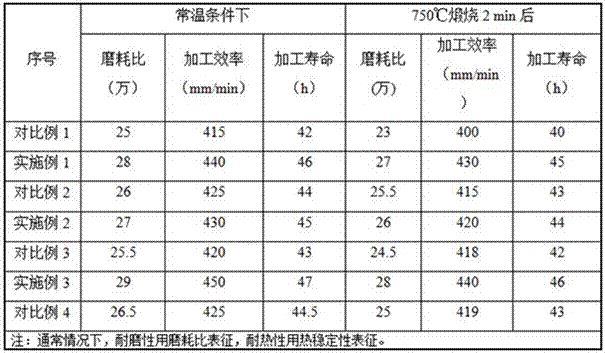
1.本发明属于超硬复合材料技术领域,具体涉及一种聚晶金刚石复合片及其制备方法。
背景技术:2.聚晶金刚石(polycrystalline diamond,简称pcd)复合片是金刚石微粒与硬质合金基体在高温高压下烧结而成的一种新型超硬复合材料。不仅具有金刚石硬度高、耐磨性高、导热性好的特点,还兼具硬质合金的强度和韧性。随着工业技术的不断发展,聚晶金刚石复合片的应用领域得到不断的开发,尤其是目前在刀具类的应用越来越广泛,如,航空航天、汽车、能源、地质石油勘探、军工、精密制造等重要领域。
3.聚晶金刚石复合片作为刀具使用时容易因复合片的耐热性和抗冲击韧性不够,导致在刀具成形加工时复合片上的聚晶金刚石层受高温影响易产生氧化、石墨化。深圳先进技术研究院拥有的发明专利申请cn 109128192 a中公开了一种聚晶金刚石复合片及其制备方法;其聚晶金刚石复合片包括硬质合金基体层和聚晶金刚石层以及过渡层,所述过渡层层叠结合在所述硬质合金基体层与所述聚晶金刚石层之间,所述聚晶金刚石层的背离所述硬质合金基体层的表面上结合有cvd金刚石层,通过各层的协同作用,赋予其聚晶金刚石复合片优异的耐磨性能和耐高温性能,而且聚晶金刚石层与硬质合金基体的结合强度得到提高。
4.但上述发明专利申请中公开的聚晶金刚石复合片仍然存在各部位和区域性能不均一,作为刀具使用时聚晶金刚石层受高温影响易产生氧化、石墨化等问题;同时,因聚晶金刚石复合片合成过程中因聚晶金刚石层和硬质合金基体间残余应力的存在,容易导致裂纹缺陷,尤其是将复合片焊接在基底上制作工具时耐热性差,造成工具的锋利度下降,使用寿命低,生产成本增加,从而限制其广泛应用和发展。
技术实现要素:5.有鉴于此,本发明确有必要提供一种聚晶金刚石复合片及其制备方法,使其具有较高的耐热性、耐磨性和致密性,降低生产成本。
6.为此,本发明的技术方案如下:一种聚晶金刚石复合片,包括硬质合金基体和含硼聚晶金刚石层,其中,所述硬质合金基体和含硼聚晶金刚石层之间层叠设置有过渡层,所述含硼聚晶金刚石层中分散有tio2和tin。
7.基于上述,所述含硼聚晶金刚石层是由平铺设置的钛层和含硼金刚石微粉层高温高压烧结而成。其中,所述ti层的作用是:在高温高压过程中吸附含硼金刚石微粉层中的气体,并生成tio2、tin,来达到去除其中气体的目的,从而提高了聚晶金刚石复合片的耐磨性和致密度。
8.基于上述,所述钛层的厚度0.5~1 mm,所述含硼金刚石微粉中的硼元素质量百分
含量为0.003%~1.2%,所述含硼金刚石微粉层的厚度为0.8~2 mm。
9.基于上述,所述过渡层是由过渡层粉末高温高压烧结形成的,其中,按质量百分含量计,所述过渡层分别包括均匀混合的占比55%~70%的金刚石颗粒、占比25%~30%的碳化钨颗粒和占比5%~15%的结合剂,所述金刚石颗粒的粒度为3~40 μm,所述碳化钨颗粒的粒度为2~10 μm,所述结合剂的粒度为5~10 μm。
10.基于上述,所述结合剂为金属结合剂fe、co或ti中的一种或几种。
11.基于上述,所述过渡层的直径是所述含硼聚晶金刚石层直径的0.5~0.8倍,且所述过渡层的厚度低于或等于所述含硼聚晶金刚石层的厚度;如此,能够提高所述聚晶金刚石复合片中心区域的耐热性、耐磨性和致密性等性能,减少或避免复合片中心区域产生裂纹,降低成本。
12.基于上述,所述硬质合金基体是由wc-co硬质合金构成,且该wc-co硬质合金的粒度略小于或等于所述过渡层粉末的平均颗粒度。如此,所述wc-co硬质合金和过渡层粉末的粒度接近,主要是为了降低聚晶金刚石复合片内部的界面应力,缩小两者的热膨胀系数,提高界面结合力。
13.本发明提供一种聚晶金刚石复合片,是由自下至上依次平铺设置的钛层、含硼金刚石微粉层、过渡层粉末层和硬质合金基体,四者经过高温高压烧结而相互复合形成的一体结构。
