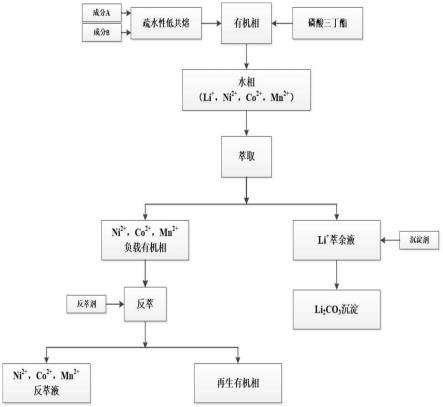
1.本发明属湿法冶金技术领域,尤其涉及一种疏水性低共熔溶剂与磷酸三丁酯协同萃取剂及其对废锂电池浸出液中锂与过渡金属萃取分离的方法。
背景技术:2.在能源和交通系统的脱碳成为最重要的国际挑战之一的时代,锂离子电池(lib)以其优异的储能能力被广泛应用于电子设备、电动汽车、可再生能源存储等方面,可以减少交通运输业对化石燃料的依赖。锂作为锂离子电池中的关键金属元素,因其重量轻而受到广泛关注,预计到2025年碳酸锂的需求量将超过500万吨。根据全球平均可回收含量(rc)数据,过渡金属在所有回收元素(尤其是镍和钴)中居于首位,这将导致自然资源枯竭。到2024年,仅汽车锂离子电池的总市场预计将达到2210亿美元。然而,锂离子电池产量的增加不仅导致锂、镍和钴的严重短缺,废旧的锂离子电池也将严重污染环境,而且其中有价金属的含量和纯度都高于自然界,如果不回收,将造成巨大的资源浪费,不符合清洁能源和资源化利用的理念。
3.目前,废锂电池的常见回收方法主要是火法冶金和湿法冶金工艺。湿法冶金工艺具有选择性高、能耗低、无有害气体等特点,比火法冶金工艺更符合绿色环保理念。在湿法冶金工艺中,电池首先经过预处理各种物理方法,然后将各种金属溶解在酸中,提纯后得到li、co、ni和mn的酸浸出液。盐酸或硫酸比其他浸出剂更经济,通常用于湿法冶金过程中锂离子电池中金属的酸还原浸出。在各种金属回收方法中,溶剂萃取因其操作简单、回收率高、可调节性好而被广泛用于金属分离。
4.cn112442596a公开了一种从含镍钴锰的电池中分离镍钴锰的方法,使用羧酸类萃取剂通过多级逆流萃取分步分离了镍、钴、锰。cn111850302b公开了一种使用双酮类化合物为萃取剂与有机膦化合物为协萃剂从废锂电池中分离金属的方法,经多级逆流萃取后镍钴锰的萃取率均达到99%以上。但这些萃取工艺大多需要进行多级萃取,在一定程度上加大了萃取剂的损耗,不仅使成本增加,而且造成了资源的浪费。同时,使用这些传统的萃取剂,不仅萃取效果有限,而且这些萃取剂具有易挥发、污染环境、有毒性等特点而受到限制,因此开发一种不仅萃取效率高,萃取方法简便,而且对环境友好的“绿色溶剂”就显得至关重要。
技术实现要素:5.针对上述问题,本发明采用一种疏水性低共熔与磷酸三丁酯协同萃取废锂电池中的镍钴锰,将锂留在萃余液中,单级萃取能达到较高的萃取分离效果,具有对环境友好,运营成本低等特点。
6.为了达到上述目的,本发明采用以下技术方案:
7.(1)配制水相:模拟废锂电池浸出液成分,配置得到含锂、镍、钴和锰金属离子的水
相;
8.(2)配制疏水性低共熔溶剂:将利多卡因与正癸酸加热混合得到疏水性低共熔溶剂;
9.(3)配制有机相:将步骤(2)中得到的疏水性低共熔溶剂与磷酸三丁酯混合,得到有机相;
10.(4)将步骤(3)中得到的有机相加入到步骤(1)得到的水相中进行混合萃取,离心分相后得到镍钴锰负载有机相和含锂萃余液;
11.(5)将沉淀剂加入到步骤(4)中的含锂萃余液中得到碳酸锂沉淀;
12.(6)将反萃剂加入到步骤(4)中的镍钴锰负载有机相中,得到镍钴锰反萃液和再生有机相;
13.进一步,步骤(1)中模拟废电池浸出液水相ph为2~6,有价金属含量分别为li=300~400mg/l,ni=1300~1500mg/l,co=600~700mg/l,mn=800~900mg/l。
