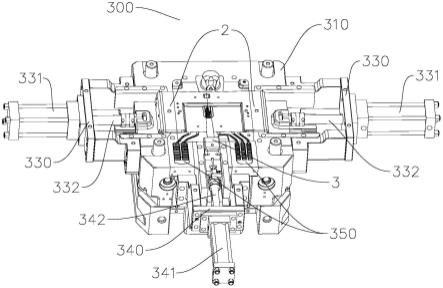
1.本实用新型涉及在压铸模具的领域,尤其是涉及一种生产带有电热管的铝铸件的压铸模具。
背景技术:2.压铸模具是铸造金属零部件的一种工具,一种在专用的压铸模锻机上完成压铸工艺的工具。压铸件所采用的合金主要是有色合金,至于黑色金属(钢、铁等)由于模具材料等问题,较少使用。而有色合金压铸件中又以铝合金使用较广泛,锌合金次之。
3.如图1-2所示为一种铝铸件100,该铝铸件100内设有电热管110,电热管110两端设有导电脚111,常规的模具无法顺利地生产出铝铸件100,需要工程师设计出一套能够生产该铝铸件100的压铸模具。
技术实现要素:4.本实用新型所要解决的技术问题是提供一种生产带有电热管的铝铸件的压铸模具,电热管两端插入定位套的定位孔内,导电脚被支撑杆向上托起,于是电热管位置被限定住了,而下模组对铝铸件成型并实现脱模。
5.本实用新型解决上述技术问题所采用的技术方案为:一种生产带有电热管的铝铸件的压铸模具,包括上模组和下模组,所述的上模组设有上模芯和上溢料板;所述的下模组设有下模板和推板,所述的下模板设有下溢料板、下模芯、前滑块、以及两个位于下模板两侧的侧滑块;所述的下模芯固定设有两个定位套,所述的定位套设有定位孔,所述的推板设有顶杆和支撑杆,所述的支撑杆的端部穿至定位孔内;所述的前滑块设有成型杆;所述的侧滑块设有镶块组,所述的镶块组包括上镶块、下镶块、侧镶块。
6.本实用新型的优点在于结构简单,设计合理,制造方便,可以顺利地成型出铝铸件并且实现脱模。两个定位套固定设置在下模芯处,先把电热管两端插入定位套的定位孔内,此时电热管位置被限定住了,支撑杆起到向上托起导电脚的作用;然后两个侧滑块相互合拢,前滑块朝电热管靠近,成型杆插入电热管的中心孔内;接下来上模组和下模组合拢,上模芯和下模芯之间留有模腔,铝铸件在模腔内成型,成型杆用来成型铝铸件中部的导热孔,镶块组的上镶块、下镶块、侧镶块用来成型铝铸件的侧面;高温的铝水流到模腔内,模腔内充满后,多余的铝水流到上溢料板与下溢料板之间而形成料头,这样可以使模腔内成型的铝铸件结实饱满,不易出现缺料的现象;开模后,侧滑块和前滑块移动而脱离铝铸件,推板带动顶杆、支撑杆移动,于是铝铸件被顶出下模板而实现脱模。
7.作为本实用新型进一步改进:所述的前滑块固定设有前成型块,所述的前成型块设有安装孔,所述的成型杆一端固定设在安装孔内。前成型块既起到成型的作用,也起到固定成型杆的作用。
8.作为本实用新型进一步改进:所述的成型杆设有水道,所述的前滑块设有外水管,所述的外水管插入水道内。分模后,外水管用来给成型杆降温,成型杆降温后体积缩小而有
利于抽芯。
9.作为本实用新型进一步改进:所述的外水管内设有内水管,所述的内水管与外水管间隔着出水槽。冷却水流到顺序依次是:内水管、水道、出水槽、外水管,这样就能对成型杆进行降温了。
10.作为本实用新型进一步改进:所述的上镶块和下镶块进行上下叠放,所述的侧镶块贴在上镶块和下镶块的侧面。镶块组结构复杂,加工困难,其拆分成上镶块、下镶块、侧镶块这三个零件后,加工变得简单,后期维护时可以对单个零件进行保养或者更换,维护方便、成本低。
11.作为本实用新型进一步改进:所述的侧滑块固定设有侧成型块,所述的侧成型块设有连接孔,所述的镶块组安装在连接孔内。侧成型块既起到成型的作用,也起到固定镶块组的作用。
12.作为本实用新型进一步改进:所述的上镶块设有上镶孔,所述的下镶块设有下镶孔,所述的侧镶块设有侧镶孔;所述的侧成型块设有第一固定孔和第二固定孔,所述的第一固定孔设有贯穿上镶孔和下镶孔的螺钉,所述的第二固定孔也设有螺钉且该螺钉贯穿侧镶孔。于是镶块组先通过三个螺钉与侧成型块固定连接,然后侧成型块再通过螺栓与侧滑块固定连接。
13.作为本实用新型进一步改进:所述的下模板设有前支架和两个侧支架,所述的前支架设有前气缸,所述的前气缸的活塞杆与前滑块连接,所述的侧支架设有侧气缸,所述的侧气缸的活塞杆与侧滑块连接。前气缸的活塞杆可以带动前滑块移动,侧气缸的活塞杆可以带动侧滑块移动。
14.作为本实用新型进一步改进:所述的上溢料板设有多个溢料凸块,所述的下溢料板设有多个溢料槽,所述的溢料凸块与溢料槽一一配对。高温铝水充满到模腔内再流到溢料槽内,而溢料凸块使溢料槽内的铝水体积较小,于是铝水凝固后形成厚度较薄的料头,便于工人切除料头。
附图说明
15.图1为铝铸件的分解示意图;
