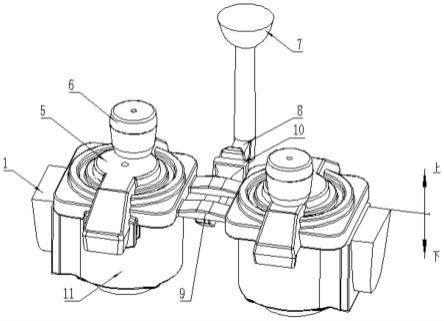
1.本发明属于铸造技术领域,具体涉及一种生产液压柱塞泵泵盖铸件的铸造方法。
背景技术:2.液压柱塞泵是液压系统的动力元件,属于液压系统的“心脏”部件,液压柱塞泵运行时内部液压油随负载变化存在高压,甚至交变冲击,要求泵盖铸件具备在高压下连续承压的要求,因此对泵盖内部和外观铸件的质量要求严格,首先泵盖外观薄壁处不能有穿透性砂或渣孔缺陷,其次内部不允许有缩孔、缩松、裂纹、气孔缺陷,再者内部油道和油腔必须洁净无夹砂、夹渣。由于柱塞泵泵盖铸件的材料为高牌号的球墨铸铁,为增加凝固时组织中的珠光体含量需要控制较低的碳当量(ce)和加入微量的合金元素,但较低的碳当量和合金加入增强了铁液的收缩倾向,易在铸件热节区或最后凝固区产生内部缩松、缩孔,还有泵盖内部油腔形状分层,结构复杂,需要砂芯成型,而制作的砂芯覆膜砂在浇注过程中受热燃烧产生大量气体,如果排气不通畅也容易在泵盖中心最后液相凝固区产生气孔或和缩松共存的气缩孔,直接造成铸铁本体组织出现疏松,泵盖铸件无法承压而直接报废。
3.传统的生产柱塞泵泵盖铸件的铸造工艺如附图1和附图2所示,泵盖铸件11的上顶面完全由盖板砂芯16形成,砂芯下芯到下砂型后,形成铸件的型腔被盖板砂芯16完全覆盖,人工下芯操作时视线被盖板砂芯遮挡,下芯定位芯头不易对准,发生砂芯与粘土砂型磕碰,特别容易发生粘土砂粒掉入型腔,浇注后在铸件底面形成砂孔缺陷;其次下芯操作时掉入型腔的散砂砂粒由于盖板砂芯覆盖中根本无法吹出来,铁液浇注后造成泵盖铸件底面薄壁处砂眼缺陷;由于盖板砂芯包覆了泵盖整个顶面,盖板砂芯体积较大,需要形成砂芯的覆膜砂用量较多,砂芯成本较高;同时由于盖板砂芯重量较重,形成铸件的砂芯全部组装为一个整体砂芯再下芯操作,砂芯重量有约40kg,操作者连续搬运、抓举下芯作业,劳动强度高,操作者容易疲劳;由于铸件顶面被密实热芯盖板砂芯包覆,浇注时形成砂芯的覆膜砂原料燃烧发气,无法顺利排出的气体会聚集在铸件最后凝固起的中心热节区,极易在泵盖铸件内部产生凝固收缩和气体共存的气缩孔缺陷。
技术实现要素:4.本发明的目的是解决传统生产柱塞泵泵盖铸件的铸造工艺存在的下芯困难、排气不通畅和容易出现铸造缺陷的技术问题,提出一种液压柱塞泵泵盖铸件的铸造方法。
5.为解决上述技术问题,本发明采用的技术方案是:
6.一种生产液压柱塞泵泵盖铸件的铸造方法,其包括下列步骤:
7.1)铸造工艺设计:泵盖铸件外形采用粘土砂水平造型线机器造型,内腔和油道用覆膜砂热芯盒法制作;考虑砂芯放入粘土砂型腔中的稳定性,泵盖铸件分型面设置在顶面方形法兰下端位置;采用三维建模软件进行砂芯组装和定位芯头设计,并仿真优化砂芯组装和下芯,形成泵盖铸件中心孔的各个砂芯中间设计直径8mm-20mm的贯通的排气孔,铸件顶面形状局部采用热芯盒砂芯,其他由上砂型中粘土砂形成,砂芯单独制作后,组装为两个
砂芯组合体,然后依次分别放置在粘土砂下砂型中;内浇道从分型面进入型腔,浇注系统采用半封闭式;中心热节区采用微型发热冒口进行补缩,实现由铸件到发热冒口的顺序凝固;
8.2)模具制作:根据工艺设计,保证精度前提下制作金属的泵盖外形型板模具和内腔热芯盒模具,在泵盖铸件热节顶面对应的型板模具上做出点补缩自发热冒口的定位杆;
9.3)砂芯制作和组装:分别用覆膜砂和热芯盒模具制作形成泵盖铸件内腔的若干个内腔油道砂芯,所述内腔油道砂芯通过抽芯机构做出排气孔,热芯盒模具固化温度230-250℃,把若干个独立的内腔油道砂芯再组装为两个砂芯组合体,其中几个内腔油道砂芯组装在长条形状盖板砂芯上形成第二砂芯组合体,其余组装为第一砂芯组合体,砂芯成型面浸涂铸铁涂料然后烘干,涂料层厚度0.15-0.2mm,烘干温度190-200℃;
