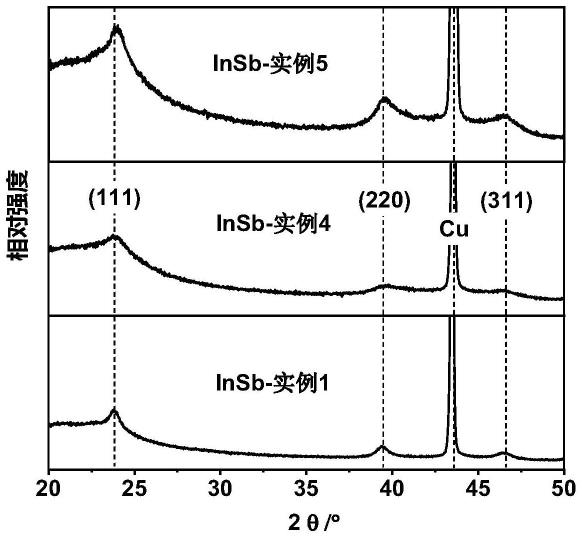
一种insb多晶薄膜负极材料的制备方法及其应用
技术领域
1.本发明属于锂离子电池制造技术领域,具体涉及一种insb多晶薄膜负极材料的制备方法及其应用
背景技术:2.近年来,电动汽车等行业的快速发展对锂离子电池(lib)的各项性能提出了更高的要求,例如更高的能量密度、更长的循环性能和更大范围温度的适应能力。然而,当前主流的商业锂离子电池在低温下都会出现显著的能量和容量损失。目前商业化中主要使用的石墨负极在零度以下极难充电,且容易锂离子沉积形成锂枝晶造成安全隐患。通过外部热源和电池自热的方式能有效提高锂离子电池的温度,但对于小型设备而言这类方法影响了设备的便携性同时大大降低了电池的工作效率。在-40℃及以下的超低温条件下对锂离子电池材料的要求将更加苛刻。
3.解决锂离子电池低温应用难题的关键在于寻找具有适中嵌锂电位、能够快速完成嵌锂/脱锂过程的新型负极材料。截止目前,insb作为锂离子电池负极材料时具有好的循环稳定性,这是由于在充放电循环过程中insb始终保留其整体闪锌矿结构,并且在此过程中只有很小的体积变化。其中in不仅能够作为缓冲基质,还能够在低电位(0.6v以下)下进一步锂化,从而提供更多容量。因此insb能够在拥有较高容量的情况下稳定循环。
技术实现要素:4.本发明的目的在于克服现有技术的上述不足,提供一种insb多晶薄膜负极材料的制备方法及其应用。
5.本发明的目的之一是提供一种更高容量、更高循环稳定性、更高低温性能的锂离子电池负极材料。为实现上述发明目的,本发明采用的技术方案如下:
6.一种闪锌矿结构的多晶insb薄膜,以insb靶材为原料,通过控制参数的方式制备多晶insb薄膜,所述多晶薄膜负极材料仅含有一种闪锌矿结构的insb晶体结构。
7.优选的,作为一个较佳的实施方式,将电池级铜箔作为insb负极流体基底,晶体均匀生长在铜箔集流体上。
8.优选的,作为一个较佳的实施方式,所述电池级铜箔集流体的厚度为5-20μm。
9.优选的,作为一个较佳的实施方式,所述多晶薄膜的厚度为300~3000nm。
10.优选的,作为一个较佳的实施例方式,所述insb晶体颗粒的尺寸为1~5μm。
11.本发明的另一目的在于提供一种多晶锂电子负极材料的制备方法,所述制备方法包括如下步骤:在高纯氩气氛围内,将insb靶材安装在电源靶头上,通电进行磁控溅射,溅射物沉积在集流体材料上,得到insb多晶薄膜负极材料。
12.优选的,作为一个较佳的实施方式,进行磁控溅射时氩气气压为0.5~5pa。
13.优选的,作为一个较佳的实施方式,所述磁控溅射时间为5-30min。
14.优选的,作为一个较佳的实施方式,所述磁控溅射功率为100-200w。
15.优选的,作为一个较佳的实施方式,在电池级铜箔基体材料使用时进行清洗,从而减少衬底的表面油污及氧化物对膜基结合的影响。
16.优选的,作为一个较佳的实施例,所述清洗方式为在超声波中使用蒸馏水、无水乙醇、丙酮进行清洗处理。
17.优选的,作为一个较佳的实施方式,所述磁控溅射为射频溅射。
18.优选的,作为一个较佳的实施事实方式,所述磁控溅射仓室内真空度应达到1.0
×
10-4
pa后方可通入氩气。
19.优选的,作为一个较佳的实施方式,所述高纯氩气为纯度99.99%以上的氩气。