14.本发明还提供一种上述聚晶金刚石复合片的制备方法,采用六面顶压机高温高压的方法制备,包括步骤:先将钛粉平铺在金属杯底部上形成钛层,再在所述钛层平铺上含硼金刚石微粉形成含硼金刚石微粉层;将过渡层粉末均匀平铺在所述含硼金刚石微粉层上,形成过渡层粉末层;将硬质合金基体轻置于所述过渡层粉末层上,扣上杯盖并轻轻按压使其平整,得到组装块;将所述组装块置于所述六面顶压机中,于压力5~8 gpa和温度1450~2000℃的条件下烧结处理,制得所述聚晶金刚石复合片。
15.其中,所述聚晶金刚石复合片从六面定压机取出后,经过切割定型、研磨、抛光等步骤处理即制得多个成品。其中,定型处理步骤可以将上述聚晶金刚石复合片按照需求做成片状、三角形、长条状等多种形状。
16.基于上述制备方法,所述形成过渡层粉末层的步骤包括:将所述过渡层粉末均匀平铺在所述含硼金刚石微粉层的中心部位上,并用模具轻轻按压使其平整形成过渡层粉末层,且所述过渡层粉末层的直径是所述含硼金刚石微粉层直径的0.5~0.8倍。
17.所以,本发明提供的上述聚晶金刚石复合片包括硬质合金基体、含硼聚晶金刚石层、层叠结合在所述硬质合金基体和含硼聚晶金刚石层之间的过渡层,通过各层之间的协同作用,使得上述聚晶金刚石复合片具有较好的耐热性、耐磨性、致密性,而且提高了含硼聚晶金刚石层与硬质合金基体之间的结合强度。
18.本发明提供的上述聚晶金刚石复合片的制备方法主要是该方法主要是先将钛层、含硼金刚石微粉层、过渡层粉末层和硬质合金基体自下至上依次平铺设置在金属杯中,然后四者经过高温高压烧结形成一体结构,其中的含金刚石微粉层中硼元素是一种耐热、导
电材料,使得上述聚晶金刚石复合片具有较好的耐热性;同时,由于位于中间的过渡层粉末层的热膨胀系数分别与含硼金刚石微粉层和硬质合金基体的热膨胀系数相近,改善了聚晶金刚石复合片界面处的结合性能,降低了其内部应力的产生,尤其是底部的ti层,在高温高压过程中吸附含硼金刚石微粉层中的气体,生成tio2、tin,来达到去气化的目的,从而提高了聚晶金刚石复合片的耐磨性、致密度。
19.因此,本发明提供的上述聚晶金刚石复合片具有加好的耐热性、耐磨性、致密性和界面结合强度,提高了其作为工具,尤其是刀具的耐磨性和锋利度,降低了内应力;克服了因工具制作过程中焊接时耐热性差等问题,提高了工具的加工效率,延长了工具的使用寿命。
附图说明
20.图1为本发明实施例一提供的聚晶金刚石复合片的照片图。
21.图2为本发明实施例一提供的聚晶金刚石复合片制备过程中的原料铺设结构示意图。
22.其中,以上各图中元件符号:1、硬质合金基体,2、过渡层粉末层,3、含硼金刚石微粉层,4、钛层。
具体实施方式
23.下面通过具体实施方式,对本发明的技术方案做进一步的详细描述。
24.实施例一请参阅图1和图2,本实施例提供一种聚晶金刚石复合片,由硬质合金基体、过渡层和含硼聚晶金刚石层组成,且所述过渡层层叠结合在所述硬质合金基体和含硼聚晶金刚石层之间,所述含硼聚晶金刚石层中分散有tio2和tin。
25.上述聚晶金刚石复合片是按照由下至上的顺序依次层叠平铺钛层4、含硼金刚石微粉层3、过渡层粉末层2和硬质合金基体1,四者经过高温高压烧结而相互复合形成一种超硬复合材料。其中,所述钛层的厚度为0.5 mm,所述含硼金刚石微粉层的厚度为0.8 mm,其中的硼元素的质量百分含量为0.05%。所述过渡层粉末层由均匀混合的15 μm的金刚石颗粒 60%、10 μm的碳化钨颗粒25%和5 μm的金属结合剂ti 15%组成。所述过渡层粉末层的直径是含硼金刚石微粉层直径的0.8倍,厚度为0.8 mm。所述的硬质合金基体是由wc-co硬质合金构成,所述合金基体的粒度略小于所述过渡层粉末层的颗粒度。
26.本实施例还提供一种上述聚晶金刚石复合片的具体制备方法,包括以下步骤:(1)先将钛粉平铺在金属杯底部上形成0.5 mm厚的钛层4,再在所述钛层4平铺上含硼金刚石微粉形成0.8 mm厚的含硼金刚石微粉层3;(2)将过渡层粉末均匀平铺在所述含硼金刚石微粉层3的中心部位上,并用模具轻轻按压使其平整形成0.8 mm厚的过渡层粉末层2,且所述过渡层粉末层2的直径是所述含硼金刚石微粉层直径的0.8倍;(3)将硬质合金基体1轻置于所述过渡层粉末层2上,扣上杯盖并轻轻按压使其平整,得到组装块;(4)将所述组装块置于所述六面顶压机中,于压力5 gpa和温度1480℃的条件下烧
