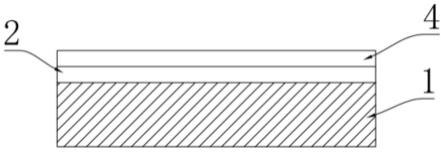
1.本发明涉及材料表面改性技术领域,具体而言,涉及一种表面改性金刚石膜片及其制备方法。
背景技术:2.金刚石材料由于具有极高的热导率、禁带宽度、电子迁移率、抗辐射等特殊且优异的性能。在航空航天、核聚变能开发、高频通讯等尖端科技领域具有不可代替的重大作用。尤其在极高热流密度器件、高能热流密度窗口等应用中,大尺寸金刚石更成为了重要的材料解决方案。在实际应用中,金刚石往往需要与金属基底或框架进行连接,但是金刚石晶体结构中碳原子由共价键结合,化学稳定性极高,具有很高的化学惰性,与绝大多数金属均难以形成有效的界面结合,即使采用钎焊方法,普通的钎料也难以润湿金刚石表面,使得金刚石工具的性能和寿命大大降低。因此,需要对金刚石进行表面改性,以改善金刚石的润湿性和提高金刚石与异种材料基体的结合强度。
3.常用的金刚石表面改性方法主要是在金刚石表面沉积金属化薄膜,使其对异种材料基体具有良好的化学亲和性、可焊性和可镀性。目前,主要采用单元素进行金刚石表面金属化,其中cr和ti是目前最常用的金刚石金属化元素,但单元素金属化薄膜只适于连接金属化薄膜与金刚石,无法同时改善金刚石的可加工性能,且金刚石与金属化薄膜的结合强度不高。
技术实现要素:4.本发明旨在解决金刚石与金属化薄膜的结合强度不高、单元素金属化薄膜无法同时改善金刚石与金属化薄膜结合强度和金刚石的可加工性能问题。
5.为解决上述问题中的至少一个方面,本发明提供一种表面改性金刚石膜片,包括金刚石膜片和设置在金刚石膜片表面的金属化薄膜,其中,金属化薄膜包括依次设置在金刚石膜片表面的cr金属层和niti合金层。
6.与现有技术相比,本发明的表面改性金刚石膜片具有以下有益效果:
7.本发明的表面改性金刚石膜片引入多元素多层级金属化薄膜,在表面改性金刚石膜片中,cr金属层作为界面反应层,可与金刚石界面间的碳原子相互扩散,实现金属化薄膜与金刚石表面的冶金结合,一部分cr元素以原子状态进入金刚石中,另一部分cr元素与金刚石形成碳化铬;其次,与其它强碳化物形成元素相比,cr元素与金刚石的反应更为可控;再者,niti合金层作为连接层,可以与常见的ag-cu钎料、sn-cu钎料、cu-ti钎料、au-si钎料等合金钎料反应形成可靠连接,提升金刚石膜片的可加工性能,从而达到同时改善金刚石与金属化薄膜结合强度和金刚石可加工性能的效果。
8.优选地,金属化薄膜还包括mo金属层,mo金属层设置于cr金属层与niti合金层之间。
9.优选地,金属化薄膜还包括ag金属层,ag金属层设置于niti合金层的外侧。
10.本发明还提供一种表面改性金刚石膜片的制备方法,包括以下步骤:
11.步骤s1,将金刚石膜片进行预处理,除去金刚石膜片表面的杂质;
12.步骤s2,依次将cr金属、mo金属、niti合金和ag金属磁控溅射到预处理后的金刚石膜片表面,得到金刚石/cr/mo/niti/ag膜片;
13.步骤s3,对步骤s2的金刚石/cr/mo/niti/ag膜片进行热处理,得到表面改性金刚石膜片。
14.与现有技术相比,本发明的表面改性金刚石膜片的制备方法具有以下有益效果:
15.本发明的表面改性金刚石膜片的制备方法采用磁控溅射表面改性技术,可以快速地实现多层金属及合金薄膜的沉积,镀层表面平整,厚度可以得到有效控制。磁控溅射后的金属化薄膜处于非晶状态,金属化薄膜与金刚石之间的结合力较弱,本发明对沉积得到的金刚石/cr/mo/niti/ag膜片进一步热处理,随着温度升高,金属化薄膜与金刚石间发生元素扩散,cr金属层与金刚石之间反应生成碳化铬层,可有效提高金刚石与金属化薄膜的结合强度。热处理过程中,mo金属层作为应力缓解层,也起到了隔离元素扩散的作用,防止了外侧的niti合金向金刚石扩散,否则过多的触媒元素和金刚石发生反应,也会降低整体的结合强度。niti合金层可以缓解和改善金刚石表面润湿性及可加工性能。ag金属层可使改性后的金刚石可以在空气环境中较长时间存储而不被氧化。
16.优选地,预处理工艺为:
17.步骤s11,将金刚石膜片浸泡到酒精中,超声清洗5-10min后,取出烘干;
