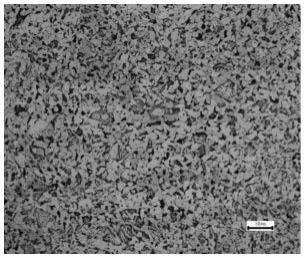
一种350~400mm厚心部细晶钢s355nl的生产方法
技术领域
1.本发明属于特厚钢板生产技术领域,具体涉及到一种350~400mm厚s355nl心部细晶钢的生产方法。
背景技术:2.随着客户需求的提升,特厚板质量方面更加注重心部位置性能及晶粒度;目前我们正常轧制生产的350~400mm厚s355nl模铸板心部晶粒度仅在5级左右,不能满足高端客户需求。
3.鉴于此,提出本发明。
技术实现要素:4.本发明的目的是提供一种350~400mm厚心部细晶钢s355nl的生产方法,通过该工艺制得的350~400mms355nl特厚板心部晶粒度细小达到7级以上,心部(1/2位置)性能也满足en10025-3标准。
5.本发明是通过如下方式实现的:一种350~400mm厚s355nl心部细晶钢的生产方法,所述钢板包含如下熔炼成分(单位,wt%):c:0.07~0.10、si:0.10~0.40、mn:1.55~1.65、p:≤0.010、s:≤0.003、nb:0.030~0.040、ni:0.18~0.22、cu:0.20~0.25、als:0.030~0.050,其它为fe和残留元素;
6.所述钢板的生产方法是通过以下工艺流程实现的:铁水kr脱硫
→
转炉冶炼
→
lf精炼
→
vd真空脱气
→
模铸浇铸
→
铸锭处理
→
铸锭低温加热
→
轧制及模拟一次正火
→
二次正火
→
堆冷
→
检测
→
切割成型
→
入库:
7.各环节点生产方法要求如下:
8.1)kr铁水预处理:铁水到站后开始扒渣,液面渣层厚度≤20mm,铁水经kr搅拌脱硫s≤0.005%,脱硫时间≤10min、脱硫温降≤10℃。
9.2)转炉冶炼:入炉铁水s≤0.005%、p≤0.070%,铁水温度≥1270℃,冶炼过程添加优质废钢,出钢目标c0.05~0.07%、p≤0.010%、s≤0.010%,出钢过程中向钢包内加入硅铝钡钙、锰铁合金、硅铁合金和石灰、萤石。出钢前用挡渣塞挡前渣出钢,出钢结束前采用挡渣锥挡渣,保证渣层厚度≤20mm,转炉出钢过程中全程吹氩。
10.3)lf精炼:精炼采用小渣量控制,精炼脱氧剂以电石、铝粒为主,加入量根据钢水中氧含量及造白渣情况适量加入,总加热时间≥25min,终渣为流动性良好、粘度合适的泡沫白渣;离站前加入硅钙线,上钢温度1600~1610℃。
11.4)vd真空脱气:vd真空度45pa,保压时间≥25min,保压过程翻腾效果良好;破真空后软吹1~2min,软吹过程中钢水不得裸露。vd定氢≤1.0ppm,上钢温度1565~1570℃。
12.5)模铸浇注:采用45t定厚调宽水冷模铸锭,铸锭规格1050*2000*2800mm。钢水到模铸平台后,吹氩控制浇钢温度,吹氩时间约8min,浇注温度控制1550~1560℃;浇注前,模铸保护渣一半采取草绳吊挂的方式挂在锭模中,吊挂高度离锭模底部300mm,另一半在开浇
后2min内加完,浇注到帽口1/3位置时,向每个锭模内添加40kg碳化稻壳,浇注完毕后,先用氧管将帽口内的碳化稻壳铺平后,再向每个锭内添加60kg的碳化稻壳,并用氧管均匀铺平;浇注完毕60min内,要对每支锭及时补加40kg以上的碳化稻壳保证帽口部位不见红,同时在注毕1h内,向每个锭模内补加40kg的碳化稻壳。
13.6)铸锭处理:铸锭脱模后堆冷≥12小时拆垛清理,清理合格后装炉加热。
14.7)铸锭低温加热:钢锭清理合格后装均热坑,采用低温加热工艺,加热温度1160~1180℃,保证钢锭均匀烧透,但要严防钢锭过热、过烧;确保原始奥氏体晶粒度不过度长大。
15.8)轧制及模拟一次正火:分两阶段控温轧制:第一阶段开轧温度≥1000℃,轧机工作辊转速≤20r/min,每道次压下量60~70mm,轧制8~10道次至锭厚450~490mm时快速进入acc降温冷却,使钢锭心部冷却至再结晶区温度1023℃以下(表面温度约900℃以下),避免混晶问题。钢锭返红均温1~2分钟后开始二阶段轧制,二阶段小压下量10~20mm,以控制原始板型为主,终轧温度控制在860~880℃;终轧结束后20s内进入acc冷却,模拟一次正火,acc辊速0.8~1.0m/s连续冷却3~4次(反复冷却前需充分返红),钢锭冷却速度约4℃/s;水冷过程测量监控钢板返红温度进行调整,最终冷床测量目标返红温度约550~580℃。通过轧制及模拟一次正火工艺,细化钢板心部晶粒,提高晶粒的均匀度,使钢板获得初步的细晶组织。下线后入缓冷坑,钢锭温度400~450℃,缓冷时间≥48h。
