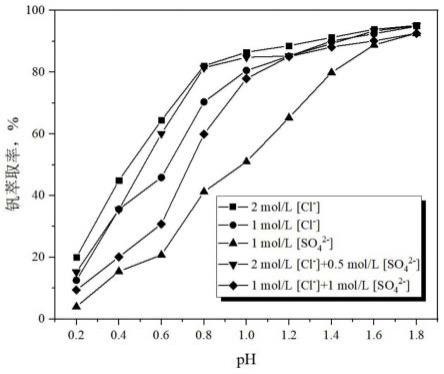
1.本发明属于钒页岩提取技术领域。具体涉及一种从钒页岩中提取有价元素的方法。
背景技术:2.钒页岩,又称石煤,是我国的一种重要的含钒资源。从钒页岩中提取五氧化二钒已经成为一种获取钒的重要途径。直接酸浸工艺和焙烧酸浸工艺是两种主要的提钒方法,这两种方法一般均采用硫酸作为浸出剂得到浸出液,再通过溶剂萃取和铵盐沉钒的方法得到五氧化二钒产品。
[0003]“一种从云母型含钒石煤中浸出钒的方法”(cn105420517a)专利技术,用硫酸作为浸出剂,并加入硫酸盐或硫酸氢盐类添加剂,在加压反应釜中浸出钒。该方法虽浸出时间较短和钒浸出率较高,但是采用该方法使钒页岩中的多种元素不能同时回收,且由于浸出过程中加入大量硫酸盐或硫酸氢盐类添加剂,得到的浸出尾渣产生量大、成分复杂且利用价值低。
[0004]“一种从石煤钒矿中选择性浸出分离钒和铁的方法”(cn110066920b)专利技术,采用一段稀硫酸和一段浓硫酸的两段浸出工艺选择性浸出铁和钒,虽从源头上阻止了石煤钒矿中的铁等杂质元素大量进入含钒溶液中,降低了含钒浸出液中杂质离子的浓度,但浸出过程中矿浆粘度大,尤其是第二段浸出过程中浸出效率低。
[0005]“一种石煤一步法制备高纯五氧化二钒的方法”(cn106282538a)专利技术,该方法采用焙烧-酸浸-萃取的方法制备高纯五氧化二钒产品,提取效率虽较高和产品质量较好。但是该需加入大量钙介质,要将ph值调节至1.7~2.0才能满足后续萃取的合适ph值,导致硫酸钙等微溶物易在管道沉淀。因此,该工艺存在低ph值下钒萃取效果差、管道易结垢的问题。
[0006]“一种含钒石煤选择性浸出钒的方法”(cn105624435a)专利技术,该技术采用草酸和氟化物的混合物作为浸出剂浸出石煤中的钒,虽实现了石煤浸出过程中钒和铁的选择性分离,降低了铁对后续钒萃取分离的影响。但是由于草酸是弱酸,加入量大,浸出效率低,且铁以草酸亚铁的形式进入尾渣,导致尾渣产生量大、成分复杂且利用价值低。
[0007]
综上所述,现有钒页岩提取过程中存在矿浆粘度大、浸出效率低、只能回收有价原始钒、低ph值下钒萃取效果差、管道易结垢、尾渣产生量大、尾渣成分复杂且利用价值低等问题。
技术实现要素:[0008]
本发明旨在克服现有技术缺陷,目的是提供一种从钒页岩中提取有价元素的方法,该方法不仅矿浆粘度小、浸出效率高、所需ph值低、能避免管道结垢和尾渣产生量少,且在回收钒的同时能回收钙、钒、锌、硅等有价元素。
[0009]
为实现上述目的,本发明采用的技术方案是:
[0010]
步骤1、一级盐酸浸出
[0011]
将钒页岩破碎,磨细,得到原矿粉料;再按固液比为1∶(1~2.5)kg/l,将所述原矿粉料与盐酸溶液混合,得到一级浸出浆;将所述一级浸出浆在10~40℃条件下搅拌10~60min,固液分离,得到一级浸出液和一级浸出渣。
[0012]
所述一级浸出液用于钙的回收。
[0013]
所述钒页岩的化学成分:v2o5含量为0.4~1.5wt%;cao含量为4~12wt%;sio2含量为60~85wt%;zno的含量为0.05~0.5wt%;云母类矿物含钒量占总钒量的30~95wt%。
[0014]
所述原矿粉料的粒度为小于0.074μm占30~60wt%。
[0015]
步骤2、二级混酸浸出
[0016]
按照固液比为1∶(1~2.5)kg/l,将所述一级浸出渣与二级浸出剂混合,得到二级浸出浆;再向所述二级浸出浆中加入助浸剂,调浆,得到二级浸出混浆;然后将所述二级浸出混浆在95~98℃和转速为10~50r/min的条件下搅拌6~12h,固液分离,得到二级浸出液和二级浸出渣。
[0017]
所述二级浸出剂为硫酸和盐酸的混合溶液,所述混合溶液中:cl-离子浓度为2~6mol/l,so
42-离子浓度为0.1~2mol/l。
[0018]
所述助浸剂为氟化钙或为氟化钠,所述助浸剂的加入量为原矿粉料的2~6wt%。
[0019]
步骤3、浸出液调整
[0020]
向所述二级浸出液中加入氢氧化钠或氢氧化钙,调节ph值至0.8~1.5,得到调节后的二级浸出液;再按照液固比为1∶(1.5~2)l/g,向所述调节后的二级浸出液中加入亚硫酸钠;然后在60~80℃和转速为2~10r/min的条件下搅拌10~30min,过滤,得到萃原液和ph调节渣。
