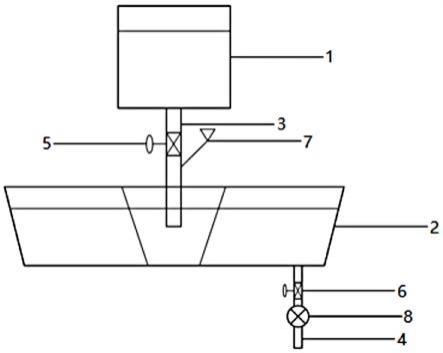
1.本发明属于连铸的技术领域,涉及一种浇注末期下渣的吹氩控制装置及使用方法。
背景技术:2.在连铸过程中,中间包是必不可少的冶金容器;其连接着钢包和结晶器,具有稳定成分温度、分流钢液、夹杂上浮去除等重要功能。但是中间包作为钢液浇铸的中间环节,存在着如中间包开浇、更换长水口、更换钢包、浇铸末期等非稳态过程,对钢液质量稳定性有一定影响。
3.其中,在浇注末期由于钢包或中间包内钢液不足,非常容易发生旋流下渣现象,这些钢包或中间包渣进入下一个冶金容器后,可能没有及时上浮去除,从而造成钢液的二次氧化或卷渣现象,最终在铸坯内形成了夹渣等缺陷,严重影响了产品的质量稳定。
4.中国专利cn115090841a公开了一种研究覆盖剂在中间包运动行为的装置及使用方法,其中的装置结构中显然并未考虑如何对浇注末期下渣的吹氩进行有效控制,整个研究覆盖剂在中间包运动行为过程中并未吹氩,油脂模拟的也是中间包覆盖剂。
5.中国专利cn111992680a公开了一种中包吹氩保护浇注的装置及控制方法,其中的氩气通过连接管14进入中间包,显然并未考虑浇注末期下渣的吹氩控制,其中的吹氩保护的浇注过程和影响机理也与浇注末期下渣的过程和影响机理完全不同。
6.中国专利cn110394433a公开了一种有效去除中间包夹杂物的长水口吹氩精炼装置及方法,其中的氩气通入的装置结构由长水口、旋流室及旋流室出口组成,所述长水口内壁靠近顶部处预留环形槽,环形槽内置环状弥散型进气室,环状弥散型进气室通过长水口壁开设的进气孔与氩气输送系统相连,所述进气孔进气方向为水平方向,与长水口的轴向互相垂直;长水口下部与旋流室切向相连。显然氩气通入的装置结构复杂,去除夹杂物通过钢液流过旋流室和吹入的氩气泡协同去除,并未考虑浇注末期下渣的过程和影响机理。
技术实现要素:7.本发明所要解决的技术问题是如何克服现有技术浇注末期下渣的吹氩控制过程中存在的钢液的二次氧化或卷渣、铸坯内形成了夹渣等缺陷、产品成品率低、以及需要钢液和钢渣的真实成分进行实验研究的成本高、效率低的技术缺陷;而且通过钢液流过旋流室和吹入的氩气泡去除中间包夹杂物的方式复杂,还存在下渣过程中的渣料污染问题。
8.为解决上述技术问题,本发明提供如下技术方案:一种浇注末期下渣的吹氩控制装置,所述吹氩控制装置包括钢包模型、中间包模型、长水口模型和中间包出水口模型;所述钢包模型的底部通过所述长水口模型与所述中间包模型连通,所述中间包出水口模型设置在所述中间包模型的底部;其中:所述长水口模型按照实际生产中钢包和长水口、中间包的位置关系、连接关系与所述钢包模型和所述中间包模型进行装置结构设置;
所述中间包出水口模型按照实际生产中中间包和出水口的位置关系、连接关系与所述中间包模型进行装置结构设置;所述长水口模型上设置有第一流量调节阀、用于装油脂的漏斗和吹氩气孔,所述中间包出水口模型上设置有第二流量调节阀和流量计。
9.优选地,所述吹氩控制装置中的钢包模型、中间包模型、长水口模型和中间包出水口模型的材质为有机玻璃。
10.优选地,所述吹氩控制装置中的钢包模型、中间包模型内均设置有测量液位深度的刻度线。
11.优选地,所述吹氩气孔与吹氩气设备连接,吹氩气设备包括氩气储存装置、氩气抽吸装置、氩气流量调节阀和氩气流量计。