10.4)造型:泵盖上型板模具进入造型机前在点补缩发热冒口定位杆处放置发热冒口,通过造型主机填砂和紧实后,发热冒口预埋在上砂型中,使用上、下型板模具分别造出铸件外形上、下砂型;
11.5)下芯:将步骤3)组装好的两个砂芯组合体按芯头定位依次放置到下箱砂型中;通过长条形状盖板砂芯和下箱砂型之间设计的敞开空挡使用压缩空气枪吹出下砂型中散落的砂粒,防止下芯时掉落的散砂在铸件地面形成砂眼缺陷;
12.6)合箱:造型设备利用砂箱上自带的销子和销套配合将上、下箱砂型组合形成铸件完整的型腔;
13.7)铁液熔炼:熔炼合格铁液,球化处理,控制浇铸温度1380-1420℃,每型浇铸时间14-16s;
14.8)浇注:浇铸时添加重量占比0.15%随流孕育剂,浇铸后2h冷却后震动落砂;
15.9)清理:首先去除泵盖铸件浇冒系统,接着进行粗抛丸处理,抛丸时间8-10min,然后打磨光洁浇冒口和分型线,最后进行精抛丸处理,抛丸时间12-15min;
16.10)检测:首先进行泵盖铸件外观和内部油腔100%进行目视检查,薄壁区不允许有砂孔、渣孔、有视觉可见的粘砂、外观裂纹,内部比较细小的油道使用内窥镜100%检测,不允许有粘砂结疤、断芯、孔洞,加工区允许有可切屑掉的空洞缺陷;然后分别抽取浇铸第一型铸件、中间型铸件和末尾型铸件,用锯床解剖进行泵盖内部检测,不允许有可见的内部缩松、缩孔和气孔缺陷。
17.本发明的有益效果是:
18.1、本发明把固定油道砂芯和形成泵盖顶面的盖板砂芯减小设计为长条形状,较大减小了砂芯体积,减少了制作砂芯的覆膜砂用量,节约成本;
19.2、本发明简化顶面盖板砂芯为长条形状,下芯作业后长条形状砂芯两侧型腔是敞开的,利于检查砂芯是否到位和利于吹出型腔内的散砂,避免泵盖尺寸形状不合格,降低泵盖外观砂眼缺陷;
20.3、本发明砂芯分块制作后组装为两个砂芯组合体,然后依次把两个砂芯组合体单独依次下芯操作,降低下芯操作时单个组装砂芯的重量,降低劳动强度;
21.4、本发明对形成泵盖型腔砂芯内部做出贯穿排气孔,并与上砂型外界联通,对中心热节采用点补缩发热冒口进行补缩,消除铸件中心区的由砂芯发气和液相热节共生形成的气缩孔缺陷。
附图说明
22.图1是现有泵盖铸造工艺方案示意图;
23.图2是现有盖板砂芯下芯到下砂型中的示意图;
24.图3是本发明方案的示意图;
25.图4是图3的俯视图;
26.图5是图4中的a-a剖视图;
27.图6是本发明中第一砂芯组合体和第二砂芯组合体依次下芯示意图;
28.图7是本发明中砂芯组合体在下箱砂型中下芯后示意图;
29.图8是本发明上、下砂型合箱示意图;
30.图中:1-1#砂芯,2-2#砂芯,3-3#砂芯,4-4#砂芯,5-长条形状盖板砂芯,6-微型发热冒口,7-浇口杯和直浇道,8-横浇道,9-内浇道,10-过滤片,11-铸件,12-第一砂芯组合体,13-第二砂芯组合体,14-上箱砂型,15-下箱砂型,16-传统工艺的盖板砂芯。
具体实施方式
31.下面结合附图和实施例对本发明进行详细描述。
32.如图3~图8所示,本实施例中的一种生产液压柱塞泵泵盖铸件的铸造方法,其包括下列步骤:
33.1)铸造工艺设计:泵盖铸件外形采用粘土砂水平造型线机器造型,内腔和油道用覆膜砂热芯盒法制作;考虑砂芯放入粘土砂型腔中的稳定性,泵盖铸件分型面设置在顶面方形法兰下端位置,如图3所示;采用三维建模软件进行砂芯组装和定位芯头设计,如图4、图5所示;并仿真优化砂芯组装和下芯,形成泵盖铸件中心孔的各个砂芯中间设计直径8mm-20mm的贯通的排气孔;铸件顶面形状局部采用热芯盒砂芯,其他由上砂型中粘土砂形成,砂芯分别单独制作后,组装为两个砂芯组合体,然后依次分别放置在粘土砂下砂型中;内浇道9从分型面进入型腔,浇注系统采用半封闭式;中心热节区采用微型发热冒口6进行补缩,实现由铸件到发热冒口的顺序凝固;
