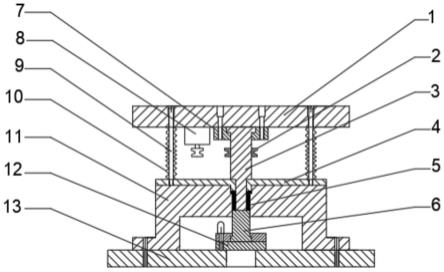
1.本发明涉及一种轴套零件触变旋转挤压方法及装置,属于半固态成形领域。
背景技术:2.金属轴套零件具有支撑回转轴、导向和定位等作用,常被用于机械、化工、航天、汽车等诸多领域。金属半固态成形技术自20世纪70年代提出以来,得到快速发展。与传统铸造或锻造相比,具有成形温度低、气孔少、组织致密、材料利用率高等特点。因此采用半固态成形方法制备轴套零件有望解决现有轴套生产中材料利用率低、力学性能低、生产周期长、缺陷多等问题。在采用半固态触变成形制备轴套零件过程中往往需要将制备好的坯料重新加热至半固态区间再向模具中转移后挤压成形。在成形过程中零件上端和底端往往存在成分分布不均的显现,影响产品质量。半固态坯料容易出现固液分离的现象,这使得挤压后组织中固液两相会有不同程度的偏聚现象,最终影响产品的性能,对产品质量有较大影响,尤其在制备较高液相率的半固态合金零件时更明显。尤其是航天、汽车等领域中,轴套作为关键性零件,所以对其力学性能的要求较高,如何提高轴套零件性能的方法具有重要研究意义。
技术实现要素:3.本发明的目的是针对现有半固态轴套制备方法中坯料转移过程中半固态浆料固液分离,导致挤压后产品的组织不均匀问题,以及零件组织粗大,产品性能不高问题,提供一种轴套零件触变旋转挤压方法,该方法利用半固态成形技术,使用旋转凸头在挤压过程中与浆料充分搅拌,使得产品内壁和外壁产生较大剪切力,细化组织;同时凸模下压,轴向力和剪切力共同作用,晶粒细化效果显著。使用该方法成形制备出材料利用率高、生产效率高、力学性能优异的轴套零件,具体包括以下步骤:
4.(1)将加热到半固态温度的金属浆料转移到预热后的模具中;
5.(2)凸模旋转并快速下压,凸模旋转过程为变速过程,当凸模即将接触浆料时开始低速旋转,凸模继续下压并加速旋转,当浆料完全充型时凸模旋转速度达到最大,保持最大旋转速度2-4s后停止旋转并保压;旋转速度为:
6.v=0.3fs(x3+1)
7.式中:v为旋转速度rps/min,fs:固相率,x:下压进程(mm),其中fs由不同材料和性能要求确定。
8.(4)对挤压后轴套零件进行快速水淬。
9.(5)对水淬后轴套零件进行t6热处理。
10.优选的,本发明步骤(1)中模具预热温度为400-500℃。
11.优选的,本发明所述凸模的挤压速度为10-15mm/s。
12.优选的,本发明所述fs推导如下:
13.[0014][0015]
由(ⅰ)和(ⅱ)联立得:
[0016][0017]
式中:cs为固相溶质浓度,c
l
为液相溶质浓度,ts为固相线温度,t
l
为液相线温度,k0为平衡分配系数。
[0018]
本发明的另一目的在于提供一种轴套零件触变旋转挤压装置,包括上模固定板1、凸模3、凹模11、下模固定板13;上模固定板1下面固定有凸模3,下模固定板13上固定有凹模11,其特征在于:所述上模固定板1的下面固定有电机8,凸模3上固定有皮带轮2,电机8的输出轴通过皮带与皮带轮2连接;凹模11上设有法兰4,凸模3、凹模11合模后与法兰4形成的型腔与轴套零件形状相对应,法兰4在防止液体飞溅的同时,往凹模内延伸的一小段辅助轴套轴肩的形成。
[0019]
本发明所述上模固定板1两侧设有导杆9,导杆9上套有弹簧,导杆9下端固定在法兰4上,法兰4与导杆9相固定,开模时法兰也拿起来,然后顶杆顶出产品。
[0020]
本发明所述凸模3通过凸模固定件7固定在上模固定板1下面,凸模固定件7的下端设有l型凹槽,与凸模3顶部的t型凸起相配合,使凸模3可在凸模固定件7内转动。
[0021]
本发明所述凹模11下方设有顶杆6,顶杆6固定在顶杆固定板12上,顶杆固定板12与液压机连接。
[0022]
本发明所述所述凸模3、凹模11材料选用h13模具钢。
[0023]
本发明的有益效果:
[0024]
