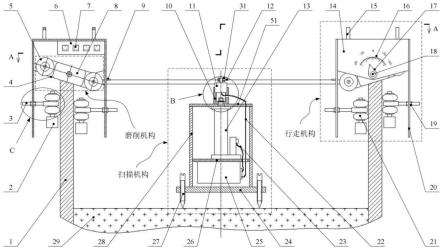
1.本发明涉及一种风电机组维修设备,尤其是一种风电基础环端面自动磨削找平方法及装置。
背景技术:2.我国是全球风电装机容量最大的国家,为确保我国风电产业健康发展,国家标准和行业要求必须保障风电机组的安装质量,而良好的安装是保障我国风电装备安全高效运行的重要前提。作为风电机组的基础、关键部件,风电基础环的水平度直接关系到风电塔筒的稳定性和可靠性,因此在塔筒安装之前必须检测基础环的水平度。由于基础环与混凝土基座固连在一起,受混凝土收缩和焊接应力释放,不可避免地会出现端面水平度不达标的情况。
3.目前,改善基础环水平度普遍采用的方法是:首先用水平仪查找基础环倾斜的方向,并手动标记出基础环偏低的部位,然后在位于这些部位的螺栓孔处增加一些平垫片,使基础环偏低的部位大部分都能接近水平位置。由于垫片的厚度大都为标准值,所以很难使基础环端面重新恢复水平。当塔筒安装在加装了垫片的基础环上时,塔筒法兰面与基础环端面仅在有垫片的部分位置良好接触,其余大部分位置均存在空隙。由于基础环端面和塔筒法兰面均加工有坡口,以增加接触面积并起到防水、防尘等作用,而加装垫片后塔筒法兰面与基础环端面之间存在大量空隙,不仅接触面积大幅减小,更难以防止雨水、尘土等进入,加速塔筒和基础环锈蚀。另外,通过加装垫片实现基础环找平的技术方式,需要耗费大量人工,且需要大量重复劳动,工作效率十分低下,一定程度上拖慢了风电机组的安装进程。
4.目前,除加装垫片外,尚未见到其它调整或改善基础环水平度的有效方法。为确保风电机组长期安全服役,保障我国风电装备运行安全和风电行业健康发展,风电安装行业亟需开发一套基础环法兰面自动找平方法,以及与之配套的自动化装置。
技术实现要素:5.针对背景技术中的现实需求和技术问题,本发明提出了一种风电基础环端面自动磨削找平方法及装置,主要目的是通过磨削加工使风电基础环的端面与水平面平行,以完全满足风电塔筒的安装要求,从而确保风电机组的安装质量和运行安全。本发明的技术方案是这样实现的:
6.一方面,本发明提出了一种风电基础环端面自动磨削找平方法,其特征在于包含以下两个步骤:
7.步骤s1:扫描寻找基础环端面的最低位置。具体地,第
①
步,在基础环内侧轴线处安装一个超声波双向探头;第
②
步,使超声波双向探头360
°
旋转,且由高到低缓慢下降,每转过一个360
°
则停止下降0.5s,后继续下降且连续旋转;第
③
步,发射超声波信号,若超声波双向探头在旋转一周期间能持续接收到发射信号,则停止下降,但仍需继续旋转,此时恰
好到达基础环端面的最低位置;第
④
步,令超声波双向探头在最低位置处保持360
°
连续旋转。
8.步骤s2:边扫描判断边磨削基础环端面的其它位置。具体地,第
①
步,在基础环上架设超声波接收探头和磨削装置;第
②
步,判断超声波接收探头所在位置是否需要磨削,即判断超声波接收探头是否接收到超声波双向探头发出的信号;若未接收到信号则进入第
③
步,令磨削装置将所在位置处的基础环端面向下磨削0.5mm,后进入第
④
步,令磨削装置沿基础环端面顺时针移动50mm;若接收到信号则直接进入第
④
步,令磨削装置沿基础环端面顺时针移动50mm;第
⑤
步,人工判断基础环端面是否已磨削完毕;若已磨完整个端面则进入第
⑥
步,停止磨削并结束作业,若未磨完整个端面,则返回第
②
步,重新判断超声波接收探头所在位置是否需要磨削,并重新执行第
②
至第
⑤
步;
……
,多次循环作业,直至完成全部磨削工作,使基础环端面与水平面平行为止。
