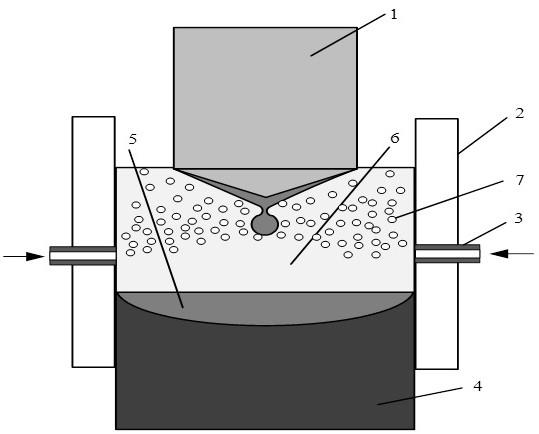
1.本发明涉及一种电渣重熔方法,尤其是一种电渣重熔超洁净钢的冶炼方法。
背景技术:2.电渣冶金是20世纪特种冶金技术的重大突破之一。自1940年,美国人霍普金斯获得了电渣专利以来,电渣冶金得到了蓬勃的发展。目前,电渣钢广泛用于航空、航天、电力等工业领域。然而,一些对有害杂质成分要求较高的高端材料,如部分高温合金、耐蚀合金和超洁净钢,目前需采用真空感应熔炼+电渣重熔+真空自耗三联工艺生产。
3.采用三联工艺生产超洁净钢不仅成本高,生产周期也长,工艺难度也大,有诸多缺点。所以,各国冶金工作者都试图改进电渣冶炼工艺,力求获得更加高效的去除夹杂物和硫的方法。
4.不难得知,电渣脱除硫及夹杂物主要集中在金属熔滴形成、下落两个阶段。熔炼过程中,自耗电极在接触熔渣的一端沿表面逐层熔化,形成薄膜和熔滴,进行渣金反应,脱除一部分杂质;在熔滴下落时,金属穿越渣层也会与熔渣反应,去除夹杂。显而易见,在这两个过程中,接触面积和作用时间是影响夹杂物去除效率的最关键因素。
5.众所周知,渣金接触面积与熔滴尺寸呈指数关系。熔滴尺寸越小,比表面积越大,接触面积也越大,反之亦然。一粒一定质量的金属熔滴,破碎成相同质量的两粒,比表面积增加了2.17倍。所以,电渣过程中控制得到较小的金属熔滴是非常有利于脱除杂质的。
6.另一方面,渣金作用时间与熔滴下落时间呈反比。金属熔滴离开电极开始下落,将受到渣子浮力、粘滞力(相当于摩擦力)和重力的共同作用。其中,渣浮力、粘滞力是阻力,越大,越有利于减缓下落速度,延长停留时间,就越有利于增加渣金反应程度。所以,从脱除夹杂物角度出发,应设法控制重熔过程中增加渣浮力和粘滞力。
7.在减小熔滴尺寸和增加渣浮力、粘滞力方面,冶金工作者做了很多研究。归纳起来,较有成效的工作主要集中在工艺参数优化、渣系成分改进两个方面,但是,这些工作有利也有弊。比如,提高电流的确会减少熔滴尺寸,提高渣洗效果,但同时也会增加熔速,造成金属凝固偏析和组织不均;另外,增加渣子密度、粘度会增加浮力和粘滞力,提高去夹杂效果,但同时也会使渣皮增厚,钢渣分离困难而致铸锭表面质量下降。
8.综上所述,目前还没有特别有效的技术手段解决电渣重熔冶炼超洁净钢的问题。
技术实现要素:9.本发明要解决的技术问题是提供一种减少金属熔滴尺寸、降低熔滴下落速度的电渣重熔超洁净钢的冶炼方法。
10.为解决上述技术问题,本发明所采取的技术方案是:采用抽锭式结晶器进行电渣熔炼;在冶炼过程中,在渣池中下部均布一圈的位置向渣池内吹入0.1~0.5l/min不参与反应的高纯气体。
11.本发明所述高纯气体水平吹入渣池内。
12.本发明所述高纯气体在渣池中下部的两侧对称吹入。
13.本发明所述高纯气体为高纯氦气。
14.本发明所述高纯气体的温度200~300℃、压力0.06~0.08mpa。
15.本发明的工艺思路是:首先,渣池会在高纯气体泡的搅动下加速对流循环,这会有效增加渣子对电极端面的冲刷作用,迫使金属熔滴不能自然长大,只会在较小尺寸下脱离电极。同时,熔滴在下落过程中,会被渣流和高纯气体泡不断冲击破碎,进一步减少了熔滴尺寸、增加熔滴的比表面积,这会显著增加渣金接触界面,加快反应进程。
16.其次,破碎的熔滴由于质量减少,可随渣池做对流运动,大大延长滴落路径,增加停留时间,使渣金反应充分进行。
17.经前述分析得知,熔滴尺寸和作用时间,正是电渣冶金脱除夹杂物和硫等杂质的两个最关键参数,所以,本发明能有效地提高去夹杂效率。