18.步骤s12,将烘干的金刚石膜片放入碱溶液中煮沸,取出后用去离子水清洗,然后放入酸溶液中煮沸,取出后冷却,再用去离子水冲洗至中性。
19.优选地,碱溶液为15%-20%的naoh溶液,酸溶液为15%-20%的hcl溶液
20.优选地,步骤s2中磁控溅射是先采用直流溅射工艺将cr金属和mo金属依次溅射到预处理过的金刚石膜片表面得到cr金属层和mo金属层,然后采用强磁溅射工艺将niti合金溅射在mo金属层外侧得到niti合金层,再采用射频溅射工艺将ag金属溅射到niti合金层外侧得到ag金属层。
21.优选地,cr金属的直流溅射工艺参数为:溅射功率150-200w,溅射时间1-3h,溅射气压1-5pa、溅射气流20sccm、溅射靶基距5-15cm;mo金属的直流溅射工艺参数为:溅射功率为120-160w,溅射时间1-3h,溅射气压1-5pa、溅射气流20sccm、溅射靶基距5-15cm。
22.优选地,niti合金的强磁溅射工艺参数为:溅射功率150-200w,溅射时间2-4h,溅射气压1-5pa、溅射气流20sccm、溅射靶基距5-15cm。
23.优选地,ag金属的射频溅射工艺参数为:溅射功率100-150w,溅射时间0.5-1h,溅射气压1-5pa、溅射气流20sccm、溅射靶基距5-15cm。
24.优选地,步骤s3的热处理工艺如下:将金刚石/cr/mo/niti/ag膜片放入真空热处理设备中,以5-10℃/min的升温速率,将温度从室温升至300-600℃,保温1-2h,再以5-10℃/min的降温速率降温至200℃,然后随炉冷却后取出,最终得到表面改性金刚石膜片。
25.优选地,步骤s3中,真空热处理设备中的真空度小于10-4
pa。
附图说明
26.图1为本发明实施例中表面改性金刚石/cr/niti膜片的结构示意图;
27.图2为本发明实施例中表面改性金刚石/cr/mo/niti膜片的结构示意图;
28.图3为本发明实施例中表面改性金刚石/cr/mo/niti/ag膜片的结构示意图;
29.图4为本发明实施例中表面改性金刚石/cr/mo/niti/ag膜片制备方法的步骤流程图;
30.图5为本发明实施例中表面改性金刚石膜片的纵切面sem扫描电镜图;
31.图6为本发明实施例中表面改性金刚石膜片的表面sem扫描电镜图。
32.附图标记说明:
33.1、金刚石膜片,2、cr金属层,3、mo金属层,4、niti合金层,5、ag金属层。
具体实施方式
34.为使本发明的上述目的、特征和优点能够更为明显易懂,下面结合附图对本发明的具体实施例做详细的说明。
35.需要说明的是,在不冲突的情况下,本发明中的实施例及实施例中的特征可以相互组合。
36.另外,术语“包含”、“包括”、“含有”、“具有”的含义是非限制性的,即可加入不影响结果的其它步骤和其它成分。如无特殊说明的,材料、设备、试剂均为市售。
37.图1为本发明提供的表面改性金刚石膜片结构示意图。结合图1所示,本发明实施例提供了一种表面改性金刚石膜片,包括金刚石膜片和设置在金刚石膜片表面的金属化薄膜,其中,金属化薄膜包括依次设置在金刚石膜片表面的cr金属层和niti合金层。
38.本发明实施例通过金刚石表面改性工艺将cr金属和niti合金依次沉积在金刚石膜片表面,其中,cr金属层作为界面反应层,可与金刚石界面间的碳原子相互扩散,实现金属化薄膜与金刚石表面的冶金结合,一部分cr元素以原子状态进入金刚石中,另一部分cr元素与金刚石形成碳化铬,其次,与其它强碳化物形成元素相比,cr元素与金刚石的反应更为可控;niti合金层作为连接层,可以与常见的ag-cu钎料、sn-cu钎料、cu-ti钎料、au-si钎料等合金钎料反应形成可靠连接,提升金刚石膜片的可加工性能,从而达到同时改善金刚石与金属化薄膜结合强度和金刚石可加工性能的效果。
39.图2为本发明实施例提供的经过改进后的表面改性金刚石膜片结构示意图,包括金刚石膜片和设置在金刚石膜片表面的金属化薄膜,其中,金属化薄膜包括依次设置在金刚石膜片表面的cr金属层、mo金属层和niti合金层。mo金属层可作为金属化薄膜的应力缓解层,这是因为mo具有较高的杨氏模量、屈服极限和低塑性,可以使残余应力从较为薄弱的界面位置转移至较硬mo中间层中,从而提高接头残余应力耐受力。
