校正了测定速率之后的一段时间内,测定速率与实际速率一致。在时刻t1进行了一次校正之后,工具因子成为恒定值,因此,随着时间经过,测定速率与实际速率逐渐偏离。若在时刻t3对更换后的晶体振子进行校正,则在之后一段时间内,测定速率与实际速率一致,但随着时间经过而偏离。此外,在图8的例子中,示出了更换前的晶体振子与更换后的晶体振子的特性近似,几乎没有由校正导致的工具因子的值的变化的例子。
[0107]
参照图9,对基于膜厚测定部310的膜厚的测定值进行成膜控制的校正的时机的另一例进行说明。图9是表示测定速率(
○
)、实际速率(
×
)、成膜中的基板上的实际膜厚(
△
)、工具因子(
□
)的时间变化的一例的图表。图9示出了在更换了晶体振子之后到下次的更换为止的期间进行多次成膜控制的校正的例子。在图9的例子中,在更换了晶体振子之后,包含适当的时机在内定期地进行校正。也可以不定期地进行多次校正。在图9的例子中,在时刻t6进行晶体振子的更换(xtal chg),在时刻t1、t2、t3、t4、t5对更换前的晶体振子进行校正,在时刻t7、t8对更换后的晶体振子进行校正。通过进行这样的校正,能够修正因晶体振子的个体差异导致的测定速率的偏差,并且,能够修正因晶体振子的时效变化导致的测定速率与实际速率的偏离。
[0108]
在图9的例子中,在时刻t1~t5,工具因子被逐渐修正为较小的值。由此,能够抑制如图8的情况那样测定速率逐渐相对于实际速率变得过大,能够维持测定速率与实际速率精度良好地一致的状态。因此,实际膜厚不会如图8那样偏离目标值,能够精度良好地进行成膜。
[0109]
《晶体振子刚更换后的控制》
[0110]
图10是表示刚更换晶体振子之后的测定速率与工具因子的变化的示意图。实线表示测定速率,单点划线表示工具因子。在时刻t1,更换晶体振子,在刚更换晶体振子之后,成膜速率监视器205的输出不稳定,但不久(时刻t2)输出稳定。之后,在基于使用更换后的晶体振子输出的测定速率初次进行的成膜完成而得到膜厚测定部310的膜厚的测定值之前(时刻t3),无法进行基于膜厚的测定值的成膜控制的校正。
[0111]
在晶体振子刚更换后的成膜控制中,在到初次得到膜厚的测定值为止的期间(时刻t1~t3),使用在对更换前的晶体振子进行的第1次校正中得到的工具因子tf1,first。即,沿用在更换晶体振子之前进行的成膜控制的校正的结果。如图9所示,工具因子随着时间经过而被修正为较小的值,因此,在第1次校正中得到的工具因子tf1,first是比即将更换之前的工具因子tf1,last大的值。因晶体振子的个体差异导致的测定速率的偏差比因晶体振子的时效变化导致的测定速率的偏差小,因此,即使沿用更换前的晶体振子的工具因子,也不会产生较大的误差。
[0112]
另外,在晶体振子刚更换后的成膜控制中,在到初次得到膜厚的测定值为止的期间(时刻t1~t3),也可以将成膜速率监视器205的输出稳定时的测定速率(时刻t2的测定速率r2)作为成膜速率的目标值进行成膜控制。如图10所示,稳定时的测定速率有时也相对于
本来的目标速率r1偏离,但由于在该时间点未进行工具因子的校正,因此,测定速率r2不一定表示实际速率。另一方面,若即使更换晶体振子而成膜控制(加热器温度等)也没有变更,则能够假定实际速率维持晶体振子更换前的值。因此,将稳定时的测定速率r2作为目标值进行成膜控制(将目标速率从r1变更到r2)。或者,考虑虽然本来应输出的测定速率是r1,但成膜速率监视器205输出了r2,也可以基于稳定时的测定速率r2和目标速率r1来修正工具因子。
[0113]
[实施例2]
[0114]
在此,说明对不是集群型的电子器件制造装置应用本发明的应用例。图11示出了对本实施例的电子器件制造装置的一部分进行校正、且是一边输送对准并紧贴的基板s和掩模m一边进行成膜的直列型的成膜装置。
[0115]
成膜装置300具有掩模送入室90、对准室100(掩模安装室)、多个成膜室110a和110b、翻转室111a和111b、输送室112、掩模分离室113、基板分离室114、载体输送室115、掩模输送室116、基板送入室117(基板安装室)以及膜厚测定室118的各腔室。保持于基板载体9的基板s沿着虚线所示的路径,掩模m沿着点线所示的路径在各腔室内输送。
[0116]
在基板送入室117中保持于基板载体9并被送入到虚线的路径的基板s在翻转室111a中通过翻转机构120a翻转姿势,在掩模送入室90中搭载于掩模m。然后,当在对准室100中进行了基板s与掩模m的对准和紧贴之后,一边在成膜室110a、110b输送,一边接受从设置于成膜室的蒸发源单元203(参照图2)放出的蒸镀材料的成膜。此外,在基板载体安装有成膜速率监视器205。因此,放出的蒸镀材料附着于基板s的被成膜面的同时也附着于成膜速率监视器205。由此,测定成膜中的成膜速率。另外,在设置于成膜室110a和110b的中途的膜厚测定室118配置有进行光学的膜厚测定的膜厚测定部310,使基板载体9暂时停止,测定成膜室110a中的成膜完成后的基板s的蒸镀材料的膜厚。
[0117]
