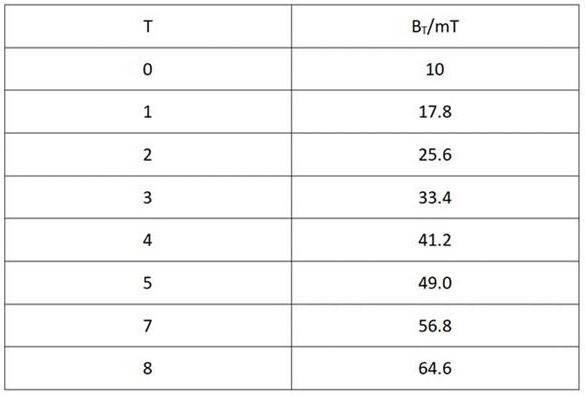
1.本发明属于金属清洗技术领域,具体涉及一种防锈金属清洗剂及其制备方法和使用方法。
背景技术:2.在机械及汽车等行业,经常需要用到柴油、煤油等清洗液来清洗金属零部件,因而在金属零部件的表面为经常残留油污,同时金属零部件的表面会随着使用时间的增加而逐渐生锈,最终影响机械零部件的运转性能,因为经常需要使用金属清洗剂对金属零部件的表面进行清洗,而现有的大多数金属清洗剂在清理金属零部件表面油污的同时无法做到同时对生锈的表面进行除锈,同时在清洗完毕后无法再次防止其生锈,导致金属零部件的清洗效率低下。
3.为了提高除锈效率,通常在清洗剂中加入适量的磨料,通过摩擦作用,达到高效除锈的目的。但是摩擦会导致金属表面划伤,磨擦生热也会导致金属表面受热膨胀发生形变,影响金属工件的使用以及后续的寿命。
4.有鉴于上述现有技术存在的缺陷,本发明人基于从事此类材料多年丰富经验及专业知识,配合理论分析,加以研究创新,开发一种防锈金属清洗剂及其制备方法和使用方法。
技术实现要素:5.本发明的第一个目的是提供一种防锈金属清洗剂。通过纳米磁性混合磨料的加入,使除锈剂形成纳米磁性流体,大幅提高除锈剂的导热性能,在清洗过程中,能够快速降低金属表面的温度,达到保护金属的目的。
6.本发明的上述技术目的是通过以下技术方案得以实现的:本发明提供的一种防锈金属清洗剂,按照重量份数计算,包括如下组分:有机溶剂20~30份,除锈剂10~15份,缓蚀剂6~8份,乳化剂5~9份,表面活性剂6~10份和水30~60份;其中,除锈剂由纳米磁性混合磨料、环糊精和水组成,其质量比为(1.5~5):(5~15):30。
7.由于本发明中,采用纳米磁性混合磨料的意义在于,通过纳米磁性粒子分散于水和有机溶剂中获得纳米磁性流体,利用纳米磁性流体的导热和快速散热性能,但是环糊精的存在会削弱纳米磁性流体的导热性能。若环糊精的含量过高,则会影响导热效果,若环糊精的含量过低,则无法形成缓冲作用,容易使磨料划伤金属表面。
8.而纳米磁性混合磨料的含量过高或过低均会降低纳米磁性流体的导热性能,因此本发明中采用上述配比,以保证纳米磁性流体的导热性能和除锈效率。
9.进一步的,纳米磁性混合磨料是sic磁性磨料、al2o3磁性磨料或cbn磁性磨料中的任意一种或几种的混合物,其粒径为3~50nm。
10.进一步的,纳米磁性混合磨料是sic磨料、al2o3磨料或cbn磨料与磁性fe3o4纳米粒
子的混合物;其质量比为(3~8):1。
11.本发明提供的纳米磁性混合磨料,能够在清洗过程中,使纳米磁性粒子通过磁性吸附在具有磁性的金属工件表面,对工件进行包覆,之后再通过磨料的摩擦作用,将金属工件表面的锈和纳米磁性粒子共同从金属工件表面去除,在这个过程中,纳米磁性粒子发挥纳米磁性流体的超导热作用,迅速将摩擦产生的热量从金属工件表面转移扩散到清洗剂中,起到快速降温的作用。同时通过纳米磁性粒子对金属的包覆,起到对摩擦进行缓冲的作用,避免磨料划伤金属工件,并通过纳米磁性粒子对锈的吸附作用,使纳米磁性粒子能够对锈的疏松孔道进行填充,通过磁性作用瓦解锈的骨架,使除锈更加彻底且高效。