34.2)模具制作:根据工艺设计,保证精度前提下制作金属的泵盖外形型板模具和内腔热芯盒模具,在泵盖铸件热节顶面对应的型板模具上做出点补缩自发热冒口的定位杆;在第二砂芯组合体13上面中心位置由造型线上扎气孔机扎出与外界联通排气孔;
35.3)砂芯制作和组装:分别用覆膜砂和热芯盒模具制作形成泵盖铸件内腔的5个内腔油道砂芯,即1#砂芯1、2#砂芯2、3#砂芯3、4#砂芯4和长条形状盖板砂芯5,上述5个内腔油道砂芯通过抽芯机构做出排气孔,热芯盒模具固化温度230-250℃,把5个独立的内腔油道砂芯再组装为两个砂芯组合体12、13,内腔油道砂芯即2#砂芯2、3#砂芯3、4#砂芯4组装在长条形状盖板砂芯5上形成第二砂芯组合体13,其余组装为第一砂芯组合体12,砂芯成型面浸涂铸铁涂料然后烘干,涂料层厚度0.15-0.2mm,烘干温度190-200℃;检查砂芯组合体中心排气孔贯通无堵塞;
36.4)造型:泵盖上型板模具进入造型机前在点补缩发热冒口定位杆处放置微型发热冒口6,通过造型主机填砂和紧实后,微型发热冒口6预埋在上砂型中,使用上、下型板模具分别造出铸件外形上、下砂型;
37.5)下芯:将步骤3)组装好的两个砂芯组合体12、13按芯头定位依次放置到下箱砂
型15中;通过长条形状盖板砂芯5和下箱砂型15之间设计的敞开空挡使用压缩空气枪吹出下砂型中散落的砂粒,防止下芯时掉落的散砂在铸件地面形成砂眼缺陷;同时通过长条形状盖板砂芯5与下箱砂型15之间敞开的空挡检测砂芯是否放置到位,避免泵盖铸件形状和尺寸偏差;
38.6)合箱:造型设备利用砂箱上自带的销子和销套配合将上箱砂型14与下箱砂型15组合形成铸件完整的型腔;
39.7)铁液熔炼:熔炼合格铁液,球化处理,控制浇铸温度1380-1420℃,每型浇铸时间14-16s;
40.8)浇注:浇铸时添加重量占比0.15%随流孕育剂,浇铸后2h冷却后震动落砂;
41.9)清理:首先去除泵盖铸件11上连接的浇口杯和直浇道7、内浇道9和微型发热冒口6,接着进行粗抛丸处理,抛丸时间8-10min,然后打磨光洁浇冒口和分型线,最后进行精抛丸处理,抛丸时间12-15min;
42.10)检测:首先进行泵盖铸件11外观和内部油腔100%进行目视检查,薄壁区不允许有砂孔、渣孔、有视觉可见的粘砂、外观裂纹,内部比较细小的油道使用内窥镜100%检测,不允许有粘砂结疤、断芯、孔洞,加工区允许有可切屑掉的空洞缺陷;然后分别抽取浇铸第一型铸件、中间型铸件和末尾型铸件,用锯床解剖进行泵盖内部检测,不允许有可见的内部缩松、缩孔和气孔缺陷。
43.本发明能生产出内部致密和外观光洁的柱塞泵泵盖铸件,同时实现降低生产成本、降低铸件废品、较低劳动强度的有益效果。本发明提出了泵盖铸件顶面砂芯设计为长条形状,长条形状盖板砂芯起到固定其他砂芯和定位整体的作用,由于长条形状盖板砂芯体积与现有盖板形砂芯相比,其体积减小,节约成本;同时长条形状盖板砂芯使下芯后砂型腔是敞开的,利于观察砂芯是否到位和吹出型腔内掉落的散砂砂粒,防止泵盖铸件底面薄壁处砂眼缺陷;其次长条形状盖板砂芯体积减小使条状砂芯本身重量下降,为了再次降低操作者单次搬运和抓取砂芯的重量,再把形成内腔的砂芯分块制作后,组装为两个砂芯组合体,然后把第一砂芯组合体和第二砂芯组合体依次单独下芯作业,降低下芯操作时单个砂芯体的重量,降低下芯操作的劳动强度;铸件顶面盖板减小为条状,有利于铁液浇注时排气;为防止对于中心环形热节出现气缩孔缺陷,在砂芯中间做出排气孔,同时采用点补缩发热冒口进行补缩;由于点补缩发热冒口体积小,铁液利用率高,冒口易于去除,后清理时降低难度。