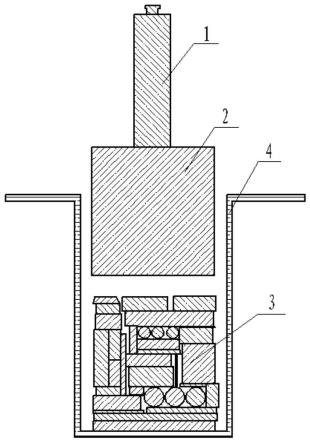
1.本发明涉及钛材加工技术领域,具体涉及一种低成本短流程钛合金残料回 收方法。
背景技术:2.钛合金是一种重要的结构金属,具有质量轻、强度高、耐腐蚀、耐热性高等 特点,主要用于航空航天、舰船兵器、生物医疗、石油化工等领域。由于钛合金 原材料昂贵、生产流程长、生产成本高等因素影响,导致其在普通商用及民用领 域应用甚少。因此低成本法残料回收制备钛合金成为钛合金行业近年来重点关注 的技术性问题,也是钛合金应用市场进一步开拓的重要途径。
3.现有技术下,残料的回收可归纳为三种方式:
4.其一是通过将钛合金残料块、料头、冒口、残屑、板条等,通过破碎或 整形方式制作为较小单元,再与高比例的海绵钛及中间合金进行混合配比 后,经过电极块压制、组拼焊接、多次var(真空自耗熔炼炉)熔炼后获得 钛合金铸锭。比如中国专利申请cn201610500892公开的“一种钛合金残料转 制异种牌号钛合金的熔炼回收方法”、中国专利申请cn201811533625公开的
ꢀ“
一种利用铝液回收钛合金废料中钛元素的方法”。这种方式单根铸锭所添加 的残料比例往往不足30%,回收率较低,同时原料配比和成分控制复杂,生 产流程长,带入异物风险高,杂质元素难于控制等问题。
5.其二是将各类残料进行分类,经机加、喷丸酸洗、锯切、锻造等多道复杂工 序处理后,再利用eb炉(电子束冷床熔炼炉)进行初熔,然后再利用var炉 进行若干次熔炼后获得钛合金铸锭。比如中国专利申请cn202010773105“一种使 用双联工艺将ta10残料制备成铸锭的方法”、中国专利申请cn201710029041 公开的“一种tc4钛合金残料的回收方法”。这种方式不仅生产流程长,同时eb 炉对物料形态要求高,针对形貌复杂物料无法实现大批量生产。另外eb炉生产 过程中对于al元素烧损大,铸锭成分稳定性差;针对难熔合金更是需要极大功 率的eb炉设备,国内钛及钛合金企业此类大功率eb炉比较罕见。
6.其三是对残废料进行机加整形、喷丸、酸碱洗,将残废料制备为较为规 则的板条状等后,通过在圆形或方形料架上进行布料,并采用等离子焊枪进 行逐个拼接点焊,将若干物料组焊为自耗电极后,再经若干次var炉熔炼 后得到钛合金铸锭。比如中国专利申请cn20161050162“一种板条状钛残料 的熔炼回收方法”。这种方法残废料处理繁琐,布料费时费力,对物料形状 限制较大;焊点极多,开裂风险高,同时最大的缺点是等离子焊枪为钨极, 极易造成高密度夹杂。
7.上述现有技术均存在回收流程长、回收费用高、质量风险高、成分及杂质元 素难控制问题。
技术实现要素:8.本发明的所要解决的技术问题是提供一种钛及钛合金残料回收方法,该回收 方
法相对简单、流程相对短、成本低,回收工序少等优点。
9.为解决上述技术问题,本发明是通过以下技术方案来解决:
10.一种低成本短流程钛及钛合金残料回收方法,具体包括以下步骤:
11.s1:收集同牌号、同成分标准下钛及钛合金残料备用;
12.s2:以堆垛、间隙填充方式将收集的残料装入坩埚内,并使残料与坩埚壁之 间留有安全间隙;
13.s3:选择同牌号钛或钛合金作为辅助电极和自耗电极,将装入残料的坩埚放 入var炉熔化站中进行var熔炼,使熔液填充坩埚内残料各个间隙,待充分填 充并包裹坩埚内残料后,断开var炉电源;得到包裹有残料的钛及钛合金铸锭;
