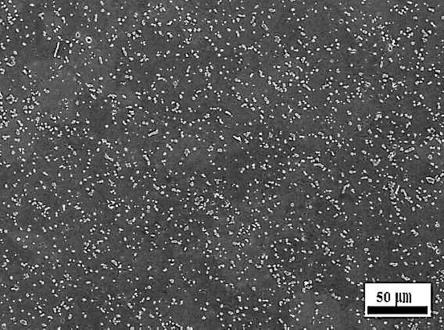
1.本发明属于铝合金技术领域,具体涉及一种利用钒辅助硼化处理制备的高强高导铝合金杆及制备方法。
背景技术:2.随着电能需求的增大,对输电线的要求也越来越高,因此出现了一批节能类导线,如钢芯铝绞线、铝合金芯铝绞线、中强度全铝合金绞线等。铝相较于铜,具有比密度大、比强度高、导电导热性能好等优点,在电力运输方面具有极大的应用前景。
3.目前,铝合金导电材料广泛应用于架空输电线、大跨度电线、电力电缆和通信电缆等领域。亚共晶al-si合金具有优异的力学性能和较好的导电性,常被用作架空传输导体。但由于导电性与力学性能(特别是导电性与强度)之间的矛盾,高导电率与良好的力学性能难以同时获得,限制了其在电气工程领域的应用,成为限制推广应用的瓶颈问题。
4.专利cn110629076b公开了一种元素组成含有al、si、mg、fe、cu、zn、la、ga、mn、ti、b的铝合金杆材,是一种高导电铝合金材料,其主要组成元素的含量极低,特别是si元素含量不高于0.08%,相应合金导电率为≥63.5%,抗拉强度≥83mpa,屈服强度≥52mpa,伸长率≥42%。
5.专利cn107236874b公开了一种高性能铝合金杆,同样其组成元素含量均较低,其中si元素含量≤0.04%,且含有稀土元素,该合金杆的导电率达到62.5-63%iacs,抗拉强度160-290mpa。
6.专利cn106939384b公开了一种铝合金杆及其制备方法,同样该合金杆的主要元素组成含量均低于1.1%,降低电阻率6-10%,宏观晶粒度达到6-8级,未对其进行力学性能的测量。
7.上述专利的共同特点是合金的组成元素含量较低,且未对微量的过渡族金属元素进行研究。在固溶性相同的前提下,过渡族金属元素(v、ti、cr、zr 等)对铝导体导电性的影响大于铁(fe)、镁(mg)、硅(si)等。过渡族金属元素在铝合金中常以固溶形式存在,引起 al基体晶格畸变,增加电子散射几率,严重损害合金导电率。通常条件下,硼化处理过程中b元素与熔体中的过渡族金属元素反应生成相应硼化物,过渡族金属硼化物的密度大于al的密度而比较容易沉于熔体底部,从而最大程度减小了过渡族金属元素对导电率的损害作用。但是传统的硼化处理效率低下,无法达到现工业化要求。
技术实现要素:8.本发明要解决的技术问题是:针对现有硼化处理技术中存在的不足,提供一种利用钒辅助硼化处理制备的高强高导铝合金杆,相比于传统的硼化处理,更大程度减小了过渡族金属元素(v、ti、cr、zr 等)在铝基体中固溶的含量,从而减小其对导电率的损害作用,同时还细化了晶粒,铝合金的强度高、导电率高;本发明还提供其制备方法,工艺简单、生产高效。
9.本发明所述的利用钒辅助硼化处理制备的高强高导铝合金杆,其元素组分与质量百分比为:si 3.9-4.1%,mg 0-0.8%,fe 0-0.3%,cu 0-0.2%,b 0.06-0.12%,v 0.03-0.09%,其余为al。
10.一种利用钒辅助硼化处理制备的高强高导铝合金杆的制备方法,先将纯硅、纯镁、al-10%fe中间合金、al-50%cu中间合金中的一种或多种与纯铝混合熔融,再依次加入al-3%b中间合金和al-10%v中间合金进行硼化处理,然后依次进行浇铸、均匀化热处理和热挤压、固溶时效,得到高强高导铝合金导电杆。
11.所述纯铝的纯度高于99.7%,所述纯硅、纯镁纯度均高于99.9%。