12.本发明提供的纳米磁性混合磨料的采用的配比,能够保证除锈效率的情况下,提高纳米磁性粒子能够形成纳米磁性流体。
13.其中,环糊精的作用一是避免纳米磁性粒子团聚;二是同样对磨料进行缓冲,保护金属工件;三是对洗脱下来的锈进行粘附,提高清洁力。
14.进一步的,缓蚀剂是聚乙烯亚胺或聚醚醚酮中的任意一种。本发明中采用聚乙烯亚胺或聚醚醚酮作为缓蚀剂,是由于上述两种聚合物中含有酰胺键,能够吸附于金属表面,当纳米磁性粒子和锈从金属工件表面脱落后,裸露出的金属表面容易与清洗剂中的其他化合物反应,也容易被腐蚀或氧化,而聚乙烯亚胺和聚醚醚酮能够在三乙胺的作用下,迅速吸附在金属工件表面并形成薄薄的mofs膜,从而避免金属工件的二次腐蚀和氧化,达到防锈的目的。
15.进一步的,含有酰胺基团的聚合物是聚乙烯亚胺。
16.进一步的,有机溶剂是三乙醇胺、乙烯乙二醇醚或二乙二醇单丁醚中的任意一种。
17.进一步的,表面活性剂是十二烷基苯磺酸钠、十二烷基硫酸钠或脂肪醇聚氧乙烯醚中的任意一种。
18.本发明的第二个目的是提供一种防锈金属清洗剂的制备方法,具有同样的技术效果。
19.本发明的上述技术目的是由以下技术方案实现的:本发明提供的一种防锈金属清洗剂的制备方法,将纳米磁性混合磨料、环糊精与水混合,超声搅拌均匀得到除锈剂;将除锈剂加入到有机溶剂超声分散均匀;将乳化剂、表面活性剂、缓蚀剂和水加入到有机溶剂中超声分散均匀。
20.作为上述技术方案的优选,还可以将纳米磁性粒子、环糊精和水先超声混合,制备成纳米磁性流体后,再加入磨料。采用这种制备方法,能够使纳米磁性粒子在基液中分散的更加均匀,提高导热效率。
21.作为上述技术方案的优选,还可以先将环糊精和水混合均匀,制备成基液,再在超声的条件下依次加入纳米磁性粒子和磨料,避免纳米磁性粒子与磨料发生团聚。
22.作为上述技术方案的优选,还可以先将磨料与环糊精、水共同搅拌均匀后,加入纳米磁性粒子,这样做的方式可以在加入纳米磁性粒子前,采用环糊精对磨料进行一个预裹附,在后续使用中,提高环糊精的缓冲作用。
23.本发明的第三个目的是提供一种防锈金属清洗剂的使用方法,能够进一步提高除锈剂的导热性能,避免金属受热产生形变,影响金属工件的使用寿命;同时通过附加的场强使磁性磨料产生定向移动,避免无规律的摩擦使磨料擦伤金属工件表面。
24.本发明的上述技术目的是通过以下技术方法实现的:本发明提供的一种防锈金属清洗剂的使用方法,在清洗金属过程中,对金属清洗剂附加磁场。
25.在外加磁场的作用下,纳米磁性流体的导热性能进一步提高,提高了散热效率;同时,由于外加磁场的作用,纳米磁性粒子吸附在金属工件表面时,定向排列于金属工件表面且形成链状结构,使磨料的清洗作用达到定向清洗的效果,一方面提高了清洗效率,另一方面,避免磨料以及纳米磁性粒子的无序移动,使摩擦力分布不均匀,影响清洗效果的同时,提高划伤金属工件表面的风险。
26.作为上述技术方案的优选,附加磁场的方向应与金属工件上最大平面的延展方向一致。