14.s4:将s3得到的钛及钛合金铸锭再经过两次或两次以上var熔炼后,得到 钛及钛合金成品铸锭;
15.进一步地,所述s1中,对收集的钛或钛合金残料进行成分确认;成分确认 后,对表面氧化、污渍的残料进行喷丸、酸洗、烘干处理。
16.进一步地,所述s1中,喷丸磨料为直径2~3mm的铸铁丸,酸洗采用硝酸和 氢氟酸的混合熔液,浸泡时长1小时以上;烘干温度应保持在70~90℃。
17.进一步地,所述s2中,根据残料形貌、大小特点直接以堆垛、间隙填充方 式将残料装入坩埚内,残料间错位码放。所述s2中,残料错位码放时错位尺寸 应保持在10~15mm;残料与坩埚之间留有的安全间隙应保持在50~60mm之间。
18.进一步地,所述s3中,同牌号自耗电极体积应大于坩埚内待回收残料需填 充间隙的体积,且自耗电极熔化后能彻底包裹坩埚内待回收残料。
19.进一步地,所述s3中,当var炉室真空≤1pa时侧漏,漏气率≤0.8pa/min 时,开启var熔炼电源起弧熔炼,起弧期熔炼电流保持在6~12ka,充分加热 坩埚内残料,待坩埚内残料开始熔化时,将熔炼电流逐渐提升至16~30ka,自 耗电极开始逐渐熔化进入坩埚,当熔液充分填充并包裹残料后,停止var熔炼。
20.进一步地,所述s3中,起弧期电流保持在6~12ka,保持时长≥30min,电 压26~34v,稳弧电流12~15a,稳弧周期15s;所述s3中熔后冷却时长≥6h。
21.进一步地,所述s4中,熔炼真空均≤1pa,漏气率≤0.6pa/min。
22.本发明与现有技术相比,具有以下有益效果:
23.本发明是提供一种低成本短流程钛合金残料回收方法,解决钛及钛合金残料 回收工序流程长、残料利用率低问题,同时降低异物及高密度夹杂带入风险,有 效控制杂质元素增加。所获得的钛及钛合金铸锭质量更可靠,成分分布更均匀, 成分满足并优于gb/t 3620.1《钛及钛合金牌号和化学成分》国标。
24.本发明是提供一种低成本短流程钛合金残料回收方法,不需要进行配料、电 极制备、电极焊接、布料点焊、eb炉熔炼等复杂流程,对于钛及钛合金生产企 业来说,设备配备少、操作简单,残料回收成本进一步降低。
附图说明
25.图1为本发明技术原理示意图。
26.图中标记:1、辅助电极,2、自耗电极,3、钛及钛合金残料,4、紫铜坩 埚。
具体实施方式
27.针对上述技术方案,现举较佳实施例并结合图示进行具体说明。
28.下述步骤s4中,var熔炼工艺为钛及钛合金领域中的常规var熔炼工艺, 因此,熔炼工艺参数则不再赘述。
29.本发明的低成本短流程钛及钛合金残料回收方法,具体包括以下步骤:
30.s1:将同牌号、同成分标准下钛及钛合金残料块、棒料头、冒口、残屑等残 料收集后,进行成分确认。并对外表存在氧化、油渍等的残料进行喷丸酸洗处理, 烘干处理后备用;残料成分确认采用x射线成分分析仪;喷丸磨料为直径2~3mm 的铸铁丸,酸洗是hno3+hf+水按比例配比的酸液,浸泡时长1小时以上;残 料烘干温度应保持在70~90℃。酸洗是本领域常规技术,具体比例根据实际表面 情况决定。
31.s2:选择规格合适的var紫铜坩埚,根据残料形貌、大小特点直接以堆垛、 间隙填充方式将残料装入紫铜坩埚内,残料间错位码放,并使残料与紫铜坩埚壁 之间留有一定安全间隙,残料错位码放时错位尺寸应保持在10~15mm;残料与 坩埚之间留有的安全间隙应保持在50~60mm之间。装配坩埚后备用,如图1所 示,在紫铜坩埚4内码放钛及钛合金残料3。