12.所述al-10%fe中间合金中fe质量含量为10%,制备方法为:(1)按照质量比al:fe=9:1称取铝料和铁料,铝料和铁料的纯度均高于99.9%;(2)将铝料熔化后,加入精炼剂,得到熔融物;(3)将熔融物升温到910
±
5℃,保温5-10min,然后在上述熔融物高度的1/2以下位置加入铁料,待铁料熔化后,搅拌,得到混合物;(4)将混合物进行去氢处理,浇铸,即得al-10%fe中间合金。
13.其中,精炼剂采用行业内常规精炼剂即可,例如c2cl6、氯化钠、氯化钾等。
14.所述al-50%cu中间合金中cu质量含量为50%,制备方法为:(1)按照质量比cu: al=3:1,将铜料加入到温度为950
±
5℃的铝液的熔炼炉中(铝液量为3/5熔炼炉容量),保温1-2h,让铜料充分溶解,得到w(cu)=75%的al-75%cu中间合金,其中铜料的纯度高于99.9%;(2)当al-75%cu中间合金配好后,加入温度为760
±
5℃的电解铝液,稀释到w(cu)=50%的化学成分要求,打上覆盖剂,保温20-40分钟,加入打渣剂出渣,并将表面浮渣扒除,得到铝熔体;(3)将精炼剂用纯度99.99%的氮气喷吹法加入到铝熔体中,对铝熔体进行再一次的除气、除渣、净化处理,最后浇铸,即得al-50%cu中间合金。
15.其中,覆盖剂采用行业内常规覆盖剂即可,例如碱性覆盖剂,以cao-al2o
3-sio2和cao-mgo-al2o
3-sio2系粉体料为代表。
16.打渣剂采用行业内常规打渣剂即可,例如clpbd打渣剂。
17.精炼剂采用行业内常规精炼剂即可,例如c2cl6、氯化钠、氯化钾等。
18.所述al-3%b中间合金中b质量含量为3%,制备方法为:(1)取纯铝、粉状kbf4(粒度160目-300目),按照质量比al:b=97:3准备好配料;(2)将铝块和40-80%的粉状kbf4使用中频感应炉熔炼,将温度升温至1000
±
5℃,电磁搅拌1-3min,使alb2转变成alb
12
,降低熔体粘度;(3)然后将熔体温度降至750
±
5℃,再加入剩余粉状kbf4,并对熔体进行电磁搅拌,获得所需al-3%b中间合金熔体;(4)待反应完成后,将熔体加热至100
±
5℃,电磁搅拌1-3min后,将熔体浇入模具,凝固成al-3%b中间合金。
19.所述al-10%v中间合金中v质量含量为10%,制备方法为:(1)按照质量比al:v=15:85确定原料质量比v2o5:al:caf2=1:0.61:0.09,将上述原料均匀混合;
(2)将混合均匀的原料放在石墨坩埚中,在振动平台上振动3min使粉料振实,点火进行自蔓延燃烧合成,冷却5h后拆炉得到高钒含量的al-v中间合金一次铸锭,然后对其表面进行喷丸或喷砂处理厚破碎成100-150mm规格的高钒含量中间合金颗粒;(3)按照成品al-10%v中间合金设计成分配比al:v=9:1,得到al-10%v中间合金配比;(4)将上述配料比例配制的铝块放入坩埚底部,上部放入100-150mm规格高钒含量中间合金颗粒,再抽真空并通入氩气保护下进行真空熔炼,待全部熔化后浇铸,随炉冷却至200℃以下出炉,即得al-10%v中间合金。
20.本发明优选的,混合熔融和硼化处理温度为720-750℃。
21.硼化处理时,利用b与熔体中v、ti、cr、zr 等杂质元素的反应,可以降低杂质元素含量,有利于提高合金的导电率;而且在v辅助硼化处理下,能够促进常规硼化处理进行,更大程度上降低杂质元素含量,并能够细化晶粒。
22.本发明优选的,浇铸得到的铸棒尺寸为直径80-85mm、高度0.5-0.55m,最优选为直径80mm、高度0.5m。
