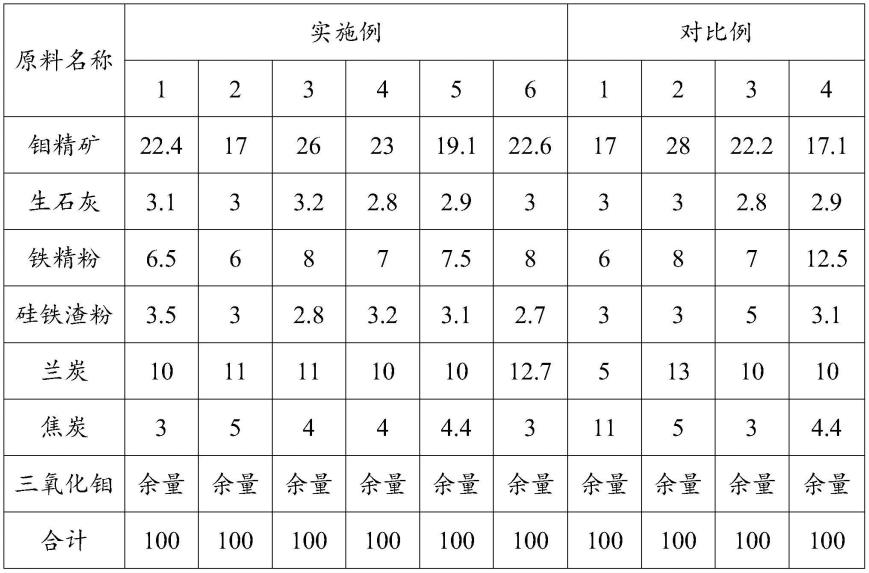
1.本发明属于钼铁合金技术领域,具体涉及一种多孔钼球团及其制备方法。
背景技术:2.钼是合金钢中常见的合金元素之一,与其他合金元素共同作用能提高钢铁材料的强度、硬度和耐腐蚀性。炼钢过程中通常采用工业三氧化钼冶炼成钼铁合金,然后再将钼铁合金作为冶炼钼合金钢的添加剂。但钼铁合金价格昂贵,且钼铁密度大于铁水的密度,加入钢液时易沉降在炉底,增加了钢水的合金化过程,甚至少量钼铁沉积在炉底,造成钼元素的收得率降低,增加了冶炼过程的能耗和原料成本。
3.研究者开发了采用初级原料三氧化钼作为钼合金钢的添加剂,具有熔化速度快、成本低的优势,在国内外都得到了快速的发展。例如:中国文献cn103469049a公开了一种采用三氧化钼直接合金化炼钢工艺。但是,采用三氧化钼直接合金化炼钢,三氧化钼在高温下易挥发,致使钼的收得率波动大,必须依赖操作人员的操作经验;且将三氧化钼还原为金属钼需要消耗较多的还原剂,产生较多的产物,渣量显著增大;而且存在冶炼电耗增加以及炼钢过程中的沸腾等问题,这些问题都难以有效解决。中国专利文献cn105970073a一种采用二氧化钼为钼元素的添加剂用于冶炼含钼钢的方法,以钼精矿焙烧得到的工业级三氧化钼为原料,通过配碳还原,制备工业级二氧化钼,作为钼源直接合金化冶炼。该方法克服了三氧化钼容易挥发的缺点,具有钼收得率高等优点。但是,该方法仍然存在产品有害元素高、增加炼钢能耗、还原期加入收得率低、炼钢环节反应过程较慢的问题。
技术实现要素:4.为了克服现有技术存在的渣量生成多、钼含量低、冶炼电耗增加以及炼钢过程易沸腾等问题,本发明的目的是提供一种多孔钼球团及其制备方法,有效降低炼钢过程中钼元素的引入成本,且不增加现场工艺操作难度。
5.本发明的目的是通过以下技术方案来实现的:
6.本发明的一种多孔钼球团,其特征在于,采用以下质量分数的原料制成:钼精矿为17%~26%,生石灰为2.8%~3.2%,铁精粉为6%~8%,硅铁渣粉为2.7%~3.5%,兰炭为10%~13%,焦炭为3%~5%,余量为三氧化钼原料矿;
7.优选地,本发明所述的多孔钼球团,采用以下质量分数的原料制成:钼精矿为22.4%,生石灰为3.1%,铁精粉为6.5%,硅铁渣粉为3.5%,兰炭为10%,焦炭为3%,余量为三氧化钼原料矿;
8.所述钼精矿的牌号为kmo-51,粒度≥80目,80~120目的粉粒占比≤5wt%;所述生石灰的cao≥90wt%,粒度≥325目;所述铁精粉中含有fe元素含量≥90wt%、s元素含量≤0.18wt%,粒度≥80目;粒度≥200目的粉粒占比》80wt%,粒度≥325目的粉粒占比》40wt%;
9.所述硅铁渣粉为75#硅铁冶炼渣,经智能光电色选设备筛选,si元素含量≥
65wt%,粒度≥120目,c≤0.75wt%;
10.所述兰炭为ⅱ级,其中:s元素含量≤0.40wt%,灰分加权平均值≤7wt%,粒度≥200目,机械强度加权平均值≥60%;所述焦炭为冶金焦炭,粒度≥200目;所述三氧化钼原料矿中mo元素含量≥58wt%,s元素含量≤0.085wt%,粒度≥80目。
11.本发明的一种多孔钼球团的制备方法,其特征在于,包括以下步骤:
12.(1)将所述钼精矿、生石灰、铁精粉、硅铁渣粉、兰炭、焦炭和三氧化钼原料矿依次装入混合机中进行混合,搅拌时间5min以上至均匀,得到混合干料;
