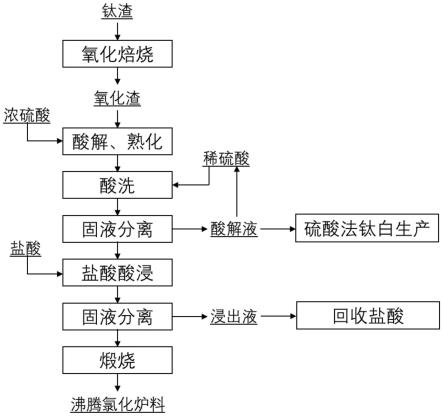
1.本发明属于钛资源利用技术领域,涉及一种钛渣升级制备沸腾氯化炉料的方法,具体涉及一种钛渣深度除杂制备沸腾氯化炉料的方法。
背景技术:2.目前钛工业的主要产品有钛白粉和钛合金,钛白粉的生产方法有硫酸法和氯化法,钛合金的主要原料海绵钛主要由氯化法-克劳尔法生产,硫酸法钛白粉属中低端钛产品,氯化法钛白粉和海绵钛属高端钛产品。我国85%以上钛原料用来生产中低端的硫酸法钛白粉,硫酸法生产过程中产生大量废酸和绿矾,造成严重环境污染。氯化法主要有沸腾氯化法和熔盐氯化法两类,沸腾氯化法要求原料中tio2》90%,(cao+mgo)《1.5%,一般采用高品质富钛料作为沸腾氯化原料;熔盐氯化法虽对原料杂质含量无明确要求,但原料中杂质含量过高会导致氯化废渣量大,废熔盐量增加,一般采用tio2含量大于85%的富钛料作为原料。
3.我国90%以上钛资源以钒钛磁铁矿的形式赋存在四川攀西地区,其中钙镁杂质含量高,经磨选后可获得钒钛磁铁精矿和钛铁矿两种含钛产品,钒钛磁铁精矿目前仅能通过高炉法回收其中的铁和钒,钛赋存在高炉钛渣中难以提取利用。钛铁矿经电炉冶炼可获得铁水和钛渣,钛渣中tio2含量在72%左右,并含有大量的钙、镁杂质,目前主要用作硫酸法钛白粉原料,导致我国钛资源利用水平低。钛渣中主要矿物有黑钛石及少量硅酸盐,钛渣中部分铁、镁、铝杂质分布在黑钛石中,钙、硅及其余镁、铁、铝杂质分布在硅酸盐中,杂质元素赋存状态复杂,难以脱除,不能直接用作氯化法原料。
4.因此需开发一种钛渣深度除杂制备沸腾氯化炉料的方法,提高我国攀西地区钛资源的利用水平。
技术实现要素:5.针对钛铁矿电炉冶炼钛渣中杂质含量高、赋存状态复杂,难以用作氯化法原料的问题,本发明的目的在于提供一种钛渣升级制备沸腾氯化炉料的方法,该工艺流程设计合理、操作简单、无环境污染。
6.本发明提供以下技术方案:一种钛渣升级制备沸腾氯化炉料的方法,包括以下步骤:
7.s1.将钛渣进行氧化焙烧反应,得到氧化焙烧产物;
8.s2.将步骤s1所得氧化焙烧产物破碎,得到预定细度的氧化焙烧钛渣;
9.s3.将步骤s2所得氧化焙烧钛渣进行硫酸酸解反应,将酸解后的料浆进行固液分离,得到酸解液和酸解渣,酸解液可返回酸洗工序反复使用,至钛含量超过120g/l时用作硫酸法钛白生产,酸解渣进行深度除杂;
10.s4.将步骤s3所得酸解渣进行盐酸浸出反应,将浸出后的料浆进行固液分离,获得浸出渣和浸出液;
11.s5.将步骤s4所得浸出渣进行煅烧,得到所述沸腾氯化炉料。
12.所述的氧化焙烧反应中,钛渣中的部分黑钛石转变为稳定的金红石,并且金红石颗粒粒度聚集长大,氧化焙烧后钛渣中物相主要有金红石、黑钛石、硅酸盐。
13.所述的硫酸酸解反应中,氧化焙烧钛渣中金红石稳定不被酸解,氧化焙烧过程未转化的黑钛石被酸解,其中的钛、铁、镁、铝杂质进入酸解液中,部分硅酸盐也被酸解,其中钙、硅等元素进入酸解液中,剩余钙以硫酸钙、硅以偏硅酸的形式存在于酸解渣中。