结处理,合成复合片毛坯;(5)对上述合成的复合片毛坯进行研磨、抛光处理得到多个上述聚晶金刚石复合片成品。其中,该多个聚晶金刚石复合片成品的耐磨性、致密性、耐热性以及加工性能等基本一致。
27.实施例二本实施例提供一种聚晶金刚石复合片,其结构与实施例一提供的聚晶金刚石复合片的结构基本相同,主要不同之处在于:本实施例中,所述钛层的厚度为0.8 mm,所述含硼金刚石微粉层的厚度为1 mm,其中的硼元素的质量百分含量为0.003%;所述过渡层粉末层由均匀混合的10μm的金刚石颗粒 55%、8μm的碳化钨颗粒30%和10μm的金属结合剂15%组成,其中,金属结合剂为质量比为3:1.5的co和ti;所述过渡层粉末层的直径是含硼金刚石微粉层直径的0.6倍,厚度为0.5 mm;所述合金基体的粒度略小于所述过渡层粉末层的颗粒度。
28.本实施例提供一种上述聚晶金刚石复合片的制备方法,该制备方法与实施例一提供的复合片的制备方法基本相同,主要不同之处在于:本实施例中,原料组成不同;各原料层的厚度不同;所述过渡层粉末层的直径不同;烧结压力8 gpa、烧结温度1800℃。
29.实施例三本实施例提供一种聚晶金刚石复合片,其结构与实施例一提供的聚晶金刚石复合片的结构基本相同,主要不同之处在于:本实施例中,所述钛层的厚度为1 mm,所述含硼金刚石微粉层的厚度为1.2 mm,其中的硼元素的质量百分含量为1.2%;所述过渡层粉末层由均匀混合的20 μm的金刚石颗粒 65%、5 μm的碳化钨颗粒25%和10 μm的金属结合剂10%组成,其中,金属结合剂为质量比为3 : 2的co和ti;所述过渡层粉末层的直径是含硼金刚石微粉层直径的0.5倍,厚度为1.0 mm;所述合金基体的粒度等于所述过渡层粉末层的颗粒度。
30.本实施例提供一种上述聚晶金刚石复合片的制备方法,该制备方法与实施例一提供的复合片的制备方法基本相同,主要不同之处在于:本实施例中,原料组成不同;所述过渡层粉末层的直径不同;烧结压力6 gpa、烧结温度1500℃。
31.性能验证对实施例1~3和对比例1和2提供的聚晶金刚石复合片的耐磨性、热稳定性及加工寿命方面进行测试。
32.其中,对比例1为市场常规聚晶金刚石复合片。
33.对比例2~4均为含硼聚晶金刚石复合片,其制备方法分别与实施例1~3提供的方法基本相同,主要不同之处在于:对比例2~4中不含有钛层,且其中的过渡层粉末层的直径与对应的含硼金刚石微粉层的直径相等。其中,对比例2与实施例1相比缺少钛层,对比例3与实施例2相比缺少钛层,对比例4和实施例3相比缺少钛层。
34.磨耗比检测参照jb-t3235-1999。
35.加工效率和加工寿命的检测方法是:将实施例1~3及对比例1~4提供的聚晶金刚石复合片分别制成相同规格和结构的切削刀片,在切削参数(刀具转速n=4000 r/min、刀具进给f=400 mm/min)相同条件下加工铝合金时加工效率和加工寿命的对比。
36.热稳定性是指各聚晶金刚石复合片经过750℃煅烧2 min后的磨耗比和加工寿命。
37.其中,聚晶金刚石复合片的检测结果如表1所示。
38.表1各实施例和对比例所得聚晶金刚石复合片的性能检测结果因此,本发明实施例提供的上述聚晶金刚石复合片及其由上述方法制备出的聚晶金刚石复合片,采用含硼金刚石微粉制作复合片,提高了复合片的耐热性;同时,在含硼金刚石微粉层和硬质合金层之间设置同金刚石热膨胀系数相近的过渡层,改善了聚晶金刚石复合片界面处的结合性能,降低了内部应力的产生,提高其耐磨性,尤其是底部的钛金属层的使用,减少了金刚石层的中的气体,生成钛氮化物提高了金刚石层中心部位的致密性,提高了加工效率,延长了工具的使用寿命。上述聚晶金刚石复合片可以用于制作铣削、切削类型工具,可以加工金属材料、合金材料、木材等。
39.最后应当说明的是:以上实施例仅用以说明本发明的技术方案而非对其限制;尽管参照较佳实施例对本发明进行了详细的说明,所属领域的普通技术人员应当理解:依然可以对本发明的具体实施方式进行修改或者对部分技术特征进行等同替换;而不脱离本发明技术方案的精神,其均应涵盖在本发明请求保护的技术方案范围当中。