[0021]
步骤4、溶剂萃取钒
[0022]
按照有机相a∶所述萃原液的体积比为1∶(2~3),将所述有机相a与所述萃原液混合,在10~30℃条件下进行逆流正萃,分相,得到萃钒余液和负载钒有机相;将所述负载钒有机相与硫酸溶液按照体积比为(4~10)∶1,将所述负载钒有机相与所述硫酸溶液混合,在10~30℃条件下进行逆流反萃,分相,得到富钒液和贫有机相1。
[0023]
将所述富钒液进行铵盐沉钒,脱氨,制得五氧化二钒。
[0024]
贫有机相1经再生后于步骤4中作为有机相a循环使用。
[0025]
所述有机相a为10~25vol%的钒萃取剂、3~7vol%的相调节剂和68~87vol%的磺化煤油的混合物。
[0026]
步骤5、溶剂萃取锌
[0027]
按照有机相b∶所述萃钒余液的体积比1∶(2~3),将所述有机相b与所述萃钒余液混合,在10~30℃条件下进行逆流正萃,分相,得到萃锌余液和负载锌有机相;再按照将所述负载锌有机相∶氢氧化钠溶液的体积比为(4~10)∶1,将所述负载锌有机相与所述氢氧化钠溶液混合,在10~30℃条件下进行逆流反萃,分相,得到富锌液和贫有机相2。
[0028]
所述富锌液通过电解法,制得金属锌。
[0029]
所述贫有机相2经再生后于步骤5中作为有机相b循环使用。
[0030]
所述有机相b为10~30vol%的胺类萃取剂、3~7vol%的相调节剂和63~87vol%的磺化煤油的混合物。
[0031]
步骤6、二级浸出渣脱碳
[0032]
将所述二级浸出渣在650~800℃条件下焙烧0.5~2h,得到富硅渣。
[0033]
本技术方案中:
[0034]
所述盐酸溶液的浓度为1.5~3mol/l;
[0035]
所述钒萃取剂为二(2-乙基己基)膦酸酯、2-乙基己基膦酸单2-乙基己基酯中的一种以上;
[0036]
所述胺类萃取剂为仲胺、叔胺和季胺中的一种;
[0037]
所述相调节剂为仲辛醇或为磷酸三丁酯;
[0038]
所述硫酸溶液的浓度为1~2mol/l;
[0039]
所述氢氧化钠溶液的浓度为1.5~2.5mol/l。
[0040]
由于采用上述技术方案,本发明与现有技术相比具有如下有益效果:
[0041]
(1)矿浆粘度小、浸出效率高
[0042]
在现有的硫酸浸出技术的浸出过程中发生的主要反应是:
[0043]
caco3+h2so4=caso4↓
+h2o+co2↑
(1)
[0044]
即原矿中的含钙物相在硫酸的作用下,先发生溶解反应,生成钙离子;再与硫酸反应,生成硫酸钙微溶物。所述硫酸钙微溶物粒度小、粘度大,导致浸出矿浆的粘度非常大,降低了浸出效率。
[0045]
本发明第一段采用浓度为1.5~3mol/l盐酸浸出,发生的主要反应如式(2)和(3)所示:
[0046]
hcl=h
+
+cl-ꢀꢀꢀ
(2)
[0047]
caco3+2h
+
=ca
2+
+h2o+co2↑ꢀꢀꢀ
(3)
[0048]
在本发明的一级盐酸浸出过程中,原矿中钙的浸出率为85~98%,钙浸出后主要以离子形态存在,一级盐酸浸出得到的一级浸出渣中cao含量仅为0.08~1.8wt%。
[0049]
另外,二级混酸浸出中的浸出剂含有2~6mol/l的盐酸,大量氯离子的存在能显著提高硫酸钙的溶解度,有效避免了微溶物硫酸钙的生成。
[0050]
因此,本发明在浸出过程中微溶物硫酸钙难以生成,相较于现有技术的矿浆粘度小,浸出效率高。经测定:本发明的浸出矿浆粘度仅为1.1~1.5mpa
·
s。
[0051]
(2)能有效回收钙、钒、锌、硅等多种有价元素
[0052]
①
钙的回收
[0053]
本发明的一级盐酸浸出为常温稀盐酸浸出,在一级盐酸浸出过程中,原矿主要发生方解石、黄铁矿等耗酸矿物的溶解过程,而云母等矿物不溶解,如式(4)、(5)和(6)所示:
[0054]
hcl=h
+
+cl-ꢀꢀꢀ
(4)
[0055]
caco3+2h
+
=ca
2+
+h2o+co2↑ꢀꢀꢀ
(5)
[0056]
2fes2+o2+4h
+
=2fe
2+
+2h2o+4s
↓ꢀꢀꢀ
(6)
[0057]
虽然黄铁矿也会溶解,但由于原矿中铁含量小于钙,且铁浸出率小于钙浸出率。因此,一级浸出液为含有铁杂质的氯化钙溶液,该溶液可进一步处理回收钙元素。经测定:钙的总回收率可以达到88%以上。