27.采用上述附加磁场的方向,能够使纳米磁性粒子的定向排列方向与金属工件上最大平面的延展方向一致,在纳米磁性粒子定向排列的过程中,形成长程有序的排列方式,在磨料的作用下,纳米磁性粒子之间也会形成长程有序的相互挤压,从而提高瓦解锈的骨架的同时,使锈与金属工件之间的结合力变弱,有序的将锈从金属工件表面剥离开来。
28.若金属工件为圆形或类似于圆柱形的立方体,则可采用旋转磁场,旋转方向为逆时针旋转,旋转角度为5~10
°
/s。
29.然而,当磁场强度过大时,纳米磁性粒子与金属工件表面之间的吸附力过大,增大了除锈的难度,同时提高了磨料与金属工件表面的摩擦力,提高划伤金属工件表面的风险;同时磁场强度过大会导致纳米磁性流体的导热性能下降,且当磁场撤走时,纳米磁性粒子中残存的磁性会导致磁性纳米粒子的团聚。
30.若磁场强度过小,则无法提高纳米磁性流体的导热系数,也无法使所有的纳米磁性粒子形成长程有序的定向排列。因此本发明中采用磁场强度为50~80mt。
31.作为上述技术方案的优选,为了提高纳米磁性流体的导热性能,本发明中还可以采用梯度场强的附加磁场。
32.作为上述技术方案的优选,本发明还提供了梯度磁场场强的计算模型,使纳米磁性粒子能够长程有序排列的同时,保证了纳米磁性流体的导热性能,具体如下:;其中b
t
为第t次所加的附加磁场的场强,t为≥1的整数;x为环糊精在除锈剂的质量百分比;d
50
和d
90
是纳米磁性粒子的粒径分布,该粒径分布是通过激光粒度分析仪测试得到的;b0为初始场强,取值为5~15mt。由于本发明提供的纳米磁性流体在场强的作用下会自组装为链状结构,而这种链状结构是提高纳米磁性流体的导热性能的根本因素。因此如何有序快速的组成链状结构是附加磁场的最终目的。体系内环糊精的存在,链状结构的自组装过程会受到环糊精的阻碍,因此当环糊精的含量越高时,体系粘度越大,则阻力越大,需要更高的场强使纳米磁性粒子突破阻碍完成自组装,因此梯度场强下,场强的升高速率应该更快;若纳米磁性粒子的粒径分布均匀度差,则由于粒径大小的差异,导致自组装过程更加难以实现,因此当粒度分布中,d90和d50的比值越大,则说明粒度分布越不均匀,则应提高场强升高速率以满足链状结构自组装所需的场强。
33.作为另一种优选方案,在清洗金属的过程中,对金属清洗剂附加电场。
34.作为上述技术方案的优选,附加电场的方向应与金属工件上最大平面的延展方向一致。
35.采用上述附加电场的方向,能够使纳米磁性粒子的定向排列方向与金属工件上最大平面的延展方向一致,在纳米磁性粒子定向排列的过程中,形成长程有序的排列方式,在磨料的作用下,纳米磁性粒子之间也会形成长程有序的相互挤压,从而提高瓦解锈的骨架的同时,使锈与金属工件之间的结合力变弱,有序的将锈从金属工件表面剥离开来。
36.若金属工件为圆形或类似于圆柱形的立方体,则可采用旋转磁场,旋转方向为逆时针旋转,旋转角度为5~10
°
/s。
37.作为上述技术方案的优选,所附加的电场的场强为500~800oe。
38.综上所述,本发明具有以下有益效果:本发明提供的防锈金属清洗剂及其制备方法和应用方法,通过纳米磁性混合磨料的加入,使除锈剂形成纳米磁性流体,大幅提高除锈剂的导热性能,在清洗过程中,能够快速降低金属表面的温度,达到保护金属的目的。
