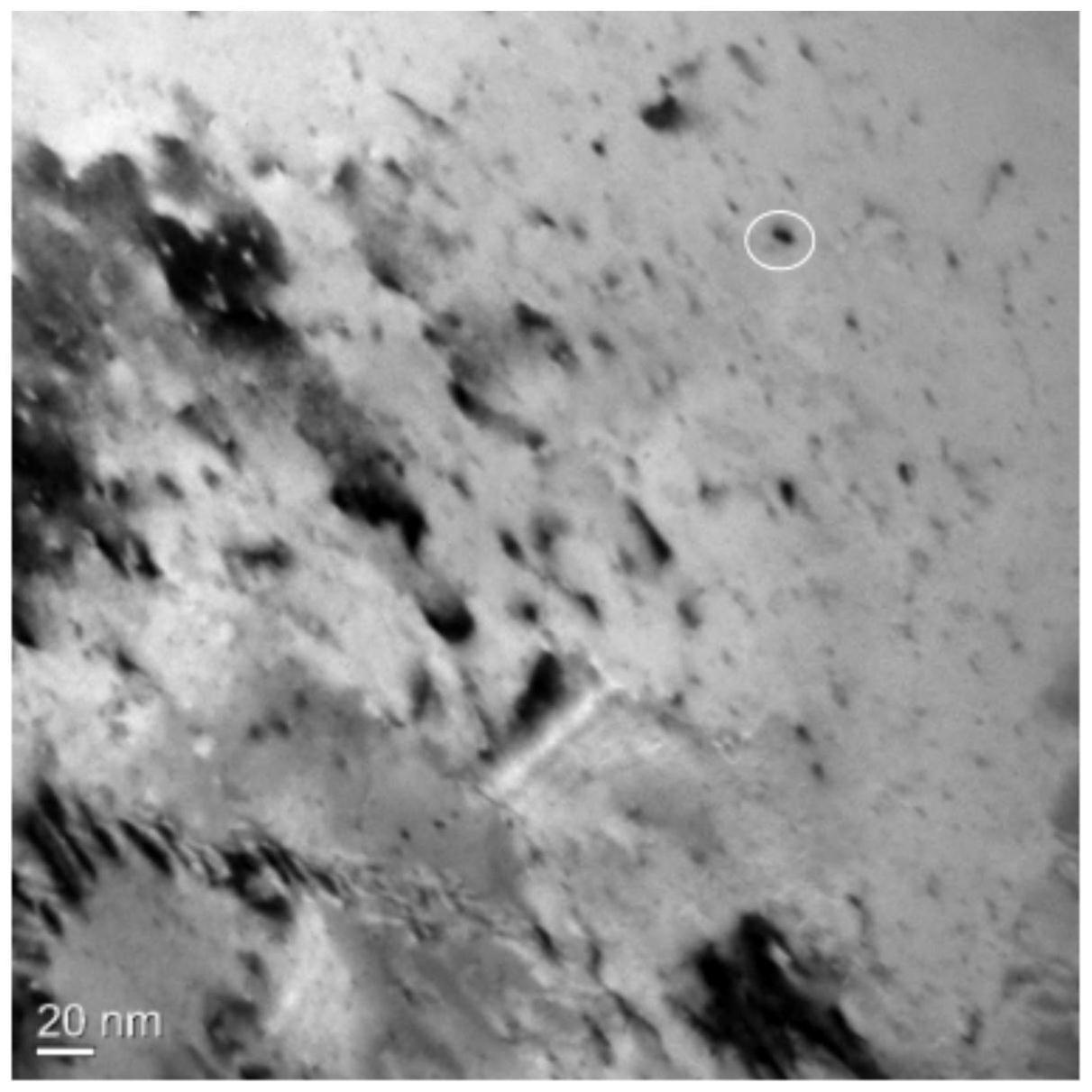
cu-zn-cr-zr-fe-si系合金及其制备方法
技术领域
1.本发明属于合金制备技术领域,具体涉及cu-zn-cr-zr-fe-si系合金及其制备方法。
背景技术:2.cu-cr-zr系合金具有良好的导电性、导热性、耐磨性和适中的强度,在5g通讯、高端集成电路等现代信息产业以及轨道交通、先进武器等高端制造业具有广泛的应用。相关技术中,大部分cu-cr-zr系铜合金的抗拉强度为500~600mpa,导电率70~85%iacs。随着上述高新技术产业的快速发展,对合金的使用要求越来越高。以集成电路引线框架为例,随着集成电路向极大规模化方向发展,引线框架向多脚化、高密度化、超薄化、微型化等方向发展,除了要求铜合金具有较高的强度和导电率以外,还要求具有高抗软化温度、低残余应力、易焊接、良好的蚀刻性能等,现有的cu-cr-zr系合金难以满足制造高端集成电路引线框架的要求。
3.cn1254554c公开了一种高强高导稀土铜合金及其制备方法。该技术采用添加稀土元素提高合金的力学性能,所制备合金的抗拉强度仅为500~600mpa,导电率为70~80%iacs。cn108060323b公开了一种高强高导cu-cr-zr-mg系合金丝材及其制备方法,该技术所制备合金丝材的抗拉强度为760mpa,导电率为84.7%iacs,成分组成:cr 1.5%,zr 0.1%,mg 0.05%,余量为cu和不可避免的杂质。该技术中cr含量较高,为1.5~15.0wt%,由于室温下铜基体中的cr固溶度极低,在1070℃铬在铜合金的最大固溶度为0.65%,通过大变形拉拔加工使铜基体中形成的大量的纤维状cr相颗粒强化了合金丝材。但是,第一方面,对于工业应用量大的cu-cr-zr-mg系合金板带材,通过大变形热轧和冷轧加工,使铜基体中cr相以层片状形式存在,强化效果较弱,合金的强度较低;第二方面,较高的cr含量(>1wt%),容易在铜基体中形成粗大的cr相颗粒,由于cr相和铜基体变形行为的差异较大,会导致加工后合金中的残余应力较大,合金的带型、尺寸精度控制难度大,微区腐蚀不均匀现象严重,无法满足制造集成电路引线框架的要求;第三方面,添加较高cr含量使合金的原材料成本增加。因此,仍需开发高强度、高导电、高抗软化温度、低残余应力的新合金。
技术实现要素:4.本发明旨在至少解决现有技术中存在的上述技术问题之一。为此,本发明提供了一种cu-zn-cr-zr-fe-si系合金,该合金实现了多相协同强化、应变强化、亚晶强化和固溶强化等综合作用,具有高强度、高导电、高抗软化温度和低残余应力的特点。
5.本发明还提供了制备cu-zn-cr-zr-fe-si系合金的方法。
6.本发明的第一方面提供了cu-zn-cr-zr-fe-si系合金,以质量百分比计,包括以下组分:
7.zn:0.1wt%~1.00wt%,
8.cr:0.01wt%~1.00wt%,
9.zr:0.10wt%~0.60wt%,
10.fe:0.05wt%~1.00wt%,
11.si:0.05wt%~1.00wt%,
12.余量为铜。
13.本发明关于cu-zn-cr-zr-fe-si系合金的技术方案中的一个技术方案,至少具有以下有益效果:
14.本发明的cu-zn-cr-zr-fe-si系合金,硬度为180~250hv,抗拉强度为600~750mpa,屈服强度为550~700mpa,弹性模量为125~135mpa,伸长率为3~10%,导电率为70~85%iacs,耐热温度≥580℃,残余应力≤30mpa,解决了现有cu-cr-zr合金的强度、导电性能、抗软化性能、低残余应力难以兼顾和匹配的问题。
15.本发明的cu-zn-cr-zr-fe-si系合金,可满足极大规模集成电路、5g通讯、高端电子元件等现代信息产业以及轨道交通快速发展对高性能合金的需求。
16.本发明的cu-zn-cr-zr-fe-si系合金,通过添加合金元素,在铜基体中引入多种强化相,使合金元素以高硬度、高耐热的纳米级fesi和cr相颗粒充分弥散析出,强化析出相颗粒和位错之间的交互作用,实现了多相协同弥散强化、应变强化、亚晶强化和固溶强化等综合强化作用,同时提高了铜合金的强度和导电率。
17.本发明的cu-zn-cr-zr-fe-si系合金,通过合理控制zn和zr的含量和配比,一方面利用zn元素的固溶作用强化铜基体,减小合金的残余应力和提高蚀刻性能,另一方面在铜基中形成耐热稳定性好的cu3zr相,同时发挥添加zn促进纳米级cr相颗粒弥散析出和较大固溶强化作用,同时结合制备工艺的调控,使亚微米级cu3zr、cr2si相在晶界断续分布,能有效钉扎高温条件下位错和晶界的运动,在确保铜合金高强度和高导电的基础上,大幅度提高铜合金的耐高温软化。
18.本发明的cu-zn-cr-zr-fe-si系合金中:
19.zn、fe、si的价格低廉,将其加入到铜合金中,通过加工和热处理工艺的调控,能够显著提高铜合金的力学性能,同时对导电率的影响较小。本发明利用zn元素在铜基体中固溶度较大,具有明显的固溶强化作用,可有效提高铜合金基体的强度,缩小了铜基体与析出相之间的强度和硬度,有利于减小铜合金后续加工过程中产生的残余应力。同时,通过添加zn元素可调控铜基体的电极电位,有利于提高铜合金的蚀刻性能。
20.本发明利用fe与si具有较强的结合能,形成高硬度、高耐热的fe-si相。另外,fe-si相的析出能力强于fe相,促进了基体中fe原子的析出。因此,添加贱金属fe元素与si结合,形成硬质fe-si相代替cr相,可解决现有cu-cr-zr系合金仅依靠cr相析出强化导致强度不足的问题,无论是在原料成本还是在使用性能提升方面都意义重大。
21.fe元素和si元素所能形成的析出相包括fesi、β-fesi2、α-fesi2、fe2si、fe5si3、fe
11
si5、fe3si。其中fesi相具有最大的剪切模量和杨氏模量,这表明fesi相的抗变形能力最强,硬度最大,强化效果最好。此外,与fe相比,fesi相具有更小的泊松比,其泊松比为0.21(低于0.25),表明fesi相是一种硬质脆性相。较高的脆性使fesi初生相在冷加工过程中更容易破碎,并在后续热处理过程中以细小弥散的粒子分布在基体中,有助于提高合金的弥散强化效果。因此fe和si元素的含量和配比非常重要。合金导电率主要受基体中溶质原子对电子散射效应的影响,因此随着微量元素的析出,合金的导电率显著提高。为了使合