[0058]
②
钒和锌的回收
[0059]
本发明的二级混酸浸出过程中发生的主要反应如式(7)~(11)所示:
[0060]
kal2(alsi3o
10
)(oh)2+10h
+
=k
+
+3al
3+
+3h4sio4ꢀꢀꢀ
(7)
[0061]
zns+2h
+
=zn
2+
+2h2s
↑ꢀꢀꢀ
(8)
[0062]
naf=na
+
+f-ꢀꢀꢀ
(9)
[0063]
f-+h
+
=hf
ꢀꢀꢀ
(10)
[0064]
kal2(alsi3o
10
)(oh)2+12hf+10h
+
=k
+
+3al
3+
+3sif4+12h2o
ꢀꢀꢀ
(11)
[0065]
由式(7)~(11)可知,本发明在二级混酸浸出过程中实现了钒和锌的共同溶出,但在二级浸出液中,钒离子主要以vocl+形式存在,而萃钒余液中的锌离子主要以zncl
3-形式存在。由于两种离子不同的电性,分别采用可萃取阳离子的膦酸类萃取剂和可萃取阴离子的胺类萃取剂,实现了钒和锌的分步萃取和回收。
[0066]
经测定:钒的浸出率大于85%;锌的浸出率大于65%;钒的萃取率大于98.5%;锌的萃取率大于98.5%;钒的反萃率大于99.8%;锌的反萃率大于99.8%。
[0067]
③
硅的回收
[0068]
原矿粉料中的石英等含硅矿物不参加一级浸出和二级浸出,而原矿粉料中的其他大部分矿物已在浸出过程中溶解。因此,二级浸出渣经脱碳后,能得到纯度大于95%的富硅渣,实现了原矿中硅的回收。经测定,硅的总回收率达到99.5%以上。
[0069]
(3)萃取所需ph值低于现有技术
[0070]
不同溶液体系中钒萃取率与ph值有密切的关系。在低ph值下,钒在本发明的氯离子体系中的萃取率显著高于钒在其他体系中的萃取率。
[0071]
本发明在二级混酸浸出过程采用的浸出剂为硫酸和盐酸的混合物,得到的二级浸出液中氯离子浓度为0.5~5mol/l,非常有利于钒在低ph值下的萃取分离。
[0072]
(4)能有效避免管道结垢
[0073]
由于本发明采用分段浸出,大部分钙质已在一级浸出过程中溶解,使得二段浸出液中的钙含量低,钙离子在溶液中难以沉淀。另由于二级浸出液为硫酸和盐酸的混合介质,钙离子在二级浸出液中的溶解度大于其在纯硫酸介质中的溶解度。故能有效避免管道结垢。
[0074]
(5)尾渣产生量少且利用价值高
[0075]
页岩提取过程中主要产生两种尾渣。一种是浸出渣,另一种是ph调节渣。
[0076]
关于浸出渣:现有技术的浸出渣中含有大量的硫酸钙等杂质,sio2的纯度仅为75.2%,故常用于制备低端建材;而本发明的浸出渣经处理后得到的富硅渣的sio2纯度95.5%以上。同时,经计算,每吨v2o5产生的浸出渣量降低了28.9%。
[0077]
关于ph调节渣:现有技术浸出液的ph值需要调节至1.8~2.2;而本发明的ph值的调节范围仅为0.8~1.5,ph值的调节范围缩小,ph调节渣的产生量降低。故本发明的ph调节渣产生量少且利用价值高。
[0078]
因此,本发明不仅具有矿浆粘度小、浸出效率高、可回收钙、钒、锌、硅等元素、萃取所需ph值低、可避免管道结垢、尾渣产生量少且利用价值高的特点。
附图说明
[0079]
图1为本发明及与本发明相关的现有技术的钒萃取率与ph值的关系对比图。
具体实施方式
[0080]
下面结合附图和具体实施方式对本发明技术方案做进一步的描述,并非对其保护范围的限制。
[0081]
一种从钒页岩中提取有价元素的方法。本具体实施方式所述方法的步骤是:
[0082]
步骤1、一级盐酸浸出
[0083]
将钒页岩破碎,磨细,得到原矿粉料;再按固液比为1∶(1~2.5)kg/l,将所述原矿粉料与盐酸溶液混合,得到一级浸出浆;将所述一级浸出浆在10~40℃条件下搅拌10~60min,固液分离,得到一级浸出液和一级浸出渣。
[0084]
所述一级浸出液用于钙的回收。
[0085]
所述钒页岩的化学成分:v2o5含量为0.4~1.5wt%,cao含量为4~12wt%,sio2含量为60~85wt%,zno的含量为0.05~0.5wt%,云母类矿物含钒量占总钒量的30~95wt%。
[0086]
所述原矿粉料的粒度为小于0.074μm占30~60wt%。
[0087]