23.本发明优选的,均匀化热处理温度为520
±
5℃,时间为3-6h。
24.本发明优选的,热挤压温度为500
±
5℃,挤压速度为1-3mm/s,冷却方式为空冷。
25.本发明优选的,固溶温度520
±
5℃,时间为1-3h,时效温度240
±
5℃,时间12-24h。
26.作为一种优选方案,所述制备方法包括以下步骤:(1)备料:按照原料配比准备纯铝、纯硅、纯镁、al-10%fe中间合金、al-50%cu中间合金、al-3%b中间合金、al-10%v中间合金;(2)熔融:将纯铝熔化并升温至720-750℃,然后向熔体中加入纯硅、纯镁、al-10%fe中间合金、al-50%cu中间合金中的一种或多种,搅拌均匀后保温5-10min,得到熔体;(3)硼化:将熔体温度保持在720-750℃,加入al-3%b中间合金,搅拌均匀后,再加入al-10%v中间合金,搅拌均匀,除去杂质熔渣,保温15-20min,得到硼化处理后的熔体;(4)浇铸:将硼化处理后的熔体进行浇铸,得到直径80-85mm、高度0.5-0.55m的铸棒;(5)热处理和热挤压:将铸棒在520
±
5℃温度下进行均匀化热处理3-6h,然后在500
±
5 ℃挤压温度条件下以1-3mm/s的挤压速度挤成实心棒材,空冷后,得到铝合金挤压杆;(6)固溶时效:将铝合金挤压杆进行固溶时效热处理,固溶温度520
±
5℃,时间为1-3h,时效温度240
±
5℃,时间12-24h,得到高强高导铝合金杆。
27.本发明主要围绕铝合金中过渡族金属元素严重损害合金导电率的问题,纯铝中含有微量v、ti、cr、zr 等元素,杂质元素溶解在铝基体中,会造成晶格畸变,改变畸变区电场的周期性,增加的电子散射概率,从而降低导电性。
28.与常规硼化处理相比,本发明在熔体处理过程中加入硼和钒进行钒辅助硼化处理,促进硼化处理反应过程中形成更多的硼化物,能够更大程度减小过渡族金属元素(v、ti、cr、zr 等)在铝基体中固溶的含量,减小其对导电率的损害作用,除此之外,还可以细化晶粒。
29.本发明添加v辅助硼化处理,在钒的高浓度和低反应活化能的驱动下,alb2容易与
v反应生成(al,v)b2。一方面v与硼化物中未反应的b发生反应,因为过渡族金属元素可以相互替代,促进了更多过渡族金属元素掺杂到常规硼化物中,尤其是zr、ti、cr元素;另一方面v与过量的b反应,然后将ti、zr、cr 掺杂到(al,v)b2中,减少未反应的b对导电率的影响。同时,添加v还能增加了zr、ti、cr的反应浓度差,改变硼反应平衡,促进反应进行,提高硼化处理的效率。
30.此外,少量的添加过渡族金属元素钒还可以改善si的形貌,最后利用热处理、热挤压变形改变共晶si、alfesi、mg2si 等第二相的颗粒尺寸和分布,使其呈现细小颗粒状、弥散分布,在保证合金优异力学性能的同时使其具有良好的导电率。
31.与现有技术相比,本发明的有益效果如下:(1)本发明在合金熔炼过程中向铝熔体中添加适量合金化元素并进行钒辅助硼化处理,能够最大程度上降低杂质元素并细化晶粒,后浇铸成锭,然后进行热挤压变形及热处理,一方面改善了共晶si、mg2si及alfesi等第二相颗粒尺寸及分布,另一方面强化合金力学性能,获得一种高强高导铝合金导电杆,该合金杆的室温极限拉伸强度≥250mpa,延伸率≥20%,导电率≥58%iacs,满足大部分架空输电线的实际性能需求;(2)本发明通过成分设计、改善熔体处理工艺,得到了一种钒辅助的硼化处理新工艺,该工艺大大提高了硼化处理的效率,细化了晶粒,改善了铝合金力学性能和导电率匹配差的问题,且处理工艺简单、生产效率高、成本低,处理后的al-si系合金杆元素组成含量较高,同时具有优异的力学性能和良好的导电性,属于高强、高导铝合金,满足当今架空输电线对铝合金的综合性能需求,适合大规模生产及应用。