14.进一步,步骤(2)配制的疏水性低共熔溶剂中利多卡因与正癸酸通过氢键作用结合,物质的量之比为1:1。将正癸酸加热融化后加入到利多卡因中,在50℃水浴加热条件下混合得到疏水性低共熔溶剂。
15.进一步,步骤(3)配制的有机相中包含如下结构式:
[0016][0017]
进一步,步骤(3)配制的有机相中磷酸三丁酯与疏水性低共熔体积之比=6:4~4:6;
[0018]
进一步,步骤(4)中萃取工艺参数为加入的水相与有机相的体积之比(a/o)=3:1~1:3,萃取温度为10~30℃,萃取级数为1级,混匀搅拌时间为20~30min,混匀搅拌转速为200~500r/min,将水相与有机相充分混匀后置于离心机中,离心转速为6000~8000r/min,离心时间为10~30min进行分相,得到镍钴锰负载有机相和含锂萃余液。
[0019]
进一步,步骤(5)中加入的沉淀剂为1.5mol/的碳酸钠溶液,加入的碳酸钠与含锂
萃余液的体积的比值为2。
[0020]
进一步,步骤(6)反萃取工艺使用2mol/l的hcl作为反萃剂,反萃取参数为加入的盐酸与镍钴锰负载有机相的体积的比(a/o)=2:1,反萃取温度为24℃,反萃取级数为1级,混匀搅拌时间为30min,混匀搅拌转速为300r/min,充分混匀后置于离心机中,离心转速为8000r/min,离心时间为10min后分相得到镍钴锰反萃液和再生有机相。
附图说明
[0021]
图1为本发明提供的废锂电池浸出液中有价金属萃取分离方法的工艺流程图。
[0022]
下面结合实例对本发明进一步详细说明,但下述的实例仅仅是本发明的简易例子,并不代表或限制本发明的权利保护范围,本发明的保护范围以权利要求书为准。
具体实施方式
[0023]
为了更好地说明本发明,便于理解本发明的技术方案,本发明的典型但非限制性的实施例如下:
[0024]
实施例1
[0025]
本实施例提供的一种疏水性低共熔溶剂与磷酸三丁酯协同萃取剂及其对废锂电池浸出液中锂与过渡金属萃取分离的方法流程如图1所示。
[0026]
本实施例的模拟废锂电池酸性浸出液中成分如下:
[0027]
元素linicomn含量(mg/l)377.91502601.9885.3
[0028]
本实施例所述的萃取分离方法,配制的模拟废锂电池水相ph=2;
[0029]
本实施例所述的萃取分离方法,配制的疏水性低共熔溶剂中利多卡因与正癸酸通过氢键作用结合,物质的量之比为1:1。将正癸酸加热融化后加入到利多卡因中,在50℃水浴加热条件下混合得到疏水性低共熔溶剂;
[0030]
本实施例所述的萃取分离方法,将配置好的疏水性低共熔溶剂加入到磷酸三丁酯中,其中加入的磷酸三丁酯与疏水性低共熔的体积比为6:4,得到有机相;
[0031]
本实施例所述的萃取分离方法,将配置好的有机相加入到水相中,萃取工艺参数为水相与有机相的体积比(a/o)=2:1,萃取温度为10℃,萃取级数为1级,混匀搅拌时间20min,转速200r/min,充分混匀后置于离心机中,离心转速6000r/min,离心10min后分相得到镍钴锰负载有机相和含锂萃余液。
[0032]
本实施例所述的萃取分离方法,向含锂萃余液中加入浓度为1.5mol/l的碳酸钠溶液,加入的碳酸钠溶液与含锂萃余液的体积比为2:1,充分沉淀洗涤后得到碳酸锂溶液。
[0033]