16.图2为铝铸件铸造成型后的示意图;
17.图3为本实用新型的分解示意图;
18.图4为下模组的分解示意图;
19.图5为侧滑块的分解示意图;
20.图6为侧滑块的剖面示意图;
21.图7为前滑块的分解示意图;
22.图8为前滑块的剖面示意图;
23.图9为下模组中部分零件的示意图;
24.图10为下模组的示意图;
25.图11为本实用新型的示意图。
具体实施方式
26.为了使本实用新型的目的、技术方案及优点更加清楚明白,以下结合附图及实施例,对本实用新型进行进一步详细说明。应当理解,此处所描述的具体实施例仅用以解释本实用新型,并不用于限定本实用新型。
27.如图1-11所示:一种生产带有电热管的铝铸件的压铸模具,包括上模组200和下模组300,上模组200设有上模芯220和上溢料板210;下模组300设有下模板310和推板320,下模板310设有下溢料板350、下模芯360、前滑块3、以及两个位于下模板310两侧的侧滑块2;下模芯360固定设有两个定位套1,定位套1设有定位孔11,推板320设有顶杆322和支撑杆321,支撑杆321的端部穿至定位孔11内;前滑块3设有成型杆9;侧滑块2设有镶块组,镶块组包括上镶块5、下镶块6、侧镶块7。下模芯360设有两个嵌孔361,定位套1固定在嵌孔361内。
28.前滑块3固定设有前成型块31,前成型块31设有安装孔32,成型杆9一端固定设在安装孔32内。先把成型杆9一端装入安装孔32内,然后前成型块31通过螺栓与前滑块3固定连接,如图7所示成型杆9一端设有凸台,于是安装孔32可以锁住该凸台,这样前滑块3、前成型块31、成型杆9三者固定连接在一起了。
29.成型杆9设有水道91,前滑块3设有外水管8,外水管8插入水道91内。外水管8的外周与水道91密封连接。成型杆9用来成型铝铸件100的导热孔101,且成型杆9具有锥度,便于成型杆9从导热孔101内抽出;但因为导热孔101较长,成型杆9抽芯过程中容易划伤导热孔101内壁,而插入水道91内的外水管8就给成型杆9迅速降温,成型杆9降温后外形缩小,那么缩小后的成型杆9外周与导热孔101内壁没有接触,就能顺利抽芯而不划伤导热孔101内壁。
30.外水管8内设有内水管81,内水管81与外水管8间隔着出水槽80。外部的冷却水通过两根管道分别与内水管81、外水管8接通,冷却水从内水管81进入到水道91而对成型杆降温,然后冷却水再从水槽80回流到外水管8,最后冷却水从外水管8流到外部的供水冷却装置,如此反复流动循环。内水管81凸出外水管8端部,所以内水管81更靠近成型杆9的端部,起到有效地降温。
31.上镶块5和下镶块6进行上下叠放,侧镶块7贴在上镶块5和下镶块6的侧面。上镶块5、下镶块6、侧镶块7共同对铝铸件100侧面成型。
32.侧滑块2固定设有侧成型块21,侧成型块21设有连接孔22,镶块组安装在连接孔22内。先把下镶块6装入连接孔22内,然后下镶块6上放置上镶块5,最后连接孔22侧面的空间装入侧镶块7,这样镶块组安装在连接孔22内了。
33.上镶块5设有上镶孔51,下镶块6设有下镶孔61,侧镶块7设有侧镶孔71;侧成型块21设有第一固定孔24和第二固定孔23,第一固定孔24设有贯穿上镶孔51和下镶孔61的螺钉4,第二固定孔23也设有螺钉4且该螺钉4贯穿侧镶孔71。如图5-6所示,镶块组安装到连接孔22后,两个螺钉4拧入第一固定孔24,并且该螺钉4贯穿上镶孔51、下镶孔61;一个螺钉4拧入第二固定孔23,并且该螺钉4贯穿侧镶孔71,于是镶块组就与侧成型块21固定连接了。
34.下模板310设有前支架340和两个侧支架330,前支架340设有前气缸341,前气缸341的活塞杆342与前滑块3连接,侧支架330设有侧气缸331,侧气缸331的活塞杆332与侧滑块2连接。前支架340和两个侧支架330都是通过螺栓固定到下模板310的,前支架340用来支撑前气缸341,侧支架330用来支撑侧气缸331。
35.上溢料板210设有多个溢料凸块211,下溢料板350设有多个溢料槽351,溢料凸块
211与溢料槽351一一配对。高温的铝水流到模腔内,模腔内充满后,多余的铝水流到溢料槽351内,这样可以使模腔内成型的铝铸件100结实饱满,不易出现缺料的现象。
36.以上所述仅为本实用新型的较佳实施例而已,并不用以限制本实用新型,凡在本实用新型的精神和原则之内所作的任何修改、等同替换和改进等,均应包含在本实用新型的保护范围之内。