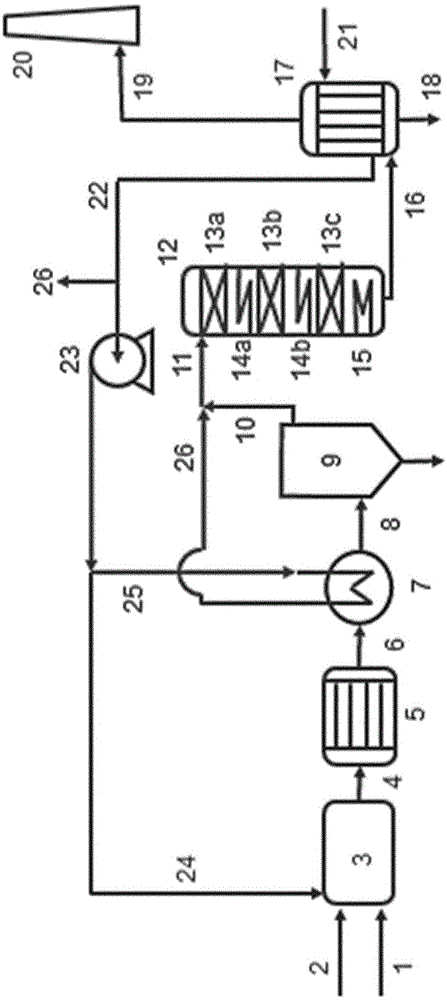
更具体地,本发明提供了由包含含硫化合物和溶解的金属如碱金属的进料流生产三氧化硫的方法,所述方法包括以下步骤:在富含o2的流的存在下焚烧,由此将进料流中的含硫化合物转化为so2,在废热锅炉中将气体冷却,从而以高压蒸汽的形式回收热量,其中废热锅炉中负荷的至少50%被气体和颗粒辐射传递,在稀释空气加热器中将离开废热锅炉的工艺气体进一步冷却,向工艺气体中添加稀释空气,以便为so2转化器中的so2氧化成so3提供足够的氧气,以及将稀释后的工艺气体进料至so2转化器,该so2转化器由多个催化剂层组成,在催化剂层之间安装有热交换器。本发明还涉及一种用于通过上述方法生产三氧化硫的设备,所述设备包括焚化炉、废热锅炉、稀释空气加热器和除尘吸收器。具体地,为了用于硫酸生产,该设备还包括so2转化器和硫酸冷凝器。进料流可以是来自烷基化工艺的废硫酸,在该烷基化工艺中硫酸已经作为用于生产烷基化物(即燃料添加剂)的催化剂。在烷基化工艺中,硫酸被以下物质污染:水和酸溶性油以及在某种程度上的来自工厂设备的腐蚀产物(fe、cr、ni离子)和碱性(na、k)离子的侵入,例如,来自烷基化物纯化设备。该酸从烷基化工艺中排出,在单独的硫酸设备中再生成浓硫酸并返回烷基化工艺。进料流的另一个实例是来自焦炉煤气清洁工艺的产物,其中焦炉煤气中存在的h2s和hcn被吸收到碱性水溶液中并被转化成元素硫(s)以及scn-、s2o32-和so42-的盐。通常,相应的阳离子是nh4+或na+,这取决于碱度是如何控制的,例如,是通过nh3还是naoh。这种焦炉煤气清洁工艺的商品名称是例如hpf、pds、perox和stretford。这些产品的质量和价值低,并且可以被转化成浓硫酸,以提高硫的质量和价值。在下文中,参考附图更详细地描述了本发明,其中图1是用于将进料流转化成浓硫酸的已知工艺布局,图2显示了根据本发明使用的具有新型辐射式锅炉的硫酸工艺,以及图3至6显示了根据本发明使用的不同的替代辐射式热交换器。用于将这些进料转化成浓硫酸的常用工艺布局如图1所示。在第一步中,将包含硫化合物和溶解的金属和碱金属的进料流1进料到在900-1100℃下操作的炉3中。在该炉中,根据进料的确切组成,发生以下反应:h2so4->so2+0.5o2+h2o酸溶性油+o2->co2+h2o+so2s+o2->so2scn-+2o2->so2+co2+0.5n2s2o32-+0.5o2->2so2so42-->so2+o2ch4+2o2->co2+2h2o为了维持炉内的高温,经常有必要提供支持燃料2以确保进料的足够高的热值。这种载体燃料可以是ch4、c2h6和其他烃基燃料,但也可以使用h2s、co和h2。为了为上述氧化反应提供足够的o2,将富o2流24引入到炉中。大多数情况下,使用大气空气作为离开设备中的硫酸冷凝器17的热空气22。在一些应用中,使用富集的o2(即>21体积%)可能是有益的,但通常空气富集的成本高于较高o2浓度所带来的益处。在废热锅炉5中,将离开炉的工艺气体4冷却到450-600℃,从而以高压蒸汽的形式回收热量。蒸汽压力在20-85巴表压范围内。用于这些应用的最常见类型的废热锅炉是所谓的火管锅炉,其中工艺气体流过多个平行的水平管。气体速度很高(通常为25-50米/秒),以提供高的对流传热系数,以有效地将热量传递到管的壳侧上的冷却介质。冷却介质通常是高压水,并且通过相转移(即沸腾)吸收热量。这种设计是公知的并且在工业中使用。另一种类型的废热锅炉是所谓的水管锅炉,其中工艺气体在管的壳侧流动并且水/蒸汽在管的内部流动。