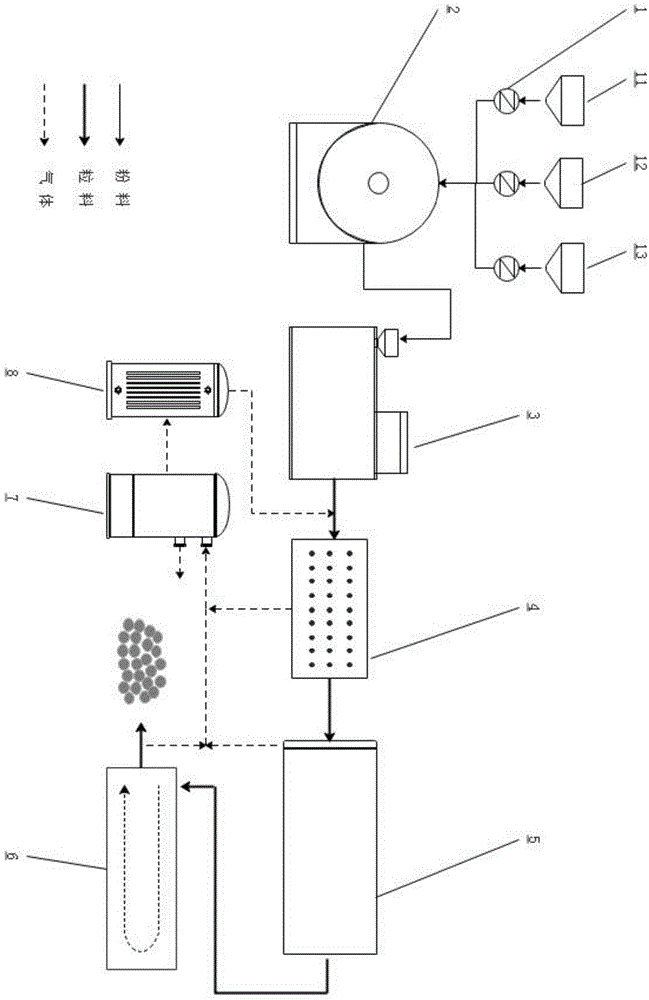
本发明涉及一种疏浚底泥制备轻质陶粒的装置及方法。
背景技术:
:近年来,河涌治理工作如火如荼,其中,河道的疏浚清淤是改善河道、湖泊等水体水质的常用技术。随着河湖治理工作的开展,疏浚清淤工程产生大量的底泥,疏浚底泥粒度细,含大量有机物、重金属污染物等,目前多以浓缩、填埋或焚烧的方式处理,造成大量土地占用和资源浪费,还容易产生对环境的二次污染。我国当前对此类底泥存在处理能力不足、技术相对落后、成本高等问题,大量污泥的无害化、资源化处理任务繁重,形势严峻。目前,疏浚底泥主要用做轻质建材、园林及农用填料等。污泥烧结陶粒技术是1998年首次由nakouzis.等提出,污泥陶粒具有质轻、比表面大、表面电位可调控等特点,是水环境处理中一种优质的生物滤料。但目前污泥陶粒的制备工艺普遍存在污泥掺量少、制备能耗高、效率低、工艺复杂、成本高等技术难题,应用过程还存在安全风险,对其研究多停留在实验室,实际应用较少。碱渣是纯碱生产过程中产生的废渣。据统计,每生产1吨纯碱会产生0.3~0.6吨碱渣,碱渣中含有大量重金属等有害物质,环境污染风险大,碱渣的处理一直是行业的难题。碱渣颗粒粒径小,主要含大量的cao、mgo、k2o等碱金属氧化物。目前,碱渣的综合利用主要集中在制备建筑材料和治理环境污染两方面。因此,随着河道治理工作的开展,以及固废治理与资源化的要求日趋提高,怎样以疏浚底泥、碱渣等固废为原料,以清洁的生产方式制备优质轻质陶粒,并形成工艺简单、效率高、制备成本低、陶粒强度高、性能好的制备方法和制备装置,是当前该领域亟待解决的问题。技术实现要素:为了克服现有技术存在的问题,本发明的目的在于提供一种疏浚底泥制备轻质陶粒的装置及方法,该装置特别适合于处理黑臭水体、河流、湖泊等清淤工程产生的疏浚底泥制备优质轻质陶粒。本发明所采取的技术方案是:一种疏浚底泥制备轻质陶粒的装置,包括定量给料机、混磨机、双辊造粒机、振动流化床干燥机、焙烧回转窑、滚筒式冷却机、尾气处理系统、余热回收系统;定量给料机的进料口分别与疏浚底泥料仓、碱渣料仓、粉煤灰料仓相连,定量给料机的出料口与混磨机的进料口相连;混磨机的出料口与双辊造粒机的进料口相连,双辊造粒机的出料口与振动流化床干燥机的进料口相连,振动流化床干燥机的出料口与焙烧回转窑的进料口相连,焙烧回转窑的出料口与滚筒式冷却机的进料口相连;振动流化床干燥机的出气口、焙烧回转窑的出气口、滚筒式冷却机的出气口分别与尾气处理系统的进气口相连;尾气处理系统的出气口与余热回收系统的进气口相连,余热回收系统的出气口与振动流化床干燥机的进气口相连。优选的,这种疏浚底泥制备轻质陶粒的装置中,混磨机的出料口与双辊造粒机的进料口之间设有螺旋输送机。优选的,这种疏浚底泥制备轻质陶粒的装置中,混磨机为润磨机。优选的,这种疏浚底泥制备轻质陶粒的装置中,焙烧回转窑的长径比为(11~15):1。优选的,这种疏浚底泥制备轻质陶粒的装置中,焙烧回转窑窑体与水平面的夹角为2°~6°;进一步优选的,焙烧回转窑窑体与水平面的夹角为3°~5°。优选的,这种疏浚底泥制备轻质陶粒的装置中,焙烧回转窑的转速为1r/min~3r/min;进一步优选的,焙烧回转窑的转速为1.5r/min~2r/min。