金的强度和导电率协同提升,必须尽可能使溶解在基体中的si、fe元素分别以fesi相的形式析出。
22.此外,本发明cu-zn-cr-zr-fe-si系合金的关键点还包括合理调控zn、cr、zr、fe、si等元素含量和配比,适当提高cr、fe和si的含量,通过目标析出相如cr、cr2si、fesi等的质量比,得到合金中各元素含量的上下限,并结合cr-si和fe-si相图,定向设计合金成分。
23.若zn含量太少,一方面合金的固溶强化效果较小,另一方面,对调控合金残余应力和蚀刻性能的作用不明显;若zn含量太大,则明显降低合金的导电率。若cr含量太少,时效后析出的cr相数量较少,析出强化效果不明显,合金的强度较低;若cr含量太多,容易在铜基体中形成粗大的cr相颗粒,cr相强化效果较低,同时由于cr相和铜基体变形行为的差异较大,导致加工后合金中的残余应力较大,合金的带型、尺寸精度控制难度大,特别是制造蚀刻引线框架时,微区腐蚀不均匀现象严重,无法满足制造集成电路引线框架的要求;另外,添加较高cr含量使合金的原材料成本增加。
24.若fe含量太少,合金中形成的fesi相数量较少,析出强化效果不明显;若fe含量太多,一方面将消耗掉绝大多数si原子而形成粗大的脆性fesi初生相,导致铸坯在后续加工过程易开裂,成材率低,另一方面过量fe加入会使导电率下降。
25.若si含量太少,一方面不能使cr、fe元素以fesi、cr2si相充分析出,强化效果有限,另一方面残留在基体内的溶质原子尤其是fe元素严重危害合金的导电率。若si含量太多,虽然能促进第二相尽可能析出,但多余的si元素仍残留在铜基体内,同样导致合金导电率下降。其中si含量的控制应主要以充分消耗fe元素为基础。
26.添加zr元素的作用是抑制时效过程中cr相的粗化和细化基体晶粒。若zr含量太少,时效过程中cr相易长大粗化,cr相析出强化效果降低,且在晶界处形成的亚微米级cu3zr相较小,不利于提高其抗高温软化能力;若zr含量太多,合金铸造过程中会产生较多粗大的cu3zr和cu5zr相,降低强化作用。因此需要综合考虑各元素的含量和配比,才能制备出本发明设计的高强高导cu-zn-cr-zr-fe-si合金。
27.根据本发明的一些实施方式,以质量百分比计,所述cu-zn-cr-zr-fe-si系合金包括以下组分:
28.zn:0.40wt%~1.00wt%,
29.cr:0.30wt%~1.00wt%,
30.zr:0.15wt%~0.60wt%,
31.fe:0.20wt%~1.00wt%,
32.si:0.40wt%~1.00wt%,
33.余量为铜。
34.本发明的第二方面提供了制备上述cu-zn-cr-zr-fe-si系合金的方法,包括以下步骤:
35.s1:按配比备料,先将铜熔化后,加入锌和覆盖剂,然后加入铁,第一次保温后加入硅,降温后加入铬和锆进行第二次保温,得到铸锭;
36.s2:将步骤s1得到的铸锭在保护气氛中进行均匀化退火处理;
37.s3:将步骤s2处理后的铸锭进行热加工变形处理后,进行淬火处理,得到热加工坯料;
38.s4:将步骤s3得到的坯料在保护性气氛下进行固溶处理、冷加工处理和时效处理。