(1)本发明采用触变旋转挤压方法制备半固态轴套零件,通过凸模旋转,使得半固态浆料与凸模外壁摩擦,横向剪切力充分破碎并细化晶粒,组织致密气孔少,零件力学性能高,成形速度快大幅提高生产效率,极大地降低了零件生产成本,缩短了生产周期。
[0025]
(2)本发明采用触变旋转挤压方法制备半固态轴套零件,凸模旋转并快速向下运动,充分搅拌浆料,成形后半固态组织中固液两相均匀分布,力学性能更好。
[0026]
(3)本发明能生产具有较高力学性能的产品,通过调控凸模旋转速度,能够适用于不同金属的半固态的成形,可对产品的性能进行调控,更易实现零件定制化生产。
[0027]
(4)凸模旋转为变速过程,在接触浆料时低速旋转,防止液体飞溅到凹模壁上,避免造成宏观偏析;凸模继续下压并加速旋转,半固态浆料能够平稳充型;当浆料充型完成时达到最大旋转速度,该过程能充分抑制球形半固态晶粒的生长,使晶粒细化,提高材料力学性能。
[0028]
(5)在凹模上添加法兰防止液体飞溅,且与凸凹模共同构成轴套型腔。
[0029]
(6)本发明挤压成形后快速水淬,水淬后轴套零件进行t6热处理,进一步改善组织均匀性,提高力学性能。
[0030]
(7)本发明所述模具结构合理,可以安装在立式挤压机上,占地面积小、操作简单方便,可实现机械化和自动化生产。
附图说明
[0031]
图1是本发明所述触变旋转挤压成形的模具结构示意图。
[0032]
图2为凸模旋转方向。
[0033]
图3是本发明凸模旋转过程中速度变化示意图。
[0034]
图4不同实施例中半固态合金硬度性能对比。
[0035]
图5不同实施例中半固态合金抗拉强度对比。
[0036]
图1中:1-上模固定板;2-皮带轮;3-凸模;4-法兰;5-金属浆料;6-顶杆;7-凸模固定件;8-电机;9-导杆;10-弹簧;11-凹模;12-顶杆固定板;13-下模固定板。
具体实施方式
[0037]
下面结合附图和具体实施例对本发明作进一步详细说明,但本发明的保护范围并不限于所述内容。
[0038]
本发明实施例所用模具结构如图1所示,包括上模固定板1、皮带轮2、凸模3、法兰4、金属浆料5、顶杆6、凸模固定件7、电机8、导杆9、弹簧10、凹模11、顶杆固定板12、下模固定板13;液压机控制凸模3上下移动;合模时当凸模3和电机8同时向下运动,单片机控制电机8速度,凸模3由电机8皮带传动,速度传感器监控并反馈凸模3旋转速度,由电机8调节凸模转速,合模完成后凸模保持转速2-4s后停止旋转;开模时液压机卸载,凸模抬起,上模达到最高位置时在弹簧10的作用下回到初始位置;弹簧10套在导杆9外;凸模3与法兰4,法兰4与凹模11间隙配合;模具凸模3内壁和下模凸台设置拔模斜度1
°
;凸模3、法兰4、凹模11合模后形成的型腔与轴套零件形状相对应;上模固定板1与凸模固定件7螺栓连接,上模固定板1通过t型板固定在液压机顶端位置;下模固定板13与凹模11螺栓连接,下模固定板13通过t型板固定在液压机工作台面位置,挤压过程中保持固定;凸模3、凹模11材料选用h13模具钢。
[0039]
本发明所述模具的使用过程:轴套零件挤压成形前,液压机控制上模退至液压机最顶端;对;凸模3、凹模11的表面喷涂石墨脱模剂;将金属浆料5倒入凹模11中、弹簧10处于放松状态;启动电机8且由皮带传动带动凸模旋转,通过单片机控制电机的功率控制凸模旋转速度;驱动液压机使整个上模具垂直向下运动且凸移动速度由液压机控制,凸模3、凹模11闭合后2-4s电机8停止旋转,保压一段时间;然后控制液压机使整个上模退回至液压机最顶端,弹簧10处于放松状态,顶杆顶出轴套零件后取出,最后进行t6热处理;整个挤压成形过程,模具结构简单,易于实现机械化、连续化生产,最终获得的轴套零件综合力学性能较好。
[0040]
实施例1
[0041]
本实施例所述一种铜合金轴套零件触变旋转挤压成形方法,模具结构如图1所示,具体步骤如下:
[0042]
(1)本实施例材料为zcusn10p1铜合金,测得zcusn10p1铜合金固相线温度为876.1℃,液相线温度为1024.2℃。
[0043]