优选的,这种疏浚底泥制备轻质陶粒的装置中,焙烧回转窑的窑头、窑尾均密封,窑头设有窑头罩和燃烧室,窑尾设置有烟气收集室,烟气收集室的出气口与尾气处理系统的进气口相连。一种疏浚底泥制备轻质陶粒的方法,是使用上述的装置制备,包括以下步骤:1)将疏浚底泥、碱渣、粉煤灰按质量比(40~65):(10~20):(15~35)配料,在混磨机中进行混磨,得到混合物料;2)将混合物料经双辊造粒机挤压成型,得到陶粒生料;3)将陶粒生料经振动流化床干燥机干燥,再在焙烧回转窑中预热,烧结,然后经滚筒式冷却机冷却,得到轻质陶粒。优选的,这种疏浚底泥制备轻质陶粒的方法步骤1)中,疏浚底泥、碱渣、粉煤灰的质量比为(50~65):(15~20):(15~35)。优选的,这种疏浚底泥制备轻质陶粒的方法步骤1)中,疏浚底泥为含水率15%~30%的干化疏浚底泥。优选的,这种疏浚底泥制备轻质陶粒的方法步骤1)中,疏浚底泥任选自处理黑臭水体、河流、湖泊清淤产生的疏浚底泥。优选的,这种疏浚底泥制备轻质陶粒的方法步骤1)中,碱渣为生产纯碱产生的废渣,具体而言,碱渣是纯碱生产过程中产生的澄清桶底流物。优选的,这种疏浚底泥制备轻质陶粒的方法步骤1)中,混合物料的含水率为8wt%~15wt%。优选的,这种疏浚底泥制备轻质陶粒的方法步骤1)中,混合物料的粒径为50μm~250μm。优选的,这种疏浚底泥制备轻质陶粒的方法步骤2)中,陶粒生料的粒径为6mm~10mm。优选的,这种疏浚底泥制备轻质陶粒的方法步骤3)中,干燥为在100℃~180℃下干燥30min~60min。优选的,这种疏浚底泥制备轻质陶粒的方法步骤3)中,预热为在300℃~450℃下加热10min~30min。优选的,这种疏浚底泥制备轻质陶粒的方法步骤3)中,烧结为在950℃~1200℃下烧结10min~25min。本发明的有益效果是:通过使用本发明的装置,以疏浚底泥、碱渣与粉煤灰为原料制备轻质陶粒,可以提高陶粒成型效率和质量,降低生产能耗和成本,能实现底泥的资源化利用。具体而言,本发明具有以下的优点:本发明以干化疏浚底泥、碱渣与粉煤灰为原料,可满足轻质陶粒烧制对原料的要求,陶粒强度高,表面呈微孔结构,并强化底泥中重金属污染物的固化;采用高效双辊造粒机和振动流化床干燥机有利于提高陶粒成型效率和质量。制备的陶粒密度小、强度高、生物亲和性好、无二次污染,可作为生物填料应用于水处理,实现底泥资源化处置。附图说明图1是疏浚底泥制备轻质陶粒的装置示意图。具体实施方式以下通过具体的实施例对本发明的内容作进一步详细的说明。实施例中所用的装置或原料如无特殊说明,均可从常规商业途径得到。实施例中所述的装置/设备之间的“相连”、“相连接”或“连接”,均是指通过管道/管线连接。实施例中所述的含水率指质量含量。附图1是疏浚底泥制备轻质陶粒的装置示意图。图1中,1-定量给料机,2-混磨机,3-双辊造粒机,4-振动流化床干燥机,5-焙烧回转窑,6-滚筒式冷却机,7-尾气处理系统,8-余热回收系统,11-疏浚底泥料仓,12-碱渣料仓,13-粉煤灰料仓。