12.优选地,所述吹氩控制装置还包括以下模块:钢种信息获取模块,用于获取浇铸的目标钢种的钢液密度、钢包出口直径、钢包直径以及钢包内残钢量;通钢量获取模块,用于根据所述钢液密度、钢包出口直径、钢包直径以及钢包内残钢量,获得所述目标钢种浇铸末期的通钢量大小;氩气流量控制模块,用于根据所述通钢量大小,确定浇注末期最有利于控制下渣上浮去除的最佳水口吹氩流量。
13.优选地,所述钢种信息获取模块、通钢量获取模块和氩气流量控制模块以软件功能模块的形式实现并作为独立的产品销售或使用时,可以存储在一个计算机可读取存储介质中。
14.基于所述的浇注末期下渣的吹氩控制装置的使用方法,所述使用方法包括如下步骤:s1、实际测量钢包、中间包、长水口和中间包出水口的尺寸及各装置结构的位置关系和连接关系,然后按照前述尺寸等比例缩小制备对应的钢包模型、中间包模型、长水口模型和中间包出水口模型,并将制备的模型按照前述各装置结构的位置关系和连接关系进行装置结构设置;s2、向步骤s1中装置结构设置好的钢包模型内加入水,调节长水口模型和中间包出水口模型的流量,使中间包模型内的液位逐渐上升;s3、根据相似原理选择与中间包液态渣和固态渣的物理及流动特性近似的油脂来模拟钢包渣,选择适合的油脂成分和含量,配料和称量所需成分和含量的油脂,并将油脂装入长水口模型的漏斗中;s4、向步骤s2中装置结构设置好的长水口模型内通入氩气,模拟生产过程中的长水口吹氩;s5、在步骤s4之后继续加水,待中间包模型内的液位上升到指定工作液位深度高度后,调节进出口流量使得中间包模型内的液位稳定;s6、在步骤s5之后打开长水口模型盛放油脂的漏斗,模拟实际生产中下渣的过程,采用摄像机实时记录油脂通过中间包出口的数量。
15.s7、在不同的包括吹氩流量、通钢量的工艺参数下重复步骤s1到s6,得到不同吹氩条件下下渣的变化规律;
s8、分析检测得到油脂通过中间包出口的数量,通过拟合不同吹氩条件下下渣的吹氩量和油脂通过中间包出口的数量,从而得到实际生产中有利于下渣上浮去除的最优吹氩流量。
16.优选地,所述步骤s5中调节的进出口流量需根据实际生产的通钢量改变。
17.优选地,实际生产的通钢量根据钢液密度、钢包出口直径、钢包直径以及钢包内残钢量来确定,计算公式如下:其中,其中,q为通钢量,单位为kg/s;ρ为钢液密度,单位为kg/m3;d为钢包出口直径,单位为mm;d为钢包直径,单位为mm;w为钢包内残钢量,单位为kg。
18.优选地,所述使用方法中的全部或部分流程,也可以通过计算机程序来指令相关的硬件来完成,所述的计算机程序可存储于一计算机可读存储介质中,该计算机程序在被处理器执行时,可实现上述各个方法实施例的步骤。
19.优选地,所述使用方法中的计算机程序包括计算机程序代码,所述计算机程序代码可以为源代码形式、对象代码形式、可执行文件或某些中间形式等。所述计算机可读介质可以包括:能够携带所述计算机程序代码的任何实体或装置、记录介质、u盘、移动硬盘、磁碟、光盘、计算机存储器、只读存储器(rom,read-only memory)、随机存取存储器(ram,random access memory)、电载波信号、电信信号以及软件分发介质等。
20.需要说明的是,所述计算机可读介质包含的内容可以根据司法管辖区内立法和专利实践的要求进行适当的增减,例如在某些司法管辖区,根据立法和专利实践,计算机可读介质不包括电载波信号和电信信号。
21.优选地,所述步骤s3中的油脂为染色硅油,或染色煤油,或染色大豆油。
