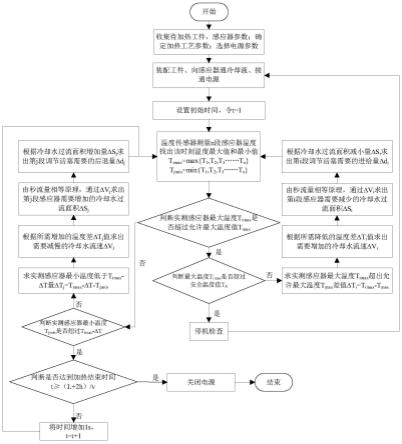
1.本发明涉及材料热加工技术领域,具体而言,尤其涉及一种灵活调节热处理器冷却的控制方法及其实验装置。
背景技术:2.感应加热过程中,感应器多为铜管制作。在采用非埋入式沿表面具有凹凸几何结构的工件扫描淬火工艺时,因感应器与工间之间间隙较小,受加热面的热辐射,以及某些部位有限尺寸的约束,该部位对应的感应器铜管极易过热烧坏,使感应器损坏。感应器进出大型工件端面时,磁力线集中,工件温度的突变也会导致感应线圈温度大幅上升和下降。同时,感应器的物理特性受本身的温度影响,进而使被加热工件周围磁场发生改变,影响加热效果。为使感应器线圈温度均匀,需要保证有足够流量和压力的冷却介质通过。为节约成本,大多数情况下采用常温下的水作为冷却介质。在一定范围内,冷却水的流速越高,带走的热量越多,从而使铜管达到更好的散热效果。
3.目前,市面上常采用一条冷却水路流经全感应器内部的方法进行冷却,全感应器范围内,过低的冷却水流速无法达到较好的散热效果,过高的冷却水流速将导致线圈内部压力过大,既容易造成安全隐患,同时也增加了生产成本。因此,亟需一种通过改变感应线圈内各段冷却水流速的控制方法及实验装置,实现感应器温度分布均匀,使电流在感应器内流动路径保持水平,产生更加合理的磁场分布,提高感应器使用寿命的同时,实现工件温度场均匀分布。
技术实现要素:4.根据上述提出的技术问题,提供一种灵活调节热处理器冷却的控制方法及其实验装置。本发明将电磁热处理中所使用的的感应器分成若干段,通过灵活控制每段感应器内部的冷却水流量,实现对各部分感应器散热量的调节,避免了在移动感应加热过程中由于外界参数改变使感应器整体或某段温度急剧变化导致的加剧损坏的情况。
5.本发明采用的技术手段如下:
6.一种灵活调节热处理器冷却的控制方法,包括:
7.根据工件参数,确定感应器参数、热加工工艺参数及电源参数;
8.基于确定的感应器参数、热加工工艺参数及电源参数,感应器通电对工件进行电磁感应加热,对感应器各段温度值进行监测,并获取该时刻实测感应器的温度最大值和最小值;
9.对实测感应器的温度最大值进行限定,判断获取的实测感应器的温度最大值是否超过允许感应器的温度最大值;
10.基于限定后的实测感应器的温度值以及实测感应器的温度最小值进行均匀化处理,判断实测感应器的温度最小值是否超过实测感应器的温度最大值与允许感应器温差的差值;
11.判断感应器是否达到加热时间,若没有达到加热时间,则温度传感器继续对感应器各段温度值进行监测,并获取该时刻实测感应器的温度最大值和最小值,若达到加热时间,则结束运行,关闭电源。
12.进一步地,所述根据工件参数,确定感应器参数、热加工工艺参数及电源参数,包括:根据大坯料工件参数,确定感应器参数、热加工工艺参数及电源参数;具体包括:
13.确定工件物理参数及几何参数:设工件需加热的长度为l,加热工件的目标温度为tw;
14.确定感应器物理参数及几何参数:设感应器沿电流流经路径方向长度为l,单次有效加热宽度为h,感应器移动速度v,冷却管道内部调节活塞最大行程为d
max
,设初始时d=50%d
max
,冷却水过流面积s;
15.确定热加工工艺参数:设冷却水流速v,感应器安全温度为ta,允许感应器的温度最大值为t
max
,允许感应器温差δt,实测感应器的温度最大值为t
imax
,实测感应器的温度最小值为t
jmin
,加热时间为t=(l+2h)/v;
16.确定电源参数:设电源频率p,电流密度j。
17.进一步地,所述基于确定的感应器参数、热加工工艺参数及电源参数,感应器通电对工件进行电磁感应加热,对感应器各段温度值进行监测,并获取该时刻实测感应器的温度最大值和最小值,包括:
18.将感应器沿电流流经路径方向长度平均分成n段,温度传感器分别监测n段感应器温度;
19.找出该时刻实测感应器最大温度t
imax
=max{t1,t2,t3……
tn}和该时刻实测感应器最小温度t
jmin
=min{t1,t2,t3……
tn}。
20.进一步地,所述对实测感应器的温度最大值进行限定,判断获取的实测感应器的温度最大值是否超过允许感应器的温度最大值,包括:
21.当实测感应器的温度最大值t
imax
超过允许感应器的温度最大值t