附图说明
32.图1为本发明实施例2制备的铝合金杆的金相试样fesem图。
具体实施方式
33.下面结合实施例对本发明作进一步说明,但本发明的保护范围不仅限于此,该领域专业人员对本发明技术方案所作的改变,均应属于本发明的保护范围内。实施例中所使用的原料,如无特别说明,均为本领域常规市售原料;实施例中所使用的工艺方法,如无特别说明,均为本领域常规方法。
34.实施例中所使用的纯铝纯度高于99.7%,纯硅、纯镁纯度均高于99.9%,采用市售产品。
35.实施例中所使用的al-10%fe中间合金中fe质量含量为10%,制备方法为:(1)按照质量比al:fe=9:1称取铝料和铁料,铝料和铁料的纯度均高于99.9%;(2)将铝料熔化后,加入c2cl6精炼剂,得到熔融物;(3)将熔融物升温到910
±
5℃,保温8min,然后在上述熔融物高度的1/2以下位置加入铁料,待铁料熔化后,搅拌,得到混合物;(4)将混合物进行去氢处理,浇铸,即得al-10%fe中间合金。
36.实施例中所使用的al-50%cu中间合金中cu质量含量为50%,制备方法为:(1)按照质量比cu: al=3:1,将铜料加入到温度为950
±
5℃的铝液的熔炼炉中(铝液量为3/5熔炼炉容量),保温2h,让铜料充分溶解,得到w(cu)=75%的al-75%cu中间合金,其
中铜料的纯度高于99.9%;(2)当al-75%cu中间合金配好后,加入温度为760
±
5℃的电解铝液,稀释到w(cu)=50%的化学成分要求,打上碱性覆盖剂,保温30分钟,加入clpbd打渣剂出渣,并将表面浮渣扒除,得到铝熔体;(3)将c2cl6精炼剂用纯度99.99%的氮气喷吹法加入到铝熔体中,对铝熔体进行再一次的除气、除渣、净化处理,最后浇铸,即得al-50%cu中间合金。
37.实施例中所使用的al-3%b中间合金中b质量含量为3%,制备方法为:(1)取纯铝、粉状kbf4(粒度200目),按照质量比al:b=97:3准备好配料;(2)将铝块和70%的粉状kbf4使用中频感应炉熔炼,将温度升温至1000
±
5℃,电磁搅拌2min,使alb2转变成alb
12
,降低熔体粘度;(3)然后将熔体温度降至750
±
5℃,再加入剩余粉状kbf4,并对熔体进行电磁搅拌,获得所需al-3%b中间合金熔体;(4)待反应完成后,将熔体加热至100
±
5℃,电磁搅拌2min后,将熔体浇入模具,凝固成al-3%b中间合金。
38.实施例中所使用的al-10%v中间合金中v质量含量为10%,制备方法为:(1)按照质量比al:v=15:85确定原料质量比v2o5:al:caf2=1:0.61:0.09,将上述原料均匀混合;(2)将混合均匀的原料放在石墨坩埚中,在振动平台上振动3min使粉料振实,点火进行自蔓延燃烧合成,冷却5h后拆炉得到高钒含量的al-v中间合金一次铸锭,然后对其表面进行喷丸或喷砂处理厚破碎成120mm规格的高钒含量中间合金颗粒;(3)按照成品al-10%v中间合金设计成分配比al:v=9:1,得到al-10%v中间合金配比;(4)将上述配料比例配制的铝块放入坩埚底部,上部放入120mm规格高钒含量中间合金颗粒,再抽真空并通入氩气保护下进行真空熔炼,待全部熔化后浇铸,随炉冷却至200℃以下出炉,即得al-10%v中间合金。