22.本发明与现有技术相比,具有以下有益效果:上述方案中,本发明的装置结构设置简单,是实际生产过程中的装置结构等比例缩小的模型,部分装置结构的材质为有机玻璃,便于肉眼直接观察模拟吹氩条件下下渣的吹氩流量和实际生产的通钢量之间的关系,得到实际生产中最优的吹氩流量。
23.本发明采用与中间包液态渣和固态渣的物理及流动特性近似的油脂来模拟钢包渣,浇注末期下渣过程模拟与实际相符,偏差不超过3%,经过实际生产验证,最优的吹氩流量数值精准率高,利于工业推广。
24.本发明实际生产的通钢量根据实际的钢液密度、钢包出口直径、钢包直径以及钢包内残钢量来确定,使得模拟结果更符合实际情况。
25.本发明采用分析检测得到油脂通过中间包出口的数量,通过拟合不同吹氩条件下下渣的吹氩量和油脂通过中间包出口的数量,从而得到实际生产中有利于下渣上浮去除的最优吹氩流量。
26.综上,本发明的装置结构简单,能够与实际生产过程中的装置结构很好的匹配,成本低,效率高,且能一次能够获得不同吹氩条件下下渣的变化规律,主要是通过油脂的属性来模拟,可得到不同工况条件下油脂通过中间包出口的数量,通过拟合获得最优吹氩流量;最后确定的吹氩流量能够促进下渣的上浮去除,减轻渣滴卷入钢液,提高了铸坯的洁净度和质量。
附图说明
27.为了更清楚地说明本发明实施例中的技术方案,下面将对实施例描述中所 需要使用的附图作简单地介绍,显而易见地,下面描述中的附图仅仅是本发明 的一些实施例,对于本领域普通技术人员来讲,在不付出创造性劳动的前提下, 还可以根据这些附图获得其他的附图。
28.图1为本发明中的一种浇注末期下渣的吹氩控制方法流程图;图2为本发明中的一种浇注末期下渣的吹氩控制装置的功能模块图;其中:m1为钢种信息获取模块;m2为通钢量获取模块;m3为氩气流量控制模块;图3为本发明中的一种浇注末期下渣的吹氩控制装置的结构示意图;其中:1为钢包模型;2为中间包模型;3为长水口模型;4中间包出水口模型;5为第一流量调节阀;6为第二流量调节阀;7为漏斗;8为流量计。
具体实施方式
29.下面将结合本发明实施例,对本发明实施例中的技术方案和解决的技术问题进行阐述。显然,所描述的实施例仅仅是本发明专利的一部分实施例,而不是全部实施例。
30.实施例1一种浇注末期下渣的吹氩控制装置,所述吹氩控制装置包括钢包模型1、中间包模型2、长水口模型3和中间包出水口模型4;所述钢包模型1的底部通过所述长水口模型3与所述中间包模型4连通,所述中间包出水口模型4设置在所述中间包模型2的底部;其中:所述长水口模型3按照实际生产中钢包和长水口、中间包的位置关系、连接关系与所述钢包模型1和所述中间包模型2进行装置结构设置;所述中间包出水口模型4按照实际生产中中间包和出水口的位置关系、连接关系与所述中间包模型2进行装置结构设置;所述长水口模型3上设置有第一流量调节阀5、用于装油脂的漏斗7和吹氩气孔,所述中间包出水口模型上设置有第二流量调节阀6和流量计8;所述吹氩控制装置中的钢包模型1、中间包模型2、长水口模型3和中间包出水口模型4的材质为有机玻璃;所述吹氩控制装置中的钢包模型1、中间包模型2内均设置有测量液位深度的刻度线;所述吹氩气孔与吹氩气设备连接,吹氩气设备包括氩气储存装置、氩气抽吸装置、氩气流量调节阀和氩气流量计;所述吹氩控制装置还包括以下模块:钢种信息获取模块m1,用于获取浇铸的目标钢种的钢液密度、钢包出口直径、钢包直径以及钢包内残钢量;通钢量获取模块m2,用于根据所述钢液密度、钢包出口直径、钢包直径以及钢包内残钢量,获得所述目标钢种浇铸末期的通钢量大小;氩气流量控制模块m3,用于根据所述通钢量大小,确定浇注末期最有利于控制下渣上浮去除的最佳水口吹氩流量。