18.另外,选择氦气作为吹入介质,也与它的物理化学性质有关。氦气是一种惰性气体,不与金属反应,作为吹入介质不会引起成分变化;同时,它的密度比氩气还小,吹入渣层会急剧膨胀而快速上浮,不会残留在钢中;再者,氦气充入前经过脱水、升温、稳压处理,不会增h,也不会降低渣温而增加操作难度,工艺适应性好。它的使用量也较小,仅0.1~0.5l/min,经济实用。
19.采用上述技术方案所产生的有益效果在于:本发明突破传统的方式方法,借助“外力”干涉电渣冶炼过程,能大幅减少金属熔滴尺寸、显著降低熔滴下落速度,从而增加渣金反应时间、提高去夹杂效率。本发明电渣后无需再次熔炼,所冶炼的超洁净钢中的夹杂物、硫含量比传统的电渣重熔低50%以上。
附图说明
20.下面结合附图和具体实施方式对本发明作进一步详细的说明。
21.图1是本发明所述电渣重熔装置的结构示意图。
22.图中:1―自耗电极;2―结晶器;3―吹气孔;4―钢锭;5―金属熔池;6―渣池;7―高纯气体泡。
具体实施方式
23.本电渣重熔超洁净钢的冶炼方法适用于电渣钢,例如gcr15、gh4169、w18cr4v、ns333等超洁净钢,采用抽锭式结晶器,尤其适用于φ300mm及以上抽锭式结晶器;所述抽锭式结晶器在渣池中下部设置有吹气孔,吹气孔至少为两个、在渣池周边的同一平面上均匀布置;吹气孔最好为两个,对称设置在渣池的两侧;所述对抽锭式结晶器需要进行改进,可采用下述抽锭式结晶器结构:图1所示,在结晶器2中间部位中心对称穿2个细孔,平行焊接铜制导管,接口处打磨光滑,导管内径0.12~0.16mm,所述导管即为吹气孔3;所述吹气孔3水平设置;结晶器其余部分与常规的抽锭式结晶器结构相同。
24.采用下述工艺:(1)选用抽锭式结晶器,底水箱上放置引弧剂,引弧剂周围放置渣料;安装结晶器2、自耗电极1、保护罩,通入氩气;(2)接通熔炼电源,引燃起弧,加入渣料,待渣温升至1700~1800℃时进入正常熔炼阶段;所述渣料加入前进行烘烤,最好在600~650℃加热炉烘烤8~12h;所述渣料熔化形
成渣池6,自耗电极1熔化形成的金属液滴沉入渣池6底部,逐渐累积形成金属熔池5;金属熔池4冷却凝固,形成钢锭4;(3)所述正常熔炼阶段,待渣层漫过吹气孔3时开始吹气,吹气孔位置位于渣层中下部时开始抽锭,直至熔炼结束。所述吹气孔3向渣池中下部水平吹入总流量0.1~0.5l/min不参与反应的高纯气体,所述高纯气体最好为高纯氦气。所述高纯氦气通入结晶器前经脱水、加热、稳压处理,进入结晶器时气体含水量≤0.0001vol%、温度200~300℃、压力0.06~0.08mpa。所述吹气孔3吹气过程中在渣池6内形成高纯气体泡7,熔滴在下落过程中被渣流和高纯气体泡7不断冲击破碎,从而减少熔滴尺寸、增加熔滴的比表面积、延长滴落路径,进而加快反应进程、使渣金反应充分进行。
25.(4)熔炼结束,停止吹入氦气,30~120min后脱模。
26.实施例1:本电渣重熔超洁净钢的冶炼方法采用下述具体工艺。
27.电渣冶炼gcr15。具体包括:抽锭式结晶器规格:φ300
×
700mm;自耗电极规格:φ200
×
2600mm;钢种成分:c 1.02%、si 0.24%、mn 0.26%、p 0.010%、s 0.008%、cr 1.49%,余量为fe会不可避免的杂质;渣成分(wt):70%caf2、30%al2o3;渣量:28kg。在结晶器中间部位对称设置2个吹气孔,内径0.12mm;冶炼工艺如下:(1)自耗电极打磨光亮、焊接;(2)将渣料放置在600℃加热炉烘烤8h;(3)铺设固渣引弧剂、安装电极,向结晶器内通入ar;(4)给电引弧、加渣,化渣30min后升温至1750℃;(5)进入熔炼阶段,待渣层漫过吹气孔时开始吹入230℃、0.06mpa、0.3l/min、含水量0.00006vol%的高纯氦气;(6)熔炼至吹气孔位置位于渣层中下部时开始抽锭,直至熔炼结束;(7)停止吹入氦气,45min后脱模。