13.(2)边搅拌边向所述混合干料中加入适量结合剂,加完后继续搅拌10min以上至均匀;出料并直接挤压形成压球料团,然后进行干燥;
14.(3)将干燥球团置入回转窑中,在温度400~700℃、常压下进行金属还原2~3h,反应结束后自然冷却;
15.(4)将冷却球团进行破碎,筛分获得所需的粒径,即得到所述的多孔钼球团。
16.优选地,所述结合剂为羧甲基纤维素cmc、聚乙二醇、淀粉和水的混合物,由河南建杰实业有限公司生产;所述结合剂的加入量为所述混合干料总质量的8%~11%,更优选为所述混合干料总质量的10%。
17.所述混合机采用u型双螺带卧式混合机,具有可靠性好,噪音低,搅拌均匀,节省结合剂,混合料紧实,产线易布置等优点;所述回转窑是卧式回转窑,具有投资少、产量大、球团中非金属粉料易脱落等优点。
18.本发明的多孔钼球团中,mo元素含量≥68wt%,s元素含量≤0.10wt%,fe元素含量≥9wt%,作为钼源直接用于合金化冶炼,可在炼钢的熔化期或还原期加入。
19.与现有技术相比,本发明的积极效果是:
20.本发明通过预还原工艺,以硅铁渣粉、兰炭和焦炭作为还原剂,将三氧化钼原料矿中高温下易挥发的moo3还原为不易挥发的mo和moo2,因此多孔钼球团中钼元素以mo和moo2为主要成分。与钼铁合金相比,用于冶炼钼合金钢时,本发明的多孔钼球团价格低廉,可大幅降低生产成本;多孔钼球团的多孔结构,不仅降低了颗粒密度,而且可以减缓还原期加入时在钢水中的下降速度,不会沉积在炉底,显著增大mo溶入钢水的速度,增加了炼钢过程中钼元素的收得率,加快钢水的冶炼过程。
具体实施方式
21.下面通过具体的实施方式对本发明做进一步的说明,所述实施例仅用于说明本发明而不是对本发明的限制。
22.本实施例选用的压球机压力形式为液压式,转速为13r/min,轧辊直径为650mm,轧辊材质为65mn,结构形式为双辊单压;压球料团的压球成球率≥90%,生球落下强度≥6.5次/球,筛分指数≤5%,干燥后球团强度≥20mpa,放置1周后球团强度≥25mpa。
23.下列实施例中,钼精矿的牌号为kmo-51,粒度≥80目,80~120目的粉粒占比≤5wt%;生石灰的cao≥90wt%,粒度≥325目;铁精粉中含有fe元素含量≥90wt%、s元素含量≤0.18wt%,粒度≥80目;粒度≥200目的粉粒占比》80wt%,粒度≥325目的粉粒占比》40wt%;硅铁渣粉为75#硅铁冶炼渣,经智能光电色选设备筛选,si元素含量≥65wt%,粒度≥120目,c≤0.75wt%;兰炭为ⅱ级兰炭,s元素含量≤0.40wt%,灰分加权平均值≤7wt%,
粒度≥200目,机械强度加权平均值≥60%;焦炭为冶金焦炭,二级,粒度≥200目;所述氧化钼中mo元素含量≥58wt%,s元素含量≤0.085wt%,粒度≥80目。
24.兰炭机械强度加权平均值的测试方法,步骤为:(1)称取兰炭样品,筛分,得6~13mm兰炭样品;(2)分别称取150g(精确到0.1g)兰炭样品置于全方位行星式球磨机的1#、2#、3#、4#球磨罐中,分别记作m1、m2、m3、m4,每个球磨罐放入6个直径为15mm、10个直径为6mm的氧化锆磨球;(3)球磨机的自转速度为270r/min,公转速度为135r/min,球磨时间为6min;(4)将球磨后兰炭样品筛分,称量球磨后6~13mm的样品重量,记作m61、m62、m63、m64;(5)兰炭机械强度q的计算公式为:q=(m61/m1+m62/m2+m63/m3+m64/m4)/4。本实施例1-6和对比例1-4中所用兰炭的机械强度加权平均值为64.8%。