39.本发明关于制备cu-zn-cr-zr-fe-si系合金的方法中的一个技术方案,至少具有以下有益效果:
40.本发明的cu-zn-cr-zr-fe-si系合金的制备方法,制备得到的cu-zn-cr-zr-fe-si系合金,硬度为180~250hv,抗拉强度为600~750mpa,屈服强度为550~700mpa,弹性模量为125~135mpa,伸长率为3~10%,导电率为70~85%iacs,耐热温度≥580℃,残余应力≤30mpa,解决了现有cu-cr-zr合金的强度、导电性能、抗软化性能、低残余应力难以兼顾和匹配的问题。
41.本发明制备cu-zn-cr-zr-fe-si系合金的方法,通过设计冷加工与热处理协同控制的组合形变热处理技术,调控zn、cr、zr、fe、si等元素在合金中的存在形式、空间分布状态,发挥多尺度、多形态、多相协同强化作用,能够同时提高强度与导电率,获得优异的综合性能。采用“大变形量冷加工+高温短时间时效处理”,使cr、fesi初生相破碎细化。后续形变热处理进一步细化cr、fesi、cr2si相粒子,并促进剩余cr、si、fe原子以细小豆瓣状、椭球状纳米级粒子的形式在冷加工引入的位错、亚晶、孪晶等缺陷处形核析出。但溶质原子的析出形式对温度、时间等因素十分敏感,因此工艺参数的制定对元素在合金中的存在形式、空间分布状态具有重要作用。
42.若冷加工变形量太小,则无法提供cr相、fesi相的形核储能,也影响其他原子的析出,同时不足以破碎合金凝固过程中形成的cu3zr、cr2si初生相,造成后续加工性能差等问题;若冷加工变形量太大,一方面导致合金加工硬化严重,易产生裂纹等缺陷,降低成材率,另一方面,形成较大的变形储能,易诱发后续时效过程的铜基体再结晶,使合金的强度显著下降。
43.若热处理温度太低,则溶质原子扩散速度减弱,一方面cr相、fesi相无法充分弥散析出,强化效果较小,另一方面溶质原子来不及扩散而继续残留在基体中增大了对电子的散射,不利于导电率提高。若热处理温度太高,cr和fesi相粒子易长大,也容易诱发铜基体的再结晶,使合金的强度明显降低;若时效时间太短,虽然能析出一部分cr和fesi相粒子,但还有绝大多数cr、si、fe原子来不及析出,残留在铜基中,同样会恶化强度和导电率。若时效时间太长,各种析出相粒子长大、粗化,强化效果差。
44.本发明综合考虑了成分设计和加工—热处理制度间的综合作用,一方面优化zn、cr、zr、fe、si等元素含量和配比,利用zn元素的固溶作用强化铜基体、减小合金的残余应力和提高蚀刻性能,利用fe和si元素结合形成高硬度、高耐热的fesi相,弥补单一cr相强化作用不足,提高合金的强度和抗高温软化性能;另一方面通过调控加工和热处理制度,使cr、si、fe等元素分别以纳米级cr、fesi相充分析且弥散均匀分布在基体中,钉扎位错与晶界运动,发挥多尺度多形态多相协同弥散强化、应变强化、亚晶强化和固溶强化等综合作用,进而获得cu-zn-cr-zr-fe-si合金。
45.根据本发明的一些实施方式,步骤s1中,第一次保温的温度1300℃~1500℃,时间为1min~3min。
46.根据本发明的一些实施方式,步骤s1中,第一次保温的温度1400℃,时间为2min。