步骤2、二级混酸浸出
[0088]
按照固液比为1∶(1~2.5)kg/l,将所述一级浸出渣与二级浸出剂混合,得到二级浸出浆;再向所述二级浸出浆中加入助浸剂,调浆,得到二级浸出混浆;然后将所述二级浸出混浆在95~98℃和转速为10~50r/min的条件下搅拌6~12h,固液分离,得到二级浸出液和二级浸出渣。
[0089]
所述二级浸出剂为硫酸和盐酸的混合溶液,所述混合溶液中:cl-离子浓度为2~6mol/l,so
42-离子浓度为0.1~2mol/l。
[0090]
所述助浸剂为氟化钙或为氟化钠,所述助浸剂的加入量为原矿粉料的2~6wt%。
[0091]
步骤3、浸出液调整
[0092]
向所述二级浸出液中加入氢氧化钠或氢氧化钙,调节ph值至0.8~1.5,得到调节后的二级浸出液;再按照液固比为1∶(1.5~2)l/g,向所述调节后的二级浸出液中加入亚硫酸钠;然后在60~80℃和转速为2~10r/min的条件下搅拌10~30min,过滤,得到萃原液和ph调节渣。
[0093]
步骤4、溶剂萃取钒
[0094]
按照有机相a∶所述萃原液的体积比为1∶(2~3),将所述有机相a与所述萃原液混合,在10~30℃条件下进行逆流正萃,分相,得到萃钒余液和负载钒有机相;将所述负载钒有机相与硫酸溶液按照体积比为(4~10)∶1,将所述负载钒有机相与所述硫酸溶液混合,在10~30℃条件下进行逆流反萃,分相,得到富钒液和贫有机相1。
[0095]
将所述富钒液进行铵盐沉钒,脱氨,制得五氧化二钒。
[0096]
贫有机相1经再生后于步骤4中作为有机相a循环使用。
[0097]
所述有机相a为10~25vol%的钒萃取剂、3~7vol%的相调节剂和68~87vol%的磺化煤油的混合物。
[0098]
步骤5、溶剂萃取锌
[0099]
按照有机相b∶所述萃钒余液的体积比1∶(2~3),将所述有机相b与所述萃钒余液混合,在10~30℃条件下进行逆流正萃,分相,得到萃锌余液和负载锌有机相;再按照将所述负载锌有机相∶氢氧化钠溶液的体积比为(4~10)∶1,将所述负载锌有机相与所述氢氧化钠溶液混合,在10~30℃条件下进行逆流反萃,分相,得到富锌液和贫有机相2。
[0100]
所述富锌液通过电解法,制得金属锌。
[0101]
所述贫有机相2经再生后于步骤5中作为有机相b循环使用。
[0102]
所述有机相b为10~30vol%的胺类萃取剂、3~7vol%的相调节剂和63~87vol%的磺化煤油的混合物。
[0103]
步骤6、二级浸出渣脱碳
[0104]
将所述二级浸出渣在650~800℃条件下焙烧0.5~2h,得到富硅渣。
[0105]
本具体实施方式中:
[0106]
所述盐酸溶液的浓度为1.5~3mol/l;
[0107]
所述钒萃取剂为二(2-乙基己基)膦酸酯、2-乙基己基膦酸单2-乙基己基酯中的一种以上;
[0108]
所述胺类萃取剂为仲胺、叔胺和季胺中的一种;
[0109]
所述相调节剂为仲辛醇或为磷酸三丁酯;
[0110]
所述硫酸溶液的浓度为1~2mol/l;
[0111]
所述氢氧化钠溶液的浓度为1.5~2.5mol/l。
[0112]
实施例1
[0113]
一种从钒页岩中提取有价元素的方法。本实施例所述方法的具体步骤是:
[0114]
步骤1、一级盐酸浸出
[0115]
将钒页岩破碎,磨细,得到原矿粉料;再按固液比为1∶1kg/l,将所述原矿粉料与盐酸溶液混合,得到一级浸出浆;将所述一级浸出浆在10℃条件下搅拌10min,固液分离,得到一级浸出液和一级浸出渣。
[0116]
所述一级浸出液用于钙的回收。
[0117]
所述钒页岩的化学成分:v2o5含量为0.41wt%,cao含量为4.2wt%,sio2含量为60.9wt%,zno的含量为0.06wt%,云母类矿物含钒量占总钒量的31wt%。
[0118]
所述原矿粉料的粒度为小于0.074μm占30wt%。
[0119]
步骤2、二级混酸浸出
[0120]
按照固液比为1∶1kg/l,将所述一级浸出渣与二级浸出剂混合,得到二级浸出浆;再向所述二级浸出浆中加入助浸剂,调浆,得到二级浸出混浆;然后将所述二级浸出混浆在95℃和转速为10r/min的条件下搅拌6h,固液分离,得到二级浸出液和二级浸出渣。
[0121]