32.s3:选择同牌号辅助电极1和自耗电极2各一根,在var炉内进行对焊, 作为阴极;将s2已备好残料的坩埚吊入var炉熔化站作为阳极,并封炉抽真空。 当炉室真空≤1pa时侧漏,漏气率≤0.8pa/min时,开启var炉熔炼电源起弧熔炼, 起弧期电流保持在6~12ka,保持时长≥30min,电压26~34v,稳弧电流12~15a, 稳弧周期15s;充分加热坩埚内残料;待坩埚内残料开始熔化时,进入熔炼期, 将熔炼电流逐渐提升至16~30ka,阴极开始逐渐熔化,熔液开始填充下方残料 各个间隙,待熔液充分填充并包裹坩埚内残料后,断开var炉电源。熔后冷却 时间≥6h,出炉并得到钛及钛合金铸锭一根。
33.s4:将s3得到的钛及钛合金铸锭再经过两次或两次以上var熔炼后,两次 熔炼真空均≤1pa,漏气率≤0.6pa/min;得到一根钛及钛合金成品铸锭。
34.s5:对s4得到的钛及钛合金铸锭进行扒皮处理,并在铸锭头中尾取样检测, 锯切铸锭冒口。
35.实施例1:tc4牌号残料的回收
36.s1:将牌号为tc4的残料块、棒料头、冒口等收集后,利用x射线成分分 析仪进行成分再次确认。并对外表存在氧化、油渍等残料进行喷丸酸洗处理, 喷丸磨料选择直径2~3mm的铸铁丸,在hno3+hf+水按比例配比的酸液中浸泡 时长1小时,然后放入烘箱烘干处理后备用,烘干温度应保持在70~90℃。
37.s2:选择φ540mm规格紫铜坩埚,根据残料形貌、大小特点直接以堆垛、 间隙填充方式将残料装入紫铜坩埚内,残料间错位码放,错位尺寸控制在 10~15mm,并使残料与紫铜坩埚壁之间留有50~60mm安全间隙,装配坩埚后备 用,如图1所示。
38.s3:选择φ280mm tc4辅助电极和φ430mm tc4自耗电极各一根,在var 炉内进行对焊,作为阴极;将s2已备好残料的坩埚吊入var炉熔化站作为阳极, 并封炉抽真空。当炉室真空≤1pa时侧漏,漏气率≤0.8pa/min时,开启var炉熔 炼电源起弧熔炼,起弧期熔炼工艺参数如表1所示。
39.充分加热坩埚内的残料,待坩埚内残料开始熔化时,采用表2熔炼工艺参数 进行
熔炼,自耗电极开始逐渐熔化,熔液开始填充下方坩埚内残料各个间隙,待 熔液充分填充并包裹坩埚内残料后,断开var炉电源。熔后冷却6h,出炉并得 到φ540mm tc4铸锭一根。
40.表1熔炼起弧期工艺参数
41.电流/ka电压/v稳弧电流/a稳弧周期/s时间/min62420151072620158830201551030201510
42.表2熔炼期工艺参数
43.电流/ka电压/v稳弧电流/a稳弧周期/s时间/min1632301552232301552832301560
44.s4:将s3得到φ540mm tc4铸锭进行机加平头处理后,进行一次var熔 炼,坩埚规格φ630mm;再进行机加平头处理,进行二次var熔炼,坩埚规格 φ720mm。即经过两次var熔炼后,得到一根φ720mm tc4成品铸锭;
45.s5:对s4得到的φ720mm tc4铸锭进行扒皮处理,并在铸锭头中尾取样屑 样及气体块样检测,锯切铸锭冒口。
46.最终获得成分的tc4残料回收铸锭各元素成分合格,并优于国标,其成分 如表5所示:
47.表3 tc4牌号残料回收铸锭化学成分(wt%)
[0048][0049]
实施例2:ta1牌号残料的回收
[0050]