31.本实施例所述的浇注末期下渣的吹氩控制装置的使用方法,所述使用方法包括如
下步骤:s1:实际测量钢包、中间包、长水口和中间包出水口的尺寸及各装置结构的位置关系和连接关系,然后按照三分之一前述尺寸等比例缩小制备对应的钢包模型1、中间包模型2、长水口模型3和中间包出水口模型4,并将制备的模型按照前述各装置结构的位置关系和连接关系进行装置结构设置;s2:向步骤s1中装置结构设置好的钢包模型1内加入水,调节长水口模型3流量最大,中间包出水口模型4关闭,使中间包模型2内的液位逐渐上升;s3:根据相似原理选择与钢包液态渣和固态渣的物理及流动特性近似的染色硅油来模拟钢包渣,将90 ml染色硅油装入长水口模型3的漏斗7中;s4:向步骤s3中装置结构设置好的长水口模型3内通入氩气,模拟生产过程中的长水口吹氩;s5:在步骤s4之后继续加水,待中间包模型内的液位上升到指定工作液位深度高度300 mm后,调节进出口流量为25.4 l/min使得中间包模型内的液位稳定;其中,所述步骤s5中调节的进出口流量需根据实际生产的通钢量改变;而实际生产的通钢量根据钢液密度、钢包出口直径、钢包直径以及钢包内残钢量来确定,计算公式如下:其中:钢液密度为7000kg/m3,长水口直径为81mm,钢包直径为2300mm,钢包内残钢量为2430kg,计算得到通钢量为46.2 kg/s;s6:在步骤s80之后打开长水口模型盛放油脂的漏斗7,模拟实际生产中下渣的过程,采用摄像机记录油脂通过中间包出口的数量;s7:在不同的吹氩流量、通钢量参数下重复步骤s1到s6,得到不同吹氩条件下下渣的变化规律;s8:分析前述检测得到油脂通过中间包出口数量,通过拟合吹氩量和中间包流出油脂的量,得到实际生产中有利于下渣上浮去除的最优吹氩流量为13.0-18.0 l/min。
32.上述方案中,本发明的装置结构设置简单,是实际生产过程中的装置结构等比例缩小的模型,部分装置结构的材质为有机玻璃,便于肉眼直接观察模拟吹氩条件下下渣的吹氩流量和实际生产的通钢量之间的关系,得到实际生产中最优的吹氩流量。
33.本发明采用与中间包液态渣和固态渣的物理及流动特性近似的油脂来模拟钢包渣,浇注末期下渣过程模拟与实际相符,偏差不超过3%,经过实际生产验证,最优的吹氩流量数值精准率高,利于工业推广。
34.本发明实际生产的通钢量根据实际的钢液密度、钢包出口直径、钢包直径以及钢包内残钢量来确定,使得模拟结果更符合实际情况。
35.本发明采用分析检测得到油脂通过中间包出口的数量,通过拟合不同吹氩条件下下渣的吹氩量和油脂通过中间包出口的数量,从而得到实际生产中有利于下渣上浮去除的最优吹氩流量。
36.综上,本发明的装置结构简单,能够与实际生产过程中的装置结构很好的匹配,成本低,效率高,且能一次能够获得不同吹氩条件下下渣的变化规律,主要是通过油脂的属性来模拟,可得到不同工况条件下油脂通过中间包出口的数量,通过拟合获得最优吹氩流量;
最后确定的吹氩流量能够促进下渣的上浮去除,减轻渣滴卷入钢液,提高了铸坯的洁净度和质量。
37.以上所述是本发明的优选实施方式,应当指出,对于本技术领域的普通技术人员来说,在不脱离本发明所述原理的前提下,还可以做出若干改进和润饰,这些改进和润饰也应视为本发明的保护范围。