所述二级浸出剂为硫酸和盐酸的混合溶液,所述混合溶液中:cl-离子浓度为2mol/l,so
42-离子浓度为0.1mol/l。
[0122]
所述助浸剂为氟化钙,所述助浸剂的加入量为原矿粉料的2wt%。
[0123]
步骤3、浸出液调整
[0124]
向所述二级浸出液中加入氢氧化钠,调节ph值至1.5,得到调节后的二级浸出液;再按照液固比为1∶1.5l/g,向所述调节后的二级浸出液中加入亚硫酸钠;然后在60℃和转速为2r/min的条件下搅拌10min,过滤,得到萃原液和ph调节渣。
[0125]
步骤4、溶剂萃取钒
[0126]
按照有机相a∶所述萃原液的体积比为1∶2,将所述有机相a与所述萃原液混合,在10℃条件下进行逆流正萃,分相,得到萃钒余液和负载钒有机相;将所述负载钒有机相与硫酸溶液按照体积比为4∶1,将所述负载钒有机相与所述硫酸溶液混合,在10℃条件下进行逆
流反萃,分相,得到富钒液和贫有机相1。
[0127]
将所述富钒液进行铵盐沉钒,脱氨,制得五氧化二钒;
[0128]
贫有机相1经再生后于步骤4中作为有机相a循环使用。
[0129]
所述有机相a为10vol%的钒萃取剂、3vol%的相调节剂和87vol%的磺化煤油的混合物。
[0130]
步骤5、溶剂萃取锌
[0131]
按照有机相b∶所述萃钒余液的体积比1∶2,将所述有机相b与所述萃钒余液混合,在10℃条件下进行逆流正萃,分相,得到萃锌余液和负载锌有机相;再按照将所述负载锌有机相∶氢氧化钠溶液的体积比为4∶1,将所述负载锌有机相与所述氢氧化钠溶液混合,在10℃条件下进行逆流反萃,分相,得到富锌液和贫有机相2。
[0132]
所述富锌液通过电解法,制得金属锌。
[0133]
所述贫有机相2经再生后于步骤5中作为有机相b循环使用。
[0134]
所述有机相b为10vol%的胺类萃取剂、3vol%的相调节剂和87vol%的磺化煤油的混合物。
[0135]
步骤6、二级浸出渣脱碳
[0136]
将所述二级浸出渣在650℃条件下焙烧0.5h,得到富硅渣。
[0137]
本实施例中:
[0138]
所述盐酸溶液的浓度为1.5mol/l;
[0139]
所述钒萃取剂为二(2-乙基己基)膦酸酯;
[0140]
所述胺类萃取剂为仲胺;
[0141]
所述相调节剂为仲辛醇;
[0142]
所述硫酸溶液的浓度为1mol/l;
[0143]
所述氢氧化钠溶液的浓度为1.5mol/l。
[0144]
本实施例经检测:
[0145]
一级浸出过程中,原矿中钙的浸出率为85.2%;
[0146]
一级浸出渣中cao含量为0.09%;
[0147]
浸出矿浆粘度为1.13mpa
·
s;
[0148]
钙的总回收率为89.2%;
[0149]
钒的浸出率为85.2%;锌的浸出率为65.2%;钒的萃取率为98.6%;锌的萃取率为98.6%;钒的反萃率为99.81%;锌的反萃率为99.82%。
[0150]
硅的总回收率为99.6%;
[0151]
浸出渣的sio2纯度为95.6%;
[0152]
每吨v2o5产生的浸出渣量降低了29.0%。
[0153]
实施例2
[0154]
一种从钒页岩中提取有价元素的方法。本实施例所述方法的具体步骤是:
[0155]
步骤1、一级盐酸浸出
[0156]
将钒页岩破碎,磨细,得到原矿粉料;再按固液比为1∶2.5kg/l,将所述原矿粉料与盐酸溶液混合,得到一级浸出浆;将所述一级浸出浆在40℃条件下搅拌60min,固液分离,得到一级浸出液和一级浸出渣。
[0157]
所述一级浸出液用于钙的回收。
[0158]
所述钒页岩的化学成分:v2o5含量为1.48wt%,cao含量为11.9wt%,sio2含量为84.8wt%,zno的含量为0.49wt%,云母类矿物含钒量占总钒量的94wt%。
[0159]
所述原矿粉料的粒度为小于0.074μm占60wt%。
[0160]
步骤2、二级混酸浸出
[0161]
按照固液比为1∶2.5kg/l,将所述一级浸出渣与二级浸出剂混合,得到二级浸出浆;再向所述二级浸出浆中加入助浸剂,调浆,得到二级浸出混浆;然后将所述二级浸出混浆在98℃和转速为50r/min的条件下搅拌12h,固液分离,得到二级浸出液和二级浸出渣。
[0162]
所述二级浸出剂为硫酸和盐酸的混合溶液,所述混合溶液中:cl-离子浓度为6mol/l,so