max
时,继续判断实测感应器的温度最大值t
imax
是否超过感应器安全温度ta,若实测感应器的温度最大值t
imax
超过感应器安全温度ta,则停机检修,检修完成后,继续对感应器各段温度值进行监测;若实测感应器的温度最大值t
imax
未超过感应器安全温度ta,则计算实测感应器的温度最大值t
imax
超出允许感应器的温度最大值t
max
的差值δti,根据需要减少的温度差δti,计算需要增加的冷却水流速δvi,控制进水口和出水口的压力差恒定,进而得到第i段感应器需要减少的冷却水过流面积δsi,最终得到第i段感应器的调节活塞所需进给量δdi,调节活塞进给δdi后,继续对感应器各段温度值进行监测;
22.当实测感应器的温度最大值t
imax
未超过允许感应器的温度最大值t
max
,则判断实测感应器的温度最小值t
jmin
是否超过实测感应器的温度最大值与允许感应器温差的差值t
imax-δt。
23.进一步地,所述基于限定后的实测感应器的温度值以及实测感应器的温度最小值进行均匀化处理,判断实测感应器的温度最小值是否超过实测感应器的温度最大值与允许感应器温差的差值,包括:
24.当实测感应器的温度最小值t
jmin
未超过限定后的实测感应器的温度最大值与允许感应器温差的差值t
imax-δt,则计算实测感应器的温度最小值t
jmin
低于t
imax-t的差值δ
tj,根据所需增加的温度差δtj,计算需要减慢的冷却水流速δvj,控制进水口和出水口的压力差恒定,进而得到第j段感应器需增加的冷却水过流面积δsj,最终得到第j段调节活塞需要的后退量δdj,调节活塞后退δdi后,继续对感应器各段温度值进行监测;
25.当实测感应器的温度最小值t
jmin
超过限定后的实测感应器的温度最大值与允许感应器温差的差值t
imax-δt时,则判断感应器是否达到加热时间。
26.进一步地,所述感应器安全温度ta根据工件目标温度tw进行设定,设定范围为ta=0.8~1.0tw;所述冷却水过流面积s为调节活塞与感应器最小截面面积。
27.本发明还提供了一种基于上述灵活调节热处理器冷却的控制方法的灵活调节热处理器冷却的实验装置,包括:感应器,进水管,上通水管,连接管,压力泵,上入水管,冷却管道,下出水管,调节活塞,温度传感器,其中:
28.感应器的内侧设置温度传感器,感应器外侧设置有冷却管道,感应器与冷却管道的下方通过高温耐火胶粘接下出水管,感应器与冷却管道的上方通过高温耐火胶粘接上进水管,上进水管的外侧设置压力泵,压力泵的另一端通过连接管焊接上通水管,上通水管的上部焊接进水管,调节活塞依次排布在冷却管道周围的活塞孔内部;冷却管道包括入水口,活塞口,出水口,板式止回阀,板式止回阀铰接在冷却管道的下方,用于防止冷却水回流。
29.进一步地,所述感应器的冷却水由上至下流动,通过压力泵调节入口压力进而保证各段进、出口的压力差恒定。
30.进一步地,所述上入水管分割成n段独立管道,并与对应的压力泵及所述冷却管道形成独立管路。
31.进一步地,所述上入水管、冷却管道、下出水管、调节活塞、板式止回阀均为绝缘材料,所述调节活塞在活塞孔内前后移动,形状、大小、数量随感应器的形状和待加工参数而定。
32.较现有技术相比,本发明具有以下优点:
33.1、本发明针对大坯料的梯度感应加热时的感应器冷却问题,考虑到感应器各段冷却区别不大,设计了一套冷却水通路便可灵活改变全感应器范围内各段的冷却水流速的实验装置,其将冷却管道固定在感应器外侧,解决了感应器的工装问题,减少其受热变形,并且本发明节约水资源,降低了生产过程中的安全隐患。
34.2、本发明实现了对感应器分区域动态精确冷却控制,使感应器整体温度保持稳定;对感应器通电时,稳定的感应器温度使电流在感应器内流动路径保持水平,减少了电流凸点问题的出现,产生更加合理的磁场分布,使得工件产生均匀温度场,进而工件的加工质量得到提升,解决了大坯料工件梯度感应加热过程中感应器温度不均匀的问题。
35.3、本发明按照感应器形状和待加工参数巧妙地将感应器沿长度方向划分为n部分,冷却水在各段感应器内独立流动,在温度传感器的监控下,计算并调整调节活塞的前后移动,通过调整冷却水的过流面积改变感应器各段冷却水的流速,从而灵活控制感应器各段温度,实现全感应器范围内温度均匀,既使感应器的物理性能稳定,又可提高感应器寿命。