16.9)二次正火:钢锭拆垛后转外机炉正火,采用860℃的临界温度正火来细化心部晶粒度,保温系数2.2min/mm;即将钢板加热到内部晶粒刚刚完全奥氏体化温度,将刚刚完全奥氏体化的细小晶粒通过正火水冷后遗传下来,正火水池水温≤25℃,同时在冷却过程中开启压缩空气对冷却水进行搅拌,以促进均匀散热,提高钢板与水之间的传热速度;返红温度560~580℃,此时钢板的强韧性适中。
17.10)堆冷:钢板水冷出钢后集中堆垛缓冷,垛顶用石棉布覆盖保温,缓冷温度约500℃,缓冷>12h,利用钢板余热进行一次中温回火,消除正火水冷后钢板内部产生的应力,稳定组织,改善钢板加工性能。
18.本发明的有益效果是:通过低温加热、轧制及模拟一次正火、二次正火+堆冷方式,获得350~400mm厚s355nl心部细晶粒钢,心部晶粒度达到7~8级,相比常规生产方式,心部晶粒度可提高2~3级,从而满足高端客户对特厚板心部性能和晶粒度的要求。
附图说明
19.下面结合附图及实施例,对本发明的技术特征作进一步描述。
20.图1是本发明中350mm厚度1/4位置的金相组织示意图。
21.图2是本发明中350mm厚度1/2位置的金相组织示意图。
22.图3是本发明中400mm厚度1/4位置的金相组织示意图。
23.图4是本发明中400mm厚度1/2位置的金相组织示意图。
具体实施方式
24.为了更好地理解本技术,下面结合实施例进一步清楚阐述本技术的内容,但本技术的保护内容不仅仅局限于下面的实施例。在下文的描述中,给出了大量具体的细节以便提供对本技术更为彻底的理解。然而,对于本领域技术人员来说显而易见的是,本技术可以
无需一个或多个这些细节而得以实施。
25.本发明一种特厚s355nl心部细晶粒钢的工艺流程为:铁水kr脱硫
→
转炉冶炼
→
lf精炼
→
vd真空脱气
→
模铸浇铸
→
铸锭处理
→
铸锭低温加热
→
轧制及模拟一次正火
→
二次正火
→
堆冷
→
检测
→
切割成型
→
入库。包含如下熔炼成分(单位,wt%):c:0.07~0.10、si:0.10~0.40、mn:1.55~1.65、p:≤0.010、s:≤0.003、nb:0.030~0.040、ni:0.18~0.22、cu:0.20~0.25、als:0.030~0.050,其它为fe和残留元素;
26.各环节点生产方法要求如下:
27.(1)kr铁水预处理:铁水到站后开始扒渣,液面渣层厚度≤20mm,铁水经kr搅拌脱硫s≤0.005%,脱硫时间≤10min、脱硫温降≤10℃。
28.(2)转炉冶炼:入炉铁水s≤0.005%、p≤0.070%,铁水温度≥1270℃,冶炼过程添加优质废钢,出钢目标c0.05~0.07%、p≤0.010%、s≤0.010%,出钢过程中向钢包内加入硅铝钡钙、锰铁合金、硅铁合金和石灰、萤石。出钢前用挡渣塞挡前渣出钢,出钢结束前采用挡渣锥挡渣,保证渣层厚度≤20mm,转炉出钢过程中全程吹氩。
29.(3)lf精炼:精炼采用小渣量控制,精炼脱氧剂以电石、铝粒为主,加入量根据钢水中氧含量及造白渣情况适量加入,总加热时间≥25min,终渣为流动性良好、粘度合适的泡沫白渣;离站前加入硅钙线,上钢温度1600~1610℃。
30.(4)vd真空脱气:vd真空度45pa,保压时间≥25min,保压过程翻腾效果良好;破真空后软吹1~2min,软吹过程中钢水不得裸露。vd定氢≤1.0ppm,上钢温度1565~1570℃。
31.(5)模铸浇注:采用45t定厚调宽水冷模铸锭,铸锭规格1050*2000*2800mm。钢水到模铸平台后,吹氩控制浇钢温度,吹氩时间约8min,浇注温度控制1550~1560℃;浇注前,模铸保护渣一半采取草绳吊挂的方式挂在锭模中,吊挂高度离锭模底部300mm,另一半在开浇后2min内加完,浇注到帽口1/3位置时,向每个锭模内添加40kg碳化稻壳,浇注完毕后,先用氧管将帽口内的碳化稻壳铺平后,再向每个锭内添加60kg的碳化稻壳,并用氧管均匀铺平;浇注完毕60min内,要对每支锭及时补加40kg以上的碳化稻壳保证帽口部位不见红,同时在注毕1h内,向每个锭模内补加40kg的碳化稻壳。
32.(6)铸锭处理:铸锭脱模后堆冷≥12小时拆垛清理,清理合格后装炉加热。
33.(7)铸锭低温加热:钢锭清理合格后装均热坑,采用低温加热工艺,加热温度1160~1180℃,保证钢锭均匀烧透,但要严防钢锭过热、过烧;确保原始奥氏体晶粒度不过度长大。