42-离子浓度为2mol/l。
[0163]
所述助浸剂为氟化钠,所述助浸剂的加入量为原矿粉料的6wt%。
[0164]
步骤3、浸出液调整
[0165]
向所述二级浸出液中加入氢氧化钙,调节ph值至0.8,得到调节后的二级浸出液;再按照液固比为1∶2l/g,向所述调节后的二级浸出液中加入亚硫酸钠;然后在80℃和转速为10r/min的条件下搅拌30min,过滤,得到萃原液和ph调节渣。
[0166]
步骤4、溶剂萃取钒
[0167]
按照有机相a∶所述萃原液的体积比为1∶3,将所述有机相a与所述萃原液混合,在30℃条件下进行逆流正萃,分相,得到萃钒余液和负载钒有机相;将所述负载钒有机相与硫酸溶液按照体积比为10∶1,将所述负载钒有机相与所述硫酸溶液混合,在30℃条件下进行逆流反萃,分相,得到富钒液和贫有机相1。
[0168]
将所述富钒液进行铵盐沉钒,脱氨,制得五氧化二钒。
[0169]
贫有机相1经再生后于步骤4中作为有机相a循环使用。
[0170]
所述有机相a为25vol%的钒萃取剂、7vol%的相调节剂和68vol%的磺化煤油的混合物。
[0171]
步骤5、溶剂萃取锌
[0172]
按照有机相b∶所述萃钒余液的体积比1∶3,将所述有机相b与所述萃钒余液混合,在30℃条件下进行逆流正萃,分相,得到萃锌余液和负载锌有机相;再按照将所述负载锌有机相∶氢氧化钠溶液的体积比为10∶1,将所述负载锌有机相与所述氢氧化钠溶液混合,在30℃条件下进行逆流反萃,分相,得到富锌液和贫有机相2。
[0173]
所述富锌液通过电解法,制得金属锌。
[0174]
所述贫有机相2经再生后于步骤5中作为有机相b循环使用。
[0175]
所述有机相b为30vol%的胺类萃取剂、7vol%的相调节剂和63vol%的磺化煤油的混合物。
[0176]
步骤6、二级浸出渣脱碳
[0177]
将所述二级浸出渣在800℃条件下焙烧2h,得到富硅渣。
[0178]
本实施例中:
[0179]
所述盐酸溶液的浓度为3mol/l;
[0180]
所述钒萃取剂为2-乙基己基膦酸单2-乙基己基酯;
[0181]
所述胺类萃取剂为叔胺;
[0182]
所述相调节剂为磷酸三丁酯;
[0183]
所述硫酸溶液的浓度为2mol/l;
[0184]
所述氢氧化钠溶液的浓度为2.5mol/l;
[0185]
本实施例经检测:
[0186]
一级浸出过程中,原矿中钙的浸出率为97.6%;
[0187]
一级浸出渣中cao含量为1.78%;
[0188]
浸出矿浆粘度为1.32mpa
·
s;
[0189]
钙的总回收率为97.5%;
[0190]
钒的浸出率为94.1%;锌的浸出率为85.1%;钒的萃取率为99.5%;锌的萃取率为99.8%;钒的反萃率为99.95%;锌的反萃率为99.96%。
[0191]
硅的总回收率为99.9%;浸出渣的sio2纯度为97.2%;
[0192]
每吨v2o5产生的浸出渣量降低了32.1%。
[0193]
实施例3
[0194]
一种从钒页岩中提取有价元素的方法。本实施例所述方法的具体步骤是:
[0195]
步骤1、一级盐酸浸出
[0196]
将钒页岩破碎,磨细,得到原矿粉料;再按固液比为1∶1.8kg/l,将所述原矿粉料与盐酸溶液混合,得到一级浸出浆;将所述一级浸出浆在25℃条件下搅拌35min,固液分离,得到一级浸出液和一级浸出渣。
[0197]
所述一级浸出液用于钙的回收。
[0198]
所述钒页岩的化学成分:v2o5含量为0.79wt%,cao含量为8.6wt%,sio2含量为78.2wt%,zno的含量为0.27wt%,云母类矿物含钒量占总钒量的75wt%。
[0199]
所述原矿粉料的粒度为小于0.074μm占45wt%。
[0200]
步骤2、二级混酸浸出
[0201]
按照固液比为1∶1.8kg/l,将所述一级浸出渣与二级浸出剂混合,得到二级浸出浆;再向所述二级浸出浆中加入助浸剂,调浆,得到二级浸出混浆;然后将所述二级浸出混浆在97℃和转速为30r/min的条件下搅拌9h,固液分离,得到二级浸出液和二级浸出渣。
[0202]
所述二级浸出剂为硫酸和盐酸的混合溶液,所述混合溶液中:cl-离子浓度为4mol/l,so
42-离子浓度为1.05mol/l。
[0203]