本实施例所述的萃取分离方法,反萃取工艺使用2mol/l的hcl作为反萃剂,反萃取参数为,加入的hcl与镍钴锰负载有机相的体积比(a/o)=2:1,反萃取温度为24℃,反萃取级数为1级,混匀搅拌时间为30min,转速为300r/min,充分混匀后置于离心机中,离心转速为8000r/min,离心时间为10min后分相,得到镍钴锰反萃液和再生有机相。
[0034]
实施例1的萃取实验结果如下:
[0035]
元素初始溶液浓度(mg/l)萃余液浓度(mg/l)萃取率li377.9348.87.70%
ni150212.899.15%co601.91397.84%mn885.367.892.34%
[0036]
在本实施例中,经单级萃取后,镍钴锰的萃取率均达到92%以上,同时萃余液中得到高纯度的锂盐溶液,实现了废锂电池中锂与过渡金属的有效分离。
[0037]
实施例2
[0038]
本实施例提供的一种疏水性低共熔溶剂与磷酸三丁酯协同萃取剂及其对废锂电池浸出液中锂与过渡金属萃取分离的方法流程如图1所示。
[0039]
本实施例的模拟废锂电池酸性浸出液中成分如下:
[0040]
元素linicomn含量(mg/l)377.91502601.9885.3
[0041]
本实施例所述的萃取分离方法,配制的模拟废锂电池水相ph=6;
[0042]
本实施例所述的萃取分离方法,配制的疏水性低共熔溶剂中利多卡因与正癸酸通过氢键作用结合,物质的量之比为1:1。将正癸酸加热融化后加入到利多卡因中,在50℃水浴加热条件下混合得到疏水性低共熔溶剂;
[0043]
本实施例所述的萃取分离方法,将配置好的疏水性低共熔溶剂加入到磷酸三丁酯中,其中加入的磷酸三丁酯与疏水性低共熔的体积比为4:6,得到有机相;
[0044]
本实施例所述的萃取分离方法,将配置好的有机相加入到水相中,萃取工艺参数为水相与有机相的体积比(a/o)=2:1,萃取温度为30℃,萃取级数为1级,混匀搅拌时间30min,转速500r/min,充分混匀后置于离心机中,离心转速8000r/min,离心30min后分相,得到镍钴锰负载有机相和含锂萃余液。
[0045]
本实施例所述的萃取分离方法,向含锂萃余液中加入浓度为1.5mol/l的碳酸钠溶液,加入的碳酸钠溶液与含锂萃余液的体积比为2:1,充分沉淀洗涤后得到碳酸锂溶液。
[0046]
本实施例所述的萃取分离方法,反萃取工艺使用2mol/l的hcl作为反萃剂,反萃取参数为,加入的hcl与镍钴锰负载有机相的体积比(a/o)=2:1,反萃取温度为24℃,反萃取级数为1级,混匀搅拌时间为30min,转速为300r/min,充分混匀后置于离心机中,离心转速为8000r/min,离心时间为15min后分相,得到镍钴锰反萃液和再生有机相。
[0047]
实施例2的萃取实验结果如下:
[0048]
元素初始溶液浓度(mg/l)萃余液浓度(mg/l)萃取率li377.9323.714.34%ni15022.299.85%co601.91.999.68%mn885.316.698.12%
[0049]
在本实施例中,经单级萃取后,镍钴锰的萃取率均达到98%,同时萃余液中得到高纯度的锂盐溶液,实现了废锂电池中锂与过渡金属的有效分离。
[0050]
实施例3
[0051]
本实施例提供的一种疏水性低共熔溶剂与磷酸三丁酯协同萃取剂及其对废锂电池浸出液中锂与过渡金属萃取分离的方法流程如图1所示。
[0052]