20.本发明的另一目的还在于提供一种insb薄膜负极材料的应用,通过将所述通过磁控溅射方式制备的insb薄膜负极材料应用到锂离子电池中,锂离子电池的性能具有显著提升。当温度为30℃,充放电电压范围为0~2.0v,充放电电流密度为0.2a/g时,其首次充电容量高达561.8mah/g,在800次循环后仍有534.6mah/g的容量,容量保持率高达95.2%。当温度为-50℃,充放电电压范围为0~2.0v,充放电电流密度为0.1a/g时,其首次充电比容量为511.9mah/g,在250次充放电循环后仍有348.3mah/g的容量,容量保持率为68.1%。
21.与现有材料与技术相比,本发明的优点在于:
22.1)本发明率先使用闪锌矿结构insb多晶负极作为锂离子电池负极材料,制备出insb多晶薄膜材料。
23.2)本发明提供的insb多晶负极材料的制备方式简单。
24.3)本发明的insb多晶负极材料可作为锂离子电池负极材料,该材料克服了合金化负极材料充放电过程中体积膨胀率大的缺点,而相较于现有的商业石墨负极具有极高的容量,同时保持了极高的循环稳定性。
25.4)本发明的insb多晶负极材料可作为超低温锂离子电池负极材料,该材料在低温下容量衰减极小,克服了锂离子电池在低温条件下充放电效率低以及容量大幅度降低的缺点,同时兼具了高容量和高循环稳定性的特点。
附图说明
26.图1为本发明实施例1、4、5制备的insb多晶薄膜负极材料的x射线衍射谱图;
27.图2为本发明实施例1、4、5制备的insb多晶薄膜负极材料的扫描电子显微镜图;
28.图3为本发明实施例1制备的insb多晶薄膜负极材料的首次充放电曲线图;
29.图4为本发明实施例1制备的insb多晶薄膜负极材料的在30℃条件下的循环-比容量性能曲线图;
30.图5为本发明实施例4制备的insb多晶薄膜负极材料的扫描电子显微镜图;
31.图6为本发明实施例4制备的insb多晶薄膜负极材料的首次充放电曲线图;
32.图7为本发明实施例4制备的insb多晶薄膜负极材料的在30℃条件下的循环-比容量性能曲线图;
33.图8为本发明实施例4制备的insb多晶薄膜负极材料的在-30℃和30℃条件下的循环-比容量性能曲线图;
34.图9为本发明实施例4制备的insb多晶薄膜负极材料的在-50℃条件下的循环-比容量性能曲线图;
35.图10为本发明实施例5制备的insb多晶薄膜负极材料的首次充放电曲线图;
36.图11为本发明实施例5制备的insb多晶薄膜负极材料的在30℃条件下的循环-比容量性能曲线图;
37.图12为本发明实施例8制备的lifepo4||insb全电池在-10℃条件下的循首次充放电曲线图;
38.图13为本发明实施例8制备的lifepo4||insb全电池在-10℃条件下的循环-比容量性能曲线图;
具体实施方式
39.为了使本发明要解决的技术问题、技术方案及有益效果更加清楚明白,以下结合实施例,对本发明作出进一步详细说明。应当理解,此处所描述的具体实施例仅用以解释本发明,但本发明的实施方式不限于此。
40.除非另有定义,下文中所使用的所有专业术语与本领域技术人员通常理解的含义相同。本文中所使用的专业术语只是为了描述具体实施例的目的,并不是旨在限制本发明的保护范围。
41.一、制备及应用实施例
42.1、实施例1
43.(1)insb多晶薄膜负极材料的制备与结构分析
44.采用超高真空磁控溅射系统(jgb-560,kyky)进行磁控溅射,将insb合金靶材安装在射频电源靶头上,磁控溅射功率设为100w;将磁控溅射仓抽真空至真空度达到1
×
10-4
pa后通入高纯氩气(纯度99.99%),控制气流大小为40sccm,仓内气压为2.5pa。