具体实施方式
39.为更进一步阐述本发明为达成预定发明目的所采取的技术手段及功效,对依据本发明提出的一种防锈金属清洗剂及其制备方法和使用方法,其具体实施方式、特征及其功效,详细说明如后。
40.本具体实施方式中采用的原材料来源如下:磁性fe3o4纳米粒子:苏州凯发新材料科技有限公司。
41.实施例1本实施例提供的一种防锈金属清洗剂,按照重量份数计算,包括如下组分:三乙醇胺30份,除锈剂15份,聚乙烯亚胺8份,十二烷基苯磺酸钠10份和水60份;其中,除锈剂包括sic磨料4份,磁性fe3o4纳米粒子1份,环糊精6份和水20份。
42.本实施例提供的防锈金属清洗剂的制备方法如下:s1、制备除锈剂:常温常压下,将sic磨料、磁性fe3o4纳米粒子、环糊精和水混合超声,分散均匀备用;s2、将步骤s1制备的除锈剂与剩余水、三乙醇胺、聚乙烯亚胺和十二烷基苯磺酸钠共同混合,超声分散均匀得到清洗剂。
43.本实施例提供的防锈金属清洗剂的使用方法如下:将金属工件浸没于本实施例提供的防锈金属清洗剂中,外加场强为75mt的磁场,清洗10min,清洗过程中采用常规温度测量仪器测试金属工件表面的平均温度,测试值为30℃。
44.实施例2本实施例提供的一种防锈金属清洗剂,按照重量份数计算,包括如下组分:三乙醇胺30份,除锈剂15份,聚乙烯亚胺8份,十二烷基苯磺酸钠10份和水60份;其中,除锈剂包括sic磨料4份,磁性fe3o4纳米粒子1份,环糊精6份和水20份。
45.本实施例提供的防锈金属清洗剂的制备方法如下:s1、制备除锈剂:常温常压下,先将环糊精和水混合均匀,制备成基液,再在超声的
条件下依次加入磁性fe3o4纳米粒子和sic磨料分散均匀;s2、将步骤s1制备的除锈剂与剩余水、三乙醇胺、聚乙烯亚胺和十二烷基苯磺酸钠共同混合,超声分散均匀得到清洗剂。
46.本实施例提供的防锈金属清洗剂的使用方法如下:将金属工件浸没于本实施例提供的防锈金属清洗剂中,外加场强为80mt的磁场,清洗10min,清洗过程中采用常规温度测量仪器测试金属工件表面的平均温度,测试值为29.2℃。
47.实施例3本实施例提供的一种防锈金属清洗剂,按照重量份数计算,包括如下组分:三乙醇胺30份,除锈剂15份,聚乙烯亚胺8份,十二烷基苯磺酸钠10份和水60份;其中,除锈剂包括sic磨料4份,磁性fe3o4纳米粒子1份,环糊精6份和水20份。
48.本实施例提供的防锈金属清洗剂的制备方法如下:s1、制备除锈剂:常温常压下,先将sic磨料与环糊精、水共同搅拌均匀后,加入磁性fe3o4纳米粒子;s2、将步骤s1制备的除锈剂与剩余水、三乙醇胺、聚乙烯亚胺和十二烷基苯磺酸钠共同混合,超声分散均匀得到清洗剂。
49.本实施例提供的防锈金属清洗剂的使用方法如下:将金属工件浸没于本实施例提供的防锈金属清洗剂中,外加场强为65mt的磁场,清洗10min,清洗过程中采用常规温度测量仪器测试金属工件表面的平均温度,测试值为30.6℃。