水管锅炉也依赖于对流传热,因此气体速度必须很高并且管之间的距离必须很小。然后在稀释空气加热器7中将离开废热锅炉的工艺气体6进一步冷却至375-450℃。如果不需要空气稀释,则可以安装蒸汽过热器,或者可以将上游的废热锅炉5设计成将工艺气体冷却至375-400℃。为了保护下游的设备,在静电除尘器9中从工艺气体中除去粉尘。也可以使用其他类型的除尘设备,例如陶瓷过滤器。在除尘后,将热稀释空气26添加到工艺气体10中,以便为so2催化氧化成so3提供足够的氧气。该空气添加位置确保使炉3、废热锅炉5、稀释空气加热器7和静电除尘器9的尺寸最小化。然后,经稀释的工艺气体11在375-420℃进入so2转化器12。转化器由多个催化剂层13组成,在催化剂层之间安装有热交换器14。so2到so3的转化是放热反应,并且为了使总so2转化率最大化,通常的做法是使用多个催化剂层,每个连续的层在更低温度下操作,以确保可能的最高转化效率。催化剂层的数目为1至4,其中3是这些应用中最常见的数目。催化剂层之间的热交换器14被设计成在每个催化剂层13的入口处提供最佳的工艺气体温度。作为冷却介质,通常使用饱和的和/或过热的蒸汽,但也可以使用空气、熔盐或热的加压水(锅炉水)。在最终催化剂层13c之后,在工艺气体离开so2转化器12之前,将转化的工艺气体在锅炉15中冷却至250-310℃。在此温度范围内,so3开始在气相中与h2o反应以形成h2so4蒸气。该反应在硫酸冷凝器17中进行至完全,在该硫酸冷凝器17中将工艺气体冷却至60-200℃。大部分硫酸蒸汽冷凝,将液态的浓h2so418从冷凝器的底部排出,而清洁的气体19从冷凝器的顶部离开。根据环境法规,清洁的气体可能需要进一步的清洁步骤,然后通过烟囱20排放到大气中。将h2so4产物18冷却至约40℃并送至界区以便储存或直接使用。h2so4浓度为93-98.5%w/w,取决于工艺气体16中的h2o/so3比率。用于硫酸冷凝的冷却介质21是空气,并且离开冷凝器的热空气22可以作为预热的燃烧空气24和热稀释空气25再循环回到硫酸设备的前端。需要热空气鼓风机23使热空气再循环。可以将未用于这些目的的任何热空气26与经清洁的气体19混合以提供干燥的清洁气体(并因此提供干燥的烟囱),或者可以将热量用于例如锅炉给水预热或其他加热/干燥目的。在硫酸冷凝器17中,使用玻璃管将工艺气体与冷却空气分离,因为金属不能承受热的浓硫酸的腐蚀性质。所谓的干气硫酸技术有不同的布局。炉和废热锅炉与上述的且如图1所示的湿气技术中使用的相似,但在废热锅炉后,将工艺气体骤冷至50-60℃以从工艺气体中洗去粉尘并除去水。然后将冷的干燥的含so2的工艺气体再加热,将so2催化氧化成so3,并在专用吸收塔中将形成的so3吸收到浓硫酸中。只要形成粉尘的金属和碱金属的浓度足够低,湿法和干法都能够转化上述进料。如果超过对这些杂质的耐受性,则两种方法都会受到粉尘形成和沉积的影响。由于粘性粉尘颗粒的形成取决于进料中存在的不同金属之间的相互作用以及工艺气体组成,因此难以量化对进料中金属和碱金属浓度的耐受性。na和k是粘性颗粒的形成的主要原因。随着na和k浓度的增加,粘性颗粒的形成增加。这可以通过例如fe、al和mg的存在得到一定的补偿,fe、al和mg在某种程度上可以“干燥”颗粒并降低它们的粘性。此外,工艺气体中so3的存在将增强粘性颗粒的形成。此外,火管废热锅炉中的管的直径是重要的,因为具有较大直径的管比具有较小直径的管更耐结垢和堵塞。一般规则是,对于来自烷基化设备的废酸,低于25-50重量ppm的na和k的浓度提供了废热锅炉的无故障操作。在炉3中,进料中溶解的金属和碱金属将形成固态或液态的氧化物和/或硫酸盐。