9.另一方面,本发明还提出了一种风电基础环端面自动磨削找平装置,其特征在于主要包括扫描机构、行走机构和磨削机构三部分,所述扫描机构竖直放置于基础环内部的混凝土基座上面,而基础环下部与混凝土基座固连在一起,扫描机构的轴线与基础环的轴线基本重合,且扫描机构上设有超声波双向探头;两套所述行走机构分别自上而下套装于基础环左右两侧的管壁上,且两套行走机构位于基础环内部的一侧均水平安装有超声波接收探头;两套所述磨削机构分别置于行走机构内部且位于基础环端面的上方,由于基础环的端面为向内的坡口,故两套磨削机构均沿基础环的坡口倾斜放置,而倾斜的角度恰好与基础环的坡口倾角一致。
10.所述扫描机构主要由底板、调节螺钉、箱罩、隔板、电动缸、顶板、套杯、舵机、扫描块、超声波双向探头组成,其中底板边缘竖直加工有四个螺纹孔,四个螺纹孔内竖直安装有四个调节螺钉,调节螺钉下部尖端与混凝土基座接触,上端位于底板上方,用平口螺丝刀转动调节螺钉上端即可调节底板高度。底板上面竖直焊接有一个箱罩,箱罩顶部水平放置有一块顶板,顶板上面放置有一个套杯,顶板和套杯的中央各加工有一个通孔,电动缸上部伸出一根电缸主轴,电缸主轴穿过顶板和套杯中央的通孔,并通过螺母垫片组件将电动缸、顶板和套杯固连在一起。电动缸的底部固定在隔板上侧面中部,隔板下侧面固定有电瓶。套杯内侧上部竖直安装有舵机,舵机轴上部套装在扫描块中部,扫描块左侧加工有一个螺纹孔,螺纹孔内水平地安装有紧定螺钉,紧定螺钉使舵机轴与扫描块固连在一起;扫描块右侧也加工有一个螺纹孔,螺纹孔内水平地安装有超声波双向探头。舵机底部接出一根舵机导线,舵机导线穿过套杯右侧的穿线孔后从顶板右侧的通孔向下穿出,电动缸右侧接出一根电缸导线,舵机导线与电缸导线同时从隔板右侧的通孔向下穿出,后一并接入电瓶右侧,使电瓶同时为舵机和电动缸供电。
11.所述行走机构主要由竖板、壳体、芯轴、指针、螺杆、橡胶轮、电动机、电池组成,其中两块竖板下部通过八个成对螺母安装有四根螺杆,四根螺杆的端部固定焊接有四根连杆,四根连杆中部各套装有一对轴承,轴承的内圈套装在电动机轴的中部,轴承两侧的电动机轴上套装有两个橡胶轮,两个橡胶轮两侧的电动机轴上套装有四个电动机轴卡簧,用于固定橡胶轮和连杆在电动机轴上的相对位置。位于两块竖板前端的两根电动机轴上,连接有两台电动机,电动机轴是专为电动机定制的加长主轴。每个橡胶轮的边缘均与基础环的侧壁贴合。两块竖板上部之间水平焊接有一块壳体,两块竖板与壳体相交的四个角处各焊
接有一块三角形的肋板,壳体的上侧面上固定焊接有两个手柄,壳体的下侧面右部固定安装有一块电池,电池的前侧面上设置有四个插座,两台电动机可从电池前侧面上的任意两个插座处取电。壳体前侧面中部设有转角刻度,转角刻度中间的刻度为0
°
,左右两侧的刻度分别从0
°
依次增大至-60
°
或+60
°
。壳体的前后侧面下部中央同一位置处分别加工有一个通孔,芯轴一端过盈安装有一个指针,另一端穿过壳体前侧面的通孔后,从壳体后侧面的通孔穿出,并通过芯轴卡簧固定在壳体的前后两侧面之间。芯轴发生转动时可带动指针发生偏转,使指针尖端指向转角刻度的不同度数。