39.实施例1一种利用钒辅助硼化处理制备的高强高导铝合金杆(al-4si合金),其元素组分与质量百分比如下:si 4.0%,b 0.06%,v 0.06%,其余为al。
40.制备方法包括以下步骤:(1)备料:按照原料配比准备纯铝、纯硅、al-3%b中间合金、al-10%v中间合金;(2)熔融:将纯铝熔化并升温至720℃,然后依次向熔体中加入纯硅,搅拌均匀后保温5min,得到熔体;(3)硼化:将熔体温度保持在720℃,加入al-3%b中间合金,搅拌均匀后,再加入al-10%v中间合金,搅拌均匀,用漏勺除去杂质熔渣,保温15min,得到硼化处理后的熔体;硼化处理时,利用b与熔体中v、ti、cr、zr等杂质元素的反应,降低杂质元素含量,有利于提高合金的导电率;而且在v辅助硼化处理下,能够促进常规硼化处理进行,更大程度上降低杂质元素含量,并能够细化晶粒;(4)浇铸:将硼化处理后的熔体进行浇铸,得到直径 80mm、高度0.5m的铸棒;(5)热处理和热挤压:将铸棒放入热处理炉中,在520
±
5℃温度下进行均匀化热处
理3h,然后在500
±
5℃挤压温度条件下以2mm/s的挤压速度挤成实心棒材,空冷后,得到铝合金挤压杆;(6)固溶时效:将铝合金挤压杆进行固溶时效热处理,固溶温度520
±
5℃,时间为1h,时效温度240
±
5℃,时间12h,得到高强高导的al-4si合金杆。
41.实施例2一种利用钒辅助硼化处理制备的高强高导铝合金杆(al-3.9si-0.8mg-0.2fe合金),其元素组分与质量百分比如下:si 3.9%,mg 0.8%,fe 0.2%,b 0.09%,v 0.09%,其余为al。
42.制备方法包括以下步骤:(1)备料:按照原料配比准备纯铝、纯硅、纯镁、al-10%fe中间合金、al-3%b中间合金、al-10%v中间合金;(2)熔融:将纯铝熔化并升温至750℃,然后依次向熔体中加入纯硅、纯镁、al-10%fe中间合金,搅拌均匀后保温10min,得到熔体;(3)硼化:将熔体温度保持在750℃,加入al-3%b中间合金,搅拌均匀后,再加入al-10%v中间合金,搅拌均匀,用漏勺除去杂质熔渣,保温20min,得到硼化处理后的熔体;硼化处理时,利用b与熔体中v、ti、cr、zr 等杂质元素的反应,降低杂质元素含量,有利于提高合金的导电率;而且在v辅助硼化处理下,能够促进常规硼化处理进行,更大程度上降低杂质元素含量,并能够细化晶粒;(4)浇铸:将硼化处理后的熔体进行浇铸,得到直径 85mm、高度0.55m的铸棒;(5)热处理和热挤压:将铸棒放入热处理炉中,在520
±
5℃温度下进行均匀化热处理3h,然后在500
±
5℃挤压温度条件下以1mm/s的挤压速度挤成实心棒材,空冷后,得到铝合金挤压杆;(6)固溶时效:将铝合金挤压杆进行固溶时效热处理,固溶温度520
±
5℃,时间为2h,时效温度240
±
5℃,时间16h,得到高强高导的al-3.9si-0.8mg-0.2fe合金杆。
43.将实施例2制备的铝合金杆制成金相试样,并利用fesem分析其微观组织,如图1所示。从图1可以看出,合金中的共晶si、mg2si及alfesi等第二相呈细小颗粒状、弥散分布在铝基体上,相比于粗大板片状或针条状的第二相,颗粒状的第二相对电子流散射作用明显减小,对铝基体的割裂作用也明显减小,故合金的导电率和力学性能均较高。