50.实施例4本实施例提供的一种防锈金属清洗剂,按照重量份数计算,包括如下组分:三乙醇胺30份,除锈剂15份,聚乙烯亚胺8份,十二烷基苯磺酸钠10份和水60份;其中,除锈剂包括sic磨料5份,磁性fe3o4纳米粒子1份,环糊精6份和水20份。
51.本实施例提供的防锈金属清洗剂的制备方法如下:s1、制备除锈剂:常温常压下,将sic磨料、磁性fe3o4纳米粒子、环糊精和水混合超声,分散均匀备用;s2、将步骤s1制备的除锈剂与剩余水、三乙醇胺、聚乙烯亚胺和十二烷基苯磺酸钠共同混合,超声分散均匀得到清洗剂。
52.本实施例提供的防锈金属清洗剂的使用方法如下:将金属工件浸没于本实施例提供的防锈金属清洗剂中,外加场强为80mt的磁场,磁场方向与金属工件最大平面的延展方向一致,清洗10min,清洗过程中采用常规温度测量仪器测试金属工件表面的平均温度,测试值为29.6℃。
53.实施例5本实施例提供的一种防锈金属清洗剂,按照重量份数计算,包括如下组分:三乙醇胺30份,除锈剂15份,聚乙烯亚胺8份,十二烷基苯磺酸钠10份和水60份;其中,除锈剂包括sic磨料4份,磁性fe3o4纳米粒子1份,环糊精6份和水20份。
54.本实施例提供的防锈金属清洗剂的制备方法如下:s1、制备除锈剂:常温常压下,将sic磨料、磁性fe3o4纳米粒子、环糊精和水混合超
声,分散均匀备用;s2、将步骤s1制备的除锈剂与剩余水、三乙醇胺、聚乙烯亚胺和十二烷基苯磺酸钠共同混合,超声分散均匀得到清洗剂。
55.本实施例提供的防锈金属清洗剂的使用方法如下:将金属工件浸没于本实施例提供的防锈金属清洗剂中,外加场强为梯度的磁场,增加到一定场强后,不再增加,磁场方向与金属工件最大平面的延展方向一致,清洗10min,清洗过程中采用常规温度测量仪器测试金属工件表面的平均温度,测试值为28.4℃。
56.其中,磁场场强的计算模型如下:;其中b
t
为第t次所加的附加磁场的场强,梯度选择为8组,既t=1~8;x为环糊精在除锈剂的质量百分比;d
50
和d
90
是纳米磁性粒子的粒径分布,该粒径分布是通过激光粒度分析仪测试得到的,测试可知,d
50
=4.2nm;d
90
=6.8nm,初始场强b0为10mt。
57.计算可知,梯度磁场的施加方式如下表:表1.梯度磁场场强实施例6本实施例提供的一种防锈金属清洗剂,按照重量份数计算,包括如下组分:三乙醇胺30份,除锈剂15份,聚乙烯亚胺8份,十二烷基苯磺酸钠10份和水60份;其中,除锈剂包括sic磨料4份,磁性fe3o4纳米粒子1份,环糊精6份和水20份。
58.本实施例提供的防锈金属清洗剂的制备方法如下:s1、制备除锈剂:常温常压下,将sic磨料、磁性fe3o4纳米粒子、环糊精和水混合超声,分散均匀备用;
s2、将步骤s1制备的除锈剂与剩余水、三乙醇胺、聚乙烯亚胺和十二烷基苯磺酸钠共同混合,超声分散均匀得到清洗剂。
59.本实施例提供的防锈金属清洗剂的使用方法如下:将金属工件浸没于本实施例提供的防锈金属清洗剂中,外加场强为68oe的电场,电场方向与金属工件最大平面的延展方向一致,清洗10min,清洗过程中采用常规温度测量仪器测试金属工件表面的平均温度,测试值为29.8℃。