14.所述的盐酸浸出反应中,剩余硅酸盐也被分解,其中钙、硅等元素进入酸解液中,硫酸钙被分解后钙元素进入浸出液中,浸出液经除杂浓缩后回收盐酸循环利用。
15.优选的方案,步骤s1中,所述的钛渣中tio2含量大于70%。
16.优选的方案,步骤s1中,氧化温度为1000~1600℃,氧化时间为10~180min。
17.优选的方案,步骤s2中,破碎至颗粒粒度小于0.5mm占80%以上。
18.优选的方案,步骤s3中,向细磨后的氧化焙烧钛渣中加入浓硫酸进行酸解,然后依次进行熟化、酸洗处理,将酸解后的料浆进行固液分离,得到酸解液和酸解渣。
19.进一步,步骤s3中,所述浓硫酸的浓度为90~98.3wt%,酸渣比为0.5:1~3:1。
20.进一步,步骤s3中,熟化温度为150~330℃,熟化时间为10~180min。
21.进一步,步骤s3中,熟化后进行硫酸酸洗,酸洗用稀硫酸浓度为5~50wt%,酸洗液固比为0~20:1,酸洗温度为20~100℃,酸洗时间为10~180min。
22.优选的方案,步骤s4中,所述盐酸的浓度为5~30wt%,酸浸液固比为0~20:1,酸浸温度为20~200℃,酸浸时间为0.5~8h。
23.优选的方案,步骤s4中,回收浸出液中的盐酸。
24.优选的方案,步骤s5中,所述的煅烧温度为200~1000℃,煅烧时间为10~180min。
25.本发明技术方案的原理为:
26.本发明的氧化焙烧过程目的为将黑钛石中低价钛氧化物和铁氧化物转化为金红石相和高价铁氧化物,并促使金红石相长大,氧化焙烧渣中主要物相为金红石、黑钛石和少量的硅酸盐。钛渣氧化焙烧过程发生的反应:
27.2ti3o
5(s)
+o
2(g)
=6tio
2(s)
ꢀꢀꢀꢀꢀꢀꢀꢀꢀꢀꢀꢀꢀꢀꢀꢀꢀꢀꢀꢀꢀꢀꢀꢀꢀꢀꢀꢀꢀꢀꢀꢀꢀꢀꢀꢀꢀꢀꢀꢀꢀꢀꢀ
(1)
28.4feti2o
5(s)
+o
2(g)
=2fe2tio
5(s)
+6tio
2(s)
ꢀꢀꢀꢀꢀꢀꢀꢀꢀꢀꢀꢀꢀꢀꢀꢀꢀꢀꢀꢀꢀꢀꢀꢀꢀꢀꢀꢀꢀꢀꢀ
(2)
29.本发明的硫酸酸解过程目的为将氧化钛渣中的黑钛石和部分硅酸盐酸解,使其转变为可溶的含钛、镁、铝的离子,氧化钛渣中金红石相稳定,不会发生酸解反应,达到脱除镁、铁、铝及部分钙、硅杂质的目的。氧化钛渣硫酸酸解过程发生的化学反应:
30.fe2tio
5(s)
+4h2so
4(l)
=2fe
3+(aq)
+tio
2+(aq)
+4so
42-(aq)
+4h2o
(aq)
ꢀꢀꢀꢀꢀꢀꢀꢀꢀꢀꢀꢀꢀ
(3)
31.al2tio
5(s)
+4h2so
4(l)
=2al
3+(aq)
+tio
2+(aq)
+4so
42-(aq)
+4h2o
(aq)
ꢀꢀꢀꢀꢀꢀꢀꢀꢀꢀꢀꢀꢀ
(4)
32.mgti2o
5(s)
+3h2so
4(l)
=mg
2+(aq)
+2tio
2+(aq)
+3so
42-(aq)
+3h2o
(aq)
ꢀꢀꢀꢀꢀꢀꢀꢀꢀꢀꢀ
(5)
33.casio
3(s)
+h2so
4(l)
=caso
4(s)