44.实施例3一种利用钒辅助硼化处理制备的高强高导铝合金杆(al-4.1si-0.3mg-0.1fe-0.2cu合金),其元素组分与质量百分比如下:si 4.1%,mg 0.3%,fe 0.1%,cu 0.2%,b 0.12%,v 0.06%,其余为al。
45.制备方法包括以下步骤:(1)备料:按照原料配比准备纯铝、纯硅、纯镁、al-10%fe中间合金、al-50%cu中间合金、al-3%b中间合金、al-10%v中间合金;(2)熔融:将纯铝熔化并升温至750℃,然后依次向熔体中加入纯硅、纯镁、al-10%fe中间合金、al-50%cu中间合金,搅拌均匀后保温8min,得到熔体;(3)硼化:将熔体温度保持在750℃,加入al-3%b中间合金,搅拌均匀后,再加入al-10%v中间合金,搅拌均匀,用漏勺除去杂质熔渣,保温18min,得到硼化处理后的熔体;硼化
处理时,利用b与熔体中v、ti、cr、zr 等杂质元素的反应,降低杂质元素含量,有利于提高合金的导电率;而且在v辅助硼化处理下,能够促进常规硼化处理进行,更大程度上降低杂质元素含量,并能够细化晶粒;(4)浇铸:将硼化处理后的熔体进行浇铸,得到直径 80mm、高度0.5m的铸棒;(5)热处理和热挤压:将铸棒在520
±
5℃温度下进行均匀化热处理4h,然后在500
±
5℃挤压温度条件下以3mm/s的挤压速度挤成实心棒材,空冷后,得到铝合金挤压杆;(6)固溶时效:将铝合金挤压杆进行固溶时效热处理,固溶温度520
±
5℃,时间为2h,时效温度240
±
5℃,时间18h,得到高强高导的al-4.1si-0.3mg-0.1fe-0.2cu合金杆。
46.实施例4一种利用钒辅助硼化处理制备的高强高导铝合金杆(al-4si-0.6mg-0.3fe-0.2cu合金),其元素组分与质量百分比如下:si 4.0%,mg 0.6%,fe 0.3%,cu 0.2%,b 0.06%,v 0.03%,其余为al。
47.制备方法包括以下步骤:(1)备料:按照原料配比准备纯铝、纯硅、纯镁、al-10%fe中间合金、al-50%cu中间合金、al-3%b中间合金、al-10%v中间合金;(2)熔融:将纯铝熔化并升温至730℃,然后依次向熔体中加入纯硅、纯镁、al-10%fe中间合金、al-50%cu中间合金,搅拌均匀后保温10min,得到熔体;(3)硼化:将熔体温度保持在730℃,加入al-3%b中间合金,搅拌均匀后,再加入al-10%v中间合金,搅拌均匀,用漏勺除去杂质熔渣,保温20min,得到硼化处理后的熔体;硼化处理时,利用b与熔体中v、ti、cr、zr 等杂质元素的反应,降低杂质元素含量,有利于提高合金的导电率;而且在v辅助硼化处理下,能够促进常规硼化处理进行,更大程度上降低杂质元素含量,并能够细化晶粒;(4)浇铸:将硼化处理后的熔体进行浇铸,得到直径 80mm、高度0.5m的铸棒;(5)热处理和热挤压:将铸棒在520
±
5℃温度下进行均匀化热处理5h,然后在500
±
5℃挤压温度条件下以2mm/s的挤压速度挤成实心棒材,空冷后,得到铝合金挤压杆;(6)固溶时效:将铝合金挤压杆进行固溶时效热处理,固溶温度520
±
5℃,时间为3h,时效温度240
±
5℃,时间24h,得到高强高导的al-4si-0.6mg-0.3fe-0.2cu合金杆。
48.实施例5一种利用钒辅助硼化处理制备的高强高导铝合金杆(al-4si-0.8mg-0.2fe-0.1cu合金),其元素组分与质量百分比如下:si 4.0%,mg 0.8%,fe 0.2%,cu 0.1%,b 0.09%,v 0.09%,其余为al。
