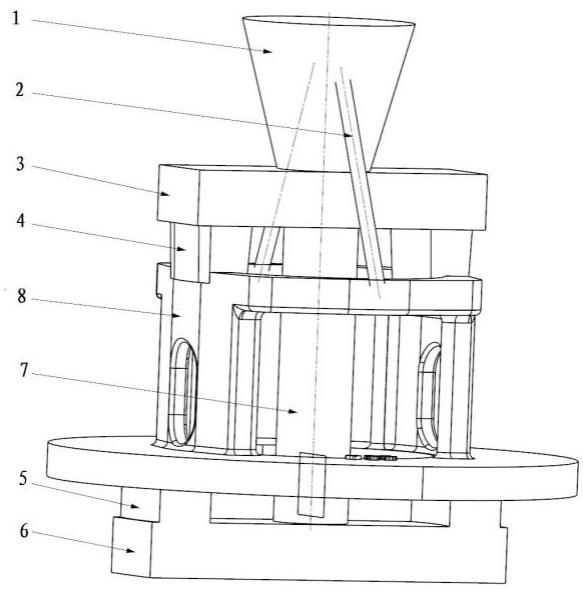
1.本实用新型涉及全硅溶胶精密铸造技术领域,尤其涉及一种支架件全硅溶胶精密铸造系统。
背景技术:2.支架是各个行业(诸如:石油、化工、太阳能等)用于连接的零部件,起到对各个零部件支撑的作用。其特点为安装边厚大,与中间部分壁厚相差较大,存在方槽、孔等铸造缺陷容易产生的结构;再则规格型号较多,每种型号其产品结构都存在差异;由于支架属于支撑件因此要求内部金相组织必须要致密,冶金质量要求(铸件内部质量)高,不得有疏松、气孔、夹渣、冷隔等铸造缺陷,否则,支架会出现裂纹而使整个设备不稳定,甚至有报废的风险。目前采用精密铸造工艺进行生产,对于常规的顶注式或底注式浇注系统而言,很难做到对铸件充分补缩且平稳充型避免气孔产生,在浇注过程中,合金液直接冲击铸件型腔内部,很容易使方槽、小径孔中跑火,使产品合格率下降。虽然铸件允许补焊,但是大大降低了生产效率且增加了生产成本。
技术实现要素:3.本实用新型目的是解决上述技术问题,提供一种支架件全硅溶胶精密铸造系统。
4.为了实现上述技术目的,达到上述的技术要求,本实用新型所采用的技术方案是:一种支架件全硅溶胶精密铸造系统,包括浇口杯,其特征在于:所述浇口杯底部设置有第一直浇道,所述第一直浇道底部通过第二直浇道连接有第三直浇道,所述第一直浇道底部两侧对称设置有第一内浇口,所述第三直浇道上对称设置有第二内浇口,所述浇口杯两侧对称设置有通气棒,所述通气棒与铸件相连。
5.优选的:所述第一直浇道、第三直浇道分别位于铸件两侧。
6.优选的:所述第二直浇道设置为圆柱体。
7.优选的:所述第二直浇道截面直径不小于40cm。
8.优选的:所述第一直浇道、第二直浇道、第三直浇道中心线位于同一平面上。
9.优选的:所述浇口杯设置为倒锥形。
10.与传统结构相比,本实用新型的有益效果:
11.1、本实用新型结构简单,设计合理,采用混合式(顶住+底注)浇注系统,使用混合直浇道,即上下两个长方体直浇道对铸件各个热节部位起到了有效的补缩作用,中间的圆柱体直浇道起到连接作用,充分保证了底部直浇道对底部热节部位的补缩,杜绝了铸件内部疏松缺陷的产生;在浇注时能有效的减少合金液对铸件型壳内部的直接冲击,实现了对合金液的合理分流,避免因为冲击力大而使铸件方槽部位出现跑火现象致使报废。
12.2、通过在铸件上方两侧设置排气棒,在保证充分补缩铸件的同时又合理的将气体排出,避免了平面位置气体难以逸出,提高了铸件的合格率。
13.3、本实用新型适用范围广,采用混合式浇注系统(顶住+底注)可适用于各种规格
的支架件,均能保证其表面以及内部质量,且铸件合格率高。
附图说明
14.图1为本实用新型结构示意图;
15.在图中:1.浇口杯,2.通气棒,3.第一直浇道,4.第一内浇口,5.第二内浇口,6.第三直浇道,7.第二直浇道,8.铸件。
具体实施方式
16.下面对本实用新型作进一步说明。
17.参照附图,一种支架件全硅溶胶精密铸造系统,包括浇口杯1,其特征在于:所述浇口杯1底部设置有第一直浇道3,所述第一直浇道3底部通过第二直浇道7连接有第三直浇道6,所述第一直浇道3底部两侧对称设置有第一内浇口4,所述第三直浇道6上对称设置有第二内浇口5,所述浇口杯1两侧对称设置有通气棒2,所述通气棒2与铸件8相连。
18.本优选实施例中,所述第一直浇道3、第三直浇道6分别位于铸件8的顶部、底部,第二直浇道7位于铸件8中间。
19.本优选实施例中,所述第二直浇道7设置为圆柱体。
20.本优选实施例中,所述第二直浇道7截面直径不小于40cm。
21.本优选实施例中,所述第一直浇道3、第二直浇道7、第三直浇道6中心线位于同一平面上。
22.本优选实施例中,所述浇口杯1设置为倒锥形。