本实施例的模拟废锂电池酸性浸出液中成分如下:
[0053]
元素linicomn含量(mg/l)360.91453587.1862.8
[0054]
本实施例所述的萃取分离方法,配制的模拟废锂电池水相ph=3;
[0055]
本实施例所述的萃取分离方法,配制的疏水性低共熔溶剂中利多卡因与正癸酸通过氢键作用结合,物质的量之比为1:1。将正癸酸加热融化后加入到利多卡因中,在50℃水浴加热条件下混合得到疏水性低共熔溶剂;
[0056]
本实施例所述的萃取分离方法,将配置好的疏水性低共熔溶剂加入到磷酸三丁酯中,其中加入的磷酸三丁酯与疏水性低共熔的体积比为4:6,得到有机相;
[0057]
本实施例所述的萃取分离方法,将配置好的有机相加入到水相中,萃取工艺参数为水相与有机相的体积比(a/o)=3:1,萃取温度为24℃,萃取级数为1级,混匀搅拌时间30min,转速300r/min,充分混匀后置于离心机中,离心转速8000r/min,离心10min后分相。得到镍钴锰负载有机相和含锂萃余液。
[0058]
本实施例所述的萃取分离方法,向含锂萃余液中加入浓度为1.5mol/l的碳酸钠溶液,加入的碳酸钠溶液与含锂萃余液的体积比为2:1,充分沉淀洗涤后得到碳酸锂溶液。
[0059]
本实施例所述的萃取分离方法,反萃取工艺使用2mol/l的hcl作为反萃剂,反萃取参数为,加入的hcl与镍钴锰负载有机相的体积比(a/o)=2:1,反萃取温度为24℃,反萃取级数为1级,混匀搅拌时间为30min,转速为300r/min,充分混匀后置于离心机中,离心转速为8000r/min,离心时间为10min后分相,得到镍钴锰反萃液和再生有机相。
[0060]
实施例3的萃取实验结果如下:
[0061]
元素初始溶液浓度(mg/l)萃余液浓度(mg/l)萃取率li360.1306.914.96%ni145318.798.71%co587.113.997.63%mn862.851.993.98%
[0062]
在本实施例中,经单级萃取后,镍钴锰的萃取率均达到93%,同时萃余液中得到高纯度的锂盐溶液,实现了废锂电池中锂与过渡金属的有效分离。
[0063]
实施例4
[0064]
本实施例提供的一种疏水性低共熔溶剂与磷酸三丁酯协同萃取剂及其对废锂电池浸出液中锂与过渡金属萃取分离的方法流程如图1所示。
[0065]
本实施例的模拟废锂电池酸性浸出液中成分如下:
[0066]
元素linicomn含量(mg/l)360.91453587.1862.8
[0067]
本实施例所述的萃取分离方法,配制的模拟废锂电池水相ph=3;
[0068]
本实施例所述的萃取分离方法,配制的疏水性低共熔溶剂中利多卡因与正癸酸通过氢键作用结合,物质的量之比为1:1。将正癸酸加热融化后加入到利多卡因中,在50℃水浴加热条件下混合得到疏水性低共熔溶剂;
[0069]
本实施例所述的萃取分离方法,将配置好的疏水性低共熔溶剂加入到磷酸三丁酯中,其中加入的磷酸三丁酯与疏水性低共熔的体积比为4:6,得到有机相;
[0070]
本实施例所述的萃取分离方法,将配置好的有机相加入到水相中,萃取工艺参数为水相与有机相的体积比(a/o)=1:3,萃取温度为24℃,萃取级数为1级,混匀搅拌时间30min,转速300r/min,充分混匀后置于离心机中,离心转速8000r/min,离心10min后分相,得到镍钴锰负载有机相和含锂萃余液。