12.所述磨削机构主要由砂带、带轮、压块、电机、定位盘组成,其中压块中部沿轴向加工有通孔,压块上部中央沿竖直方向加工有定位孔,定位孔内安装有紧定螺栓,压块通过通孔套装在芯轴上,并处于壳体的前后两个侧面之间,紧定螺栓下端与芯轴紧密贴合,使芯轴与压块同步转动。压块左右两侧伸出两个侧耳,两个侧耳上通过电机安装螺栓安装有两台电机,两台电机可从电池前侧面上的其余两个插座处取电。两台电机的前端伸出两根电机轴,电机轴是专为电机定制的加长主轴,两根电机轴前端分别加工有一端螺纹,两根电机轴中部各套装有一个电机轴卡簧。螺母和定位盘同轴焊接成一体,并通过定位螺栓固定在带轮的前端面上,带轮、定位盘和螺母通过电机轴上前端的螺纹套装在电机轴上,带轮后侧面与电机轴卡簧紧密贴合。螺母与电机轴之间通过定位销相互定位,使电机轴带动带轮一起转动。每两个带轮之间套装有一条砂带,砂带的内侧面与压块的上下侧面贴合,砂带的外侧面下方与基础环的端面贴合。两台电机带动两个带轮同步逆时针旋转时,砂带随之逆时针转动,此时砂带表面的磨粒可将基础环端面的金属材料磨削掉。两套行走机构带动两套磨削机构在基础环上顺时针行走时,根据上述步骤s2,通过判断超声波接收探头是否接收到超声波双向探头发出的信号,即可令砂带在基础环端面的不同位置磨削掉不同厚度的金属材料,最终使基础环端面与水平面平行,以完全满足风电塔筒的安装要求,从而确保风电机组的安装质量和运行安全。
13.现行的风电基础环端面找平方法,是通过在基础环端面若干个位置增加平垫片来实现的,完全依靠人工,相对于现有技术,本发明具有4个显著的优点:
14.1、接触面积更大。现有技术中塔筒端面与基础环端面多在垫片表面接触,而本发明提出的技术方案是将整个基础环端面磨削至水平,从而使塔筒端面与基础环端面全部接触,因此接触面积更大。
15.2、配合精度更高。现有技术中塔筒端面与基础环端面上的垫片的坡口并不完全一致,基础环上的部分支撑位置难以达到预期的高度,各接触点处的配合情况也不一致,而本发明提出的技术方案是将基础环端面整体磨削至水平,且坡口情况完全一致,因此塔筒端面与基础环端面全截面配合一致,配合精度更高。
16.3、自动化程度更高。现有技术通过人手工增加垫片来逐渐将基础环端面垫高,接近水平,其间需要不断更换不同厚度的垫片,劳动强度很大,重复劳动居多,而本发明提出的技术方案通过整个端面的磨削,全程由机器自动完成,省时省力,自动化程度高。
17.4、使用寿命更长。现有技术中塔筒端面与基础环端面仅在垫片表面接触,在风载荷作用下塔筒长期随机摆动,在垫片上持续时间随机挤压载荷,垫片极易发生疲劳或冲击破坏,连接螺栓也易发生剪切破坏,而本发明提出的技术方案能使塔筒端面与基础环端面全截面接触,在塔筒摆动过程中承载能力更好,因此使用寿命更长。
附图说明
18.图1为本发明所涉及的一种风电基础环端面自动磨削找平方法的流程图。
19.图2为本发明所涉及的一种风电基础环端面自动磨削找平装置的正视剖视图。
20.图3为图2中的a向视图。
21.图4为图2中的b向局部放大图。
22.图5为图2中的c向局部放大图。
23.图6为本发明中所提及的磨削机构的半剖结构图。
24.图7为图6中的d向视图。
25.图8为图6中的e向视图。
26.图中:1.基础环 2.电动机 3.螺杆 4.砂带 5.带轮 6.电池 7.插座 8.压块 9.超声波接收探头 10.套杯 11.舵机 12.超声波双向探头 13.电动缸 14.壳体 15.手柄 16.倾角刻度 17.指针 18.芯轴 19.成对螺母 20.竖版 21.橡胶轮 22.舵机导线 23.电缸导线 24.底板 25.电瓶 26.隔板 27.调节螺钉 28.箱罩 29.混凝土基座 30.电机 31.扫描块 32.肋板 33.芯轴卡簧 34.紧定螺钉 35.舵机轴 36.穿线孔 37.螺母垫片组件 38.电缸主轴 39.电动机轴 40.连杆 41.轴承 42.电动机轴卡簧 43.电机轴卡簧 44.内六角螺栓 45.定位孔 46.电机轴 47.螺母 48.定位螺栓 49.定位盘 50.紧定螺栓 51.顶板 52.通孔 53.定位销