34.(8)轧制及模拟一次正火:分两阶段控温轧制:第一阶段开轧温度≥1000℃,轧机工作辊转速≤20r/min,每道次压下量60~70mm,轧制8~10道次至锭厚450~490mm时快速进入acc降温冷却,使钢锭心部冷却至再结晶区温度1023℃以下(表面温度约900℃以下),避免混晶问题。钢锭返红均温1~2分钟后开始二阶段轧制,二阶段小压下量10~20mm,以控制原始板型为主,终轧温度控制在860~880℃;终轧结束后20s内进入acc冷却,模拟一次正火,acc辊速0.8~1.0m/s连续冷却3~4次(反复冷却前需充分返红),钢锭冷却速度约4℃/s;水冷过程测量监控钢板返红温度进行调整,最终冷床测量目标返红温度约550~580℃。通过轧制及模拟一次正火工艺,细化钢板心部晶粒,提高晶粒的均匀度,使钢板获得初步的细晶组织。下线后入缓冷坑,钢锭温度400~450℃,缓冷时间≥48h。
35.(9)二次正火:钢锭拆垛后转外机炉正火,采用860℃的临界温度正火来细化心部
晶粒度,保温系数2.2min/mm;即将钢板加热到内部晶粒刚刚完全奥氏体化温度,将刚刚完全奥氏体化的细小晶粒通过正火水冷后遗传下来,正火水池水温≤25℃,同时在冷却过程中开启压缩空气对冷却水进行搅拌,以促进均匀散热,提高钢板与水之间的传热速度;返红温度560~580℃,此时钢板的强韧性适中。
36.(10)堆冷:钢板水冷出钢后集中堆垛缓冷,垛顶用石棉布覆盖保温,缓冷温度约500℃,缓冷>12h,利用钢板余热进行一次中温回火,消除正火水冷后钢板内部产生的应力,稳定组织,改善钢板加工性能。
37.具体实施例(各实施例根据厚度不同,设计的成分不同,控轧控冷不同,性能检测不完全相同):
38.实施例1
39.350mm厚s355nl心部细晶粒钢包含如下质量百分比的化学成分单位(wt%):c:0.09、si:0.10、mn:1.55、p:0.010、s:0.002、nb:0.035、ni:0.22、cu:0.25、als:0.030,其它为fe和残留元素;
40.采用45t定厚调宽水冷模铸锭,铸锭规格1050*2000*2800mm。第一阶段开轧温度1000℃,轧机工作辊转速18r/min,每道次压下量60mm,轧制10道次至锭厚450mm时快速进入acc降温冷却,表面返红温度880℃。二阶段轧制压下量10-20mm,终轧温度860℃,acc辊速0.8m/s连续冷却3次,最终返红温度550℃,板厚350mm。下线后堆冷48h,堆冷温度405℃。钢锭拆垛后转外机炉正火,正火保温温度860℃,保温系数2.2min/mm,正火出钢后水冷300s,返红580℃,正火池水温24℃;水冷结束后立即集中堆垛缓冷,缓冷温度485℃。
41.实施例2
42.400mm厚s355nl心部细晶粒钢包含如下质量百分比的化学成分单位(wt%):c:0.08、si:0.30、mn:1.63、p:0.008、s:0.001、nb:0.037、ni:0.21、cu:0.21、als:0.042,其它为fe和残留元素;
43.采用49t定厚调宽水冷模铸锭,铸锭规格1050*2200*2800mm。第一阶段开轧温度1050℃,轧机工作辊转速20r/min,每道次压下量70mm,轧制8道次至锭厚490mm时快速进入acc降温冷却,表面返红温度900℃。二阶段轧制压下量10-20mm,终轧温度880℃,acc辊速0.8m/s连续冷却3次,最终返红温度580℃,板厚400mm。下线后堆冷48h,堆冷温度440℃。钢锭拆垛后转外机炉正火,正火保温温度860℃,保温系数2.2min/mm,正火出钢后水冷380s,返红560℃,正火池水温25℃;水冷结束后立即集中堆垛缓冷,缓冷温度480℃。
44.各实施例的机械力学性能按en10025-3标准平均值具体见下表。
[0045][0046]
各实施例的金相组织检测见下图。
[0047]
350mm和400mm厚1/4位置和心部(1/2位置)检测金相组织均为:铁素体+珠光体,其1/4位置晶粒度8~9级,心部位置晶粒度7~8级。
[0048]
综上所述,采用本技术生产方法生产的350~400mm厚度s355nl钢板,心部晶粒度达7~8级,较常规方法生产同类钢板心部晶粒度提升2级以上,满足高端客户对特厚板心部细晶钢的需求。
[0049]
以上所描述的仅为本发明的较佳实施例,上述具体实施例不是对本发明的限制,凡本领域的普通技术人员根据以上描述所做的润饰、修改或等同替换,均属于本发明的保护范围。