49.制备方法包括以下步骤:(1)备料:按照原料配比准备纯铝、纯硅、纯镁、al-10%fe中间合金、al-50%cu中间合金、al-3%b中间合金、al-10%v中间合金;(2)熔融:将纯铝熔化并升温至750℃,然后依次向熔体中加入纯硅、纯镁、al-10%fe中间合金、al-50%cu中间合金,搅拌均匀后保温10min,得到熔体;(3)硼化:将熔体温度保持在750℃,加入al-3%b中间合金,搅拌均匀后,再加入al-10%v中间合金,搅拌均匀,用漏勺除去杂质熔渣,保温20min,得到硼化处理后的熔体;硼化处理时,利用b与熔体中v、ti、cr、zr 等杂质元素的反应,降低杂质元素含量,有利于提高合
金的导电率;而且在v辅助硼化处理下,能够促进常规硼化处理进行,更大程度上降低杂质元素含量,并能够细化晶粒;(4)浇铸:将硼化处理后的熔体进行浇铸,得到直径 85mm、高度0.55m的铸棒;(5)热处理和热挤压:将铸棒在520
±
5℃温度下进行均匀化热处理6h,然后在500
±
5℃挤压温度条件下以2mm/s的挤压速度挤成实心棒材,空冷后,得到铝合金挤压杆;(6)固溶时效:将铝合金挤压杆进行固溶时效热处理,固溶温度520
±
5℃,时间为3h,时效温度240
±
5℃,时间16h,得到高强高导的al-4si-0.8mg-0.2fe-0.1cu合金杆。
50.对比例1本对比例制备纯铝金属杆,步骤如下:(1)备料:纯铝;(2)熔融:将纯铝熔化并升温至750℃,搅拌均匀后保温2min,得到熔体;(3)浇铸:将熔体进行浇铸,得到直径80mm、高度0.5m的铸棒;(4)热处理和热挤压:将铸棒在520
±
5℃温度下进行均匀化热处理6h,然后在500
±
5℃挤压温度条件下以2mm/s的挤压速度挤成实心棒材,空冷后,得到纯铝挤压杆;(6)固溶时效:将纯铝挤压杆进行固溶时效热处理,固溶温度520
±
5℃,时间为3h,时效温度240
±
5℃,时间16h,得到纯铝金属杆。
51.对比例2本对比例与实施例5相比,不进行硼化处理,制备铝合金杆(al-4si-0.8mg-0.2fe-0.1cu合金),其元素组分与质量百分比如下:si 4.0%,mg 0.8%,fe 0.2%,cu 0.1%,b 0.09%,v 0.09%,其余为al。
52.制备方法包括以下步骤:(1)备料:按照原料配比准备纯铝、纯硅、纯镁、al-10%fe中间合金、al-50%cu中间合金;(2)熔融:将纯铝熔化并升温至750℃,然后依次向熔体中加入纯硅、纯镁、al-10%fe中间合金、al-50%cu中间合金,搅拌均匀后保温10min,得到熔体;(3)浇铸:将熔体进行浇铸,得到直径 80mm、高度0.5m的铸棒;(4)热处理和热挤压:将铸棒在520
±
5℃温度下进行均匀化热处理6h,然后在500
±
5℃挤压温度条件下以2mm/s的挤压速度挤成实心棒材,空冷后,得到铝合金挤压杆;(5)固溶时效:将铝合金挤压杆进行固溶时效热处理,固溶温度520
±
5℃,时间为3h,时效温度240
±
5℃,时间16h,得到al-4si-0.8mg-0.2fe-0.1cu合金杆。
53.对比例3本对比例与实施例2相比,常规硼化处理工艺,制备铝合金杆(al-3.9si-0.8mg-0.2fe合金),其元素组分与质量百分比如下:si 3.9%,mg 0.8%,fe 0.2%,b 0.09%,其余为al。
54.制备方法包括以下步骤:(1)备料:按照原料配比准备纯铝、纯硅、纯镁、al-10%fe中间合金、al-3%b中间合金;(2)熔融:将纯铝熔化并升温至750℃,然后依次向熔体中加入纯硅、纯镁、al-10%fe中间合金,搅拌均匀后保温10min,得到熔体;