具体实施方式
27.下面结合图1至图8,对本发明的具体实施方式进行详细说明。
28.如图1所示,一种风电基础环端面自动磨削找平方法,主要包含两个步骤:
29.步骤s1:扫描寻找基础环端面的最低位置,具体地,第
①
步,在基础环内侧轴线处安装一个超声波双向探头;第
②
步,使超声波双向探头360
°
旋转,且由高到低缓慢下降,每转过一个360
°
则停止下降0.5s,后继续下降且连续旋转;第
③
步,发射超声波信号,若超声波双向探头在旋转一周期间能持续接收到发射信号,则停止下降,此时恰好到达基础环端面的最低位置,但仍需继续旋转;第
④
步,令超声波双向探头在基础环的最低位置处保持360
°
连续旋转。
30.步骤s2:边扫描判断边磨削基础环端面的其它位置,具体地,第
①
步,在基础环上架设超声波接收探头和磨削装置;第
②
步,判断超声波接收探头所在位置是否需要磨削,即判断超声波接收探头是否接收到超声波双向探头发出的信号;若未接收到信号则进入第
③
步,令磨削装置将所在位置处的基础环端面向下磨削0.5mm,后进入第
④
步,令磨削装置沿基础环端面顺时针移动50mm;若接收到信号则直接进入第
④
步,令磨削装置沿基础环端面顺时针移动50mm;第
⑤
步,人工判断基础环端面是否已磨削完毕;若已磨完整个端面则进入第
⑥
步,停止磨削并结束作业;若未磨完整个端面,则返回第
②
步,重新判断超声波接收探头所在位置是否需要磨削,并依次执行第
②
至第
⑤
步,
……
,如此不断重复,直至完成全部磨削工作。
31.如图2和图3所示,一种风电基础环端面自动磨削找平装置,主要包括扫描机构、行走机构和磨削机构三部分,所述扫描机构竖直放置于基础环1内部的混凝土基座29上面,而基础环1下部与混凝土基座29固连在一起,扫描机构的轴线与基础环1的轴线基本重合,且
扫描机构上设有超声波双向探头12;两套所述行走机构分别自上而下套装于基础环1左右两侧的管壁上,且两套行走机构位于基础环1内部的一侧均水平安装有超声波接收探头9;两套所述磨削机构分别置于行走机构内部且位于基础环1的端面上方,由于基础环1的端面为向内的坡口,故两套磨削机构均沿基础环1的坡口倾斜放置,而倾斜的角度恰好与基础环1的坡口倾角一致。
32.如图2、图3和图4,所述扫描机构主要由底板24、调节螺钉27、箱罩28、隔板26、电动缸13、顶板51、套杯10、舵机11、扫描块31、超声波双向探头12组成,其中底板24边缘竖直加工有四个螺纹孔,四个螺纹孔内竖直安装有四个调节螺钉27,调节螺钉27下部尖端与混凝土基座29接触,上端位于底板24上方,用平口螺丝刀转动调节螺钉27上端即可调节底板高度。底板24上面竖直焊接有一个箱罩28,箱罩28顶部水平放置有一块顶板51,顶板51上面放置有一个套杯10,顶板51和套杯10的中央各加工有一个通孔,电动缸13上部伸出一根电缸主轴38,电缸主轴38穿过顶板51和套杯10中央的通孔,并通过螺母垫片组件37将电动缸13、顶板51和套杯10固连在一起。电动缸13的底部固定在隔板26上侧面中部,隔板26下侧面固定有电瓶25。结合图4,套杯10内侧上部竖直安装有舵机11,舵机轴35上部套装在扫描块31中部,扫描块31左侧加工有一个螺纹孔,螺纹孔内水平地安装有紧定螺钉34,紧定螺钉34使舵机轴35与扫描块31固连在一起;扫描块31右侧也加工有一个螺纹孔,螺纹孔内水平地安装有超声波双向探头12。舵机11底部接出一根舵机导线22,舵机导线22穿过套杯10右侧的穿线孔36后从顶板51右侧的通孔向下穿出,电动缸13右侧接出一根电缸导线23,舵机导线22与电缸导线23同时从隔板26右侧的通孔向下穿出,后一并接入电瓶25右侧,使电瓶25同时为舵机11和电动缸13供电。