[0071]
本实施例所述的萃取分离方法,向含锂萃余液中加入浓度为1.5mol/l的碳酸钠溶液,加入的碳酸钠溶液与含锂萃余液的体积比为2:1,充分沉淀洗涤后得到碳酸锂溶液。
[0072]
本实施例所述的萃取分离方法,反萃取工艺使用2mol/l的hcl作为反萃剂,反萃取参数为,加入的hcl与镍钴锰负载有机相的体积比(a/o)=2:1,反萃取温度为24℃,反萃取级数为1级,混匀搅拌时间为30min,转速为300r/min,充分混匀后置于离心机中,离心转速为8000r/min,离心时间为10min后分相,得到镍钴锰反萃液与再生有机相。
[0073]
实施例4的萃取实验结果如下:
[0074]
元素初始溶液浓度(mg/l)萃余液浓度(mg/l)萃取率li360.1299.916.90%ni14530.899.94%co587.11.299.80%mn862.86.599.25%
[0075]
在本实施例中,经单级萃取后,镍钴锰的萃取率均达到99%,同时萃余液中得到高纯度的锂盐溶液,实现了废锂电池中锂与过渡金属的有效分离。
[0076]
实施例5
[0077]
本实施例提供的一种疏水性低共熔溶剂与磷酸三丁酯协同萃取剂及其对废锂电池浸出液中锂与过渡金属萃取分离的方法流程如图1所示。
[0078]
本实施例的模拟废锂电池酸性浸出液中成分如下:
[0079][0080][0081]
本实施例所述的萃取分离方法,配制的模拟废锂电池水相ph=3;
[0082]
本实施例所述的萃取分离方法,配制的疏水性低共熔溶剂中利多卡因与正癸酸通过氢键作用结合,物质的量之比为1:1。将正癸酸加热融化后加入到利多卡因中,在50℃水浴加热条件下混合得到疏水性低共熔溶剂;
[0083]
本实施例所述的萃取分离方法,将配置好的疏水性低共熔溶剂加入到磷酸三丁酯中,其中加入的磷酸三丁酯与疏水性低共熔的体积比为4:6,得到有机相;
[0084]
本实施例所述的萃取分离方法,将配置好的有机相加入到水相中,萃取工艺参数为水相与有机相的体积比(a/o)=1:2,萃取温度为24℃,萃取级数为1级,混匀搅拌时间30min,转速300r/min,充分混匀后置于离心机中,离心转速8000r/min,离心10min后分相,得到镍钴锰负载有机相和含锂萃余液。
[0085]
本实施例所述的萃取分离方法,向含锂萃余液中加入浓度为1.5mol/l的碳酸钠溶液,加入的碳酸钠溶液与含锂萃余液的体积比为2:1,充分沉淀洗涤后得到碳酸锂溶液。
[0086]
本实施例所述的萃取分离方法,反萃取工艺使用2mol/l的hcl作为反萃剂,反萃取
参数为,加入的hcl与镍钴锰负载有机相的体积比(a/o)=2:1,反萃取温度为24℃,反萃取级数为1级,混匀搅拌时间为30min,转速为300r/min,充分混匀后置于离心机中,离心转速为8000r/min,离心时间为10min后分相,得到镍钴锰反萃液和再生有机相。
[0087]
实施例5的萃取实验结果如下:
[0088]
元素初始溶液浓度(mg/l)萃余液浓度(mg/l)萃取率li377.9307.318.68%ni15020.699.96%co601.91.399.78%mn885.39.298.96%
[0089]
在本实施例中,经单级萃取后,镍钴锰的萃取率均达到98%,同时萃余液中得到高纯度的锂盐溶液,实现了废锂电池中锂与过渡金属的有效分离。