40.图3为本发明实施例提供的经过进一步改进后的表面改性金刚石膜片结构示意图,包括金刚石膜片和设置在金刚石膜片表面的金属化薄膜,其中,金属化薄膜包括依次设置在金刚石膜片表面的cr金属层、mo金属层、niti合金层和ag金属层。ag金属层可以有效地隔绝空气,因此可以防止niti层在空气中氧化失效,另外,由于制备的ag金属层含量很少,并且ag作为多种体系钎料的添加元素,与钎料相容性好,常见的ag基钎料、sn基钎料、au基钎料都可以将ag层溶解,所以不会对niti合金层与目标材料的连接造成影响
41.图4为本发明提供的表面改性金刚石膜片的制备方法的步骤流程图。结合图4所示,本发明实施例提供了一种表面改性金刚石膜片的制备方法,包括以下步骤:
42.步骤s1,将金刚石膜片进行预处理,除去金刚石膜片表面的杂质;
43.步骤s2,依次将cr金属、mo金属、niti合金和ag金属磁控溅射到预处理后的金刚石膜片表面,得到金刚石/cr/mo/niti/ag膜片;
44.步骤s3,对步骤s2的金刚石/cr/mo/niti/ag膜片进行热处理,得到表面改性金刚石膜片。
45.金刚石表面改性工艺主要有磁控溅射法、化学镀法、真空蒸发镀膜法,其中磁控溅射法主要利用气体辉光放电时气体等离子化产生的离子对阴极靶轰击,使靶原子等颗粒物飞溅出来落到基底表面,进而形成薄膜。但现有的磁控溅射法只是将靶原子沉积在金刚石表面,靶原子与金刚石之间仅靠范德华力结合,膜基结合力弱,导致金刚石与金属化薄膜的结合强度不高。
46.本发明实施例的表面改性金刚石膜片的制备方法采用磁控溅射表面改性技术,可以快速地实现多层金属及合金薄膜的沉积,镀层表面平整,厚度可以得到有效控制。磁控溅射后的金属化薄膜处于非晶状态,金属化薄膜与金刚石之间的结合力较弱,本发明对沉积得到的金刚石/cr/niti膜片进一步热处理,随着温度升高,金属化薄膜与金刚石间发生元素扩散,cr金属层与金刚石之间反应生成碳化铬层,可有效提高金刚石与金属化薄膜的结合强度。mo金属层作为应力缓解层,也起到了隔离元素扩散的作用,防止了外侧的niti合金向金刚石扩散,否则过多的触媒元素和金刚石发生反应,也会降低整体的结合强度。niti合金层可以缓解和改善金刚石表面润湿性及可加工性能。ag金属层可使改性后的金刚石可以在空气环境中较长时间存储而不被氧化。
47.作为本发明实施例表面改性金刚石膜片的制备方法的进一步改进,具体地预处理工艺为:
48.步骤s11,将金刚石膜片浸泡到酒精中,超声清洗5-10min后,取出烘干;
49.步骤s12,将烘干的金刚石膜片放入碱溶液中煮沸,取出后用去离子水清洗,然后放入酸溶液中煮沸,取出后冷却,再用去离子水冲洗至中性。
50.优选地,碱溶液为15%-20%的naoh溶液,酸溶液为15%-20%的hcl溶液。
51.作为本发明实施例表面改性金刚石膜片的制备方法中磁控溅射的进一步改进,步骤s2中磁控溅射是先采用直流溅射工艺将cr金属和mo金属依次溅射到预处理过的金刚石膜片表面得到cr金属层和mo金属层,然后采用强磁溅射工艺将niti合金溅射在mo金属层外侧得到niti合金层,再采用射频溅射工艺将ag金属溅射到niti合金层外侧得到ag金属层。
52.其中,cr金属的直流溅射工艺参数为:溅射功率150-200w,溅射时间1-3h,溅射气压1-5pa、溅射气流20sccm、溅射靶基距5-15cm;mo金属的直流溅射工艺参数为:溅射功率为120-160w,溅射时间1-3h,溅射气压1-5pa、溅射气流20sccm、溅射靶基距5-15cm;niti合金的强磁溅射工艺参数为:溅射功率150-200w,溅射时间2-4h,溅射气压1-5pa、溅射气流20sccm、溅射靶基距5-15cm;ag金属的射频溅射工艺参数为:溅射功率100-150w,溅射时间0.5-1h,溅射气压1-5pa、溅射气流20sccm、溅射靶基距5-15cm。