所述助浸剂为氟化钠,所述助浸剂的加入量为原矿粉料的4wt%。
[0204]
步骤3、浸出液调整
[0205]
向所述二级浸出液中加入氢氧化钙,调节ph值至1.1,得到调节后的二级浸出液;再按照液固比为1∶1.7l/g,向所述调节后的二级浸出液中加入亚硫酸钠;然后在70℃和转速为6r/min的条件下搅拌20min,过滤,得到萃原液和ph调节渣。
[0206]
步骤4、溶剂萃取钒
[0207]
按照有机相a∶所述萃原液的体积比为1∶2.5,将所述有机相a与所述萃原液混合,在20℃条件下进行逆流正萃,分相,得到萃钒余液和负载钒有机相;将所述负载钒有机相与硫酸溶液按照体积比为7∶1,将所述负载钒有机相与所述硫酸溶液混合,在20℃条件下进行逆流反萃,分相,得到富钒液和贫有机相1。
[0208]
将所述富钒液进行铵盐沉钒,脱氨,制得五氧化二钒。
[0209]
贫有机相1经再生后于步骤4中作为有机相a循环使用。
[0210]
所述有机相a为15vol%的钒萃取剂、5vol%的相调节剂和80vol%的磺化煤油的混合物。
[0211]
步骤5、溶剂萃取锌
[0212]
按照有机相b∶所述萃钒余液的体积比1∶2.5,将所述有机相b与所述萃钒余液混合,在20℃条件下进行逆流正萃,分相,得到萃锌余液和负载锌有机相;再按照将所述负载锌有机相∶氢氧化钠溶液的体积比为7∶1,将所述负载锌有机相与所述氢氧化钠溶液混合,在20℃条件下进行逆流反萃,分相,得到富锌液和贫有机相2。
[0213]
所述富锌液通过电解法,制得金属锌。
[0214]
所述贫有机相2经再生后于步骤5中作为有机相b循环使用。
[0215]
所述有机相b为20vol%的胺类萃取剂、5vol%的相调节剂和75vol%的磺化煤油的混合物。
[0216]
步骤6、二级浸出渣脱碳
[0217]
将所述二级浸出渣在750℃条件下焙烧1.7h,得到富硅渣。
[0218]
本实施例中:
[0219]
所述盐酸溶液的浓度为2mol/l;
[0220]
所述钒萃取剂为二(2-乙基己基)膦酸酯和2-乙基己基膦酸单2-乙基己基酯的混合物;
[0221]
所述胺类萃取剂为季胺;
[0222]
所述相调节剂为磷酸三丁酯;
[0223]
所述硫酸溶液的浓度为1.5mol/l;
[0224]
所述氢氧化钠溶液的浓度为2mol/l。
[0225]
本实施例经检测:
[0226]
一级浸出过程中,原矿中钙的浸出率为92.1%;
[0227]
一级浸出渣中cao含量为1.15%;
[0228]
浸出矿浆粘度为1.48mpa
·
s;
[0229]
钙的总回收率为90.1%;
[0230]
钒的浸出率为91.6%;锌的浸出率为78.6%;钒的萃取率为98.9%;锌的萃取率为99.2%;钒的反萃率为99.9%;锌的反萃率为99.91%。
[0231]
硅的总回收率为99.7%;
[0232]
浸出渣的sio2纯度为98.6%;
[0233]
每吨v2o5产生的浸出渣量降低了31.6%。
[0234]
本具体实施方式与现有技术相比具有如下有益效果:
[0235]
(1)矿浆粘度小、浸出效率高
[0236]
在现有的硫酸浸出技术的浸出过程中发生的主要反应是:
[0237]
caco3+h2so4=caso4↓
+h2o+co2↑ꢀꢀꢀ
(1)
[0238]
即原矿中的含钙物相在硫酸的作用下,先发生溶解反应,生成钙离子;再与硫酸反应,生成硫酸钙微溶物。所述硫酸钙微溶物粒度小、粘度大,导致浸出矿浆的粘度非常大,降低了浸出效率。
[0239]
本具体实施方式第一段采用浓度为1.5~3mol/l盐酸浸出,发生的主要反应如式(2)和(3)所示:
[0240]
hcl=h
+
+cl-ꢀꢀꢀ
(2)
[0241]
caco3+2h
+
=ca
2+
+h2o+co2↑ꢀꢀꢀ
(3)
[0242]
在本具体实施方式的一级盐酸浸出过程中,原矿中钙的浸出率为85~98%,钙浸出后主要以离子形态存在,一级盐酸浸出得到的一级浸出渣中cao含量仅为0.08~1.8wt%。
[0243]
另外,二级混酸浸出中的浸出剂含有2~6mol/l的盐酸,大量氯离子的存在能显著提高硫酸钙的溶解度,有效避免了微溶物硫酸钙的生成。
[0244]
因此,本具体实施方式在浸出过程中微溶物硫酸钙难以生成,相较于现有技术的矿浆粘度小,浸出效率高。经测定:本具体实施方式的浸出矿浆粘度仅为1.1~1.5mpa