下面结合图1对本发明疏浚底泥制备轻质陶粒的装置实施例作进一步说明,该制备装置包括定量给料机1、混磨机2、双辊造粒机3、振动流化床干燥机4、焙烧回转窑5、滚筒式冷却机6、尾气处理系统7、余热回收系统8;定量给料机1的进料口分别与疏浚底泥料仓11、碱渣料仓12、粉煤灰料仓13相连,定量给料机1的出料口与混磨机2的进料口相连;混磨机2的出料口与双辊造粒机3的进料口相连,双辊造粒机3的出料口与振动流化床干燥机4的进料口相连,振动流化床干燥机4的出料口与焙烧回转窑5的进料口相连,焙烧回转窑5的出料口与滚筒式冷却机6的进料口相连;振动流化床干燥机4的出气口、焙烧回转窑5的出气口、滚筒式冷却机6的出气口分别与尾气处理系统7的进气口相连;尾气处理系统7的出气口与余热回收系统8的进气口相连,余热回收系统8的出气口与振动流化床干燥机4的进气口相连。混磨机2的出料口与双辊造粒机3的进料口之间设有螺旋输送机。混磨机优选为润磨机,润磨介质为耐磨钢球,硬度大,更适应较硬质的石英砂粉磨,润磨处理物料含水率为8%~15%,可免去混合物料干燥环节,缩短工艺流程,粉磨效率高、设备使用寿命长。双辊造粒机3的出料口与振动流化床干燥机4的进料口之间设有皮带输送机。振动流化床干燥机4热源为热空气。焙烧回转窑的窑头、窑尾均密封,窑头设有窑头罩和燃烧室,窑尾设置有烟气收集室,烟气收集室的出气口与尾气处理系统的进气口相连。尾气处理系统7中尾气余热由余热回收系统8收集。余热回收系统8与振动流化床干燥机风机入口(进气口)相连,为振动流化床干燥机提供热源。所用的尾气处理系统主要包括除尘装置和尾气喷淋装置,为常规装置。所用的余热回收系统主要为采用热交换处理的装置,如换热器,也为常规装置。疏浚底泥为含水率15%~30%的干化疏浚底泥,其粒度细、河沙含量大、有机质含量高,作为原料可制备多孔结构、比表面积大的轻质陶粒;碱渣是纯碱生产过程中产生的澄清桶底流物,含大量的cao、mgo、k2o等碱金属氧化物,可促进陶粒烧结过程中液相的生成,降低陶粒烧结能耗;粉煤灰粒度细,含大量的sio2、al2o3及微量金属元素,可提高陶粒强度;调控陶粒表面的电荷性能,提高陶粒生物亲和性。这些原料均为固体废弃物,廉价易得。以下通过具体的应用实施例,进一步说明应用本发明的制备装置制备轻质陶粒的方法。实施例1参照图1,将干化疏浚底泥、碱渣和粉煤灰分别通过定量给料机1按照65∶20∶15的质量比例配料,然后加入润磨机2中混磨均匀,得到含水率为10%、粒径为50~100μm的混合物料。混合物料通过螺旋输送机送入双辊造粒机3,经挤压成型得到直径为10mm的陶粒生料。所得陶粒生球经皮带输送机送入振动流化床干燥机4,在180℃条件下干燥30min;干燥后的陶粒由窑尾段进入焙烧回转窑5中。在预热段,于450℃条件下预热10min;在烧结段,于1200℃条件下烧结10min,得到的陶粒由窑头排出,进入滚筒式冷却机6进行冷却,得到陶粒成品。具体实施过程中,焙烧回转窑长径比为11:1,窑体与水平面夹角为3°,转速为1.5r/min,窑头、窑尾均密封,窑头设有窑头罩和燃烧室,窑尾设置有烟气收集室,烟气收集室与尾气处理系统7相连。振动流化床干燥机4和滚筒式冷却机6设置的出气口(排风口)均与尾气处理系统7连接,尾气余热由余热回收系统8收集,余热回收系统8与振动流化床干燥机4进气口(风口)相连,为振动流化床干燥机4提供热源。本实施例得到的疏浚底泥轻质陶粒的堆密度为628kg/m3,筒压为3.05mpa,吸水率为12.6%。本实施例得到的疏浚底泥轻质陶粒重金属浸出结果见表1。