53.作为本发明实施例表面改性金刚石膜片的制备方法中热处理步骤的进一步改进,步骤s3中金刚石/cr/mo/niti/ag膜片的热处理步骤如下:将金刚石/cr/mo/niti/ag膜片放入真空热处理设备中,以5-10℃/min的升温速率,将温度从室温升至300-600℃,保温1-2h,再以5-10℃/min的降温速率降温至200℃,然后随炉冷却后取出,最终得到表面改性金刚石
膜片。
54.本发明实施例的热处理步骤中,真空钎焊炉的真空度小于10-4
pa,随着退火温度的提高,氧化反应的速度会显著增加,但较好真空度可控制高温热处理时伴随的氧化反应。真空钎焊炉的保温温度越高与保温时间越长,表面改性金刚石膜片越厚。随着温度升高,金属化薄膜与金刚石间发生元素扩散,cr层与金刚石之间反应生成碳化铬层,且随着热处理温度的升高以及保温时间的延长,界面处产生的碳化物逐渐增多,碳化物层的厚度也随之升高,但过厚的脆性碳化铬层会降低cr层与金刚石的结合强度。因此需要将温度控制在300-600℃之间,否则生成过多的脆性碳化物反而会降低界面的结合强度。在300-600℃热处理温度中,随着热处理温度升高,cr/金刚石界面的宽度加大,扩散反应加剧。热处理温度低于500℃时,基本不能形成稳定的cr2c碳化物层,界面反应物为cr2c3;只有当温度高于500℃后,才能形成cr2c稳定碳化物层。延长热处理时间也会导致不同的界面产物生成。当热退火时间少于4h时,界面反应产物主要为cr2c3,而在更长的时间热退火处理后则以cr2c碳化物为主。
55.为了对本发明进行进一步详细说明,下面结合具体实施例对本发明进行进一步说明。本发明中的实施例中所使用的实验方法如无特殊说明,均为常规方法;本发明中的实施例中所用的材料、试剂等,如无特殊说明,均为市场购买所得。
56.实施例1
57.本实施例提供一种表面改性金刚石膜片的制备方法,包括以下步骤:
58.步骤s1,将金刚石膜片浸泡到酒精,超声清洗5min后,取出烘干;
59.步骤s2,将烘干的金刚石膜片放入15%的naoh溶液中煮沸,取出后用去离子水清洗,然后放入15%的hcl溶液中煮沸,取出后冷却并用去离子水冲洗至中性;
60.步骤s3,将cr金属靶放置到磁控溅射装置中的直流靶位,再将预处理好的金刚石膜片粘贴到磁控溅射设备的载物盘上,之后开始溅射,溅射的工艺参数为:溅射功率150w,溅射时间1h,溅射气压3pa、溅射气流20sccm、溅射靶基距10cm;
61.步骤s4,将直流靶位更换为mo金属靶,将niti合金靶和ag金属靶分别放置到强磁靶位和交流靶位,溅射开始后先溅射mo金属层,保持溅射气压、气流、靶基距不变,溅射功率为120w,溅射时间1h;之后溅射niti合金层,溅射功率150w,溅射时间2h;最后溅射ag金属层,溅射功率100w,溅射时间0.5h。
62.步骤s5,将金刚石/cr/mo/niti/ag膜片放入真空度优于10-4
pa的真空钎焊炉中,以5℃/min的升温速率,将金刚石/cr/mo/niti/ag膜片的温度从室温升至300℃,保温1h,再以5℃/min的降温速率降温至200℃,然后随炉冷却后取出,最终得到表面改性金刚石膜片。
63.实施例2
64.将实施例1得到的表面改性金刚石膜片纵向切面,利用sem扫描电镜观察不同层级的表面改性金刚石膜片,如图5所示,可以发现sem图中的ag金属层的厚度为0.77μm,ag金属层的平均厚度可达到0.5-1.0μm。另外,对实施例1得到的表面改性金刚石膜片表面进行sem扫描,如图6所示,可见ag金属层致密,与金属化薄膜结合良好,可以防止niti合金层在热处理工艺中被氧化。
65.实施例3
66.用球痕法对实施例1得到的表面改性金刚石膜片进行金刚石膜片与金属化薄膜的
结合力测量,测量结果显示,通过实施例1的制备方法制得的金刚石膜片与金属化薄膜的膜基结合力达到11mpa,结合强度较高,满足改性后的金刚石后续的工艺要求。
67.虽然本公开披露如上,但本公开的保护范围并非仅限于此。本领域技术人员在不脱离本公开的精神和范围的前提下,可进行各种变更与修改,这些变更与修改均将落入本发明的保护范围。