45.将电池级铜箔作为导电基体材料在超声波中分别使用蒸馏水、无水乙醇以及丙酮按顺序进行清洗处理掉导电基体材料(衬底)的表面油污及氧化物后,将该导电基体材料安装在溅射仓的样品基座上,并保持靶材与衬底的距离为10cm左右。
46.开通靶头电源,保持样品台以30rpm速度旋转以减少薄膜成分的不均匀性,溅射物沉积在导电基体材料上,溅射5分钟,得到溅射沉积后的insb多晶薄膜负极材料。
47.对本实施例所制备的insb多晶薄膜负极材料进行结构和物相分析,如图1、2所示,可知薄膜中仅存在一种insb晶体结构,且晶体沿铜箔岛屿状结构生长。
48.(2)insb多晶薄膜负极材料的充电/放电循环性能测试
49.将磁控溅射制备的insb多晶薄膜负极材料作为工作电极进行性能测试,在高纯ar环境的手套箱(super 1220,上海米开罗那机电技术有限公司)中进行,
50.水氧含量低于0.01ppm。以纯锂片作为对电极,使用1mlipf
6-ec:dec:pc(1:1:1 by vol),另加入10wt%fec的电解液,组装成扣式电池进行性能测试。
51.测试条件:充放电电流密度为0.2a/g,充放电电压范围为0.01v~2.0v。充放电循环测试过程如下:首次循环时,电池首先恒流放电至0.01v,然后接着恒流充电至2.0v;从第二次循环开始,放电时从2.0v放电至0.01v,充电时从0.01v充电至2.0v。
52.通过上述电池测试条件及步骤进行测试(所用电池充放电测试系统为land ct2001a电池测试系统,武汉蓝和电子有限公司),如图3、4所示,得到制备的insb多晶薄膜负极的首次充电比容量为580.0mah/g,在800次循环后仍有510.8mah/g的容量,容量保持率
为89.9%。
53.2、实施例2
54.(1)insb多晶薄膜负极材料的制备
55.本实施例的insb多晶薄膜负极材料的制备步骤与实施例1步骤(1)所述基本相同,所不同的是磁控溅射功率为150w。
56.(2)insb多晶薄膜负极材料的充电/放电循环性能测试
57.本实施例制得的insb多晶薄膜薄膜负极材料的首次放电性能测试方法和步骤与实施例1步骤(2)所述相同,按照该方法进行充放电测试,得到该复合薄膜负极的首次充电容量为592.3mah/g,在800次循环后仍有521.7mah/g的容量,容量保持率为88.1%。
58.3、实施例3
59.(1)insb多晶薄膜负极材料的制备
60.本实施例的insb多晶薄膜负极材料的制备步骤与实施例1步骤(1)所述基本相同,所不同的是磁控溅射功率为200w。
61.(2)insb多晶薄膜负极材料的充电/放电循环性能测试
62.本实施例制得的insb多晶薄膜薄膜负极材料的首次放电性能测试方法和步骤与实施例1步骤(2)所述相同,按照该方法进行充放电测试,得到该复合薄膜负极的首次充电容量为601.7mah/g,在800次循环后仍有533.7mah/g的容量,容量保持率为88.6%。
63.4、实施例4
64.(1)insb多晶薄膜负极材料的制备
65.本实施例的insb多晶薄膜负极材料的制备步骤与实施例1步骤(1)所述基本相同,所不同的是磁控溅射时间为15分钟。
66.(2)insb多晶薄膜负极材料的结构分析
67.通过图5的表面低倍sem可以观察到insb沉积时沿cu箔表面的岛屿状结构结晶,因此二次颗粒的表面形貌与cu箔形貌相似。而通过高倍sem可以观察到insb一次颗粒为纳米尺寸,通过紧密堆积形成了二次颗粒的岛屿状结构。同时纳米尺寸的insb一次颗粒说明即使insb具有较低的熔点(525.2℃),但依然不易团聚。