(2)将下模凸台预热至450℃,然后将半固态zcusn10p1浆料放入下模。
[0044]
(3)驱动上模以10mm/s运动速度挤压金属浆料,凸模由电机带动旋转,转速v如表1所示。挤压结束后保压15s。
[0045]
(4)将挤压后轴套零件快速水淬,然后加热至550℃并保温60min,随后空冷至室
温,获得轴套零件。
[0046]
本实施例中上模旋转速度v(rps/min)满足公式v=0.3fs(x3+1)其中fs取0.91,下压进程为0-14mm,下压速度为10mm/s,具体参数如表1所示;
[0047]
表1 zcusn10p1铜合金旋转反挤压工艺2
[0048][0049]
本实施例制备得到的铜合金轴套零件表面光洁、尺寸精确、无划痕及裂纹等缺陷,与普通反挤压方法(将下模凸台预热至450℃,然后将半固态zcusn10p1浆料放入下模,然后驱动上模以10mm/s运动速度挤压金属浆料,挤压结束后保压10s,挤压后轴套零件快速水淬,然后加热至550℃并保温60min,随后空冷至室温,获得轴套零件)制备轴套零件相比,力学性能有所提升,如图4和5所示。
[0050]
实施例2
[0051]
本实施例所述一种7075铝合金轴套零件触变旋转挤压成形方法,制备工艺流程如图1所示,具体步骤如下:
[0052]
(1)本实施例材料为7075铝合金,测得7075铝合金固液相线温度区间为540~638℃。
[0053]
(2)将下模凸台预热至400℃,然后将半固态7075铝合金浆料放入下模。
[0054]
(3)然后驱动上模以15mm/s运动速度挤压金属管,凸模由电机带动旋转,转速v如2所示;挤压结束后保压10s。
[0055]
(4)将挤压后轴套零件快速水淬,然后加热至380℃并保温30min,随后空冷至室温,获得轴套零件。
[0056]
本实施例中上模旋转速度v(rps/min)满足公式v=0.3fs(x3+1)其中fs取0.95,下压进程为0-14mm,下压速度为15mm/s,具体参数如表2所示;
[0057]
表2 7075铝合金旋转反挤压工艺2
[0058][0059]
本实施例制备得到的铝合金轴套零件表面光洁、尺寸精确、无划痕及裂纹等缺陷,与普通反挤压方法(将下模凸台预热至400℃,然后将半固态7075铝合金浆料放入下模。然后驱动上模以15mm/s运动速度挤压金属浆料,挤压结束后保压10s。将挤压后轴套零件快速水淬,然后加热至380℃并保温30min,随后空冷至室温,获得轴套零件)制备轴套零件相比,力学性能有所提升,如图4和5所示。
[0060]
实施例3
[0061]
本实施例所述一种az91d镁合金轴套零件触变旋转挤压成形方法,制备工艺流程如图1所示,具体步骤如下:
[0062]
(1)本实施例材料为az91d镁合金,测得az91d镁合金的固液相线温度区间为470~595℃。
[0063]
(2)将下模凸台预热至350℃,然后将半固态az91d镁合金浆料放入下模。
[0064]
(3)驱动上模以13mm/s运动速度挤压金属浆料,凸模由电机带动旋转,转速v如表3所示;挤压结束后保压7s。
[0065]
(4)将挤压后轴套零件快速水淬,然后加热至320℃并保温90min,随后空冷至室温,获得轴套零件。
[0066]
本实施例中上模旋转速度v(rps/min)满足公式v=0.3fs(x3+1)其中fs取0.98,下压进程为0-14mm,下压速度为13mm/s,具体参数如表3所示。
[0067]
表3 az91d镁合金旋转反挤压工艺3
[0068][0069]
本实施例制备得到的铜合金轴套零件表面光洁、尺寸精确、无划痕及裂纹等缺陷,与普通反挤压方法(将下模凸台预热至350℃,然后将半固态az91d镁合金浆料放入下模;驱
动上模以13mm/s运动速度挤压金属浆料,挤压结束后保压7s。将挤压后轴套零件快速水淬,然后加热至320℃并保温90min,随后空冷至室温,获得轴套零件)制备轴套零件相比,力学性能有所提升,如图4和5所示。