(3)硼化:将熔体温度保持在750℃,加入al-3%b中间合金,搅拌均匀,用漏勺除去杂质熔渣,保温20min,得到硼化处理后的熔体;硼化处理时,利用b与熔体中v、ti、cr、zr 等杂质元素的反应,降低杂质元素含量,有利于提高合金的导电率;(4)浇铸:将硼化处理后的熔体进行浇铸,得到直径80mm、高度0.5m的铸棒;(5)热处理和热挤压:将铸棒放入热处理炉中,在520
±
5℃温度下进行均匀化热处理3h,然后在500
±
5℃挤压温度条件下以1mm/s的挤压速度挤成实心棒材,空冷后,得到铝合金挤压杆;(6)固溶时效:将铝合金挤压杆进行固溶时效热处理,固溶温度520
±
5℃,时间为2h,时效温度240
±
5℃,时间16h,得到al-3.9si-0.8mg-0.2fe合金杆。
55.对比例4本对比例利用钒辅助硼化处理制备铝合金杆(al-4si-0.6mg-0.3fe-0.2cu合金),与实施例4相比,不同点仅在于其元素组分与质量百分比如下:si 4.0%,mg 0.6%,fe 0.3%,cu 0.2%,b 0.06%,v 0.12%,其余为al。制备方法与实施例4相同。
56.对比例5本对比例利用钒辅助硼化处理制备铝合金杆(al-3.9si-0.8mg-0.2fe合金),与实施例2相比,不同点仅在于其元素组分与质量百分比如下:si 3.9%,mg 0.8%,fe 0.2%,b 0.03%,v 0.09%,其余为al。制备方法与实施例2相同。
57.对实施例和对比例制备的纯铝金属杆或铝合金杆进行性能测试,其中:(1)室温极限拉伸强度、延伸率参照gb/t228.1-2010《金属材料拉伸试验方法》,利用万能试验机进行测试;(2)导电率利用四电极法进行测试,一般定义标准退火纯铜的导电率为100%iacs;(3)杂质元素含量采用光谱分析仪进行定量分析,检测的杂质元素为v、ti、cr、zr、ca;(4)硼化处理效率计算公式如下:;式中,η
bt
表示硼化处理效率;c
i0
表示硼化处理前熔体中元素i的含量;∑c
i0
表示硼化处理前熔体中的主要杂质元素含量之和;c
ib
表示硼化处理后熔体中元素i的含量;∑c
ib
表示硼化处理后熔体中的主要杂质元素含量之和。
58.(5)热导率采用lfa427/457激光导热分析仪测试,将样品放在导热分析仪中以10℃/min升温至400℃,计算机自动计算出材料所在不同温度时的扩散系数以及热导系数。
59.(6)平均线性热膨胀系数的测试温度范围为20-100℃,采用netzsch dil 402c线性热膨胀测试仪测试。
60.(7)布氏硬度:使用hb-3000c布氏硬度计测量硬度,压力载荷为250kg,压头直径为5mm,保压时间为15s,每个硬度值均为4次测量的平均值。
61.检测结果如表1所示。
62.表1 实施例和对比例制备的产品性能测试结果从表1可以看出,未硼化处理时,熔体中的主要杂质元素(v、ti、cr、zr、ca)含量总和范围为247-476ppm,常规硼化处理后含量总和降至53-65ppm,添加钒辅助硼化处理后主要杂质元素含量总和降至12-19ppm;常规硼化处理效率为76.37-78.35%,加v辅助的硼化处理效率为90.31-94.3%,拉伸强度≥250mpa,延伸率≥20.1%,导电率≥58.7%iacs,热导率和未硼化处理、常规硼化处理相近,平均线性膨胀系数低,力学性能好,属于高强高导铝合金的一种。