36.基于上述理由本发明可在材料热加工等领域广泛推广。
附图说明
37.为了更清楚地说明本发明实施例或现有技术中的技术方案,下面将对实施例或现有技术描述中所需要使用的附图做以简单地介绍,显而易见地,下面描述中的附图是本发明的一些实施例,对于本领域普通技术人员来讲,在不付出创造性劳动性的前提下,还可以根据这些附图获得其他的附图。
38.图1为本发明方法工艺流程图。
39.图2为本发明实验装置总体结构示意图。
40.图3为本发明实施例提供的上进水系统装配图。
41.图4为本发明实施例提供的感应线圈与冷却管道结构图。
42.图5为本发明实施例提供的进出水截面示意图。
43.图6为本发明实施例提供的一种调节活塞示意图。
44.图7为本发明实施例提供的另一种调节活塞示意图。
45.图中:1、感应器;2、进水管;3、上通水管;4、连接管;5、压力泵;6、上入水管;7、冷却管道;701、上入水口;702、活塞口;703、出水口;704、板式止回阀;8、调节活塞;9、下出水管;10、温度传感器。
具体实施方式
46.为了使本技术领域的人员更好地理解本发明方案,下面将结合本发明实施例中的附图,对本发明实施例中的技术方案进行清楚、完整地描述,显然,所描述的实施例仅仅是本发明一部分的实施例,而不是全部的实施例。基于本发明中的实施例,本领域普通技术人员在没有做出创造性劳动前提下所获得的所有其他实施例,都应当属于本发明保护的范围。
47.需要说明的是,本发明的说明书和权利要求书及上述附图中的术语“第一”、“第二”等是用于区别类似的对象,而不必用于描述特定的顺序或先后次序。应该理解这样使用的数据在适当情况下可以互换,以便这里描述的本发明的实施例能够以除了在这里图示或描述的那些以外的顺序实施。此外,术语“包括”和“具有”以及他们的任何变形,意图在于覆盖不排他的包含,例如,包含了一系列步骤或单元的过程、方法、系统、产品或设备不必限于清楚地列出的那些步骤或单元,而是可包括没有清楚地列出的或对于这些过程、方法、产品或设备固有的其它步骤或单元。
48.如图1所示,本发明提供了一种灵活调节热处理器冷却的控制方法,包括:
49.s1、根据工件参数,确定感应器参数、热加工工艺参数及电源参数;
50.在本实施例中,根据大坯料工件参数,确定感应器参数、热加工工艺参数及电源参数;具体包括:
51.s11、确定工件物理参数及几何参数:设工件需加热的长度为l,加热工件的目标温度为tw;
52.s12、确定感应器物理参数及几何参数:设感应器沿电流流经路径方向长度为l,有效加热宽度为h,感应器移动速度v,冷却管道内部调节活塞最大行程为d
max
,设初始时d=50%d
max
,冷却水过流面积s;
53.s13、确定热加工工艺参数:设冷却水流速v,感应器安全温度为ta,允许感应器的
温度最大值为t
max
,允许感应器温差δt,实测感应器的温度最大值为t
imax
,实测感应器的温度最小值为t
jmin
,加热时间为t=(l+2h)/v;
54.s14、确定电源参数:设电源频率p,电流密度j。
55.s2、基于确定的感应器参数、热加工工艺参数及电源参数,对感应器各段温度值进行监测,并获取该时刻实测感应器的温度最大值和最小值;
56.在本实施例中,所述步骤s2具体包括:
57.s21、将感应器沿电流流经路径方向长度平均分成n段,温度传感器分别监测n段感应器温度;
58.s22、找出该时刻实测感应器最大温度t
imax
=max{t1,t2,t3……
tn}和该时刻实测感应器最小温度t
jmin
=min{t1,t2,t3……
tn}。
59.s3、对实测感应器的温度最大值进行限定,判断获取的实测感应器的温度最大值是否超过允许感应器的温度最大值;
60.在本实施例中,所述步骤s3具体包括:
61.s31、当实测感应器的温度最大值t
imax
超过允许感应器的温度最大值t
max
时,继续判断实测感应器的温度最大值t
imax
是否超过感应器安全温度ta,若实测感应器的温度最大值t
imax
超过感应器安全温度ta,则停机检修,检修完成后,继续对感应器各段温度值进行监测;若实测感应器的温度最大值t
imax