68.(3)insb多晶薄膜负极材料的充电/放电循环性能测试
69.本实施例制得的insb多晶薄膜薄膜负极材料的首次放电性能测试方法和步骤与实施例1步骤(2)所述相同,按照该方法进行充放电测试,如图6,7所示,得到该复合薄膜负极的首次充电容量为570.3mah/g,在1000次循环后仍有498.2mah/g的容量,容量保持率为92.6%。如图8所示,insb负极在-30℃与30℃之间反复切换也没有发生容量衰减,说明insb材料不仅具有极好的低温容量保持率,还具有极好的抗热冲击性能。如图9所示,insb负极能够在0.1a/g的条件下正常充放电,首次充电比容量为511.9mah/g,是常温条件下容量的91.1%。在250次充放电循环后insb负极仍有348.3mah/g的比容量,容量保持率为68.1%。
70.5、实施例5
71.(1)insb多晶薄膜负极材料的制备
72.本实施例的insb多晶薄膜负极材料的制备步骤与实施例1步骤(1)所述基本相同,所不同的是磁控溅射时间为30分钟。
73.(2)insb多晶薄膜负极材料的充电/放电循环性能测试
74.本实施例制得的insb多晶薄膜薄膜负极材料的首次放电性能测试方法和步骤与实施例1步骤(2)所述相同,按照该方法进行充放电测试,如图10、11所示,得到该复合薄膜负极的首次充电容量为628.5mah/g,在400次循环后仍有527.7mah/g的容量,容量保持率为90.6%。
75.6、实施例6
76.(1)insb多晶薄膜负极材料的制备
77.本实施例的insb多晶薄膜负极材料的制备步骤与实施例1步骤(1)所述基本相同,所不同的是磁控溅射仓内氩气气压为0.5pa。
78.(2)insb多晶薄膜负极材料的充电/放电循环性能测试
79.本实施例制得的insb多晶薄膜薄膜负极材料的首次放电性能测试方法和步骤与实施例1步骤(2)所述相同,按照该方法进行充放电测试,得到该复合薄膜负极的首次充电容量为585.4mah/g,在800次循环后仍有499.4mah/g的容量,容量保持率为85.3%。
80.7、实施例7
81.(1)insb多晶薄膜负极材料的制备
82.本实施例的insb多晶薄膜负极材料的制备步骤与实施例1步骤(1)所述基本相同,所不同的是磁控溅射仓内氩气气压为5.0pa。
83.(2)insb多晶薄膜负极材料的充电/放电循环性能测试
84.本实施例制得的insb多晶薄膜薄膜负极材料的首次放电性能测试方法和步骤与实施例1步骤(2)所述相同,按照该方法进行充放电测试,得到该复合薄膜负极的首次充电容量为607.6mah/g,在800次循环后仍有537.8mah/g的容量,容量保持率为88.5%。
85.8、实施例8
86.(1)insb多晶薄膜负极材料的制备
87.本实施例的insb多晶薄膜负极材料的制备步骤与实施例1步骤(1)所述基本相同,所不同的是磁控溅射时间为15分钟。
88.(4)insb多晶薄膜负极材料与lifepo4配对全电池的充电/放电循环性能测试
89.负极电极片采用步骤(1)中获得的insb多晶薄膜负极材料,正极电极片采用商用lifepo4。正极电极片的主要制备步骤如下:将商用电极片正极粉末、导电剂super-p和粘结剂pvdf(聚偏氟乙烯)以8:1:1的质量比混合,以nmp(n-甲基吡咯烷酮)为溶剂使用搅拌脱泡机搅拌30min制浆。将制得的正极浆料使用自动涂布机进行涂覆,集流体为al箔。再将涂覆的极片置于80℃的真空干燥箱中烘干12h备用。将备好的极片使用切片机切成不同直径的圆片来实现不同的正负极容量配比。在氩气气氛手套箱中,电解质为1mlipf