s1:将牌号为ta1的残料块、棒料头、冒口等收集后,利用x射线成分分 析仪进行成分再次确认。并对外表存在氧化、油渍等残料进行喷丸酸洗处理, 喷丸磨料选择直径2~3mm的铸铁丸,在hno3+hf+水按比例配比的酸液中浸泡 时长1小时,然后放入烘箱烘干处理后备用,烘干温度应保持在(70~90)℃。
[0051]
s2:选择φ630mm规格紫铜坩埚,根据残料形貌、大小特点直接以堆垛、 间隙填充方式将残料装入紫铜坩埚内,残料间错位码放,错位尺寸控制在 10~15mm,并使残料与紫铜坩埚壁之间留有50~60mm安全间隙,装配坩埚后备 用,如图1所示。
[0052]
s3:选择φ300mm ta1辅助电极和φ540mm ta1自耗电极各一根,在var 炉内进行对焊,作为阴极;将s2已备好残料的坩埚吊入var炉熔化站作为阳极, 并封炉抽真空。当炉
室真空≤1pa时侧漏,漏气率≤0.8pa/min时,开启var熔炼 电源起弧熔炼,起弧期工艺如表4所示。充分加热坩埚内残料,待坩埚内残料开 始熔化时,采用表5熔炼工艺,阴极开始逐渐熔化,熔液开始填充坩埚内残料各 个间隙,待熔液充分填充并包裹坩埚内残料后,断开var炉电源。熔后冷却7h, 出炉并得到φ630mm ta1铸锭一根。
[0053]
表4熔炼起弧期工艺参数
[0054]
电流/ka电压/v稳弧电流/a稳弧周期/s时间/min626201510828201581032201581232201510
[0055]
表5熔炼期工艺参数
[0056]
电流/ka电压/v稳弧电流/a稳弧周期/s时间/min1834301552434301553034301560
[0057]
s4:将s3得到φ630mm ta1铸锭进行机加平头处理后,一次var熔炼, 坩埚φ720mm;再进行机加平头处理,二次var熔炼,坩埚规格φ830mm。经 过两次var熔炼后,得到一根φ830mm ta1成品铸锭;
[0058]
s5:对s4得到的φ830mm ta1铸锭进行扒皮处理,并在铸锭头中尾取样屑 样及气体块样检测,锯切铸锭冒口。
[0059]
最终获得成分的ta1残料回收铸锭各元素成分合格,并优于国标,其成分 如表6所示:
[0060]
表6 ta1牌号残料回收铸锭化学成分(wt%)
[0061][0062]
综合以上,本发明是提供一种低成本短流程钛合金残料回收方法,解决钛及 钛合金残料回收工序流程长、残料利用率低问题,同时降低异物及高密度夹杂带 入风险,有效控制杂质元素增加。所获得的钛及钛合金铸锭质量更可靠,成分分 布更均匀,成分满足并优于gb/t 3620.1《钛及钛合金牌号和化学成分》国标。
[0063]
同时,本发明是提供一种低成本短流程钛合金残料回收方法,通过将同牌号、 同成分标准下的残料进行收集,在坩埚内堆垛,通过残料自身的外周部分熔融与 自耗电极的熔化的熔液相结合,使残料紧密结合成整体铸锭,不需要进行配料、 电极制备、电极焊接、
布料点焊、eb炉熔炼等复杂流程,对于钛及钛合金生产 企业来说,设备配备少、操作简单,残料回收成本进一步降低。
[0064]
以上所述仅是本发明的具体实施方式,使本领域技术人员能够理解或实现本 发明。对这些实施例的多种修改对本领域的技术人员来说将是显而易见的,本文 中所定义的一般原理可以在不脱离本发明的精神或范围的情况下,在其它实施例 中实现。
[0065]
应当理解的是,本发明并不局限于上述已经描述的内容,并且可以在不脱离 其范围进行各种修改和改变。本发明的范围仅由所附的权利要求来限制。