颗粒的温度和化学性质将决定颗粒为液体的程度。这些颗粒将与工艺气体4一起从炉中带出。业内公知的是,高浓度的na和k会导致硫酸盐(例如na2so4/k2so4,但还有nahso4/khso4和na2s2o7/k2s2o7)的形成,其在高炉温下会至少部分液化。硫酸盐还可以与其他固体化合物结合,从而形成熔融温度不同于纯态硫酸盐熔点的混合物。所谓的共晶混合物(其中混合物的熔融温度低于纯态组分的熔融温度)的实例是na3fe(so4)3、nafe(so4)2、k3fe(so4)3和kfe(so4)2,其熔融温度在600-700℃的范围内,而na2so4的熔融温度为885℃。当这些“粘性”颗粒与废热锅炉5的冷表面接触时,颗粒将粘附在表面上并迅速固化,形成固体沉积层。沉积层的厚度随着时间而增长,并且最终该层将变得如此厚,以至于阻碍了工艺气体流过废热锅炉管(在火管锅炉中)或在废热锅炉管之间(在水管锅炉中)流动,其阻碍程度使得不再可能操作该设备,因此必须关闭设备以移除这些沉积物。对于非常干净的进料,这种关闭之间的操作时间可以超过一年,但对于具有非常高浓度的特别是碱金属的进料,管可以在不到24小时的操作后堵塞。在某种程度上,可以通过向进料流中添加“防粘”化合物(例如mgo或al2(so4)3)和/或进行废热锅炉的某种在线清洁来延长关闭之间的时间。这样的系统可以是例如吹灰器、空气喷射器、机械清洁和声波喇叭。由于具有小直径的长管(火管锅炉)的废热锅炉的机械布局,这些清洁系统的有效性不好。对于管之间具有小距离的管束(水管锅炉),通过将水管锅炉分成管束的更多部分,并在部分之间安装清洁系统,可以提高这些清洁系统的有效性。对于具有非常高浓度的碱金属的进料,还可以通过进行工艺气体的水骤冷从大约1000℃直接降至30-60℃来牺牲热回收。在该过程中,粘性粉尘溶解在水中并与废水一起取出,但该过程的能源效率非常低,耗水量大,且废水量大。为了具有用于处理上述困难的进料流而且具有高的热回收率的工艺,建议使用不同的热交换器。这种热交换器必须能够冷却工艺气体并结合对粘性粉尘沉积的高抵抗力。这种热交换器可以是辐射式冷却器。一种很少使用的设计基于两个同心的圆柱形管道,其中含有粘性粉尘的热工艺气体在内部管道中流动,而冷却剂在两个管道之间的环形空间中流动。与工艺气体流动方向相比,冷却剂的流动方向可以是逆流或并流。冷却剂通常是热空气,其在高于热工艺气体中的硫酸露点温度的温度下提供。内部管道的直径很大(>500mm),因此不可能堵塞。这种辐射冷却器的缺点是传热能力有限:由于管道的高金属温度,辐射传热速率降低。此外,冷却空气侧的对流传热系数相对较低,并且热冷却空气的利用需要额外的热交换器以将热量转换成例如在加工工业中更可用的蒸汽。高金属温度需要高级钢,这是昂贵的。对于本申请,推荐使用替代的辐射式热交换器。不同的布局如图3至6所示。新的辐射式锅炉的硫酸工艺如图2所示。只有废热锅炉5已被改变,而其余的工艺布局保持不变。这种替代的辐射式热交换器是所谓的膜壁结构,其中壁构成冷却表面。这确保了传热面积最大化,同时确保锅炉没有冷点,在该冷点硫酸会冷凝并导致腐蚀。辐射式废热锅炉布局的一个实例如图3所示。来自炉4的热工艺气体以900-1100℃的温度进入废热锅炉5。工艺气体包含so2、co2、h2o、n2、o2和少量的so3、nox和由通常为fe、na、k、cr和ni的氧化物/硫酸盐组成的粉尘颗粒。当工艺气体流通过废热锅炉时,来自工艺气体的热量通过锅炉壁传递到锅炉水中,从而形成蒸汽。冷却的工艺气体通过底部出口6离开废热锅炉。该壁由多个垂直管40组成,每个垂直管40通过金属板/条41彼此分开,金属板/条41完全焊接到管上,以形成气密结构。