23.具体实施时,为减轻整个设备的重量,在支架中间部位设计了方槽,但对于全硅溶胶精密铸造工艺有一定的制造难度,即合金液浇注后使其分流,致使底部或顶部的热节部位因难于补缩而产生疏松缺陷。为此设计混合式(顶住+底注)浇注系统,直浇道7为圆柱体型,为合金液进入型腔提供足够的充型压力,为铸件8底部热节点提供了充分的补缩。直浇道7设计时采用了s内浇口:s直浇道:s横浇道=1: 1.8:1.2;(h直浇道+h内浇口)/d内浇口宽度=1.5;经过计算,其截面直径不得小于40cm,使其大小达到最佳数据比例。与传统的浇注系统相比较,能够很好地减缓合金液冲刷铸件型腔,使其平稳的充型,避免了冲刷型腔导致的面层脱落,铸件尺寸变形,铸件方槽处跑火;产品标识模糊不清等问题,铸件的表面外观质量有较大提升,对铸件的合格率和成本率也有很大提高。
24.两个第一内浇口4与第一直浇道3相连,在浇注过程中,使合金液合理分流,对容易产生冶金缺陷的位置起到了有效的补缩,内浇道按照一定的角度设计,拔模角度为10
°
~15
°
,既提供了必要的充型压力,也为后续的清理提供了方便,提高工人的工作效率,且不会伤及铸件本体。
25.两个第二内浇口5与直浇道6相连,在保证平稳分流的同时又保证了铸件8热节部位的补缩。
26.第二直浇道7连接第一直浇道3和第三直浇道6,保证了铸件各个热节部位的补缩;
27.两个排气棒2与铸件8相连,避免了因为浇注速度过快而引起型腔内气体难以排出的问题,提高铸件的质量。
28.本实用新型通过铸件内部合金液的分流,保证铸件各个热节部位的充分补缩,且
减少合金液直接对型壳内部的冲刷,对容易产生冶金缺陷的位置起到了控制作用。两侧的排气棒位于铸件上可将气体排出,提高了铸件的合格率,适用于绝大部分不同规格支架的全硅溶胶精密铸造生产工艺,能充分保证铸件的外部和内部质量,具有较高的经济效益和长远的应用前景。
29.本实用新型的上述实施例,仅仅是清楚地说明本实用新型所做的举例,但不用来限制本实用新型的保护范围,所有等同的技术方案也属于本实用新型的范畴,本实用新型的专利保护范围应由各项权利要求限定。
技术特征:1.一种支架件全硅溶胶精密铸造系统,包括浇口杯(1),其特征在于:所述浇口杯(1)底部设置有第一直浇道(3),所述第一直浇道(3)底部通过第二直浇道(7)连接有第三直浇道(6),所述第一直浇道(3)底部两侧对称设置有第一内浇口(4),所述第三直浇道(6)上对称设置有第二内浇口(5),所述浇口杯(1)两侧对称设置有通气棒(2),所述通气棒(2)与铸件(8)相连。2.根据权利要求1所述的一种支架件全硅溶胶精密铸造系统,其特征在于:所述第一直浇道(3)、第三直浇道(6)分别位于铸件(8)两侧。3.根据权利要求1所述的一种支架件全硅溶胶精密铸造系统,其特征在于:所述第二直浇道(7)设置为圆柱体。4.根据权利要求3所述的一种支架件全硅溶胶精密铸造系统,其特征在于:所述第二直浇道(7)截面直径不小于40cm。5.根据权利要求1所述的一种支架件全硅溶胶精密铸造系统,其特征在于:所述第一直浇道(3)、第二直浇道(7)、第三直浇道(6)中心线位于同一平面上。6.根据权利要求1所述的一种支架件全硅溶胶精密铸造系统,其特征在于:所述浇口杯(1)设置为倒锥形。
技术总结本实用新型公开了一种支架件全硅溶胶精密铸造系统,包括浇口杯,所述浇口杯底部设置有第一直浇道,所述第一直浇道底部通过第二直浇道连接有第三直浇道,所述第一直浇道底部两侧对称设置有第一内浇口,所述第三直浇道上对称设置有第二内浇口,所述浇口杯两侧对称设置有通气棒,所述通气棒与铸件相连。本实用新型结构简单,采用混合式浇注系统,使用混合直浇道,实现了对合金液的合理分流,充分保证了底部直浇道对底部热节部位的补缩,杜绝了铸件内部疏松缺陷的产生,适用于各种规格的支架件,均能保证其表面以及内部质量,且铸件合格率高。高。高。
技术研发人员:贾珮 王道红 侯桂臣 谢君 周亦胄 李志海
受保护的技术使用者:江苏金研新材料科技有限公司
技术研发日:2022.12.05
技术公布日:2023/3/28