6-ec:dec:pc(1:1:1by vol),另加入10wt%fec的电解液,组装成lifepo4||insb全电池进行测试。测试温度为30℃和-10℃,充放电电流密度为1.0a g-1
,充放电截止电压为2.0v-3.4v(vs.li/li
+
)。
90.图12、13示出了本实施例制备的全电池的在-10℃条件下的充放电曲线,insb//lfp全电池进行小电流长循环时,全电池容量略有衰减,由首圈570mah/g衰减至第40圈的483mah/g。电流为1a/g循环时,由于副反应时间缩短,电池容量损耗减少,循环至140圈依然剩有359mah/g的容量,相比于第50圈的375mah/g,容量保持率约为95.7%,远高于常温容量保持率,甚至在循环400圈后依然有313mah/g的容量。
91.二、对比实施例
92.(1)insb非晶薄膜负极材料的制备与结构分析
93.采用超高真空磁控溅射系统(jgb-560,kyky)进行磁控溅射,将insb合金靶材安装在射频电源靶头上,磁控溅射功率设为50w;将磁控溅射仓抽真空至真空度达到1
×
10-4
pa后通入高纯氩气(纯度99.99%),控制气流大小为40sccm,仓内气压为0.5pa。
94.将电池级铜箔作为导电基体材料在超声波中分别使用蒸馏水、无水乙醇以及丙酮按顺序进行清洗处理掉导电基体材料(衬底)的表面油污及氧化物后,将该导电基体材料安装在溅射仓的样品基座上,并保持靶材与衬底的距离为10cm左右。
95.开通靶头电源,保持样品台以30rpm速度旋转以减少薄膜成分的不均匀性,溅射物沉积在导电基体材料上,溅射5分钟,得到溅射沉积后的insb非晶薄膜负极材料。
96.对本实施例所制备的insb非晶薄膜负极材料进行结构和物相分析,可知薄膜中不存在insb晶体结构。
97.(2)insb非晶薄膜负极材料的充放电循环性能测试
98.将磁控溅射制备的insb多晶薄膜负极材料作为工作电极进行性能测试,在高纯ar环境的手套箱(super 1220,上海米开罗那机电技术有限公司)中进行,水氧含量低于0.01ppm。以纯锂片作为对电极,使用1m lipf
6-ec:dec:pc(1:1:1by vol),另加入10wt%fec的电解液,组装成扣式电池进行性能测试。
99.测试条件:充放电电流密度为0.2a/g,充放电电压范围为0.01v~2.0v。充放电循环测试过程如下:首次循环时,电池首先恒流放电至0.01v,然后接着恒流充电至2.0v;从第二次循环开始,放电时从2.0v放电至0.01v,充电时从0.01v充电至2.0v。
100.通过上述电池测试条件及步骤进行测试(所用电池充放电测试系统为land ct2001a电池测试系统,武汉蓝和电子有限公司),得到制备的insb非晶薄膜负极的首次充电比容量仅为198.7mah/g。
101.通过实施例4与对比例的对比可知,多晶insb薄膜负极相较于非晶insb薄膜负极有着更好的容量以及倍率性能。实施例4制备的insb薄膜负极材料具有高首效、高倍率,高循环稳定性的优异表现。如上所述,便可较好地实现本发明,上述实施例仅为本发明的部分实施例,并非用来限定本发明的实施范围;即凡依本发明内容所作的均等变化与修饰,都为本发明权利要求所要求保护的范围所涵盖。