28.(8)使用该结晶器,采用上述工艺冶炼同成分同规格电极,但冶炼过程不吹氦气,做对比实验,生产得到对比电渣。本实施例所得电渣(下述本方法电渣)和对比电渣进行检测,检测渣层熔滴尺寸及质量见表1,铸锭硫磷及非金属夹杂物含量见表2。
29.表1:电渣重熔金属熔滴尺寸及数量
由表1得出,本方法电渣的金属熔滴平均粒径2.86mm,而对比电渣为7.44mm,降低了61.5%,同质量下比表面积增加了130%;本方法电渣渣中熔滴残余量130.7g,对比电渣80.9g,说明本方法电渣的停留时间比对比电渣增加61.6%。
30.表2:电渣熔炼后非金属夹杂物及硫磷含量(wt)从表2可以看出,本方法电渣的夹杂物总量、评级、s含量均低于对比电渣;其中,夹杂物总量低于对比电渣61.9%,硫含量低于对比电渣70.0%。
31.实施例2:本电渣重熔超洁净钢的冶炼方法采用下述具体工艺。
32.电渣冶炼gh4169。具体包括:抽锭式结晶器规格:φ220
×
600mm;自耗电极规格:φ160
×
1800mm;钢种成分:c 0.05%,p 0.008%,s 0.005%,cr 19%,mo 3%,ni 52%,fe 19%,nb 5.2%,al 0.5%,ti 1.0%,以及不可避免的杂质;渣成分(wt):50%caf2、25%cao、20%al2o3、5%tio2;渣量:10kg。在结晶器中间部位对称设置2个吹气孔,内径0.16mm;冶炼工艺如下:(1)自耗电极打磨光亮、焊接;(2)将渣料放置在600℃加热炉烘烤8h;(3)铺设固渣引弧剂、安装电极,向结晶器内通入ar;(4)给电引弧,加渣,化渣15min后升温至1700℃;
(5)进入熔炼阶段,待渣层漫过吹气孔时开始吹入300℃、0.06mpa、0.1l/min、含水量0.00009vol%的高纯氦气;(6)熔炼至吹气孔位置位于渣层中下部时开始抽锭,直至熔炼结束;(7)停止吹入氦气,30min后脱模。
33.(8)使用该结晶器,采用上述工艺冶炼同成分同规格电极,冶炼过程不吹氦气,做对比实验,生产得到对比电渣。本实施例所得电渣(下述本方法电渣)和对比电渣进行检测,检测渣层熔滴尺寸质量见表3,铸锭硫磷及非金属夹杂物含量见表4。
34.表3:电渣重熔金属熔滴尺寸及数量由表3得出,本方法电渣的金属熔滴平均粒径1.49mm,而对比电渣为3.02mm,降低了50.7%,同质量下比表面积增加103%;本方法电渣渣中熔滴残余量81.4g,对比电渣50.5g,说明停留时间比对比电渣增加61.4%。
35.表4:电渣熔炼后非金属夹杂物及硫磷含量(wt)从表4可以看出,本方法电渣夹杂物总量、评级、s含量均低于对比电渣。其中,夹杂物总量低于对比电渣53.7%,硫含量低于对比电渣62.5%。
36.实施例3:本电渣重熔超洁净钢的冶炼方法采用下述具体工艺。
37.电渣冶炼w18cr4v。具体包括:抽锭式结晶器规格:φ550
×
1000mm;自耗电极规格:φ400
×
3900mm;钢种成分:c 0.75%,si 0.30%,mn 0.28%,p 0.010%,s 0.009%,cr 4%,w 18%,mo 0.3%,v 1.2%,以及不可避免的杂质。渣成分(wt):40%caf2、30%cao、30%al2o3;渣量:
95kg。在结晶器中间部位的平面均布3个吹气孔,内径0.14mm;冶炼工艺如下:(1)自耗电极打磨光亮、焊接;(2)将渣料放置在620℃加热炉烘烤12h;(3)铺设固渣引弧剂、安装电极,向结晶器内通入ar;(4)给电启动,加渣,化渣60min后升温至1800℃;(5)进入熔炼阶段,待渣层漫过吹气孔时开始吹入200℃、0.08mpa、0.5l/min、含水量0.0001vol%的高纯氦气;(6)熔炼至吹气孔位置位于渣层中下部时开始抽锭,直至熔炼结束;(7)停止吹入氦气,120min后脱模。
38.(8)使用该结晶器,采用上述工艺冶炼同成分同规格电极,过程不吹氦气,做对比实验,生产得到对比电渣。本实施例所得电渣(下述本方法电渣)和对比电渣进行检测,检测渣层熔滴尺寸及质量见表5,铸锭硫磷及非金属夹杂物含量见表6。
39.表5:电渣重熔金属熔滴尺寸及数量由表5得出,本发明电渣金属熔滴平均粒径4.55mm,而对比电渣为9.67mm,降低了52.9%,同质量下比表面积增加112%;本方法电渣渣中熔滴残余量165.9g,对比电渣97.8g,说明停留时间比对比电渣增加69.6%。
40.表6:电渣熔炼后非金属夹杂物及硫磷含量(wt)从表6可以看出,本发明电渣夹杂物总量、评级、s含量均低于对比电渣。其中,夹杂
物总量低于对比电渣62.4%,硫含量低于对比电渣73.6%。
41.实施例4:本电渣重熔超洁净钢的冶炼方法采用下述具体工艺。
42.电渣冶炼ns333。具体工艺:抽锭式结晶器规格:φ400
×
850mm;自耗电极规格:φ300
×
2800mm;合金成分:c 0.04%,si 0.4%,mn 0.4%,p 0.008%,s 0.005%,cr 15%,mo 16%,co 2.5%,w 4%,fe 5%,v 0.2%,余量ni和不可避免的杂质;渣成分(wt):60%caf2、25%cao、10%al2o3、5%mgo;渣量:50kg。在结晶器中间部位的平面均布4个吹气孔,内径0.15mm;冶炼工艺如下:(1)自耗电极打磨光亮、焊接;(2)将渣料放置在650℃加热炉烘烤10h;(3)铺设固渣引弧剂、安装电极,向结晶器内通入氦气;(4)给电启动,加渣,化渣45min后升温至1750℃;(5)进入熔炼阶段,待渣层漫过吹气孔时开始吹入250℃、0.07mpa、0.35l/min、含水量0.00007vol%的高纯氦气;(6)熔炼至吹气孔位置位于渣层中下部时开始抽锭,直至熔炼结束;(7)停止吹入氦气,80min后脱模。
43.(8)使用该结晶器,采用上述工艺冶炼同成分同规格电极,过程不吹氦气,做对比实验,生产得到对比电渣。本实施例所得电渣(下述本方法电渣)和对比电渣进行检测,检测渣层熔滴尺寸及质量见表7,铸锭硫磷及非金属夹杂物含量见表8。
44.表7:电渣重熔金属熔滴尺寸及数量由表7得出,本方法电渣金属熔滴平均粒径3.74mm,而对比电渣为8.16mm,降低了
54.2%,同质量下比表面积增加118%;本方法电渣渣中熔滴残余量143.8g,对比电渣88.5g,说明停留时间比对比电渣增加62.5%。
45.表8:电渣熔炼后非金属夹杂物及硫磷含量(wt)从表8可以看出,本方法电渣夹杂物总量、评级、s含量均低于对比电渣。其中,夹杂物总量低于对比电渣63.0%,硫含量低于对比电渣66.7%。
46.从以上4个实施例可以得出,断面越大,本方法的优势越大,φ300mm及以上结晶器,硫、夹杂物含量均比传统电渣降低60%以上,所以,本方法有很广阔的应用价值。