47.根据本发明的一些实施方式,步骤s1中,加入硅后,降温至1250℃。
48.根据本发明的一些实施方式,步骤s1中,第二次保温的温度1250℃~1300℃,时间
为2min~4min。
49.根据本发明的一些实施方式,步骤s1中,第二次保温的时间为3min。
50.根据本发明的一些实施方式,步骤s2中,所述均匀化退火处理的温度为880℃~980℃,时间为1h~8h。
51.根据本发明的一些实施方式,步骤s2中,均匀化退火处理时,将熔炼后的铜合金铸锭在保护气氛里,铸锭周围铺满木炭,进行均匀化退火处理。
52.根据本发明的一些实施方式,步骤s3中,进行热加工处理前,先将铸锭铣面至表面没有缺陷。
53.根据本发明的一些实施方式,步骤s3中,所述热加工变形处理的温度为880℃~960℃,时间为0.5h~2h,变形量为50%~90%。
54.根据本发明的一些实施方式,步骤s3中,进行热加工处理后,进行淬火处理,淬火处理的方式为水淬,淬火后,再次铣面至铸锭表面无氧化层。
55.根据本发明的一些实施方式,步骤s4中,所述固溶处理的温度为880℃~960℃,时间为1h~8h。
56.根据本发明的一些实施方式,步骤s4中,固溶处理后,进行淬火处理,淬火处理的方式为水淬,淬火后,再次铣面至铸锭表面无氧化层。
57.本发明的一些实施方式,步骤s4中,所述冷加工处理的变形量为50%~90%。
58.根据本发明的一些实施方式,步骤s4中,冷加工处理的对象形状为板材。
59.根据本发明的一些实施方式,步骤s4中,冷加工处理后,在保护气氛中,于400℃~550℃时效1min~24h。将时效后样品再进行变形量40%~90%冷加工。根据厚度再决定进行第二次或者第三次冷加工的变形量。一般而言,若首次变形量小于50%,优选后续进行70~90%变形量。若首次变形量大于50%,再次进行30%~50%变形,最终按照同样方法于400~500℃时效后15min~2h后得到最终的合金。
60.本发明中,热加工包括热挤压、热轧和热锻造。
61.本发明中,冷加工包括拉拔、轧制、旋压和旋锻。
附图说明
62.图1是实施例1制备的合金材料的透射电镜测试结果。
63.图2是实施例2制备的合金材料的透射电镜测试结果。
具体实施方式
64.以下是本发明的具体实施例,并结合实施例对本发明的技术方案作进一步的描述,但本发明并不限于这些实施例。
65.实施例1
66.本实施例具体制备了一种cu-zn-cr-zr-fe-si系合金,本实施例的cu-zn-cr-zr-fe-si系合金包括以下组分:
67.zn:0.3wt%,
68.cr:0.58wt%,
69.zr:0.2wt%,
70.fe:0.25wt%,
71.si:0.12wt%,
72.余量为铜。
73.具体的制备方法,包括以下步骤:
74.s1:按配比备料,先将铜熔化后,加入锌和覆盖剂,然后加入铁,第一次保温后加入硅,降温后加入铬和锆进行第二次保温,得到铸锭;
75.s2:将步骤s1得到的铸锭在保护气氛中进行均匀化退火处理;
76.s3:将步骤s2处理后的铸锭进行热加工变形处理后,进行淬火处理,得到热加工坯料;
77.s4:将步骤s3得到的坯料在保护性气氛下进行固溶处理、冷加工处理和时效处理。
78.步骤s1中:
79.第一次保温的温度1400℃,时间为2min。
80.加入硅后,降温至1250℃。
81.第二次保温的温度1300℃,时间为3min。
82.步骤s2中:
83.均匀化退火处理的温度为960℃,时间为1h~8h。
84.均匀化退火处理时,将熔炼后的铜合金铸锭在保护气氛里,铸锭周围铺满木炭,进行均匀化退火处理。
85.步骤s3中:
86.进行热加工处理前,先将铸锭铣面至表面没有缺陷。
87.热加工变形处理的温度为940℃,时间为2h,进行七道次热轧,第一道次热轧变形量为25%,第二道至第五道次变形量分别为22%,25%,32%,34%,第六道次24%,第七道次20%,。
88.进行热加工处理后,进行淬火处理,淬火处理的方式为水淬,淬火后,再次铣面至铸锭表面无氧化层。
89.步骤s4中:
90.固溶处理的温度为940℃,时间为8h。
91.固溶处理后,进行淬火处理,淬火处理的方式为水淬,淬火后,再次铣面至铸锭表面无氧化层。
92.冷加工处理的变形量为70%。
93.冷加工处理后,在保护气氛中,于400℃时效150min。
94.将时效后样品再进行第一道次冷轧变形量为20%,第二道次冷轧的道次变形量为40%,得到冷轧坯。根据厚度决定进行第二次冷加工的变形量。所得冷轧坯经40%变形量的冷轧后,在300℃气垫炉中进行退火,出炉氮气淬火,得到铜合金板材。
95.合金硬度为213hv,抗拉强度为720mpa,电导率为70.2%iacs,伸长率5.5%。
96.实施例2
97.本实施例具体制备了一种cu-zn-cr-zr-fe-si系合金,本实施例的cu-zn-cr-zr-fe-si系合金包括以下组分:
98.zn:0.29wt%,
fe-si系合金包括以下组分:
129.zn:0.3wt%,
130.cr:0.4wt%,
131.zr:0.17wt%,
132.fe:0.2wt%,
133.si:0.4wt%,
134.余量为铜。
135.具体的制备方法,包括以下步骤:
136.s1:按配比备料,先将铜熔化后,加入锌和覆盖剂,然后加入铁,第一次保温后加入硅,降温后加入铬和锆进行第二次保温,得到铸锭;
137.s2:将步骤s1得到的铸锭在保护气氛中进行均匀化退火处理;
138.s3:将步骤s2处理后的铸锭进行热加工变形处理后,进行淬火处理,得到热加工坯料;
139.s4:将步骤s3得到的坯料在保护性气氛下进行固溶处理、冷加工处理和时效处理。
140.步骤s1中:
141.第一次保温的温度1400℃,时间为2min。
142.加入硅后,降温至1250℃。
143.第二次保温的温度1300℃,时间为3min。
144.步骤s2中:
145.均匀化退火处理的温度为960℃,时间为6h。
146.均匀化退火处理时,将熔炼后的铜合金铸锭在保护气氛里,铸锭周围铺满木炭,进行均匀化退火处理。
147.步骤s3中:
148.进行热加工处理前,先将铸锭铣面至表面没有缺陷。
149.热加工变形处理的温度为940℃,时间为2h,进行七道次热轧,第一道次热轧变形量为25%,第二道至第五道次变形量分别为22%,25%,32%,34%,第六道次24%,第七道次20%,。
150.进行热加工处理后,进行淬火处理,淬火处理的方式为水淬,淬火后,再次铣面至铸锭表面无氧化层。