表1实施例1陶粒重金属浸出结果项目cdcrcunipbzn含量(mg/l)0.0010.0070.083nd0.010.065注:表1中nd表示notdetect,未检到。本实施例得到的疏浚底泥轻质陶粒完全符合《轻集料及其试验方法》(gb/t17431.1-2010)和《危险废物鉴别标准-浸出毒性鉴别》(gb5085.3-2007)的标准要求。实施例2参照图1,将干化疏浚底泥、碱渣和粉煤灰分别通过定量给料机1按照50∶15∶35的质量比例配料,然后加入润磨机2中混磨均匀,得到含水率为15%、粒径为100~250μm的混合物料。混合物料通过螺旋输送机送入双辊造粒机3,经挤压成型得到直径为8mm的陶粒生料。所得陶粒生球经皮带输送机送入振动流化床干燥机4,在100℃条件下干燥60min;干燥后的陶粒由窑尾段进入焙烧回转窑5中。在预热段,于350℃条件下预热30min;在烧结段,于950℃条件下烧结25min,得到的陶粒由窑头排出,进入滚筒式冷却机6进行冷却,得到陶粒成品。具体实施过程中,焙烧回转窑长径比为15:1,窑体与水平面夹角为5°,转速为2r/min,窑头、窑尾均密封,窑头设有窑头罩和燃烧室,窑尾设置有烟气收集室,烟气收集室与尾气处理系统7相连。振动流化床干燥机4和滚筒式冷却机6设置的出气口(排风口)均与尾气处理系统7连接,尾气余热由余热回收系统8收集,余热回收系统8与振动流化床干燥机4进气口(风口)相连,为振动流化床干燥机4提供热源。本实施例得到的疏浚底泥轻质陶粒的堆密度为712kg/m3,筒压为3.28mpa,吸水率为11.8%。本实施例得到的疏浚底泥轻质陶粒重金属浸出结果见表2。表2实施例2陶粒重金属浸出结果项目cdcrcunipbzn含量(mg/l)0.0010.0170.15nd0.010.103注:表2中nd表示notdetect,未检到。本实施例得到的疏浚底泥轻质陶粒完全符合《轻集料及其试验方法》(gb/t17431.1-2010)和《危险废物鉴别标准-浸出毒性鉴别》(gb5085.3-2007)的标准要求。通过上述的实施例可知,通过使用本发明的装置制备轻质陶粒,具有以下的优点:1)干化疏浚底泥粒度细、河沙含量大、有机质含量高,作为原料可制备多孔结构、比表面积大的轻质陶粒。2)碱渣含大量的cao、mgo、k2o等碱金属氧化物,可促进陶粒烧结过程中液相的生成,降低陶粒烧结能耗。3)粉煤灰粒度细,含大量的sio2、al2o3及微量金属元素,可提高陶粒强度;调控陶粒表面的电荷性能,提高陶粒生物亲和性。4)采用润磨机作为混磨装置,处理物料含水率为8%~15%,可免去混合物料干燥环节,缩短工艺流程,粉磨效率高、设备使用寿命长。5)陶粒干燥、预热、烧结过程中均进行尾气收集和处理,不会造成空气污染;余热回收系统,可将陶粒预热与烧结过程中的烟气余热回收,用于陶粒生料的干燥,热能利用率高,生产能耗和成本低。6)高温烧结过程可有效去除疏浚底泥中有机污染物,陶粒内部形成的玻璃质硅铝酸盐能有效固定底泥中重金属污染物,进一步强化疏浚底泥无害化处理,降低陶粒应用过程中的污染风险。7)陶粒原料均为固体废弃物,廉价易得,制备的陶粒密度小、强度高、可调控性能高、生物亲和性好,是良好的水处理生物填料,实现底泥资源化处理。当前第1页12