水/蒸汽在管内流动并冷却管壁和金属板,但同时确保金属表面的最低温度。对于这些应用,这是非常有用的,因为它将防止硫酸蒸气冷凝,否则会导致金属腐蚀。将锅炉给水通过底部歧管(31)供给到所有管道,底部歧管(31)接收来自位于热交换器顶部上方一定距离处的蒸汽鼓的水。升高的位置是必要的,以确保水和蒸汽均通过自然循环流动。如果使用强制循环,则不需要将蒸汽鼓升高到废热锅炉上方。离开废热锅炉顶部的管道的水/蒸汽被收集在顶部歧管32中,然后被送到相同的蒸汽鼓以进行水/蒸汽分离。由于需要控制工艺气体出口温度6以使下游设备最佳地运行,因此必须能够使一部分热工艺气体从长的冷却路径绕过并提供低工艺气体冷却程度的短路径。在图3中,这通过具有主通道气门34和旁路气门33来实现,两者的操作均由位于锅炉下游的温度控制器来控制。当设备在减小的负载下运行时,旁路气门也是控制出口温度的必要条件,即,对于该操作,安装的冷却表面大于所需的冷却表面。此外,通常的做法是增加额外的传热面积,使得即使在热交换表面的部分上存在沉积物,并因此阻碍从工艺气体到冷却表面的传热,锅炉也可以在设计负荷下良好地运行。由于长的壁间距离,实际上不可能积累如此厚的沉积层,使得流动限制变得如此之高以至于由于压降限制而必须关闭设备。但是,一些沉积物会聚集在锅炉壁上,从而阻碍传热。这些沉积物可以通过如上所述的用于水管和火管锅炉的清洁系统除去。膜壁锅炉的优点是,所有传热表面都暴露在外(即,没有管束遮蔽或长管,在这些位置处清洁系统的能力很快地消失),因此清洁系统将在系统和壁之间具有不间断的路径,从而确保清洁系统的最大效率。在图3中,与工艺气体入口4相比,热旁路33位于略微升高的位置。这是为了保护旁路气门免受来自锅炉上游的炉膛空间的任何直接辐射,并将工艺气体温度降低100-200℃,以保护气门的未冷却表面免受过高温度的影响。在图3中,锅炉被设计为具有主通道和旁路气门两者。原则上锅炉只能使用单个气门(在主通道上或旁路上)操作,但锅炉中的压降非常低(<5mbar),因此,仅使用一个气门将很难在冷却的工艺气体和热的旁路工艺气体之间的分布方面产生大的变化。使用两个气门,原则上可以将分布控制为0-100%流过旁路气门。图4示出了锅炉布局,其中旁路气门33和主通道气门34位于锅炉外部。通过该布局,工艺气体温度控制与图3中描述的一样好。该布局的优点是锅炉中管的结构更简单,因为管不需要弯曲以便为气门和气门轴腾出空间。该设计的缺点可能是,热管道和旁路气门正在经历来自炉的高温,并且可能需要使用特殊的建筑材料和/或导致材料的寿命缩短。为了减少规划面积,废热锅炉由两个垂直的方形管道组成,其中工艺气体向上流动并在锅炉顶部转向。然后它向下流动并在锅炉6的底部离开。在图5中,锅炉出口位于锅炉的顶部,但是其他布局如图4所示。该布局的优点是更加小的规划面积和减小的管道长度,条件是下游设备位于更高的高度,例如具有多个催化剂层和相应的床间热交换器的催化转化器12的入口。这种布局的缺点是结构的高度,这需要甚至更高位置的蒸汽鼓,以便提供锅炉水进入和离开锅炉的自然循环。在图6中,示出了废热锅炉的第四布局,其适用于需要将工艺气体冷却至低于辐射传热的最佳温度的温度的情况。公知的是,通过辐射的传热在高温下最有效(传热与温度的四次方成比例),因此对锅炉出口处的温度存在实际的下限。该温度为500-600℃,如果需要进一步冷却,则必须使用对流传热,例如通过在锅炉的最冷部分安装管束。这些管之间的距离将类似于普通火管锅炉和水管锅炉中使用的距离。管可以是水平的或垂直的。一种广泛用于例如大型发电厂锅炉的替代方案是强制循环,其中水和蒸汽通过管道的流动由专用泵控制。在下面的实施例中进一步说明本发明。