151.步骤s4中:
152.固溶处理的温度为940℃,时间为8h。
153.固溶处理后,进行淬火处理,淬火处理的方式为水淬,淬火后,再次铣面至铸锭表面无氧化层。
154.冷加工处理的变形量为70%。
155.冷加工处理后,在保护气氛中,于400℃时效150min。
156.将时效后样品再进行第一道次冷轧变形量为20%,第二道次冷轧的道次变形量为40%,得到冷轧坯。根据厚度决定进行第二次冷加工的变形量。所得冷轧坯经40%变形量的冷轧后,在300℃气垫炉中进行退火,出炉氮气淬火,得到铜合金板材。
157.合金硬度为210hv抗拉强度为715mpa,电导率为71.5%iacs,伸长率6.1%
158.测试例1
159.测试了实施例1至实施例3制备的合金试样的硬度、延伸率、抗拉强度、屈服强度、弹性模量、伸长率、导电率、耐热温度和残余应力。
160.其中:
161.硬度测试依据的标准为gb/t 7997-2014。
162.屈服强度、抗拉强度、弹性模量和伸长率测试依据的标准为gb/t 34505-2017。
163.导电率测试依据的标准为gb/t 32791-2016。
164.耐热温度测试依据的标准为gb/t 33370—2016。
165.残余应力测试依据的标准为gb/t 33163-2016。
166.结果如表1所示。
167.合金硬度为213hv,抗拉强度为720mpa,电导率为70.2%iacs,伸长率5.5%。
168.合金硬度为214hv,抗拉强度为722mpa,电导率为69.2%iacs,伸长率5.7%
169.合金硬度为210hv抗拉强度为715mpa,电导率为71.5%iacs,伸长率6.1%
170.表1实施例1至实施例3制备的合金性能测试结果
[0171] 实施例1实施例2实施例3硬度/hv213214210延伸率/%5.55.76.1抗拉强度/mpa720722715屈服强度/mpa650655648弹性模量125mpa125mpa127mpa导电率/%iacs74.273.670.1残余应力/mpa25mpa25mpa24mpa
[0172]
测试例2
[0173]
通过透射电镜观察了实施例1至实施例3制备的合金试样的微观形貌,结果如图1至图2所示。
[0174]
从图1至图2可以看出,铜合金中有大量纳米级析出相,大量位错与析出相交互,说明有钉扎位错的作用。
[0175]
强化相粒子钉扎位错运动,形成胞状结构,细晶强化效果显著。
[0176]
本发明的cu-zn-cr-zr-fe-si系合金,硬度为180~250hv,抗拉强度为600~750mpa,屈服强度为550~700mpa,弹性模量为125~135mpa,伸长率为3~10%,导电率为70~85%iacs,残余应力≤30mpa,解决了现有cu-cr-zr合金的强度、导电性能、抗软化性能、低残余应力难以兼顾和匹配的问题。不仅适用于制备蚀刻型引线框架,还可以满足极大规模集成电路、5g通讯、高端电子元件等现代信息产业对高性能铜合金的需求。
[0177]
上面结合实施例对本发明作了详细说明,但是本发明不限于上述实施例,在所属技术领域普通技术人员所具备的知识范围内,还可以在不脱离本发明宗旨的前提下作出各种变化。