25.实施例1
26.实施例1~6和对比例1~4的多孔钼球团,采用以下质量分数的原料制成:钼精矿为17%~26%,生石灰为2.8%~3.2%,铁精粉为6%~8%,硅铁渣粉为2.7%~3.5%,兰炭为10%~13%,焦炭为3%~5%,余量为三氧化钼原料矿;具体配方列于表1中。
27.表1实施例1~6和对比例1~4的原料组成,wt%
[0028][0029]
实施例1~6和对比例1~4的多孔钼球团的制备方法,包括以下步骤:
[0030]
(1)将表1中所列的钼精矿、生石灰、铁精粉、硅铁渣粉、兰炭、焦炭和三氧化钼原料矿依次装入u型双螺带卧式混合机进行混合,搅拌时间10min至均匀,得到混合干料;
[0031]
(2)边搅拌边向所述混合干料中加入结合剂,结合剂的加入量为混合干料总质量的10wt%,结合剂的持续加入时间为5min,加完后继续搅拌20min至均匀;出料并直接挤压形成压球料团,压球料团的尺寸为50
×
35mm;将压球料团放在网带式干燥机中或自然放置干燥,形成干燥球团;结合剂为河南建杰实业有限公司生产的环保型粘合剂;
[0032]
(3)将干燥球团送入卧式回转窑中,在500℃、常压下进行金属还原反应2.5h,然后自然冷却至室温;检测金属化后的球团性能指标,达到了mo元素含量≥68wt%、s元素含量
≤0.10wt%和fe元素含量≥9wt%要求;
[0033]
(4)将冷却球团进行破碎,筛分获得所需的粒径,即得到多孔钼球团。
[0034]
将实施例1~6和对比例1~4的多孔钼球团进行检测,mo元素含量按照《yb/t 5039-2012氧化钼钼含量的测定钼酸铅重量法》进行测试;s元素含量按照《yb/t 5040-2012氧化钼硫含量的测定硫酸钡重量法》进行测试;fe元素含量按照《gb/t 6730.6-2016铁矿石金属铁含量的测定三氯化铁-乙酸钠滴定法》进行测试;压球料团理化指标按照《gb/t 32787-2016锰系铁合金粉尘冷压复合球团》技术规范中的测试方法进行;测试结果列于表2中。
[0035]
表2实施例1~6和对比例1~4的测试结果
[0036][0037]
对比例1中兰炭为5wt%含量偏低,焦炭为11wt%含量偏高,导致产品中s元素含量过高,增加了炼钢的脱硫成本和工艺操作难度。
[0038]
对比例2中钼精矿为28wt%含量偏高,相应引入的杂质较多,降低了球团在回转窑内的金属化率,导致mo元素含量过低,导致在炼钢过程中非金属氧化物的增多,增加炼钢成本和工艺操作难度,不利于钢水表面渣液粘度的调整。
[0039]
对比例3中硅铁渣粉为5w%含量偏高,一方面增加原料成本,另一方面增加了球团中si元素含量,导致在炼钢过程中渣的粘度过大,造成冶炼过程操作困难且增加能耗。
[0040]
对比例4中铁精粉为12.5w%含量偏高,导致mo的还原能力不足,且铁精粉颗粒间的结合强度弱,使得压球成球率低、生球落下强度,干燥后球团强度、放置1周后球团强度都偏低,增加了压球返料成本,同时产品中mo元素含量不合格。