·
s。
[0245]
(2)能有效回收钙、钒、锌、硅等多种有价元素
[0246]
①
钙的回收
[0247]
本具体实施方式的一级盐酸浸出为常温稀盐酸浸出,在一级盐酸浸出过程中,原矿主要发生方解石、黄铁矿等耗酸矿物的溶解过程,而云母等矿物不溶解,如式(4)、(5)和(6)所示:
[0248]
hcl=h
+
+cl-ꢀꢀꢀ
(4)
[0249]
caco3+2h
+
=ca
2+
+h2o+co2↑ꢀꢀꢀ
(5)
[0250]
2fes2+o2+4h
+
=2fe
2+
+2h2o+4s
↓ꢀꢀꢀ
(6)
[0251]
虽然黄铁矿也会溶解,但由于原矿中铁含量小于钙,且铁浸出率小于钙浸出率。因此,一级浸出液为含有铁杂质的氯化钙溶液,该溶液可进一步处理回收钙元素。经测定:钙的总回收率可以达到88%以上。
[0252]
②
钒和锌的回收
[0253]
本具体实施方式的二级混酸浸出过程中发生的主要反应如式(7)~(11)所示:
[0254]
kal2(alsi3o
10
)(oh)2+10h
+
=k
+
+3al
3+
+3h4sio4ꢀꢀꢀ
(7)
[0255]
zns+2h
+
=zn
2+
+2h2s
↑ꢀꢀꢀ
(8)
[0256]
naf=na
+
+f-ꢀꢀꢀ
(9)
[0257]
f-+h
+
=hf
ꢀꢀꢀ
(10)
[0258]
kal2(alsi3o
10
)(oh)2+12hf+10h
+
=k
+
+3al
3+
+3sif4+12h2o
ꢀꢀꢀ
(
11
)
[0259]
由式(7)~(11)可知,本具体实施方式在二级混酸浸出过程中实现了钒和锌的共同溶出,但在二级浸出液中,钒离子主要以vocl+形式存在,而萃钒余液中的锌离子主要以zncl
3-形式存在。由于两种离子不同的电性,分别采用可萃取阳离子的膦酸类萃取剂和可萃取阴离子的胺类萃取剂,实现了钒和锌的分步萃取和回收。
[0260]
经测定:钒的浸出率大于85%;锌的浸出率大于65%;钒的萃取率大于98.5%;锌的萃取率大于98.5%;钒的反萃率大于99.8%;锌的反萃率大于99.8%。
[0261]
③
硅的回收
[0262]
原矿粉料中的石英等含硅矿物不参加一级浸出和二级浸出,而原矿粉料中的其他大部分矿物已在浸出过程中溶解。因此,二级浸出渣经脱碳后,能得到纯度大于95%的富硅渣,实现了原矿中硅的回收。经测定,硅的总回收率达到99.5%以上。
[0263]
(3)萃取所需ph值低于现有技术
[0264]
不同溶液体系中钒萃取率与ph值的关系如图1所示。图1为本具体实施方式及与本具体实施方式相关的现有技术的钒萃取率与ph值的关系对比图。由图1可知,在低ph值下,钒在本具体实施方式的氯离子体系中的萃取率显著高于钒在与本具体实施方式相关的现有技术的体系中的萃取率。
[0265]
本具体实施方式在二级混酸浸出过程采用的浸出剂为硫酸和盐酸的混合物,得到的二级浸出液中氯离子浓度为0.5~5mol/l,非常有利于钒在低ph值下的萃取分离。
[0266]
(4)能有效避免管道结垢
[0267]
由于本具体实施方式采用分段浸出,大部分钙质已在一级浸出过程中溶解,使得二段浸出液中的钙含量低,钙离子在溶液中难以沉淀。另由于二级浸出液为硫酸和盐酸的混合介质,钙离子在二级浸出液中的溶解度大于其在纯硫酸介质中的溶解度。故能有效避免管道结垢。
[0268]
(5)尾渣产生量少且利用价值高
[0269]
页岩提取过程中主要产生两种尾渣。一种是浸出渣,另一种是ph调节渣。
[0270]
关于浸出渣:现有技术的浸出渣中含有大量的硫酸钙等杂质,sio2的纯度仅为75.2%,故常用于制备低端建材;而本具体实施方式的浸出渣经处理后得到的富硅渣的sio2纯度95.5%以上。同时,经计算,每吨v2o5产生的浸出渣量降低了28.9%;
[0271]
关于ph调节渣:现有技术浸出液的ph值需要调节至1.8~2.2;而本具体实施方式的ph值的调节范围仅为0.8~1.5,ph值的调节范围缩小,ph调节渣的产生量降低。故本具体实施方式的ph调节渣产生量少且利用价值高。
[0272]
因此,本具体实施方式不仅具有矿浆粘度小、浸出效率高、可回收钙、钒、锌、硅等元素、萃取所需ph值低、可避免管道结垢、尾渣产生量少且利用价值高的特点。