60.对比实施例1本实施例提供的一种防锈金属清洗剂,按照重量份数计算,包括如下组分:三乙醇胺30份,除锈剂15份,聚乙烯亚胺8份,十二烷基苯磺酸钠10份和水60份;其中,除锈剂包括sic磨料4份,环糊精6份和水20份。
61.本实施例提供的防锈金属清洗剂的制备方法如下:s1、制备除锈剂:常温常压下,将sic磨料、环糊精和水混合超声,分散均匀备用;s2、将步骤s1制备的除锈剂与剩余水、三乙醇胺、聚乙烯亚胺和十二烷基苯磺酸钠共同混合,超声分散均匀得到清洗剂。
62.本实施例提供的防锈金属清洗剂的使用方法如下:将金属工件浸没于本实施例提供的防锈金属清洗剂中,外加场强为75mt的磁场,清洗10min,清洗过程中采用常规温度测量仪器测试金属工件表面的平均温度,测试值为38℃。
63.对比实施例2本实施例提供的一种防锈金属清洗剂,按照重量份数计算,包括如下组分:三乙醇胺30份,除锈剂15份,聚乙烯亚胺8份,十二烷基苯磺酸钠10份和水60份;其中,除锈剂包括sic磨料4份,磁性fe3o4纳米粒子1份,环糊精6份和水20份。
64.本实施例提供的防锈金属清洗剂的制备方法如下:s1、制备除锈剂:常温常压下,将sic磨料、磁性fe3o4纳米粒子、环糊精和水混合超声,分散均匀备用;s2、将步骤s1制备的除锈剂与剩余水、三乙醇胺、聚乙烯亚胺和十二烷基苯磺酸钠共同混合,超声分散均匀得到清洗剂。
65.本实施例提供的防锈金属清洗剂的使用方法如下:将金属工件浸没于本实施例提供的防锈金属清洗剂中,清洗10min,清洗过程中采用常规温度测量仪器测试金属工件表面的平均温度,测试值为34℃。
66.性能测试将实施例1~6和对比实施例1~2清洗后的金属工件进行表面测试,测试结果如下表。
67.其中测试方法:取8块尺寸相同,锈蚀程度相同,厚度为80mm的热轧钢板,将其依次编号为1~8,分别采用实施例1~6以及对比实施例1~2的清洗剂和清洗方法对编号1~8的钢板进行清洗,根据国家标准gb/t14977-94标准,对编号1~8钢板的缺陷度进行测试;根据hg/t 2387-2016《化工设备化学清洗质量标准》对钢板样品进行腐蚀率、除垢率测试。
68.表2.测试结果
由实施例2和实施例1对比可知,采用更高的场强后,清洗温度进一步降低,且不影响腐蚀率以及除垢率和金属表面的平整度;根据实施例5与实施例1对比可知,采用梯度场强后,清洗温度降低的同时,清洗效果有所提升,且能够有效降低金属表面的划伤程度;根据对比实施例1与实施例1对比可知,当不采用本发明提供的磁性粒子时,碳化硅与磁性粒子的协同作用消失,清洗温度提高,清洗效果下降,且金属表面划痕深度提高;根据对比实施例2与实施例1对比可知,不外加磁场的情况下,清洗温度提高,清洗效果下降,金属表面有明显划痕。
69.以上所述,仅是本发明的较佳实施例而已,并非对本发明作任何形式上的限制,虽然本发明已以较佳实施例展示如上,但并非用以限定本发明,任何熟悉本专业的技术人员,在不脱离本发明技术方案范围内,当可利用上述揭示的技术内容做出些许更动或修饰为等同变化的等效实施例,但凡是未脱离本发明技术方案的内容,依据本发明的技术实质对以上实施例所作的任何简单修改、等同变化与修饰,均仍属于本发明技术方案的范围内。