+h2sio
3(s)
ꢀꢀꢀꢀꢀꢀꢀꢀꢀꢀꢀꢀꢀꢀꢀꢀꢀꢀꢀꢀꢀꢀꢀꢀꢀꢀꢀꢀꢀꢀꢀ
(6)
34.本发明的盐酸酸浸过程的目的为将未酸解的硅酸盐以及硫酸酸解过程生成的硫酸钙进一步分解,使其中含有的钙杂质元素转变为可溶的氯化钙,达到深度脱除钙、硅杂质的目的。酸解渣盐酸酸浸反应:
35.casio
3(s)
+2hcl
(aq)
=cacl
2(aq)
+h2sio
3(aq)
ꢀꢀꢀꢀꢀꢀꢀꢀꢀꢀꢀꢀꢀꢀꢀꢀꢀꢀꢀꢀꢀꢀꢀꢀꢀꢀꢀꢀꢀꢀꢀꢀ
(7)
36.caso
4(s)
+2hcl
(aq)
=cacl
2(aq)
+h2so
4(aq)
ꢀꢀꢀꢀꢀꢀꢀꢀꢀꢀꢀꢀꢀꢀꢀꢀꢀꢀꢀꢀꢀꢀꢀꢀꢀꢀꢀꢀꢀꢀꢀ
(8)
37.本发明的有益技术效果:
38.本发明可以有效提高钛渣tio2品位,降低钛渣中杂质元素含量,特别是钙、镁杂质,实现钛渣脱除钙、镁、铁、铝、硅,升级成沸腾氯化炉料的目的,成为氯化法原料;并且硫酸酸解液可作为硫酸法钛白原料,实现钛的有效回收;盐酸浸出液通过除杂浓缩后可循环利用。该工艺流程设计合理,操作简单,无环境污染。
附图说明
39.图1为本发明实施例1的工艺流程图。
具体实施方式
40.下面通过实施例来进一步说明本发明的具体实施方式,但本发明的具体实施方式不局限于以下实施例。
41.在本发明实施例中,如无特别说明,采用的手段均为本领域常规的手段,采用的试剂均可通过常规的商业途径获取。
42.以下通过具体实施例和附图对本发明技术方案进行详细的阐述。
43.实施例1
44.以含钛炉渣(72.52%tio2、9.35%tfe、5.39%sio2、2.75%al2o3、1.38%cao、8.25%mgo)为原料,氧化焙烧过程温度为1450℃,氧化时间为120min。将氧化焙烧产物破碎至粒度为-0.5mm占84.25%。硫酸酸解过程硫酸浓度为92%,酸渣比为1.7:1,熟化温度为250℃,熟化时间为120min,熟化后进行硫酸酸洗,酸洗用硫酸浓度为20%,酸洗液固比为5:1,酸洗温度为60℃,酸洗时间为120min。酸洗后过滤所得酸解渣用盐酸酸浸,盐酸浓度为15%,酸浸液固比为8:1,酸浸温度为120℃,酸浸时间为4h。盐酸酸浸后固液分离获得的浸出渣煅烧过程中煅烧温度为900℃,煅烧时间为30min。
45.实施例1最终获得tio2为89%,cao为0.35%,mgo为0.55%的沸腾氯化炉料,杂质镁、铁、钙、硅的总脱除率可达91.33%,89.67%,81.96%,42.77%。具体工艺流程如图1所示。
46.实施例2
47.以含钛炉渣(74.46%tio2、8.84%tfe、9.69%sio2、0.72%al2o3、1.94%cao、6.61%mgo)为原料,氧化焙烧过程温度为1500℃,氧化时间为120min。将氧化焙烧产物破碎至粒度为-0.5mm占82.13%。硫酸酸解过程硫酸浓度为92%,酸渣比为2:1,熟化温度为250℃,熟化时间为120min,熟化后进行硫酸酸洗,酸洗用硫酸浓度为30%,酸洗液固比为10:1,酸洗温度为60℃,酸洗时间为120min。酸洗后过滤所得酸解渣用盐酸酸浸,盐酸浓度为15%,酸浸液固比为10:1,酸浸温度为120℃,酸浸时间为4h。盐酸酸浸后固液分离获得的浸出渣煅烧过程中煅烧温度为900℃,煅烧时间为30min。