接下来,保持于基板载体的基板s向输送室112送入。在输送室112也配置有膜厚测定部310,测定成膜室110b中的成膜完成后的基板s的蒸镀材料的膜厚。然后,基板s在掩模分离室113中分离了掩模m之后,在翻转室111b中通过翻转机构120b翻转姿势,在基板分离室114中从基板载体9分离,向成膜装置300的外部送出。另一方面,基板载体9经过载体输送室115向基板送入室117输送,保持下一个基板s。
[0118]
另外,成膜装置300具备成膜控制部206。在具有本实施例的结构的成膜装置300中,搭载于基板载体9的成膜速率监视器205测定成膜中的成膜速率,膜厚测定部310光学地测定完成了成膜的基板上的蒸镀材料的膜厚。成膜控制部206通过基于成膜速率的测定值来调整基板载体9的输送速度,控制配置于成膜室内的蒸发源单元203与基板s的相对速度,并且,通过控制向蒸发源单元203投入的电流来控制蒸镀材料的蒸镀量。成膜控制部206基于膜厚测定部310的膜厚的测定值对这样的成膜控制进行校正。因此,根据与上述实施例同样的原理,能够进行精度良好的成膜控制。
[0119]
[实施例3]
[0120]
(有机电子器件的制造方法)
[0121]
在本实施例中,说明使用了成膜装置的有机电子器件的制造方法的一例。以下,作为有机电子器件的例子,例示有机el显示装置的结构和制造方法。首先,说明要制造的有机el显示装置。图12的(a)表示有机el显示装置50的整体图,图12的(b)表示一个像素的截面
构造。
[0122]
如图12的(a)所示,在有机el显示装置50的显示区域51,具备多个发光元件的像素52呈矩阵状配置有多个。发光元件分别具有具备夹在一对电极之间的有机层的构造。此外,在此所说的像素是指能够在显示区域51显示所期望的颜色的最小单位。在本图的有机el显示装置的情况下,由显示相互不同的发光的第1发光元件52r、第2发光元件52g、第3发光元件52b的组合构成像素52。像素52往往由红色发光元件、绿色发光元件以及蓝色发光元件的组合构成,但也可以是黄色发光元件、青色发光元件以及白色发光元件的组合,只要是至少1种颜色以上,就没有特别限制。
[0123]
图12的(b)是图12的(a)的a-b线的局部剖视示意图。像素52具有在基板53上具备第1电极(阳极)54、空穴传输层55、发光层56r、56g、56b中的任一个、电子传输层57、第2电极(阴极)58的有机el元件。其中,空穴传输层55、发光层56r、56g、56b、电子传输层57相当于有机层。另外,在本实施例中,发光层56r是发出红色的有机el层,发光层56g是发出绿色的有机el层,发光层56b是发出蓝色的有机el层。
[0124]
发光层56r、56g、56b分别形成为与发出红色、绿色、蓝色的发光元件(也有时记述为有机el元件)对应的图案。另外,第1电极54按每个发光元件分离地形成。空穴传输层55、电子传输层57以及第2电极58可以与多个发光元件52r、52g、52b共通地形成,也可以按每个发光元件形成。此外,为了防止第1电极54和第2电极58因异物而短路,在第1电极54之间设置有绝缘层59。并且,由于有机el层因水分、氧而劣化,因此,设置有用于保护有机el元件免受水分、氧的影响的保护层60。
[0125]
下面,具体说明作为电子器件的有机el显示装置的制造方法的例子。首先,准备形成有用于驱动有机el显示装置的电路(未图示)和第1电极54的基板53。
[0126]
接下来,在形成有第1电极54的基板53上通过旋涂形成丙烯酸树脂,通过光刻法以在形成有第1电极54的部分形成开口的方式对丙烯酸树脂进行图案化,形成绝缘层59。该开口部相当于发光元件实际发光的发光区域。
[0127]
接下来,将绝缘层59形成图案的基板53向第1成膜装置送入,通过基板支承单元支承基板,将空穴传输层55作为共通的层在显示区域的第1电极54上成膜。空穴传输层55通过真空蒸镀进行成膜。实际上,空穴传输层55形成为比显示区域51大的尺寸,因此,不需要高精细的掩模。在此,本步骤中的成膜、在以下的各层的成膜中使用的成膜装置是上述各实施例的任一个记载的成膜装置。
[0128]
接下来,将形成至空穴传输层55的基板53向第2成膜装置送入,通过基板支承单元进行支承。进行基板与掩模的对准,将基板载置于掩模上,在基板53的配置发出红色的元件的部分形成发出红色的发光层56r。根据本例,能够使掩模与基板良好地重合,能够进行高精度的成膜。
[0129]
与发光层56r的成膜同样地,通过第3成膜装置形成发出绿色的发光层56g,然后通过第4成膜装置形成发出蓝色的发光层56b。在发光层56r、56g、56b的成膜完成之后,通过第5成膜装置在整个显示区域51对电子传输层57进行成膜。电子传输层57作为共通的层形成于3色的发光层56r、56g、56b。
[0130]
将形成至电子传输层57的基板向溅射装置移动,对第2电极58进行成膜,之后移动到等离子cvd装置,对保护层60进行成膜,完成有机el显示装置50。
[0131]
从将绝缘层59形成图案的基板53送入成膜装置到保护层60的成膜完成为止,若暴露在包含水分、氧的气氛中,则由有机el材料构成的发光层有可能因水分、氧而劣化。因而,在本例中,成膜装置之间的基板的送入送出在真空环境或非活性气体气氛下进行。
[0132]
本公开的膜厚测定方法、使用了膜厚的成膜控制方法能够优选利用于以发光层为首的上述各层的形成。结果,能够实现提高了对基板的成膜工艺中的膜厚的测定和控制的精度的良好的成膜控制。