未超过感应器安全温度ta,则计算实测感应器的温度最大值t
imax
超出允许感应器的温度最大值t
max
的差值δti,根据需要减少的温度差δti,计算需要增加的冷却水流速δvi,控制进水口和出水口的压力差恒定,进而得到第i段感应器需要减少的冷却水过流面积δsi,最终得到第i段感应器的调节活塞所需进给量δdi,调节活塞进给δdi后,转入步骤s2继续对感应器各段温度值进行监测;
62.s32、当实测感应器的温度最大值t
imax
未超过允许感应器的温度最大值t
max
,则转入步骤s4,判断实测感应器的温度最小值t
jmin
是否超过实测感应器的温度最大值与允许感应器温差的差值t
imax-δt。
63.s4、基于限定后的实测感应器的温度值以及实测感应器的温度最小值进行均匀化处理,判断实测感应器的温度最小值是否超过实测感应器的温度最大值与允许感应器温差的差值;
64.在本实施例中,所述步骤s4具体包括:
65.s41、当实测感应器的温度最小值t
jmin
未超过限定后的实测感应器的温度最大值与允许感应器温差的差值t
imax-δt,则计算实测感应器的温度最小值t
jmin
低于t
imax-t的差值δtj,根据所需增加的温度差δtj,计算需要减慢的冷却水流速δvj,控制进水口和出水口的压力差恒定,进而得到第j段感应器需增加的冷却水过流面积δsj,最终得到第j段调节活塞需要的后退量δdj,调节活塞后退δdi后,转入步骤s2继续对感应器各段温度值进行监测;
66.s42、当实测感应器的温度最小值t
jmin
超过限定后的实测感应器的温度最大值与允许感应器温差的差值t
imax-δt时,则转入步骤s5,判断感应器是否达到加热时间。
67.s5、判断感应器是否达到加热时间,若没有达到加热时间,则温度传感器继续对感应器各段温度值进行监测,并获取该时刻实测感应器的温度最大值和最小值,若达到加热时间,则结束运行,关闭电源。
68.具体实施时,作为本发明优选的实施方式,所述感应器安全温度ta根据工件目标温度tw进行设定,设定范围为ta=0.8~1.0tw;安全温度ta的设定原因为:感应器与工件之间间隙通常为0.5~1mm,当装配精度不够时,易造成感应器与高温工件发生接触,导致感应器温度急速上升,发生烧毁;当参数选择错误时,也会发生上述情况,故设置安全温度ta,当线圈温度发生异常,超过安全温度ta,立即停止通电,检修装配和参数设置情况,然后重新启动装置。
69.具体实施时,作为本发明优选的实施方式,所述冷却水过流面积s为调节活塞与感应器最小截面面积。
70.如图2-5所示,本发明提供了一种基于上述灵活调节热处理器冷却的控制方法的灵活调节热处理器冷却的实验装置,包括:感应器1、进水管2、上通水管3、连接管4、压力泵5、上入水管6、冷却管道7、下出水管9、调节活塞8、温度传感器10,其中:
71.感应器1的内侧设置温度传感器10,感应器1外侧设置有冷却管道7,感应器1与冷却管道7的下方通过高温耐火胶粘接下出水管9,感应器1与冷却管道7的上方通过高温耐火胶粘接上进水管2,上进水管2的外侧设置压力泵5,压力泵5的另一端通过连接管焊接上通水管3,上通水管3的上部焊接进水管2,调节活塞8依次排布在冷却管道7周围的活塞孔内部;冷却管道7包括入水口701,活塞口702,出水口703,板式止回阀704,板式止回阀704铰接在冷却管道7的下方,用于防止冷却水回流。
72.具体实施时,作为本发明优选的实施方式,所述上入水管6分割成n段独立管道,并与对应的压力泵5及所述冷却管道7形成独立管路。
73.具体实施时,作为本发明优选的实施方式,所述上入水管6、冷却管道7、下出水管9、调节活塞8、板式止回阀704均为绝缘材料,如图6所示,所述调节活塞8在活塞孔内前后移动,形状和大小随感应器1的形状和待加工参数而定。调节活塞8的截面为圆弧形,可减少冷却水在入水口701流入和出水口703流出时产生的冲击。
74.最后应说明的是:以上各实施例仅用以说明本发明的技术方案,而非对其限制;尽管参照前述各实施例对本发明进行了详细的说明,本领域的普通技术人员应当理解:其依然可以对前述各实施例所记载的技术方案进行修改,或者对其中部分或者全部技术特征进行等同替换;而这些修改或者替换,并不使相应技术方案的本质脱离本发明各实施例技术方案的范围。