实施例1在常用的火管和水管锅炉设计中,传热机制主要是对流。为了设计一种高效且紧凑的对流式热交换器,工艺气体速度必须尽可能高,因此管(水管锅炉中)之间的距离和管直径(火管锅炉中)必须尽可能小。这种设计的缺点是对堵塞的耐受性低:从金属表面到相对的金属表面的距离短,因此相对薄的沉积层可能导致流动的高度受限。借助于辐射的传热距离显著高于借助于对流的传热距离,因此可以将辐射式热交换器设计成在相对的表面之间具有较大的距离。例如,将火管锅炉设计为具有例如多个3”管(内径63mm),且将辐射热交换器设计为在相对的金属表面之间具有例如1800mm的开口管道。下面的表1显示了用于处理来自烷基化工艺的约4吨/小时的废硫酸的火管废热锅炉设计和根据本发明的膜壁锅炉设计之间的比较。火管废热锅炉是双回程锅炉,其中在第一回程中具有3”管以增加对堵塞的抵抗力,在第二回程中具有2”管以提高传热速率。膜式锅炉为正方形管道结构,如图3所示,壁侧宽度为1800mm。将工艺气体从1000℃冷却至550℃。表1显示了双回程火管废热锅炉与膜壁废热锅炉的相对比较。对废硫酸再生设备(4吨/小时),评价了废热锅炉,其中工艺气体在废热锅炉中从1000℃冷却至550℃。表1双回程火管废热锅炉膜壁废热锅炉冷却的换热面积100140工艺气体侧的压降10020相对的金属壁之间的距离1002500成本100<100可见,在两个废热锅炉之间存在一些主要差异。首先,通过对流进行的传热比通过辐射进行的传热更有效,因此膜壁废热锅炉需要更高的热交换面积来去除相同的热量。由于膜壁热交换器中的工艺气体速度相当低(<5米/秒),所以压降将显著更低,从而降低了工艺气体鼓风机的运行成本。最显著的是相邻壁之间的距离差异,这意味着膜壁废热锅炉几乎不可能堵塞。即使在膜壁热交换器中安装更多的热交换面积,该结构也比火管锅炉的结构更便宜。这是因为膜壁的结构更简单,其中高压水/蒸汽被限制在小管中,而在火管锅炉中,高压水/蒸汽被限制在大的壳中。后者需要增加管板和压力壳的金属厚度。实施例2使用来自实施例1的废热锅炉尺寸,一些粗略的计算显示了膜壁结构的抗堵塞性的改进。为了计算,假设恒定的沉积层积累速率为1mm/天,即工艺气体粉尘具有高的堵塞潜力。下面的表2说明了沉积物积累对通过火管废热锅炉中的管和膜壁废热锅炉中的管道的流量和压降的影响。假设恒定的沉积层积累速率为1mm/天,即工艺气体粉尘表现出高的堵塞潜力。表2如上所示,火管锅炉在运行三周后基本上堵塞,而在膜壁废热锅炉上只看到非常小的影响。实施例3在下面示出了用于冷却来自所谓的废硫酸的焚烧的工艺气体的不同废热锅炉配置布局。更具体地,工艺气体流为5000nm3/h(在0℃和1atm下评估的m3/h),10vol%so2、25vol%h2o和10vol%co2。负责从工艺气体向冷却的金属表面的辐射热量的气体组分是so2、co2和h2o。火管锅炉中的传热主要是对流传热,因此气体速度必须很高。在该实施例中,火管锅炉中只有5-20%的传热来自气体辐射;80-95%的热量通过对流传热来传递。对流和辐射传热之间的这种分布对于火管锅炉和水管锅炉来说都是典型的。对于辐射式废热锅炉,传热分布是相反的,即80-95%的热量通过辐射传递,而只有5-20%的热量通过对流传热来传递。气体速度很低,降低了对流传热速率,同时允许足够的停留时间来辐射热量。表3单回程火管废热锅炉,3”管辐射式废热锅炉入口温度1000℃1000℃出口温度540℃535℃热交换面积31m235m2横截面积0.12m21.5m2气体方向上的长度3.67.0气体速度40000nm/h2500nm/h辐射分布5-20%80-95%当前第1页12