48.实施例2最终获得tio2为91.3%,cao为0.15%,mgo为0.32%的沸腾氯化炉料,杂质镁、铁、钙、硅的总脱除率可达93.45%,91.21%,86.46%,46.74%。
49.实施例3
50.以含钛炉渣(72.43%tio2、8.84%tfe、7.39%sio2、2.55%al2o3、0.86%cao、3.12%mgo)为原料,氧化焙烧过程温度为1500℃,氧化时间为120min。将氧化焙烧产物破碎
至粒度为-0.5mm占81.68%。硫酸酸解过程硫酸浓度为94%,酸渣比为2:1,熟化温度为300℃,熟化时间为120min,熟化后进行硫酸酸洗,酸洗用硫酸浓度为20%,酸洗液固比为5:1,酸洗温度为60℃,酸洗时间为120min。酸洗后过滤所得酸解渣用盐酸酸浸,盐酸浓度为10%,酸浸液固比为10:1,酸浸温度为120℃,酸浸时间为4h。盐酸酸浸后固液分离获得的浸出渣煅烧过程中煅烧温度为900℃,煅烧时间为30min。
51.实施例3最终获得tio2为94.13%,cao为0.12%,mgo为0.23%的沸腾氯化炉料,杂质镁、铁、钙、硅的总脱除率可达94.12%,90.13%,87.86%,43.14%。
52.对比例1
53.以含钛炉渣(72.52%tio2、9.35%tfe、5.39%sio2、2.75%al2o3、1.38%cao、8.25%mgo)为原料,氧化焙烧过程温度为1450℃,氧化时间为120min。将氧化焙烧产物破碎至粒度为-0.5mm占84.25%。硫酸酸解过程硫酸浓度为92%,酸渣比为1.7:1,熟化温度为250℃,熟化时间为120min,熟化后进行硫酸酸洗,酸洗用硫酸浓度为30%,酸洗液固比为5:1,酸洗温度为60℃,酸洗时间为120min。固液分离获得的浸出渣煅烧过程中煅烧温度为900℃,煅烧时间为30min。最终煅烧渣tio2为71.05%,cao为3.44%,mgo为0.90%。
54.对比例2
55.以含钛炉渣(72.52%tio2、9.35%tfe、5.39%sio2、2.75%al2o3、1.38%cao、8.25%mgo)为原料,氧化焙烧过程温度为1450℃,氧化时间为120min。将氧化焙烧产物破碎至粒度为-0.5mm占84.25%。盐酸浓度为36.5%,酸浸液固比为10:1,酸浸温度为120℃,酸浸时间为4h。盐酸酸浸后固液分离获得的浸出渣煅烧过程中煅烧温度为900℃,煅烧时间为30min。最终煅烧渣tio2为81.59%,cao为1.71%,mgo含量为0.65%。
56.以上所述仅是本发明的优选实施方式,本发明的保护范围并不仅局限于上述实施例。对于本技术领域的技术人员来说,在不脱离本发明技术构思前提下所得到的改进和变换也应视为本发明的保护范围。