33.如图2、图3和图5,所述行走机构主要由竖板20、壳体14、芯轴18、指针17、螺杆3、橡胶轮21、电动机2、电池6组成,其中两块竖板20下部通过八个成对螺母19安装有四根螺杆3,四根螺杆3的端部固定焊接有四根连杆40,四根连杆40中部各套装有一对轴承41,轴承41的内圈套装在电动机轴39的中部,轴承41两侧的电动机轴39上套装有两个橡胶轮21,两个橡胶轮21两侧的电动机轴39上套装有四个电动机轴卡簧42,用于固定橡胶轮21和连杆40在电动机轴39上的相对位置。位于两块竖板20前端的两根电动机轴39上,连接有两台电动机2,电动机轴39是专为电动机2定制的加长主轴。每个橡胶轮21的边缘均与基础环1的侧壁贴合。两块竖板20上部之间水平焊接有一块壳体14,两块竖板(20)与壳体(14)相交的四个角处各焊接有一块三角形的肋板32,壳体14的上侧面上固定焊接有两个手柄15,壳体14的下侧面右部固定安装有一块电池6,电池6的前侧面上设置有四个插座7,两台电动机2可从电池6前侧面上的任意两个插座7处取电。壳体14前侧面中部设有转角刻度16,转角刻度16中间的刻度为0
°
,左右两侧的刻度分别从0
°
依次增大至-60
°
或+60
°
。壳体14的前后侧面下部中央同一位置处分别加工有一个通孔,芯轴18一端过盈安装有一个指针17,另一端穿过壳体14前侧面的通孔后,从壳体14后侧面的通孔穿出,并通过芯轴卡簧33固定在壳体14的前后两侧面之间。芯轴18发生转动时可带动指针17发生偏转,使指针17尖端指向转角刻度16的不同度数。
34.如图2、图3和图6所示,所述磨削机构主要由砂带4、带轮5、压块8、电机30、定位盘49组成,其中压块8中部沿轴向加工有通孔52,结合图7,压块8上部中央沿竖直方向加工有定位孔45,定位孔45内安装有紧定螺栓50,压块8通过通孔52套装在芯轴18上,并处于壳体
14的前后两个侧面之间,紧定螺栓50下端与芯轴18紧密贴合,使芯轴18与压块8同步转动。压块8左右两侧伸出两个侧耳,两个侧耳上通过电机安装螺栓44安装有两台电机30,两台电机30可从电池6前侧面上的其余两个插座7处取电。两台电机30的前端伸出两根电机轴46,电机轴46是专为电机30定制的加长主轴,两根电机轴46前端分别加工有一端螺纹,两根电机轴46中部各套装有一个电机轴卡簧43。结合图8,螺母47和定位盘49同轴焊接成一体,并通过定位螺栓48固定在带轮5的前端面上,带轮5、定位盘49和螺母47通过电机轴46上前端的螺纹套装在电机轴46上,带轮5后侧面与电机轴卡簧43紧密贴合。螺母47与电机轴46之间通过定位销53相互定位,使电机轴46带动带轮5一起转动。每两个带轮5之间套装有一条砂带4,砂带4的内侧面与压块8的上下侧面贴合,砂带4的外侧面下方与基础环1的上端面贴合。两台电机30带动两个带轮5同步逆时针旋转时,砂带4随之逆时针转动,此时砂带4表面的磨粒可将基础环1端面的金属材料磨削掉。
35.参见图2和图3,两套行走机构带动两套磨削机构在基础环1上顺时针行走时,根据图1所示的流程,通过判断超声波接收探头9是否接收到超声波双向探头12发出的信号,即可令砂带4在基础环1的不同位置磨削掉不同厚度的金属材料,最终使基础环1的端面与水平面平行,以完全满足风电塔筒安装要求,从而确保风电机组的安装质量和运行安全。